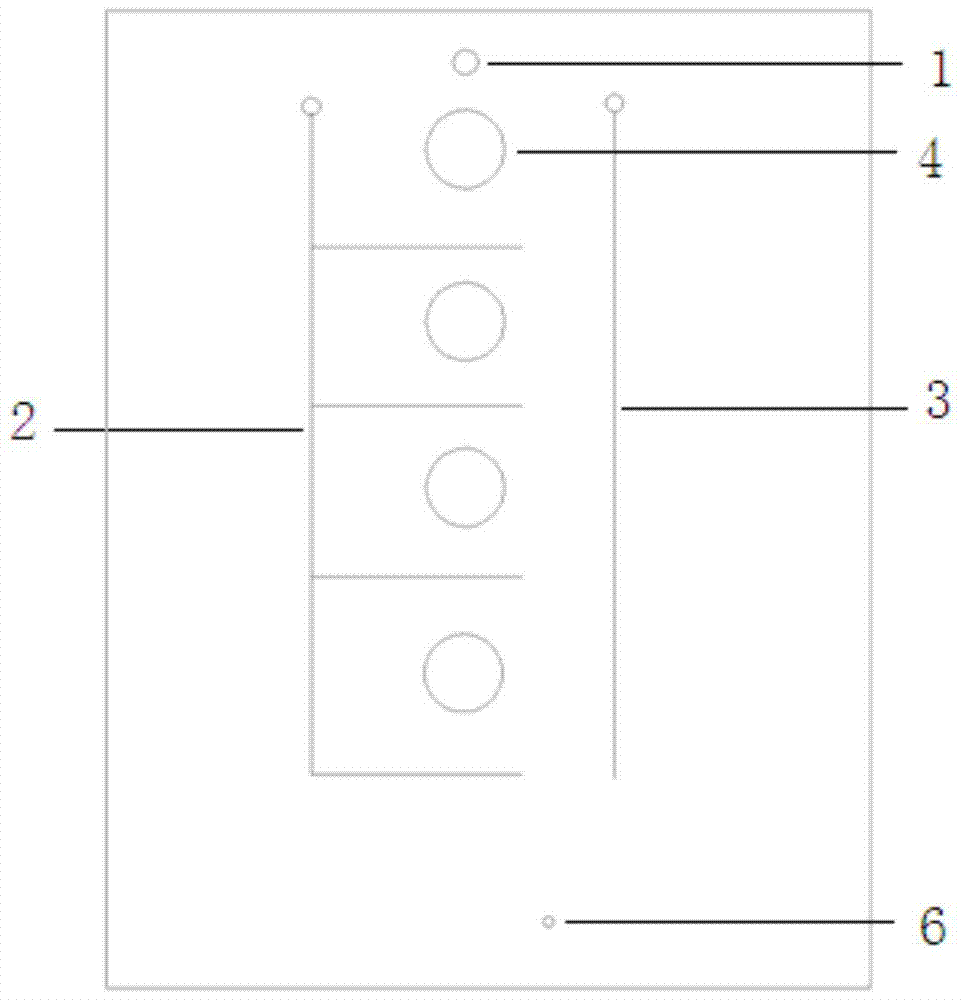
本发明涉及微流控芯片分析领域,尤其涉及一种多指标检测的微流控芯片。
背景技术:微流控芯片又称芯片实验室,指的是一种在一块几平方厘米的芯片上构建的生物或化学实验室。它把生物和化学领域中所涉及的反应、分离、培养、分选、检测等基本操作单元分别做成微/纳米量级的构件,集成到一块很小的芯片上,由微通道形成网络,以可控流体贯穿整个系统,用以实现常规生物或化学的各种功能。以生化样品分析为目的而进行的酶反应、免疫反应、PCR反应、酶联免疫分析等反应都可在微流控芯片上实现。由于微流控芯片技术具有进样量小、集成度高、易实现自动化控制和高通量分析的特点,在微流控芯片上进行生化反应操作较常规的分析而言样品前处理更方便、快速、成本低廉。而且,高特异性的生化反应与微流控芯片强大的分离、检测能力相结合将显示出更为显著的优势。应用微流控芯片进行多指标生化检测时,由于检测指标的多样性,需在芯片上设置多个供检测反应发生的反应池对同一样品进行检测,如何在快速高效的对样品进行多指标检测的同时保证各检测反应的独立进行以及参与各检测反应的样品量一致成为微流控芯片设计中的关键环节。发明专利CN102671729公开了一种用于多指标生化检测的微流控芯片,该芯片包括微流体通道、若干个反应池和气动微阀,反应池内固定有生化反应所需的试剂,若干个反应池通过微流体通道串行或并行连接。虽然该芯片可通过控制气动微阀的开关来实现各反应池之间的连通和隔离,但是在样品进样的流动过程中容易造成反应试剂的交叉污染,样品注入后需要流经多个相连的反应池才能将各反应池充满,通道内液体流速各有差异,导致位置不同的反应池间参与各检测反应的样品量存在较大差异,不利于各检测反应的精确控制及检测结果的准确分析。基于以上背景,发明一种结构简单、操作便捷的支持多指标同时检测,且各指标间不存在交叉污染,各反应池样品量相同的微流控芯片是是十分必要的。
技术实现要素:本发明的目的在于提供一种多指标检测的微流控芯片,同时保证参与各检测反应的样品量相同并且各指标检测反应之间独立发生无交叉污染,实现简便、高效、低成本的多指标检测。为实现上述目的,本发明采用如下技术方案:一种多指标检测的微流控芯片,包括气体控制通道层(100),有机高分子聚合物薄膜(200),微流体通道层(300),各层材料集成键合封接形成芯片结构,其特征在于:气体控制通道层包括进样孔(1)、出气孔(6)和两个气动微阀(2,3)和多个串联储液池(4)的上半部分;有机高分子聚合物薄膜上设有进样孔(1)、气动微阀结构(2,3)、储液池(4)和出气孔(6)对应位置大小的孔;微流体通道层设置多个串联储液池(4)下半部分和多个反应池(9)、连通各储液池(4)间的液体通道(7)、连通储液池(4)和反应池(9)的液体通道(8)。