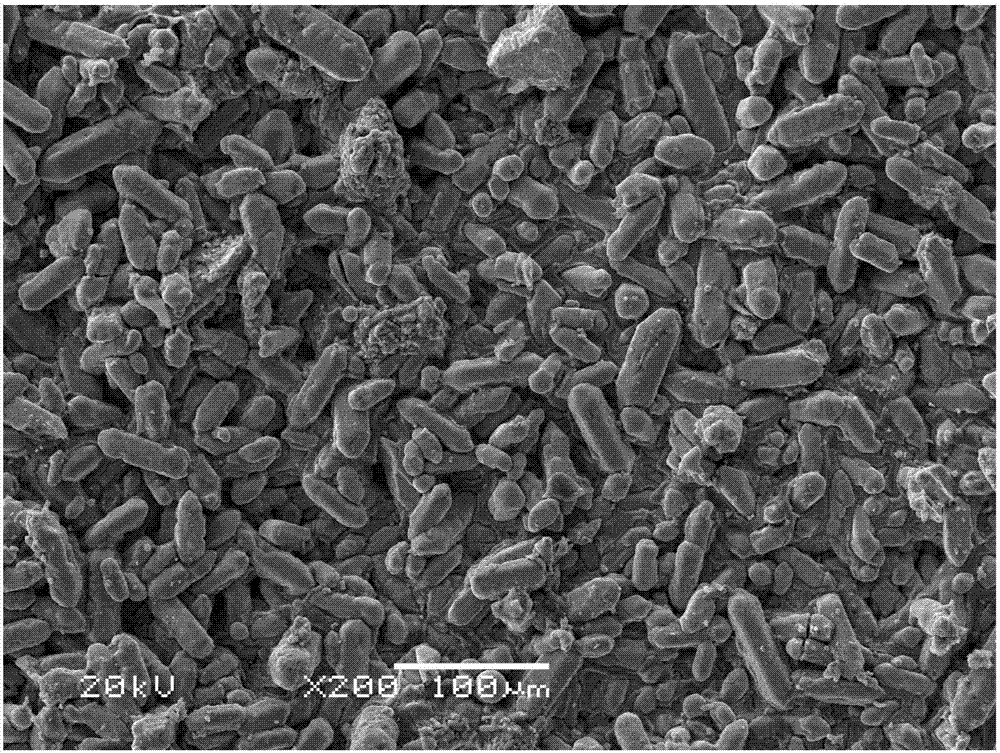
本发明涉及涂层
技术领域:
,尤其涉及一种钼基复合涂层及其制备方法。
背景技术:
:钼属于难熔金属,具有高熔点和高强度的优点,应用于航空航天、化工、冶金、医疗器械等多个领域。但钼及其合金在高温有氧环境下会发生剧烈的破坏性氧化而失效破坏,严重限制了钼及其合金在高温环境下的使用。在钼、钼合金表面涂覆抗氧化涂层,可以最大程度保有合金力学性能,同时大幅提高钼合金抗氧化温度,是一种经济、有效的防护手段。目前,高温抗氧化涂层包括硅化物涂层、铝化物涂层以及耐热合金涂层等,均能一定程度提高钼的工作温度和抗氧化性能。申请号为201110383828.6的中国专利介绍了三步原位反应合成法生成涂层的方法,首先在高温下对基材通氮气使其氮化,再经过高温包埋渗硅,最后再高温包埋渗硼,制得一种Mo-N-Si-B系的抗氧化涂层。申请号为201310180081.3的中国专利先对预处理的钼基材表面进行渗钨处理,然后进行氮化处理,最后高温渗硅,得到一种Mo-W-N-Si系硅化物涂层。申请号为201410733680.8的中国专利介绍了一种主要组成为:Al为15~20wt%,Ni为3~5wt%,W为2~3wt%,MoSi2为1.5~3wt%,Cr为0.5~0.8wt%,余量为Si的抗氧化涂层材料,采用真空料浆法制备。申请号为201410208597.9的中国专利公开了一种Hf-Y氧化物涂层,使用氯氧化铪与氯化钇以适量的比例混合溶于正丙醇溶液,刷涂在钼基材表面,然后置于马弗炉中在400℃左右焙烧,经15~30次刷涂-烧结后形成涂层。申请号为201510441949.X的中国专利公开了采用掺钾钼作为发热体基体材料,对发热体基体表面包埋于硅10~30wt%,硼、铝、铬、钨粉末中的至少一种粉末5~10wt%,余量为氧化铝的反应粉末中进行元素扩散反应制备出涂层钼发热体。此外,贾中华等使用料浆熔烧法,在钼表面熔烧制备硅化物防护涂层。肖来荣等通过真空烧结法,在钼表面烧结出MoSi2-ZrB2涂层。汤德志使用磁控溅射技术,在钼表面制备硅铝涂层。汪异采用大气等离子喷涂法和原位化学气相沉积法在钼表面制备二硅化钼涂层和二硅化钼/硼化钼复合涂层。马小冲等采用料浆法在钼基体上制备ZrO2和SnO2玻璃基抗氧化涂层。此外,王亮兵使用双辉离子镀法在钼基体上制备Ir涂层。上述专利与文献所记载的涂层材料中,包埋法制备涂层对过程要求苛刻,控制难度大;磁控溅射对设备要求较高,经济性差;刷涂-烧结法简单易行,容易控制,但制备的Hf-Y氧化物涂层对基体的保护时间短。双辉离子镀法目前仍处于研究阶段,所制备的Ir涂层成本昂贵,且目前测试寿命仅有60s(2000℃)。如上所述,目前仍缺乏一种可以使用在1600℃以上,具有长寿命、低成本、便于实施和控制的涂层材料及其制备方法。技术实现要素:本发明解决的技术问题在于提供一种钼基复合涂层,本申请提供的复合涂层使钼基材的工作温度与抗氧化效果大幅度提高。有鉴于此,本申请提供了一种钼基复合涂层,包括:钼基材,复合于钼基材表面的硅化物底层;复合于所述硅化物底层表面的硅酸盐外层;所述硅化物底层由以下组分制备得到:5~12wt%的W,2~7wt%的Cr,0.3~6wt%的B、B2O3或B4C,0.5~7wt%的HfO2;下述组分中的至少一种:1~5wt%的Mo,0.5~1.5wt%的Ta,1~4wt%的Fe,0.5~1.5wt%的S,0.2~0.5wt%的TiB2,1~5wt%的SiC,1~5wt%的ZrO2或Zr,1~5wt%的MoSi2;余量的Si;所述硅酸盐外层由以下组分制备得到:3~18wt%的Mo,0.5~5wt%的W,0.5~3wt%的Nb,1~5wt%的HfO2;下述组分中的至少一种:0.2~2wt%的Ta或其氧化物,0.2~1.5wt%的V,0.7~1.5wt%的La或其氧化物,0.3~2.2wt%的Y或其氧化物,0.2~1wt%的BaO,0.7~4wt%的Ge或其氧化物,1~7wt%的Zr或其氧化物,1~5wt%的B或其氧化物;余量的Si。