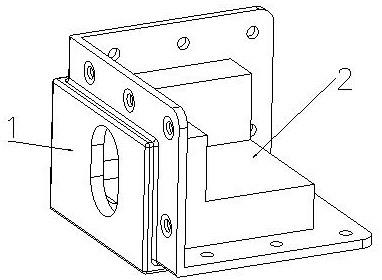
[0001]
本发明涉及方舱技术领域,特指一种复合材料方舱角件、成型模具及其成型方法。
背景技术:[0002]
方舱技术在国内外已普遍应用。方舱因有其特有的优点,使用领域不断扩大。随着我国军工国防事业的发展,对方舱的轻量化、耐腐蚀等性能提出更高要求。现有的方舱角件采用铝合金和铸钢制作,不能满足三防要求,特别是沿海地区盐雾腐蚀要求,同时也不能满足方舱轻量化的趋势。复合材料具有耐腐蚀、轻量化、耐疲劳、抗断裂能力强等优点,是未来方舱产品的重要发展方向。因此,采用复合材料方舱角件是十分必要的。
[0003]
目前,方舱行业通用角件多采用铝合金或钢制角件,耐盐雾性能差、重量大。
技术实现要素:[0004]
针对现有技术存在的缺陷,本发明提供一种复合材料方舱角件、成型模具及其成型方法。
[0005]
为实现上述技术目的,本发明的技术方案是:复合材料方舱角件,包括角件本体,角件本体由玻璃纤维布及环氧树脂通过真空袋压灌注工艺成型,角件本体包括外壳层以及加厚层。所述外壳层由相互垂直的三个侧面围合而成,三个侧面上分别开设有第一侧孔、第二侧孔和第三侧孔,各侧面的内侧外缘设置有一定宽度的外边,各外边彼此垂直连接在一起形成外壳层外边框,外壳层外边框上设有安装孔,外壳层外边框内侧围合形成外壳层内腔;外壳层内腔由内到外依次叠置有一层以上的结构相同的加厚层。各加厚层由相互垂直的三个侧面围合而成,且加厚层的三个侧面上分别开设有与外壳层对应侧面上所开侧孔相通的侧孔,加厚层的三个侧面的外缘设有彼此连接的直角折边,直角折边内侧形成能够叠置下一层加厚层的加厚层内腔。
[0006]
作为本发明的进一步限定,角件本体还包括底加厚层,至少一个加厚层内腔的底侧壁上设置有底加厚层,所述底加厚层上对应开设有侧孔。
[0007]
作为本发明的进一步限定,角件本体还包括外加强层,外加强层为框架结构,包括连接为一体的折边框和外加强层外边框,外加强层设在最外层加厚层上,其中折边框对应叠置在最外层加厚层的折边上,外加强层外边框叠置在外壳层外边框上,外加强层外边框上设有与外壳层外边框上安装孔一一对应的安装孔。
[0008]
作为本发明的进一步限定,还包括防雨罩,防雨罩采用玻璃纤维布及环氧树脂通过真空袋压灌注工艺单独成型,防雨罩套罩在角件本体上,将角件本体内侧腔体密封。
[0009]
本发明提供一种上述复合材料方舱角件的成型模具,包括底板、第一侧板、第二侧板、底压板、第一侧压板、第二侧压板、内腔成型块及侧孔成型块;底板、第一侧板和第二侧板相互垂直拼装在一起,底板、第一侧板和第二侧板内侧面均设置有内腔且内腔内均安装有用于成型侧孔的侧孔成型块,底板、第一侧板和第二侧板的
凹腔外围面板设置有一圈安装孔成型凸块,底压板、第一侧压板、第二侧压板通过螺栓分别安装在底板、第一侧板和第二侧板的安装孔成型凸块外围。内腔成型块用于成型复合材料方舱角件其各加厚层的直角折边以及加厚层内腔。内腔成型块的各个侧面分别对应连接在底板、第一侧板和第二侧板上。
[0010]
作为进一步优化方案,内腔成型块包括第一下层内腔成型块、第二下层内腔成型块、第三下层内腔成型块、第一上层内腔成型块和第二上层内腔成型块,第一下层内腔成型块通过螺栓安装在底板上的侧孔成型块上,第二下层内腔成型块、第一上层内腔成型块均分别通过螺栓安装在第一侧板上的侧孔成型块上,第三下层内腔成型块、第二上层内腔成型块均分别通过螺栓安装在第二侧板上的侧孔成型块上。