所述的两个微阀(2,3)包括阀座(10,12)和微阀气路通道(11,13),通过控制气压,控制微阀开启关闭,进而控制微流体通道层中液体流向,外界空气进入微阀后,挤压中间层薄膜使之凸起堵塞下层通道,达到控制效果;其中微阀(2)具阀座(10)和多路分支气路通道(11),通道相交设于各储液池(4)连接通道上方,控制各储液池(4)间液体通道(7)开关;微阀(3)具阀座(12)和与之垂直的气路通道(3),相交设置于储液池(4)和反应池(9)连接通道(8)上,控制连接通道(8)的开关。所述气动微阀(2,3)的阀座(10)和(12)可与气体钢瓶或注射器等外源设备相连通,进而向所述微阀气路通道(11)和(13)内提供正、负压。所述的储液池(4)为大小相同,并行串联,液体通道(7)由其最上端接入和接出,最末端连接缓冲池(5),储存过量的样品。所述的微流控芯片材质可选择玻璃、聚二甲基硅氧烷(PDMS)、聚甲基丙烯酸甲酯(PMMA)、聚对苯二甲酸乙二醇酯(PET)或聚碳酸酯(PC)中任何一种。所述的样品储液池(4)上半侧的弹性薄膜的材质可为聚二甲基硅氧烷(PDMS)、硅橡胶、记忆合金或聚四氟乙烯。所述反应池(9)内预先固定有多指标检测所需的试剂,例如酶和底物、抗原或抗体以及PCR引物等,可以通过物理吸附、化学交联、溶胶-凝胶包埋、微珠固定或膜固定等方式进行固定。一种多指标检测的微流控芯片的工作方法,包括如下步骤:步骤一:加样时,微阀(2)开启,微阀(3)关闭。通过阀座(12)向微阀气路通道(13)内通入加压气体,关闭储液池向反应池方向液体通道。样品从进样孔(1)注入,样品流经液体通道(7)流入各样品储液池(4)中,多余的样品流入样品缓冲池(5)中。步骤二:当各样品储液池(4)均充满时,微阀(2)关闭,微阀(3)开启,通过阀座(10)向微阀气路通道(11)内通入加压气体,关闭控制各储液池(4)间液体通道(7)内液体流动的微阀,实现各样品储液池(4)间的隔离;打开控制各样品储液池与对应的反应池的液体通道的微阀,按压各样品储液池(4)上方的弹性薄膜,使样品从各样品储液池(4)中流入对应的反应池(9)中,样品流入反应池(9)后与预先固定在反应池(9)中的多指标检测用试剂进行反应。有益效果本发明提供了一种多指标检测的微流控芯片,基于微流控芯片技术平台,集样品进样、多指标检测于一体,检测时只需结合进样装置注入样品,利用外加的气源控制微阀的开启与闭合,手动或其他方式按压腔壁即可实现检测,结构简单,使用方便,成本低廉;利用多个串行连接的相同大小的样品储液池使参与各检测反应的样品量相同,样品储存与反应设在不同的区域,利用集成的气动微阀使各反应池形成独立的反应区域,避免了样品进样及反应过程中由液体流动造成的试剂污染及相互干扰,提高了参与检测反应样品量的精度,保证了检测结果的可靠性。