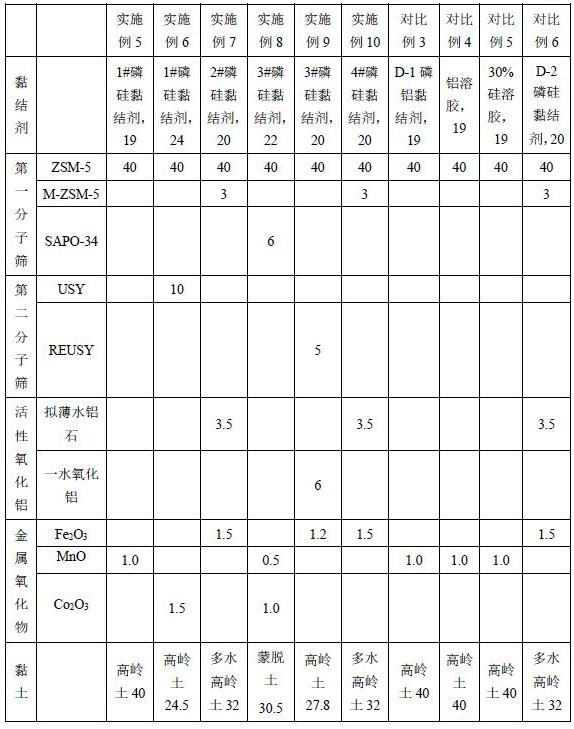
1.本发明涉及化工技术领域,具体的,涉及含磷硅复合粘结剂的催化裂解催化剂及其制备方法。
背景技术:2.随着石油化工产业的快速发展,乙烯和丙烯为主的低碳烯烃需求量不断增长。石脑油蒸汽裂解提供了我国90%的乙烯和30%的丙烯。虽然蒸汽裂解工艺很成熟,但存在建设成本高、装置能耗大(反应温度大于800℃)、碳排放量大等弊端。为了应对全球日益严峻的能源消耗和环境污染问题,已经开发了采用微球催化剂的烃类催化裂解工艺技术。这种工艺使长链烃类在较高反应温度下(600℃-700℃)转化为高附加值的乙烯、丙烯等低碳烯烃。烃类的裂解反应路径可分为正碳离子机理和自由基机理,前者通过固体酸作用主要生成丙烯和丁烯特征产物,后者则在热引发条件下生成乙烯为特征的产物。在微球催化裂解催化剂中,一般采用中小孔径的择形裂化分子筛和辅助的金属元素作为主要裂解组分,通过协调正碳离子和自由基反应达到增产丙烯和乙烯的目的。而中小孔径分子筛孔道容易堵塞,因此,催化剂的孔道畅通性对生产低碳烯烃具有重要影响。
3.目前,催化裂解催化剂在制备过程中主要采用铝溶胶或磷铝无机粘结剂为主的粘结剂,但是含铝溶胶粒径较小,会导致催化剂孔道的堵塞,限制中小孔分子筛增产低碳烯烃的功效,从而导致催化裂解催化剂的催化效果不理想。
技术实现要素:4.本发明提出磷硅复合粘结剂的催化裂解催化剂及其制备方法,解决了相关技术中催化裂解催化剂的催化效果差的问题。
5.本发明的技术方案如下:含磷硅复合粘结剂的催化裂解催化剂,以重量干基计,由5%-35%磷硅复合粘结剂、25%-50%第一分子筛、0-25%第二分子筛、0.2%-10%金属氧化物、0-15%活性氧化铝和余量黏土组成;所述磷硅复合粘结剂为将磷酸和硅溶胶混合后在30℃-95℃老化得到。
6.作为进一步技术方案,所述老化反应0.1-5小时。
7.作为进一步技术方案,所述黏土包括高岭土、多水高岭土、蒙脱土、交联层状粘土,海泡石、膨润土、水滑石、硅藻土、累托石中的一种或多种。
8.作为进一步技术方案,所述磷酸包括正磷酸、亚磷酸中的一种或多种。
9.作为进一步技术方案,所述磷酸的质量浓度以p2o5含量计为20%-62%,硅溶胶的质量浓度以sio2含量计为15%-50%。
10.作为进一步技术方案,所述硅溶胶的ph为1.0-7.0,氧化钠20ppm-200ppm,粒径4nm-35nm。
11.作为进一步技术方案,所述磷硅复合粘结剂的组成,p2o5含量15%-45%,sio2含量5%-25%,粒径5nm-35nm,ph 0.4-4.0。
12.作为进一步技术方案,所述磷硅复合粘结剂的粒径为5-35nm。
13.作为进一步技术方案,所述第一分子筛为择形裂化分子筛,所述第二分子筛包括usy、re-usy、p-usy、pre-usy中的一种或多种。
14.作为进一步技术方案,所述择形裂化分子筛包括zsm-5、m-zsm-5、im-5、sapo-34、eu-1、itq-13、β、mcm-22中的一种或多种。