[0011]
作为进一步优化方案,安装在底板、第一侧板和第二侧板上的侧孔成型块可以选择相同的侧孔成型块,也可以选择尺寸、形状不同的侧孔成型块,这样就可以实现一套模具生产不同的复合材料方舱角件的目的。
[0012]
进一步地,所述底板、第一侧板、第二侧板、底压板、第一侧压板、第二侧压板、第一下层内腔成型块、第二下层内腔成型块、第三下层内腔成型块、第一上层内腔成型块、第二上层内腔成型块及侧孔成型块均由碳钢加工而成。
[0013]
本发明提供一种上述复合材料方舱角件的成型方法,包括:第一步,准备复合材料方舱角件的成型模具、玻璃纤维布及混合环氧树脂;第二步,将成型模具的底板、第一侧板、第二侧板相互垂直拼装在一起,并将各侧孔成型块分别安装到底板、第一侧板、第二侧板上;第三步,依次铺外壳层、加厚层以及底加厚层的玻璃纤维布;第四步、安装内腔成型块;第五步,将各加厚层的玻璃纤维布依次包裹到内腔成型块上;第六步,铺外加强层的玻璃纤维布;第七步,依次安装底压板、第一侧压板、第二侧压板;第八步,采用真空袋压导入工艺成型;第九步,制备防雨罩;第十步,粘接角件本体及防雨罩,即可。
[0014]
与现有技术相比,本发明的有益效果是:首先本发明整体采用由玻璃纤维布及环氧树脂通过真空袋压灌注工艺成型,复合材料具有耐腐蚀、轻量化、耐疲劳、抗断裂能力强等优点,是未来方舱产品的重要发展方向。因此,采用复合材料方舱角件是十分必要的。另外,本发明的角件结构设计合理,通过加厚层增强其整体的强度,同时通过设计直角折边以及加厚层内腔,使得其在轻质的前提下,具有更好的抗压、抗断裂能力,整体的强度性能优越。
附图说明
[0015]
为了更清楚地说明本发明实施例或现有技术中的技术方案,下面将对实施例或现有技术描述中所需要使用的附图作简单地介绍,显而易见地,下面描述中的附图仅仅是本发明的一些实施例,对于本领域普通技术人员来讲,在不付出创造性劳动的前提下,还可以根据这些附图示出的结构获得其他的附图。
[0016]
图1为本发明一实施例提供的复合材料方舱角件的结构示意图;图2为图1的爆炸图;图3为本发明一实施例提供的角件本体的铺层结构示意图;图4为本发明一实施例提供的成型模型的结构示意图;图5为图4的爆炸图;图6为一种侧孔成型块的结构示意图;图7为本发明一实施例提供的复合材料方舱角件的成型方法流程图。
[0017]
图中标号:1、角件本体;101、外壳层;102、外加厚层;103、底加厚层;104、内加厚层;105、内壳层;106、外加强层;107、侧孔;108、外壳层外边框;109、安装孔;110、外壳层内腔;111、直角折边;112、加厚层内腔;113、折边框;114、外加强层外边框;2、防雨罩;3、底板;4、第一侧板;5、第二侧板;6、底压板;7、第一侧压板;8、第二侧压板;9、内腔成型块;901、第一下层内腔成型块;902、第二下层内腔成型块;903、第三下层内腔成型块;904、第一上层内腔成型块;905、第二上层内腔成型块;10、侧孔成型块;11、安装孔成型凸块。
具体实施方式
[0018]
下面将结合本发明实施例中的附图,对本发明实施例中的技术方案进行清楚、完整地描述,显然,所描述的实施例仅仅是本发明的一部分实施例,而不是全部的实施例。基于本发明中的实施例,本领域普通技术人员在没有作出创造性劳动前提下所获得的所有其他实施例,都属于本发明保护的范围。
[0019]
需要说明,本发明实施例中所有方向性指示(诸如上、下、左、右、前、后
……
