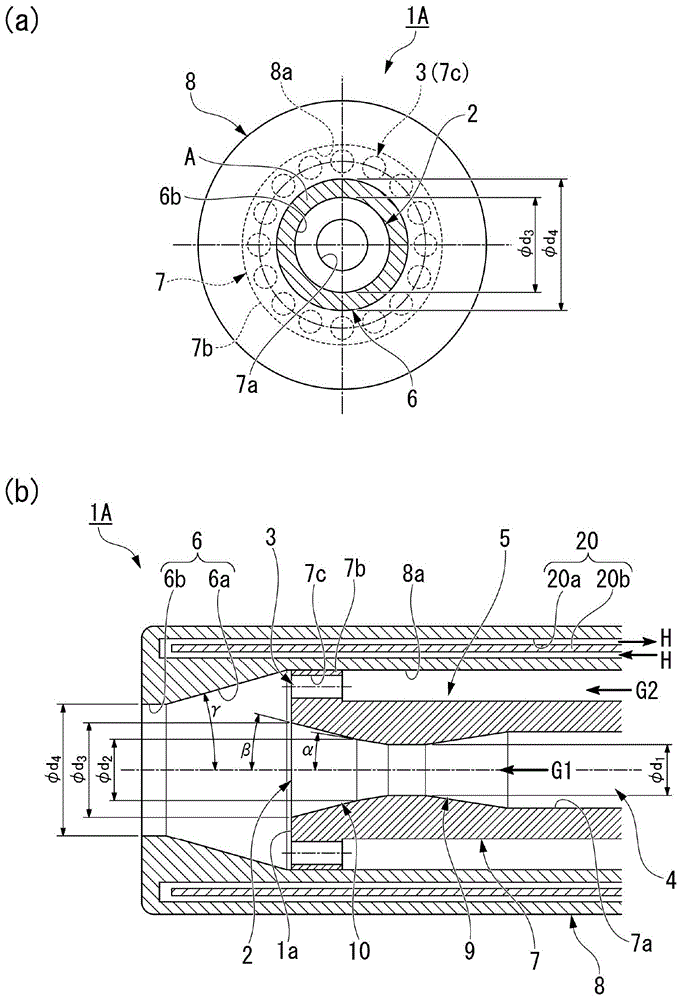
本发明涉及燃烧器、燃烧器的操作方法及冷铁源的熔解和提纯方法。
背景技术:
:在冷铁源的熔解提纯炉中,使用例如从喷嘴喷射含氧的助燃性气体和燃料,并通过燃烧的火焰加热被加热物的燃烧器。例如,在电弧炉炼钢工艺中,在将成为原料的铁屑等冷铁源在炉内进行加热并使其熔融时,有时在原料中产生称为冷点的低温部分,原料在该部分难以熔融。因此,用燃烧器加热该低温部分的原料来促进其熔融。通过使用这种燃烧器,能够提高原料的加热效率,减少原料的熔融中所需要的用电量,降低熔融成本。另外,已知通过助燃性气体使一部分原料氧化及熔融,由此促进切割,并提高对于原料的加热效率。在燃烧器中,通过增加助燃性气体的流速,可以提高被加热物的切割速度,并且可以提高加热效率,因此要求助燃性气体的高速化。然而,当使助燃性气体的流速高速化时,火焰从喷嘴分离,并且燃烧变得不稳定。此外,在电弧炉中,由于伴随着来自钢水及炉渣的co气体的产生而沸腾的熔融金属和炉渣飞散、高速火焰与原料碰撞,由此熔融金属和炉渣产生反跳。在燃烧器中,由于上述的熔融金属或炉渣,喷嘴可能发生堵塞,也可能发生熔损。因此,需要经常维护燃烧器。特别是,由于燃料的喷出速度无法与助燃性气体的喷出速度一样快,喷嘴容易堵塞。为了抑制这种燃料喷嘴的堵塞,采用尽可能提高燃料的喷出速度等方法。例如,在下述的专利文献1中所述的燃烧器中,在中心设置助燃性气体的喷出孔,在该喷出孔的出口设置用于保持火焰的凹槽,并在这些喷出孔和凹槽之间设置燃料的喷出孔来形成稳定的高速火焰。另一方面,在下述的专利文献2中所述的燃烧器中,在中心设置助燃性气体的喷出孔,在该喷出孔的出口设置用于保持火焰的凹槽,在这些喷出孔与凹槽之间设置第一燃料喷出孔,并在助燃性气体的出口的外周围设置第二燃料喷出孔来形成稳定的高速火焰。另一方面,在下述专利文献3中所述的燃烧器中,在中心配置主助燃性气体的喷出孔,在其外侧配置燃料喷出孔,在更外侧配置副助燃性气体的喷出孔,在主助燃性气体的喷流的周围形成火焰包围面,从而获得主气体的集束射流并形成高速火焰。并且,在喷嘴的前表面上设置挡板,使得火焰向内并朝向助燃性气体喷射的方向,从而抑制主助燃性气体的流速的衰减。此外,记载有如下重要内容:当将燃料气体的燃烧热设为q[mmbtu/h],将挡板的孔径为d[英寸]时,则q/d≥0.6;以及当将助燃性气体的流速设为v[千立方英尺/h],将助燃性气体中的氧浓度设为p[容积%],将挡板的孔径为d[英寸]时,则vp/d≥70。基于该条件,例如,假设燃烧器的液化天然气(lng)流量为435nm3/h,氧流量为1000nm3/h,则挡板的孔径d为709mm(27.9英寸)。并且,根据vp/d≥70的关系,挡板的孔径d为1361mm(53.6英寸)。[专利文献1]日本特开2003-194307号公报[专利文献2]日本特开2004-93110号公报[专利文献3]日本特开平10-267220号公报在电弧炉中,为了防止喷嘴被上述飞散的熔融金属或炉渣堵塞,当使用低供应压力的燃料或可燃性差的燃料时,必须减慢从燃料喷嘴喷出的速度。然而,在这种情况下,喷嘴孔容易被飞溅物阻塞,则喷嘴损坏或维护频率增加。