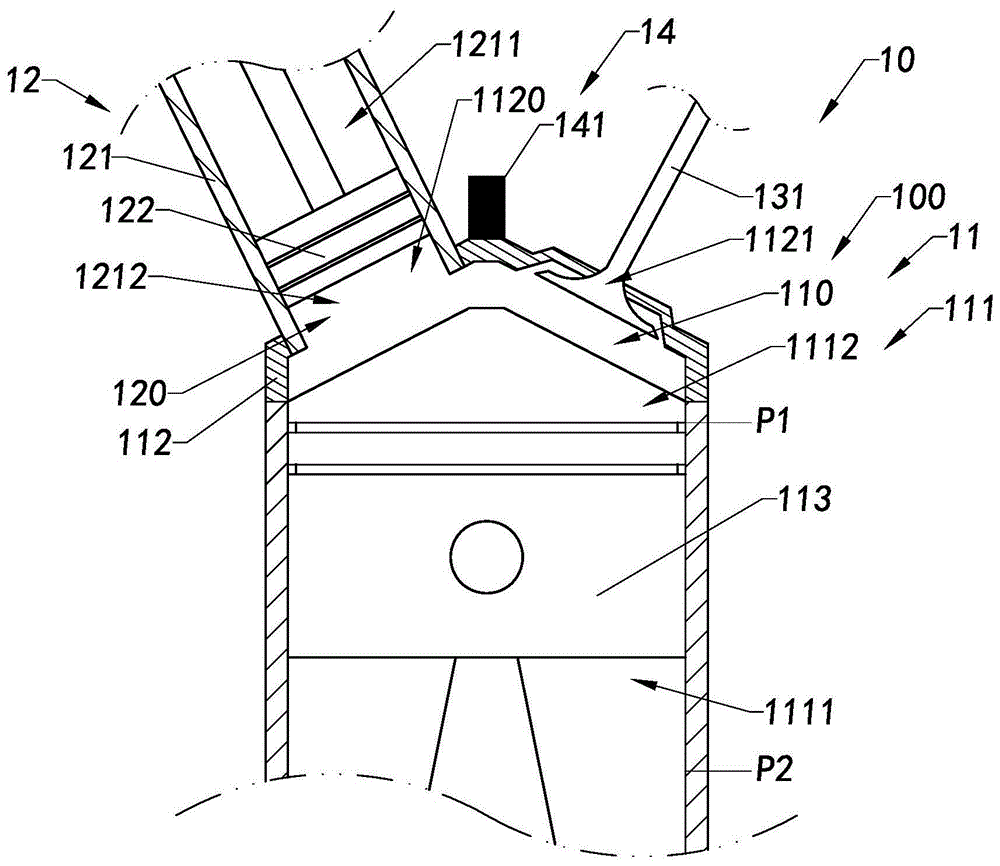
本发明涉及到移动设备领域,尤其涉及到一发动机和机械设备及应用。
背景技术:
:内燃机是一种典型的提供动力的机械,其能够将燃料燃烧释放出的热能直接转换成动力。而汽车、摩托车、轮船、火车以及飞机等配置有发动机的机械设备存在一个很大的问题在于不同工况下时整个汽车系统的效率低下。以常见的内燃机式汽车为例进行说明。导致汽车系统效率低下的原因之一在于内燃机式汽车在最佳效率工作时的输出功率远大于汽车所需要的行驶阻力的需求,因此汽车发动机只能降低效率和行驶阻力匹配。而内燃机式汽车预留的后备功率非常大,特别是在低车速时,负载率非常小。虽然可以兼顾汽车的动力性能和载重性能,但是汽车发动机实际的效率仍非常低。以汽油为燃料的汽车主要是空燃比不变,通过减少进气量,降低压缩比,以降低输出功率。以柴油为燃料的汽车主要是压缩比不变,通过减少油量,增大空燃比,以降低输出功率。这都使得发动机的效率下降,并且发动机效率损耗增大,同时汽车无法在压缩比和空燃比最佳状态下工作,使得燃烧时间延长,汽车效率也会下降。进一步地,内燃机式汽车的发动机最佳效率区的转速范围很小,它的最大转速和最小转速比值为2~3,无法通过大范围的调整转速,高效的改变输出功率。而汽车不同工况下阻力功率变化的范围很大,汽车发动机只能降低效率和行驶阻力匹配使在最佳效率区范围之外工作的发动机效率将会明显下降。另一个问题在于,整个汽车系统十分复杂,提高系统效率受到众多因素的影响,单独提高一个因素会影响到其他的因素,使得最后系统效率并不一定得到提高。技术实现要素:本发明的一目的在于提供一发动机和机械设备及应用,其中所述机械设备在不同工况下能够以高系统效率工作。本发明的另一目的在于提供一发动机和机械设备及应用,其中所述机械设备能够在以高系统效率工作时,保证动力性能。本发明的另一目的在于提供一发动机和机械设备及应用,其中不论进气量多少,所述机械设备能够接近最佳压缩比和空燃比工作,使得发动机效率损耗系数接近于1。本发明的另一目的在于提供一发动机和机械设备及应用,其中所述机械设备能够降低后备功率,以提高系统效率,特别是在低速匀速区。本发明的另一目的在于提供一发动机和机械设备及应用,其中所述机械设备的发动机最佳效率状态下的输出功率,更接近行驶阻力功率曲线。本发明的另一目的在于提供一发动机和机械设备及应用,其中所述机械设备的轻载损耗能够被降低。本发明的另一目的在于提供一发动机和机械设备及应用,其中所述机械设备的变速器损耗能够被降低。附图说明图1是根据本发明的一实施例的一种可变燃烧室体积的发动机的结构示意图。图2示出了根据本发明的上述实施例的所述可变燃烧室体积的发动机的主气缸的主气缸盖的俯视示意图。图3a示出了根据本发明的上述实施例的所述可变燃烧室体积的发动机的辅助气缸的结构示意图。图3b示出了根据本发明的上述实施例的所述辅助气缸的工作示意图。图4a示出了根据本发明的上述实施例的所述辅助气缸的一个变形实施方式。图4b示出了根据本发明的上述变形实施方式的所述辅助气缸的作动机构中传动机构的凸轮的结构示意图。图4c示出了根据本发明的上述变形实施方式的所述辅助气缸的工作示意图。图5示出了配置有根据本发明的上述实施例的所述可变燃烧室体积的发动机的机械设备的一个示例。图6示出了根据本发明的一实施例的一种可变燃烧室体积的发动机的操作方法的示意图。图7是车辆在不同速度下的行驶阻力功率、百公里阻力功耗、风阻力功率一级阻力功率变化示意图。图8是车辆在不同速度下的阻力功率百分比和阻力百分比变化的曲线图示意图。图9是国五尾气排放测试标准示意图。图10是传统的汽车系统的发动机的最大输出功率和汽车行驶阻力功率变化的曲线图示意图。图11根据发明的一较佳实施例所述的所述高效率汽车系统在不同车速匀速行驶的各项数据变化示意图。具体实施方式以下描述用于揭露本发明以使本领域技术人员能够实现本发明。以下描述中的优选实施例只作为举例,本领域技术人员可以想到其他显而易见的变型。在以下描述中界定的本发明的基本原理可以应用于其他实施方案、变形方案、改进方案、等同方案以及没有背离本发明的精神和范围的其他技术方案。本领域技术人员应理解的是,在本发明的揭露中,术语“纵向”、“横向”、“上”、“下”、“前”、“后”、“左”、“右”、“竖直”、“水平”、“顶”、“底”、“内”、“外”等指示的方位或位置关系是基于附图所示的方位或位置关系,其仅是为了便于描述本发明和简化描述,而不是指示或暗示所指的装置或元件必须具有特定的方位、以特定的方位构造和操作,因此上述术语不能理解为对本发明的限制。可以理解的是,术语“一”应理解为“至少一”或“一个或多个”,即在一个实施例中,一个元件的数量可以为一个,而在另外的实施例中,该元件的数量可以为多个,术语“一”不能理解为对数量的限制。根据本发明的一方面,本发明设计了一内燃机式的高效率机械设备,其中所述高效率机械设备能够克服目前的内燃机式机械设备的缺点,在不同的工况下,能够以较高效率下进行工作。本发明设计的所述内燃机式的高效率机械设备,可被实施为多种移动设备,如摩托车、轮船、火车等,在此以高效率汽车系统为例进行描述。本领域技术人员应当理解的是,所述高效率汽车系统仅为所述高效率机械设备的一种实施方式,仅为举例说明并且本发明的所述高效率机械设备并不限制于所述高效率汽车系统。目前市场上的内燃机式汽车的发动机在其最佳效率区工作时对应的转速范围很小,发动机的最大转速和最小转速的比值,也就是转速比一般为2到3,无法通过大范围的调整转速,高效的改变输出功率。而汽车不同工况下阻力功率变化的范围很大,因此只能够通过降低发动机的效率降低输出功率。例如,假定传统汽油机最大进气量的最佳效率为40%,转速范围为1000~6000r/min,转速比为6,假定发动机最佳效率状态下对应转速范围为1750~4500r/min,此转速范围之外,汽油机效率明显下降,是一个类似不规则的倒盆状效率曲线。换档除1档外,一般在1800~2500r/min,1000r/min、最大进气量时,压缩比或者空燃比无法在最佳状态下工作,故传统汽车发动机最佳效率状态下的转速比为2~3。轿车车速10~60km/h时,负载率约为0.02~0.18%,实际小进气量下,汽油机的效率约为14~25%,轿车实际的系统效率为4~20%,它反映的就是系统效率存在提升的巨大潜力。在此以目前的内燃机式汽车的运行状态为例进行说明,并且值得注意的是,在对于汽车系统,不管是目前的内燃机汽车系统还是本发明提供的高效率的汽车系统进行分析之前,首先需要建立如何对于一个汽车系统进行有效的分析的方法。汽车系统本身十分复杂,由于各种复杂的工况和运行状态。在本发明中,着重考察汽车的最大阻力功率比、汽车在最小载重量的最大加速时间以及汽车在最小载重量的水平均速行驶的状态。汽车的最大阻力功率比非常大,反映的就是汽车系统中发动机所要面对的巨大的负荷变化,是评价系统效率提高的障碍因素。汽车在最小载重量的水平匀速行驶下,假定市郊混合平均车速为50km/h,是评价系统效率的工况因素。汽车在最小载重量的最大加速时间是评价系统的动力性因素,反映了汽车的最大动力性及载重能力。首先对于为何汽车的最大阻力功率比是评价系统效率提高的障碍因素进行说明。在此之前,要明确的一个概念是,影响到汽车效率的因素是多个,发动机本身的因素、汽车发动机之外的因素、比如说风阻、行驶阻力功率、变速器等因素,其中有三个因素对于汽车效率的影响最为关键,分别为发动机效率损耗系数,变速器损耗系数、发动机轻载损耗系数。汽车的驱动功率是指发动机驱动车轮效率的功率。发动机的有效功率是指发动机曲轴传出来的实际输出功率,也就是发动机的实际输出功率,不特别说明的情况下也指发动机的输出功率。发动机的指示功率是指燃料的燃烧对活塞所作的功。发动机最佳效率状态是指发动机在最佳压缩比、空燃比机最佳转速范围内,发动机的效率最高,在固定转速下,发动机的有效功率最大,也就是满载有效功率。在发动机最佳效率时,机械损耗功率约占发动机指示功率10~30%。汽车的系统效率≈发动机的最佳效率*汽车系统总损耗系数=发动机实际效率*变速器损耗系数*轻载损耗系数=汽车驱动功率/汽车的燃料消耗,其中,发动机实际效率=发动机的最佳效率*发动机效率损耗系数,发动机的最大输出功率=汽车的燃料消耗*发动机的最佳效率,发动机的有效功率=发动机的最大输出功率*发动机效率损耗系数。多数情况下可变体积燃烧室发动机,使得发动机的实际效率≈发动机最佳效率,发动机效率损耗系数≈1。也就是说,汽车的系统效率≈发动机的最佳效率*发动机效率损耗系数*变速器损耗系数*轻载损耗系数。对于汽车的固定一个发动机而言,发动机的最佳效率一般是固定的,那么对于汽车系统效率的影响最关键的三个因素就是发动机效率损耗系数、变速器损耗系数以及轻载损耗系数。汽车的指示功率=有效功率+机械损耗功率。在发动机的最佳效率下,负载率=阻力功率/发动机最大有效功率,后备功率=发动机最大有效输出功率-阻力功率。当汽车的驱动功率等于汽车的行驶阻力功率时,汽车水平匀速行驶。假定汽车水平匀速行驶,暂时忽略汽车内部的耗损,比如说传动系的摩擦损耗,发动机的轻载损耗对于小负荷的影响,汽车电子电器的功率消耗等,此时发动机输出功率等于行驶阻力功率。这里只考虑滚动阻力系统、空气阻力系统、迎风面积对行驶阻力的影响,并且假设三个系数是固定的,通篇均采用如下计算方法。车速下的行驶阻力功率及百公里阻力功耗的公式组如下:pz=f*v→pz=(mg+(c*a*ρ/2)*v^2)*v,wz=pz/v*100km,wz∝f,其中pz代表阻力功率,单位为w;f代表阻力,单位为n;v代表速度,单位为m/s;m代表车辆质量,单位为kg;g代表重力加速度,单位为n/kg;c代表空气阻力系数;a代表迎风面积,单位为m2;ρ代表空气阻力空气密度系数,单位为ns2/m4;wz代表百公里阻力功耗,单位为kwh。假定一车辆,比如说标致3008,这一车辆的整车最小质量(整备质量)m=1540kg,整车最大质量为2000kg,g=9.8n/kg、滚动阻力系数f=0.015、空气阻力系数c=0.338、迎风面积a=2.46m2、空气阻力空气密度系数ρ=1.2258ns2/m4。