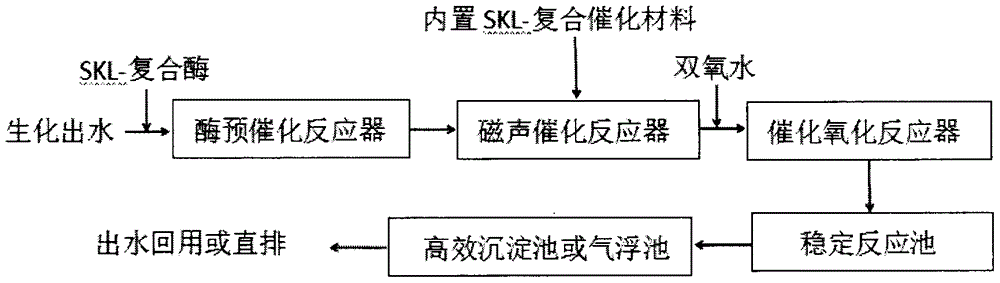
本发明涉及水污染防治研究领域,尤其涉及一种酶预催化-磁声催化氧化深度水处理方法。
背景技术:
:工业废水性质复杂、毒性大、盐份高、B/C低,经生化法(如A2/O)处理后出水中仍含有多环芳烃、卤代烃、杂环类、苯酚、酚的同系物以及萘、蒽、苯并芘等多环类化合物,这类污染物属于“三抗”,抗生化、抗光化、抗氧化的难降解性污染物。工业废水提标升级要求出水达到国家一级A标,从各工程建设运行后的情况调查来看,芬顿、臭氧、活性炭吸附、MBR等常规工艺,处理效果不理想,难以稳定达标且运行成本过高导致反复技改投资。催化氧化法是对化学氧化法的改进与强化,根据所采取的不同改进措施,发展出湿式催化氧化法、光催化氧化法、均相催化氧化法和多相催化氧化法。湿式催化氧化法是利用对系统加压加温,可利用已有的工业催化剂,使反应迅速完成。而其对设备与配套设施要求高,需要高温、高压;催化剂损耗很大,易发生中毒、致污等现象而失活。光催化氧化法是反应过程中辅以紫外光照,使氧化剂H2O2、O3吸收光能迅速分解形成·OH自由基,攻击水中有机物基团,使之分解。工艺需要紫外线发生装置,需拆换,反应选择性差,废水有机物的光解常受其他竞争反应的干扰,可能产生更毒的物质。均相催化氧化法是向反应体系中投加可溶性的酸、金属盐等物质,通过引发O3、H2O2的自由基型反应并不断再生而对水中有机物氧化反应起催化作用。但均相催化氧化法采用的催化剂无法回收,药剂费用偏高,处理过程中向水质带进其它杂质。多相催化氧化法是一种新型的深度处理技术,其主要向反应体系中装入固体催化剂,对有机物氧化分解的催化作用在催化剂表面进行,目前其存在着处理效率不稳定,催化剂与废水性质是否匹配对处理效率影响很大。因此,如何根据目前多相催化氧化法存在的问题进行改进,并寻求一种高效广谱的多相催化氧化技术成为难点。常规催化氧化工艺仅将废水中的部分污染物分解成为小分子有机物,而这些小分子有机物(醇、醛、羧酸等)难以完全分解,一些复杂有机物,如苯类、芳香烃类衍生物也很难降解。在本发明之前,针对这类“三抗”废水实施深度处理,仍然存在着两大主要问题,一是难以稳定达到日趋严格的排放标准;二是处理成本居高不下。技术实现要素:本发明的目的就在于解决上述缺陷,研制一种酶预催化-磁声催化氧化深度水处理方法。本发明技术方案是:一种酶预催化-磁声催化氧化深度水处理方法,其主要技术特征在于步骤如下:(1)将经物化+生化二级处理后的废水泵提升进入酶预催化反应器,在进酶预催化反应器之前的管道上添加SKL-复合酶,通过水力搅拌混合均匀后进入酶预催化反应器进行生物酶催化反应,SKL-复合酶添加量依据废水浓度变化;(2)酶预催化反应器出水自流进入磁声催化反应器,磁声催化反应器由磁化装置、超声装置和SKL-复合催化材料组成,SKL-复合催化材料装填密度5kg/m3,废水在磁声催化反应器中进行多电位差多金属化学催化反应,降低下一步催化氧化反应的处理负荷;(3)磁声催化反应器出水自流进入催化氧化反应器,在催化氧化反应器进水主管上添加双氧水,废水在催化氧化反应器中进行强氧化反应,催化双氧水产生的羟基自由基(·OH)与经过酶预催化和磁声催化处理后的有机污染物发生快速的链式反应,无选择性地把有害物质氧化成CO2、H2O或矿物盐;(4)催化氧化反应器出水自流进入稳定反应池,进一步调节水质水量,完善反应,将未进行完全的催化氧化反应继续,达到彻底降解污染物和充分使用药剂的目的;(5)稳定反应池出水自流进入固液分离系统,固液分离可使用高效沉淀池或气浮池等,达到去除SS,保证出水达标排放或回用的目的,投加PAM。所述步骤(1)中SKL-复合酶投加量为0.1-1mg/L。