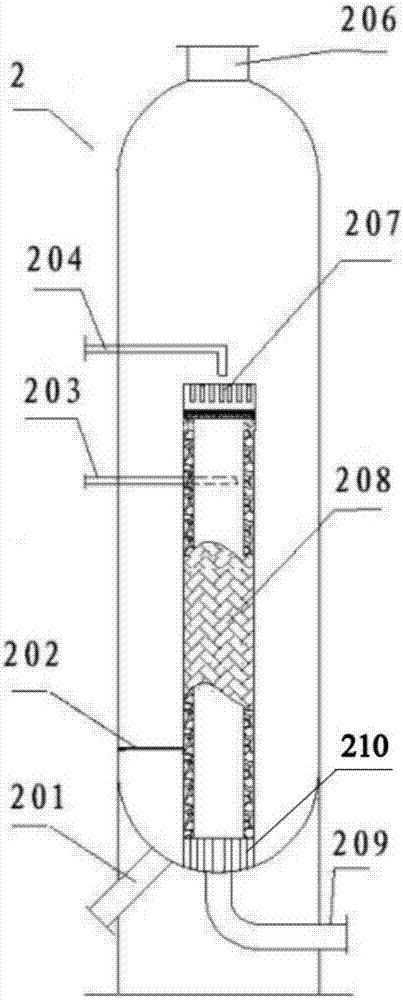
本发明属于加氢
技术领域:
,具体涉及一种沸腾床加氢反应系统和沸腾床加氢方法。
背景技术:
:沸腾床加氢反应指原料油(主要为液相)、氢气(气相)在催化剂(固相)上进行加氢反应的过程,加氢反应主要发生加氢脱硫、加氢脱氮、加氢脱氧、加氢饱和、加氢裂化等。反应器在气、液、固三相的沸腾状态下操作,催化剂在从反应器底部进入的原料油和氢气的带动下,处于沸腾状态,与固定床反应器处于完全不同的流体状态。沸腾床加氢反应可以处理高金属、高沥青质含量的劣质原料油,反应具有压力降小、温度均匀、可以在线加排催化剂以保持催化剂活性等特点。目前存在两种主要类型的沸腾加氢技术,一类是采用油相循环的方式,如usre25,770中描述的沸腾床工艺,此工艺在实际应用中的不足在于:为保持液固分离效果,反应器内催化剂用量不能太多,反应器利用率低,工业沸腾床反应器利用率一般只有40%左右(利用率一般指催化剂装填量占反应器容积(不计封头空间)的百分数,固定床反应器利用率一般90%以上);反应器有较大空间是液体物料在没有催化条件下的停留时间过长,此部位没有加氢反应,物料在高温下容易反应结焦。另一类是在反应器内设置三相分离器,在反应器内上部进行气-液-固分离,如cn02109404.7介绍的沸腾床反应器,按该方案通过设置内置三相分离器,可以提高催化剂的用量,即提高反应器的利用空间,但在实际使用时,催化剂用量提高有限,如果催化剂用量增加,三相分离器的分离效果快速下降,实际上比第一类沸腾床反应器利用率提高有限;中国专利cn101721961b对上述专利技术进行改进,三相分离器的内筒和外筒上段均为倒置的锥台形结构,下段均为圆柱筒形结构,并在反应器中部设置有内构件,该专利催化剂沉降主要还是集中在筒壁附近,虽然采用的内构件,在一定程度上利于流体径向速度分布更均匀,但是分离效果较差,尤其在大规模伸长中,催化剂的添加量很大,催化剂的携带量较大。中国专利cn101376092b对上述技术进行了进一步改进,在三相分离器下部沿筒壁设置导向结构,利用导向结构,增加三相分离器的操作弹性,确保三相分离器的高效分离,减少催化剂的带出量,提高催化剂藏量,提高反应器利用率,但在使用时,仍需在三相分离器下部一定区设置催化剂稀相区(如其附图所示,该区域催化剂量很少,基本不发生加氢反应),否则三相分离器的分离效果仍不能满足要求,而稀相区的存在,影响反应器利用率的进一步提升(虽然其说明书中指出反应器筒体内的催化剂装量可以为反应器容积的40%~70%,但一般也只有在50%左右的情况下可以稳定运转),也影响加氢反应效果,并且反应器规模放大后,催化剂装量更难以提高,难以达到实验装置的效果。同时,经过大量深入研究表明,影响沸腾床反器内三相分离器分离效果的因素不仅在于三相分离器的结构、物料体系状态,还与地球自转有很大关系。沸腾床反器内气、液、固三相状态,气、液相整体处于向上流动状态,固体催化剂处于沸腾浮动状态。地球自转对上述物料状态具有一定的作用力,形成轻度的旋流作用,在工业较大反应器中,由于规模较大,这种旋流作用更为显现。其结果是催化剂在靠近反应器内壁的区域更为聚集,反应器径向中心区域更为稀疏。这种效应对现有三相分离器的分离效果产生了明显影响,即当催化剂装填量增加时,三相分离器分离出来的固体催化剂沉降回反应器中的阻力增加,被液体物料带出反应器的机会提高,使反应器带出催化剂量增大。