该车辆在不同速度下的行驶阻力功率和百公里阻力功耗如下表1-1所示:v的单位为m/s;pz的单位为w;wz的单位为kwh。v1020304050607080100110120150200pz0.641.352.23.24.56.18.110.617.221.526.446100wz6.46.77.38.09.010.211.613.317.219.52230.950表1-1参考表1-1所示,车辆最大和最小车速比为200/10=20,对应的百公里阻力功耗比值为50/6.4=7.8,它反映的就是扭矩变化比。汽车最大阻力功率比bz,指在不使用离合器下,最大车速的最大载重量的最大阻力功率与最小车速的最小载重量的最小阻力功率的比,bz=162,汽车最大阻力功率比的大小由车速与载重量决定,其中轿车主要受到车速的影响,卡车还受载重量的影响,卡车的最大阻力功率比要小于上述轿车。参考上述附图7和图8所示,滚动阻力功率和车速是线性的,风阻力功率受到车速影响是非线性的。汽车的阻力功率变化范围非常大,单一通过转速变化也无法使得输出功率和负荷严格匹配。可以观察到现有汽车系统中存在的一个客观问题在于,最大阻力功率比非常大。最大阻力功率比bz反映的就是汽车系统巨大的负荷变化,它是评价系统效率提高的障碍因素。最大阻力功率比bz的变化越大,说明汽车系统的效率提高的阻碍越大,因为汽车系统需要通过降低效率的方式降低输出功率,从而使得汽车的输出功率和行驶阻力功率相匹配。汽车系统的系统效率受到多种因素的牵制,通过单一的方法以及发动机系统内的因素,无法使得发动机在最佳效率状态下的输出功率和负荷严格匹配。降低所述车辆最大阻力功率的直观办法是,提高最小车速,降低最高速度,降低车身重量以及特别是:减少风阻系数。百公里阻力功耗反映车速越高消耗的功率越大,百公里阻力功耗和阻力成正比。其次,对于选择汽车在最小载重量的水平匀速行驶下,假定市郊混合平均车速为50km/h,为评价系统效率的工况因素,并选择汽车在最小载重量的最大加速时间为评价系统的动力性因素,下面进行具体地说明。汽车主要在城市路况下,为了便于系统效率的比较,选择一个参考车速。根据国五尾气排放测试标准如下图9所示.城市路口为郊区及市区混合,假定轿车的郊区平均车速为75km/h(50~100km/h),占1/3,市区平均车速35km/h(20~50km/h),占2/3,计算郊区和市区混合车速为(75km/h+35km/h*2)/3≈48km/h,故假定城市路况下,市郊混合车速为50km/h。进一步地,汽车拥有各种复杂的工况,需要选择一种工况作为效率分析的切入点。汽车由加速、匀速、减速、怠速空转四中行驶状态组成。匀速行驶状态还可以分重载、轻载、高车速、低车速以及怠速行驶,还有最大法规车速、常用主要工况、不常用的特殊工况等。路面摩擦阻力和风速风向等影响了汽车的工况。汽车的工况非常的复杂。最大法规车速指轿车高速公路最高行驶车速120km/h,卡车车速90km/h,是高效率汽车系统的车速界限因素,用于选择可变体积燃烧室工作在经济区或动力区。汽车常用工况指小于等于最大法规车速的匀速车速、标称载重量内及小加速的变化。不常用工况指大于最大法规车速、超载、大加速度等。汽车的驱动功率等于汽车的行驶阻力功率,使得汽车水平匀速行驶。汽车驱动功率大于汽车的行驶阻力功率,使得汽车水平加速行驶。汽车的驱动功率小于汽车的行驶阻力功率,使得汽车水平减速行驶。汽车驱动功率始终等于零,发动机怠速空转,汽车静止。此处汽车的驱动功率是指发动机输出经传动系驱动车轮旋转,用以克服行驶阻力,推动汽车行驶所消耗的功率。固定车速下,轿车从最小载重量到最大载重量的阻力功率变化不大,故轿车最小载重量水平均速行驶是最基本的行驶方法,是本文中选取的效率比较的数据组,其中,50km/h车速是本文中系统效率方案改进前后的比较点,是评价系统效率的工况因素。对于卡车来说,在固定车速下,卡车从空载到满载的阻力功率变化很大,可以考虑空载及满载2个的效率比较数据组,但是卡车的实际平均载货状态很难评价,方案改进前后,效率提高很难对比。汽车在固定车速下,固定档位,从最小载重量逐步增加载重量到最大载重量,从匀速逐步增大加速度到最大加速度,以及连接上坡,发动机的后备功率减小,负载率增加,负荷增大,发动机的效率逐步增大,也反映出了汽车的动力性和载重能力。进一步地,最大加速度时,除汽油发动机采用涡轮增压外,发动机的效率最高,用于比较传统汽车和高效率汽车的加速时间,无需效率比较。因此可以采用最大加速度来评价系统的动力性因素,反映汽车的最大动力性和载重能力。路面摩擦阻力及风速风向影响等,载重量变化,坡度变化等因素都可以看成固定车速下动力性的变化因素。通过这样的方式,就可以将对于汽车复杂工况的分析,集中于分析在不同车速下,水平匀速行驶状态下的系统效率和最大加速时间两个关键的指数上。汽车减速行驶分3种类型,消耗动能的刹车减速、借助动能的滑行减速以及提供动力的供油减速,其中,固定车速下的供油减速及供油下坡行驶,出现的概率较小,发动机的效率都比匀速低,传统汽车驾驶时需要避免。通过上述的分析,可以建立起一个系统效率的评价模型,从而能够在这一个模型下对于汽车系统进行有效的评价。进一步地,前文中提到汽车系统效率≈发动机的最佳效率*发动机效率损耗系数*变速器损耗系数*轻载损耗系数,其中发动机效率损耗因素、变速器损耗系数以及轻载损耗系数是影响到汽车系统效率的最关键的三个因素。具体对于变速器损耗和发动机轻载损耗对于汽车系统的影响进行分析,如下所示:第一、对于变速器损耗的分析:汽车系统中传动系效率主要由变速器决定,变速器的损耗系数与档位的速比有直接关系,同时自动档变速器内部有复杂的处理机构,损耗大于手动档。轿车一般为4~10速变速器,卡车一般为5~16速变速器。为了便于分析,假定传统轿车采用自动变速器,卡车采用手动变速器。假定6at自动变速器的最低~最高档的损耗系数为0.88~0.96,6档手动档变速器的最低~最高档的损耗系数为0.92~0.98。假定6at自动变速器档位与损耗系数的关系为如下数据表(1-5):6at档位123456速比4.1482.371.5561.1550.8590.686变速器损耗系数0.880.920.940.950.960.96表1-5通过参考表1-5可以发现,通过提高档位可以在一定程度上增大变速器损耗系数。第二、对于轻载损耗系数的分析:发动机系统的机械损耗主要有三大类。第一类与输出扭矩或有效功率有关,叫它扭矩损耗,如活塞靠近上止点,气体压缩压力越大,燃烧压力越大,燃烧室越大,摩擦力就越大;第二类与发动机的转速有关,叫它转速损耗,如活塞的流体动力润滑摩擦力损耗,转速越大,损耗越大;第三类是发动机的附件的功率损耗,如水泵、风机、机油泵等辅助机械消耗的功率,它可以变相的看成主要是扭矩损耗。另外,如曲柄、连杆以及轴承组成的机构的摩擦损失等,两者都有。为了便于分析,假定扭矩损耗与输出扭矩成正比,转速损耗与转速成正比,如果有效功率或输出扭矩为0,那么扭矩损耗接近为0。假定汽油机的机械损耗占指示功率的10.7%,占有效功率的12%,其中满载扭矩损耗8%,满载转速损耗4%。当固定转速下,降低有效功率时,轻载扭矩损耗与有效功率基本同比例下降,不影响发动机的实际效率值,而轻载转速损耗与有效功率是反比方向,它影响发动机的实际效率值,轻载转速损耗是机械损耗间接派生的一个轻载损耗影响量,包含轻载损耗功率及轻载损耗系数。当发动机输出功率小于最大有效功率时,转速越高,轻载损耗影响越大,阻力功率越小,轻载损耗影响也越大,有效功率或阻力功率为零,轻载损耗影响最大。传统汽车低速行驶时,转速范围很小,阻力功率很小,无法大幅度降低转速,轻载损耗系数很小,直接使系统效率下降。同样柴油机也是如此。相反,如果增大转速比,降低转速,系统效率就提高了。例如,假定汽油机在最佳效率40%下,转速范围为1750~3500r/min,3500r/min时,最大有效功率为60kw,满载扭矩损耗4.8kw,满载转速损耗2.4kw,1750r/min时,最大有效功率为30kw,满载扭矩损耗为2.4kw,满载转速损耗为1.2kw,此时发动机的效率与轻载损耗影响没有关系。例如,质量1.54吨的轿车,车速20km/h,阻力功率仅为1.35kw。如果1750r/min下,有效功率为0,汽油机轻载损耗功率为1.2kw,可以理解为空档怠速状态。如果有效功率小于30kw,轻载损耗影响就存在了。如果阻力功率为30kw,轻载损耗功率=(1-30/30)*30*4%=0,轻载损耗系数=1.35/(0+1.35)=100%,不存在轻载损耗影响。阻力功率为1.35kw,轻载损耗功率=(1-1.35/30)*30*4%=1.15kw,轻载损耗系数=1.35/(1.15+1.35)=54%。传统的办法是使用更小排量发动机,降低固定转速下的最大有效功率,使轻载损耗影响下降。另一种方法是降低转速,如果最小转速下降到500r/min,轻载损耗功率=(1-1.35/(30*500/1750))*30*500/1750*4%=0.29kw,轻载损耗系数=1.35/(0.29+1.35)=82%,轻载损耗影响大幅度下降。因此,可以得出的结论是,在低速行驶区,受轻载损耗影响,汽车的系统效率明显下降。提高系统效率,从降低轻载损耗影响出发,降低发动机的转速很重要,这也是一些船用柴油发动机采用转速106r/min的原因。本发明提供了一高效率汽车系统相比于传统的汽车而言,所述高效率汽车系统采用可变体积燃烧室,使得发动机始终能够在最佳效率状态下工作。具体地说,所述高效率汽车系统在小负荷或小扭矩时,使用小燃烧室的小排量发动机,大负荷或大扭矩时,使用大燃烧室的大排量发动机,进气量及转速随负荷变化,始终使压缩比及空燃比在最佳状态下工作,发动机的效率就可以被提高。传统的汽车系统方案a如下:一轿车,采用6at变速器,总变速比为6.05,载重量1.54~2吨,6000r/min时,发动机最大输出功率为100kw。最佳效率区的转速范围为1750~3500r/min,转速1000~6000r/min,对应车速5.5~200km/h,发动机转速比*总变速比=车速比≌变速器转速比=36.3,当车速小于100km/h时,后备功率很大,整个汽车系统效率较低。