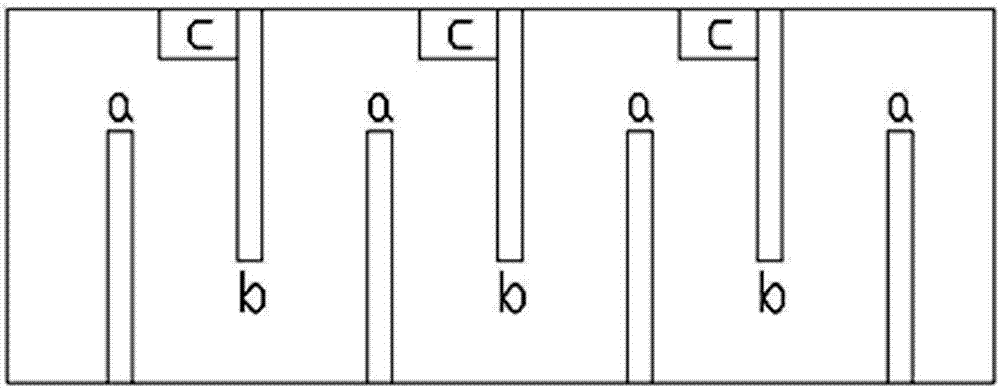
本发明属于工业废水处理
技术领域:
,具体涉及一种处理肉类加工废水的模块化集成工艺系统及方法,该系统及方法针对肉类加工企业在生产过程中产生的高浓度废水处理的问题,进行工艺集成与参数化设计,实现工艺模块化、智能化、集成化。
背景技术:
:近年来随着人民生活水平的提高,肉制品需求不断增加,肉类加工工业发展迅猛。我国肉类年总产量从改革开放时的1790万吨增长到2010年的7925万吨。自1990年以来,我国肉类总产量一直居世界首位。到2008年全国国有及规模以上肉类屠宰及肉类加工企业资产总额达到1813.7亿元,销售总收入达到4242.3亿元。目前,全国已有肉类加工企业3700余家,从业人员50万以上。肉类加工工业是食品工业中主要排污大户,废水排放量较大,其水质又具有一定的特性,我国对于肉类加工工业废水的排放单独制定了国家排放标准:《肉类加工工业水污染物排放标准》(gb13457-92),即肉类加工工业废水的排放,必须符合gb13457-92的规定。肉类加工工业废水主要来自:宰前饲养场排放的畜粪冲洗水;屠宰车间排放的含血污和畜粪的地面冲洗水;烫毛时排放的含大量猪毛的高温水;剖解车间排放的含肠胃内容物的废水;炼油车间排放的油脂废水等。此外,还有来自冷冻机房的冷却水和来自车间卫生设备、锅炉、办公楼等排放的生活污水。肉类加工废水含有大量的血污、毛皮、碎肉、内脏杂物、未消化的食物以及粪便等污染物,悬浮物浓度很高,水呈红褐色并有明显的腥臭味,是一种典型的有机废水。该废水包含下列5种污染物:①半漂浮在废水中的固体物质,如血块碎肉、大小肠的片段、猪毛、皮屑、胃内容物和粪便等;②悬浮在废水中的油脂、蛋白质、胶体物质等;③溶解于废水中的尿液、消化液等;④冲洗猪身体表时夹带的灰尘和泥土;可能存在的致病菌以及大肠菌群和杂菌等。此废水一般不含重金属及有毒化学物质。肉类加工废水的污染负荷一般随加工深度的增加而增加,同时,与其它工业污染相似,一般小厂比大厂的污染负荷要高。不同的肉类加工联合企业,由于生产和加工工艺的不同,废水水质不尽相同,即使是同一企业,不同加工阶段的废水水质也有很大差异。肉类加工废水的最大特点是废水排放量变化较大,其主要体现在以下几方面:①肉类加工一般具有明显的季节性,即有所谓淡、旺季,有些厂在淡季时甚至停产,所以肉类加工废水的排放量在一年之中变化是很大的;②肉类加工生产一般时非连续性的,每日只有一班或两班生产,所以废水量在一日之中变化也较大,在时变化系数上,一般可达2.0;③由于生产工艺、加工对象、生产管理水平等的差异,也造成其废水量差异较大。肉类加工废水属于易生物降解的高悬浮物有机废水,废水水质、水量变化范围较大。目前对该类废水的治理,均采用以生物法为主的处理工艺,包括好氧、厌氧、兼氧等处理系统。但无论采用什么生物处理工艺,都必须充分重视预处理工艺,应设置捞毛机、格栅、隔油池、调节池或沉淀池等,以尽量降低进入生物处理构筑物的悬浮物和油脂含量,确保处理设施的正常运行。目前国内对肉类加工废水的处理,主要采用厌氧-好氧或好氧处理工艺,例如uasb、abr、sbr、氧化沟、接触氧化等工艺,生化工艺前设置去除悬浮物的预处理工艺,后设置去除微生物的沉淀工艺。虽然上述工艺在肉类加工废水处理中已经广泛采用并取得一定的效果,但还是存在以下缺点。(1)肉类废水的最大特点就是废水中含有大量的固体废物和悬浮物,预处理工艺通常采用捞毛机和格栅,在处理过程中会产生大量的固体废物,对这部分固体废物的处理费时费力,极大地增加企业的人力物力负担和经济负担。