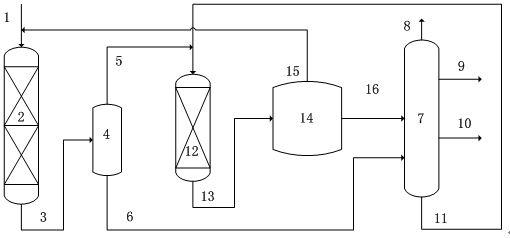
1.本发明涉及一种两段加氢裂化方法,具体地说涉及一种多产重石脑油的两段加氢裂化方法。
背景技术:2.加氢裂化技术是“油化纤”结合的核心,是转化的关键纽带,已经越来越多的受到了人们的关注。特别是在化工原料高需求化的今天,其发挥的作用越来越大。目前国内市场燃油需求量低迷,相对于原油加工量的逐年上涨,燃油产品在炼油产品结构中的比例逐年降低,必然需要将大部分原油转变为市场需求更加旺盛的化工原料。炼油企业产品结构调整趋势是由燃料型向化工型转变已成为必然,需要加氢裂化装置提供更多的催化重整原料和蒸汽裂解制乙烯原料等优质化工原料,伴随装置大型化,最大量生产化工料两段加氢裂化技术开发成为必走之路。
3.在两段加氢裂化技术需求逐步旺盛的今天,其自身在加工原料的同时,产品结构也需调整为最大量生产化工原料,在压减燃料油的同时为催化重整装置和乙烯装置提供优质原料,适应国内市场芳烃和乙烯等基础化工原料需求的快速增长。而对于芳烃的需求,多产重石脑油的两段加氢裂化就成为了最炙手可热的工艺单元,如何更进一步的提高重石脑油的收率为催化重整装置提供优质进料已经成为技术先进性的关键评判。
4.cn201510557589.x公开了一种两段全循环加氢方法,以克服现有加氢装置能耗高,生成的烟气对环境有破坏等缺点。其方法是:新鲜进料与一段反应产物换热并加热后进入一段加氢精制反应器进行反应;一段精制产物与二段混合进料换热后进入一段加氢裂化反应器,一段加氢裂化反应器的一段反应产物再与二段反应产物混合,然后经蒸汽发生器冷却后依次进入反应部分分离系统和分馏部分分离系统进行分离得到加氢产品。
5.cn201210408340.9公开了一种由劣质原料生产优质喷气燃料的加氢裂化方法。劣质原料油进行加氢精制反应,加氢精制流出物进行气液分离,液体进行分馏,分馏得到尾油进行加氢裂化反应,其中裂化反应区包括两种具有不同分子筛含量的加氢裂化催化剂i和ii。所述方法中,裂化反应区内的上游催化剂i具有较强的芳烃转化能力,能够将原料重组分中的芳烃转化为更小分子,并分布到石脑油和航煤馏分中,下游催化剂ii具有较强的烷烃裂化能力。
[0006] cn201110353765.x公开一种生产溶剂油的两段法加氢方法。以生物油脂为原料油,在加氢条件下,原料油与氢气混合通过第一段加氢反应区,加氢生成物流分离得到的富氢气体在第一段循环利用,分离得到的液体进入第二段加氢裂化反应区,第二段加氢生成油分离得到的副氢气体在第二段循环使用,分离得到的液体产品分馏得到各种溶剂油产品。
[0007]
cn201110353593.6发明涉及一种高氮原料两段加氢裂化方法,以高氮重质馏分油为原料,采用两段工艺流程,在加氢精制条件下,重质馏分油原料和氢气混合进入第一段反应区,第一段反应区流出物进入分离系统;第一段反应区流出物分离出的液相与氢气进入
第二段反应区,反应流出物进入分离系统,得到加氢裂化反应产物。
[0008]
上述现有技术中,有对两段工艺能耗进行优化的、有脱除产品芳烃的、也有提高装置运行周期的,但均未涉及如何提升二段的重石脑油收率。
技术实现要素:[0009]
针对现有技术存在的不足,本发明公开一种两段加氢裂化方法,所述方法可以使得二段加氢裂化催化剂在失活速率降低的同时增加优质重石脑油产品的选择性。
[0010]
一种两段加氢裂化方法,包括如下内容:一段加氢裂化反应流出物进入闪蒸分离器,分离出液相流及气相流,所述液相流进入分馏系统分离出重石脑油及尾油,所述气相流同所述尾油混合后进行二段加氢裂化反应,二段加氢裂化反应流出物经气液分离后,分离出的气相作为一段加氢裂化反应的循环氢,液相进入分馏系统分离出气相产品、轻石脑油、重石脑油及尾油。
[0011]
上述方法中,原料油为蜡油或者柴油组分,优选为蜡油,所述蜡油终馏点一般为450~540℃,优选480~530℃,密度一般在0.93g/cm3以下,优选0.92g/cm3以下,氮含量一般在0.08wt%以上优选为0.10%以上,硫含量一般在0.5wt%以上优选0.8 wt%以上。所述的蜡油可以为加工环烷基原油、中间基原油或石蜡基原油得到的各种直馏蜡油或者二次加工的蜡油等,也可以是上述各种蜡油混合后的油品,只要是适合作为加氢裂化装置原料的液相油品均在适用范围内。