因此,如何提高沸腾床反应器的利用效率,提高反应效果,是本领域需要解决的技术问题。此外,沸腾床反应器由于物料处于“沸腾”状态,虽然有多种防止催化剂带出的技术措施,但液相产物中仍不可避免有少量的催化剂被带出,虽然数量较少,但由于装置处理量巨大(大型沸腾床装置年加工量可达几百万吨),因此带出的催化剂总量较大,对后续的处理(如固定床装置、分馏装置等)造成一定影响。从液相中脱除固体物质可以采用常规的过滤设备、旋流分离设备等,但处理沸腾床反应器液相流出物时存在使用时间短、影响装置正常稳定运转等问题。热高压分离器可用于将沸腾床反应器反应产物进行气液固三相的再次分离,减少液相中携带的固体杂质对下游的影响。中国专利cn104998491b介绍了一种热高压分离器,在热高压分离器筒体内中部设置锥形挡板,气液混合物喷到挡板上散开,气体因扩散作用上升,液体(包含部分固体催化剂)因自身重力下落。热高分底部注入低温vgo,将分离下来的高含固量的热高分液稀释,避免了热高分底部结焦堵塞。但是加氢反应产物进入热高压分离器时,气液两相共用一个入口,分离时间短,影响气液分离效果。有鉴于此,特提出本发明。技术实现要素:针对现有技术的不足,本发明提供一种沸腾床加氢反应系统,本发明的目的之一在于提高沸腾床反应器的利用率(即提高反应器内催化剂藏量),可以进一步提升加氢反应效果。本发明的另一个目的在于沸腾床加氢反应的产物经本发明所述的热高压分离器处理,提高分离效果,减少液相中携带的固体对后续设备的影响。为实现上述目的,采用以下技术方案:一种沸腾床加氢反应系统,包括沸腾床反应器,所述沸腾床反应器具有反应器筒体,所述反应器筒体内的上部设置三相分离器,所述三相分离器包括内筒和外筒,所述内筒和外筒的上下两端均开口,其特征在于:所述外筒的上端开口低于所述内筒的上端开口,所述外筒的下端开口低于所述内筒的下端开口;所述内筒为直筒段;所述外筒上部为直筒段,下部为锥台形收缩段,所述收缩段的下端开口为外筒的下端开口;所述内筒的下端开口与所述外筒收缩段之间设置间隙,以便于物料通过。进一步,所述三相分离器外筒收缩段下部设置直筒段,所述外筒的结构从上至下依次为直筒段、收缩段、直筒段。进一步,所述三相分离器外筒下端开口的下方设置导流体;优选的,所述导流体为上下两端小、中间大的纺锤形,纺锤形轴向横截面最大处直径为外筒体下端开口直径的1~3倍。进一步,所述三相分离器内筒内部的中上位置处设置液体排出管线,用于将分离的液体导出沸腾床反应器。进一步,所述三相分离器与所述沸腾床反应器筒体同轴心设置,三相分离器的外筒通过支撑结构固定在反应器筒体内壁上,三相分离器的内筒通过支撑结构固定在外筒内壁上。进一步,所述三相分离器的外筒上部直筒段的直径为反应器筒体内径的50%~90%;内筒与外筒之间的环隙距离为外筒相应位置半径的30%~70%;内筒上端与外筒上端的高度差为外筒半径的10%~50%;内筒的下端开口与外筒收缩段之间的间隙为外筒直筒段半径的5%~40%;外筒收缩段下端开口直径为外筒直筒段直径的10%~50%;外筒下部收缩段的收缩角为20°~80°。优选的,所述三相分离器的外筒上部直筒段的直径为反应器筒体内径的75%~85%;内筒与外筒之间的环隙距离为外筒相应位置半径为40%~60%;内筒上端与外筒上端的高度差为外筒半径的20%~40%;内筒的下端开口与外筒收缩段之间的间隙为外筒直筒段半径的10%~30%;外筒收缩段下端开口直径为外筒直筒段直径的15%~35%;外筒下部收缩段的收缩角为30°~60°。