(2)肉类加工废水具有明显的季节性特点,即在旺季时,水量大,水质差,而在淡季时,水量小甚至无水,水量和水质的明显变化会对污水处理系统产生冲击负荷,导致系统变得不稳定,出水指标也会变差。(3)肉类加工废水是典型的有机废水,一般生化阶段采用厌氧和好氧联合处理系统,但肉类加工废水具有季节性特点,冬季无水的情况下,厌氧系统会受到极大影响,可能会导致厌氧细菌全部死亡,第二年要面对厌氧系统的重新启动,增大企业的治理负担。技术实现要素:针对现有技术存在的问题,本发明提供一种处理肉类加工废水的模块化集成工艺系统及方法。本发明的技术方案为:一种处理肉类加工废水的模块化集成工艺系统,包括在线监测分析系统、plc可编程逻辑控制器和废水处理系统,所述在线监测分析系统用于对肉类加工废水的水质成分进行监测分析,并将监测分析数据传送至所述plc可编程逻辑控制器;所述plc可编程逻辑控制器对所述监测分析数据处理后输出控制信号至所述废水处理系统;所述废水处理系统包括依次连接的一级预处理模块、二级生化处理模块和三级深度处理模块;所述二级生化处理模块和所述三级深度处理模块根据所述plc可编程逻辑控制器输出的控制信号指令对肉类加工废水进行处理;所述一级预处理模块包括依次连接的粗格珊、高速破碎机和隔油调节水池,所述粗格珊进口连接肉类加工废水出口;所述二级生化处理模块包括依次连接的多模式生物脱氮反应器和生物流化床反应器;所述多模式生物脱氮反应器由多个反应区组成,每个反应区底部都设置有曝气系统,最后一个反应区出口连接所述生物流化床反应器进口;所述多模式生物脱氮反应器进口连接所述隔油调节水池出口;所述三级深度处理模块包括依次连接的高密度沉淀池、活性砂滤池和臭氧消毒反应器。进一步地,所述隔油调节水池内设有间隔设置的多级隔油下挡板和多级隔油上挡板,并且在每级隔油上挡板前设置有浮子撇油器。进一步地,所述多模式生物脱氮反应器的反应区优选设置为12个,相应地所述多模式生物脱氮反应器的出口处还设置有4台并列连接的硝化液回流泵,每台硝化液回流泵的回流量均为设计水量的100%,并且第1、2、4、5、6、7、8、9个反应区与所述4台硝化液回流泵之间通过回流管道连接,所述回流管道上设置电动阀门一;所述第1、2、3、4、5、6、7、8、9个反应区的曝气系统设有电动阀门二,通过控制所述电动阀门一和所述电动阀门二的启闭,从而控制所述多模式生物脱氮反应器的反应模式。进一步地,所述生物流化床反应器进口处设置有电动阀门三,所述电动阀门三用于根据工艺要求决定是否启用所述生物流化床反应器。进一步地,所述活性砂滤池进口处设置有电动阀门四,所述电动阀门四用于根据工艺要求决定是否启用所述活性砂滤池。一种处理肉类加工废水的模块化集成工艺方法,是采用上述系统,包括以下步骤:步骤一,将肉类加工废水引入粗格珊先除去废水中较大物质;步骤二,启动高速破碎机对步骤一出来的废水进行高速破碎处理,将废水中的固体物质破碎至5mm以下的悬浮物;步骤三,启动隔油调节水池,对步骤二出来的废水水量水质进行调节,并去除废水中的浮油;步骤四,在线监测分析隔油调节水池中废水的cod和氨氮值,计算c/n比,根据水质数据选择多模式生物脱氮反应器的反应模式;步骤五,启动多模式生物脱氮反应器,根据所选定的反应模式去除步骤四出来的废水中污染物;步骤六,在线监测分析多模式生物脱氮反应器出水的废水cod和氨氮值,当cod>80mg/l,或者bod>30mg/l,或者氨氮>15mg/l时,进入步骤七,否则进入步骤八;步骤七,启动运行生物流化床反应器,进一步去除水中的cod、bod、氨氮;步骤八,启动高密度沉淀池,对废水进行沉淀排泥;步骤九,在线监测出水水质要求,并根据出水水质要求,当出水水质要求ss<60mg/l,进入步骤十,否则进入步骤十一;步骤十,启动活性砂滤池,对废水进行过滤处理;步骤十一,启动臭氧消毒反应器,对废水进行消毒处理。