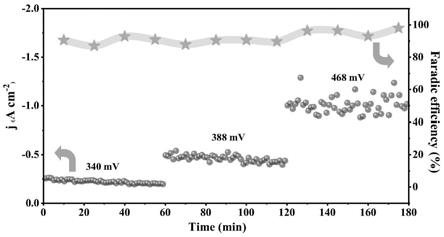
具有安培级电流密度析氢性能的mo/moo2面内异质结的制备
技术领域
1.本发明属于电催化析氢技术领域,更具体地,涉及一种具有安培级电流密度析氢性能的mo/moo2面内异质结的制备。
背景技术:2.构建全球可持续发展能源储存与转化系统是目前人类生存与发展的一个最为核心的挑战。作为最具潜力的清洁能源,氢能已纳入国家能源战略,成为优化能源消费结构和保障国家能源供应安全的重要选择。在众多的电解水制氢方法中,电解水制氢具有产氢量稳定、氢纯度高、装置简单、技术相对成熟等优势,是最有希望实现大规模产氢的方法。当前,制约电解水制氢工业化的关键因素在于电解水催化剂。尽管铂等贵金属催化剂具有显著的电催化产氢反应活性,但其价格高昂、储量极度稀缺,难以大规模工业化利用。安培级制氢(电流密度>1000ma cm
‑2)仍面临长足挑战。
3.在众多材料化学先驱学者们探索中,电催化领域有了长足的进步。然而当前电催化析氢材料仍存在电流密度低(10ma cm
‑2级别)等关键挑战。金属性过渡金属氧族化合物moo2因其独特的物理、化学性质,在电催化及能源储存及转化等领域具有潜在的应用。表面电子结构调控是丰富moo2等二维材料内在性质、拓宽其应用的前提。同时,对于多相催化反应,材料表面局域的双电层结构同样至关重要。面内结材料的制备是在moo2等二维材料的二维平面内引入外来物相晶格点阵的过程,这为设计调控材料性质提供了新的自由度。目前基于moo2的电催化析氢材料多局限于将moo2的二维平面作为锚定和分散活性相的基底,其催化电流往往较低,其制备繁琐,需要额外的工艺引入活性相。
4.因此,需要设计开发一种新型解决方案,充分利用moo2独特物理化学性质的同时,能调制其表面的电荷分布和局域的双电层结构,以设计和开发新型的基于moo2的安培级电催化析氢材料。
技术实现要素:5.针对现有技术的以上缺陷或改进需求,本发明的目的在于提供一种具有安培级电流密度析氢性能的mo/moo2面内异质结的制备,其中通过对制备方法的反应机理、整体流程工艺设计等进行改进,利用两步焙烧还原反应,可以由商业moo3粉末原料制备得到moo2/mo面内结材料,制备方法简单可控,得到的mo/moo2面内异质结材料富有褶皱结构,作为电催化制氢催化剂应用时,具有安培级的电催化反应活性,仅需468mv过电位即可提供超过1a cm
‑2的电流密度。将基于本发明制备方法得到的富褶皱的moo2/mo面内结材料作为例如以0.5m h2so4为电解液制备氢气的电催化剂应用时,该催化剂具有丰富的面内应变,此类应变对材料表面的电子结构和局域的双电层结构具有调制作用,有利于氢离子在催化剂表面富集并促进其吸附活化,为电催化析氢提供了丰富的活性位点和高的氢离子浓度,因此该材料表现出安培级电流密度析氢活性。对于面内结材料,moo2本身金属性可以确保在大电流催化时快速和充足的电子供应,同时由于其二维特性,在构建纳米级面内结后,可以最大化
活性表面积。在形成面内结后,材料表面可能存在局域不平衡的电场分布,能对双电层结构进行调制。同时要求面内结引入安全可控,成本低廉,能表现出安培级催化电流。
6.为实现上述目的,按照本发明,提供了一种具有安培级电流密度析氢性能的mo/moo2面内异质结的制备方法,其特征在于,包括以下步骤:
7.(1)前驱体moo2纳米片的制备:将原料moo3粉末放置于瓷舟内,随后将瓷舟置于加热炉中,在氢气和惰性载气的混合气氛下于800~1000℃进行焙烧,得到前驱体moo2纳米片;