根据本发明的实施例,所述的沸腾床加氢系统还包括热高压分离器,所述热高压分离器设置有液相入口和气相入口,所述液相入口位于所述气相入口上方;所述高压分离器内部设置过滤筒,所述热高压分离器的液相入口与沸腾床反应器的液相出口连通,所述热高压分离器的气相入口通过管路通入过滤筒内,过滤筒底部与热高压分离器底部通过连接部连接并与热高压分离器的液相排出口连通。进一步,过滤筒顶部设置液体分布器,热高压分离器液相入口通过管路引至液体分布器。进一步,所述液体分布器为底部封闭、顶部敞开、侧壁开孔的筒体,且筒体直径与过滤筒直径相同。进一步,所述过滤筒与热高压分离器同轴心设置,过滤筒高度为热高压分离器的40%~80%,过滤筒直径为热高压分离器直径的30%~70%。本发明在上述研究的基础上,针对地球自转对大型沸腾床反应器内物料流态的影响,重新设计了新型的沸腾床三相分离器以及热高压分离器,解决了现有技术的问题,获得了如下技术效果:1、将三相分离器分离下来的固体催化剂在反应器径向中心区域沉降回流到反应器内,解决了高催化剂装填量时,催化剂沉降回流的阻力大问题,保证了三相分离器在高催化剂装填量时仍具有良好的分离效果。2、可以进一步提高催化剂装填量比例,特别是大规模工业沸腾床反应器的催化剂装填比例。在提高反应器容积利用率的同时,减少或取消了催化剂稀相区,提升了加氢反应效果。3、克服了地球自转引起的催化剂分布不均造成的影响反应效果问题。现有技术中,未考虑地球自转的旋流影响,催化剂在一定程度上分布不均,而现有三相分离器将分离下来的催化剂沉降至反应器内壁区域,加剧了这种分布不均,在影响三相分离器分离效果的同时,也影响反应效果。本发明方法解决了该不足。4、本发明热高压分离器设置了气相和液相入口,并且增加了过滤功能,气相引入过滤筒内,在气相向过滤筒外流动的过程中,通过气相反向冲刷和气相夹带液相的反向冲刷,进一步提高了过滤效果;此外,在过滤的同时实现过滤介质的自净作用,可以有效保持过滤筒的长周期运转。附图说明图1是本发明的一种实施例的沸腾床反应器的结构示意图;图2是本发明的一种实施例的热高压分离器的结构示意图。其中:1、沸腾床反应器;101、物料入口;102、分配盘;103、反应器筒体;104、导流体;105、三相分离器外筒;106、三相分离器内筒;107、催化剂加入口;108、气体出口;109、液体出口;110、反应区域;111、催化剂排出口;112、液体排出管线;2、热高压分离器;201、热高压分离器固体排出口;202、过滤筒固定结构;203、热高压分离器气相入口;204、热高压分离器液相入口;206、热高压分离器气相排出口;207、液相分配器;208、过滤筒;209、热高压分离器液相排出口;210、连接部。具体实施方式下面将结合本发明实施例中的附图,对本发明实施例中的技术方案进行清楚、完整地描述,显然,所描述的实施例仅仅是本发明一部分实施例,而不是全部的实施例。基于本发明中的实施例,本领域普通技术人员在没有付出创造性劳动前提下所获得的所有其他实施例,都属于本发明保护的范围。本发明中提供了一种沸腾床加氢反应系统,包括沸腾床反应器1和热高压分离器2。