优选的,所述硅化物底层中,所述Cr的含量为5.5~7wt%;所述B、B2O3或B4C的含量为3~6wt%;所述HfO2的含量为5.5~7wt%。优选的,所述硅酸盐外层中,所述Mo的含量为16~18wt%,所述W的含量为3.5~4wt%。优选的,所述复合涂层的厚度为80~130μm。优选的,钼基材的材质为纯钼或钼合金。本申请还提供了所述的钼基复合涂层的制备方法,包括以下步骤:A),将权利要求1中硅化物底层中的各种组分混合,得到第一抗氧化材料;将权利要求1中硅酸盐外层中的各种组分混合,得到第二抗氧化材料;将所述第一抗氧化材料、有机溶剂、粘结剂与反应催化剂混合,球磨后得到第一涂层浆料;将所述第二抗氧化材料、有机溶剂、粘结剂与反应催化剂混合,球磨后得到第二涂层浆料;B),将所述第一涂层浆料涂覆于预处理后的钼基材表面,熔烧后保温,得到硅化物底层;C),将第二涂层浆料涂覆于所述硅化物底层表面,熔烧后保温,得到硅酸盐外层。优选的,得到第一涂层浆料的步骤中,所述有机溶剂为乙酸乙酯或无水乙醇,所述粘结剂为硝基清漆或聚乙二醇,所述反应催化剂为卤化物;得到第二涂层浆料的步骤中,所述有机溶剂为乙酸乙酯或无水乙醇,所述粘结剂为硝基清漆或聚乙二醇,所述反应催化剂为卤化物。优选的,所述第一抗氧化材料与所述有机溶剂的体积比为1:(1~2),所述第一抗氧化材料与所述硝基清漆的质量比为1:(0.5~2),所述第一抗氧化材料与所述聚乙二醇的质量比为1:(0.01~0.06),所述第一抗氧化材料与所述卤化物的质量比为1:(0.003~0.03);所述第二抗氧化材料与所述有机溶剂的体积比为1:(1~2),所述第二抗氧化材料与所述硝基清漆的质量比为1:(0.5~2),所述第二抗氧化材料与所述聚乙二醇的质量比为1:(0.01~0.06),所述第二抗氧化材料与所述卤化物的质量比为1:(0.003~0.03)。优选的,步骤B)中,所述熔烧的温度为1300~1550℃,真空度大于0.1Pa;保温时间为15~60min。优选的,步骤C)中,所述熔烧的温度为1350~1550℃,真空度大于0.1Pa,保温时间为15~60min。本申请提供了一种钼基复合涂层,所述钼基复合涂层中包括硅化合物底层与硅酸盐外层,本申请通过采用两组配比不同的涂层材料,得到了高熔点、高致密度的陶瓷-玻璃相外层,其使钼基材工作温度与抗氧化效果大幅度提升;进一步的,硅化物底层与硅酸盐外层的不同成分使形成的涂层的热胀系数呈现梯度变化,使硅化物底层与钼基材产生了冶金结合,确保涂层与基材结合牢固,使涂层在急冷急热环境下工作。实验结果表明,本申请的复合涂层可在1700℃下提供100h以上的抗氧化防护,在1800~室温热震性能可达1000次以上。附图说明图1为本发明复合涂层制备过程流程图;图2为本发明实施例1制备的复合涂层的表面微观形貌图;图3为本发明实施例1制备的复合涂层的截面微观形貌图;图4为本发明实施例1制备的复合涂层在1800℃静态测试50h后涂层的EDS分析;图5为本发明实施例1制备的复合涂层在1800℃测试50h后表面形成的陶瓷-玻璃相照片;图6为本发明实施例3制备的复合涂层1800℃下静态测试30h后的截面形貌照片。具体实施方式为了进一步理解本发明,下面结合实施例对本发明优选实施方案进行描述,但是应当理解,这些描述只是为进一步说明本发明的特征和优点,而不是对本发明权利要求的限制。