传统系统最大进气量下,1000r/min时,发动机效率为15%,6000r/min为35%,1750~3500r/min为40%。此处进气量的大小用实际进气量和发动机的气缸容积的比值衡量,假定进气量减少时效率下降的指标均采用如下数据下表2-1所示:表2-1传统汽车系统在匀速行驶时,各项数据如下表2-2所示:表2-2这里是把变速器换档看成最佳状态在车速点下的反映,并且涵盖了变速器损耗及轻载损耗对汽车的系统效率的影响。如数据表(2-2)中,车速50km/h,后备功率31kw,负载率13%;发动机最佳效率为40%,而实际效率为23%,轻载损耗系数0.78,变速器损耗系数0.96,轿车的系统效率17%。车速10km/h,后备功率34kw,负载率2%;发动机最佳效率为40%,而实际效率14%,轻载损耗系数0.32,变速器损耗系数0.88,轿车系统效率仅4%。因为在低速行驶区,汽车的阻力功率很小,如果汽车系统不能把发动机转速下降的很低,当汽车的车速越低时,阻力功率越小,轻载损耗对于汽车系统效率的影响越大。影响传统的汽车系统效率主要有6个方面的因素,部分可以参考上述的图表,以下进行具体说明:第一、在低速行驶时,发动机工作在最佳效率状态下,发动机输出功率远大于汽车所需要的行驶阻力功率。发动机的最佳效率区的转速范围很小,发动机的的最大转速和最小转速比值(转速比),一般为2~3,无法通过大范围的调整转速,高效的改变输出功率,和汽车的行驶阻力功率相匹配,而是只能通过降低发动机效率的方式来降低输出功率,导致的一个结果就是预留的后备功率非常大,负载非常小,这样的方式可以保证汽车的动力性及载重量的需求,但是发动机实际效率非常低,发动机效率损耗大。第二、在低速行驶区,汽车的阻力功率很小,如果汽车系统不能把发动机转速下降的很低,当汽车的车速越低时,阻力功率越小,轻载损耗对于汽车系统效率的影响越大。第三、变速器是从最低档逐步上升的,变速器损耗系数对低速行驶区系统效率影响大。第四、在不同的工况下,发动机适应不同行驶阻力功率及动力性等的要求无法使压缩比及空燃比在最佳状态下工作,使得发动机的效率无法接近最佳状态,发动机效率损耗系数无法接近1。第五、在常用工况下,发动机无法使尾气常压排放,冷却系统、尾气温度、尾气压力的能量损耗非常大。第六、传统发动机,如果采用节气门配气,进气量受到转速影响,不是高转速进气量不足,就是低转速进气量过大。进一步地,继续参考表2-2,在传统汽车中,当车速10km/h,后备功率34kw,负载率2%,假设转速比为2,把负载率调节到100%,后备功率为零,根据本发明的一些实施例,所述高效率汽车系统的燃烧室的体积的变化范围为1/50~1,需要搭配大型发动机,然后单一通过调整可变体积燃烧室,来实现发动机输出功率和阻力功率的匹配。存在的一个问题就是,因为燃烧室需要在较大的范围内变化体积,所以对于燃烧室的设计要求较高。进一步,本发明提供的所述高效率汽车系统不仅采用可燃烧室发动机来提高效率,还可以增大了发动机的转速范围,低速行驶对应的发动机的转速就下降了,那么对应的最大功率也下降了,后备功率=发动机最大有效输出功率-阻力功率,后备功率也可以下降,从而使得整个系统的效率提高。具体地说,在上述的数据表(2-2)中车速10km/h,后备功率34kw,负载率2%,假设转速比为2,把负载率调节到100%,后备功率为零,燃烧室的体积的变化范围为1/50~1,除非是大型发动机,常规车载发动机是不现实的,故无法单一通过调整可变体积燃烧室发动机,使发动机的输出功率与阻力功率匹配。可变压缩比发动机的压缩比为1~8到1~14,燃烧室体积的变化量<2倍,尾气正压排放,可变体积燃烧室发动机的体积变化量必须远大于可变压缩比发动机,才能使发动机的输出功率与阻力功率匹配。注:燃烧室的最大体积为最大进气量/最小压缩比,最小压缩比用于调节不同燃料的特性。采用增大发动机转速范围调节后备功率的方法后,也可以结合使发动机输出功率衰减的方式,使低速匀速行驶时,在发动机最佳效率下,输出功率大幅度下降,使进一步通过缩小燃烧室体积,降低发动机功率的要求下降,大幅度降低了最小燃烧室的设计难度。例如,采用增大发动机转速范围调节后备功率的方法,把转速比增大为10~20,使得汽车在低速行驶时,发动机的输出功率下降5倍,燃烧室的体积的变化范围约为1/10~1,最小燃烧室的体积为1/10,使得燃烧室设计难度大幅度下降。采用可变体积燃烧室发动机、并采用增大发动机转速范围调节后备功率的方法、以及采用使发动机输出功率衰减的方式组成的高效汽车系统,可以体现传统阿特金森、米勒循环发动机比奥托循环发动机效率高的优点,而避免了传统阿特金森、米勒循环发动机的缺陷:低速行驶需要外部电子增压器提高压缩比,无法实现低速行驶、小负荷、高效率的输出方式,在需要动力性、大负荷时,无法提高气缸的功率密度。取代了传统奥托循环发动机利用尾气动能的涡轮增压器,取代了阿特金森循环发动机的3连杆结构。高效汽车系统,无论进气量大小,通过调整燃烧室体积,使发动机工作在最佳效率状态下,发动机的效率损耗系数接近为1。在低速行驶区,通过增大转速比,降低转速,降低发动机的轻载损耗。通过提高变速器档位,降低变速器损耗。汽车常用工况下,使发动机工作在尾气常压排放的经济区。不常用工况下,使发动机工作在尾气正压排放的功率密度大的动力区。依靠降低变速器档位,增大转速,增大燃烧室体积,采用使发动机输出功率衰减的方式,释放发动机的输出功率,共同增大发动机的输出功率,符合动力性及载重量的需要。最终使不同工况下,汽车的系统效率大幅度提高。注:进气量的临界值lj:选择一个实际进气量占最大进气量的比值,在最佳状态下燃烧后,恰好使发动机的尾气常压排放,此时为发动机的临界功率。设可变燃烧室的最大进气量为1(指进气量=最大气缸容积时,进气量相对值为1),临界进气量为lj,设可变燃烧室的最大体积为1,临界体积也为lj。燃烧室的可变体积比bt:可变燃烧室的最大体积与最小体积之间的比,设最大进气量为1,最小进气量为1/bt。燃烧室的体积变化范围(变化量):可变燃烧室的最大体积到最小体积的范围,在最佳压缩比与空燃比固定下,进气量与燃烧室体积成基本对应关系,设最大体积为1,燃烧室的体积变化范围为1~1/bt。燃烧室动力性区的可变体积比btd:可变燃烧室的最大体积与临界体积之间的比,设最大进气量为1,btd=1/lj。动力性区燃烧室体积变化范围为1~lj。燃烧室经济性区的可变体积比btj:可变燃烧室的临界体积与最小体积之间的比,设最小进气量为1/bt,btj=bt*lj。经济性区燃烧室体积变化范围为lj~1/bt。发动机的进气量的临界值lj约为0.37~0.3,对应的体积变化量约为2.7~3.3倍。这个临界值主要与压缩比有关,压缩比越大临界值越大,还与空燃比、进气温度、大气压、散热系数、机械损耗系数及燃料热值等有关。进气量为lj~1时,尾气正压排放,发动机的最佳效率最终降到传统发动机的水平,但提高发动机的功率密度,动力性区用于大加速、超载、超高速行驶等不常用工况。进气量为lj~1/bt时,尾气常压排放,发动机的效率基本一致,发动机的效率高于传统发动机的水平,是发动机最佳效率状态,增大汽车的经济性,经济性区用于主要的常用匀速行驶范围、小加速、常规载重量变化及常用法规车速等工况。为了使发动机的尾气常压排放,可以选择燃烧室的可变体积比bt的范围为lj~15,即燃烧室的体积变化范围可以在1/(lj)~1到1/15~1之间,变化量越大,发动机输出功率的变化越大,但精度越差,效率也会逐步稍有下降,同时设计难度越大。例如,假定汽油机压缩比为10,进气量的临界值lj=0.33,燃烧室的可变体积比bt=12,进气量为1,压缩比及空燃比在最佳状态下,使尾气正压排放,发动机的最佳效率为40%,临界进气量时,压缩比及空燃比在最佳状态下,使尾气常压排放,发动机的最佳效率为60%。动力性区的体积变化量为1~0.33,动力性区可变体积比btd=1/0.33=3,动力性区发动机的效率为40~60%,发动机的最佳效率最终降到传统发动机的水平。经济性区体积变化量为0.33~1/12,经济性区可变体积比btj=12*0.33=4,经济性区发动机的效率基本保持在60%,发动机的效率高于传统发动机的水平。实际过程中,btj取1~5,或者bt取lj~15,比较好。btj值不能太大,否则最小燃烧室的设计难度大,发动机的效率也会稍有下降。压缩比不变,对应进气量为0.33/btj*vt~0.33vt。尾气接近常压排放,发动机的效率为60%,发动机的效率高于传统发动机的水平,是发动机最佳效率状态,增大汽车的经济性,经济性区用于主要的常用匀速行驶范围、小加速、常规载重量变化及常用法规车速等工况。例如,汽油机燃烧室的体积为1,进气量为1,压缩比为10,压缩比及空燃比在最佳状态下,使尾气正压排放,负载率100%,后备功率为零,发动机的输出功率与阻力功率匹配,假定汽油机的最佳效率为40%。假定进气量的临界值为0.33,燃烧室的体积缩小到0.33,进气量为0.33,压缩比还是10,压缩比及空燃比在最佳状态下,使尾气常压排放,负载率100%,后备功率为零,发动机的输出功率与阻力功率匹配,假定汽油机的最佳效率为60%,发动机的效率大幅度提升。进一地,根据本发明的一些实施例,本发明提供的所述高效率汽车系统还可以采用发动机输出功率衰减方法,使得发动机在最佳效率区工作。具体地说,所述高效率汽车系统改变发动机输出功率的方法包括:间隔进油、降低进油的气缸数目、使用大小气缸组合等。降低进油的气缸数目现在称之为停缸技术,是指使得部分气缸停止喷油,已经在低速行驶中运用。间隔进油是指所有气缸同时供油后又同时停止供油,交替进行。使用大小气缸组合是指小负载时小气缸可以单独工作,使用中等负荷和大负荷时,大小气缸可以共同工作。转速和车速越低,需要停油间隔越短及轻载损耗越低,车速比下降越小,越平稳。如果停油时间长,气缸漏气量大,进气量不符合要求,那么可以借助通气孔开合,使得气缸逐次工作。