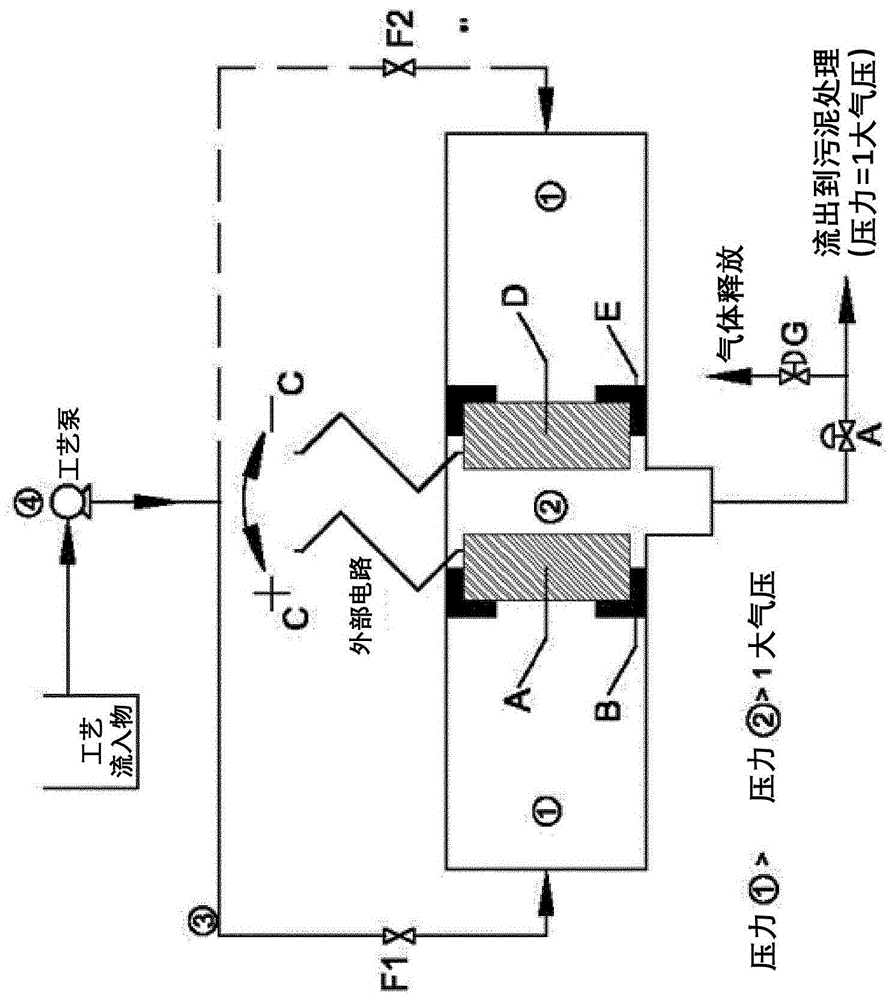
本发明的实施方案涉及电凝(electrocoagulation)装置。该装置可用于处理工艺料流,如污染水、废水和工业废物。本发明的实施方案进一步涉及使用所述装置从工艺料流中除去污染物的电凝方法。概述本发明的一个方面是一种用于处理工艺料流,如污染水、废水和工业废物的新型电凝装置。该装置含有包含在加压系统,如加压管道系统中的多孔和可透牺牲阳极。该阳极可含有压实铁粉。在一些实施方案中,该阳极可以是压实和烧结铁粉,而在另一些实施方案中,该阳极是压实但未烧结的。代替烧结步骤或除烧结步骤外,阳极可以例如在200-400℃的温度下热处理以烧除润滑剂。本发明的另一方面是通过使用所述装置的电凝除去工艺料流,如水、废水或工业废物中的污染物的方法。典型的工业废物包括采矿、纺织、金属电镀、制革、微电子学、纸浆和纸以及酿酒(distillery)。该工艺料流可以是含水流体,如地下水、河水、工业废水、民用废水和/或地表水,以降低流体中的选自含氯化合物、硝酸盐、亚硝酸盐、重金属、有毒无机物质、有毒有机化合物、微生物和/或其组合的污染物的含量。本发明的某些方面和实施方案尤其适用于促进多种污染物的减少。目标污染物可由铬、砷、铅、氟化物、硒、放射性核素、氮类、重金属、磷和有机化合物构成但不限于此。本发明的某些方面和实施方案适合在使用比常规系统少的动力的同时促进至少同等的污染物减少。特别地,本发明的某些方面和实施方案另外提供阳极的高完整性和因此改进的易操作性。背景电凝是通过金属,如铁和铝的电解氧化在水/废水内生成金属氢氧化物混凝剂的简单和有效的方法。电凝的示意性和基本概念显示在图19中。当电流经过该系统时,从牺牲阳极释放金属离子,而在阴极处产生氢氧根离子和氢气。金属离子和氢氧根离子容易组合形成聚合金属氢氧化物,其是优异的混凝剂。下面以铁和/或铝作为阳极材料显示在阳极、阴极和bulk液体处发生的反应。在阳极处:金属的氧化:fe(s)→fe2++2e-fe2+→fe3++e-水的氧化:2h2o→o2+4e-+4h+在阴极处:氢气和氢氧根离子的产生:2h2o→h2+2oh-4e-+4h+→2h2在bulk液体中:金属氢氧化物的形成:fe2++2oh-→fe(oh)2fe3++3oh-→fe(oh)3对于铝阳极,金属的相应氧化是:al(s)→al3++3e-和在bulk液体中,金属氢氧化物的形成是:al3++3oh-→al(oh)3根据bulk液体ph,可如下形成金属的单氢氧化物和多氢氧化物:fe(oh)2+,fe(oh)2+,fe(oh)2,fe(oh)3,fe(oh)63-,fe(oh)4-,并且当使用铝作为阳极材料时,形成的氢氧化物的实例是:al(oh)2+,al(oh)3,al(oh)4-,al13(oh)345+,al13(oh)327+金属氢氧化物形成絮凝剂并通过离子交换、吸附、中和和sweep-floc作用除去污染物。金属阳离子中和胶体粒子和污染物的负表面电荷。然后粒子靠得更近并在范德华力的影响下附聚。除各种类型的离子外,可通过电凝以沉降絮凝体的形式有效地除去有机物质。如电流密度、ph、电极类型、反应时间等因素在金属氢氧化物的形成中起到重要作用。通常,较高电流密度在溶液中产生较多的金属离子。同样地,金属氢氧化物的溶解度极大依赖于该溶液的ph。用于形成铁和铝氢氧化物絮凝剂的最佳ph范围在5至8之间。但是,在更低或更高ph下絮凝体变得可溶。ph对金属絮凝剂与污染物的相互作用同样重要。例如,通过氢氧化铝除去氟化物被认为是离子交换法。氟离子替代氢氧化铝中的一个氢氧根离子并根据下列反应制造络合物:al(oh)3+xf-→al(oh)(3-x)fx(s)+oh-下列方程提供适用于本发明的方法和本发明的装置的电凝法的基本特征之间的理论关系。理论阳极材料消耗在电凝法中,阳极是牺牲的并随时间经过损失质量。阳极质量的损失随电荷载量(电流)和电极类型而变。可以使用下列方程计算理论质量损失:al(oh)3+xf-→al(oh)(3-x)fx(s)+oh-其中mm是每分钟的阳极质量损失(g*min-1),i是电流(a),mw是金属的分子量(g*mol-1),z是在金属氧化过程中释放的电子数量(对fe而言为2或3,对al而言为3),且f是法拉第常数(96,486c*mol-1)。基于上述方程,每当1法拉第的电荷经过电路,8.99克铝和18.6克铁从阳极溶解到溶液中。阳极质量的损失直接影响污染物脱除。理论能量消耗、电导率和法拉第产率(faradicyield)能量消耗取决于跨过电极施加的电压差、电流和反应时间。另一方面,反应时间取决于污染物浓度。可使用下列方程计算每单位质量的污染物脱除的能量消耗:ec=vitr/cr其中ec是脱除每单位质量的污染物的总能量消耗(kwh*g-1),v是电池电位(v),i是电流(a),tr是反应时间,且cr是在时间tr内脱除的污染物质量。在恒定的外加电池电位下,经过电路的电流取决于水的电导率。大多数地下水和废水具有足够高的电导率以确保对该反应而言足够的电流流量。