[0012]
上述方法中,一段加氢裂化反应和二段加氢反应区装填的加氢裂化催化剂含有加氢活性金属、酸性分子筛组分,所述加氢裂化催化剂可选择现有的各种商业催化剂,也可以按照现有技术制备。
[0013]
上述方法中,所述一段加氢裂化反应设置一段加氢预处理反应区、一段加氢裂化反应区,一段加氢预处理反应区装填加氢预处理催化剂,一段加氢裂化反应区装填加氢裂化反应区。
[0014]
上述方法中,所述一段加氢预处理催化剂包括载体和所负载的加氢活性金属。以催化剂的重量为基准,通常包括元素周期表中第ⅵb族的金属组分,如钨和/或钼以氧化物计量为10%~35%,优选为15%~30%;第
ⅷ
族金属如镍和/或钴以氧化物计量为1%~7%,优选为1.5%~6%。载体为无机耐熔氧化物,可以选自氧化铝、无定型硅铝、二氧化硅、氧化钛等。其中加氢裂化预处理催化剂可以选择现有的各种常规商业催化剂,例如大连石油化工研究院(fripp)研制开发的ff-36、ff-46、ff-56、ff-66等加氢裂化预处理催化剂;也可以根据实际需要按本领域的常识进行制备。
[0015]
上述方法中,所述一段加氢预处理反应区的操作条件如下:操作压力11.5~14.5 mpa,氢油体积比600∶1~1100∶1,体积空速为0.3~5.0 h-1
;优选操作压力12.0~14.0 mpa,氢油体积比600∶1~1000∶1。
[0016]
上述方法中,所述一段加氢裂化反应区装填的加氢裂化催化剂按重量含量计含有10%~30%,优选为15%~25%加氢活性金属氧化物,大于50%的分子筛,所述的加氢活性金属包括wo、mo、co、ni中的一种或几种,所述分子筛包括但不限于y型或usy分子筛。例如大连石油化工研究院(fripp)研制开发的fc-24、fc-46、fc-52等加氢裂化催化剂;也可以根据实际需要按本领域的常识进行制备。
[0017]
上述方法中,所述一段加氢裂化反应区的反应条件为操作压力11.5~14.5 mpa,氢油体积比700∶1~1200∶1,体积空速为0.4~6.0 h-1
;优选操作压力12.0~14.0 mpa,氢油体积比700∶1~1100∶1。
[0018]
上述方法中,所述的闪蒸分离器为可以为闪蒸罐,操作压力为11~14mpa,优选11.5~13.5mpa,温度为80~120℃,优选85~115℃。所述闪蒸条件能够闪蒸出硫化氢、氨气及轻质烃类组分,发明人发现,在轻质烃类的存在下能够抑制硫化氢和氨气的结晶,避免了堵塞管线,影响运转周期。
[0019]
上述方法中,二段加氢裂化反应设置加氢裂化反应区,所述加氢裂化反应区装填的加氢裂化催化剂可以同一段加氢裂化反应采用的加氢裂化催化剂相同,也可以不同。所述的加氢裂化催化剂按重量含量计含有10%~30%,优选为15%~25%加氢活性金属氧化物,大于50%的分子筛,所述的加氢活性金属包括wo、mo、co、ni中的一种或几种,所述分子筛包括但不限于y型或usy分子筛。例如大连石油化工研究院(fripp)研制开发的fc-24、fc-46、fc-52等加氢裂化催化剂;也可以根据实际需要按本领域的常识进行制备。
[0020]
上述方法中,二段加氢反应的反应条件为操作压力10.5~13.5 mpa,氢油体积比700∶1~1200∶1,体积空速为0.5~6.0 h-1
;优选操作压力11.0~13.0 mpa,氢油体积比700∶1~1000∶1。
[0021]
上述方法中,控制一段加氢裂化反应的转化率为50~75%,优选55~70%,二段加氢裂化反应的转化率为50~75%,优选55~70%。所述转化率的定义一段为》177℃馏分的转化程度,[1-(未转化油量/新鲜进料量)]
×
100%,二段为》177℃的循环油单程转化率,一般为{1-[循环油量/(新鲜进料量+循环油量) ]}
×