发动机输出功率衰减的公式组:pc=p1*n*n,ps=p1*ny*ny,bs=pc/ps=(n/ny)*(n/ny);其中,传统发动机的输出功率pc、一个气缸一次进油的输出功率p1、气缸总数n、气缸转速n;衰减后的输出功率ps、进油的气缸数目ny、气缸进油频率ny、发动机输出功率衰减系数bs。例如,当气缸转动时,间隔进油,那么n/ny>1,气缸每转动2圈中进油1圈或每连续转动2x圈中连续进油x圈,那么n/ny=2,类似于脚踏油门1秒,停止1秒,交替进行。例如,当只有部分气缸进油,那么n/ny>1,如4缸中2个气缸始终进油,那么n/ny=2。另外,在使用停缸技术的同时,还可以使用不同大小的气缸组合。小负载时小气缸可以单独工作,使用中等及大负荷时,通过调整燃烧室的体积,大小气缸等功率输出,减少震动。需要特殊大扭矩或超高速行驶时,使用大小气缸不等功率输出,最终增大发动机输出功率衰减系数。例如,当气缸为大小一样的组合时,固定转速下两个气缸组功率输出分别是5kw,一个气缸组单独工作与两个气缸组同时工作的输出功率范围为5kw~10kw;当气缸为大小气缸的组合,小气缸组功率输出4kw,大气缸组为6kw,小气缸组单独工作与两个气缸组同时工作的输出功率范围为4kw~10kw,输出功率衰减系数为2.5倍。当汽车启动、超低速行驶、低速行驶(<50km/h)、不使用空调、小载重量、低加速等时,发动机需要输出的功率非常小,如果采用了发动机输出功率衰减的方式,有利于降低固定转速下的输出功率,虽然增加了发动机的最大震动幅度,但它是一种改变发动机输出功率的有效方法,与可变体积燃烧室发动机及采用增大发动机转速范围调节后备功率的方法配合使用,使发动机的效率接近最佳状态,适应不同工况下巨大负荷变化要求。间隔进油这项技术可以单独用于传统发动机,非常容易实现,可以在一定车速范围内大幅度降低的油耗。轿车的档位比较少,即使在最高档位下,要保留后备功率,要给风速及载重量等增大提供一定空间,轿车的发动机实际工作的压缩比及进气量要比最佳状态值小,轻卡的档位也比较少,通过增大过量空气系数及少量降低压缩比降低发动机的功率,具体数值与档位数量及厂家设置有关。通过程序计算出两者功率输出的比为1/bw,那么连续在最佳效率状态下供油为(1/bw)时间周期,连续停止供油为(1-1/bw)时间周期,供油与停止交替进行,平均输出功率保持不变,使发动机的效率提高。停止供油时间不能太短,要考虑传统发动机的响应速度,油门角度代表的是一个平均功率的值。停止供油时间越短,汽车的瞬时速度变化越小,车速越平稳,发动机承受更的冲击或变化越小。相同停止供油时间,车速越快,动能越大,发动机轻载损耗对动能影响越小,车速相对变化越小,感觉越平稳,车速越低,越要缩短停油时间,对传统汽车改造难度增大,越不适合间隔进油方式。现实使用过程中,得出可以使用的上述计算的供油及停油时间范围后,采用比当前发动机输出功率更大的功率加速,加速时间为t1,车速从v1增加到v2,停油时间为t2,车速从v2下降到v1,加速前后车速变化量为δv=v2-v1,那么平均车速及变化量为(v2+v1)/2±δv/2。它包含汽车实际的空气阻力系数及滚动阻力系数,变速器损耗、轻载损耗等汽车系统的各种参数影响,同时也是最容易实现的一种控制手段。例如,假定某轿车车速100km/h时,进气量100%,最佳效率为40%,压缩比10,最大输出功率57kw;实际工作时,阻力功率17.2kw,多余的后备功率为40kw,进气量43%,压缩比4.3,实际工作效率下降为28%,转速2400r/min=40r/s,百公里油耗7.7l。采用间隔进油方法初步计算,连续停止2秒,以57kw的功率供油2秒,发动机停止供油约80圈,如果传统发动机的响应速度及漏气量可以接受,车速约为97~103km/h,供油与停止交替进行,平均输出功率基本保持不变,百公里油耗大概下降到7.7*28%/40%=5.4l。本发明提供的所述高效率汽车系统,采用了可变体积燃烧室、并采用增大发动机转速范围调节后备功率的方法,还可以采用发动机输出功率衰减的方法,具有传统阿特金森、米勒循环发动机比奥托循环发动机效率高的优点,而避免了传统阿特金森、米勒循环发动机的缺陷。这一缺陷是指在低速行驶中需要外部电子增压器提高压缩比,无法实现低速行驶、小负荷、高效率的输出方式,在需要动力性、大负荷时,无法提供气缸的功率密度。本发明提供的所述高效率汽车系统取代了传统奥托循环发动机利用尾气动能的涡轮增压器,取代了阿特金森循环发动机的3连杆结构。本发明提供的所述高效率汽车系统,无论进气量大小,通过调整燃烧室的体积,可以使得发动机工作在最佳效率状态,发动机的效率损耗系数接近于1。在低速行驶区,通过增大转速比,降低转速,降低发动机的轻载损耗。通过提高变速器的档位,降低变速器的损耗。本发明提供的所述高效率汽车系统,使得汽车在常用工况下,发动机工作在尾气常用排放的经济区,使得汽车在不常用工况下,发动机工作在尾气正压排放的功率密度大的动力区。本发明提供的所述高效率汽车系统,依靠降低变速器档位,增大转速,增大燃烧室体积,采用使得发动机输出功率衰减的方法,释放了发动机的输出功率,共同增大了发动机的输出功率,符合动力性及载重量的需要。最终使得汽车的系统效率大幅度提高。在采用增大发动机转速范围调节后备功率的方法、以及采用使发动机输出功率衰减的方式、并采用可变体积燃烧室发动机组成的高效汽车系统中,通过3种方法,使发动机始终工作在经济性区、在最佳状态,使发动机的输出功率,与常用工况的阻力功率匹配,找到一个可以初步计算,直观选取3种方法中的参数的公式,十分重要。发动机工作在最佳状态时,发动机的转速与输出功率基本成正比,故转速比与它对应输出的功率比一致;传统汽车,发动机转速比*总变速比=车速比≌变速器转速比,发动机的小转速范围通过变速器速比的变化增大了变速器转速范围,对应了车速范围,在采用增大发动机转速范围调节后备功率的方法后,转速比范围增大,发动机转速比*总变速比>车速比≌变速器转速比时,变速器多余的变速比就可以调节发动机的输出功率及后备功率,改变变速比时,实际就是改变转速,多余的变速比可以看成输出功率比;发动机工作在最佳状态时,进气量变化与发动机的输出成正比,故经济性区燃烧室可变体积比基本可以看成输出功率比,发动机工作在动力性区时,尾气排放从正压到常压,发动机最佳状态下的效率变化很大,故动力区燃烧室可变体积比,除以两者的效率比,也可以看成输出功率比;发动机输出功率衰减系数是通过间隔进油、停止进油的气缸数目、使用大小气缸组合方式降低发动机的输出功率,它也与发动机输出功率比基本成正比。在汽车水平匀速行驶下,汽车的驱动功率=行驶阻力功率汽,汽车的驱动功率=发动机的有效功率(发动机的实际输出功率)*轻载损耗系数*变速器损耗系数=汽车的燃料消耗*汽车的系统效率;这里只分析发动机效率与各参数之间的关系,故不考虑轻载损耗系数、变速器损耗系数的影响;就建立了行驶阻力功率比汽车系统中与各功率比及效率比之间的关系。故得到估算高效汽车系统中主要参数的方法,最大法规车速的阻力功率比与高效汽车系统的关系公式组:本发明提供了一种简单的直观推算高效率汽车系统中主要参数的方法,具体如下:bf=pzmax/pfmin,如果bf>bbj*bn*btj*bs,那么bηj>1;如果bf≤bbj*bn*btj*bs,那么bηj≈1,bt=btj*btd。bf是最大法规车速的最大阻力功率比、pfmax是最大法规车速的最大载重量的阻力功率、pfmin是最小车速最小载重量的阻力功率,bηj是最佳经济区与最低的系统效率比、bη是最佳与最低的系统效率比、bbj是降低后备功率的变速比、bn是最高与最低的转速比、btj是经济性区燃烧室可变体积比、bs是发动机输出功率衰减系数,bt是燃烧室可变体积比、btd是动力性区燃烧室可变体积比。最大法规车速的阻力功率比bf:指在不使用离合器下,最大法规车速的最大载重量的最大阻力功率pfmax与最小车速的最小载重量的最小阻力功率pfmin的比。用最大法规车速的阻力功率比bf代替汽车最大阻力功率比bz,可以使经济性区用于主要的常用匀速行驶范围、小加速、常规载重量变化及常用法规车速等工况。bηj≈1:指发动机在经济区的最佳效率状态下工作;bηj>1:指发动机无法在经济区的最佳效率状态下工作;此时汽车系统唯一的方法是通过降低系统效率的方式与行驶阻力功率匹配,这就是传统汽车系统的特征。但这组公式中没有考虑轻载损耗系数、变速器损耗系数等的影响,上述只是一个近似的推理公式,用于体现增加发动机输出功率比的重要性及关系。故在匀速行驶中,在任何车速及载重变化下,驱动功率始终等于行驶阻力功率,并成一一对应关系,否则无法匀速行驶;当发动机在最佳状态下输出的汽车驱动功率范围小于行驶阻力功率的范围时,即bf>bbj*bn*btj*bs,汽车系统唯一的方法就是,降低效率,才能形成一一对应关系。降低效率的方法有很多,如降低压缩比、增大或减小空燃比、在动力区工作、增大空载损耗、增大变速器损耗等。例如,某轿车,采用6at变速器的总变速比6.05,载重量1.54~2吨,经济区车速10~120km/h,动力区车速120~200km/h,转速范围500~5000r/min,假定最佳经济区发动机的效率为60%,动力区发动机的效率为40~38%;bf=29/0.64=45,bbj=1.156/0.686=1.69、bn=10、btj=3,bs=1。bf≤bbj*bn*btj*bs→45≤1.69*10*3*1=50,故bηj≈1。所述高效率汽车系统工作在最佳经济区,始终发动机的效率为60%。根据本发明的一些实施例,可以把进气量的临界值的输出功率与100km/h的阻力功率匹配,并通过档位调整到≥120km/h,120km/h是轿车最高法规车速值,实际为140km/h时,发动机的效率为60%,车速140~200km/h,发动机的效率逐步下降,但在40~60%之间。所述高效率汽车系统在不同车速匀速行驶的数据如下表(3-1)、图11所示:车速单位为km/h,转速单位为r/min,功率单位为kw,油耗单位为l。表3-1从图10与图11比较,很容易看出,发动机的临界输出功率更接近汽车的行驶阻力功率曲线,它是新方法提高汽车系统效率的关键因素。对比表(2-2)与表(3-1)中,新方法的变速器损耗系数、轻载损耗系数也明显提高。