本发明实施例公开了一种钼基复合涂层,包括:钼基材,复合于钼基材表面的硅化物底层;复合于所述硅化物底层表面的硅酸盐外层;所述硅化物底层由以下组分制备得到:5~12wt%的W,2~7wt%的Cr,0.3~6wt%的B、B2O3或B4C,0.5~7wt%的HfO2;下述组分中的至少一种:1~5wt%的Mo,0.5~1.5wt%的Ta,1~4wt%的Fe,0.5~1.5wt%的S,0.2~0.5wt%的TiB2,1~5wt%的SiC,1~5wt%的ZrO2或Zr,1~5wt%的MoSi2;余量的Si;所述硅酸盐外层由以下组分制备得到:3~18wt%的Mo,0.5~5wt%的W,0.5~3wt%的Nb,1~5wt%的HfO2;下述组分中的至少一种:0.2~2wt%的Ta或其氧化物,0.2~1.5wt%的V,0.7~1.5wt%的La或其氧化物,0.3~2.2wt%的Y或其氧化物,0.2~1wt%的BaO,0.7~4wt%的Ge或其氧化物,1~7wt%的Zr或其氧化物,1~5wt%的B或其氧化物;余量的Si。本申请提供了一种钼基复合涂层,其包括依次复合的硅酸盐外层、硅化物底层与钼基材,本申请通过调整钼基材外层与底层组分及其含量,使底层与钼基材能够形成良好的冶金结合,保证复合涂层不脱落,同时形成的复合涂层形成高熔点、高致密的陶瓷-玻璃相外层,使钼基材的工作温度与抗氧化效果大幅度提升。在形成的硅化物底层中,所述W的含量为5~12wt%,在某些实施例中,所述W的含量为7~12wt%,示例的,所述W的含量为7wt%、7.8wt%、8.1wt%、8.5wt%、9.0wt%、9.8wt%、10.0wt%、10.7wt%、11.2wt%或11.6wt%。所述Cr的含量为2~7wt%,在实施例中,所述Cr的含量为5.5~7wt%,示例的,所述Cr的含量可为6.0wt%、6.2wt%、6.5wt%、6.8wt%或7wt%。所述B、B2O3或B4C的含量为0.3~6wt%,在实施例中,所述B、B2O3或B4C的含量为2.5~6wt%,示例的,所述B、B2O3或B4C的含量为2.5wt%、3.2wt%、3.7wt%、4.3wt%、4.7wt%、5.0wt%、5.4wt%或6wt%。所述HfO2的含量为0.5~7wt%,在实施例中,所述HfO2的含量为2~7wt%,示例的,所述HfO2的含量为2.6wt%、3.0wt%、3.2wt%、3.8wt%、4.5wt%、5.2wt%、6.8wt%或7.0wt%。在所述硅化物底层中,所述W、Cr、B或其化合物、HfO2与Si为主要必要添加元素,除此之外,可根据具体形成的硅化物底层选择添加1~5wt%的Mo,0.5~1.5wt%的Ta,1~4wt%的Fe,0.5~1.5wt%的S,0.2~0.5wt%的TiB2,1~5wt%的SiC,1~5wt%的ZrO2或Zr与1~5wt%的MoSi2中的至少一种。在上述元素中,可添加其中的一种组分,或添加多种组分,可根据具体的形成的硅化物底层的性质进行选择。在具体的实施例中,所述Mo的含量为1.5~4.0wt%,更具体的,所述Mo的含量为1.8wt%、2.4wt%、3.0wt%、3.2wt%、3.5wt%或4.0wt%。在具体实施例中,所述Ta的含量为0.8wt%~1.2wt%。在具体实施例中,所述Fe的含量为1.5~3.0wt%。在具体实施例中,所述S的含量为1~1.5wt%。在具体实施例中,所述TiB2的含量为0.2wt%、0.3wt%、0.4wt%或0.5wt%。在具体实施例中,所述SiC的含量为2.5~4.0wt%,具体的,所述SiC的含量为2.8wt%、3.2wt%、3.5wt%或3.8wt%。在具体实施例中,所述ZrO2的含量为1.8~4.2wt%,具体的,所述ZrO2的含量为2.0wt%、2.2wt%、2.8wt%、3.4wt%、3.8wt%或4.0wt%。在具体实施例中,所述MoSi2的含量为1.6wt%~4.2wt%,具体的,所述MoSi2的含量为2.0wt%、2.4wt%、2.8wt%、3.4wt%或4.0wt%。涂层底层中添加了较多的活化元素,其作用是形成高硅化物,在高温下分解形成单质硅和低硅化合物,硅元素向表层跃迁,为表层提供抗氧化元素,从而起到“储备层”的作用;部分非金属元素的作用是在高温下腐蚀钼及钼合金基材表面,提高基材比表面积,用以提高涂层与合金的反应程度,提升涂层与合金的结合力。