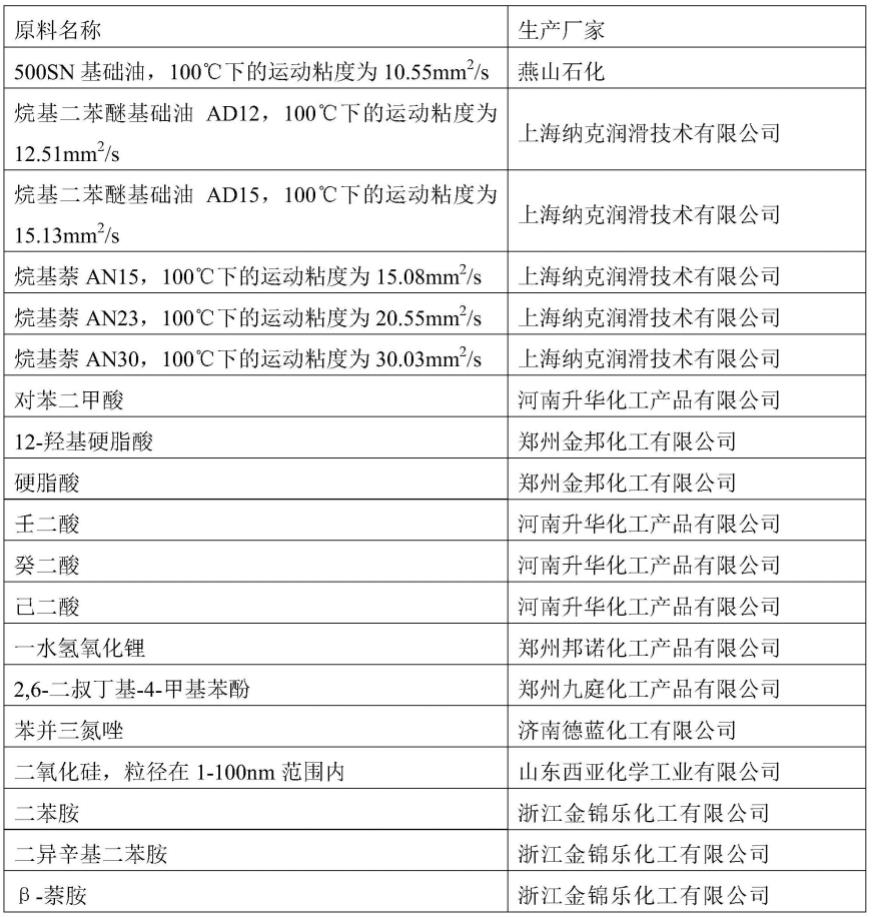
1.本发明涉及润滑脂领域,具体涉及一种具有抗辐射性能的润滑脂组合物及其制备方法。
背景技术:2.当前,全球都在推动温室气体减排,co2减排需求推动着清洁能源的发展,核电在清洁能源中拥有一定优势,同时也是刺激内需、促进经济发展的重要措施之一。核电建设和核电产业发展的黄金期正在到来,核电产业进入了批量化、产业化的发展阶段,前景越来越好。
3.由于核电站工况的特殊性,要求所用润滑脂具有优异的抗辐射性能,国内外学者对抗辐射润滑脂进行了大量的研究。us3083160a报道了使用炭黑稠化矿物油并添加增稠剂制备了一种抗辐射润滑脂。cn1197838a用复合锂皂稠化矿物油,并添加抗氧剂、极压抗磨剂、防锈防腐剂等研制了抗辐射轴承用润滑脂和抗辐射齿轮箱用润滑脂。
4.随着核电站的发展对核电设备用润滑油脂提出了新的要求,一般矿物油基润滑油已不能满足使用要求。cn107805534a用聚脲粉稠化烷基二苯醚,同时添加聚四氟乙烯、二氧化硅、氧化锌,制备了一种核级泵抗辐射高低温专用润滑脂。该脂具有优异的抗高低温性能和稳定性,寿命长,抗氧化性能、抗老化性能、抗辐射性能,同时具有较好的极压抗磨性。cn105018208a选用聚α-烯烃和茂金属pao合成基础油复合为基础油,稠化剂选用甲苯二异腈酸酯和乙酸钙,同时添加抗氧剂、防锈剂、极压抗磨剂、粘附剂等添加剂,制备的润滑脂组合物具有优异的抗高温性能、抗水淋性、泵送性和极压性能。cn104119993a选用全氟聚醚油和聚四氟乙烯制备的机械润滑剂,具有优异的耐高温性能、防腐蚀性能、防燃性能以及防酸防碱抗辐射性能。
5.在现有抗辐射润滑脂中,仍存在着寿命短、抗辐射剂量偏小,极压抗磨性差,胶体安定性差等问题,难以满足核电站内高辐射剂量工况的润滑需求。
技术实现要素:6.本发明的目的是为了克服现有技术存在的问题,提供一种具有抗辐射性能的润滑脂组合物及其制备方法。
7.为了实现上述目的,本发明一方面提供一种具有抗辐射性能的润滑脂组合物,该润滑脂组合物包括基础油、稠化剂和任选的添加剂,其特征在于,所述基础油为重量比是1:0.3-3的烷基萘和烷基二苯醚的混合油,所述添加剂选自结构改进剂、抗氧剂、防锈剂和极压剂中的至少一种。
8.本发明第二方面提供了一种制备润滑脂组合物的方法,该方法包括:将部分基础油、水、酸、锂前驱体与结构改进剂混合进行皂化反应,升温炼制,然后与剩余的基础油和任选的其它添加剂混合,所述其它添加剂选自抗氧剂、防锈剂和极压剂中的至少一种。
9.本发明第三方面提供了由第二方面所述的方法制得的润滑脂组合物。
10.本发明的润滑脂组合物的使用寿命较长,且具有优异的抗辐射性能、极压性能、抗氧化性能、防腐蚀性能、防锈性能,能够满足有辐射工况的润滑要求。
11.在本发明最优选的实施方式中,通过以特定比例配合特定的基础油、稠化剂、结构改进剂、抗氧剂、防锈剂和极压剂,能够获得寿命更长、极压性能、胶体安定性、氧化安定性更优异的润滑脂组合物。
具体实施方式
12.在本文中所披露的范围的端点和任何值都不限于该精确的范围或值,这些范围或值应当理解为包含接近这些范围或值的值。对于数值范围来说,各个范围的端点值之间、各个范围的端点值和单独的点值之间,以及单独的点值之间可以彼此组合而得到一个或多个新的数值范围,这些数值范围应被视为在本文中具体公开。