表(2-2)与(3-1)中,市郊混合平均车速50km/h上看,匀速行驶百公里油耗比为6/2=3倍,新方法,使不同工况下发动机的效率大幅度提升。当根据本发明的一所述高效率汽车系统在车速10~60km/h时,发动机在低输出功率下,因为转速接近500r/min,震动也稍有增加。还可以把10~20km/h转速下降到接近250r/min,震动感增加并不明显,但油耗大幅度下降。举例说明,表(3-1)中,如果把车速10km/h的转速下降到250r/min,由于发动机输出功率只有0.91kw,震动感增加并不明显,系统效率从23%提高到42%,怠速行驶可以不必采用电动机驱动,百公里油耗从3.1l下降到1.7l。所述高效率汽车系统缓慢启动时的档位在2档(或4档),到车速30~100km/h时,采用5~6档,均使发动机的转速尽可能接近500r/min,降低了发动机的转速,使发动机的临界输出功率更接近汽车的行驶阻力功率曲线。到车速200km/h时使用的档位不再是传统的最高档,比如说6档,而是4档,通过增加降低变速器的档位,来提高发动机的转速,增大输出功率。这里是把变速器换档看成最佳状态在车速点下的反映,并且涵盖了变速器损耗及轻载损耗对汽车系统效率的影响。根据本发明的一些实施例的所述高效率汽车系统的加速时间及效率---临界加速及最大加速行驶的数据表(3-3)如下:表3-3表(3-3),常规最大加速的选择,发动机采用进气量的临界值对应的输出功率,百公里加速时间合计为17.4s,在市区从启动到穿过50m的路口,最大车速为20~50km/h,需要10~6s,发动机此时在最佳效率状态下工作,汽车的系统效率约为60%*0.85。极端最大加速的选择,发动机采用最大进气量对应的最大输出功率,百公里加速时间合计为7.75s,在市区从启动到穿过50m的路口,最大车速为20~50km/h,需要9.5~4.8s,此时汽车的系统效率为40%*0.85。上述分析反映,在市区的最大车速为60km/h,路口的加速行驶没有必要选择极端最大加速的方式。另外,上述方案中发动机衰减系数为bs=1,实例中均没有采用使发动机输出功率衰减的方式进行分析,它本质上与采用增大发动机转速范围调节后备功率的方法、采用可变体积燃烧室发动机的方法相同,都是最终使车速下发动机的经济区的输出功率更接近行驶阻力功率曲线,也符合动力性等的需要。同理,不同工况下,柴油机的卡车,同汽油机的轿车方法基本相同。只是柴油机的卡车,通过可变体积燃烧室发动机,并采用增大发动机转速范围调节后备功率的方法,它对最大转速可以比传统柴油机稍微有所提高。例如,当所述高效率汽车系统是一重卡拖车时,采用变速器的总变速比20,重卡载重量8.8~40吨,车速10~100km/h,转速范围500~2500r/min;bz=259/6.36=62,bbj=5、bn=5、btj=2.5,bs=1,bz≤bηj*bbj*bn*btj*bs,那么bηj≈1,假定最佳经济区临界值效率为64%,那么,在不考虑轻载损耗、变速器损耗及极端加速度等影响时,10~100km/h的发动机的效率约为64%。值得注意的是,所述高效率汽车系统采用可变体积燃烧室发动机后,在高转速下,可以始终使压缩比及空燃比在最佳状态下工作。所述高效率汽车系统增大后备功率,是依靠变速器降低档位及增大燃烧室体积,不会出现压缩比下降及空燃比增大带来的燃烧时间延长的问题,就可以部分提高发动机的转速,而不降低发动机的效率,特别适合增大压燃式柴油机的转速,从而增大发动机的转速比低速行驶区,低转速发动机产生的震动感,由轻载损耗功率及行驶阻力功率及转速决定,故低频小功率的减震系统的成本增大。低速行驶区,最大加速度下,发动机的震动基本与传统汽车系统相差不大,通过降低变速器档位,使发动机的转速及最大输出功率,提高到传统发动机的水平。举例说明,在传统汽车中,某轿车,采用6at变速器,总变速比6.05,载重量1.54~2吨,6000r/min时,汽油机最大输出功率100kw。最佳效率区的转速范围为1750~3500r/min,转速1000~6000r/min,对应车速范围5.5~200km/h,发动机转速比*总变速比=车速比≌变速器转速比=36.3,车速≤100km/h时,后备功率很大,发动机的效率低。传统系统最大进气量下,1000r/min时,发动机的效率为15%,6000r/min为35%,1750~3500r/min为40%。当该轿车的车速为10km/h时,对应档位为1档,发动机转速为1814r/min,速比为4.15,发动机最大效率为0.4,发动机最大功率为35kw,阻力功率为0.6,最大加速度为7.9,加速时间为0.35s。根据本发明的所述高效率汽车系统的一实施例,采用6at变速器的速比,总变速比6.05,载重量1.54~2吨,5000r/min时,汽油机最大输出功率100kw。转速比增大到10,最佳效率区的转速范围为500~5000r/min,对应车速范围10~200km/h,发动机转速比*总变速比>车速比≌变速器转速比=20,最大加速时,最大转速≤6000r/min。新系统最大进气量下,500~3500r/min时效率均为40%,5000r/min为38%,6000r/min为35%。当所述高效率汽车系统的车速为20km/h时,档位为1档,发动机转速为1794r/min,并且所述高效率汽车系统的速比为4.418,发动机最大输出效率为0.4,发动机最大功率为38kw,最大加速度为4.3,加速时间为0.65s。传统汽车系统的空调,压缩机转速由发动机的转速决定,效率非常低,空调消耗的功率与车速50km/h的阻力功率的比值很大。发动机的转速比增大后,使发电机、空调压缩机等汽车辅助动力消耗设备的额定转速范围增大,平均效率继续下降。更需要小功率的可控无极变速器,输出相对固定的转速,带动发电机,也可以输出变化的转速,带动压缩机,压缩机转速的大小由需要转换的热量决定,大幅度降低发电机、空调压缩机等对汽车系统效率的影响。进一步地,传统汽车在行驶过程中,高速行驶区,车速越大,受风阻影响明显,风阻越大,行驶阻力功率越大,汽车的系统效率虽然增加,但百公里油耗越大。低速行驶区,车速越低,受风阻影响不明显,阻力功率与车速非线性变化不明显,但车速越低,汽车的系统效率越低,百公里油耗也越大。怠速行驶方法汽车的系统效率最低,百公里油耗也最大;重载量增加,后备功率减小,发动机的效率增加;加速时,后备功率减小,发动机的效率增加,最大加速时,后备功率为零,发动机的效率最高。滑行减速时,发动机不提供动力,但高转速下的发动机轻载损耗对汽车动能浪费有很大的影响,转速越高,轻载损耗影响越大,相当于增加油耗。刹车减速,车速越高,动能损失越大。怠速空转对系统效率影响大。本发明提供的所述高效率汽车系统,除怠速行驶方法外,如果汽车系统效率变化小于风阻的变化,车速越低,百公里油耗越小,车速越大,风阻越大,行驶阻力功率越大,百公里油耗越大,其它与传统汽车系统基本一致。假定所述高效率汽车系统的混合动力系统总损耗系数为0.57。低速行驶区,如果发电机驱动的混合动力系统总损耗系数>发动机驱动的系统总损耗系数,采用电动机驱动可以节能。参考传统汽车系统的数据表(2-2)中,当车速60km/h时,总损耗系数为0.51,车速≤60km/h时就可以采用电动机驱动,在较高速行驶下,甚至采用电动机驱动与发动机驱动及充电交替工作方式,部分发动机功率驱动的效率更高,这就是混合动力系统存在于传统汽车系统的意义。根据本发明的一些实施例,根据本发明的所述高效率汽车系统的一实施例,采用6at变速器的速比,总变速比6.05,载重量1.54~2吨,5000r/min时,汽油机最大输出功率100kw。转速比增大到10,最佳效率区的转速范围为500~5000r/min,对应车速范围10~200km/h,发动机转速比*总变速比>车速比≌变速器转速比=20,最大加速时,最大转速≤6000r/min。新系统最大进气量下,500~3500r/min时效率均为40%,5000r/min为38%,6000r/min为35%。当所述高效率汽车系统的车速为40km/h时,档位为6档,发动机转速为593r/min,并且所述高效率汽车系统的速比为0.686,发动机最大输出效率为0.4,发动机最大功率为12kw,总损耗系数为0.60。参考所述高效率汽车系统的数据表(3-1)中,车速10km/h,转速513r/min,总损耗系数为0.52,可以采用电动机驱动,如果转速降为250r/min,总损耗系数0.70,不能采用电动机驱动。举例说明,假定市区路口长度100km,行驶车速分别为20及50km/h,每1km一个路口,刹车1次,刹车时动能损耗50%,排队等候0~2次,平均1次,排队等候时间0~60s,平均30s,其中每次以10km/h的怠速车速移动100m。市区工况下,假定传统轿车系统采用最大加速,汽油机在最佳效率为40%的状态下行驶,系统效率为36.8%,刹车节约的50%动能相当于减少加速的能耗。怠速空转油耗1.8l/h,车速10~50km/h的油耗来源于数据表(2-2)。传统轿车系统车速、怠速空转等对行驶系统效率的影响,如下数据表(4-1):表4-1当车速50km/h,速度高,加速更费油,刹车动能损失大,但行驶系统效率比车速20km/h提高1.5倍。如果把怠速行驶的速度从传统的10km/h增加到20km/h,路口排队行驶油耗可以节约=1.79+(0.11-0.03)-(1.13+(0.32-0.1))=1.87-1.35=0.52l,可以提高5%的行驶系统效率。传统汽车系统,低速行驶区,提高行驶系统效率的关键,是使汽车尽快工作在高车速区,在低速行驶区“轻踩油门,轻踩刹车省油”的观点是不正确的,应该是“重踩油门,轻踩刹车省油”。路口排队怠速空转占行驶系统效率的15%,采用停车熄火技术可以提高汽车的系统效率。怠速车速10km/h,采用小功率电动机驱动,油耗为0.32l/100km,可以提高15%的行驶系统效率,采用电动机及发动机混合启动及驱动的方式,可以同时解决停车熄火及怠速移动2个问题。如果电动机驱动可以提高汽车系统低速行驶区的效率,电动机与发动机并联驱动汽车,电动机可以连接变速器的输入或输出端,它与一般混合动力汽车的区别是,只是用于城市道路的频繁启动、短距离及小功率的低速行驶及倒库行驶,采用小功率电动机驱动,蓄电池的容量大幅度减小,并省去外充电的麻烦。