另外,当燃料喷出速度较慢时,容易受到炉内的燃烧气体流动等引起的外部干扰的影响,不能在中心喷流的周围形成良好的火焰。在这种情况下,中心氧的衰减加速,加热性能和切割性能降低。此外,当使用低热值的燃料时,每单位体积的容积增加,因此必须增加燃料喷嘴的孔径,并且喷嘴孔容易堵塞。此外,当使用可燃性差的燃料时,火焰容易被吹散,因此不能增加燃料的喷出速度。在专利文献1中所述的燃烧器中,由于燃料喷出孔配置在助燃性气体喷出孔的内表面,从而燃料喷出孔的剖面积不能增加,并且喷出速度不能降低。因此,难以应用于低供应压力的燃料或可燃性差的燃料。另一方面,在专利文献2中所述的燃烧器中,尽管可以增加燃料喷出孔的剖面积,但是燃料喷出孔设置在燃烧器的前表面,因此容易被飞散的熔融金属或炉渣堵塞。此外,当使用具有低热值的燃料时,每单位热值的容积变大,使得燃料喷出孔的剖面积变大,并且变得更容易堵塞。另一方面,在专利文献3中所述的燃烧器中,如上所述,挡板的孔径为709mm或1361mm,则不能防止喷嘴被飞散的熔融金属或炉渣堵塞。此外,在专利文献3中所述的燃烧器中,如果挡板的孔径超出上述范围,则中心的助燃性气体射流不会被火焰包围,从而助燃性气体的衰减加快,无法获得高速火焰。技术实现要素:本发明是鉴于上述情况所提出,其目的在于提供一种可以防止喷嘴被熔融金属或炉渣堵塞或损伤等的燃烧器、燃烧器的操作方法及冷铁源的熔解和提纯方法。为了达到上述目的,本发明提供了以下的技术方案。[1]一种燃烧器,其特征在于,其具备:助燃性气体供给路,朝向设置于所述燃烧器的前端侧中心部的助燃性气体喷出口供给助燃性气体;燃料供给路,朝向设置于所述助燃性气体喷出口的周围的燃料喷出口供给燃料;以及防护喷嘴,从围绕所述燃料喷出口的周围,相比于设置有所述助燃性气体喷出口及所述燃料喷出口的前端面向前方更突出,所述助燃性气体供给路包括拉瓦尔喷嘴和扩径喷嘴,所述扩径喷嘴从所述拉瓦尔喷嘴的前端朝向所述助燃性气体喷出口逐渐扩径,所述防护喷嘴具有从所述前端面朝向前方逐渐缩径的形状。[2]根据上述[1]所述的燃烧器,其特征在于,所述助燃性气体供给路包括从所述扩径喷嘴的前端朝向所述助燃性气体喷出口且为相同直径的同径喷嘴。[3]根据上述[2]所述的燃烧器,其特征在于,在整个所述同径喷嘴的内周面上设置有凹槽部。[4]根据上述[1]~[3]中任一项所述的燃烧器,其特征在于,在所述扩径喷嘴中,将直径最大的前端侧的剖面积设为a1,将直径最小的基端侧的剖面积设为a2时,满足1.5≤a1/a2≤3.0。[5]根据上述[1]~[4]中任一项所述的燃烧器,其特征在于,所述扩径喷嘴的开口角为所述拉瓦尔喷嘴的扩径侧的开口角以上,并且所述扩径喷嘴的半顶角为30°以下。[6]根据上述[1]~[5]中任一项所述的燃烧器,其特征在于,所述燃料喷出口由相对于所述助燃性气体喷出口排列为同心圆状的多个孔部构成。[7]根据上述[1]~[5]中任一项所述的燃烧器,其特征在于,所述燃料喷出口由相对于所述助燃性气体喷出口形成为同心圆状的孔部构成。[8]根据上述[1]~[7]中任一项所述的燃烧器,其特征在于,所述防护喷嘴的半顶角为5°~45°。