具体的,如图1所示,所述沸腾床反应器1具有反应器筒体103,所述反应器筒体103内设置三相分离器,所述三相分离器包括内筒106和外筒105,所述内筒106和外筒105的上下两端均开口,所述外筒105的上端开口低于所述内筒106的上端开口,所述内筒上端开口与外筒上端开口高度差为内筒高度的10%~50%,所述外筒105的下端开口低于所述内筒106的下端开口;所述内筒106为直筒段;所述外筒105上部为直筒段,下部为一锥台形收缩段,所述收缩段的下端开口为外筒105的下端开口;所述内筒106的下端开口与所述外筒105收缩段之间设置间隙,以便于物料通过。需要说明的是,本发明三相分离器内外筒结构的设置,使得待分离的三相物质沿着图1箭头所示的方向进行流通,固体催化剂在反应器的中心沿着外筒下端的出口沉降返回至反应区域110继续参加反应,分离后的液相区处于内筒中,通过管路引至液相出口109排出反应器,分离后的气体通过反应器顶部设置的气相出口108排出反应器。通过上述设置的三相分离器,固体催化剂在反应器径向中心区域沉降回流到反应器内,避免了催化剂在靠近反应器内壁的区域聚集,解决了高催化剂装填量时,催化剂沉降回流的阻力大问题,保证了三相分离器在高催化剂装填量时仍具有良好的分离效果。此外,在大规模沸腾床反应器的催化剂高装填时,提高反应器容积利用率的同时,减少或取消了催化剂稀相区,进而提升了加氢反应效果。同时,本发明的三相分离器的设置克服了地球自转引起的催化剂分布不均造成的影响反应效果问题。现有技术中,未考虑地球自转的旋流影响,催化剂在一定程度上分布不均,而现有三相分离器将分离下来的催化剂沉降至反应器内壁区域,加剧了这种分布不均,在影响三相分离器分离效果的同时,也影响反应效果。本发明中,所述三相分离器外筒105收缩段下部设置直筒段,所述外筒105的结构从上至下依次为直筒段、收缩段、直筒段。通过在外筒105收缩段下部设置直筒段,进一步利于固体催化剂径向中心区域沉降回流到反应器内。本发明中,所述三相分离器外筒105下端开口的下方设置导流体104,所述导流体104为上下两端小、中间大的纺锤形,纺锤形轴向横截面最大处直径为外筒体下端开口直径的1~3倍。导流体104与三相分离器外筒105下端开口之间设置间隙。在三相分离器下部设置外筒105下端开口的下方设置导流体104,利用导流体104,增加三相分离器的操作弹性,确保三相分离器的高效分离,减少催化剂的带出量,提高催化剂藏量,提高反应器利用率。本发明中,所述三相分离器内筒内部的中上位置处设置液体排出管线112,用于将分离的液体导出沸腾床反应器1,液体排出管线112的高度距三相分离器内筒106上部的水平切面的高度为三相分离器高度的2%~10%。本发明中,所述三相分离器与所述反应器筒体103同轴心设置,三相分离器的外筒105通过支撑结构固定在反应器筒体内壁上(图中未示出),三相分离器的内筒106通过支撑结构固定在外筒内壁上(图中未示出)。通过所述三相分离器与所述反应器筒体103同轴心设置,进一步克服了地球自转引起的催化剂分布不均造成的影响反应效果问题。本发明中,沸腾床反应器1内三相分离器的外筒105上部直筒段的直径一般为反应器筒体106内径的50%~90%,优选为75%~85%。内筒106与外筒105之间的环隙距离一般为外筒105相应位置半径的30%~70%,优选为40%~60%。内筒106上端与外筒上端的高度差为外筒半径的10%~50%,优选为20%~40%。