进一步地,所述步骤二中高速破碎机采用六叶大直径刀片,工作转速为40000rpm。进一步地,所述步骤三中隔油调节水池对废水水量水质进行调节的具体控制参数为:当设计水量<100t/d时,水力停留时间为24.0~48.0h;当100t/d<设计水量<1000t/d时,水力停留时间为18.0~24.0h;当设计水量>1000t/d时,水力停留时间为12.0~18.0h。进一步地,所述步骤四中多模式生物脱氮反应器的具体结构设置为:所述多模式生物脱氮反应器的反应区设置为12个,所述多模式生物脱氮反应器的出口处设置4台并列连接的硝化液回流泵,并且第1、2、4、5、6、7、8、9个反应区与所述4台硝化液回流泵之间通过回流管道连接,所述回流管道上设置电动阀门一;所述第1、2、3、4、5、6、7、8、9个反应区的曝气系统设有电动阀门二,通过控制所述电动阀门一和所述电动阀门二的启闭,所述多模式生物脱氮反应器具有以下九种反应模式:反应模式一:当cod<500mg/l,氨氮<50mg/l,c/n≥10时,硝化液回流比为100%,即启动1台消化液回流泵,只开启第1反应区回流管道上的电动阀门一,使废水全部回流至第1反应区,同时关闭第1、2、3反应区曝气系统的电动阀门二,多模式生物脱氮反应器为ao工艺,缺氧段水力停留时间为9h,好氧段水力停留时间为27h;反应模式二:当cod<500mg/l,氨氮<50mg/l,5≤c/n<10时,硝化液回流比为200%,即启动2台消化液回流泵,开启第1、6反应区回流管道上的电动阀门一,使废水平均回流至第1、6反应区,同时关闭第1、6、7反应区曝气系统的电动阀门二,多模式生物脱氮反应器为aoao工艺,第一缺氧段水力停留时间为3h,第一好氧段水力停留时间为12h,第二缺氧段水力停留时间为6h,第二好氧段水力停留时间为15h;反应模式三:当cod<500mg/l,氨氮<50mg/l,c/n<5时,硝化液回流比为300%,即启动3台消化液回流泵,开启第1、5、9反应区回流管道上的电动阀门一,使废水平均回流至第1、5、9反应区,同时关闭第1、5、9反应区曝气系统的电动阀门二,多模式生物脱氮反应器为aoaoao工艺,第一缺氧段水力停留时间为3h,第一好氧段水力停留时间为9h,第二缺氧段水力停留时间为3h,第二好氧段水力停留时间为9h,第三缺氧段水力停留时间为3h,第三好氧段水力停留时间为9h;反应模式四:当500≤cod<1000mg/l,50≤氨氮<100mg/l,c/n≥10时,硝化液回流比为200%,即启动2台消化液回流泵,开启第1、7反应区回流管道上的电动阀门一,使废水平均回流至第1、7反应区,同时关闭第1、2、7反应区曝气系统的电动阀门二,多模式生物脱氮反应器为aoao工艺,第一缺氧段水力停留时间为6h,第一好氧段水力停留时间为12h,第二缺氧段水力停留时间为3h,第一好氧段水力停留时间为15h;反应模式五:当500≤cod<1000mg/l,50≤氨氮<100mg/l,5≤c/n<10时,硝化液回流比为300%,即启动3台消化液回流泵,开启第1、2、6反应区回流管道上的电动阀门一,使废水平均回流至第1、2、6反应区,同时关闭第1、2、6、7反应区曝气系统的电动阀门