所述步骤(3)中双氧水浓度为27.5%,双氧水投加量100-300mg/L。所述步骤(4)中稳定反应池停留时间为0.5-2h。所述步骤(5)中投加PAM为1-3mg/L。本发明的优点和效果在于利用酶预催化,生物酶由漆酶、木聚糖酶、纤维素酶、半纤维素酶、果胶酶等复配而成,针对废水的预催化具有广谱性,且成本低;再利用磁化、超声联合催化的作用,超声波发生空化作用的因素除超声波强度、频率外,液体的表面张力也是关键因素,液体的表面张力越大,空化强度越高,越不易于产生空化作用,而废水先通过磁场后,使原来较大缔合水分子集团变成较小缔合水分子集团,水的表面张力变小,使水在超声波的作用下更易于发生空化作用,提高了超声波的催化速度。本发明的优点和效果还在于利用SKL-复合催化材料的多相金属作为反应活性中心,催化活性点多,催化活性高,氧化反应速率和氧化能力高;与双氧水异相催化反应后能够从反应体系中分离并重复利用,解决了传统均相Fenton反应过程中产生大量铁污泥的问题,减少二次污染的产生,还降低了处理的成本;实现在接近中性条件下催化降解污染物。本发明的优点和效果还在于联合生物酶催化-多相金属化学催化-羟基自由基氧化的机理于一组反应器中,针对经二级生化处理后仍含有多环芳烃、卤代烃、杂环类、苯酚、酚的同系物以及萘、蒽、苯并芘等多环类化合物的废水具有高效的降解效率,对COD、色度去除率高并且出水稳定,达到要求的排放标准或回用水水质。处理后的废水可以循环使用,节约了工业用水。本发明已具备设备成套化和工程规模化应用。本发明主要针对“三抗”废水实施深度处理,解决其常规工艺存在处理效果较差、费用较高、工艺条件要求较高等问题,能够将工业废水出水稳定达到国家一级A标,并具有经济性、高效广谱性。附图说明图1——本发明的流程示意图。具体实施方式本发明的技术思路是:提供一种酶预催化-磁声催化氧化深度水处理方法。主要适用于不同类型不同浓度废水的三级深度处理,处理后出水达到国家一级A标或超低污染物排放标准,可直排或直接回用。本发明提供的一种酶预催化-磁声催化氧化深度水处理方法的特征,首先利用高效生物酶进行预催化,SKL-生物酶由漆酶、木聚糖酶等多种酶及介体复配而成,属生物催化体系,将生物酶催化技术应用于污染物的去除,是采用不同于普通微生物菌的系列生物酶、菌结合技术,通过酶打开污染物质中更复杂的化学链,降低后续化学催化氧化处理负荷,吨水处理成本低(0.01-0.02元/吨水),大大降低污水处理费用。再利用SKL-复合催化材料辅以磁化、超声进一步催化反应,与现有催化剂相比,比表面积大,SKL-复合催化材料以Fe、Cu、Mn、Co、Ni多相金属作为反应活性中心,催化活性点增多,催化活性提高,氧化反应速率和氧化能力提高。通过磁化、超声波共同催化作用:一是使水分子与有机污染物分子重新排列,减少了有机污染物分子与药剂分子的反应屏障,提高了反应效率;二是使废水中微粒子极性增强,凝聚力减弱,形成分散稳定小晶体,防止大晶体结晶,可有效防止系统结垢;三是使得高分子分解、化学键断裂和产生自由基等。本发明提供的一种酶预催化-磁声催化氧化深度水处理方法技术原理分析:前端经生化二级处理后的废水利用SKL-生物酶的催化降解功能,促使废水中酚、萘、吡啶、喹啉、蒽、苯胺、苯并芘等杂环芳香物的降解,再经超声/磁化/复合催化材料的联合催化作用,促使废水中多键、高碳架、硝基、偶氮类等污染物进行开环断链,水分子按照磁力线的方向重新排列,降低有机物活性点与药剂分子的反应屏障,提高后续催化氧化的反应速度和降解效率,难降解有机污染物经过酶、超声、磁化和金属催化后,转化为羧酸、醇、酯类易氧化的有机物,再通过双氧水在催化作用下产生的羟基自由基将这些有机物氧化为无机态,最终达到彻底降解污染物的目的。下面具体说明本发明。