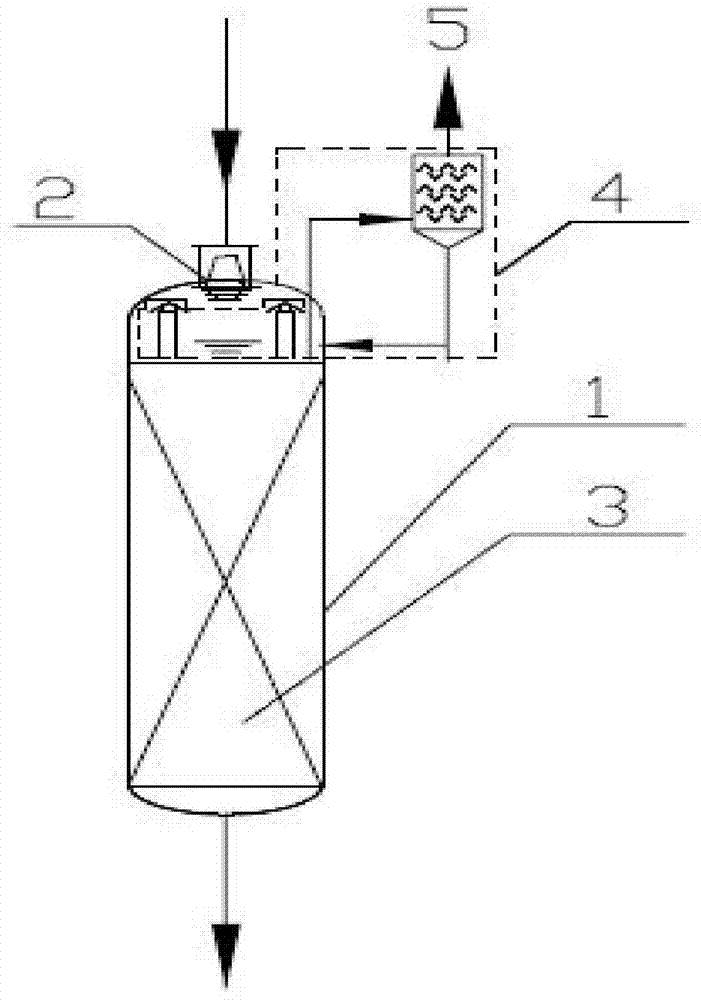
本实用新型涉及一种加氢反应器的排气系统,尤其适用于直馏煤油的液相加氢精制反应。
背景技术:
:液相加氢工艺是一种新型、高效、低能耗的加氢技术,与常规的滴流床加氢工艺相比具有以下优势:(1)可以消除氢气传质的影响。这主要是由于滴流床加氢工艺中,氢气从气相扩散并溶解到油中的速度为整个加氢反应的控制步骤,而液相加氢工艺使加氢反应在动力学控制区进行,即将氢气溶解于原料油中来满足加氢反应所需氢气,使加氢反应在纯液相中进行,消除氢气从气相到液相的传质影响;(2)烃油加氢过程实际上参与反应的氢气只有用于化学氢耗的氢气,而传统滴流床反应器加氢技术,需要有大量过剩的氢气存在,使得反应器的体积比较大,而液相加氢过程则将氢气溶解于原料油中,因此反应器及反应系统体积能够大幅度减小;(3)与传统的滴流床工艺相比,液相加氢工艺需要维持大量的过剩氢气,因而需要用循环氢压缩机,液相加氢工艺流程中不设置复杂的循环氢系统,可以节省循环氢压缩机和高压分离器等设备的投资。而在液相加氢工艺中,加氢脱硫副产物H2S对加氢脱硫、脱氮、脱芳反应也有明显的抑制作用,少量H2S存在就会大大降低加氢脱硫速率,并且H2S在催化剂表面的吸附为单层吸附,一旦吸附中心被H2S占据,反应速率将不再随H2S分压提高而下降,因此液相加氢需要间断外排出硫化氢组分,消除H2S的影响,才能实现深度脱硫。现有液相加氢工艺中,液相加氢反应器顶部一般采取间断或连续排气的方式,一方面控制反应器顶部压力,另一方面排出含有H2S的气体,而在气体外排的过程中,一般均采用常规简单的排气口及排气系统,具有排放气量大、排放气带液、排气时反应系统波动等问题,而现有的专利大多集中在液相加氢工艺、反应原料油混氢、反应器内部混氢等方面,对反应器排气方面的报道较少。CN102358847A提出了一种全液相加氢处理生产清洁柴油的方法,该方法包括:原料、氢气及循环液体加氢产物在管线中进行氢气饱和,形成一种原料/加氢产物/氢的液相混合物,在加氢工艺条件下,饱和溶解氢的液相混合物分段进入多级常规加氢反应器,并从反应器顶部排出含有副产物H2S、NH3的油气。该方法同时具有加氢反应器和将副产物H2S、NH3排出的功能。但是该加氢反应器中含有副产物H2S、NH3的油气排放口及排气系统为常规,存在排气量大、排放气带液、排气时反应器操作波动等问题。技术实现要素:针对现有技术的不足,本实用新型提供一种加氢反应器的排气系统。该排气系统的使用有利于实现均匀排气,有效减少排放气带液的现象发生,减少排放气的逸出量,改善加氢脱硫效果,降低了氢气消耗。本实用新型的加氢反应器的排气系统包括反应器封头内的排气组件和反应器外的气液分离组件,反应器顶部设置气体出口,气体出口通过输气管线与气液分离组件连接;所述的排气组件包括分布板、若干组升气筒和挡液帽;每组升气筒和挡液帽在分布板表面均匀布置,挡液帽通过筋板与升气筒顶部连接。所述排气组件的分布板,为表面均匀开孔的筛板结构,与加氢反应器内壁密封连接。