)仅用于解释在某一特定姿态(如附图所示)下各部件之间的相对位置关系、运动情况等,如果该特定姿态发生改变时,则该方向性指示也相应地随之改变。
[0020]
另外,在本发明中如涉及“第一”、“第二”等的描述仅用于描述目的,而不能理解为指示或暗示其相对重要性或者隐含指明所指示的技术特征的数量。由此,限定有“第一”、“第二”的特征可以明示或者隐含地包括至少一个该特征。在本发明的描述中,“多个”的含义是至少两个,例如两个,三个等,除非另有明确具体的限定。
[0021]
在本发明中,除非另有明确的规定和限定,术语“连接”、“固定”等应做广义理解,例如,“固定”可以是固定连接,也可以是可拆卸连接,或成一体;可以是机械连接,也可以是电连接,还可以是物理连接或无线通信连接;可以是直接相连,也可以通过中间媒介间接相连,可以是两个元件内部的连通或两个元件的相互作用关系,除非另有明确的限定。对于本领域的普通技术人员而言,可以根据具体情况理解上述术语在本发明中的具体含义。
[0022]
另外,本发明各个实施例之间的技术方案可以相互结合,但是必须是以本领域普通技术人员能够实现为基础,当技术方案的结合出现相互矛盾或无法实现时应当认为这种技术方案的结合不存在,也不在本发明要求的保护范围之内。
[0023]
参照图1和图2,在一实施例中,提供一种复合材料方舱角件,包括角件本体1和防雨罩2,角件本体1由玻璃纤维布及环氧树脂通过真空袋压灌注工艺单独成型,防雨罩采用玻璃纤维布及环氧树脂通过真空袋压灌注工艺单独成型,防雨罩2套罩在角件本体1上,将角件本体1内侧腔体密封。
[0024]
参照图3,在一实施例中,角件本体1包括外壳层101、一层以上的加厚层以及外加强层106。本实施例中一层以上的加厚层依次包括外加厚层102、内加厚层104和内壳层105,其中在外加厚层102和内加厚层104之间的底部还包括底加厚层103。
[0025]
所述外壳层101由相互垂直的三个侧面围合而成,三个侧面上分别开设有侧孔107,分别为第一侧孔、第二侧孔和第三侧孔。各侧面的内侧外缘设置有一定宽度的外边,各外边彼此垂直连接在一起形成外壳层外边框108,外壳层外边框108上设有安装孔109,外壳层外边框108内侧围合形成外壳层内腔110。
[0026]
外加厚层102、内加厚层104和内壳层105均由相互垂直的三个侧面围合而成,且三个侧面上均分别开设有与外壳层101对应侧面上所开侧孔相通的侧孔107,且三个侧面的外缘设有彼此连接的直角折边111,直角折边内侧形成能够叠置下一层加厚层的加厚层内腔112。加厚层的设置使得角件本体在三个侧面上的整体强度得到大大的提升,进一步地,在各加厚层上设置直角折边并形成加厚层内腔,形成一个立体的加强结构,这样能够对加厚层的边缘等比较薄弱的地方进行加强,大大提升了角件本体整体的抗冲击能力。
[0027]
本发明还包括外加强层106,外加强层106为框架结构,包括连接为一体的折边框113和外加强层外边框114,外加强层106设在最外层加厚层(即图3中的内壳层)上,其中折边框113对应叠置在最外层加厚层的折边上,外加强层外边框114叠置在外壳层外边框108上,外加强层外边框114上设有与外壳层外边框108上安装孔109一一对应的安装孔109。外加强层106的折边框113对加厚层的直角折边111进一步加强和保护,同时外加强层106的外加强层外边框114对外壳层的外壳层外边框108进行加强和保护,进一步提升了整体的抗冲击能力和强度,使本发明的整体性更好,强度更优越。
[0028]