15.含磷硅复合粘结剂的催化裂解催化剂的制备方法,包括以下步骤:将磷硅复合粘结剂、第一分子筛、第二分子筛、金属化合物、活性氧化铝、黏土和水混合后,得到固含量为20%-60%的浆液,将浆液经过干燥、焙烧处理后,得到催化裂解催化剂。
16.作为进一步技术方案,所述干燥为喷雾干燥,喷雾干燥入口温度为300-600℃,尾气温度为100-300℃。
17.作为进一步技术方案,所述焙烧温度为300℃-600℃,焙烧时间为0.3h-3.0h。
18.本发明还提出所述的含磷硅复合粘结剂的催化裂解催化剂在烃类催化裂解反应中的应用。
19.本发明的工作原理及有益效果为:1、本发明中粘结剂为含磷硅的复合粘结剂,采用磷酸和硅溶胶老化后得到磷硅复合粘结剂,得到的磷硅复合粘结剂的粒径>5nm,将磷硅复合粘结剂应用到催化裂解催化剂中,可以提高催化剂的孔体积及抗磨强度,充分发挥了中小孔径择形裂化分子筛的反应性能,从而有效提高乙烯和丙烯等低碳烯烃产率。
20.2、本发明制备得到的催化裂解催化剂液化气产率和双烯(乙烯+丙烯)收率高,显示了更优的催化裂解反应性能,将其应用在烃类催化裂解反应中,解决了催化剂孔道易堵塞的问题,提高了产物收率,具有良好的应用前景。
具体实施方式
21.下面将结合本发明实施例,对本发明实施例中的技术方案进行清楚、完整地描述,显然,所描述的实施例仅仅是本发明一部分实施例,而不是全部的实施例。基于本发明中的实施例,本领域普通技术人员在没有作出创造性劳动前提下所获得的所有其他实施例,都涉及本发明保护的范围。
22.下述实施例及对比例中:1#zsm-5:硅铝比50,相对结晶度93%,氧化钠0.07%,固含量95.0%;2#zsm-5:硅铝比70,相对结晶度89%,氧化钠0.10,固含量94.5%;fe-zsm-5,fe2o31.8%,固含量92.0%;usy分子筛,晶胞参数2.427nm,固含量96.0%;re-usy,re2o31.9%,固含量95.2%;sapo-34;相对结晶度88%,固含量93.2%,均为工业品;高岭土:高岭石含量87%,固含量87.5%,平均粒度3.9μm;均为工业品;多水高岭土:埃洛石含量76%,固含量85.4%,平均粒度4.1μm;蒙脱土:固含量84.6%,平均粒度4.3μm,均为工业品;拟薄水铝石,固含量61.0%;一水氧化铝,固含量71.5%;铝溶胶,al2o323.5%,均为工业品。
23.实施例1将900g p2o5含量61.5%的正磷酸和1100g sio2含量30%的硅溶胶混合后,在80℃下反应0.2h,得到粒径为8nm的磷硅复合粘结剂,记为1#磷硅复合粘结剂;其中硅溶胶的ph为2.8,氧化钠含量为120ppm,粒径为12nm;1#磷硅复合粘结剂中p2o5含量27.7%,sio2含量
16.5%。
24.实施例2将1340g p2o5含量61.5%的正磷酸和660g sio2含量30%的硅溶胶混合后,在35℃下反应2h,得到粒径为12nm的磷硅复合粘结剂,记为2#磷硅复合粘结剂;其中硅溶胶的ph为2.8,氧化钠含量为120ppm,粒径为12nm;2#磷硅复合粘结剂中p2o5含量41.2%,sio2含量9.9%。
