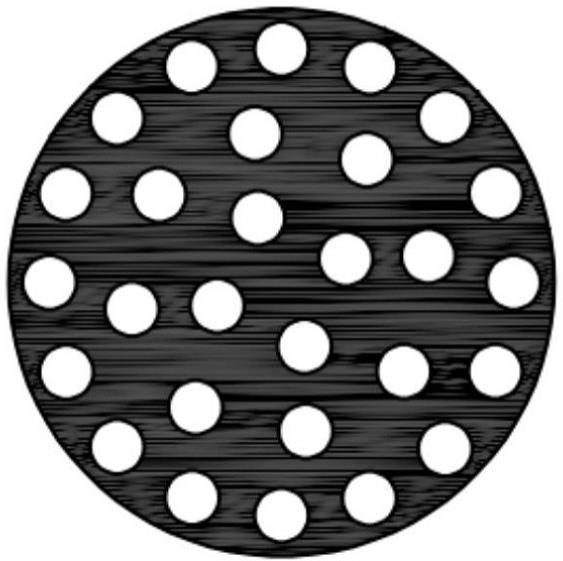
10mm;优选的,预成型体的规格为以下之一:圆柱端面半径为1cm,圆柱体高度为5cm,通孔孔径为1mm;圆柱端面半径为5cm,圆柱体高度为25cm,通孔孔径为5mm;圆柱端面半径为10cm,圆柱体高度为50cm,通孔孔径为10mm。
8.所述预成型中,活性炭粉末与酚醛树脂的重量份比值为4-5:1;活性炭粉末的规格为100-200目;干压成型过程中,干压成型压力为100-120mpa;烧结过程中,烧结温度为1000-1200℃,升温速率为10-15℃/min。
9.所述制浆,将聚丙烯酰胺、十二烷基氨基乙酸投入至去离子水中,搅拌均匀,制得第一溶液;然后将金属氧化物、聚甲基丙烯酸酯、聚乙烯醇、聚丙烯酸钠、氧化钇或氧化钛、第一溶液投入至球磨机内,控制球磨时间为12-48h后,过筛,制得浆料;所述制浆中,金属氧化物为氧化铁、氧化锌、znfe2o4;所述制浆中,去离子水、金属氧化物的重量份比值为1:1-10;金属氧化物、聚丙烯酰胺、聚甲基丙烯酸酯、聚乙烯醇、聚丙烯酸钠、氧化钇或氧化钛、十二烷基氨基乙酸的重量份比值为48-92:0.01-1:1-10:5-20:0.01-1:0.98-10:1-10。
10.所述注浆,浆料在真空度为5-100pa环境下,真空搅拌一定时间后,真空注入至预成型体中,制得注浆后的预成型体;所述注浆中,真空搅拌转速为300-600rpm,真空搅拌时间为30-90min;真空注浆过程中,真空度为0.01-0.08mpa。
11.所述成型,注浆后的预成型体经干燥、微波烧结,制得负载活性炭。
12.所述成型中,干燥温度为80-120℃,干燥时间为10-40min;所述成型中,微波烧结包括:第一升温阶段、第二升温阶段、保温烧结;所述第一升温阶段的温度范围为常温至500℃,升温速率为2-20℃/min;所述第二升温阶段的温度范围为500℃至烧结温度,升温速率为5-25℃/min;所述保温烧结的烧结温度为600-1000℃,保温烧结时间为10-60min。
13.一种负载活性炭,采用前述的制备方法制得。
14.所述负载活性炭在处理炭素纯化炉废气的应用。
15.与现有技术相比,本发明的有益效果为:(1)本发明的负载活性炭,采用预成型的活性炭作为预成型体,将金属氧化物等活性组分预制成浆料后,经真空注浆、微波烧结处理,将金属氧化物等活性组分负载至预成型体上,制得的负载活性炭的活性组分反应活性高,有效提高负载活性炭对含硫废气的处理性能及处理效率,有效提高负载活性炭的长期稳定性。
16.(2)将本发明的负载活性炭装填至炭素纯化炉上,对二氧化硫含量为300mg/cm3,硫化氢含量为50mg/cm3的炭素纯化炉废气进行处理后,废气中二氧化硫含量为11-74mg/cm3,硫化氢含量为0.57-4.1mg/cm3。
17.(3)本发明的负载活性炭用于炭素纯化炉废气的处理中,负载活性炭重复回用60次后,仍能够保持好的废气处理效果,长期稳定性好;经检测,负载活性炭重复回用60次后,对二氧化硫含量为300mg/cm3,硫化氢含量为50mg/cm3的炭素纯化炉废气进行处理后,废气中二氧化硫含量为12-78mg/cm3,硫化氢含量为0.59-4.4mg/cm3。