附图说明图1多指标检测芯片整体示意图。图2多指标检测芯片中的上层气体控制通道层结构示意图。图3多指标检测芯片中的中间层PDMS薄膜结构示意图。图4多指标检测芯片中的下层微流体通道层结构示意图。图5多指标检测芯片中整体结构组成示意图。图6多指标检测芯片中的微阀开启与关闭示意图。1为进样孔,2为储液池气动微阀,3为反应池气动微阀,4为样品储液池,5为样品缓冲池,6为出气孔,7为储液池液体通道,8为反应池液体通道,9为反应池,10为储液池微阀阀座,11储液池微阀气路通道,12为反应池微阀阀座,13为反应池微阀气路通道,100为气体控制通道层,200为有机高分子聚合物薄膜,300为微流体通道层。具体实施方式下面的实例对本发明做进一步说明,该实例仅是本发明装置的实施方式之一,并不对本发明做出任何限制。实施例一:微流控芯片结构如图1、2、3、4、5所示:一种用于多生化指标检测的微流控芯片,由集成了微阀的芯片材料键合封接而成,包括气体控制通道层100,有机高分子聚合物薄膜200,微流体通道层300,其中:气体控制通道层100上设有样品进样孔1、出气孔6、两个气动微阀2、3及多个串联样品储液池4的上半部分,样品储液池4的上半部分的一侧为弹性薄膜且暴露于空气中;微流体通道层300包括连通进样孔与各样品储液池的液体通道7、连通各样品储液池与对应的反应池的液体通道8、样品储液池的下半部分,与样品注入通道末端连通的样品缓冲池5以及反应池9,反应池内固定有多指标检测用的反应试剂;有机高分子聚合物薄膜200夹于气体控制通道层100与微流体通道层300之间,薄膜上对应进样孔1、阀座10和12、出气孔6及样品储液池4的位置设有相应大小的孔;上述的用于多指标检测的微流控芯片中,所述的微流控芯片的材质为PC、PDMA、PMMA、PET中的一种,本实施例选用材料为PC,控制通道层的厚度为3~5mm,液体通道层的厚度为120~180um(根据实际情况可改变不同厚度大小);上述的用于多指标检测的微流控芯片中,所述样品储液池4上半部分侧壁的的弹性薄膜的材质为硅橡胶、PDMS、、记忆合金或聚四氟乙烯中的一种,本实施例选用硅橡胶,弹性薄膜的厚度为60~100um;上述的用于多指标检测的微流控芯片中,所述气动微阀12的阀座2和11与气体注射器相连通,进而可向所述微阀气路通道3和10内通入加压气体,使薄膜14发生弹性形变,薄膜的厚度为60~100um;上述的用于多指标检测的微流控芯片中,所述4个反应池9内分别预先固定有用于4种生化指标检测所需的酶和底物;进样孔的横截面为圆形,直径为0.75mm;出气孔的横街面为圆形,直径为0.3mm;样品储液池的横截面为圆形,直径为7.5mm,高度为0.2mm;反应池的横截面为椭圆形,直径为15mm×8mm,高度为0.2mm;样品缓冲池为矩形,长10mm,宽6mm,高度为0.2mm;液体通道高100um,宽300um,横截面为半圆形;气体控制通道高100um,宽300um,横截面为半圆形,上述数据仅限于本实施例,本发明并不局限于本实施例中数据,在其他实施例中数据依实际情况可适当调整变化。