设定城市路况的小加速度及匀速行驶模式,在车速大于某设定值,如车速10~60km/h时,加速度大于某设定值,设定值与是否节能有关,可以主动从电动驱动切换为发动机驱动模式,或者借助汽车行驶惯性启动发动机运行,减小电动机的功率,减少发动机效率损耗、轻载损耗、变速器损耗及离合器的摩擦损耗对低速行驶区汽车系统效率的影响。并且设定山区、障碍物及大加速度路况的汽车启动模式,直接采用传统从发动机启动的方式,怠速启动速度可以任意变换,不影响各种工况启动的运行。市区工况下,所述高效率汽车系统被实施为一轿车,并且采用临界功率加速,发动机在最佳效率为60%的状态下行驶。车速10~50km/h的油耗来源于数据表(3-1)。根据本发明的一些实施例,所述高效率汽车系统车速、怠速空转等对行驶系统效率的影响,方案1,数据表(4-2)如下:表4-2根据本发明的一些实施例,所述高效率汽车系统车速、怠速空转等对行驶系统效率的影响,方案2,数据表(4-3)如下:表4-3方案1比方案2的转速低0.5倍,故怠速空转及车速10km/h的油耗低一些。通过路口的车速越高,越费油。如果把怠速行驶的速度从传统的10km/h增加到20km/h,方案1百公里油耗没有落差,故不省油,方案2使行驶系统效率提高1.5%,没有实际意义。在所述高效率汽车系统中,在行驶过程中可以采取“轻踩油门、轻踩刹车”的措施以节约油耗。路口排队怠速空转占行驶行驶效率的6~11%,采用停车熄火技术可以提高本发明的所述高效率汽车系统的效率。方案1中,车速10km/h,转速为250r/min,总损耗系数>57%,不能采用电动机驱动,但可以在倒库行驶下采用0.5kw小功率电动机驱动,采用电动机及发动机混合启动及驱动的方式,可以同时解决停车熄火及倒库行驶2个问题。方案2可以采用1kw小功率电动机驱动,省油量为0.31-0.22=0.09l,采用电动机及发动机混合启动及驱动的方式,可以同时解决停车熄火及怠速行驶2个问题。倒库行驶指汽车停靠车位时的行驶方法,一般车速≤5km/h。因此,根据本发明的一些实施例,可以恰当的采用混合动力启动及驱动的方式,并且采用停车熄火技术来提高所述高效率汽车系统的效率。进一步,混动动力车作为节约油耗的代表,相对于本发明的所述高效率汽车系统而言并没有明显的优势。也就是说,本发明提供的所述高效率汽车系统在油耗上表现尚佳。混合动力车中,不同工况下,由始终工作在最佳效率状态下的发动机驱动发电机,车载发电机效率90%,固定大型发电机平均可以达到95%以上,使用不现实;铅蓄电池充放电效率利用率在75%~90%(取85%),磷酸铁锂电池充放电利用率稍高为85%~90%,功率密度大,成本高,锂电池要考虑复杂的充电电路损耗0.95,实际比铅电池效率并没有提高;电动机效率70~80%(取75%);采用轮毂电机直接驱动车轮,传动系损耗可以忽略;从发电、充电、放电、驱动角度看,混合动力车的系统总损耗系数≈0.9*0.85*0.75=57%,混合动力车的系统效率=发动机最佳效率*混合动力车总损耗系数。假定4种燃料的热值、密度、价格如下数据表(5-1):压缩比为20的柴油机的热效率为64%,压缩比为10的汽油机的效率为60%,压缩比为10的甲醇或乙醇的效率为60%,不同工况下汽车的系统效率为0.85。实际使用中可以采用高比例的醇类柴油或者汽油的混合燃料,降低燃料的成本,汽油及柴油的价格取7.5元/l。燃油种类柴油汽油甲醇乙醇密度(kg/l)0.830.730.790.79热值(mj/kg)46432028价格(元/kg)9.0410.271.84.8系统效率0.64*0.850.60*0.850.60*0.850.60*0.85成本(元/kwh)1.301.690.641.21表5-12018年用电的平均价格为0.61元/kwh。纯电动车的动力成本为:电价/(充电、放电、驱动的损耗)=0.61/0.64=0.94元/kwh。煤电约占中国发电量的60%,是高电价的主要原因,煤炭及石油均是化石能源,价格主要与稀缺性及物价指数有关,醇类等燃料可以是生物再生能源,再生能源主要与物价指数有关,即随着时间的推移,较大的时间范围内,以煤为发电主体的电价与石油价上涨比例接近,但电价始终会高于醇类的上涨比例,这里价格分析没有考虑政治、技术进步、环保、新发现大储量等因素。故上述分析反映,纯电动车与本发明的所述高效率汽车系统相比较,动力成本优势不明显。根据本发明的另一方面,本发明提供了一种可变燃烧室体积的发动机,其能够在不降低发动机效率的情况下,适应不同工况下负荷的变化。所述高效率汽车系统包括一车辆主体和所述可变燃烧室体积的发动机,所述可变燃烧室体积的发动机被装配于所述机械设备的一机械设备主体,用于为所述机械设备本体提供动力。参考附图1至图3b所示,根据本发明的一实施例的一种可变燃烧室体积的发动机被阐明。具体地,如图1所示,所述可变燃烧室体积的发动机10包括一主气缸11和至少一辅助气缸12。所述主气缸11具有一体积恒定的主燃烧室110。所述至少一辅助气缸12被设置于所述主气缸11,并且每所述辅助气缸12具有一体积可变的辅助燃烧室120,其中所述至少一辅助气缸12的所述辅助燃烧室120与所述主气缸11的所述主燃烧室110连通,以形成所述可变燃烧室体积的发动机10的燃烧室100,进而通过调整所述辅助燃烧室120的体积来改变所述燃烧室100的体积。可以理解的是,当所述辅助气缸12的所述辅助燃烧室120的体积为零时,所述可变燃烧室体积的发动机10的所述燃烧室100的体积等于所述主气缸11的所述主燃烧室110的体积;当所述辅助气缸12的所述辅助燃烧室120的体积不为零时,所述可变燃烧室体积的发动机10的所述燃烧室100的体积等于所述主燃烧室110的体积与所述辅助燃烧室120的体积之和。值得注意的是,由于所述辅助气缸12的所述辅助燃烧室120的体积可以远大于所述主燃烧室110的体积,并且所述辅助气缸12的数量可以多于一个,因此本发明的所述可变燃烧室体积的发动机10的所述燃烧室100的体积变化量可以远大于两倍,从而使得所述可变燃烧室体积的发动机10的发动机效率得以大幅度提升,这是可变压缩比的发动机无法达到的。值得一提的是,尽管在附图1至图3b和接下来的描述中以所述可变燃烧室体积的发动机10仅包括一个所述主气缸11为例,阐述本发明的所述可变燃烧室体积的发动机的特征和优势,本领域的技术人员可以理解的是,附图1至图3以及接下来的描述中揭露的所述可变燃烧室体积的发动机仅为举例,其并不构成对本发明的内容和范围的限制,例如,在所述可变燃烧室体积的发动机的其他示例中,所述主气缸11的数量也可以超过一个,以形成多缸发动机。同样地,在本发明的其他示例中,所述辅助气缸12的数量也可以超过一个,本发明对此不再赘述。更具体地,如图1所示,在本发明的这个实施例中,所述可变燃烧室体积的发动机10的所述主气缸11包括一主气缸体111、一主气缸盖112以及一主气缸活塞113。所述主气缸体111具有一主活塞腔1111和一主气缸口1112,其中所述主气缸口1112与所述主活塞腔1111连通。所述主气缸盖112被设置于所述主气缸体111,以封闭所述主气缸体111的所述主气缸口1112。所述主气缸活塞113被可滑动地设置于所述主气缸体111的所述主活塞腔1111,并且当所述主气缸活塞113滑动至所述主气缸体111上的主近止点(即邻近所述主气缸口1112的止动点)时,所述主气缸盖112和所述主气缸活塞113之间的空间形成所述主气缸11的所述主燃烧室110。可以理解的是,所述可变燃烧室体积的发动机10的所述主气缸11的所述主气缸盖112可以但不限于被实施为具有诸如平面、锲形、半球形、盆形、以及扁球形等等之类形状的气缸盖。相应地,所述主气缸活塞113也可以但不限于被实施为具有相似形状的活塞顶部,以在所述主气缸活塞113的活塞顶部与所述主气缸盖112之间形成一个狭窄的缝隙,即体积较小的所述主燃烧室110。例如,当所述主气缸盖112具有半球形形状时,所述主气缸活塞113的活塞顶部也具有半球形形状,有助于大幅缩小所述主燃烧室110的体积。值得注意的是,如图1所示,由于所述主气缸体111上的所述主近止点的位置基本不发生变化,因此所述主气缸11的所述主燃烧室110的体积基本保持恒定。此外,当所述主气缸活塞113滑动至所述主气缸体111上的所述主近止点时,所述主气缸盖112和所述主气缸活塞113之间的距离最小,即所述主气缸盖112和所述主气缸活塞113之间的空间最小;而当所述主气缸活塞113滑动至所述主气缸体111上的主远止点(即远离所述主气缸口1112的止动点)时,所述主气缸盖112和所述主气缸活塞113之间的距离最大,即所述主气缸盖112和所述主气缸活塞113之间的空间最大。特别地,如图1和图2所示,所述主气缸11的所述主气缸盖112设有至少一连通口1120,每所述辅助气缸12被对应地设置于所述主气缸11的所述主气缸盖112,并通过所述连通口1120将所述辅助气缸12的所述辅助燃烧室120与所述主气缸体111的所述主活塞腔1111连通,也就是说,通过所述连通口1120可以将所述辅助气缸12的所述辅助燃烧室120与所述主气缸11的所述主燃烧室110连通。进一步地,如图1和图3a所示,所述可变燃烧室体积的发动机10的所述辅助气缸12包括一辅助气缸体121、一辅助缸活塞122以及一作动机构123。所述辅助气缸体121具有一辅助活塞腔1211和一辅助气缸口1212,其中所述辅助气缸体121被对应地设置于所述主气缸盖112,并且所述辅助气缸体121的所述辅助气缸口1212对应于所述主气缸盖112的所述连通口1120,以通过所述连通口1120将所述辅助气缸体121的所述辅助活塞腔1211与所述主气缸体111的所述主活塞腔1111连通。所述辅助缸活塞122被可滑动地设置于所述辅助气缸体121的所述辅助活塞腔1211,以在所述辅助缸活塞122和所述主气缸盖112之间形成所述辅助燃料室120。