8.(2)moo2/mo面内结材料的制备:将所述步骤(1)得到的所述前驱体moo2纳米片置于加热炉中,在氢气和惰性载气的混合气氛下于400~700℃进行焙烧,得到moo2/mo面内结材料;该moo2/mo面内结材料能够在468mv过电位条件下即可提供超过1a cm
‑2的电流密度。
9.作为本发明的进一步优选,所述步骤(1)中,所述混合气氛中氢气和惰性载气的的流量比为10:1~1:10;所述混合气氛的流量为50sccm~600sccm。
10.作为本发明的进一步优选,所述步骤(1)中,原料moo3粉末的质量不超过10g。
11.作为本发明的进一步优选,所述步骤(1)中,所述焙烧的时间为10min~120min。
12.作为本发明的进一步优选,所述步骤(1)中,所述加热炉为滑轨管式炉,并且所述焙烧是当所述滑轨管式炉的温度升温至预设的焙烧温度后,将该滑轨管式炉的中心温区移动至所述moo3粉末的中心进行的;
13.优选的,所述滑轨管式炉的升温速率为5~30℃min
‑1。
14.作为本发明的进一步优选,所述步骤(2)中,所述混合气氛中氢气和惰性载气的流量比为10:1~1:10;所述混合气氛的流量为50sccm~600sccm。
15.作为本发明的进一步优选,所述步骤(2)中,所述前驱体moo2纳米片的质量不超过9g。
16.作为本发明的进一步优选,所述步骤(2)中,所述焙烧的时间为10min~300min。
17.作为本发明的进一步优选,所述步骤(2)中,所述加热炉为滑轨管式炉,并且所述焙烧是当所述滑轨管式炉的温度升温至预设的焙烧温度后,将该滑轨管式炉的中心温区移动至所述前驱体moo2纳米片的中心进行的;
18.优选的,所述滑轨管式炉的升温速率为5~30℃min
‑1。
19.通过本发明所构思的以上技术方案,与现有技术相比,利用两步焙烧还原反应,可以由商业moo3粉末原料制备得到moo2/mo面内结材料,制备方法简单可控,得到的mo/moo2面内异质结材料富有褶皱结构,作为电催化制氢催化剂应用时,具有安培级的电催化反应活性。
20.本发明有效实现了前驱体moo2纳米片的宏量快速制备和mo/moo2面内异质结的可控构筑。常用的液相法或者cvd法往往很难得到二维moo2纯相纳米片,同时存在产量较低、制备周期长、制备过程繁琐和难以放大的问题。在本发明采用的两步焙烧还原法中,首先直接利用商用moo3粉末作为合成二维moo2纳米片的原料。moo3是一种层状材料,其熔点为795℃,在低于熔点的情况下,该材料也能发生显著升华。利用moo3特殊的晶体结构和物理性质,本发明采用的快速还原焙烧使得商用moo3粉末骤热,随后升华成片状moo3晶体。片状moo3晶体在流动的氢气和惰性载气的混合气氛中发生短暂的还原反应,最终得到当量二维moo2纳米片。容易理解,仅需控制商用moo3粉末的量和混合气氛的流量比例,即可在一定程
度上实现实验的放大,得到宏量的二维moo2纳米片前驱体。
21.本发明优选采用滑轨管式炉,以确保商用moo3粉末能骤热并升华成片状moo3晶体;本发明采用快速还原焙烧法,能够避免随炉升温焙烧产生副产物mo粉末。考虑到反应时间极短,容易理解,理论上仅需控制氢气过量及焙烧温度即可实现该过程。随后本发明利用得到的moo2纳米片作为前驱体,利用其二维平面作为模板,利用氢气的还原性,对表面的氧含量进行调控,从而引入mo/moo2面内结。为了引入丰富的表面褶皱,本发明优选采用快速还原焙烧法对moo2前驱体进行处理,氧的快速丢失引发局域的晶格失配并产生应变,最终得到富褶皱的moo2/mo面内结催化剂。容易理解,理论上仅需控制反应时间、焙烧温度和氢气含量中任一参数,即可对氧含量即mo/moo2面内结含量进行调控。