二,多模式生物脱氮反应器为aoao工艺,第一缺氧段水力停留时间为6h,第一好氧段水力停留时间为12h,第二缺氧段水力停留时间为6h,第一好氧段水力停留时间为12h;反应模式六:当500≤cod<1000mg/l,50≤氨氮<100mg/l,c/n<5时,硝化液回流比为300%,即启动3台消化液回流泵,开启第1、5、9反应区回流管道上的电动阀门一,使废水平均回流至第1、5、9反应区,同时关闭第1、2、5、9反应区曝气系统的电动阀门二,多模式生物脱氮反应器为aoaoao工艺,第一缺氧段水力停留时间为6h,第一好氧段水力停留时间为6h,第二缺氧段水力停留时间为3h,第三好氧段水力停留时间为9h,第三缺氧段水力停留时间为3h,第三好氧段水力停留时间为9h;反应模式七:当cod≥1000mg/l,氨氮≥100mg/l,c/n≥10时,硝化液回流比为300%,即启动3台消化液回流泵,开启第1、2、7反应区回流管道上的电动阀门一,使废水平均回流至第1、2、7反应区,同时关闭第1、2、7、8反应区曝气系统的电动阀门二,多模式生物脱氮反应器为aoao工艺,第一缺氧段水力停留时间为6h,第一好氧段水力停留时间为12h,第二缺氧段水力停留时间为6h,第一好氧段水力停留时间为12h;反应模式八:当cod≥1000mg/l,氨氮≥100mg/l,5≤c/n<10时,硝化液回流比为400%,即启动4台消化液回流泵,开启第1、2、6、9反应区回流管道上的电动阀门一,使废水平均回流至第1、2、6、9反应区,同时关闭第1、2、6、9反应区曝气系统的电动阀门二,多模式生物脱氮反应器为aoaoao工艺,第一缺氧段水力停留时间为6h,第一好氧段水力停留时间为9h,第二缺氧段水力停留时间为3h,第二好氧段水力停留时间为6h,第三缺氧段水力停留时间为3h,第三好氧段水力停留时间为9h;反应模式九:当cod≥1000mg/l,氨氮≥100mg/l,c/n<5时,硝化液回流比为400%,即启动4台消化液回流泵,开启第1、4、7、10反应区回流管道上的电动阀门一,使废水平均回流至第1、4、7、10反应区,同时关闭第1、4、7、10反应区曝气系统的电动阀门二,多模式生物脱氮反应器为aoaoaoao工艺,第一缺氧段水力停留时间为3h,第一好氧段水力停留时间为6h,第二缺氧段水力停留时间为3h,第二好氧段水力停留时间为6h,第三缺氧段水力停留时间为3h,第三好氧段水力停留时间为6h,第四缺氧段水力停留时间为3h,第四好氧段水力停留时间为6h。进一步地,所述步骤七中生物流化床反应器的具体控制参数为:空床停留时间为2.5h,填料采用改性聚乙烯悬浮填料,填料粒径为12±2mm,最大膨胀率为150%,bod负荷为10~12kgbod5/m3·d。本发明的有益效果在于:1、本发明适用于悬浮物多、水质水量变化较大的小型、零散肉类加工场高浓度废水处理;本发明工艺过程采用多个单元串联形式,通过改变设备运行参数自动控制转换工艺,节省占地面积的同时节省造价;2、本发明未采用厌氧系统,冬季无水时可以停运,不存在次年启动时,厌氧系统启动困难,耗费人力物力的问题;3、本发明的一级预处理模块采用高速破碎器,将半漂浮在废水中的固体物质完全打散,使其能够在后续生化模块能被微生物利用除去,并且极大地减少了固体废弃物的产量,极大地降低了这部分的处理成本;并且预处理模块采用的隔油调节池,同时具有隔油和调节水质水量的功能;4、本发明的二级生化处理模块采用多模式生物脱氮反应器,可根据不同的cod、氨氮值自动选择反应模式,合理分配缺氧和好氧区域,同时具有十分优良的cod和氨氮处理效果,无需外加碳源,最大限度地节省能耗,降低处理费用;5、本发明的三级深度处理模块采用臭氧消毒处理器,能够有效去除肉类加工中的臭味、血色和细菌,并且强化水的澄清、沉淀和过滤效果,提高出水水质,节省消毒剂用量;6、本发明的系统及方法模块化程度高,有利于将技术转化为集成设备,节省空间的同时保证工艺组合技术的先进性,使肉类加工废水稳定达标。