25.实施例3将1340g p2o5含量30%的正磷酸和1000g sio2含量40%的硅溶胶混合后,在55℃下反应0.5h,得到粒径为17nm的磷硅复合粘结剂,记为3#磷硅复合粘结剂;其中硅溶胶的ph为4.6,氧化钠含量为150ppm,粒径为18nm;3#磷硅复合粘结剂中p2o5含量17.2%,sio2含量17.1%。
26.实施例4将1340g p2o5含量61.5%正磷酸和660g sio2含量30%的硅溶胶混合后,在95℃下反应2h,得到粒径为12nm的磷硅复合粘结剂,记为4#磷硅复合粘结剂;其中硅溶胶的ph为2.8,氧化钠含量为120ppm,粒径为12nm;4#磷硅复合粘结剂中p2o5含量41.2%,sio2含量9.9%。
27.实施例5将去离子水、高岭土和1#zsm-5混合打浆60分钟,然后加入mno,搅拌20分钟,再加入1#磷硅复合粘结剂,打浆30分钟,经过高速剪切处理,得到固含量45%的浆液,然后喷雾干燥成型后,喷雾微球在550℃焙烧60分钟,制得催化裂解催化剂a-1,其配比列于表1;喷雾干燥入口温度560℃,尾气温度190℃。
28.实施例6将去离子水、高岭土、usy和1#zsm-5混合打浆80分钟,然后加入co2o3,搅拌30分钟,再加入1#磷硅复合粘结剂,打浆40分钟,经过高速剪切处理,得到固含量50%的浆液,然后喷雾干燥成型后得到喷雾微球,喷雾微球在600℃焙烧40分钟,制得催化裂解催化剂a-2,其配比列于表1;喷雾干燥入口温度540℃,尾气温度170℃。
29.实施例7将去离子水、多水高岭土、拟薄水铝石、fe-zsm-5和2#zsm-5混合打浆60分钟,然后加入fe2o3,搅拌20分钟,再加入2#磷硅复合粘结剂,打浆30分钟,经过高速剪切处理,得到固含量40%的浆液,然后喷雾干燥成型后得到喷雾微球,喷雾微球在550℃焙烧60分钟,制得催化裂解催化剂a-3,其配比列于表1;喷雾干燥入口温度540℃,尾气温度170℃。
30.实施例8将去离子水、蒙脱土、sapo-34和2#zsm-5混合打浆80分钟,然后加入co2o3和mno,搅拌30分钟,再加入3#磷硅复合粘结剂,打浆40分钟,经过高速剪切处理,得到固含量45%的浆液,然后喷雾干燥成型后得到喷雾微球,喷雾微球在600℃焙烧40分钟,制得催化裂解催化剂a-4,其配比列于表1;喷雾干燥入口温度540℃,尾气温度170℃。
31.实施例9将去离子水、高岭土、一水氧化铝、reusy和2#zsm-5混合打浆80分钟,然后加入fe2o3,搅拌30分钟,再加入3#磷硅复合粘结剂,打浆40分钟,经过高速剪切处理,得到固含量38%的浆液,然后喷雾干燥成型后得到喷雾微球,喷雾微球在600℃焙烧40分钟,制得催化裂
解催化剂a-5,其配比列于表1;喷雾干燥入口温度560℃,尾气温度180℃。