内筒106的下端开口与外筒收缩段之间的间隙为外筒105直筒段半径的5%~40%,优选为10%~30%。外筒105收缩段下端开口直径为外筒105直筒段直径的10%~50%,优选为15%~35%。外筒下部收缩段与水平面的锐角夹角为20°~80°,优选30°~60°。外筒105上部直筒段的高度为0.4~3m,优选0.5~1m;外筒105锥形段的高度为0.2~2m,优选为0.3~0.8m;外筒105下部直筒段的高度为0.03~0.8m,优选为0.05~0.5m。本发明中,沸腾床反应器1内三相分离器上部设置气相空间,气相空间高度为反应器筒体103(不包括反应器封头部分)的0~20%,优选为5%~10%。本发明中,反应器筒体103的底部设有物料入口101(液体原料油和氢气的入口)和分配盘102,物料入口101和分配盘102之间设置一定的物料流动空间。在反应器筒体顶部设有气体出口108,在反应器筒体侧壁上设置有液相出口109。反应器的顶部还设置有催化剂加入口107,在反应器底部还设置有催化剂排出口111,分别用于催化剂的添加与卸载。本发明中,沸腾床反应器1可以根据需要设置其它构件,如温度检测系统、压力检测系统、流体流态检测系统、催化剂分布状态检测系统、物料再分配系统、催化剂在线加入、卸载系统等一种或几种。上述构件可以由本领域技术人员按现有技术确定。本发明中,沸腾床加氢反应系统可以根据需要设置配套装置,如原料泵、换热器、加热炉、分离器、氢气输送系统、反应产物分离系统等。上述配套装置可以由本领域技术人员按现有技术确定。本发明的沸腾床加氢反应系统。反应原料可以重质、劣质原料,如减压渣油、煤焦油、煤液化油、沥青油砂、页岩油等。催化剂一般为固体颗粒,颗粒直径(以等体积球形计)一般为0.6~2mm,催化剂一般以氧化铝为载体,以mo、w、ni、co等至少一种为活性组分,同时可以添加相关助剂。催化剂在反应器内装量(以静止状态计)为反应器容积的50%~85%,优选为65%~80%,最优选为72%~78%。反应条件可以根据原料性质和反应深度要求确定,一般反应压力为5~25mpa、反应温度为200~500℃,氢气与原料油标准状态下体积比为300~2000,原料油与催化剂体积(静止状态)相比的体积空速为0.1~2h-1。具体的,如图2所示,在本发明中,所述的沸腾床加氢系统还包括热高压分离器2,所述热高压分离器2设置有液相入口204和气相入口203,所述液相入口204位于所述气相入口203上方,所述液相入口204与所述气相入口203的垂直高度差为热高压分离器2筒体高度的10%~50%,优选为15%~30%;所述高压分离器2内部设置过滤筒208,所述热高压分离器的液相入口204与沸腾床反应器的液相出口109连通,所述热高压分离器的气相入口203通过管路通入过滤筒内,过滤筒底部与热高压分离器底部通过过滤筒连接部210连接并与热高压分离器的液相排出口209连通,过滤筒连接部210为网状结构,热高压分离器内部的液相可自由通过,但可阻止过滤筒外的固体催化剂进入。需要说明的是,过滤筒208的筒体为丝网状结构,便于气体和液体的流通,本发明中将气相入口203通过管路引至到过滤筒内,气体在过滤筒内外流通,而位于气相入口203上方的液相入口204将液体引入热高压分离器2且位于过滤筒208外,在热高压分离器2内形成气相夹带液相的反向冲刷,进一步提高了过滤效果。