综上,本发明针对肉类加工废水的特点和目前处理系统存在的各种问题,提出一种筛选效果优良、节能降耗的先进处理系统及方法,该系统及方法进行工艺耦合集成与参数化设计,有效提高了肉类加工废水处理的模块化、智能化、集成化程度,具有较高的工业价值。附图说明图1为本发明具体实施例的处理肉类加工废水的模块化集成工艺系统的一种结构示意图,其中1-在线监测分析系统,2-plc可编程逻辑控制器,3-粗格栅,4-高速破碎机,5-隔油调节水池,6-多模式生物反应器,7-生物流化床反应器,8-高密度沉淀池,9-活性砂滤池,10-臭氧消毒反应器。图2为本发明具体实施例的隔油调节池的结构示意图,其中a、隔油下挡板;b、隔油上挡板;c、浮子撇油器。图3为本发明具体实施例的处理肉类加工废水的模块化集成工艺方法的流程示意图。图4为本发明的多模式生物脱氮反应器的九种反应模式示意图,其中,11-反应区,12-消化液回流泵,箭头表示回流方向,黑色部分表示有回流液到达的反应区。具体实施方式下面结合附图和具体的实施例对本发明做进一步详细说明,所述是对本发明的解释而不是限定。在本发明的具体实施方式中,图1提供了一种处理肉类加工废水的模块化集成工艺系统的结构示意图,包括在线监测分析系统1、plc可编程逻辑控制器2和废水处理系统,所述在线监测分析系统1用于对肉类加工废水的水质成分进行监测分析,并将监测分析数据传送至所述plc可编程逻辑控制器2;所述plc可编程逻辑控制器2对所述监测分析数据处理后输出控制信号至所述废水处理系统;所述废水处理系统包括依次连接的一级预处理模块、二级生化处理模块和三级深度处理模块;所述二级生化处理模块和所述三级深度处理模块根据所述plc可编程逻辑控制器2输出的控制信号指令对肉类加工废水进行处理。所述一级预处理模块包括依次连接的粗格珊3、高速破碎机4和隔油调节水池5,所述粗格珊3进口连接肉类加工废水出口。所述粗格珊3与水平面的夹角为60°,栅条间隙为50mm。所述高速破碎机4采用六叶大直径刀片,其工作转速为40000rpm,能实现超微粉碎,快速打破半漂浮在废水中的固体物质,如血块碎肉、大小肠的片段、猪毛、皮屑、胃内容物和粪便等。经过破碎后的废水中固体物质直径不超过5mm,可以直接进入下一个处理系统进行水处理,不产生其它固体废弃物。所述隔油调节水池5具体结构为:内设有间隔设置的4级隔油下挡板a和3级隔油上挡板b,并且在每级隔油上挡板b前设置有浮子撇油器c,其结构如图2所示。所述隔油调节水池5可同时实现调节水质水量及去除浮油的作用。在调节水质水量时,当设计水量<100t/d时,水力停留时间为24.0~48.0h;当100t/d<设计水量<1000t/d时,水力停留时间为18.0~24.0h;当设计水量>1000t/d时,水力停留时间为12.0~18.0h。所述二级生化处理模块包括依次连接的多模式生物脱氮反应器6和生物流化床反应器7。