本发明提供一种酶预催化-磁声催化氧化深度水处理方法的步骤并结合图1说明如下:1、将经物化+生化二级处理后的废水泵提升进入酶预催化反应器,在进酶预催化反应器之前的管道上添加SKL-复合酶,通过水力搅拌混合均匀后进入酶预催化反应器进行生物酶催化反应;2、酶预催化反应器出水自流进入磁声催化反应器,磁声催化反应器由磁化装置、超声装置和SKL-复合催化材料组成,废水在磁声催化反应器中进行多电位差多金属化学催化反应,降低下一步催化氧化反应的处理负荷;3、磁声催化反应器出水自流进入催化氧化反应器,在催化氧化反应器进水主管上添加双氧水,废水在催化氧化反应器中进行强氧化反应,催化双氧水产生的羟基自由基(·OH)与经过酶预催化和磁声催化处理后的有机污染物发生快速的链式反应,无选择性地把有害物质氧化成CO2、H2O或矿物盐;4、催化氧化反应器出水自流进入稳定反应池,进一步调节水质水量,完善反应,将未进行完全的催化氧化反应继续,达到彻底降解污染物和充分使用药剂的目的;5、稳定反应池出水自流进入固液分离系统,固液分离可使用高效沉淀池或气浮池等,达到去除SS,保证出水达标排放或回用的目的。上述步骤1中的SKL-复合酶添加量依据废水浓度变化,SKL-复合酶投加量0.1-1mg/L。上述步骤2中的SKL-复合催化材料为由Fe、Cu掺杂Mn、Co、Ni取代缺位多金属氧酸盐PW11后负载在修饰后的载体APS-SiO2上,制得的一种复合催化材料,复合催化材料的装填密度为5kg/m3。上述步骤2中的磁化采用内置永磁材料的方式,永磁材料选用稀土永磁材料钕铁硼Nd2Fe14B,其剩磁为1.12-1.37T,矫顽力836-915kA/m,最大磁能积239-358kJ/m3,工作温度≤80℃。上述步骤2中的超声采用内置超声波换能器,超声波发生器外置的方式,超声波发生器发出的频率f为35-50kHz。上述步骤3中的双氧水投加浓度为27.5%,投加量依据废水浓度变化,双氧水投加量100-300mg/L。上述步骤4中的稳定反应池停留时间为0.5-2h,选用曝气搅拌,稳定池底部安装穿孔曝气管,风机选用罗茨风机。上述步骤5中的固液分离投加助凝剂PAM1-3mg/L。实施例1:印染废水浙江某综合污水处理厂,其中印染废水占比75%,化工废水占比15%,生活废水占比10%,日处理水量32万吨。生化后二沉池出水COD130~160mg/L,色度较重,电导率大于4000us/cm,生化后二沉池出水通过GC-MS检出:多为分子结构复杂、分子量大的有机物,相对含量超过1%较大分子量的有机污染物有14种,合计占88.83%,苯胺类有机污染物含量为34.79%等。本发明人对该废水实施了酶预催化-磁声催化氧化深度水处理方法的中试,取得了良好的处理效果,COD、TOC、色度、苯胺类等指标降解效果明显,出水水质指标满足提标升级要求的《城镇污水处理厂污染物排放标准》GB18918-2002一级A标,由此该厂实施了本
发明内容的工程规模化应用。技术参数:每天深度水处理规模32万吨。酶预催化时间8min,酶预催化反应器容积115m3;磁声催化时间8min,磁声催化反应器容积115m3,所选永磁材料为钕铁硼Nd2Fe14B(NNF45),磁性能为剩磁为1.37T,矫顽力876kA/m,最大磁能积358kJ/m3,工作温度≤80℃,超声波发生器频率为38kHz,复合催化材料装填密度5kg/m3;催化氧化反应器氧化时间7min,氧化反应器容积100m3。药剂投加:依据设计水质要求,进水COD<160mg/L,出水COD<45mg/L,SKL-复合酶投加量为0.6mg/L,氧化剂H2O2(浓度27.5%)投加量为250mg/L,助凝剂PAM投加量2mg/L。配套3套加药装置。土建工程:依据设计反应时间,建造稳定反应池单个容积12500m3,2座;高效沉淀池单个容积2000m3,14座。