但是,在一些情况下,加入辅助电解质(secondaryelectrolytes)可能有助于提高水的电导率和因此电流流量。产生氯离子的辅助电解质尤其有用,因为氯离子有助于除去随时间经过涂覆阳极表面的一些掩蔽剂。这种掩蔽现象极大降低系统效率。也用作抗掩蔽剂的辅助电解质的实例是氯化钾或氯化钠。系统效率可通过计算法拉第产率或电流效率(ce)评估,其被定义为实际阳极消耗(ma)与理论值(mt)的比率,可如下计算:ce(%)=ma*100/mt实际阳极损耗可通过在反应之前和之后的干阳极的重量分析量化。实际上,由于金属在水中的自发氧化,法拉第产率可能高于100%。电凝污泥的理论产量电凝法产生絮凝体,其最终附聚并作为污泥沉降在反应室底部。金属氢氧化物如al(oh)3对水具有高的化学和物理亲和力。因此,尽管具有良好的可沉降性,电凝污泥具有高的水含量。可以考虑下列方程计算每分钟产生的污泥质量(g*min-1):sm=(60*l*(mw/z+17))/f在该方法的过程中产生的污泥量也可在该方法结束时通过重量分析法量化。氢气的理论产量在阴极处的水的电解产生氢气。产生的氢气体积取决于由阴极提供的电子数量。根据反应化学计量学,产生1摩尔氢气消耗2摩尔电子。在tr(sec)的反应时间期间阴极释放的电子的摩尔数(me-)可使用下列方程计算:me-=i*tr/f基于上文,在温度t(k)和压力p(atm)下在tr(sec)的反应时间期间产生的以毫升计的氢气体积(vh2)可使用下列方程计算:vh2=(11,207*i*tr/273.15)/(f*p)这一方程计算在阴极处没有竞争电子的离子时由该方法产生的氢气体积。如果存在竞争离子,如六价铬离子,氢气产量低于理论值。氢气是电凝法的有用副产物。在专利文献中,公开了用于修复水或废水的与电凝有关的许多方法和材料。公开文献的下列实例可被视为本发明的实施方案的相关技术。us2012/0055871涉及使用铁粒子和含次氯酸钠的水溶液的电解方法。该方法的特征在于其使用直流电流、来自阳极的铁粒子,且水溶液的次氯酸钠浓度为至少1g/l。该文献进一步涉及用于预处理生水的方法和装置,产生的水容易处理以产生饮用水或所谓的技术水(technicalwater)。us2005/0167285提供用于从饮用水中除去砷酸盐的电化学方法,其中通过吸附到由“原位”阳极氧化形成的金属氢氧化物上而除去砷酸盐。该申请描述了配有软钢或铝板的阳极和不锈钢阴极的电化学电池,电极间的距离为0.5至1.5厘米。ep0595178a1描述了用于废水的电解处理的装置和方法。待净化和处理的水首先流过至少一个含有不溶性阳极的阳极室,然后流过含有可溶性可透阳极的另一阳极室。在水进入可溶性阳极室之前加入焦炭粒子以引发电凝过程。多孔牺牲阳极可由铁屑制成。us4,014,766公开了在具有包含不溶性中心电极和围绕其布置并与其电接触的微粒铁屑体的阳极的电解池中对废水施以电解的方法,由此废水中的杂质包藏在通过铁屑的电解溶解形成的氢氧化铁絮凝剂内,并对含杂质的絮凝剂施以氧化加工,此后分离。可对由此处理的废水施加磁场以促进絮凝剂的沉降。可在中性或碱性条件中高效进行六价铬离子还原成三价铬离子,而不像使用铁板时的情况那样使用酸性条件。us2006/0000784描述了在至少两步法中处理水或废水以除去污染物的方法,其包含:(a)处理水,以产生至少部分处理过的中间流出物,(b)用牺牲金属处理中间流出物并产生所述牺牲金属的离子,和提供非常充分处理的流出物,(c)复原在步骤(b)中生成的牺牲金属离子并将复原离子再循环到步骤(a),来自步骤(c)的复原和再循环离子通过使用复原离子从中间流出物中另外除去污染物而改进步骤(a)的处理效率,以产生更清洁的中间流出物并因此降低步骤(b)中的污染物载量,更充分地进一步处理中间流出物,并降低步骤(b)中的牺牲金属需求量。步骤(a)优选是生物步骤、生物-非生物步骤、物理化学步骤或这些步骤的组合。应该除去各种污染物,如重金属、有机化合物、溶解物质、悬浮固体、固体粒子、营养素、氨、硝酸盐、亚硝酸盐、磷酸盐、微生物等。wo2013/059964a1描述了包括电极基底、磁性电极粒子和磁场源的自组装高表面积电极。在磁场源的影响下,磁性粒子组装在电极基底的表面上。该电极可用作用于处理被污染的供水的电凝系统中的阳极和/或阴极。该文献进一步提到适用于磁性电极粒子的材料是铁粒子。ep0015057a2描述了提供比完全由烧结粒子构成的电极便宜并产生与完全由烧结材料构成的电极一样好或更低的在气体释放中的过电位的用于水电解槽的电极的实施方案。根据这一文献的电极具有不透性、导电基底和粘结到基底上的多孔冶金粘结层(25-275μm厚、由烧结至45至65%理论密度的具有2至30μm直径的镍、镍-铁合金、铁或铁-碳合金粒子制成)。wo2014184106公开了含有牺牲电极的用于电凝的电化学电池。该牺牲电极含有非牺牲部分和含铁粉的多孔牺牲部分。su981241涉及在电凝器中净化污水。该发明的目标是通过增加三价铁盐形式的混凝剂的释放来提高生产率。公开了由不溶部分和含铁屑的可溶部分构成的电极。su1255580a1描述了含铬的无水的电化学净化方法。该描述能够降低比能消耗。