实施例二:微流控芯片工作流程步骤一:加样时,微阀2开启,微阀3关闭,通过阀座12向微阀气路通道13内通入加压气体,关闭储液池向反应池方向液体通道,样品从进样孔1注入,样品流经液体通道7流入各样品储液池4中,多余的样品流入样品缓冲池5中;步骤二:当各样品储液池4均充满时,微阀2关闭,微阀3开启,通过阀座10向微阀气路通道11内通入加压气体,关闭控制各储液池4间液体通道7内液体流动的微阀,实现各样品储液池4间的隔离;打开控制各样品储液池与对应的反应池的液体通道的微阀,按压各样品储液池4上方的弹性薄膜,使样品从各样品储液池4中流入对应的反应池9中,样品流入反应池9后与预先固定在反应池9中的多指标检测用试剂进行反应。实施例三:微流控芯片制作方法(一)制备具有微流控芯片上微结构的模具用计算机辅助设计软件设计微流控芯片的微通道与微结构,根据设计图用铬版分别制作气体控制通道层及微流体通道层的掩模版。选用硅片进行光刻和蚀刻制作模具,首先,将硅片清洗干净,清洗干净的硅片用氮气吹干之后放到匀胶机上,取适量光刻胶涂于硅片上,启动匀胶机甩涂光刻胶,将掩膜版置于涂有光刻胶的硅片上后置于光刻机中进行曝光,经过显影和后烘工艺之后利用干法刻蚀得到具有上层气体控制通道层及下层微流体通道层的微结构的模具。(二)热压法制作芯片将PDMS、PMMA、PET、PC片材中一种(本实施例选PC)按模具尺寸裁成小片,洗净,烘干后置于模具上,热压机上在180℃,加1000lb压力4.5min,脱模,分别制得具有微流体通道和气体控制通道的PC芯片。(三)将聚二甲基硅氧烷(PDMS)、硅橡胶、记忆合金或聚四氟乙烯中一种(本实施例使用PDMS)预聚体及固化剂按体积比为10:1的比例混合,将混合液浇在与芯片相同大小的玻璃几片上,升温交联2小时后,形成弹性好的厚度为80um的PDMS薄膜。(四)用超声波打孔机在步骤(二)得到的上层气体控制通道层及下层微流体通道层PC芯片上的相应位置进行超声钻孔,得到进样孔、阀座和出气孔,在步骤(三)制得的的PDMS薄膜上超声钻孔,获得与进样孔、样品储液池及出气孔位置大小相同的孔。(五)步骤(四)得到的上下PC芯片放入等离子清洗机真空轰击1min,迅速在下层微流体通道层上的反应池中装载各个反应的试剂,迅速将步骤(四)得到的PDMS置于上层气体控制通道层及下层微流体通道层之间,将步骤(三)得到的PDMS薄膜裁剪为直径大于样品储液池大小,置于上层气体控制通道层上的对应位置,进行不可逆封接得到集成了微阀的微流控芯片。