[9]根据上述[1]~[8]中任一项所述的燃烧器,其特征在于,将所述扩径喷嘴的最大直径设为d3[m],将所述防护喷嘴的前端的直径设为d4[m],将相对于供给的助燃性气体的流量以化学计量比(氧比=1)燃烧所需的燃料的流量设为qf[nm3/h]时,所述d3及所述d4被设定为由下式(1)求出的将所述qf除以面积a得到的燃料的流速v[nm/s]满足50≤v≤200,其中所述面积a为从所述防护喷嘴的出口面积减去所述扩径喷嘴的出口面积后的面积,v=(qf/3600)/a…(1)a=π/4×(d42-d32)。[10]一种燃烧器的操作方法,其特征在于,使用根据上述[1]~[9]中任一项所述的燃烧器,并使用浓度为20.95-100%的氧气作为所述助燃性气体。[11]根据上述[10]的燃烧器的操作方法,其特征在于,将从燃料喷出口喷出的燃料的流速设为10m/s以上。[12]根据上述[10]或[11]的燃烧器的操作方法,其特征在于,将氧比设为1~10。[13]一种冷铁源的熔解和提纯方法,其特征在于,使用根据上述[1]~[9]中任一项所述的燃烧器,所述方法包括:将冷铁源熔解的熔解工序;和将冷铁源熔解之后进行提纯的提纯工序,在所述熔解工序中,将氧比设为1~5,在所述提纯工序中,将氧比设为3~10,在所述熔解工序及所述提纯工序中,分别独立地设定燃料的流量。如上所述,根据本发明,能够提供一种可以防止喷嘴被熔融金属或炉渣堵塞或损伤等的燃烧器、燃烧器的操作方法及冷铁源的熔解和提纯方法。附图说明图1示出本发明第一实施方式的燃烧器的结构,图1的(a)是从其前端侧观察的主视图,图1的(b)是沿其轴线方向的剖面图。图2示出本发明第二实施方式的燃烧器的结构,图2的(a)是从其前端侧观察的主视图,图2的(b)是沿其轴线方向的剖面图。图3示出本发明第三实施方式的燃烧器的结构,图3的(a)是从其前端侧观察的主视图,图3的(b)是沿其轴线方向的剖面图。图4是对于实施例1和比较例1,测量距燃烧器的距离与助燃性气体流速之间关系的图表。图5是对于实施例2及作为参考例的实施例1,测量距燃烧器的距离与助燃性气体流速之间关系的图表。具体实施方式以下,参照附图对本发明的实施方式进行详细说明。另外,为了易于理解特征,在以下说明中所使用的附图有时为了方便而放大表示特征部分,各结构部件的尺寸比例等不限于与实际相同。并且,在以下说明中所举例的材料等为一例,本发明并不必须限定于这些材料,可以在不脱离其宗旨的范围内进行适当地修改来实施。(燃烧器)[第一实施方式]首先,作为本发明的第一实施方式,对例如图1的(a)、(b)所示的燃烧器1a进行说明。另外,图1表示燃烧器1a的结构,(a)为从其前端侧进行观察的主视图,(b)是沿其轴线方向的剖面图。如图1的(a)、(b)所示,本实施方式的燃烧器1a具备:助燃性气体喷出口2,设置于所述燃烧器1a的前端侧的中心部;燃料喷出口3,设置于助燃性气体喷出口2的周围;助燃性气体供给路4,朝向助燃性气体喷出口供给助燃性气体g1;燃料供给路5,朝向燃料喷出口3供给燃料g2;防护喷嘴6,从围绕燃烧喷出口3的周围,相比于设置有助燃性气体喷出口2及燃料喷出口3的前端面向前方更突出。燃烧器1a由设置在其中心部的第一喷嘴部件7及同心地设置在第一喷嘴部件7的外侧的第二喷嘴部件8构成。