电凝已使用多年并已证实是用于从水和废水中除去各种污染物的高效方法。但是,仍然需要改进该方法,尤其是考虑到能量效率。本发明的实施方案可在更高能量效率和明显降低的水力停留时间方面提供电凝法的改进,从而能够使用紧凑和空间要求更低的工艺设备,即降低的占地面积。本发明的各种方面和实施方案的概述本发明的实施方案包括配置成处理工艺料流,如污染水、废水或工业废物的电凝装置。该装置可含有牺牲阳极和阴极。本发明的实施方案还包括减少工艺料流,如污染水、废水或工业废物中的污染物的量的方法。在一个实施方案中,将工艺料流加压并受压穿过可透阳极。在一个实施方案中,施加的压力应该足以填充阳极的至少95体积%,优选至少99体积%,优选99.9体积%或所有孔隙和空隙并另外提供如通过ksat值规定的经过该系统的足够的工艺料流流速。本发明的方面涉及一种配置成处理工艺料流的电凝装置,所述装置包含:-阴极;-由包含铁并具有11体积%至62体积%,优选22体积%至51体积%,更优选30-42体积%的孔隙率的压实粉末构成的牺牲阳极,其中所述阳极是多孔并透水的;和-压力系统,其中所述压力系统配置成使工艺料流流过所述阳极,其中所述阳极具有第一侧和相反的第二侧,其中工艺料流从第一侧穿过所述阳极流到第二侧,且其中第二侧上的工艺料流压力小于第一侧上的压力,以使压力差为至少6.9kpa(1psi),优选至少17.9kpa(2.6psi)。在一些实施方案中,配置所述压力系统以使至少50%,优选80重量%,更优选95重量%,最优选至少99.5重量%的工艺料流流过所述阳极。在一些实施方案中,第一侧上的工艺料流压力为至少13.8kpa(2psi)。在一些实施方案中,所述阳极由压实并烧结的粉末构成。在一些实施方案中,所述压实粉末包含至少90重量%的铁,优选至少95重量%的铁,最优选至少97重量%的铁。在一些实施方案中,所述压实粉末包含具有使得小于45μm的粒子的量为最多10重量%、45至150μm之间的粒子的量为0-20重量%、150至212μm之间的粒子的量为10-50重量%、212至500μm之间的粒子的量为50-90重量%且大于500μm的粒子的量为0-30重量%的粒度分布的铁粉。在一些实施方案中,所述铁粉具有使得小于45μm的粒子的量为最多5重量%、45至150μm之间的粒子的量为0-20重量%、150至212μm之间的粒子的量为10-30重量%、212至500μm之间的粒子的量为60-90重量%且大于500μm的粒子的量为0-10重量%的粒度分布。在一些实施方案中,所述阳极包含压实铁粉和铝粉的混合物。在一些实施方案中,铁粉和铝粉之间的重量比为50:50至98:2,优选60:40至98:2,最优选70:30至95:5。根据另一方面,本文公开了一种通过电凝处理工艺料流的方法,其含有下列步骤:-提供如上文和下文公开的电凝装置,-在所述阳极和所述阴极之间供应电位差的同时,通过在穿过所述阳极之前将工艺料流加压而使工艺料流穿过所述装置。根据一些实施方案,当所述阳极和阴极在结构上相同时,所述方法进一步包含以下步骤:-在所述阳极的牺牲部分至少部分耗尽时切换极性。根据一些实施方案,在穿过所述阳极之前将工艺料流加压到大气压以上。根据一些实施方案,所述阳极具有高于0和最多19cm/天,优选4至17.5cm/天,更优选4.3至16.4cm/天,最优选7.6和至13cm/天的ksat值。ksat是指饱和导水率(hydraulicconductivity),其描述流体移动穿过饱和孔隙结构中的孔隙的简易性。根据一些实施方案,所述方法进一步包含,在使工艺料流穿过所述装置之前和/或过程中,调节ph至阻止形成的氢氧化物絮凝剂溶解的值,优选至5至8之间的值。根据一些实施方案,所述工艺料流包含重金属,如铬或砷。根据一些实施方案,所述工艺料流包含氟化物。根据另一方面,将如上文和下文公开的电凝装置配置成处理污染水或废水;其中阴极和阳极包含在加压管道系统中,且其中所述电凝装置进一步包含:-向所述电极供电的系统,-处理絮凝体的系统。附图简述图1显示根据本发明的电凝法的一个实施方案。在这一实施方案中,牺牲电极和阴极具有相同组成并具有相同形状。图2显示本发明的另一实施方案,其具有多个牺牲阳极和在组成和形状上不同于牺牲阳极的单个阴极。图3显示与图2中所示的实施方案类似的根据本发明的另一实施方案,只是牺牲阳极和阴极移动90度,即垂直布置。图4是显示生成每单位质量絮凝剂脱除的cr(vi)质量的图。比较常规电凝法与可透电极法。图5是显示在根据实施例2的本发明的实施方案的方法中由可透电极生成的絮凝剂的沉降速度的图。图6是显示在实施例2中的常规方法中由电极生成的絮凝剂的沉降速度的图。图7是显示用相同压制力和相同孔隙率(分别为27.6mpa(2tsi)和61%)以0.33、0.41和0.50的不同厚度压制的可透阳极的脱除效率比较的图;这些阳极可用于根据本发明的电凝法的一个实施方案。图8是显示用相同压制力和相同孔隙率(分别为41.4mpa(3tsi)和57%)以0.30、0.37和0.56的不同厚度压制的可透阳极的脱除效率比较的图;这些阳极可用于根据本发明的电凝法的一个实施方案。