32.实施例10将去离子水、多水高岭土、拟薄水铝石、fe-zsm-5和2#zsm-5混合打浆60分钟,然后加入fe2o3,搅拌20分钟,再加入4#磷硅复合粘结剂,打浆30分钟,经过高速剪切处理,得到固含量40%的浆液,然后喷雾干燥成型后得到喷雾微球,喷雾微球在550℃焙烧60分钟,制得催化裂解催化剂a-6,其配比列于表1;喷雾干燥入口温度550℃,尾气温度180℃。
33.对比例1按照发明专利cn112138712b实施例4制备磷铝黏结剂,制备方法为:将1.91kg拟薄水铝石(含al2o3,1.19kg)、0.56kg高岭土(干基0.5kg)与3.27kg脱阳离子水打浆30分钟,搅拌下往浆液中加入5.37kg浓磷酸(质量浓度85%),磷酸加入速度为0.04kg磷酸/min/kg氧化铝源,升温至70℃,然后在此温度下反应45分钟,得到d-1磷铝无机粘结剂。
34.对比例2将1340g p2o5含量30%的正磷酸和1000g sio2含量40%的硅溶胶混合后,超声处理2h,得到d-2磷硅复合粘结剂。
35.对比例3与实施例5相比,将其中的1#磷硅复合粘结剂替换为d-1磷铝复合粘结剂,制得对比催化剂d-3,其配比列于表1。
36.对比例4与实施例5相比,将其中的1#磷硅复合粘结剂替换为铝溶胶粘结剂,制得对比催化剂d-4,其配比列于表1。
37.对比例5与实施例5相比,将其中的1#磷硅复合粘结剂替换为30%硅溶胶粘结剂,制得对比催化剂d-5,其配比列于表1。
38.对比例6与实施例5相比,将其中的1#磷硅复合粘结剂替换为d-2磷硅复合粘结剂,制得对比催化剂d-6,其配比列于表1。
39.将实施例5~10及对比例1~6制备得到的将催化剂在800℃、100%水蒸气条件下老化处理10h。取经老化处理的催化剂装入固定床微反反应器中,对表3所述石脑油进行催化裂解,评价条件为反应温度650℃,剂油比15,催化剂装量60克,表4为各催化剂反应结果。
40.表1实施例5~10和对比例3~6制备催化裂解催化剂的配比(以重量干基计)
表2实施例5~10和对比例3~6制备催化裂解催化剂的基本性质
从表2可知,与d-3~d-6催化剂相比,本发明a-1~a-6催化裂解催化剂在满足磨损指数小于2.5%的条件下,具有更大的孔体积。采用4#磷硅粘结剂的a-6催化剂的磨损指数小于采用2#磷硅粘结剂的a-3催化剂,这表明磷酸和硅溶胶混合后的改性温度对催化剂的抗磨强度具有较大影响,较高的改性温度有利于增强黏结剂抗磨强度,且效果优于超声处理(d-6催化剂)。
41.表3石脑油理化性质及组分表4催化裂解催化剂的反应结果
从表4看出,与d-3~d-6催化剂相比,本发明a-1~a-6催化剂,由于具有更高的孔体积,充分发挥了中小孔径择形裂化分子筛的反应性能,其液化气产率和双烯(乙烯+丙烯)收率高,显示了更优的催化裂解反应性能。另外,与a-3催化剂相比,由于a-6催化剂所用磷硅黏结剂的制备温度有所提高,显示了双烯收率增加的特点,表明磷硅黏结剂的制备温度对催化剂的裂解反应性能有较大影响。
42.以上仅为本发明的较佳实施例而已,并不用以限制本发明,凡在本发明的精神和原则之内,所作的任何修改、等同替换、改进等,均应包含在本发明的保护范围之内。