100%。
[0022]
上述方法中,分馏系统可以采用分馏塔,具体操作条件不进行详细描述,其装置产出的产品主要有气相产品、轻石脑油、重石脑油,比重石脑油更重的馏分作为循环油进行二段加氢裂化反应。
[0023]
本方法通过流程的优化改造提高了炼油企业对于目的产品优质重石脑油的需求,同时也充分利用了硫化氢、氨气以及轻烃组分对于反应过程的优势特点,提升了反应效果。具体来说,不需要额外的气体引入,仅通过一段加氢裂化反应生成的硫化氢、氨气及轻质气体,达到了优化效果。
[0024]
常规的两段加氢裂化装置,二段加氢裂化催化剂由于在无硫条件下运行,其催化剂存在失硫风险,活性的损失也比较快,本发明通过硫化氢的引入,实现了对于二段加氢裂化催化剂的补硫效果,降低了其失活速率,从硫损失角度延长了装置的长周期运行。此外,常规的两段加氢裂化装置,二段加氢裂化催化剂由于在无氨抑制的条件下运行,反应过于剧烈,二次以及多次裂解的副反应较多,重石脑油收率较低,本发明通过氨气的引入,实现了对于二段加氢裂化催化剂的活性抑制作用,降低了副反应发生的概率,从而提高了重石脑油的收率,提高了其上限值。此外,由于轻烃的引入,作为理想组分提升了反应产物的浓度,抑制了重石脑油进一步转化为轻质组分,同时降低了系统的氢分压,提升了重石脑油的芳潜。此外本发明通过闪蒸罐参数的控制,避免了一段重石脑油进入二段反应器,在实现上述优势的同时,最大限度的去除了非理想组分进入二段加氢裂化反应区,从而也进一步的提高了重石脑油的收率,具有很强的实用优势。本发明不需要额外辅助材料的帮助,仅通过自身加工的原料,辅以流程的优化改进,可以实现优质重石脑油的最大化生产过程,十分符
合当下炼油化工企业对于加氢裂化装置产品结构的需求,具有较强的应用价值。
附图说明
[0025]
图1是本发明方法一种具体的流程示意图。
[0026]
其中1为原料油,2为一段加氢反应区,3为一段反应流出物,4为闪蒸分离系统,5为分离后气相,6为分离后液相,7为分馏系统,8为气相产品,9为轻石脑油,10为重石脑油,11为尾油(循环油),12为二段反应器,13为二段反应流出物,14为分离系统,15为循环氢气,16为分离后液相。
具体实施方式
[0027]
下面结合附图对本发明的两段加氢裂化工艺方法进行详细说明,图中简化整合了一些常规且必要的组成部分,如注水系统、循环氢系统、冷氢系统等。
[0028]
如图1所示,本发明的工艺流程如下:常规原料油1与氢气15混合后进入一段加氢反应区2中进行反应,底部排出的反应流出物3进入闪蒸分离系统4中进行气液分离,上部得到气相组分5,底部得到的液相组分6进入后续分馏系统7;在分馏系统7中顶部排出气相产品8,中上部排出轻石脑油9,中下部排出重石脑油10,底部得到的循环油11与气相组分5混合后进入二段反应区12中进行反应,底部排出的反应流出物13进入分离系统14后,得到的气相15与原料油1进行混合,液相16进入分馏系统7后再次进行产品的分馏及循环过程。
[0029]
下面结合实施例和比较例对本发明方法的作用和效果进行进一步说明。本发明上下文中,如果没有特殊说明,%均为质量百分比,对应的切割点均为177℃,实施例均使用本发明方法流程,比较例使用常规的两段加氢裂化流程。原料油的性质见表1,催化剂主要物化性质见表2,操作条件见表3,效果对比见表4。
[0030]
实施例1加工表1中的原料,一段反应区级配使用ff-66加氢裂化预处理剂和fc-46加氢裂化催化剂,二者的装填体积比为3:2,控制一段的转化率为60%,产出的液体组分进入闪蒸分离器,其操作压力为13.5mpa,温度为99℃。分离器底部的液相进入分馏系统,分馏系统底部的液相和分离器顶部的气相一起进入二段反应区,二段装填使用fc-46加氢裂化催化剂催化剂,控制二段的单程转化率为60%,反应后的液相进入后续分离及分馏系统。
[0031]