同时,在气相向过滤筒208外流动的过程中,通过气相反向冲刷在过滤的同时实现过滤介质的自净作用,可以有效保持过滤筒的长周期运转。本发明中,过滤筒208的顶部设置液体分布器207,热高压分离器的液相入口204通过管路引至液体分布器207处;液体分布器207优选为底部封闭、顶部敞开、侧壁开孔的筒体,且筒体直径与过滤筒直径相同。该结构实现液体与气体形成反向冲刷,并将液相物料沿过滤筒208的筒壁冲刷,液相中的固体被截留在过滤筒外,经过过滤的液体折流冲刷过滤筒208外壁后,进入过滤筒208内,最后经热高压分离器的液相排出口209排出热高压分离器2。通过气相反向冲刷和气相夹带液相的反向冲刷,进一步提高过滤效果。相比较而言,液相中携带的固体量大于气相中的固体量,采用上述结构,能够将液相中携带的较多固体催化剂截留在过滤筒外,大大减少了液相中固体含量,避免对下游管路的堵塞或磨损。本发明中,热高压分离器2的顶部设置气相排出口206,下部设置固体排出口201。过滤筒208与热高压分离器2同轴心设置,过滤筒208的高度为热高压分离器2的40%~80%,过滤筒208的直径为热高压分离器2直径的30%~70%。优选的,热高压分离器2和过滤筒208均为圆柱形筒体。下面结合实施例对本发明做进一步说明,但不构成对本发明的限制。在实际操作时,沸腾床反应器的气体出口108与热高压分离器气相入口203连通,腾床反应器的液体出口109与热高压分离器液相入口204连通。首先,物料与催化剂在沸腾床反应器的反应区域110处进行反应,反应后的产物经三相分离器进行分离,分离得到的气体通过沸腾床反应器的气相出口108排出经热高压分离器的气相入口203引入至过滤筒208内,分离得到的液相通过沸腾床反应器的液相出口109排出经热高压分离器的液相入口204引入至热高压分离器2内,在热高压分离器2中形成气相夹带液相的反向冲刷。具体的,沸腾床反应器排出的液相通过液相分配器207折流冲刷过滤筒208外壁后,进入过滤筒208内,最后经热高压分离器液相出口209排出热高压分离器2。拦截沉积在过滤筒208筒体外的固体杂质定期通过热高压分离器固体排出口201排出。以下结合实施例对本发明的具体实施方式做进一步的描述,并不因此将本发明限制在所述的实施例范围内。实施例1实施例1中使用的沸腾床反应器及三相分离器结构如图1,三相分离器分离效果采用冷模进行模拟实验。冷模装置的尺寸为:反应器筒体的内径300mm,反应器筒体的高度3500mm,三相分离器高度400mm,三相分离器的外筒上部直筒段的直径200mm,内筒与外筒之间的环隙距离为80mm,内筒上端与外筒上端的高度差为60mm,内筒的下端开口与外筒收缩段之间的间隙为60mm,外筒收缩段下端开口直径为90mm,外筒下部锥台形收缩段的收缩角(直筒段与锥台形收缩段的锐角夹角)35°。导流体纺锤形轴向横截面最大处直径为150mm。以煤油作为液体,进油量为60~120l/hr;气相选用氮气,进气量为2~4nm3/hr。固相选用粒径为0.7~0.8mm的氧化铝微球催化剂,催化剂藏量(以静止时计)为反应器有效容积(不计封头空间)的55%~80%。试验结果见表1。表1冷模装置试验结果从冷模试验可以看出,本发明沸腾床反应器具有良好的固体分离效果,适用的操作区间较广。对比例1反应器的基本结构同实施例1,不同之处在于三相分离器采用专利cn101721961b中实施例1的沸腾床反应器及三相分离器结构,反应条件和实验原料同实施例1。