配套罗茨风机、配套泵管等辅助设施并进行安装。具体实施情况如下:1、将经物化+生化二级处理后的废水泵提升进入酶预催化反应器,在进酶预催化反应器之前的管道上添加SKL-复合酶,SKL-复合酶投加量为0.6mg/L,通过水力搅拌混合均匀后进入酶预催化反应器进行生物酶催化反应,反应时间为8min;2、酶预催化反应器出水自流进入磁声催化反应器,磁声催化反应器由磁化装置、超声装置和SKL-复合催化材料组成,废水在磁声催化反应器中进行多电位差多金属化学催化反应,反应时间8min,降低下一步催化氧化反应的处理负荷;3、磁声催化反应器出水自流进入催化氧化反应器,在催化氧化反应器进水主管上添加双氧水,氧化剂H2O2(浓度27.5%)投加量为250mg/L,废水在催化氧化反应器中进行强氧化反应,催化双氧水产生的羟基自由基(·OH)与经过酶预催化和磁声催化处理后的有机污染物发生快速的链式反应,无选择性地把有害物质氧化成CO2、H2O或矿物盐;4、催化氧化反应器出水自流进入稳定反应池,进一步调节水质水量,完善反应,稳定反应池反应时间2h,将未进行完全的催化氧化反应继续,达到彻底降解污染物和充分使用药剂的目的;5、稳定反应池出水自流进入固液分离系统,固液分离使用高效沉淀池,助凝剂PAM投加量为2mg/L,高效沉淀池沉降时间2h,达到去除SS,保证出水达到国家一级A标。(1)表2-1所示为酶预催化+磁声催化氧化反应器出水以及总出水的COD、色度、SS和pH水质指标处理前后的变化情况,酶预催化+磁声催化氧化反应器出水COD去除率达到51.6%,通过稳定反应池进一步完善反应后总出水COD去除率达到73.5%,总出水COD<50mg/L,色度10倍,SS<10mg/L,pH7.6,优于《城镇污水处理厂污染物排放标准》GB18918-2002一级A标准。表2-1(2)表2-2所示为对同一种水质实施芬顿流化床催化氧化工艺与酶预催化+磁声催化氧化工艺(对照组)后水质指标COD、色度、苯胺类和TOC的去除效果。表2-2为了验证酶预催化-磁声催化氧化深度水处理方法的高效性,对同一水质分别实施酶预催化-磁声催化氧化深度处理和芬顿流化床催化氧化深度处理的中试对比,中试装置分别为自主研发的酶预催化-磁声催化氧化中型试验装置和购买的芬顿流化床中型试验装置,中试采用该污水处理厂生化后二沉池出水作为两对照组的中试装置的进水,中试周期为1个月。由此可以看出,传统催化氧化工艺改进后的芬顿流化床深度水处理方法对COD的去除率在48%-53%,对色度去除率在53%,对印染废水中苯胺类去除率在70%,对TOC的去除率在65.5%;而酶预催化-磁声催化氧化深度水处理方法对COD的去除率在70%-80%,对色度去除率在90%,对印染废水中苯胺类去除率在93.2%,对TOC的去除率在83.4%,大大提高了废水中污染指标的去除效率,达到了彻底降解污染物的目的。从经济指标出发,本次中试酶预催化-磁声催化氧化运行成本在1.35元/吨水(含药剂费、电费、污泥费),芬顿流化床运行成本在2.8元/吨水(含药剂费、电费、污泥费),由此,本发明酶预催化-磁声催化氧化深度水处理方法运行成本较芬顿流化床催化氧化深度水处理方法节约50%,大大减少了药剂投加量和污泥产生量,节约了运行成本。实施例2:制药废水石家庄某污水处理厂,日处理水量10万吨,实施深度处理废水来源为改污水处理厂上游制药企业废水与城镇生活污水,经生化(水解、好氧)处理后的二沉池出水,深度处理后要求出水达到:城镇污水处理厂污染物排放标准(GB18918-2002)一级A标准。该厂原深度处理采用臭氧/活性炭滤池工艺,运行一段时间后未能稳定达标,且随着活性炭的吸附饱和,出水效果变差。