所述排气组件的升气筒焊接于分布板上;升气筒筒体的部分浸没在反应器液面以下,优选浸没在液面下的部分为筒体总高度的1/4~1/2。本实用新型所述的气液分离组件可以为常规熟知的气液分离器结构,如重力沉降、折流分离、离心分离、丝网分离、填料分离结构等中的任意一种。优选采用下述结构的气液分离组件,所述气液分离组件包括圆筒形筒体和倒锥形底部,气液分离组件顶部设置排气口,倒锥形底部设置排液口,排液口与反应器内液相连通。所述的气液分离组件的筒形筒体内由下至上设置2N层折流组件,每层折流组件包括若干折流板,折流板为“V”形和/或“倒V”形结构,其中N≥1,N的上限根据反应实际需要确定,N优选2~8。优选每层折流组件中的折流板为相同结构;更优选相邻的奇数层和偶数层中的折流板错开排列,进一步优选为相邻的奇数层和偶数层中,奇数层的折流板为“V”形结构,偶数层的折流板为“倒V”结构。本实用新型所述的气液分离组件目的在于使气体在折流板的作用下能够发生多次折流和改变方向,避免发生气体短路,增强气液分离效果,减少气带液的现象发生。本实用新型同时提供一种采用上述的排气系统的液相加氢反应器,所述的液相加氢反应器还包括入口扩散器、催化剂床层和液体分布器。本实用新型中,液相加氢反应器内至少实现脱除其硫、氮、氧、金属杂质中一种污染物,并饱和芳烃,改变烃油分子结构。本实用新型中,加氢反应器的入口扩散器设置于物料入口处,用于对反应进料进行整流分布和节流缓冲。本实用新型中,所述的加氢反应器用于烃油的加氢脱硫、加氢脱氮、加氢脱芳烃精制;采用的新鲜原料油可以为烃油或者馏分油,如石油馏分、馏分油、柴油、脱沥青油、渣油、润滑油、煤液化油和页岩油或者其产品。本实用新型中,加氢反应器的操作条件为:反应温度为150~450℃,新鲜进料体积空速为0.5h-1~6.0h-1,氢分压为2.0~10MPa。本实用新型的加氢反应器的工作过程如下:原料首先进入加氢反应器,在入口扩散器及液体分布器进行物料均布后,进入催化剂床层发生液相加氢反应,反应流出物经由出料口离开;在反应过程中,可以利用连续或间断的方式通过反应器顶部的排气系统排出含有副产物H2S、NH3的油气,排放气冷凝液通过液体回流管返回至反应器。本实用新型具有如下优点:本排气系统的排气更加均匀,反应器内液面之下逸出的气体从挡液帽与升气筒之间的缝隙流出,另一方面通过该狭缝的限制可能使逸出气体再次溶解在原料油中,减少逸出气体量,降低氢气的消耗;可以实现在线连续排放含有副产物H2S、NH3的油气,有利于实现深度脱硫;减少了气带液现象发生,使在线连续排放的操作过程变得十分稳定,连续小流量排放操作时,氢气的损失少、物耗更低,经济性更好。附图说明图1是本实用新型的加氢反应器的结构示意图;图2是本实用新型的排气系统的结构示意图。其中:1-加氢反应器;2-入口扩散器;3-催化剂床层;4-排气系统;5-排气口;4-1-分布板;4-2-排气组件;4-3-升气筒;4-4-挡液帽;4-5-输气管线;4-6-气液分离组件;4-7-圆筒形筒体;4-8-倒锥形底部;4-9-液体回流管线;4-10-第一块折流挡板;4-11-第二块折流挡板,4-12-液体回流管线。