22.本申请将富褶皱的moo2/mo面内结催化剂作为以0.5m h2so4为电解液制备氢气的电催化剂,该催化剂具有丰富的面内应变,此类应变对材料表面的电子结构和局域的双电层结构具有调制作用,有利于氢离子在催化剂表面富集并促进其吸附活化,为电催化析氢提供了丰富的活性位点和高的氢离子浓度,因此富褶皱的moo2/mo面内结催化剂具有安培级电流密度析氢活性。实验结果表明,该催化剂仅需468mv的过电位即可提供1a cm
‑2的催化产氢电流。同时在材料的制备过程中,操作快速便捷,反应简单可控。
23.综上,基于本发明特定制备方法得到的富褶皱的moo2/mo面内结材料是种安培级电催化制氢材料,尤其可作为电催化产氢的催化剂。由于该材料具有丰富的表面应变,为电催化制氢提供了丰富的活性位点,同时能调制双电层离子的表面富集,因此该材料表现出安培级电流密度析氢活性。该材料的制备方法快速便捷,反应简单可控。同时该催化剂为粉体形式,环境适应能力强,有望应用于质子交换膜燃料电池等特殊场景。
附图说明
24.图1为本发明制备的前驱体moo2纳米片和富褶皱moo2/mo催化剂的不同放大倍数的透射电子显微镜图像。其中,图1中自左向右分别对应制备方法第二次焙烧开始前的前驱体moo2纳米片以及第二次焙烧焙烧时间为30min、90min、150min、210min的样品。在不同放大倍数下观察个样品的形貌特征可知,前驱体moo2纳米片具有平坦的二维平面,而还原焙烧后的样品由于存在表面应变,形成了丰富的表面褶皱和纳米孔洞。
25.图2为本发明制备的前驱体moo2纳米片和富褶皱moo2/mo催化剂的原子力显微镜图像,其中,图2中的(a)对应前驱体moo2纳米片,图2中的(b)对应第2步还原焙烧时间为90min得到的富褶皱moo2/mo催化剂。
26.图3为本发明制备的前驱体moo2纳米片和富褶皱moo2/mo催化剂的x射线粉末衍射谱,其中,图3中的(b)为图3中的(a)的局部放大图。
27.图4为本发明制备的前驱体moo2纳米片和富褶皱moo2/mo催化剂的拉曼光谱,其中,图4中的(b)为图4中的(a)的局部放大图。
28.图5为本发明制备的前驱体moo2纳米片和富褶皱moo2/mo催化剂和相关对照样品的线性伏安扫描曲线图谱。
29.图6为本发明制备的富褶皱moo2/mo催化剂电催化产氢的稳恒电压测试及法拉第效率(以90min样品为例)。
30.图7为本发明制备的富褶皱moo2/mo面内结催化剂高分辨透射电子显微镜图像(以
90min样品为例);其中,图7中的a1和图7中的a2分别为图7中的a所示对应区域的放大图。
31.图8为本发明在优选的实验参数下(900℃反应30min)制备的前驱体moo2纳米片与相应边界条件下制备样品的xrd衍射花样。其中800℃反应120min样品和900℃反应30min样品的xrd衍射花样指标为纯相moo2。1000℃反应10min样品的主要物相为moo2,但是存在mo
x
o
y
多聚体杂质。可能是由于反应温度过高,导致升华的二维moo3晶体过多,部分二维moo3晶体没有完全反应。
32.图9为本发明优选的实验参数(550℃反应90min)制备的mo/moo2面内结与相应边界条件制备样品的xrd衍射花样。三个样品的衍射花样均含有moo2和mo这两种物相的衍射信号。其中400℃反应300分钟样品仅含有极微量的mo,这说明400℃这个边界温度比较低,还原反应特别慢。550℃反应90分钟和700℃反应10分钟样品仅含有极微量的moo2,还原反应较为彻底。其中700度作为边界温度,是一个相对较高的温度,此时还原反应速率很快,相对而言此条件下反应更不可控。