该厂进水水质复杂且波动大,惰性COD增加,可生化性、可氧化性等大大降低,生化后二沉池出水的COD基本在80~120mg/L之间波动,且色度偏重,偶尔COD上升到150mg/L。氨氮在5.8~7.4mg/L之间,总磷在0.93~1.73mg/L之间。针对国家一级A级标,本次技改深度水处理重点处理COD、色度、总磷等。技改通过多项技术的比选,最终实施本发明的酶催化-磁声催化氧化深度水处理工艺。技术参数:每天深度水处理规模10万吨。酶预催化时间8min,酶预催化反应器容积115m3;磁声催化时间8min,磁声催化反应器容积115m3,所选永磁材料为钕铁硼Nd2Fe14B(NNF45),磁性能为剩磁为1.21T,矫顽力915kA/m,最大磁能积358kJ/m3,工作温度≤80℃,超声波发生器频率为45kHz,复合催化材料装填密度5kg/m3;催化氧化反应器氧化时间7min,氧化反应器容积100m3。药剂投加:依据设计水质要求,进水COD<120mg/L,出水COD<45mg/L,SKL-复合酶投加量为0.4mg/L,氧化剂H2O2(浓度27.5%)投加量为150mg/L,助凝剂PAM投加量1.5mg/L。配套3套加药装置。土建工程:依据设计反应时间,建造稳定反应池单个容积3125m3,2座;高效沉淀池单个容积1500m3,5座。配套罗茨风机、配套泵管等辅助设施并进行安装。具体实施情况如下:1、将该厂生化后二沉池出水经泵提升进入酶预催化反应器,在进酶预催化反应器之前的管道上添加SKL-复合酶,SKL-复合酶投加量为0.4mg/L,通过水力搅拌混合均匀后进入酶预催化反应器进行生物酶催化反应,反应时间为8min;2、酶预催化反应器出水自流进入磁声催化反应器,磁声催化反应器由磁化装置、超声装置和SKL-复合催化材料组成,废水在磁声催化反应器中进行多电位差多金属化学催化反应,反应时间8min,降低下一步催化氧化反应的处理负荷;3、磁声催化反应器出水自流进入催化氧化反应器,在催化氧化反应器进水主管上添加双氧水,氧化剂H2O2(浓度27.5%)投加量为150mg/L,废水在催化氧化反应器中进行强氧化反应,催化双氧水产生的羟基自由基(·OH)与经过酶预催化和磁声催化处理后的有机污染物发生快速的链式反应,无选择性地把有害物质氧化成CO2、H2O或矿物盐;4、催化氧化反应器出水自流进入稳定反应池,进一步调节水质水量,完善反应,稳定反应池反应时间1.5h,将未进行完全的催化氧化反应继续,达到彻底降解污染物和充分使用药剂的目的;5、稳定反应池出水自流进入固液分离系统,固液分离使用高效沉淀池,助凝剂PAM投加量为1.5mg/L,高效沉淀池沉降时间2h,达到去除SS,保证出水达到国家一级A标。表3从表3可以看出,本发明将进水COD80-150mg/L处理到出水25-50mg/L,去除率达到68.8%-80%,色度降至10倍以下,去除率达到90%,总磷降至0.1mg/L以下,SS降至10mg/L以下,各项指标均达到一级A标排放要求。充分体现了本发明抗负荷冲击能力强,用于深度处理可确保出水水质达标,这也是本发明的优势之一。从经济指标出发,该污水处理厂实施本发明的酶催化-磁声催化氧化深度水处理工艺后,深度处理段的综合运行成本在1.0-1.2元/吨水,出水稳定达到一级A标排放要求,较技改之前臭氧/活性炭滤池深度水处理工艺,深度处理段综合运行成本降低50%,且抗负荷冲击能力强,已稳定达标运行一年多。实施例3:化纤废水新疆某污水处理站,主要处理来自新疆某纤维有限公司的纤维废水及浆粕废水,日处理8万吨。实施深度水处理水量为4万吨/日,目标COD≤30mg/L进中水回用系统处理后回用于生产,达到新疆自治区环保部门中水回用要求。经物化+生化(曝气活性污泥法)处理后,现生化出水COD在70-120mg/L。