此外,添加了部分的强化元素或化合物,以提升涂层强度,调整涂层弹性模量,提升涂层抗热震能力,提高涂层的环境适应能力。在形成的硅酸盐外层中,所述Mo的含量为3~18wt%,在具体实施例中,所述Mo的含量为6~18wt%,在某些具体实施例中,所述Mo的含量为10~17wt%,具体的,所述Mo的含量为12wt%、15wt%、16.2wt%、17wt%或18wt%。所述W的含量为0.5~5wt%,在某些实施例中,所述W的含量为2~5wt%,在某些实施例中,所述W的含量为3.5~5wt%,具体的,所述W的含量为3.5wt%、3.8wt%、4.0wt%、4.2wt%或4.8wt%。所述Nb的含量为0.5~3wt%,在某些实施例中,所述Nb的含量为1~2.5wt%,具体的,所述Nb的含量为1.2wt%、1.5wt%、2.0wt%或2.2wt%。所述HfO2的含量为1~5wt%,在某些实施例中,所述HfO2的含量为1.2~3.8wt%,在某些实施例中,所述HfO2的含量为1.8~2.5wt%。在所述硅酸盐外层中,所述W、Mo、Nb、HfO2与Si为主要必要添加元素,除此之外,可根据具体形成的硅酸盐外层选择添加0.2~2wt%的Ta或其氧化物,0.2~1.5wt%的V,0.7~1.5wt%的La或其氧化物,0.3~2.2wt%的Y或其氧化物,0.2~1wt%的BaO,0.7~4wt%的Ge或其氧化物,1~7wt%的Zr或其氧化物与1~5wt%的B或其氧化物中的至少一种;在上述元素中,可添加其中的一种组分,或添加多种组分,可根据具体的形成的硅酸盐外层的性质进行选择。在具体实施例中,所述Ta或氧化物的含量为2wt%~2.8wt%。在具体实施例中,所述V的含量为1.2~1.5wt%。在具体的实施例中,所述La或其氧化物的含量为0.8~1.5wt%,更具体的,所述La或其氧化物的含量为0.9wt%、1.2wt%、1.4wt%或1.5wt%。在具体实施例中,所述Y或其氧化物的含量为0.8~2.2wt%,具体的,所述Y或其氧化物的含量为1.0wt%、1.2wt%、1.8wt%或2.0wt%。在具体实施例中,所述BaO的含量为0.4~0.9wt%。在具体实施例中,所述Ge或其氧化物的含量为1.2~3.6wt%,在具体实施例中,所述Ge或其氧化物的含量为2.0~3.0wt%。在具体实施例中,所述Zr或其氧化物的含量为3~6.8wt%,具体的,所述ZrO2的含量为3.2wt%、4.5wt%、4.8wt%、5.6wt%、6.5wt%或6.8wt%。在具体实施例中,所述B或其氧化物的含量为1.2wt%~4.5wt%,具体的,所述B或其氧化物的含量为1.4wt%、1.6wt%、2.8wt%、3.4wt%或4.2wt%。复合涂层在大气下遭遇高温环境,外层升温氧化的过程中部分金属元素的硅化物氧化后,可以形成高熔点的金属硅酸盐,与SiO2形成陶瓷-玻璃相,提升面层的高温稳定性;部分非金属、金属氧化物可以降低SiO2的软化温度,提高面层抗热冲击的能力。此外,部分金属元素的添加及硅化物的形成,起到调整面层热膨胀系数的作用。本申请还提供了上述钼基复合涂层的制备方法,制备流程如图1所示,具体的,所述钼基复合涂层的制备包括以下步骤:A),将权利要求1中硅化物底层中的各种组分混合,得到第一抗氧化材料;将权利要求1中硅酸盐外层中的各种组分混合,得到第二抗氧化材料;将所述第一抗氧化材料、有机溶剂、粘结剂与反应催化剂混合,球磨后得到第一涂层浆料;将所述第二抗氧化材料、有机溶剂、粘结剂与反应催化剂混合,球磨后得到第二涂层浆料;B),将所述第一涂层浆料涂覆于预处理后的钼基材表面,熔烧后保温,得到硅化物底层;C),将第二抗氧化浆料涂覆于所述硅化物底层表面,熔烧后保温,得到硅酸盐外层。