所述多模式生物脱氮反应器6进口连接所述隔油调节水池5出口,所述多模式生物脱氮反应器6由12个反应区11组成,每个反应区底部都设置有曝气系统,最后一个反应区出口设置4台并列连接的硝化液回流泵12,并且第1、2、4、5、6、7、8、9个反应区与所述4台硝化液回流泵之间通过回流管道连接,所述回流管道上设置电动阀门一;所述第1、2、3、4、5、6、7、8、9个反应区的曝气系统设有电动阀门二,通过控制所述电动阀门一和所述电动阀门二的启闭,从而控制所述多模式生物脱氮反应器的九种反应模式(如图4所示)。所述硝化液回流泵12的出口连接所述生物流化床反应器进7口。所述生物流化床反应器7,是指为提高生物膜法的处理效率,以砂(或无烟煤、活性炭等)作填料并作为生物膜载体,废水自下向上流过砂床使载体层呈流动状态,从而在单位时间加大生物膜同废水的接触面积和充分供氧,并利用填料沸腾状态强化废水生物处理过程的反应器。本发明具体实施例所采用的生物流化床反应器,空床停留时间为2.5h,填料采用改性聚乙烯悬浮填料,填料粒径为12±2mm,最大膨胀率为150%,bod负荷为10~12kgbod5/m3·d。所述生物流化床反应器7进口处设置有电动阀门三,所述电动阀门三用于根据工艺要求决定是否启用所述生物流化床反应器。所述三级深度处理模块包括依次连接的高密度沉淀池8、活性砂滤池9和臭氧消毒反应器10。所述高密度沉淀池8,是一种紧凑、高效、灵活的快速沉淀技术,其特点是在混凝阶段投加高密度的不溶介质颗粒(如细砂),利用介质的重力沉降及载体的吸附作用加快絮体的“生长”及沉淀。在本发明的具体实施例中,高密度沉淀池设计表面负荷为16m3/(m2·h)。所述活性砂滤池9,是一种集絮凝、澄清、过滤为一体的连续接触过滤设备,目的是将沉淀后污水进一步实现泥水分离,保证出水ss达标。在本发明的具体实施例中,活性砂滤池设计平均滤速为6m/h。并且,所述活性砂滤池9进口处设置有电动阀门四,所述电动阀门四用于根据工艺要求决定是否启用所述活性砂滤池。所述臭氧消毒反应器10,是废水处理中常用的消毒方法之一,其不局限于消毒,还可用于去除水中可溶性铁盐、锰盐、氰化物、硫化物、亚硝酸盐、色、嗅、味、微量有机物,并使原水中溶解性有机物产生微凝聚作用,强化水的澄清、沉淀和过滤效果。在本发明的具体实施例中,设计臭氧投加量为0.01~0.02kg/m3,接触反应装置的水力停留时间为10min,臭氧化气浓度为20g/m3。本发明具体实施例还提供一种处理肉类加工废水的模块化集成工艺方法,其流程示意图如图3所示,是采用上述系统,包括以下步骤:步骤一,将肉类加工废水引入粗格珊先除去废水中较大物质;步骤二,启动高速破碎机对步骤一出来的废水进行高速破碎处理,将废水中的固体物质破碎至5mm以下的悬浮物;步骤三,启动隔油调节水池,对步骤二出来的废水水量水质进行调节,并去除废水中的浮油;步骤四,在线监测分析隔油调节水池中废水的cod和氨氮值,计算c/n比,根据水质数据选择多模式生物脱氮反应器的反应模式;所述多模式生物脱氮反应器具有以下九种反应模式,如图4所示:反应模式一:当cod<500mg/l,氨氮<50mg/l,c/n≥10时,硝化液回流比为100%,即启动1台消化液回流泵,只开启第1反应区回流管道上的电动阀门一,使废水全部回流至第1反应区,同时关闭第1、2、3反应区曝气系统的电动阀门二,多模式生物脱氮反应器为ao工艺,缺氧段水力停留时间为9h,好氧段水力停留时间为27h;反应模式二:当cod<500mg/l,氨氮<50mg/l,5≤c/n<10时,硝化液回流比为200%,即启动2台消化液回流泵,开启第1、6反应区回流管道上的电动阀门一,使废水平均回流至第1、6反应区,同时关闭第1、6、7反应区曝气系统的电动阀门二,多模式生物脱氮反应器为aoao工艺,