深度处理实施本发明的酶催化-磁声催化氧化深度水处理工艺。技术参数:每天深度水处理规模4万吨。酶预催化时间8min,酶预催化反应器容积115m3;磁声催化时间8min,磁声催化反应器容积115m3,所选永磁材料为钕铁硼Nd2Fe14B(NNF45),磁性能为剩磁为1.13T,矫顽力836kA/m,最大磁能积238kJ/m3,工作温度≤80℃,超声波发生器频率为50kHz,复合催化材料装填密度5kg/m3;催化氧化反应器氧化时间7min,氧化反应器容积100m3。药剂投加:依据设计水质要求,进水COD70-120mg/L,出水COD<30mg/L,SKL-复合酶投加量为0.8mg/L,氧化剂H2O2(浓度27.5%)投加量为150mg/L,助凝剂PAM投加量2mg/L。配套3套加药装置。土建工程:依据设计反应时间,建造稳定反应池单个容积1500m3,1座;高效沉淀池单个容积1500m3,2座。配套罗茨风机、配套泵管等辅助设施并进行安装。具体实施情况如下:1、将该厂生化后二沉池出水经泵提升进入酶预催化反应器,在进酶预催化反应器之前的管道上添加SKL-复合酶,SKL-复合酶投加量为0.8mg/L,通过水力搅拌混合均匀后进入酶预催化反应器进行生物酶催化反应,反应时间为8min;2、酶预催化反应器出水自流进入磁声催化反应器,磁声催化反应器由磁化装置、超声装置和SKL-复合催化材料组成,废水在磁声催化反应器中进行多电位差多金属化学催化反应,反应时间8min,降低下一步催化氧化反应的处理负荷;3、磁声催化反应器出水自流进入催化氧化反应器,在催化氧化反应器进水主管上添加双氧水,氧化剂H2O2(浓度27.5%)投加量为150mg/L,废水在催化氧化反应器中进行强氧化反应,催化双氧水产生的羟基自由基(·OH)与经过酶预催化和磁声催化处理后的有机污染物发生快速的链式反应,无选择性地把有害物质氧化成CO2、H2O或矿物盐;4、催化氧化反应器出水自流进入稳定反应池,进一步调节水质水量,完善反应,稳定反应池反应时间50min,将未进行完全的催化氧化反应继续,达到彻底降解污染物和充分使用药剂的目的;5、稳定反应池出水自流进入固液分离系统,固液分离使用高效沉淀池,助凝剂PAM投加量为2mg/L,高效沉淀池沉降时间2h,达到去除SS,保证出水COD<30mg/L,满足中水回用要求。表4-1所示为实施本发明工艺的设计进水指标和设计出水指标,设计进水pH6-9,出水pH6-9;进水COD70-120mg/L处理到出水COD≤30mg/L;设计进水SS≤50mg/L处理到出水SS≤15mg/L,设计进水色度≤50倍处理到出水色度≤30倍。表4-1指标pHCOD(mg/L)SS(mg/L)色度(倍)进水6~970~120≤50≤50出水6~9≤30≤15≤30原设计实施本发明后将现有生化出水COD70-120mg/L处理到出水COD<30mg/L,达到中水回用要求。实施本发明后,由于企业增产导致约2万吨/日浆粕废水直接排放至现有生化系统,导致生化后出水COD上升至200mg/L以上,甚至高达300mg/L。通过调整工艺参数和提高药剂投加量,实施本发明深度水处理工艺仍然能满足出水COD<30mg/L的回用水标准。实际药剂投加:SKL-复合酶投加量为1mg/L,氧化剂H2O2(浓度27.5%)投加量为300mg/L,助凝剂PAM投加量3mg/L。表4-2所示为实施本发明后实际运行情况下的处理前后进出水的COD变化,从7月份到10月份,近4个月运行的COD均值看,实际进水COD232.6-285.3mg/L,实施本发明深度水处理工艺后出水COD23.2-30.7mg/L,COD去除率高达90%,充分验证了本发明酶催化-磁声催化氧化深度水处理工艺的高效性。表4-2当前第1页1 2 3