在制备钼基复合涂层的过程中,本申请首先进行复合涂层中原料组分的配制,即首先将硅化物底层与硅酸盐外层中的各种组分按照上述比例分别进行混合,分别得到第一抗氧化材料与第二抗氧化材料;再将得到的第一抗氧化材料与第二抗氧化材料均分别与有机溶剂、粘结剂、反应催化剂混合,球磨后,分别得到第一涂层浆料与第二涂层浆料。在上述过程中,所述有机溶剂作为载体,用于调整涂层浆料的粘度和流动性,从而提升浆料的涂覆均匀性,并且可实现快速干燥固化。所述有机溶剂优选为无水乙醇或乙酸乙酯。所述粘结剂优选为硝基清漆或聚乙二醇,所述反应催化剂优选为卤化物,具体的,所述卤化物为NH4Cl、NaF、NaCl、KF、KCl中的一种或多种。所述第一抗氧化材料与所述有机溶剂的体积比为1:(1~2),所述第一抗氧化材料与所述硝基清漆的质量比为1:(0.5~2),优选为1:(0.8~1.2),所述第一抗氧化材料与所述聚乙二醇的质量比为1:(0.01~0.06),所述第一抗氧化材料与所述卤化物的质量比为1:(0.003~0.03);所述第二抗氧化材料与上述添加剂的比例与第一抗氧化材料的范围相同,在具体实施例中,所述第一抗氧化材料与第二抗氧化材料分别与上述添加剂的比例可以相同,也可以不同,对此本申请没有特别的限制。所述球磨的转速为150~400r/min,球磨的时间为3~12h;在具体实施例中,在制备第一涂层浆料的过程中,所述球磨的转速为150~300r/min,球磨的时间为8~10h,在制备第一涂层浆料的过程中,所述球磨的转速为180~320r/min,球磨的时间为8~10h。在涂覆第一涂层浆料之前,本申请优选将钼基材进行了预处理,所述预处理为本领域技术人员熟知的技术手段,此处不进行特别的限制,示例的,所述预处理可以为打磨、喷砂、酸洗或真空退火。本申请所述钼基材的材质为纯钼或钼合金,其中,所述钼合金为本领域技术人员熟知的钼合金,对此本申请没有特别的限制。按照本发明,首先将所述第一涂层浆料涂覆于钼基材表面,熔烧后保温,得到硅化物底层。所述熔烧的温度为1300~1550℃,真空度大于0.1Pa;保温时间为15~60min;在具体实施例中,所述熔烧的温度为1350~1500℃,所述保温时间为45~60min。在得到硅化物底层之后,本申请则在其表面涂覆所述第二抗氧化涂层浆料,熔烧后保温,得到硅化物底层。所述熔烧的温度为1300~1550℃,真空度大于0.1Pa;保温时间为15~60min;在具体实施例中,所述熔烧的温度为1350~1500℃,所述保温时间为45~50min。在熔烧过程中,底层、外层配料中的部分金属与硅生成固溶体,部分金属、金属氧化物则与硅反应生成硅化物及硅酸盐,从而形成固溶体、硅化物以及硅酸盐的复杂混合体。有别于Ta、Nb等金属,同为难熔金属的Mo与其主要硅化物MoSi2的线膨胀系数(CET)相差极大(Mo为5.2×10-6/℃,MoSi2为8.1×10-6/K),因此与Nb、Ta金属及合金抗氧化涂层不同,钼及钼合金对抗氧化涂层的改性成分和结构层设计(层数、结构层厚度)要求更高,否则很容易因热胀系数匹配失当或是成分固溶不良导致涂层出现开裂、剥落或者表面凸起等质量缺陷。本申请所提供的钼及钼合金用高温抗氧化涂层材料及其制备方法的特点和优势在于:使用两组配比不同的涂层材料,采用二次叠加熔烧的方法,制备出一种复合涂层。这种复合涂层高温下表面可以形成高度致密化和稳定化的复杂陶瓷-玻璃膜层,解决了钼及钼合金硅化物涂层普遍存在的1500℃以上的快速挥发失效问题,有效提升涂层工作温度;同时底层、面层的不同成分设计使涂层的热胀系数呈现梯度变化,解决了钼及钼合金传统硅化物涂层因涂层主体MoSi2与基体Mo热胀系数相差过大导致的涂层起皮、剥落和开裂等致命缺陷,有效提升涂层性能;此外,在叠加熔烧的过程中,通过调整熔烧工艺,可以实现面层与底层、底层与合金的轻度热扩散,从而形成冶金级结合,提升涂层层间结构、涂层与合金间的结合力,避免涂层在冷热交变工况下的开裂甚至剥落,进一步提升涂层的实际工作能力。