第一缺氧段水力停留时间为3h,第一好氧段水力停留时间为12h,第二缺氧段水力停留时间为6h,第二好氧段水力停留时间为15h;反应模式三:当cod<500mg/l,氨氮<50mg/l,c/n<5时,硝化液回流比为300%,即启动3台消化液回流泵,开启第1、5、9反应区回流管道上的电动阀门一,使废水平均回流至第1、5、9反应区,同时关闭第1、5、9反应区曝气系统的电动阀门二,多模式生物脱氮反应器为aoaoao工艺,第一缺氧段水力停留时间为3h,第一好氧段水力停留时间为9h,第二缺氧段水力停留时间为3h,第二好氧段水力停留时间为9h,第三缺氧段水力停留时间为3h,第三好氧段水力停留时间为9h;反应模式四:当500≤cod<1000mg/l,50≤氨氮<100mg/l,c/n≥10时,硝化液回流比为200%,即启动2台消化液回流泵,开启第1、7反应区回流管道上的电动阀门一,使废水平均回流至第1、7反应区,同时关闭第1、2、7反应区曝气系统的电动阀门二,多模式生物脱氮反应器为aoao工艺,第一缺氧段水力停留时间为6h,第一好氧段水力停留时间为12h,第二缺氧段水力停留时间为3h,第一好氧段水力停留时间为15h;反应模式五:当500≤cod<1000mg/l,50≤氨氮<100mg/l,5≤c/n<10时,硝化液回流比为300%,即启动3台消化液回流泵,开启第1、2、6反应区回流管道上的电动阀门一,使废水平均回流至第1、2、6反应区,同时关闭第1、2、6、7反应区曝气系统的电动阀门二,多模式生物脱氮反应器为aoao工艺,第一缺氧段水力停留时间为6h,第一好氧段水力停留时间为12h,第二缺氧段水力停留时间为6h,第一好氧段水力停留时间为12h;反应模式六:当500≤cod<1000mg/l,50≤氨氮<100mg/l,c/n<5时,硝化液回流比为300%,即启动3台消化液回流泵,开启第1、5、9反应区回流管道上的电动阀门一,使废水平均回流至第1、5、9反应区,同时关闭第1、2、5、9反应区曝气系统的电动阀门二,多模式生物脱氮反应器为aoaoao工艺,第一缺氧段水力停留时间为6h,第一好氧段水力停留时间为6h,第二缺氧段水力停留时间为3h,第三好氧段水力停留时间为9h,第三缺氧段水力停留时间为3h,第三好氧段水力停留时间为9h;反应模式七:当cod≥1000mg/l,氨氮≥100mg/l,c/n≥10时,硝化液回流比为300%,即启动3台消化液回流泵,开启第1、2、7反应区回流管道上的电动阀门一,使废水平均回流至第1、2、7反应区,同时关闭第1、2、7、8反应区曝气系统的电动阀门二,多模式生物脱氮反应器为aoao工艺,第一缺氧段水力停留时间为6h,第一好氧段水力停留时间为12h,第二缺氧段水力停留时间为6h,第一好氧段水力停留时间为12h;反应模式八:当cod≥1000mg/l,氨氮≥100mg/l,5≤c/n<10时,硝化液回流比为400%,即启动4台消化液回流泵,开启第1、2、6、9反应区回流管道上的电动阀门一,使废水平均回流至第1、2、6、9反应区,同时关闭第1、2、6、9反应区曝气系统的电动阀门二,多模式生物脱氮反应器为aoaoao工艺,第一缺氧段水力停留时间为6h,第一好氧段水力停留时间为9h,第二缺氧段水力停留时间为3h,第二好氧段水力停留时间为6h,第三缺氧段水力停留时间为3h,第三好氧段水力停留时间为9h;反应模式九:当cod≥1000mg/l,氨氮≥100mg/l,c/n<5时,硝化液回流比为400%,即启动4台消化液回流泵,开启第1、4、7、10反