实验结果见表2.表2冷模装置试验结果对比例2反应器的基本结构同实施例1,不同之处在于三相分离器采用专利cn101376092b中实施例1的沸腾床反应器及三相分离器结构,反应条件和实验原料同实施例1。实验结果见表3.表3冷模装置试验结果实施例2按图2结构设计热高压分离器,模拟过滤条件下的气液分离操作。压力为10mpa,温度为270℃,液相为常压渣油,配制100目以下(100目筛下物)的催化剂固体粉末,含量为15μg/g,过滤筒过滤精度设计为30目,气体为氮气,气液体积比为600:1,过滤强度为3600kg/(平方米过滤材料·小时)。经过2000小时运转,热高压分离器压降(气相压力与液体出口压力差值)正常增加(比初始值)3.7%,过滤能力未下降,预计可以稳定运转2~3年。对比例3按实施例1所述条件,只是气相引入过滤筒外(过滤筒与热高压分离器筒之间的环隙),不设置液体分配器。经过150小时运转后,热高压分离器压降增加65.9%,过滤能力明显下降。实施例3利用本发明的沸腾床加氢方法进行煤焦油加氢试验。所述沸腾床反应器以及三相分离器按实施例1所述条件,所述的热高压分离器按实施例2所述条件,沸腾床反应器的气相出口108与热高压分离器的气相入口203相连,沸腾床反应器的液相出口109与热高压分离器的液相入口204相连。试验所采用的加氢催化剂为粒径为1.5mm的氧化铝微球催化剂,催化剂藏量(以静止时计)为反应器有效容积(不计封头空间)的75%。沸腾床反应器的反应压力15mpa,反应温度为410℃(反应器中部),原料油(不包括循环油的新鲜原料)与催化剂体积(静止状态)相比的体积空速为0.5h-1。沸腾床中催化剂的卸出量及补充量均为1吨/天。原料油性质见表4,离开所述热高压分离器的产物性质见表5。表4原料油性质原料低温煤焦油密度(20℃),g/cm31.02馏程,℃ibp/10%102.8/188.830%/50%245.2/338.070%/90%395.0/445.295%/fbp484.0/--s,wt%0.39n,μg·g-17986表5分析项目低温煤焦油密度(20℃),g/cm30.9834馏程,℃ibp/10%94.4/177.530%/50%231.0/330.270%/90%385.0/437.295%/fbp468.0/--s,wt%4.7n,μg·g-1113对比例4与实施例3的区别在于,所述的加氢系统采用专利cn101376092b所述的沸腾床加氢反应器和专利cn103773490a所述的热高压分离系统,催化剂装填量为60%,其余反应条件相同。经所述热高压分离系统后得到的产物性质见表6。表6分析项目低温煤焦油密度(20℃),g/cm30.9974馏程,℃ibp/10%97.4/180.530%/50%235.0/335.270%/90%390.0/441.295%/fbp473.0/--s,wt%9.5n,μg·g-1271从实验结果可以看出,与对比例4相比,采用实施例3的加氢方法进行加氢反应时,在沸腾床内的催化剂填量高达75%时,还可以从所述热高压分离器分离出更好的加氢产物。以上所述仅为本发明的优选实施例而已,并不用于限制本发明,对于本领域的技术人员来说,本发明实施例可以有各种更改和变化。凡在本发明的精神和原则之内,所作的任何修改、等同替换、改进等,均应包含在本发明的保护范围之内。当前第1页12