并且,关于这些构成燃烧器1a的第一喷嘴部件7及第二喷嘴部件8,使用例如铜或铜合金(黄铜)等导热性优异的金属材料形成,但不必限于使用这些金属材料。第一喷嘴部件7具有在轴线方向贯穿其中心部的截面圆形的孔部7a,从而整体形成大致圆筒状。通过该孔部7a构成助燃性气体供给路4。助燃性气体喷出口3位于第一喷嘴部件7的前端部。也就是说,助燃性气体喷出口3与孔部7a的前端位于同一表面上。并且,在第一喷嘴部件7的前端侧设置有在扩径方向突出的凸缘部7b。第二喷嘴部件8具有在轴线方向贯穿其中心部的截面圆形的孔部8a,从而整体形成大致圆筒状。第一喷嘴部件7通过插入该孔部8a的内侧,以凸缘部7b接触整个圆周的状态配置于孔部8a。另外,前端面1a由包含该凸缘部7b的第一喷嘴部件7的前端构成。燃料供应路5由形成在第一喷嘴部件7和孔部8a(第二喷嘴部件8)之间的截面圆环状的流路构成。通过在轴线方向贯穿凸缘部7b的多个孔部7c相对于助燃性气体喷出口2排列成同心圆状来构成燃料喷出口3。多个孔部7c彼此具有相同的直径而形成为截面圆形。另外,关于燃料喷出口3,不限于由上述多个孔部7c构成的情况,还可以省略上述凸缘部7b,在第一喷嘴部件7和孔部8a(第二喷嘴部件8)之间形成的流路的前端,通过相对于助燃性气体喷出口2而形成为同心圆状的截面圆环状的孔部构成。助燃性气体供给路4(孔部7a)从上游(基端)侧朝向下游(前端)侧具有拉瓦尔喷嘴9和扩径喷嘴10而构成。其中,拉瓦尔喷嘴9用于将助燃性气体g1设为超音速,并且在孔部7a的中途具有缩小直径的形状。另一方面,扩径喷嘴10用于形成稳定的火焰,并且具有从拉瓦尔喷嘴9的前端朝向助燃性气体喷出口2逐渐扩径的形状。在此,作为拉瓦尔喷嘴9的尺寸的喉部直径d1和出口直径d2取决于助燃性气体g1的流量及喷出速度、以及助燃性气体g1的组成。因此,当拉瓦尔喷嘴9的半顶角α和扩径喷嘴10的半顶角β相同时,助燃性气体喷出口2比拉瓦尔喷嘴9的出口直径d2的扩径程度更高。防护喷嘴6用于防护助燃性气体喷出口2及燃料喷出口3免受飞散的熔融金属、炉渣等的影响,并且由比前端面1a(第一喷嘴部件7的前端)向前方更突出的第二喷嘴部件8构成。也就是说,防护喷嘴6的内壁相当于形成比前端面1a向前方更突出的孔部8a的壁。防护喷嘴6具有从前端面1a朝向前方逐渐缩径的形状(称该部分为缩径部6a)。第一喷嘴部件7的前端(前端面1a)位于孔部8a的同径部分和缩径部分之间的边界。防护喷嘴6的前端具有从最缩径位置朝向前端而设为同径的形状(称该部分为同径部6b)。在第二喷嘴部件8设置有水冷套20,其通过冷却水h的循环而冷却。水冷套20具有如下结构:通过分隔壁20b在内周侧和外周侧之间将设置在第二喷嘴部件8的内部的流路20a进行分隔,并且在其前端侧连通流路20a。冷却水h通过从流路20a的内周侧向外周侧流通来进行燃烧器1的冷却。在具有如上所述结构的燃烧器1a中,作为助燃性气体g1可以使用例如氧,作为燃料g2可以使用例如液化天然气(lng)。并且,作为燃料g2,除了上述lng之外,例如可以使用城市燃气或液化丙烷气(lpg)等的碳氢类气体、焦炉煤气(cog)、高炉煤气(bfg)、一氧化碳(co)、氢(h2)以及这些的混合气体等。