应区回流管道上的电动阀门一,使废水平均回流至第1、4、7、10反应区,同时关闭第1、4、7、10反应区曝气系统的电动阀门二,多模式生物脱氮反应器为aoaoaoao工艺,第一缺氧段水力停留时间为3h,第一好氧段水力停留时间为6h,第二缺氧段水力停留时间为3h,第二好氧段水力停留时间为6h,第三缺氧段水力停留时间为3h,第三好氧段水力停留时间为6h,第四缺氧段水力停留时间为3h,第四好氧段水力停留时间为6h;步骤五,启动多模式生物脱氮反应器,根据所选定的反应模式去除步骤四出来的废水中污染物;步骤六,在线监测分析多模式生物脱氮反应器出水的废水cod和氨氮值,当cod>80mg/l,或者bod>30mg/l,或者氨氮>15mg/l时,进入步骤七,否则进入步骤八;步骤七,启动运行生物流化床反应器,进一步去除水中的cod、bod、氨氮;步骤八,启动高密度沉淀池,对废水进行沉淀排泥;步骤九,在线监测出水水质要求,并根据出水水质要求,当出水水质要求ss<60mg/l,进入步骤十,否则进入步骤十一;步骤十,启动活性砂滤池,对废水进行过滤处理;步骤十一,启动臭氧消毒反应器,对废水进行消毒处理。实施例1本实施例采用图1和图2所示的模块化集成工艺系统以及图3所示的方法对沈阳某肉类加工厂的废水进行处理,处理过程中:步骤四选定了多模式生物脱氮反应器的反应模式二;步骤六结束后进入生物流化床反应器进一步去除水中的cod、bod、氨氮;步骤九结束后进入臭氧消毒反应器对废水进行消毒处理。经过本实施例的集成工艺系统及方法处理后的废水的水质检测结果如表1所示。表1项目单位进水出水codmg/l45080bodmg/l20030ssmg/l80060ph6—86—9色度倍>10050氨氮mg/l3515实施例2本实施例采用图1和图2所示的模块化集成工艺系统以及图3所示的方法对鞍山某肉类加工厂的废水进行处理,处理过程中:步骤四选定了多模式生物脱氮反应器的反应模式四;步骤六结束后进入高密度沉淀池,对废水进行沉淀排泥;步骤九结束后进入活性砂滤池对废水进行过滤处理。经过本实施例的集成工艺系统及方法处理后的废水的水质检测结果如表2所示。表2项目单位进水出水codmg/l100080bodmg/l40030ssmg/l120060ph6—86—9色度倍>10050氨氮mg/l7515实施例3本实施例采用图1和图2所示的模块化集成工艺系统以及图3所示的方法对沈阳某肉类加工厂的废水进行处理,处理过程中:步骤四选定了多模式生物脱氮反应器的反应模式七;步骤六结束后进入生物流化床反应器进一步去除水中的cod、bod、氨氮;步骤九结束后进入活性砂滤池对废水进行过滤处理。经过本实施例的集成工艺系统及方法处理后的废水的水质检测结果如表3所示。表3项目单位进水出水codmg/l160080bodmg/l60030ssmg/l150060ph6—86—9色度倍>10050氨氮mg/l15015本发明具体实施例的工艺过程采用多个单元串联形式,通过改变设备运行参数自动控制转换工艺,节省占地面积的同时节省造价;并且整个过程未采用厌氧系统,冬季无水时可以停运,不存在次年启动时,厌氧系统启动困难,耗费人力物力的问题;整个工艺组合模块化程度高,技术先进,处理后的废水可稳定达标,适用于悬浮物多、水质水量变化较大的小型、零散肉类加工场高浓度废水处理。尽管上面已经示出和描述了本发明的实施例,可以理解的是,上述实施例是示例性的,不能理解为对本发明的限制,本领域的普通技术人员在本发明的范围内可以对上述实施例进行变化、修改、替换和变型。当前第1页12