图9是显示用相同压制力和相同孔隙率(分别为55.2mpa(4tsi)和53%)以0.27、0.34和0.41的不同厚度压制的可透阳极的脱除效率比较的图;这些阳极可用于根据本发明的电凝法的一个实施方案。图10是显示具有相同质量(20克)和61%、57%和53%的不同孔隙率的可透阳极的脱除效率比较的图;这些阳极可用于根据本发明的电凝法的一个实施方案。图11是显示具有相同质量(25克)和61%、57%和53%的不同孔隙率的可透阳极的脱除效率比较的图;这些阳极可用于根据本发明的电凝法的一个实施方案。图12是显示具有相同质量(30克)和61%、57%和53%的不同孔隙率的可透阳极的脱除效率比较的图;这些阳极可用于根据本发明的电凝法的一个实施方案。图13是显示相对于脱除效率的ksat值的图。图14是显示在各种流速下的ksat值的图。图15是显示在各种阳极孔隙率下的ksat值的图。图16是显示在各种阳极孔隙率和流速下的ksat值的图。图17是显示在各种孔隙率下穿过可透阳极的通量的曲线的图。图18a-b是显示移置于图17中所示的通量曲线上的ksatvs.孔隙率的线性关系的图。在图18a中,标示区域d的ksat值,而在图18b中,标示区域c-e的ksat值。图19显示常规电凝法的原理图。图20显示具有不同孔隙率的可透阳极的脱除百分比的曲线图。详述图1显示待处理的工艺料流3。通过工艺泵4将工艺料流3加压,流入管道1。工艺料流3流过通过阳极支架b固定的多孔牺牲阳极a。阳极支架b密封管道1以使所有或基本所有(如至少50%,优选80重量%,更优选95重量%,最优选至少99.5重量%)工艺料流3流过阳极a。“流过”是指工艺料流3从阳极a的侧1流到阳极a的相反侧2。流过不同于工艺料流越过/沿阳极表面流动的流路。工艺料流3,在阳极a的侧1上,在高于大气压的压力p1下。跨过阳极的压差优选为至少6.9kpa(1psi),更优选至少17.9kpa(2.6psi)。在穿过阳极a流到侧2时,工艺料流3在优选高于大气压的压力p2,优选至少103kpa(15psi),更优选138kpa(20psi)下。压力p1大于压力p2。将阳极a连向直流电源c的正极。将阴极d连向直流电源c的负极。在一个实施方案中,电极可切换,其中阳极a变成阴极,阴极d变成牺牲阳极。阴极d在这一实施方案中具有与阳极相同的形状和组成,这允许在适当时刻有效切换电极。在另一些实施方案中,电极a和d可具有相同组成,但不同结构;不同组成,但相同结构;或不同组成和不同结构。通过阴极支架e固定阴极d。在电极切换后,阴极支架e密封管道1以使所有或基本所有(如至少50%,优选80重量%,更优选95重量%,最优选至少99.5重量%)工艺料流3流过阴极d(现在是牺牲阳极)。待处理的工艺料流3流过打开的阀f1,关闭阀f2。当电极切换时,工艺料流3流过打开的阀f2,关闭阀f1。在穿过牺牲阳极后,工艺料流3流过阀g、气体释放站并进一步流到污泥处理单元(未显示),其中将含污染物的污泥与清洁的水分离。在一个实施方案中,支架b、e可由任何不透水材料,如橡胶或聚合物制成。在一个实施方案中,电极a、d可配置成紧密地嵌在管道1中或挨着管道1的接合(abutment)表面。这可允许在布置中不使用单独支架密封管道1。如果电极a、d不与密封材料一起使用,电极a、d和管道1的布置应该配置成使得在工艺压力下,所有或基本所有(如至少50%,优选80重量%,更优选95重量%,最优选至少99.5重量%)的工艺料流3流过电极a、d。优选的i/q水平小于380a/m3/hr,优选小于350a/m3/hr,更优选小于340a/m3/hr,更优选小于330a/m3/hr,其中i是外加电流且q是流速。在一个实施方案中,该装置能够电凝工艺料流的连续流。图2显示该装置的另一实施方案。在这一实施方案中,该装置含有多个牺牲阳极a和单个阴极d。在这一实施方案中,阴极d可在组成和/或形状上不同于阳极a。工艺料流3流过各阳极a。通过阳极支架a固定各阳极a,其可密封管道以使所有或基本所有(如至少50%,优选80重量%,更优选95重量%,最优选至少99.5重量%)的工艺料流3流过阳极a。优选各阳极a基本相同。但是,在一个实施方案中,阳极a可包括具有不同组成和/或形状的阳极。在这一实施方案中,电极和电流不配置成逆转。图2还显示再循环回路,其中经过阳极a的一部分工艺料流3再循环以经过牺牲阳极,以进一步穿过牺牲阳极a。在这一实施方案中,可以使用单个阳极a。优选在仅使用单个阳极a时使用再循环回路。在这一实施方案中,可以使用多个阴极a。图3显示如图2中所示的类似装置,只是电极转动90度,即垂直安装。在实施方案中,牺牲阳极连向电源的正极。从阳极释放阳离子到溶液中并传送到阴极(negativecathode),在此发生水解,以产生氢氧根离子和氢气,电子从阳极经过外部电路运行到阴极,以造成水的电解和阳离子的还原。金属离子污染物的还原的一个实例是cr6+离子还原成cr3+离子,与水解竞争。同样地,砷从as5+还原成as3+,硒从se6+还原成se4+,且铀从u6+还原成u4+。铁粉用于牺牲阳极的合适的铁粉可以是雾化铁粉,如水雾化铁粉,和化学还原铁粉,如co还原或h2还原。