实施例2加工表1中的原料,一段反应区级配使用ff-66和fc-46加氢裂化催化剂,二者的装填体积比为3:2,控制一段的转化率为60%,产出的液体组分进入闪蒸分离器,其操作压力为13.5mpa,温度为99℃。分离器底部的液相进入分馏系统,分馏系统底部的液相和分离器顶部的气相一起进入二段反应区,二段装填使用fc-46加氢裂化催化剂催化剂,控制二段的单程转化率为70%,反应后的液相进入再后续分离及分馏系统。
[0032]
实施例3加工表1中的原料,一段反应区级配使用ff-66和fc-46加氢裂化催化剂,二者的装填体积比为3:2,控制一段的转化率为50%,产出的液体组分进入闪蒸分离器,其操作压力为13.5mpa,温度为101℃。分离器底部的液相进入分馏系统,分馏系统底部的液相和分离器顶部的气相一起进入二段反应区,二段装填使用fc-46加氢裂化催化剂催化剂,控制二段的单
程转化率为60%,反应后的液相进入再后续分离及分馏系统。
[0033]
实施例4加工表1中的原料,一段反应区级配使用ff-66和fc-46加氢裂化催化剂,二者的装填体积比为3:2,控制一段的转化率为60%,产出的液体组分进入闪蒸分离器,其操作压力为13.5mpa,温度为99℃。分离器底部的液相进入分馏系统,分馏系统底部的液相和分离器顶部的气相一起进入二段反应区,二段装填使用fc-52加氢裂化催化剂催化剂,控制二段的单程转化率为60%,反应后的液相进入再后续分离及分馏系统。
[0034]
实施例5加工表1中的原料,一段反应区级配使用ff-66和fc-46加氢裂化催化剂,二者的装填体积比为3:2,控制一段的转化率为60%,产出的液体组分进入闪蒸分离器,其操作压力为13.5mpa,温度为109℃。分离器底部的液相进入分馏系统,分馏系统底部的液相和分离器顶部的气相一起进入二段反应区,二段装填使用fc-46加氢裂化催化剂催化剂,控制二段的单程转化率为60%,反应后的液相进入再后续分离及分馏系统。
[0035]
比较例1加工表1中的原料,一段反应区级配使用ff-66和fc-46加氢裂化催化剂,二者的装填体积比为3:2,控制一段的转化率为60%,产出的液体组分进入分离及分馏装置后,底部液相进入二段反应区,二段反应采用纯氢气,二段装填使用fc-46加氢裂化催化剂催化剂,控制二段的单程转化率为60%,反应后的液相进入再后续分离及分馏系统。
[0036]
比较例2加工表1中的原料,一段反应区级配使用ff-66和fc-46加氢裂化催化剂,二者的装填体积比为3:2,控制一段的转化率为60%,产出的液体组分进入分离及分馏装置后,底部液相进入二段反应区,二段气相中进行补硫操作,控制硫化氢浓度为1000μl/l,二段装填使用fc-46加氢裂化催化剂催化剂,控制二段的单程转化率为60%,反应后的液相进入再后续分离及分馏系统。
[0037]
比较例3加工表1中的原料,一段反应区级配使用ff-66和fc-46加氢裂化催化剂,二者的装填体积比为3:2,控制一段的转化率为60%,产出的液体组分进入分离及分馏装置后,底部液相进入二段反应区,二段气相中进行补硫及补氨操作,控制硫化氢浓度为1000μl/l,控制氨气浓度为500μl/l,二段装填使用fc-46加氢裂化催化剂催化剂,控制二段的单程转化率为60%,反应后的液相进入再后续分离及分馏系统。
[0038]
表1 原料油性质表表2 催化剂主要物化性质
表3 加氢反应条件表4 不同条件效果对比由上述实例及比较例可以看出,未采用本发明的两段加氢裂化装置会出现重石脑油收率偏低、质量较差以及催化剂失活较快的问题。而采用本发明的加氢裂化装置通过对于一段反应过程气体的合理利用,可以充分发挥其中硫化氢、氨气以及轻烃对于反应过程的助益,实现长周期运行以及优质重石脑油增产的目的。从效果上看,突破常规两段加氢裂化装置重石脑油产率最大化的瓶颈,进一步满足炼化企业对于汽油或者芳烃原料的旺盛需求,同时也最大限度的解决了二段催化剂失硫导致周期偏短,加氢性能降低的问题。
[0039]
在工艺流程上通过增设闪蒸分离器,并辅助于温度控制的手段,降低了优质目的组分的二次反应,提升了目的组分的抑制作用,进一步提高了优质重石收率,可以获得理想的综合加工效果。在实际应用时具有操作费用低、流程简单等优点,具有广泛的应用前景。