在燃烧器1a中,可将从助燃性气体供给路4供给的助燃性气体g1从助燃性气体喷出口2朝向前方喷出,将从燃料供给路5(孔部7c)供给的燃料g2从燃料喷出口3朝向前方喷出,并且通过燃烧的火焰加热被加热物。在本实施方式的燃烧器1中,通过在拉瓦尔喷嘴9的前端处设置具有上述扩径的形状的扩径喷嘴10,从拉瓦尔喷嘴9喷出的助燃性气体g1的射流的外侧成为负压,并且在射流和扩径喷嘴10的壁面之间形成循环流。此外,燃料g2被吸入循环流中并形成稳定的火焰。因此,通过助燃性气体g1被该火焰包围,助燃性气体g1的衰减得到抑制,并且可以进一步形成更高速的火焰。并且,在本实施方式的燃烧器1中,将上述具有缩径部6a的防护喷嘴6设置为相比于设置有助燃性气体喷出口2及燃料喷出口3的前端面1a向前方更突出,从而抑制火焰的扩散,并且从各喷出口2、3喷射高速的助燃性气体g1和燃料g2。因此,在本实施方式的燃烧器1中,即使在使用了供给压力低的燃料g2的情况下,由于能够抑制飞散的熔融金属或炉渣向各喷出口2、3侵入,因此可以防止飞散的熔融金属或炉渣引起的喷嘴的堵塞或损伤等。[第二实施方式]接着,作为本发明的第二实施方式,对例如图2所示的燃烧器1b进行说明。并且,图2表示燃烧器1b的结构,(a)是从其前端侧观察的主视图,(b)是沿着其轴线方法的剖面图。并且,在以下的说明中,对于与上述燃烧器1a相同的部位省略说明,并且在附图中标出相同的附图标记。如图2所示,本实施方式的燃烧器1b构成如下:助燃性气体供给路4从上游(基端)朝向下游(前端)具有拉瓦尔喷嘴9、扩径喷嘴10及同径喷嘴11。在轴线方向上具有长度l2的同径喷嘴11具有从扩径喷嘴10的前端朝向助燃性气体喷出口2设为相同直径的形状。除此之外,其具有与燃烧器1a基本相同的结构。在本实施方式的燃烧器1b中,通过设为增加这样的同径喷嘴11的结构,将由扩径喷嘴10形成的火焰朝向轴线方向,并且能够抑制火焰的扩散。并且,火焰包围流过中心的助燃性气体g1的射流并平行于轴线方向流动。由此,抑制了助燃性气体g1的衰减,并且可以进一步形成高速火焰。[第三实施方式]接着,作为本发明的第三实施方式,对例如图3所示的燃烧器1c进行说明。并且,图3表示燃烧器1c的结构,(a)是从其前端侧观察的主视图,(b)是沿其轴线方向的剖面图。并且,在以下的说明中,对于与上述燃烧器1a、1b相同的部位省略说明,并且在附图中标出相同的附图标记。如图3所示,本实施方式的燃烧器1c为在同径喷嘴11a的内周面的整个圆周上设置有凹槽部11a的结构。除此之外,其具有与燃烧器1a、1b基本相同的结构。在本实施方式的燃烧器1b中,通过在同径喷嘴11a的内周面上设置这样的凹槽部11a,上述火焰保持效果增加,并且即使使用低热值的燃料g2或可燃性差的燃料g2,也可以形成稳定的周围火焰。[第四实施方式]接着,作为本发明的第四实施方式,对于上述燃烧器1a、1b及1c的适宜条件进行说明。在本实施方式的燃烧器1a、1b及1c中,在扩径喷嘴10中,将直径最大的前端侧的剖面积设为a1,将直径最小的基端侧的剖面积设为a2时,优选满足以下条件:1.5≤a1/a2≤3.0。通过满足该条件,在扩径喷嘴10的壁面与助燃性气体g1的射流之间形成负压区域,能够以包围助燃性气体g1的方式形成稳定的火焰。