铁粉的fe含量可优选高于90重量%。可优选选择铁粉的粒度以获得牺牲阳极的多孔结构。具有太细粒度的粉末较不合适,因为这样的粉末往往较难透过液体,另一方面太粗的粒子具有较低的表面/体积比,这阻碍正离子释放到处理的水中。较粗的铁粉也可能难以压实成具有足够强度和孔隙率的物体(bodies)。合适的粉末可具有在10μm至1mm之间的粒度分布和在0.8-3.0g/cm3之间的如根据iso3923-1:2008测得的表观密度。如根据bet测得的比表面积可以在0.1至0.5m2/g之间。所用的优选铁粉可具有至少90重量%,优选至少95重量%,最优选至少97重量%的fe含量。铁粉中的其余元素是含量最多3重量%,优选最多2.5重量%的氧和其它不可避免的杂质。氧和其它不可避免的杂质的量取决于用于生产铁粉的原材料和生产方法。除氧外不可避免的杂质的实例是总含量低于2重量%,优选低于1重量%,最优选低于0.5重量%的c、s、p、si、mn、cr、cu、mo、ni、al。在一个优选实施方案中,小于45μm的粒子的量为最多10重量%。45至150μm之间的粒子的量为0-20重量%。150至212μm之间的粒子的量为10-50重量%。212至500μm之间的粒子的量为50-90重量%。大于500μm的粒子的量为0-30重量%。在另一优选实施方案中,小于45μm的粒子的量为最多5重量%。45至150μm之间的粒子的量为0-20重量%。150至212μm之间的粒子的量为10-30重量%。212至500μm之间的粒子的量为60-90重量%。大于500μm的粒子的量为0-10重量%。在一个优选实施方案中,该铁粉是h2还原铁粉。表观密度可为0.8-3.0g/cm3,优选0.8至2.5g/cm3,最优选1.2-1.8g/cm3。根据bet测得的比表面积可为0.1至0.5m2/g。铝粉在电极的牺牲部分中含有铝粉的实施方案中,铝粉中的al含量可优选为90至99重量%,且粒度分布为4.5至875μm。铁粉和铝粉的混合物已经表明,铁和铝在牺牲阳极中的组合产生有效脱除氟化物和形成的混凝剂的充足沉降速度的联合效果。在含有这两种粉末的实施方案中铁粉和铝粉之间的重量比可为最小50:50,优选最小60:40,最优选最小70:30,从而不造成加工过的水中不可接受的高铝离子残留和延长的沉降。另一方面,在含有这两种粉末的实施方案中铁粉和铝粉之间的最大重量比可为98:2,优选95:5,以实现充分氟化物脱除能力。因此铁粉和铝粉之间的重量比可为50:50至98:2,优选60:40至98:2,最优选70:30至95:5。这也可表示为电极的牺牲部分中的铝粉含量可为2-50重量%,优选2-40重量%,最优选5-30重量%。以及例如10-30重量%或15-25重量%的铝粉。可透和多孔阳极的制造将铁粉或铁粉和铝粉的混合物转移到压实模具并压实。优选用至少10mpa,优选至少20mpa,更优选至少25mpa的力压缩阳极。在一些实施方案中,在27.6mpa(2tsi)至986mpa(71.5tsi)的压力下压实铁粉或铁粉和铝粉的混合物以获得足够的孔隙率和完整性和强度。这意味着可透(液体和气体)阳极应具有11-62%,优选22-51%,最优选30-42%的孔隙率。在压实前可加入常规润滑剂以促进压实和压实阳极的推出。为了进一步增强阳极的完整性和强度,可以进行烧结步骤。但是,更有意义的是在200-400℃的温度下热处理阳极以烧除润滑剂。选择压实或任选烧结的阳极的形状以装入管道系统和如果存在,不导电的不透性密封材料。这样的不导电的不透性密封材料可以是常规的不导电垫圈。电凝法根据本发明的实施方案的电凝法采用所述装置。待清洁的工艺料流流过可透和多孔的牺牲阳极。通常施加dc;但是可使用ac,尤其是当阳极和阴极在结构上基本相同时。ac的使用可减轻结垢问题并简化电气设备。施加的压力可足以填充阳极的至少95%,优选至少99%,优选99.9%或所有孔隙和空隙并提供经过该系统的足够流速。与已知电凝法相比,在相同脱除效率下,根据本发明的实施方案的方法可获得水力停留时间的显著降低。水力停留时间在此被定义为可透和多孔牺牲阳极的体积除以该系统中的流速:hrt=阳极的体积[m3]/流速[m3/小时]尽管本发明的实施方案的典型hrt为6秒至2分钟,已经表明,在根据本发明的实施方案的电凝法中,污染物的脱除效率极大地与饱和导水率ksat相关。ksat值描述流体移动穿过饱和孔隙结构中的孔隙的简易性。因此,根据本发明的一个实施方案的方法可在使得ksat的优选区间为4至17.5cm/天,优选4.3至16.4cm/天,最优选7.6至13cm/天的条件下进行。为了阻止形成的氢氧化物絮凝体溶解,可以在该方法开始之前和/或在该方法的过程中调节待净化的工艺料流的ph,优选至5至8之间的值。在从工艺料流中除去铀的实施方案中,可以将ph调节到至少10的值。可以调节ph以利于除去特定污染物。在该方法之前和/或过程中,可以加入电解质以提高待处理的水的电导率。实施例下列实施例旨在例示本发明的实施方案但无意限制本发明的范围。