13.第一方面,本发明提出了一种具有抗辐射性能的润滑脂组合物,该润滑脂组合物包括基础油、稠化剂和任选的添加剂,其特征在于,所述基础油为重量比是1:0.3-3的烷基萘和烷基二苯醚的混合油,所述添加剂选自结构改进剂、抗氧剂、防锈剂和极压剂中的至少一种。
14.根据本发明,优选地,所述烷基萘和烷基二苯醚之间的重量比为1:0.4-2.1。
15.根据本发明,以润滑脂组合物的总重量为基准,所述基础油的含量优选为70-92重量%,更优选为78-90重量%。
16.根据本发明,所述润滑基础油为烷基萘和烷基二苯醚的混合油,所述烷基萘基础油优选100℃运动粘度为10-30mm2/s。所述烷基二苯醚基础油优选100℃运动粘度为10-20mm2/s的润滑基础油。“运动粘度”的测试方法为gb/t 30515。
17.根据本发明,以润滑脂组合物的总重量为基准,所述稠化剂的用量优选为5-20重量%,更优选为8-15重量%。
18.根据本发明的优选实施方式,所用稠化剂为复合锂基稠化剂,由酸与氢氧化锂反应生成,所述酸为高分子酸和低分子酸的混合酸。所述高分子酸为c12-c20脂肪酸和/或c12-c20羟基脂肪酸,可以是月桂酸、棕榈酸、硬脂酸、12-羟基硬脂酸中的一种或多种,优选硬脂酸、12-羟基硬脂酸;所述低分子酸为c2-c11的有机酸,可以是醋酸、丙酸、乙二酸、己二酸、壬二酸、癸二酸、对苯二甲酸中的一种或多种,优选癸二酸、壬二酸、己二酸、对苯二甲酸中的一种或多种。其中高分子酸与低分子酸的摩尔比优选1:0.3-1。高分子酸和低分子酸的总量与氢氧化锂的摩尔比优选为化学计量比,其中氢氧化锂的量也可以过量1-10重量%。氢氧化锂的水溶液中水的含量以使皂化反应能够顺利进行为准,一般是氢氧化锂用量的0.1-10重量倍,优选0.5-5重量倍。虽然稠化剂的获得过程中使用了水,但是润滑脂组合物中水最终将被脱除。
19.根据本发明,以润滑脂组合物的总重量为基准,所述结构改进剂的含量优选为0.1-5重量%,更优选为0.2-0.8重量%。
20.根据本发明,所述结构改进剂优选为二氧化硅。所述二氧化硅的粒径优选在1-100nm范围内。
21.根据本发明,以润滑脂组合物的总重量为基准,所述抗氧剂的含量优选为0.1-3重量%,更优选为0.5-1.5重量%。
22.根据本发明,所述抗氧剂优选为芳香胺型抗氧剂,例如可以是二苯胺、二异辛基二苯胺、β-萘胺、n-苯基-α-萘胺、n-苯基-β-萘胺、n-异丙基-n
’‑
苯基对苯二胺、n-环己基-n
’‑
苯基对苯二胺、n,n
’‑
二-β-萘基对苯二胺和n,n
’‑
二仲丁基对苯二胺中的一种或多种。
23.根据本发明,以润滑脂组合物的总重量为基准,所述防锈剂的含量优选为0.1-10重量%,更优选为0.5-5重量%。
24.根据本发明,所述防锈剂优选有机磺酸盐型防锈剂,如石油磺酸钡、石油磺酸钠、二壬基萘磺酸钡、二壬基萘磺酸锌、环烷酸锌中的一种或多种。
25.根据本发明,以润滑脂组合物的总重量为基准,所述极压剂的含量优选为1-10重量%,更优选为2-5重量%。
26.根据本发明,所述极压剂优选层状结构的固体极压剂,如二硫化钼、二硫化钨、石墨、石墨烯、富勒烯中的至少一种。
27.根据本发明,优选地,所述抗氧剂、防锈剂与极压剂之间的重量比为1:1-5:2-8,更优选为1:2-4:3-6。
28.根据本发明,所述润滑脂组合物仅由以上成分组成。
29.根据本发明,通过按照优选比例配合优选种类的基础油、稠化剂、结构改进剂、抗氧剂、防锈剂和极压剂,能够获得性能更优的润滑脂组合物。