并且,在本实施方式的燃烧器1a、1b及1c中,扩径喷嘴10的开口角(半顶角β)优选为拉瓦尔喷嘴9的扩径侧的开口角(半顶角α)以上,并且扩径喷嘴10的半顶角β为30°以下。由此,在扩径喷嘴10的壁面与流过中心的助燃性气体g1的射流之间形成循环流,燃料g2被引入扩径喷嘴10,能够形成稳定的火焰。如果扩径喷嘴10的开口角(半顶角β)为拉瓦尔喷嘴的开口角α以上,则在扩径喷嘴10的壁面与流过中心的助燃性气体g1的射流之间形成循环流,能够形成稳定的火焰。此外,在扩径喷嘴10中直径最大的前端侧的剖面积固定的状态下,若缩小扩径喷嘴10的开口角(半顶角β),则循环区域的长度变长。具体而言,若将扩径喷嘴10的半顶角β设为30°以下,则形成充分的循环区域,并能够形成稳定的火焰。此外,在本实施方式的燃烧器1a、1b及1c中,防护喷嘴6的半顶角γ优选为5~45°。由此,通过助燃性气体g1或燃料g2的射流,能够有效地将侵入防护喷嘴6的内侧的熔融金属或熔渣等排出到防护喷嘴6的外侧。当防护喷嘴6的半顶角γ为5°以上时,防护喷嘴6的长度缩短,到防护喷嘴6的热损失减少,可以保持较高的热效率。而且,到防护喷嘴6的内表面的热通量变小,可以防止对防护喷嘴6的损坏。另一方面,当防护喷嘴6的半顶角γ设定为45°以下时,已侵入防护喷嘴6的熔融金属或炉渣等不会停留在防护喷嘴6内部而可以排出。(燃烧器的操作方法)[第五实施方式]接下来,作为本发明的第五实施方式,对上述燃烧器1a、1b和1c的操作方法进行说明。在使用本实施方式的燃烧器1a、1b和1c的操作方法中,使用浓度为20.95~100%的氧作为助燃性气体g1。由此,即使在使用供应压力低或热值低的燃料g2的情况下,喷嘴也不会堵塞,并且可以稳定地形成高速火焰。此外,使用本实施方式的燃烧器1a、1b和1c的操作方法优选将从燃料喷出口3喷出的燃料g2的流速设定为10m/s以上。通过将燃料g2的流速设定为10m/s以上,可以抑制飞散的熔融金属或炉渣侵入燃料喷出口3,因此可以防止熔融金属或炉渣引起的堵塞。此外,在使用本实施方式的燃烧器1a、1b和1c的操作方法中,当完全燃烧燃料g2所需的氧的比例(化学计量比)为1时,氧比优选为1~10。这里,氧比是由下式定义的值。氧比=(供给的助燃性气体g1中含有的氧量)/(完全燃烧燃料g2所需的氧量)此外,当助燃性气体g1是lng时,每1nm3的lng所需的氧量为2.3nm3,因此lng的流量可通过以下式求得。lng流量=[(供给的助燃性气体g1中含有的氧量)/2.3]/氧比由此,即使在使用低供应压力或热值低的燃料g2的情况下,喷嘴也不会堵塞,并且可以稳定地形成高速火焰。此外,在本实施方式的燃烧器1a、1b和1c中,将扩径喷嘴10的最大直径设为d3[m],将防护喷嘴6的前端的直径设为d4[m],将相对于供给的助燃性气体g1的流量以化学计量比(氧比=1)燃烧所需的燃料g2的流量设为qf[nm3/h]时,优选以燃料的流速v[nm/s]满足50≤v≤200的方式决定d3及d4。此外,如下式(1)所示,从防护喷嘴6的出口面积减去扩径喷嘴10的出口面积而得到面积a,将所述qf除以面积a而求出燃料的流速v[nm/s]。