用于测定某些性质的程序下列实施例中收集的数据由电流(i)、电压(v)、铬(cr)浓度、压力(p)、生坯强度(gs)和生坯密度(gd)构成。根据下列程序获得各数据组的值。由5a/30vdc电源的显示屏获得电流和电压。设定电源以在所需试验运行期间保持恒电流,其中电压可基于阳极和阴极之间的电阻改变。收集流入的样品并在分析前经0.45微米注射器式过滤器过滤。收集流出的样品并静置以使絮凝体沉降。然后经0.45微米注射器式过滤器过滤上清液。使用hachdr5000分光光度计(方法8023)分析过滤的流入和流出样品的铬(vi)浓度。对于六价铬[cr(vi)],分光光度计的方法检测极限(mdl)为0.01mg/l。在实施例中,低于mdl的cr(vi)浓度被认为已达到最大污染物脱除并被定义为无缺陷。生坯强度是未烧结的压实阳极可承受的力的量。根据iso标准3995测试阳极的生坯强度。生坯密度是未烧结的压实阳极的密度并使用下列公式计算:gd=mm/v其中mm是阳极的质量且v是使用圆柱体体积方程计算的体积(v=π*r2*h)。实施例1-处理每单位体积的外加电流使用图1中所示的装置进行这一实施例。牺牲阳极由具有大约97%的铁含量、1.39g/cm3的表观密度和0.22m2/g的比表面积的铁粉制成。铁粉的粒度分布含有1重量%小于45μm的粒子。45至150μm的粒子的量为10重量%。150至250μm的粒子的量为12重量%。250至850μm的粒子的量为75.6重量%。850至1000μm的粒子的量为1.4重量%。各可透阳极具有25克的重量并用27.6mpa(2tsi–吨/平方英寸)的力压制以实现62%孔隙率。优选用至少10mpa,优选至少20mpa,更优选至少25mpa的力压缩阳极。将重铬酸钾(k2cr2o7)、盐酸(hcl)和氯化钠(nacl)添加到去离子水中。初始水质由100mg/l的cr(vi)浓度、等于7.0的ph和2300μs/cm的电导率构成。在连续流工艺中使用蠕动泵将废水在压力下传送到反应器并穿过阳极。在不同的外加电流下运行试验并调节流速以实现低于0.01mg/l的流出cr(vi)浓度。表1显示电流和流速设定点以实现这一废水的最大污染物脱除,以及处理每单位体积废水所需的电流量。表1电流(a)电压(v)流速(ml/min)i/q(a/m3/hr)0.45.1144760.67.223.54260.98.6463261.810.292326表1中的结果表明可透电极在提高的流速下更高效工作并且最适合具有相对较高的污染物水平的高流速用途。这一实施例中的第二试验使用相同型式的电极但在常规电凝法中进行。将电极从汇流条组装件悬挂到反应容器中。该方法分批运行。在表2中将常规电凝法的结果与可透阳极法的结果比较。作为对比例,与根据本发明的实施方案的方法中的前述实验中所用相同的水的电凝,但以常规方式进行,其中没有迫使待处理的水穿过可透阳极。用于常规电凝法的装置包括1,200毫升玻璃烧杯、磁搅拌器、电极组件支架和电源。制造粉末金属电极以实现与根据本发明的实施方案的方法中所用的可透电极相同的质量和孔隙率。表2可透反应器能够在46ml/min的流速下用0.9a的外加电流实现100mg/l铬的最大污染物脱除。含有具有相同表面积、相同外加电流和相同初始污染物浓度的电极的常规反应器只能在37ml/min的速率下处理。除提高的脱除效率外,可透反应器需要较少功率消耗处理相同体积。常规反应器为了处理相同体积(46ml/min)的废水,需要1.1a的外加电流。可透反应器和常规反应器分别需要2.80和3.24kw/m3/hr的功率消耗。处理每单位体积的水的功率消耗(kwhr)表示为:p=(i*v)/(1000*q)其中q是以m3/hr计的流速,i是以a计的电流且v是电压。实施例2-生成每单位质量絮凝剂脱除的污染物的量对这一实验使用两个分开的试验装置。用于可透电凝法的装置使用图1中所示的装置进行。根据实施例1中规定的相同规格制造牺牲阳极。用于常规粉末金属电凝法的装置包括1,200毫升玻璃烧杯、磁搅拌器、电极组件支架和电源。制造粉末金属电极以实现与根据本发明的实施方案的电极相同的质量和孔隙率。将重铬酸钾(k2cr2o7)、盐酸(hcl)和氯化钠(nacl)添加到去离子水中。初始水质由100mg/l的cr(vi)浓度、等于7.0的ph和2300μs/cm的电导率构成。各试验用相同体积的制成的废水运行。为各试验选择外加电流以在相同时间量中有效处理相同体积的废水。表3显示运行条件和结果,因为它们涉及生成每单位质量絮凝剂脱除的污染物的质量。各试验一式三份运行。表3中报道的结果是一式三份测试的平均值。表3运行条件/结果根据本发明的实施方案的方法常规方法电极质量25g25g电极孔隙率62%62%电流0.9a1.0a处理体积1,200ml1,200ml运行时间30min30mincr(vi)的初始浓度100mg/l100mg/l脱除的总cr(vi)0.12g0.12g生成的总絮凝剂1.38g1.51g图4显示对于这两种方法,在制成的干燥絮凝剂中脱除的cr的浓度。在根据本发明的一个实施方案制成的絮凝体中脱除的cr的浓度高于根据常规方法制成的絮凝体中的cr浓度。