30.本发明的润滑脂可以通过常规的方式制得,只要含有上述成分即可。但优选情况下,所述皂化反应在结构改进剂的存在下进行且所述稠化剂采用原位合成的方式,在结构改进剂的存在下进行皂化反应能够进一步改善润滑脂的胶体安定性,同时缩短皂化时间。因此,第二方面,本发明提出了一种制备润滑脂组合物的方法,该方法包括:将部分基础油、水、酸、锂前驱体与结构改进剂混合进行皂化反应,升温炼制,然后与剩余的基础油和任选的其它添加剂混合,所述其它添加剂选自抗氧剂、防锈剂和极压剂中的至少一种。
31.优选地,所述润滑脂组合物的制备方法包括:将部分基础油、结构改进剂、高分子酸和低分子酸混合、加热,升温至80-95℃,加入氢氧化锂的水溶液进行皂化反应,再升温至190-220℃进行高温炼制,加入剩余的基础油冷却至100-120℃,之后加入必要的添加剂,碾磨成脂,得到成品。其中,皂化反应的时间优选为0.2-1.5小时,所述炼制的时间优选为5-20分钟。
32.本领域技术人员能够根据前述基础油、稠化剂和添加剂的含量获得第二方面的制备方法中各种原料的用量,在此不再赘述。
33.第三方面,本发明提供了根据第二方面所述的方法制得的润滑脂组合物。
34.以下将通过实施例对本发明进行详细描述。以下实施例和对比例中的性能评定按照如下方法进行:
35.测定滴点采用gb/t 3498方法,值越高,说明高温性能越好;
36.测定锥入度采用gb/t 269方法,值越小,说明脂越稠;
37.测定防腐蚀性采用gb/t 5018方法;
38.测定四球机试验pd采用sh/t 0202方法,值越大,说明极压性能越好;
39.测定铜片腐蚀性能采用gb/t 7326方法;
40.测定钢网分油性能采用nb/sh/t 0324方法,值越小,说明分油越少;
41.测定抗氧化性能(氧化安定性)采用sh/t 0325方法,值越小,说明氧化安定性越
好;
42.测定寿命采用sh/t 0773方法,值越大,说明寿命越长;
43.皂化反应的时间以目测制脂釜中的物料完全变成脂状所需的时间计;
44.所用的主要原料来源如表1所示。
45.表1
46.[0047][0048]
实施例1
[0049]
原料组分:烷基二苯醚基础油ad12 42kg;烷基萘an15 42kg;12-羟基硬脂酸8.2kg;壬二酸1.5kg;一水氢氧化锂1.9kg;二氧化硅0.2kg;二苯胺0.8kg;石油磺酸钡2.4kg;二硫化钼2.6kg
[0050]
先将60kg混合基础油、0.2kg二氧化硅、8.2kg的12-羟基硬脂酸和1.5kg壬二酸加入制脂釜中,加热搅拌,升温至80℃加入氢氧化锂水溶液(其中含氢氧化锂1.9kg、水5kg)进行皂化反应0.2h,升温至190℃进行高温炼制20min;加入余下混合基础油降温到105℃后,加入1kg二苯胺、2.4kg石油磺酸钡、2.4kg二硫化钼,搅拌降至室温,通过三辊机研磨2次成脂。产品性能如表2所示。
[0051]
根据投料量计算得到本实施例得到的润滑脂中各个成分的含量见表2。
[0052]
实施例2
[0053]
原料组分:烷基二苯醚基础油ad15 27kg;烷基萘an23 55.1kg;12-羟基硬脂酸8.7kg;癸二酸2.9kg;一水氢氧化锂2.6kg;二氧化硅0.4kg;二异辛基二苯胺0.5kg;石油磺酸钠2kg;二硫化钨3kg
[0054]