具体实施方式下面结合附图进一步说明本实用新型装置的结构和使用方法。本实用新型的排气系统4包括排气组件4-2和气液分离组件4-6,所述的排气组件包括分布板4-1、若干升气筒4-3和与挡液帽4-4;所述的气液分离组件4-6包括输气管线4-5、圆筒形筒体4-7、倒锥形底部4-8和液体回流管线4-12,圆筒形筒体4-7的内部设置了若干异形折流挡板4-9,每组异形折流挡板包括“V”形折流板4-10和“倒V”形折流板4-11。所述排气组件4-2的升气筒4-3在分布板表面均匀布置,焊接于分布板之上;升气筒4-3筒体部分浸没在反应器液面以下,优选浸没在液面之下的筒体高度为筒体总高度的1/4~1/2。所述排气组件4-2的挡液帽4-4通过筋板与升气筒相连4-3,一方面使反应器内液面之下逸出的气体从挡液帽与升气筒之间的缝隙流出,另一方面通过该狭缝的限制可能使逸出气体再次溶解在原料油中,减少逸出气体量。所述排气组件4-2的挡液帽4-4之上的封头内部为气相空间,气相空间与外部的气液分离组件通过输气管线4-5相连。所述气液分离组件的输气管线4-5的一端与反应器顶部相连接,另一端与圆筒形筒体4-7的下部相连接。气液分离组件4-6优选采用下述结构,气液分离组件包括圆筒形筒体4-7和倒锥形底部4-8,气液分离组件4-6顶部设置排气口5,倒锥形底部设置排液口4-12,排液口4-12与反应器内液相连通。气液分离组件4-6的圆筒形筒体4-7内由下至上设置2N层折流组件4-9,每层折流组件4-9包括若干“V”形折流板4-10和“倒V”形折流板4-11,其中N≥1,N的上限根据反应实际需要确定,N优选2~8。优选每层折流组件中的折流板为相同结构;更优选相邻的奇数层和偶数层中的折流板错开排列,进一步优选为相邻的奇数层和偶数层中,奇数层的折流板为“V”形结构,偶数层的折流板为“倒V”结构。所述的排液口4-12的器内部分浸没在反应器的液面以下。采用本实用新型的排气组件的液相加氢反应器的工作过程如下:反应原料进入加氢反应器1后,经过入口扩散器2进行整流分布和节流缓冲后,在催化剂床层3内发生加氢反应,反应流出物流出后进入下一工序;在液相加氢反应器1的顶部设置了排气组件4及排气口5;在排气过程中,排放气首先经由排气组件4-2上的升气筒4-3与挡液帽4-4之间的夹缝排出,排出后进入反应器封头内的气相空间,封头内的气体进入气液分离组件4-6,首先经气液分离组件4-6的输气管线4-5进入圆筒形筒体4-7的下部,在其中的若干组异形折流板4-9作用下发生气液分离,其中的异形折流板4-9是由若干“V”形折流板4-10和“倒V”形折流板4-11排列而成,分离出的气体经圆筒形筒体4-7顶部设置的排气口排出,分离出的液体经过倒锥形底部4-8设置的排液口进入液体回流管线4-12,并通过液体回流管线4-12下端浸没在液面以下而流回反应器内。