v=(qf/3600)/a…(1)a=π/4×(d42-d32)。通过将由上述式(1)求得的燃料的流速v设定为50~200nm/s,可以抑制熔融金属或炉渣等的侵入,并且可以稳定地形成高速火焰。如果流速v为50nm/s以上,则可以防止熔融金属或熔渣等的侵入。另一方面,当流速v为200nm/s以下时,则喷嘴内成为适合供应低供应压力燃料的压力,并且能够在流过中心的助燃性气体g1的射流的周围形成良好的火焰。(冷铁源的熔解和提纯方法)[第六实施方式]接下来,作为本发明的第六实施方式,对使用上述燃烧器1a、1b和1c的冷铁源的熔解和提纯方法进行说明。使用本实施方式的燃烧器1a、1b和1c的冷铁源的熔解和提纯方法的特征在于,包含:熔解冷铁源的熔解工序;和在将冷铁源进行熔解之后进行提纯的提纯工序,在熔解工序中,将氧比设为1~5,在提纯工序中,将氧比设为3~10,在熔解工序及提纯工序中,分别独立地设定燃料的流量。在上述氧比的条件下,当氧的流量为1000nm3/h时,氧比为1~5的情况下lng的流量设定为435nm3/h~87nm3/h。另一方面,当氧比为3~10时lng的流量设定为145nm3/h~43nm3/h。具体而言,由于以化学计量比(氧比=1)燃烧lng所需的氧量为每1nm3的lng需要2.3nm3,因此当氧流量为qo2、氧比为m时,lng流量qf由下式(2)得到。qf=(qo2/2.3)/m…(2)在熔解工序中,当lng的燃烧热用作热源时,假设该lng完全燃烧,氧比m被设定为1以上。当氧比m=1时,根据上式(2),lng流量qf设定为约435nm3/h。另一方面,当在熔解工序中用氧切割时,假设氧射流的势流核延伸至最大限度,将氧比m设定为5以下。当氧比为m=5时,根据上述(2),lng的流量qf设定为约87nm3/h。另一方面,在提纯工序中,当将本实施方式的燃烧器用作氧枪时,其用氧进行提纯,因此,假设减少燃料以使得氧没有被完全消耗,氧比m被设定为3以上。当氧比为m=3时,根据上述(2),lng的流量qf设定为约145nm3/h。另一方面,在提纯工序中,假设延伸氧射流的必要燃料的最低流量,将氧比m设定为10以下。当氧比为m=10时,根据上述(2),lng的流量qf设定为约43nm3/h。如上所述,在熔解工序和提纯工序中,为了区分燃烧器的功能,优选设置用于具有该功能的氧比,并且分别独立地设定燃料g2的流量。并且,求出将由上式(1)求出的流速v为50~200nm/s时的d4的最大条件和最小条件,并将其结果示于下述表1。[表1]d4的最大条件d4的最小条件qf[nm3/h]435435d3[mm]40.928.9v[nm/s]50200a[m2]0.0024170.000604d4[mm]68.940.1例如,当将助燃性气体的流量(纯氧气)设为1000,lng的流量qf设为435nm3/h(将氧比设为1进行计算),将助燃性气体的出口速度设为1.5马赫,d1、d2设为d1=20.2mm、d2=23.6mm而进行设计时,由1.5≤a1/a2≤3.0可得到d3=28.9mm~40.9mm。d4成为最大的条件为,在上述式(1)中v=50nm/s时,a=0.002417m2。因此,在上述式(1)中d3=40.9mm时,d4=68.9mm。