18.(4)本发明的负载活性炭失效后,可浸泡于氢氧化钠溶液中,其中的金属氧化物,以及含硫废气的反应物等均可与氢氧化钠反应,而预成型体可以保持原有形态,并直接回用至注浆、成型步骤,重新将浆料注入至预成型体中,制得负载活性炭;其预成型体可多次回收利用,有效降低使用成本。
19.(5)本发明的负载活性炭可适用于不同规格的炭素纯化炉,方便维护,有效减少炭素纯化炉停机时间,有效提高对炭素纯化炉的废气处理能力,进而有效提高生产效率。
附图说明
20.图1为预成型步骤制得的预成型体的俯视示意图。
具体实施方式
21.为了对本发明的技术特征、目的和效果有更加清楚的理解,现说明本发明的具体实施方式。
22.实施例1一种负载活性炭的制备方法,具体如下:1、预成型按4:1的重量份比值,将活性炭粉末与酚醛树脂混合均匀,制得预混料;控制干压成型压力为100mpa,将预混料干压成型为坯体;采用1000℃的烧结温度,对坯体进行烧结处理,制得预成型体。
23.烧结处理过程中,升温速率为10℃/min。
24.活性炭粉末的规格为100目。
25.预成型体为圆柱体,且圆柱体的两端面上均匀分布有贯穿圆柱体的通孔。其中,预成型体的规格为:圆柱端面半径为1cm,圆柱体高度为5cm,通孔孔径为1mm。
26.2、制浆分别称取预定量的去离子水、金属氧化物,待用;将聚丙烯酰胺、十二烷基氨基乙酸投入至去离子水中,搅拌0.5h,制得第一溶液;然后将金属氧化物、聚甲基丙烯酸酯(pmma)、聚乙烯醇(pva)、聚丙烯酸钠、氧化钛、第一溶液投入至球磨机内,控制球磨时间为12h;球磨完成后,过20目筛网,制得浆料。
27.其中,金属氧化物为氧化铁。
28.去离子水、金属氧化物的重量份比值为1:1。
29.浆料中,金属氧化物、聚丙烯酰胺、pmma、pva、聚丙烯酸钠、氧化钛、十二烷基氨基乙酸的重量份比值为48:1:10:20:1:10:10。
30.3、注浆将浆料投入至真空搅拌机内,抽真空至真空度为5pa,然后以300rpm的搅拌转速,搅拌30min;然后将预成型体置于真空搅拌机的真空室内,控制真空室真空度为0.01mpa,将浆料真空注浆至预成型体的通孔中,制得注浆后的预成型体。
31.4、成型将注浆后的预成型体置于干燥箱内,控制干燥温度为80℃,干燥10min后;置于微波烧结装置内,经第一升温阶段、第二升温阶段、保温烧结后,制得负载活性炭。
32.其中,第一升温阶段的温度范围为常温至500℃,升温速率为2℃/min。
33.第二升温阶段的温度范围为500-600℃,升温速率为5℃/min;保温烧结温度为600℃,保温时间为10min。
34.微波烧结过程中,微波频率为2.45ghz,微波功率为5kw。
35.所述负载活性炭的应用,将本实施例制得的负载活性炭装填至炭素纯化炉上,对炭素纯化炉废气进行处理。
36.经检测,炭素纯化炉废气中二氧化硫含量为300mg/cm3,硫化氢含量为50mg/cm3。将本实施例的负载活性炭装填至炭素纯化炉上,对炭素纯化炉废气进行处理后,废气中二氧化硫含量为74mg/cm3,硫化氢含量为4.1mg/cm3。
37.实施例2一种负载活性炭的制备方法,具体如下:1、预成型按4.2:1的重量份比值,将活性炭粉末与酚醛树脂混合均匀,制得预混料;控制干压成型压力为105mpa,将预混料干压成型为坯体;采用1100℃的烧结温度,对坯体进行烧结处理,制得预成型体。