为了进一步理解本发明,下面结合实施例对本发明提供的复合涂层及其制备方法进行详细说明,本发明的保护范围不受以下实施例的限制。实施例11)两组高温抗氧化材料,分别为:①W为5wt%,Cr为2wt%,B为2wt%,Ta为1.2wt%,Mo为1wt%,HfO2为2wt%,ZrO2为3wt%,SiC为2.8wt%,余量为Si;②Mo为7.2wt%,W为2.2wt%,Nb为3wt%,Y为2.2wt%,HfO2为3wt%,BaO为1wt%,Ta为2wt%,B为3wt%,余量为Si;将上述两组材料按比例混匀,分别使用行星式球磨机研磨成不大于300目的粉料,装入不同的容器;2)用喷砂的方法清洁钼基材表面(设备为长空牌GS-943型吸入式干喷砂机,80目白刚玉砂),然后浸入无水乙醇浸泡30min,晾干备用;3)在第①组抗氧化材料中分别加入粉末质量80wt%的硝基清漆(浙江油漆有限公司,宝塔牌硝基清漆)和3wt%的NaF分别作为粘结剂和催化剂,再加入粉末体积2倍的乙酸乙酯作为载体,混合均匀后用刚玉珠以150r/min转速球磨12h后制成料浆;将料浆均匀涂覆在钼基材表面,烘干后在温度1380℃,真空度≥0.1Pa的条件下熔烧,保温60min,制成抗氧化涂层底层,厚度约65~80μm;4)在第②组抗氧化材料中分别加入粉末质量120wt%的硝基清漆(浙江油漆有限公司,宝塔牌硝基清漆)和2wt%的KF分别作为粘结剂和催化剂,再加入粉末体积2倍的乙酸乙酯作为载体,混合均匀后用刚玉珠以200r/min转速球磨10h后制成料浆;将料浆均匀涂覆在抗氧化涂层底层表面,烘干后在温度1550℃,真空度≥0.1Pa的条件下熔烧,保温50min,制成抗氧化涂层面层,厚度约25~35μm;最终成型的复合型抗氧化涂层,整体厚度在90~120μm。图2为本发明实施例1制备的复合涂层的表面微观形貌图;图3为本发明实施例1制备的复合涂层的截面微观形貌图;如图2与图3可知,使用两种抗氧化材料制备的钼涂层呈典型的蜂窝状结构,整体结构致密,颗粒弥散;涂层呈典型的复合型三层结构,面层较为疏松,底层极为致密,并与合金有一定的互扩散,从而提高了涂层与合金的结合力。5)抗氧化涂层的抗氧化能力测试方法为:钼试样进行1800℃高温测试,测试方法为:使用铜电极对试样进行通电,利用其自身电阻产生热量使试样升温;使用美国Raytek公司的B17MR1SBSF型双色集成式测温仪(测温范围600~2100℃,测温精度±15.75℃)测定试样温度,使用日本SHIMADEN公司的FP23温控表控制通过试样的电流大小进而控制温度(±10℃),测试至试样表面出现黑色斑点时,涂层失效;对失效试片进行EDS分析,仪器型号ZeissSUPRA55,结果如4所示,图4为本发明实施例1制备的复合涂层在1800℃静态测试50h后涂层的EDS分析;由图4可知,抗氧化涂层1800℃静态测试50h以后,涂层中的氧元素升高,但基材中的氧元素含量很低,证明涂层对基材起到了很好的抗氧化效果。对涂层进行1700℃、1800℃高温抗氧化性能测试,如图5所示,测试结果显示,涂层在高温下表面能生成深黑色玻璃-陶瓷相保护层,可有效阻挡氧元素的侵入,使得涂层具有良好的静态、热震抗氧化能力较好,结果表1所示。表1抗氧化涂层综合性能测试数据表实施例21)两组高温抗氧化材料,分别为:①W为7wt%,Cr为7wt%,B2O3为2.5wt%,Fe为3wt%,S为1wt%,Mo为5wt%,HfO2为4wt%,SiC为3wt%,MoSi2为2.8wt%,余量为Si;②Mo为12wt%,W为3.5wt%,Nb为1wt%,Y2O3为0.8wt%,HfO2为3wt%,BaO为0.7wt%,V为1.2wt%,B为1wt%,余量为Si;将上述两组材料按比例混匀,分别使用行星式球磨机研磨成不大于300目的粉料,装入不同的容器;2)将TZM合金(钼锆钛合金)基材表面用400#砂纸打磨至表面光亮无异物附着,再用无水乙醇浸泡30min,晾