先将62kg混合基础油、0.4kg二氧化硅、8.7kg的12-羟基硬脂酸和2.9kg癸二酸加入制脂釜中,加热搅拌,升温至90℃加入氢氧化锂水溶液(其中含氢氧化锂2.6kg、水13kg)进行皂化反应0.5h,升温至200℃进行高温炼制10min;加入余下混合基础油降温到115℃后,加入0.5kg二异辛基二苯胺、2kg石油磺酸钠、3kg二硫化钨,搅拌降至室温,通过三辊机研磨2次成脂。产品性能如表2所示。
[0055]
根据投料量计算得到本实施例得到的润滑脂中各个成分的含量见表2。
[0056]
实施例3
[0057]
原料组分:烷基二苯醚基础油ad12 55kg;烷基萘an30 27kg;硬脂酸6.8kg;己二酸2.8kg;一水氢氧化锂2.8kg;二氧化硅0.6kg;β-萘胺1.2kg;二壬基萘磺酸钡3kg;石墨4.2kg
[0058]
先将60kg混合基础油、0.6kg二氧化硅、6.8kg的硬脂酸和2.8kg己二酸加入制脂釜中,加热搅拌,升温至85℃加入氢氧化锂水溶液(其中含氢氧化锂2.8kg、水10kg)进行皂化反应0.3h,升温至205℃进行高温炼制15min;加入余下混合基础油降温到110℃后,加入1.2kg的β-萘胺、3kg二壬基萘磺酸钡、4.2kg石墨,搅拌降至室温,通过三辊机研磨2次成脂。
产品性能如表2所示。
[0059]
根据投料量计算得到本实施例得到的润滑脂中各个成分的含量见表2。
[0060]
实施例4
[0061]
原料组分:烷基二苯醚基础油ad15 52kg;烷基萘an23 26kg;硬脂酸7.3kg;对苯二甲酸4.2kg;一水氢氧化锂3.4kg;二氧化硅0.8kg;n-苯基-β-萘胺1.5kg;二壬基萘磺酸锌3kg;石墨烯4.7kg
[0062]
先将60kg混合基础油、0.8kg二氧化硅、7.3kg的硬脂酸和4.2kg对苯二甲酸加入制脂釜中,加热搅拌,升温至95℃加入氢氧化锂水溶液(其中含氢氧化锂3.4kg、水10kg)进行皂化反应0.5h,升温至205℃进行高温炼制10min;加入余下混合基础油降温到110℃后,加入1.5kg n-苯基-β-萘胺、3kg二壬基萘磺酸锌、4.7kg石墨烯,搅拌降至室温,通过三辊机研磨2次成脂。产品性能如表2所示。
[0063]
根据投料量计算得到本实施例得到的润滑脂中各个成分的含量见表2。
[0064]
实施例5
[0065]
按照实施例1的方法制备润滑脂,不同的是,二苯胺的用量为1kg;石油磺酸钡的用量为4kg;二硫化钼的用量为0.8kg。产品性能测试结果以及根据投料量计算得到本实施例得到的润滑脂中各个成分的含量见表2。
[0066]
实施例6
[0067]
按照实施例2的方法制备润滑脂,不同的是,二异辛基二苯胺的用量为1kg;石油磺酸钠的用量为3.5kg;二硫化钨的用量为1kg。产品性能测试结果以及根据投料量计算得到本实施例得到的润滑脂中各个成分的含量见表2。
[0068]
实施例7
[0069]
按照实施例3的方法制备润滑脂,不同的是,β-萘胺的用量为1kg;二壬基萘磺酸钡的用量为1kg;石墨的用量为7kg。产品性能测试结果以及根据投料量计算得到本实施例得到的润滑脂中各个成分的含量见表2。
[0070]
实施例8
[0071]
按照实施例4的方法制备润滑脂,不同的是,n-苯基-β-萘胺的用量为1kg;二壬基萘磺酸锌的用量为6kg;石墨烯的用量为1.2kg。产品性能测试结果以及根据投料量计算得到本实施例得到的润滑脂中各个成分的含量见表2。
[0072]
实施例9
[0073]
按照实施例1的方法制备润滑脂,不同的是,不加入二氧化硅,具体如下:
[0074]