对比例1自罐区来的直馏煤油经原料油进料泵升压、换热至反应温度后,与氢气在混合器内进行预先混合,混合均匀后的物料进入加氢反应器发生液相加氢反应,反应器顶部设置了常规的排气口,排气口位于加氢反应器的封头位置,反应器器壁上设置了液位计口,用于控制和检测反应器内液位,以便将催化剂床层完全浸没在液面之下,发生全液相加氢反应。原料油性质见表1;加氢反应条件及结果见表2。表1原料性质项目分析结果密度(20℃),kg/m3774.5馏程,℃150~248硫含量,m%0.20氮含量,μg/g7硫醇硫,μg/g170实施例1自罐区来的直馏煤油经原料油进料泵升压、换热至反应温度后,与氢气在静态混合器内进行预先混合,混合均匀后的物料进入液相加氢反应器发生液相加氢反应,反应器顶部设置了本实用新型的排气组件和气液分离组件,排气组件设置于加氢反应器的顶部封头内部,气液分离组件位于反应器外部,反应器器壁上设置了液位计口,用于控制和检测反应器内液位,以便将催化剂床层完全浸没在液面之下,发生全液相加氢反应。加氢反应器的排气系统括反应器封头内的排气组件和反应器外的气液分离组件,反应器顶部设置气体出口,气体出口通过输气管线与气液分离组件连接;排气组件包括分布板、若干组升气筒和挡液帽,每组升气筒和挡液帽在分布板表面均匀布置,挡液帽通过筋板与升气筒顶部连接;排气组件的分布板,为表面均匀开孔的筛板结构,与加氢反应器内壁密封连接;排气组件的升气筒焊接于分布板上,升气筒筒体的1/4浸没在反应器液面以下。气液分离组件包括圆筒形筒体和倒锥形底部,气液分离组件顶部设置排气口,倒锥形底部设置排液口,排液口与反应器内液相连通,气液分离组件的圆筒形筒体内由下至上设置2层折流组件,第一层折流组件包括若干“V”形折流板,第二层折流组件包括若干“倒V”形折流板,两层折流板错开排列。原料油性质见表1;加氢反应条件及结果见表2。表2加氢反应条件及结果见表2实施例2自罐区来的直馏煤油经原料油进料泵升压、换热至反应温度后,与氢气在静态混合器内进行预先混合,混合均匀后的物料进入液相加氢反应器发生液相加氢反应,反应器顶部设置了本实用新型的排气组件和气液分离组件,排气组件设置于加氢反应器的顶部封头内部,气液分离组件位于反应器外部,反应器器壁上设置了液位计口,用于控制和检测反应器内液位,以便将催化剂床层完全浸没在液面之下,发生全液相加氢反应。加氢反应器的排气系统括反应器封头内的排气组件和反应器外的气液分离组件,反应器顶部设置气体出口,气体出口通过输气管线与气液分离组件连接;排气组件包括分布板、若干组升气筒和挡液帽,每组升气筒和挡液帽在分布板表面均匀布置,挡液帽通过筋板与升气筒顶部连接;排气组件的分布板,为表面均匀开孔的筛板结构,与加氢反应器内壁密封连接;排气组件的升气筒焊接于分布板上,升气筒筒体的1/2浸没在反应器液面以下。气液分离组件包括圆筒形筒体和倒锥形底部,气液分离组件顶部设置排气口,倒锥形底部设置排液口,排液口与反应器内液相连通,气液分离组件的圆筒形筒体内由下至上设置2层折流组件,第一层折流组件包括若干“V”形折流板,第二层折流组件包括若干“倒V”形折流板,两层折流板错开排列。当前第1页1 2 3