为了在相同时间量中实现从相同体积的水中脱除相同量的污染物,常规方法需要比根据本发明的实施方案的方法(0.9a)高的外加电流(1.0a)。由于根据本发明的实施方案的方法中所需的较低电流,为最大限度脱除六价铬而生成的絮凝剂较少。因此,根据本发明的实施方案的可透电凝法除去比常规电凝法(79.4毫克cr(vi)/克絮凝剂)多9.7%的量的污染物/单位质量絮凝剂(87.1毫克cr(vi)/克絮凝剂)。通过在室温下在刻度沉降柱中随时间经过分析压缩体积,评估从可透电极和常规电极中沉降絮凝体的速度。在某些时刻获取沉降絮凝体的高度的读数,即在絮凝体和水的界面处。使用iii型受阻区沉降速度图计算,根据本发明的实施方案的方法造成0.917m/h的沉降速度,而常规方法造成0.385m/h的沉降速度。通过根据本发明的实施方案的方法制成的絮凝体的沉降速度是常规制成的絮凝体的2.4倍。实施例3-污染物脱除率vsksat值使用图1中所示的装置进行这一实施例。牺牲阳极由具有与实施例1中规定的铁粉相同的性质的铁粉制成。表4显示为这一实施例制成的阳极的特征。表4工艺描述:将重铬酸钾(k2cr2o7)、盐酸(hcl)和氯化钠(nacl)添加到去离子水中。初始水质由100mg/l的cr(vi)浓度、等于7.0的ph和2300μs/cm的电导率构成。所有试验用0.2a的外加电流进行。穿过可透阳极施加4.5、9、23.5、46和92ml/min的流速。收集流出物以测量在所用的流速条件下六价铬的%脱除。图7至9中的脱除效率曲线显示用相同压制力压制的可透阳极的铬脱除并比较电极厚度。图7代表对在27.6mpa(2tsi)(61%孔隙率)下压制的阳极收集的数据、图8在41.4mpa(3tsi)(57%孔隙率)下且图9在55.2mpa(4tsi)(53%孔隙率)下。有意思地,所有3个图中报道的结果表明,在恒定压制力下,保持恒定孔隙率,经过较薄可透阳极的脱除效率较高。实施例中的脱除效率被定义为随时间经过的%脱除:脱除效率=(c0-cf)/c0*100/t其中c0是初始浓度,cf是所得浓度且t是时间。图10至12显示具有相同质量但用各种压制力压制以赋予各电极不同孔隙率的可透阳极的铬脱除。图10代表对具有20克质量的压制阳极收集的数据,图11具有25克质量,图12具有30克质量。令人惊讶地,所有3个图(图10至12)中报道的结果表明,在恒定阳极质量下,脱除效率与孔隙率成反比。在进行实验之前,推测越多孔的阳极由于越高的内表面积而表现得越好。考虑到关于使用更薄和孔隙率更低的可透阳极时污染物脱除提高的令人惊讶的结果,更多的注意力集中在研究其原因。可推出一个理论,即在恒定的外加电流下,通量可能对脱除效率具有直接影响。在这一实施例中,使用可透电极的饱和导水率(ksat)定义通量。ksat值表示为达西定律中的比例因子。q=k*a*(δh/δl)其中q是流速,a是阳极的横截面积,δh是水头(hydraulichead)且δl是阳极的厚度。图13显示cr(vi)脱除与可透阳极的ksat值相关。此处所示的数据是如表4和“工艺描述”中规定的完整数据集矩阵。图13中所示的结果证实ksat值与可透电极的脱除效率的直接相关性。在对阳极施加的恒定电流下,随着ksat值提高,脱除效率降低。由于流速对ksat具有大的影响,将图13拆解成恒定流速趋势并显示在图14中。图14证实甚至在恒定流速下脱除效率也与ksat成反比。图15显示在不同阳极孔隙率下ksat值对脱除效率具有的趋势。如预期,在给定的ksat值下,更多孔的阳极实现更高脱除效率。这进一步解释在图16中,其中将流速vsksat移置在与图15相同的数据上。考虑到达西定律为k=(q/a)*(δl/δh),在恒定ksat值下,比较具有相同横截面积的2个阳极(阳极1和阳极2)得出:q1xδl1/δh1=q2xδl2/δh2如果阳极具有比阳极2低的孔隙率,则δl1<δl2和δh1>δh2。因此,阳极1需要较高流速以保持相同ksat值。因此由于经过反应器的接触时间减少(即水力停留时间减少)而降低其脱除效率。基于这一实施例扩展,牺牲阳极由具有与实施例3的前一部分中所用的铁粉相同的性质的铁粉制成。阳极由相同质量和表面积但略微不同的厚度构成。使用可见于表5的不同压制力制造12.6%至62.1%的不同孔隙率的阳极。该实施例对所有阳极试验保持恒定的工艺参数。具体而言,流速设定为46ml/min且外加电流为0.2a。结果报道在图20中。为了比较,图20中拟合的趋势线包括由图11中报道的结果计算的三个数据点。使用具有此处所用的相同质量以及用0.2a的外加电流测试的阳极生成图11中的实验数据。进行计算以校正流速差。使用46ml/min的流速生成另外三个数据点。使用图20指定与表7中的脱除效率相关的区域。实施例4-生坯强度vs孔隙率使用图1中所示的装置进行这一实施例。阳极由具有大约97%的铁含量的铁粉制成。以不同的孔隙率制造阳极并测试它们的渗透率。表5显示各阳极的特性和在34.5kpa(5psi)的外加系统压力下的渗透率(以ml/min计的流速)。表5根据表5中报道的数据,具有10%或更低孔隙率的阳极不允许水流过其材料并且被视为不可透。