33.图10为本发明优选的实验参数(550℃反应90分钟)制备的mo/moo2面内结与相应边界条件制备样品的电催化产氢性能。优选的样品相对于两个边界条件样品表现出最优的电催化析氢性能。
具体实施方式
34.为了使本发明的目的、技术方案及优点更加清楚明白,以下结合附图及实施例,对本发明进行进一步详细说明。应当理解,此处所描述的具体实施例仅仅用以解释本发明,并不用于限定本发明。此外,下面所描述的本发明各个实施方式中所涉及到的技术特征只要彼此之间未构成冲突就可以相互组合。
35.实施例1
36.本发明实施例公开了一种安培级电催化制氢材料及其制备方法,包括:
37.前驱体moo2纳米片的制备:将商用moo3粉末放置于瓷舟中,随后将瓷舟置于滑轨管式炉中,在氢氩混合气氛(当然,也可以是氢气与其他惰性载气的混合气氛)中高温焙烧,得到前驱体moo2纳米片;
38.富褶皱的moo2/mo面内结材料的制备:将前驱体moo2纳米片放置于瓷舟中,随后将瓷舟置于滑轨管式炉中,在氢氩混合气氛中高温焙烧,得到富褶皱的moo2/mo面内结材料。
39.本发明提供的富褶皱的moo2/mo面内结材料可作为电催化产氢的电催化剂,由于富褶皱的moo2/mo面内结材料具有丰富的表面应变,为电催化产氢提供了丰富的活性位点,同时能调制局域的双电层结构实现氢离子的表面富集,因此该材料表现出安培级电流密度析氢活性。且该材料的制备方法快速便捷,反应简单可控。
40.在电催化产氢过程中,本申请采用的电催化剂为富褶皱的moo2/mo面内结材料,该材料具有丰富的表面应变,其形貌特征表现为多裂纹、突起和褶皱,整体为纳米片结构,片尺寸200~1000nm,厚度为2~10nm。所述富褶皱的moo2/mo面内结材料的制备方法包括前驱体moo2纳米片的制备和富褶皱的moo2/mo面内结材料的制备两个过程,即将商用moo3粉末放置于瓷舟中,随后将瓷舟置于滑轨管式炉中,在氢氩混合气氛中高温焙烧,得到前驱体moo2纳米片;随后将该前驱体放置于瓷舟中,随后将瓷舟置于滑轨管式炉中,在氢氩混合气氛下进行焙烧,化学还原拓扑转化得到富褶皱的moo2/mo面内结材料。具体的,所述富褶皱的
moo2/mo面内结材料的制备方法为:
41.前驱体moo2纳米片的制备:将商用moo3粉末放置于瓷舟中,随后将瓷舟置于滑轨管式炉中,在氢氩混合气氛中高温焙烧,得到前驱体moo2纳米片;
42.富褶皱的moo2/mo面内结材料的制备:将前驱体moo2纳米片放置于瓷舟中,随后将瓷舟置于滑轨管式炉中,在氢氩混合气氛中高温焙烧,得到富褶皱的moo2/mo面内结材料。
43.在上述前驱体moo2纳米片的制备过程中,所述商用moo3粉末的质量为0.2~10g,采用的加热方法为快速退火,升温速率为5~30℃min
‑1,焙烧时间为10~120min,上述前驱体moo2纳米片的具体制备过程为:
44.称取商用的moo3粉末放置、堆垛于瓷舟中,将瓷舟置于滑轨管式炉适当位置,通以氢氩混合气氛后升温,升温过程结束后移动滑轨炉至中心温区与商用moo3粉末中心重合,开始焙烧,焙烧结束得到前驱体moo2纳米片;在某些具体的实施例中,所述称取的商用的moo3粉末质量为0.5g,焙烧的温度为900℃,焙烧的时间为30min,升温速率为20℃min
‑1,焙烧的氢氩混合气的比例为2:8,混合气总体积100sccm。