所述作动机构123被设置以滑动所述辅助缸活塞1211,使得所述辅助缸活塞122与所述主气缸盖112之间距离发生变化,以在所述辅助缸活塞122与所述主气缸盖112之间形成体积可变的所述辅助燃烧室120。换句话说,所述作动机构123用于在所述辅助气缸体121的所述辅助活塞腔1211内滑动所述辅助缸活塞1211,使得所述辅助气缸12的所述辅助燃烧室120的体积得以改变。可以理解的是,如图3a和图3b所示,当所述辅助缸活塞122朝向靠近所述辅助气缸体121的所述辅助气缸口1212滑动时,所述辅助缸活塞122与所述主气缸盖112之间的距离变小,使得所述辅助气缸12的所述辅助燃烧室120的体积变小,直至当所述辅助缸活塞122滑动至所述辅助气缸体121上的辅助近止点(即邻近所述辅助气缸口1212的止动点)时,所述辅助气缸12的所述辅助燃烧室120的体积最小;当所述辅助缸活塞122朝向远离所述辅助气缸体121的所述辅助气缸口1212滑动时,所述辅助缸活塞122与所述主气缸盖112之间的距离变大,使得所述辅助气缸12的所述辅助燃烧室120的体积变大,直至当所述辅助缸活塞122滑动至所述辅助气缸体121上的辅助远止点(即远离所述辅助气缸口1212的止动点)时,所述辅助气缸12的所述辅助燃烧室120的体积最大。值得注意的是,在本发明的这个实施例中,所述主气缸11的所述主燃烧室110的体积恒定,而所述辅助气缸12的所述辅助燃烧室120的体积可变,使得所述可变燃烧室体积的发动机10的所述燃烧室100的体积变化量等于所述辅助气缸12的所述辅助燃烧室120的最大体积与最小体积之间的变化量。例如,所述可变燃烧室体积的发动机10的所述燃烧室100的可变体积比为3至15,即所述燃烧室100的体积变化量可以在1/3~1到1/15~1之间,变化量越大,发动机的输出功率的变化就越大。特别地,当所述可变燃烧室体积的发动机10的所述燃烧室100的体积变小时,所述可变燃烧室体积的发动机10的进气量同步减小;而当所述可变燃烧室体积的发动机10的所述燃烧室100的体积变大时,所述可变燃烧室体积的发动机10的进气量同步增大,这有助于尽可能使所述可变燃烧室体积的发动机10在压缩比和空燃比的最佳状态下工作,以便提高所述可变燃烧室体积的发动机10的发动机效率。可以理解的是,本发明还可以通过调节变速器的速比,尽可能使所述可变燃烧室体积的发动机10的进气量的临界值所对应的发动机输出功率更接近行驶阻力功率曲线(即所述发动机输出功率基本等于所述行驶阻力功率),以便提高配置有所述可变燃烧室体积的发动机10的机械设备的整体效率。根据本发明的上述实施例,如图1和图3a所示,所述可变燃烧室体积的发动机10的所述辅助气缸12的所述辅助气缸体121可以但不限于具有一中空柱状结构,以使所述辅助气缸体121的所述辅助活塞腔1211具有相同的横截面。示例性地,所述辅助气缸体121具有一连接端1213和一作动端1214,其中所述辅助气缸体121的所述连接端1213与所述主气缸盖112连接,其中所述作动机构123被设置于所述辅助气缸体121的所述作动端1214,并且所述作动机构123用于使所述辅助缸活塞122在所述辅助气缸体121的所述连接端1213和所述作动端1214之间滑动。与此同时,如图1和图3b所示,所述辅助气缸体121的所述辅助气缸口1212位于所述辅助气缸体121的所述连接端1213,并且所述辅助气缸口1212对应于所述主气缸盖112的所述连通口1120,以通过所述连通口1120将所述辅助活塞腔1211与所述主活塞腔1111连通,使得所述辅助燃烧室120与所述主燃烧室110连通,以形成所述燃烧室100。这样当所述辅助缸活塞122在所述作动机构123的作用下由所述作动端1214滑向所述连接端1213时,所述辅助气缸12的所述辅助燃烧室120的体积变小,使得所述燃烧室100的体积随之变小;当所述辅助缸活塞122在所述作动机构123的作用下由所述连接端1213滑向所述作动端1214时,所述辅助气缸12的所述辅助燃烧室120的体积变大,使得所述燃烧室100的体积随之变大。进一步地,在本发明的这个实施例中,如图3a和图3b所示,所述辅助气缸12的所述作动机构123可以包括一驱动机构1231和一传动机构1232,其中所述传动机构1232被设置于所述驱动机构1231和所述辅助缸活塞122之间。所述驱动机构1231用于提供驱动力。所述传动机构1232用于将来自所述驱动机构1231的驱动力传递至所述辅助缸活塞122,以驱动所述辅助缸活塞122在所述辅助气缸体121的所述辅助活塞腔1211内滑动,使得所述辅助气缸12的所述辅助燃烧室120的体积得以改变,从而改变所述可变燃烧室体积的发动机10的所述燃烧室100的体积。示例性地,在本发明的这个实施例中,所述驱动机构1231可以但不限于被实施为诸如带有制动的伺服电机或步进电机等等之类的电机,以通过电路来控制所述电机的旋转量,从而控制所述辅助缸活塞122的位移量,进而控制所述燃烧室100的体积变化量。此外,在本发明的这个实施例中,如图3a和图3b所示,所述传动机构1232可以但不限于包括一与所述驱动机构1231耦接的蜗轮12321和一与所述辅助缸活塞122连接的蜗杆12322,其中所述蜗轮12321被所述驱动机构1231驱动以旋转,其中所述蜗杆12322与所述蜗轮12321切向耦接,用于将所述蜗轮12321的旋转运动转换成所述蜗杆12322的直线运动,以使所述辅助缸活塞122在所述辅助气缸体121的所述辅助活塞腔1211内滑动,进而改变所述辅助燃烧室120的体积。值得注意的是,由于所述辅助缸活塞122的滑动采用蜗轮蜗杆的传动方式来控制,而所述电机的旋转量与所述蜗轮12321的旋转量成对应关系,因此可以通过电路参数来控制所述蜗轮12321的圈数和角度,进而精确控制所述辅助缸活塞122的位移量。之后,再通过数据转换建立电路参数量与所述燃烧室100的体积变化量之间的对应关系,最终实现由电路精确地控制所述燃烧室100的体积变化。可以理解的是,所述辅助缸活塞122尽可能不在所述可变燃烧室体积的发动机10处于圧缩行程和膨胀行程时滑动,以便减少所述电机的输出功率损失,以及降低所述蜗轮12321和所述蜗杆12322的磨损。根据本发明的这个实施例,如图3a和图3b所示,所述辅助气缸12还可以包括一密封机构124,其中所述密封机构124被设置于所述辅助气缸体121的所述作动端1214,用于密封所述辅助气缸体121的所述辅助活塞腔1211,以使所述燃烧室100形成一个密闭的空间。优选地,所述密封机构124可以但不限于被实施为一密封环1241,其中所述密封环1241被设置于所述辅助气缸体121的所述作动端1214,并环绕在所述蜗杆12322的外围,以密封所述辅助活塞腔1211。值得注意的是,如图1和图2所示,本发明的所述可变燃烧室体积的发动机10还包括一进气排气系统13和一燃料供应系统14。所述进气排气系统13用于控制所述可变燃烧室体积的发动机10的进气和排气;也就是说,所述进气排气系统13用于向所述燃烧室100提供空气或排出所述燃烧室100内的废气。所述燃料供应系统14用于控制所述可变燃烧室体积的发动机10的燃料供应;也就是说,所述燃料供应系统14用于向所述燃烧室100供应诸如汽油或柴油等等之类的燃油。示例性地,如图1和图2所示,所述进气排气系统13可以但不限于包括一进气门131和一排气门132,并且所述主气缸盖112设有一与所述主燃烧室110连通的进气口1121和一与所述主燃烧室110连通的排气口1122。所述进气门131被设置于所述主气缸盖112的所述进气口1121,用于控制所述可变燃烧室体积的发动机10的所述燃烧室100的进气。所述排气门132被设置于所述主气缸盖112的所述排气口1122,用于控制所述可变燃烧室体积的发动机10的所述燃烧室100的排气。可以理解的是,在本发明的其他示例中,所述进气排气系统13的所述进气门131和所述排气门132也可以被设置于所述主气缸11的其他位置或者所述辅助气缸12上,只要能够控制所述燃烧室100的进气和排气即可,本发明在此不再赘述。此外,在本发明的这个实施例中,如图1和图2所示,所述可变燃烧室体积的发动机10的所述燃料供应系统14可以但不限于被实施为一喷油器141,其中所述喷油器141被设置于所述主气缸11的所述主气缸盖112,用于向所述燃烧室100提供燃油,使得所述可变燃烧室体积的发动机10被实施为压燃式发动机。值得注意的是,由于所述可变燃烧室体积的发动机10的所述燃烧室100具有很大的体积变化量,以便在确保高效率的情况下,提供更大范围的输出功率,因此所述可变燃烧室体积的发动机10在不同工况下所需的喷油量差异较大。为了精准控制喷油量,如图2所示,所述燃料供应系统14的所述喷油器141可以包括一大喷油嘴1411和一小喷油嘴1412,其中所述大喷油嘴1411的喷油量大于所述小喷油嘴1412的喷油量。所述大喷油嘴1411用于在大负荷(即燃烧室体积较大)时供应较大的喷油量,以便在确保高效率的情况下提供较大的输出功率;而所述小喷油嘴1412用于在小负荷(燃烧室体积较小)时供应较小的喷油量,以便对喷油量进行精准控制,使得机械设备在启动、超低速、低速等工况下,更加平稳、更加节油。可以理解的是,在本发明的其他示例中,所述可变燃烧室体积的发动机10的所述燃料供应系统14也可以被实施为一化油器,用于调整在不同工况下的进气量及进油量,并对燃油雾化,使得所述可变燃烧室体积的发动机10被实施为点燃式发动机。值得一提的是,当所述可变燃烧室体积的发动机10的停机时间长时,所述主气缸和所述辅助气缸则会因气缸漏气而导致气缸内的气压逐步达到常压。如果在这种状态下启动发动机,通常所需的功率和进气量都较小,因此从发动机首次有效进气开始,就要精确控制进气量、空燃比、压缩比、以及输出功率。特别是对于具有较大体积的所述燃烧室100的所述可变燃烧室体积的发动机10,一旦所述燃烧室100出现不合理的进气量,就会出现无意义的压缩阻力和舒张阻力,进而会出现超浓油或超稀油混合气体的燃烧,从而导致发动机效率急剧降低和燃油量大幅升高。为了解决上述问题,如图3a和图3b所示,本发明的所述可变燃烧室体积的发动机10还可以包括一通气系统15,其中所述通气系统15用于控制所述燃烧室100的进气量,使得所述可变燃烧室体积的发动机10稳定且高效地工作。