随着孔隙率提高,阳极的生坯强度降低。在小于1.72mpa(250psi)的生坯强度下,阳极的完整性无法承受运输和装卸、安装、维护或施加的系统工艺条件。因此,可透阳极应具有不小于11%和不大于62%的孔隙率。实施例5-由不同材料制成的阳极在单独的实施例中,由不同的铁材料制造阳极以比较在相同压制力下的生坯强度。将用于制造可透阳极的优选可透铁复合材料与由其它铁粉(较不优选的铁粉“铁a”至“铁d”)制成的阳极比较。所有材料用689mpa(50tsi)的压制力压制且结果报道在表6中。表6与由其它铁粉制成的阳极相比,用于制造本发明的一个优选实施方案中所用的可透阳极的铁粒子不仅带来略高的孔隙率,还产生具有明显更高的生坯密度的阳极。使用图17确定可透阳极的最佳孔隙率范围。在此图中,绘制具有表5中的不同孔隙率的阳极的通量曲线。通量是阳极的每横截面积的流速的量。在34.5kpa(5psi)的外加压力下收集穿过阳极的所有通量值。为了测定提供最佳操作性能的阳极的孔隙率,首先从通量曲线的最陡(最大泵效率)和最平坦(最小泵效率)部分延伸出直线。在这两条线相交之处,以垂直于通量曲线的切线(最佳切线)的斜率绘制另一条线(垂直于切线)。使用此标绘图(图17),概括区域a至g并定义在表7中。表7:基于在有效脱除、通量和完整性方面的阳极性能得出的最佳%孔隙率范围区域%孔隙率范围脱除效率泵效率生坯强度a(不可透区域)0–10%n/a*n/a*优异b(低泵效率区域)11–21%良好差优异c(活塞流区域)22–29%优异勉强良好d(最佳性能区域)30–42%优异良好良好e(低电阻率区域)43–51%良好良好勉强f(高泵效率区域)52–62%勉强优异勉强g(低生坯强度区域)63–100%差优异差*n/a:由于没有流量,数据不可得。电极在10%孔隙率以下不可透。基于脱除效率、通量和阳极完整性的组合确定表7和图17中的优选和最佳区域。具有不同孔隙率但具有相同质量和面积以及在恒定工艺参数下运行的阳极的脱除效率比较可见于图20。在这一实施例中对脱除效率而言最佳的孔隙率范围在22%至42%之间。在使所有其它运行操作保持恒定的同时在不同流速下进行这一实施例会使该曲线垂直移动。但是,最佳脱除效率范围与实施例3中报道的发现保持一致。通量可与泵效率相关联,这作为通量曲线显示在图17中,且最佳范围规定在表7中。泵效率是由泵施加在流体上的功率与为驱动泵而供给的功率的比率。效率随排量和因此也随运行水头(operatinghead)而变。在实施例3的第一部分中,在保持恒定压力的同时对不同孔隙率的阳极施以不同流速。当保持恒定压力时,阳极孔隙率和流速成正比。具体而言,较高孔隙率的阳极在恒定压力下产生较高的排量,因此需要来自泵的等量马力。因此,较高孔隙率的阳极带来工艺泵的较高效率。各种实施例中所用的阳极尚未烧结。因此,阳极的完整性在此以其生坯强度为代表。阳极在各种孔隙率下的生坯强度可见于表5且最佳范围规定在表7中。阳极的孔隙率与生坯强度成反比。因此,随着孔隙率提高,阳极的完整性变弱。当施加34.5kpa(5psi)的水压时,具有10%或更小孔隙率的阳极不允许被流过。这被定义为不可透区域(区域a)。区域b包括具有极高生坯强度但由于需要的泵输出高而具有降低的整体系统效率的阳极。这一区域由可透阈值(10%孔隙率)和最佳切线与最小泵效率线相交之处(21%孔隙率)界定。由于这一区域中的互连孔隙率降低,存在穿过电极的沟道化(channelized)流。区域c(活塞流区域)中的孔隙率是此时互连孔隙率开始促进穿过阳极的活塞流。这一区域的范围由区域b的范围上限和切线与通量曲线相交的%孔隙率值确定。这一点也是最佳性能区域(区域d)的下限。由最佳切线和最大泵效率线的交点确定最佳性能区域的上限。这一区域是有效脱除、通量和阳极完整性的组合处于最大值的区域并且为30%-42%孔隙率。区域e具有43%-51%的范围。这一区域的上限是穿过阳极的电阻与更多孔的阳极相比显著降低的点并且由最大泵效率线断开通量曲线的点确定。就可透阳极的孔隙率而言,最后界定的范围是52%-62%范围(区域f)。在该区域中,泵性能最有利。但是,阳极的反应性能降低,完整性也如此。阳极在高泵效率区域中存在更快退化的可能性。超过62%孔隙率,阳极生坯强度太低以致无法经受运输、装卸和施加的系统工艺。可透阳极应该具有11-62%,优选22-51%,最优选30-42%的孔隙率。在22-51%的范围内,获得良好至优异的脱除效率,以及至少勉强的泵效率和至少勉强的生坯强度。在30-42%的范围内,获得优异的脱除效率,以及良好的泵效率和良好的生坯强度。这些相应孔隙率范围的最佳ksat值可见于图18a-b。因此,根据本发明的实施方案的方法可在使得ksat的优选区间为4.3至16.4cm/天,最优选7.6至13cm/天的条件下进行。如果将ksat值线移置于在各种孔隙率下的通量曲线上,可如图18a中所示界定优选的ksat范围并且可如图18b中所示界定最佳ksat范围。使用来自表7中的区域d(最佳性能区域)的30–42%的孔隙率范围,具有这一孔隙率范围的阳极的ksat值在7.6–13cm/天之间。当前第1页12