干后备用;3)在第①组抗氧化材料中分别加入粉末质量150wt%的硝基清漆(浙江油漆有限公司,宝塔牌硝基清漆)和3wt%的NaF分别作为粘结剂和催化剂,再加入粉末体积2倍的乙酸乙酯作为载体,混合均匀后用刚玉珠以150r/min转速球磨8h后制成料浆,将料浆均匀涂覆在TZM基材表面,烘干后在温度1360℃,真空度≥0.1Pa的条件下熔烧,保温60min,制成抗氧化涂层底层,厚度约75~85μm;4)在第②组抗氧化材料中分别加入粉末质量120wt%的硝基清漆(浙江油漆有限公司,宝塔牌硝基清漆)和3wt%的KF分别作为粘结剂和催化剂,再加入粉末体积2倍的乙酸乙酯作为载体,混合均匀后用刚玉珠以180r/min转速球磨8h后制成料浆;将料浆均匀涂覆在抗氧化涂层底层表面,烘干后在温度1500℃,真空度≥0.1Pa的条件下熔烧,保温45min,制成抗氧化涂层面层,厚度约20~30μm。最终成型的复合型抗氧化涂层,整体厚度在95~115μm。实施例31)两组高温抗氧化材料,分别为:①W为10%wt%,Cr为4wt%,B4C为2wt%,HfO2为4wt%,Ta为1wt%,Mo为5wt%,S为1.2Wt%,TiB2为0.5wt%,ZrO2为3wt%,余量为Si;②Mo为15wt%,W为3.5wt%,Nb为0.5wt%,HfO2为5wt%,La2O3为1.2wt%,Y为1wt%,Zr2O3为7wt%,余量为Si;将上述两组材料按比例混匀,分别使用行星式球磨机研磨成不大于300目的粉料,装入不同的容器;2)使用干式喷砂机,使用300#白刚玉砂对钼金属基材进行喷砂,至表面光亮无异物附着,表面粗糙度不大于Ra6.3μm(样板对比法),以20~30KHz频率对试样进行超声波清洗,清洗时间15~20分钟,清洗后将试片浸入无水乙醇备用。3)在第①组抗氧化材料中分别加入粉末质量5wt%的聚乙二醇和1wt%的KCl作为粘结剂和催化剂,再加入粉末体积2倍的无水乙醇作为载体,混合均匀后用刚玉珠以200r/min转速球磨12h后制成料浆,将料浆用喷枪喷涂在钼基材表面,喷涂厚度约为300μm,自然干燥后在温度1500℃,真空度≥0.1Pa的条件下熔烧,保温40min,制成抗氧化涂层底层,厚度约60~70μm;4)在第②组抗氧化材料中分别加入粉末质量5wt%的聚乙二醇和0.5wt%的KCl作为粘结剂和催化剂,再加入粉末体积2倍的无水乙醇作为载体,混合均匀后用刚玉珠以300r/min转速球磨10h后制成料浆,将料浆用喷枪喷涂在底层涂层表面,喷涂厚度约为150μm,自然干燥后在温度1500℃,真空度≥0.1Pa的条件下熔烧,保温30min,制成抗氧化涂层面层,厚度约20~30μm。图6为本发明实施例3制备的复合涂层1800℃下静态测试30h后的截面形貌照片。表2为抗氧化复合涂层的抗氧化性能测试数据表。表2抗氧化涂层抗氧化性能测试数据表试片编号涂层厚度(μm)测试项目测试性能109871800℃静态33h110891800℃热震1120次111881800℃热震1260次1161021800℃热震1211次1171051800℃静态30h1181071800℃热震1151次1191041800℃静态30h实施例41)两组高温抗氧化材料,分别为:①W为7wt%,Cr为5wt%,B4C为4wt%,HfO2为6wt%,Mo为3wt%,TiB2为0.5wt%,ZrO2为3wt%,MoSi2为4wt%,余量为Si;②Mo为16.2wt%,W为3.5wt%,Nb为1.2wt%,HfO2为2.5wt%,Ta为1wt%,V为1.2wt%,Y为2wt%,Ge为2.5wt%,B2O3为2wt%,ZrO2为3.2wt%,余量为Si;将上述两组材料按比例混匀,分别使用行星式球磨机研磨成不大于300目的粉料,装入不同的容器;2)使用240#、500#耐水砂纸对纯钼金属基材进行打磨,至表面光亮无异物附着,表面粗糙度不大于Ra3.2μm(样板对比),以20~30KHz频率对试样进行超声波清洗,清洗时间15~20分钟,清洗后将试片浸入无水乙醇备用。