45.本申请然后将得到的前驱体moo2纳米片进行焙烧,利用化学还原拓扑转化得到富褶皱的moo2/mo面内结材料;所述焙烧的温度为400~700℃,焙烧的时间为10min~300min,升温速率为5~30℃min
‑1,焙烧的氢氩混合气的比例为10:1~1:10,混合气总体50~600sccm;在某些具体的实施例中,所述称取的前驱体moo2纳米片质量为3mg,焙烧的温度为550℃,焙烧的时间为30min、90min、150min和210min,升温速率为20℃min
‑1,焙烧的氢氩混合气的比例为2:8,混合气总体积100sccm。
46.在制备富褶皱的moo2/mo面内结材料时,首先制备了前驱体moo2纳米片,利用快速还原焙烧时商用moo3粉末骤热升华并形成二维moo3晶体蒸汽,该蒸汽随后在氢氩混合还原气氛下发生还原反应得到前驱体moo2纳米片;后续在氢氩混合还原气氛下,利用高温化学还原拓扑转化的方法在moo2平坦表面引入第二相mo,得到富褶皱的moo2/mo面内结材料。
47.为了验证富褶皱的moo2/mo面内结材料的安培级电流密度析氢活性,作为示例,本申请将制备的富褶皱的moo2/mo面内结材料作为电催化剂,在0.5m h2so4中进行电催化制氢反应;即,首先将富褶皱的moo2/mo面内结材料在nafion的乙醇溶液中分散制成分散液,并滴覆在玻碳电极上晾干,随后该电极作为工作电极进行后续的电催化制氢反应。为了避免引入杂质,所述0.5m h2so4中的水一般优选为去离子水。上述分散液的制备过程具体为:
48.将富褶皱的moo2/mo面内结材料加入到nafion的乙醇溶液中,超声震荡30min。具体的,分散液中富褶皱的moo2/mo面内结材料的浓度为2~10mg ml
‑1,nafion的乙醇溶液中nafion的体积分数为0.2%~1%。用移液枪移取适量分散液滴覆在玻碳电极上晾干。具体的,移液枪移取的分散液体积为5~10μl,玻碳电极的直径为3mm。在具体的实施例中,分散液浓度为5mg ml
‑1,nafion的体积分数为0.5%,移液枪取的分散液体积为7ul。晾干后工作电极制备完成。随后对富褶皱的moo2/mo面内结材料的安培级电流密度析氢活性进行验证,将所述工作电极、饱和ag/agcl参比电极和石墨棒对电极构成三电极体系,利用辰华chi660e电化学工作站作为直流电源,在0.5m h2so4溶液中进行循环伏安测试,同时用气相色谱检测气体产物计算法拉第效率。
49.如图4和图5所示,可以证明富褶皱的moo2/mo面内结材料具有安培级电流密度析氢活性,仅需468mv过电位即可提供1000ma cm
‑2的催化产氢电流密度,且其法拉第效率接近
100%。
50.如图1所示,前驱体moo2纳米片具有平坦的二维平面,其横向尺寸在数百纳米到几个微米之间,其较低的衬底表明其厚度超薄。还原焙烧后的样品基本维持了前驱体moo2纳米片的形貌特征,同时由于存在表面应变,在样品形成了丰富的表面褶皱和纳米孔洞。以反应30min样品为例,该样品部分纳米片边缘卷起,还可以观察到纳米级孔洞和纳米级褶皱(衬度较大),这说明存在面内应变。
51.如图2所示,前驱体moo2纳米片为超薄二维纳米片,其表面平坦,厚度在6.1nm左右。以反应90min样品为例,该样品厚度略微减薄到4.89nm,表面有明显起伏的褶皱存在,与图1的观察与分析的结果一致。
52.如图3、图4所示,前驱体moo2纳米片的x射线衍射花样指标为纯相moo2。处理后的样品随着时间的延长,mo的含量逐渐增加,在本实施例的处理条件下,处理时间在150min以上的样品x射线衍射花样指标为纯相mo单质。说明可通过调节处理时间对氧含量即mo/moo2面内结含量进行调控。右侧放大区域为mo单质x射线衍射花样的特征峰,处理后样品的该峰位发生偏移,说明存在面内应变。