在本发明一实施例中,外壳层101由6层玻璃纤维布组成。外加厚层102由5层玻璃纤维布组成。底加厚层103由28层玻璃纤维布组成。内加厚层104由5层玻璃纤维布组成。内壳层105由3层玻璃纤维布组成。外加强层106由6层玻璃纤维布组成。在实际应用中,也可以根据需要将外壳层101、外加厚层102、底加厚层103、内加厚层104、内壳层105和外加强层106的玻璃纤维布层数进行调整,使其满足强度、质量等需求。
[0029]
参照图4和图5,在本发明一实施例中,提供了上述复合材料方舱角件的成型模具,包括底板3、第一侧板4、第二侧板5、底压板6、第一侧压板7、第二侧压板8、内腔成型块9及侧孔成型块10。
[0030]
底板3、第一侧板4和第二侧板5相互垂直拼装在一起,底板3、第一侧板4和第二侧板5内侧面均设置有内腔且内腔内均安装有用于成型侧孔的侧孔成型块10,底板3、第一侧板4和第二侧板5的凹腔外围面板设置有一圈安装孔成型凸块11,底压板6、第一侧压板7、第二侧压板8通过螺栓分别安装在底板3、第一侧板4和第二侧板5的安装孔成型凸块外围。内腔成型块9用于成型复合材料方舱角件其各加厚层的直角折边以及加厚层内腔。内腔成型块9的各个侧面分别对应连接在底板3、第一侧板4和第二侧板5上。
[0031]
在一实施例中,内腔成型块9包括第一下层内腔成型块901、第二下层内腔成型块902、第三下层内腔成型块903、第一上层内腔成型块904和第二上层内腔成型块905,第一下层内腔成型块901通过螺栓安装在底板上的侧孔成型块上,第二下层内腔成型块902、第一上层内腔成型块904均分别通过螺栓安装在第一侧板上的侧孔成型块上,第三下层内腔成型块903、第二上层内腔成型块905均分别通过螺栓安装在第二侧板上的侧孔成型块上。
[0032]
在一实施例中,所述底板3、第一侧板4、第二侧板5、底压板6、第一侧压板7、第二侧压板8、第一下层内腔成型块901、第二下层内腔成型块902、第三下层内腔成型块903、第一上层内腔成型块904、第二上层内腔成型块905及侧孔成型块10均由碳钢加工而成。
[0033]
作为进一步优化方案,安装在底板3、第一侧板4和第二侧板5上的侧孔成型块10可以选择相同的侧孔成型块,也可以选择尺寸、形状不同的侧孔成型块,这样就可以实现一套模具生产不同的复合材料方舱角件的目的。参照图6,提供了一种侧孔成型块的结构示意图。
[0034]
图7为本发明一实施例提供的复合材料方舱角件的成型方法流程图,包括以下步骤:第一步,准备复合材料方舱角件的成型模具并清洗干净,准备原材料即玻璃纤维布和混合环氧树脂。
[0035]
第二步,将成型模具的底板、第一侧板、第二侧板相互垂直拼装在一起,并将各侧孔成型块分别安装到底板、第一侧板、第二侧板上。
[0036]
第三步,依次铺外壳层、外加厚层、底加厚层、内加厚层以及内壳层的玻璃纤维布;第四步、安装内腔成型块,包括安装下层内腔成型块以及上层内腔成型块。
[0037]
第五步,将外加厚层、内加厚层、内壳层的玻璃纤维布依次包裹到内腔成型块上;第六步,铺外加强层的玻璃纤维布;第七步,依次安装底压板、第一侧压板、第二侧压板;第八步,采用真空袋压导入工艺成型;第九步,制备防雨罩;第十步,粘接角件本体及防雨罩,即可。
[0038]
综上所述,虽然本发明已以较佳实施例揭露如上,然其并非用以限定本发明,任何本领域普通技术人员,在不脱离本发明的精神和范围内,当可作各种更动与润饰,因此本发明的保护范围当视权利要求书界定的范围为准。