38.烧结处理过程中,升温速率为12℃/min。
39.活性炭粉末的规格为150目。
40.预成型体为圆柱体,且圆柱体的两端面上均匀分布有贯穿圆柱体的通孔。其中,预成型体的圆柱端面半径为5cm,圆柱体高度为25cm,通孔孔径为5mm。
41.2、制浆分别称取预定量的去离子水、金属氧化物,待用;将聚丙烯酰胺、十二烷基氨基乙酸投入至去离子水中,搅拌1.5h,制得第一溶液;然后将金属氧化物、聚甲基丙烯酸酯(pmma)、聚乙烯醇(pva)、聚丙烯酸钠、氧化钇、第一溶液投入至球磨机内,控制球磨时间为24h;球磨完成后,过150目筛网,制得浆料。
42.其中,金属氧化物为znfe2o4。
43.去离子水、金属氧化物的重量份比值为1:5。
44.浆料中,金属氧化物、聚丙烯酰胺、pmma、pva、聚丙烯酸钠、氧化钇、十二烷基氨基乙酸的重量份比值为92:0.01:1:5:0.01:0.98:1。
45.3、注浆将浆料投入至真空搅拌机内,抽真空至真空度为80pa,然后以500rpm的搅拌转速,搅拌60min;然后将预成型体置于真空搅拌机的真空室内,控制真空室真空度为0.06mpa,将浆料真空注浆至预成型体的通孔中,制得注浆后的预成型体。
46.4、成型将注浆后的预成型体置于干燥箱内,控制干燥温度为100℃,干燥30min后;置于微波烧结装置内,经第一升温阶段、第二升温阶段、保温烧结后,制得负载活性炭。
47.其中,第一升温阶段的温度范围为常温至500℃,升温速率为20℃/min。
48.第二升温阶段的温度范围为500-1000℃,升温速率为25℃/min。
49.保温烧结温度为1000℃,保温时间为60min。
50.微波烧结过程中,微波频率为2.45ghz,微波功率为5kw。
51.所述负载活性炭的应用,将本实施例制得的负载活性炭装填至炭素纯化炉上,对炭素纯化炉废气进行处理。
52.经检测,炭素纯化炉废气中二氧化硫含量为300mg/cm3,硫化氢含量为50mg/cm3。将本实施例的负载活性炭装填至炭素纯化炉上,对炭素纯化炉废气进行处理后,废气中二氧化硫含量为11mg/cm3,硫化氢含量为0.57mg/cm3。
53.实施例3一种负载活性炭的制备方法,具体如下:1、预成型按5:1的重量份比值,将活性炭粉末与酚醛树脂混合均匀,制得预混料;控制干压成型压力为120mpa,将预混料干压成型为坯体;采用1200℃的烧结温度,对坯体进行烧结处理,制得预成型体。
54.烧结处理过程中,升温速率为15℃/min。
55.活性炭粉末的规格为200目。
56.预成型体为圆柱体,且圆柱体的两端面上均匀分布有贯穿圆柱体的通孔。其中,预成型体的圆柱端面半径为10cm,圆柱体高度为50cm,通孔孔径为10mm。
57.2、制浆分别称取预定量的去离子水、金属氧化物,待用;将聚丙烯酰胺、十二烷基氨基乙酸投入至去离子水中,搅拌3h,制得第一溶液;然后将金属氧化物、聚甲基丙烯酸酯(pmma)、聚乙烯醇(pva)、聚丙烯酸钠、氧化钇、第一溶液投入至球磨机内,控制球磨时间为12-48h;球磨完成后,过200目筛网,制得浆料。
58.其中,金属氧化物为氧化锌。
59.去离子水、金属氧化物的重量份比值为1:10。