3)在第①组抗氧化材料中分别加入粉末质量3wt%的聚乙二醇和0.5wt%的NH4Cl作为粘结剂和催化剂,再加入粉末体积1.5倍的无水乙醇作为载体,混合均匀后用刚玉珠以300r/min转速球磨8h后制成料浆,将料浆用喷枪喷涂在钼基材表面,喷涂厚度约为300μm,自然干燥后在温度1550℃,真空度≥0.1Pa的条件下熔烧,保温20min,制成抗氧化涂层底层,厚度约50~60μm;4)在第②组抗氧化材料中分别加入粉末质量50wt%的硝基清漆和0.8wt%的NH4Cl作为粘结剂和催化剂,再加入粉末体积1.5倍的无水乙醇作为载体,混合均匀后用刚玉珠以300r/min转速球磨10h后制成料浆,将料浆用喷枪喷涂在底层涂层表面,喷涂厚度约为200μm,自然干燥后在温度1550℃,真空度≥0.1Pa的条件下熔烧,保温20min,制成抗氧化涂层面层,厚度约30~50μm。表3为抗氧化复合涂层的抗氧化性能测试数据表。表3抗氧化涂层抗氧化性能测试数据表实施例51)两组高温抗氧化材料,分别为:①W为6wt%,Cr为7wt%,B2O3为3wt%,HfO2为5.5wt%,Mo为5wt%,Ta为1wt%,S为0.6wt%,ZrO2为2wt%,MoSi2为5wt%;②Mo为18wt%,W为4wt%,Nb为2wt%,HfO2为5wt%,Ta2O5为2wt%,V为1.5wt%,Y2O3为2.2wt%,Ge为3.4wt%,B为1wt%,ZrO2为5wt%;将上述两组材料按比例混匀,分别使用行星式球磨机研磨成不大于300目的粉料,装入不同的容器;2)使用240#、500#耐水砂纸对TZM合金基材进行打磨,至表面光亮无异物附着,表面粗糙度不大于Ra3.2μm(样板对比),以20~30KHz频率对试样进行超声波清洗,清洗时间10~20分钟,清洗后将试片浸入无水乙醇备用。3)在第①组抗氧化材料中分别加入粉末质量6wt%的聚乙二醇和0.5wt%的NaF作为粘结剂和催化剂,再加入粉末体积2倍的乙酸乙酯作为载体,混合均匀后用刚玉珠以400r/min转速球磨6h后制成料浆,将料浆用喷枪喷涂在钼基材表面,喷涂厚度约为300μm,自然干燥后在温度1530℃,真空度≥0.1Pa的条件下熔烧,保温12min,制成抗氧化涂层底层,厚度约71~82μm;4)在第②组抗氧化材料中分别加入粉末质量6wt%的聚乙二醇和1wt%的KCl作为粘结剂和催化剂,再加入粉末体积1.5倍的无水乙醇作为载体,混合均匀后用刚玉珠以400r/min转速球磨8h后制成料浆,将料浆用喷枪喷涂在底层涂层表面,喷涂厚度约为200μm,自然干燥后在温度1550℃,真空度≥0.1Pa的条件下熔烧,保温20min,制成抗氧化涂层面层,厚度约25~35μm。表4为抗氧化复合涂层的抗氧化性能测试数据表。表4抗氧化涂层抗氧化性能测试数据表试片编号涂层厚度(μm)测试项目测试性能1481091900℃静态25min1491061700℃静态142h1501031700℃静态141h1511101900℃静态15min1521011800℃热震636次1531071800℃热震722次1541081700℃静态136h以上实施例的说明只是用于帮助理解本发明的方法及其核心思想。应当指出,对于本
技术领域:
的普通技术人员来说,在不脱离本发明原理的前提下,还可以对本发明进行若干改进和修饰,这些改进和修饰也落入本发明权利要求的保护范围内。对所公开的实施例的上述说明,使本领域专业技术人员能够实现或使用本发明。对这些实施例的多种修改对本领域的专业技术人员来说将是显而易见的,本文中所定义的一般原理可以在不脱离本发明的精神或范围的情况下,在其它实施例中实现。因此,本发明将不会被限制于本文所示的这些实施例,而是要符合与本文所公开的原理和新颖特点相一致的最宽的范围。当前第1页1 2 3