另一方面,d4成为最小的条件为,在上述式(1)中v=200nm/s时,a=0.000604m2。因此,在上述式(1)中d3=28.9mm时,d4=40.1mm。因此,防护喷嘴6的前端的直径d4为40.1mm~68.9mm的范围。根据本实施方式,当使用燃烧器1a、1b和1c而在炉内熔解和提纯冷铁源时,可以提高其效率。另外,本发明不限于上述实施方式,在不脱离本发明的宗旨的范围内可以进行各种变更。具体地,燃烧器1a、1b和1c由第一喷嘴部件7和第二喷嘴部件8构成,但不限于这种结构,可以适当地进行改变。例如,关于上述第一喷嘴部件7,在拉瓦尔喷嘴9和扩径喷嘴10之间进行分割,从而分别由不同的喷嘴部件构成。[实施例]以下,通过实施例将本发明的效果更明确。另外,本发明不限于以下的实施例,在不改变其宗旨的范围内,可以适当地变更实施。(实施例1)在实施例1中,以下述表2中所示的条件制造上述图1所示的燃烧器1a,使用所得燃烧器来确认燃烧状态,并测量流过中心的助燃性气体的射流的流速。另外,在实施例1中,助燃性气体使用纯氧(浓度100%),燃料使用lng。另一方面,作为比较例1,以下述表2中所示的条件制造上述专利文献1所述的燃烧器,使用所得燃烧器来进行与实施例1中相同的测量。[表2]结果,在实施例1的燃烧器中,确认到从防护喷嘴6的前端以包围流过中心的助燃性气体射流的方式形成稳定的火焰。并且,对于实施例1和比较例1,测量各燃烧器的距离[m]与助燃性气体的流速[马赫数]之间的关系。其测量结果如图4所示。另外,在图4中,以实线表示实施例1的测量结果,以虚线表示比较例1的测量结果。如图4所示,可以看出,与比较例1的燃烧器相比,实施例1的燃烧器不易引起助燃性气体的流速衰减。(实施例2)在实施例2中,以下述表3中所示的条件制造上述图3所示的燃烧器1c,使用所得燃烧器来确认燃烧状态,并测量流过中心的助燃性气体射流的流速。另外,在实施例2中,助燃性气体使用纯氧,为了模拟热值低且可燃性差的燃料,燃料使用由氮气稀释lng而成的产物。[表3]其结果,在实施例2的燃烧器中,确认到如下情况:即使在使用热值低的燃料的情况下,也从防护喷嘴6的前端以包围流过中心的助燃性气体射流的方式形成稳定的火焰。而且,对于实施例2,测量各燃烧器的距离[m]与助燃性气体的流速[马赫数]之间的关系。将其测量结果示于图5中。而且,图5还一并示出实施例1的测量结果以供参考。另外,在图5中,以实线表示实施例2的测量结果,以单点划线表示实施例1的测量结果。如图5所示,可以看到,即使在使用可燃性差的燃料的情况下,实施例2的燃烧器也能获得与实施例1的燃烧器相同的结果,并且不会引起助燃性气体的流速衰减。(实施例3)在实施例3中,将实施例1和实施例2的燃烧器安装在电弧炉中,并确认到在实际机器操作中产生的熔融金属及炉渣导致的喷嘴的堵塞状态。其结果,确认到未发生喷嘴堵塞,能够进行稳定的操作。附图标记说明1a、1b、1c燃烧器1a前端面2助燃性气体喷出口3燃料喷出口4助燃性气体供给路5燃料供给路6防护喷嘴7第一喷嘴部件8第二喷嘴部件9拉瓦尔喷嘴10扩径喷嘴11同径喷嘴11a凹槽部20水冷套g1助燃性气体g2燃料h冷却水当前第1页12