例如,所述可变燃烧室体积的发动机10可以借助所述通气系统15,使发动机的气缸逐次工作,降低启动发动机时的阻力,提高启动功率输出的平稳性。具体地,如图3a和图3b所示,所述通气系统15可以包括一通气孔151和一阀门152,其中所述通气孔151将所述燃烧室100与所述可变燃烧室体积的发动机10的外部连通,其中所述阀门152被设置于所述通气孔151,用于控制所述通气孔151的开合,以便控制所述燃烧室100的进气量。值得注意的是,所述阀门152可以但不限于被实施为一高速电磁阀,以通过所述高速电磁阀来快速控制所述通气孔151的开启和闭合,以便精确控制所述燃烧室100的进气量。在本发明的这个实施例中,示例性地,如图3a和图3b所示,所述通气系统15的所述通气孔151可以被设置于所述辅助气缸12的所述辅助缸活塞122和所述作动机构123的所述传动机构1232的所述蜗杆12322,以通过所述通气孔151将所述辅助燃烧室120与外部连通,进而将所述燃烧室100与外部连通。所述通气系统15的所述阀门152被设置于所述蜗杆12322的末端,用于控制所述通气孔151的开合。当然,在本发明的其他示例中,所述通气系统15的所述通气孔151也可以被设置于所述主气缸11的所述主气缸盖112,以通过所述通气孔151将所述主燃烧室110与外部连通。相应地,所述通气系统15被设置于所述主气缸盖112,用于控制所述通气孔151的开合。此外,所述通气系统15的所述通气孔151和所述阀门152还可以被设置于所述主气缸11或所述辅助气缸12的其他位置,只要能够将所述可变燃烧室体积的发动机10的所述燃烧室100与外部可控制地连通,以控制所述燃烧室100的进气量即可,本发明对此不再赘述。值得注意的是,正是由于所述通气系统15的存在,使得所述可变燃烧室体积的发动机10能够在确保高效率的基础上适应不同工况的需求,并能够降低发动机启动时的阻力,大幅度降低蓄电池的冲击电流及起动机的输出功率,以及降低行驶惯性启发动机时的阻力。例如,在发动机启动前,首先通过阀门打开所有的所述通气孔,使气缸内表压为零;接着在发动机缸开始转动或转动至一定速度之后,当需要工作的气缸进入进气行程前,再通过阀门关闭相应的通气孔,以便借助通气孔的开合,使发动机的气缸逐次工作,以便提高发动机启动功率的输出平稳性。而当气缸主动停止进油时,通过所述阀门又可以在排气结束后打开所述通气孔,使气缸内表压为零,以便减小发动机的内部阻力消耗功率。此外,所述可变燃烧室体积的发动机10的气缸排气完毕后,所述燃烧室100内通常会残留少量高温低密度的废气,如果所述燃烧室100内的气体不能充分对流,就不利于燃烧。而所述可变燃烧室体积的发动机10通过所述阀门152来控制所述通气孔151的开合,不仅可以彻底排除废气,而且还有助于进气后的气体混合。换句话说,所述通气系统15的所述通气孔151不仅可以根据不同位置来替代或补偿所述进气排气系统13的所述进气门131的进气量,而且还可以精确控制小的进气量。值得一提的是,尽管附图1至图3b以及上述描述以所述可变燃烧室体积的发动机10的所述传动机构1232为蜗轮蜗杆机构为例,阐述本发明的所述可变燃烧室体积的发动机的特征和优势,本领域的技术人员可以理解的是,附图1至图3b以及接下来的描述中揭露的所述可变燃烧室体积的发动机仅为举例,其并不构成对本发明的内容和范围的限制,例如,在所述可变燃烧室体积的发动机的其他示例中,所述传动机构1232也可以被实施为诸如凸轮连杆机构、齿轮齿条机构、丝杠机构、以及曲柄滑块机构等等之类的传动机构,用于将来自所述驱动机构1231的驱动力传递至所述辅助缸活塞122,以驱动所述辅助缸活塞122在所述辅助气缸体121的所述辅助活塞腔1211内滑动,使得所述辅助气缸12的所述辅助燃烧室120的体积得以改变,从而改变所述可变燃烧室体积的发动机10的所述燃烧室100的体积。示例性地,附图4a至图4c示出了根据本发明的上述实施例的所述可变燃烧室体积的发动机10的所述辅助气缸12的一个变形实施方式。相比于根据本发明的上述实施例,根据本发明的这个变形实施方式的所述辅助气缸12的区别在于:所述辅助气缸12的所述作动机构123的传动机构1232’包括一凸轮12321’和一连杆12322’,其中所述凸轮12321’被所述驱动机构1231驱动以转动,并且所述凸轮12321’具有一单圈螺旋形结构的外周缘,其中所述连杆12322’的一端与所述辅助缸活塞122连接,并且所述连杆12322’的另一端抵靠于所述凸轮12321’的所述外周缘,用于将所述凸轮12321’的旋转运动转换成所述连杆12322’的直线运动,以使所述辅助缸活塞122在所述辅助气缸体121的所述辅助活塞腔1211内滑动,进而改变所述辅助燃烧室120的体积。换句话说,所述传动机构1232’被实施为凸轮连杆机构,其中所述凸轮连杆机构被设置于所述驱动机构1231和所述辅助缸活塞122之间,用于将所述驱动机构1231的驱动力传递至所述辅助缸活塞122,使得所述辅助缸活塞122在所述辅助活塞腔1211内滑动,从而改变所述燃烧室100的体积。此外,如图4a和图4c所示,为了确保所述连杆12322’的所述另一端始终抵靠于所述凸轮12321’的所述外周缘,本发明的这个变形实施方式中的所述传动机构1232’还可以包括一弹性元件12323’,其中所述弹性元件12323’的一端连接于所述辅助气缸体121的所述作动端1214,并且所述弹性元件12323’的另一端连接于所述连杆12322’,用于为所述连杆12322’提供朝向所述凸轮12321’的弹力,使得所述连杆12322’能够在所述弹性元件12323’的作用下始终抵靠于所述凸轮12321’的所述外周缘。这样当所述凸轮12321’被驱动以转动时,所述连杆12322’带动所述辅助缸活塞122在所述辅助活塞腔1211内滑动当然,在本发明的其他示例中,所述弹性元件12323’的一端连接于所述辅助气缸体121的所述作动端1214,并且所述弹性元件12323’的另一端连接于所述辅助缸活塞122,用于为所述辅助缸活塞122提供朝向所述凸轮12321’的弹力,使得所述连杆12322’能够在所述辅助缸活塞122的推动下始终抵靠于所述凸轮12321’的所述外周缘。此时,所述弹性元件12323’可以但不限于被实施为一拉簧。进一步地,所述传动机构1232’的所述凸轮12321’可以但不限于被实施为具有单圈螺旋形结构的转轮,使得所述转轮的外周缘与所述转轮的转动轴心之间的距离逐渐变小,进而通过所述转轮的外周缘来推动所述连杆12322’移动,进而在所述连杆12322’的作用下,驱动所述辅助缸活塞122在所述辅助活塞腔1211内滑动。优选地,如图4b和图4c所示,所述凸轮12321’的外周缘设有多个平台,并且所有的所述平台与所述凸轮12321’的转动轴心之间的距离依次减小,以通过所述凸轮12321’的不同平台来固定所述辅助缸活塞122的滑动位置,进而使所述辅助燃烧室120具有不同体积的稳定空间。例如,如图5所示,所述凸轮12321’的外周缘设有六个平台,并且六个所述平台与所述凸轮12321’的转动轴心之间的距离依次减小,使得所述燃烧室100可以具有六个固定空间。值得注意的是,正是由于所述连杆12322’的一端抵靠于所述凸轮12321’的所述平台上,因此能够有效地避免因所述燃烧室100内气体膨胀而使所述辅助缸活塞122受力后,所述凸轮12321’被所述辅助缸活塞122推动而转动,以防所述燃烧室100的体积随意变动。与此同时,所述凸轮12321’的所述平台也有助于降低所述电机对转动角度精度的要求。此外,在实际设计所述凸轮12321’时,所述凸轮12321’的所述平台的数量越多,则所述辅助缸活塞122的位移量较多,相应地发动机的效率也越高,但所述凸轮连杆机构的稳定性则会降低。值得一提的是,在本发明的其他示例中,所述凸轮12321’也可以被实施为具有雨滴状结构的转轮,以便平滑地调整所述辅助缸活塞122的位移量,从而平滑地改变所述燃烧室100的体积,以满足不同工况的需求。根据本发明的另一方面,本发明进一步提供了一种机械设备,其配置有根据本发明的所述可变燃烧室体积的发动机10。具体地,如图5所示,所述机械设备1包括一设备主体20和所述可变燃烧室体积的发动机10,其中所述可变燃烧室体积的发动机10被装配于所述设备主体20,用于为所述设备主体20提供动力,以便组装成配置有可变燃烧室体积的发动机10的所述设备主体20。可以理解的是,所述机械设备1的所述设备主体20可以但不限于被实施为一汽车主体,以使所述机械设备1被实施为配置有所述可变燃烧室体积的发动机10的汽车。当然,在本发明的其他实施例中,所述机械设备1也可以被实施为配置有所述可变燃烧室体积的发动机10的其他机械设备。根据本发明的又一方面,如图6所示,本发明进一步提供了一种所述可变燃烧室体积的发动机的操作方法,包括步骤:s100:在一辅助气缸12的一辅助气缸体121内滑动所述辅助气缸12的一辅助缸活塞122,以改变所述辅助气缸12的一辅助燃烧室120的体积,其中所述辅助气缸12的所述辅助燃烧室120与一主气缸11的一主燃烧室110连通,以形成所述可变燃烧室体积的发动机10的一燃烧室100,其中所述主燃烧室110的体积恒定,以通过调整所述辅助燃烧室120的体积来改变所述燃烧室100的体积。在本发明的一示例中,如图6所示,所述可变燃烧室体积的发动机的操作方法中所述s100步骤,包括步骤:s110:通过电路控制所述辅助气缸12的一作动机构123的一驱动机构1231,以使所述驱动机构1231提供一驱动力;和s120:藉由所述作动机构123的一传动机构1232,将来自所述驱动机构1231的所述驱动力传递至所述辅助气缸12的所述辅助缸活塞122,以使所述辅助缸活塞122在所述辅助气缸体121内滑动。本领域的技术员应理解,上述描述及附图中所示的本发明的实施例只作为举例而并不限制本发明。本发明的目的已经完整并有效地实现。本发明的功能及结构原理已在实施例中展示和说明,在没有背离所述原理下,本发明的实施方式可以有任何变形或修改。当前第1页1 2 3