60.浆料中,金属氧化物、聚丙烯酰胺、pmma、pva、聚丙烯酸钠、氧化钇、十二烷基氨基乙酸的重量份比值为60:4:6:15:0.5:6:8.5。
61.3、注浆将浆料投入至真空搅拌机内,抽真空至真空度为100pa,然后以600rpm的搅拌转速,搅拌90min;然后将预成型体置于真空搅拌机的真空室内,控制真空室真空度为0.08mpa,将浆料真空注浆至预成型体的通孔中,制得注浆后的预成型体。
62.4、成型将注浆后的预成型体置于干燥箱内,控制干燥温度为120℃,干燥40min后;置于微波烧结装置内,经第一升温阶段、第二升温阶段、保温烧结后,制得负载活性炭。
63.其中,第一升温阶段的温度范围为常温至500℃,升温速率为15℃/min。
64.第二升温阶段的温度范围为500-800℃,升温速率为20℃/min。
65.保温烧结温度为800℃,保温时间为30min。
66.微波烧结过程中,微波频率为2.45ghz,微波功率为5kw。
67.所述负载活性炭的应用,将本实施例制得的负载活性炭装填至炭素纯化炉上,对炭素纯化炉废气进行处理。
68.经检测,炭素纯化炉废气中二氧化硫含量为300mg/cm3,硫化氢含量为50mg/cm3。将本实施例的负载活性炭装填至炭素纯化炉上,对炭素纯化炉废气进行处理后,废气中二氧
化硫含量为36mg/cm3,硫化氢含量为1.9mg/cm3。
69.对比例1采用实施例2的技术方案,其不同在于,省略注浆步骤,将制浆步骤制得的浆料与10倍重量的去离子水混合均匀,制得负载液;将活性炭粉末浸渍至2倍体积的负载液中,40℃温度条件下,浸渍10h后滤出;然后置于干燥箱内100℃干燥30min后,置于微波烧结设备内,按实施例2的第一升温阶段、第二升温阶段、保温方法处理后,制得负载活性炭。
70.其中,活性炭粉末的规格为150目。
71.将制得的负载活性炭置于炭素纯化炉内,对炭素纯化炉废气进行处理,并检测处理后废气中二氧化硫、硫化氢浓度。经检测,对比例1的炭素纯化炉废气经负载活性炭处理后,废气中二氧化硫含量为190mg/cm3,硫化氢含量为13mg/cm3。
72.试验例1分别对实施例1-3、对比例1制得的负载活性炭对炭素纯化炉废气的循环处理能力(即长期稳定性)进行试验,并检测处理后废气中二氧化硫、硫化氢浓度。
73.具体的,分别采用实施例1-3制得的负载活性炭对炭素纯化炉废气循环处理60次后,经检测,实施例1-3的负载活性炭重复回用60次后,仍能够保持好的废气处理效果,长期稳定性好;实施例1-3制得的负载活性炭循环处理60次后,处理后的炭素纯化炉废气中二氧化硫、硫化氢含量,如下表所示:
74.采用对比例1制得的负载活性炭对炭素纯化炉废气循环处理15次后,即无法保持有效的废气处理效果,长期稳定性差;且负载活性炭粉化严重难以回收利用。
75.除非另有说明,本发明中所采用的百分数均为质量百分数。
76.最后应说明的是:以上所述仅为本发明的优选实施例而已,并不用于限制本发明,尽管参照前述实施例对本发明进行了详细的说明,对于本领域的技术人员来说,其依然可以对前述各实施例所记载的技术方案进行修改,或者对其中部分技术特征进行等同替换。凡在本发明的精神和原则之内,所作的任何修改、等同替换、改进等,均应包含在本发明的保护范围之内。