原料组分:烷基二苯醚基础油ad12 42kg;烷基萘an15 40kg;12-羟基硬脂酸8.2kg;壬二酸1.5kg;一水氢氧化锂1.9kg;二苯胺1kg;石油磺酸钡3kg;二硫化钼4kg
[0075]
先将60kg混合基础油、8.2kg的12-羟基硬脂酸和1.5kg壬二酸加入制脂釜中,加热搅拌,升温至80℃加入氢氧化锂水溶液(其中含氢氧化锂1.9kg、水5kg)进行皂化反应1.5h,升温至190℃进行高温炼制20min;加入余下混合基础油降温到105℃后,加入1kg二苯胺、3kg石油磺酸钡、4kg二硫化钼,搅拌降至室温,通过三辊机研磨2次成脂。产品性能如表2所示。
[0076]
根据投料量计算得到本实施例得到的润滑脂中各个成分的含量见表2。
[0077]
对比例1
[0078]
按照实施例1的方法制备润滑脂,不同的是,将烷基二苯醚基础油ad12和烷基萘an15均替换为500sn基础油。产品性能测试结果以及根据投料量计算得到本实施例得到的润滑脂中各个成分的含量见表2。
[0079]
实施例10
[0080]
按照实施例2的方法制备润滑脂,不同的是,替换抗氧剂、防锈剂与极压剂,具体如下:
[0081]
原料组分:烷基二苯醚基础油ad15 27kg;烷基萘an23 55.1kg;12-羟基硬脂酸8.7kg;癸二酸2.9kg;一水氢氧化锂2.6kg;二氧化硅0.4kg;2,6-二叔丁基-4-甲基苯酚0.5kg;苯并三氮唑2kg;偏硼酸钾3kg
[0082]
先将62kg混合基础油、0.4kg二氧化硅、8.7kg的12-羟基硬脂酸和2.9kg癸二酸加入制脂釜中,加热搅拌,升温至90℃加入氢氧化锂水溶液(其中含氢氧化锂2.6kg、水13kg)进行皂化反应0.5h,升温至200℃进行高温炼制10min;加入余下混合基础油降温到115℃后,加入0.5kg的2,6-二叔丁基-4-甲基苯酚、2kg苯并三氮唑、3kg偏硼酸钾,搅拌降至室温,通过三辊机研磨2次成脂。产品性能如表2所示。
[0083]
根据投料量计算得到本实施例得到的润滑脂中各个成分的含量见表2。
[0084]
表2
[0085]
烯烃(pao合成基础油,来源上海纳克润滑技术有限公司)。产品性能测试结果见表3。
[0102]
对比例3
[0103]
按照实施例2的方法制备润滑脂,不同的是,烷基萘的用量为13.1kg,烷基二苯醚的用量为69kg。产品性能测试结果见表3。
[0104]
表3
[0105][0106]
通过以上结果可以看出,采用本发明优选实施方式的实施例1-4具有更长的寿命、更优的胶体安定性、极压性能、氧化安定性。从实施例1-4与实施例5-8、实施例10的结果可以看出,特定的抗氧剂和防锈剂、极压剂以特定比例复配使用具有协同效果,使得润滑脂产品具有优异的抗辐射性、防锈性、极压性、胶体安定性和抗氧化性能。从实施例1-4与实施例11-13可以看出,基础油、稠化剂和添加剂以特定的种类和量配合能够获得性能更优的润滑脂。从实施例1-4与实施例14-15可以看出,皂化反应在特定量的二氧化硅存在下进行能够获得性能更优的润滑脂,在二氧化硅的存在下进行皂化反应能够进一步改善润滑脂的胶体安定性,并同时缩短皂化时间。
[0107]
以上详细描述了本发明的优选实施方式,但是,本发明并不限于此。在本发明的技术构思范围内,可以对本发明的技术方案进行多种简单变型,包括各个技术特征以任何其它的合适方式进行组合,这些简单变型和组合同样应当视为本发明所公开的内容,均属于本发明的保护范围。