53.如图5所示,前驱体moo2纳米片和商用mo粉的极化电流密度很小,说明其her催化性能很差。而本实施例处理后的面内结材料随着过电位增大,极化电流密度迅速增大,均现出安培级电流密度的析氢性能。以反应90min样品为例,过电位较大时(>600mv),其性能可与商用pt/c媲美。
54.如图6所示,以反应90min样品为例,该样品的在不同极化电位下的电流时间曲线较为稳定,说明其循环稳定性能优异。该样品仅需要468mv的过电位即可提供1ma cm
‑2的催化电流密度。同时,借助气相色谱检测气体产物可知,该样品在不同电位下均表现出超过85%的法拉第效率。
55.如图7所示,以反应90min样品为例,可以观察到该样品原子相中存在两种物相,晶格间距为0.235nm的物相指标为mo(110),晶格间距为0.220nm的物相指标为moo2(021)。这说明成功引入了mo/moo2面内结。同时相比于mo(110)和moo2(021)的理论晶格间距,即分别为0.2247nm和0.2171nm,mo(110)面晶格间距显著增大,说明存在面内应变。整个原子相衬度明暗的显著变化,说明存在丰富的纳米级褶皱。
56.实施例2
57.容易理解,在制备前驱体moo2纳米片的过程中,混合气的总流速决定了升华二维moo3晶体的停留时间即还原反应时间,保温温度和还原性氢气的分压决定了还原反应的速率,焙烧时间则确保商用moo3粉末都能充分升华并还原。对于宏量放大实验,本发明建议在直径较大的石英管中进行,容易理解,当采用较大石英管时,可适当增大混合气流量来保证流速即还原反应时间恒定,还应适当延长保温时间使商用moo3粉末充分升华反应。同样的策略也适用于当焙烧温度较低如800℃时。为保证滑轨炉使用寿命,本申请不建议在较高如1000℃以上进行本实验。为确保反应可控,在具体的实施例中,本实验采用直径2.5厘米石英管进行反应,控制混合气体总流量为100sccm,以制备前驱物moo2纳米片。
58.为说明以上参数对反应的影响,本申请设计如下实验:称取0.5g商用moo3粉末置于瓷舟,在滑轨管式炉中于1000℃下在20/80sccm的氢氩混合气氛下反应10min,收集产物;称取0.5g商用moo3粉末置于瓷舟,在滑轨管式炉中于800℃下在20/80sccm的氢氩混合气氛
下反应120min收集产物;称取0.5g商用moo3粉末置于瓷舟,在滑轨管式炉中于900℃下在20/80sccm的氢氩混合气氛下反应30min,收集产物。在以上的控制实验中,后两者产物的xrd衍射花样均指标为moo2,说明本实验具有较好的可控性。其中1000℃反应10min的产物主要物相为moo2,但是由于该温度太高,商用moo3粉末的升华速度过快,导致部分升华的二维moo3晶体未完全反应。而800℃这个温度相对较低,升华速度很慢,尽管反应了120min,瓷舟中仍然有大量粉末剩余,这时可能发生了生成mo颗粒的副反应,而不能得到当量前驱体moo2纳米片。
59.实施例3
60.与前驱体moo2纳米片的制备过程不同,在制备mo/moo2面内结时,前驱体moo2作为反应物直接参与到反应中,因此焙烧时间即为还原反应时间,该参数直接影响了还原程度。混合气流速对反应的影响相对较小,还原性氢气的分压和焙烧温度则决定了还原速率。因此,对焙烧时间、氢气分压和焙烧温度这三个参数进行配合控制可对最终的还原效果进行调控。容易理解,当控制焙烧温度较低如。在宏量放大实验中,因前驱体moo2纳米片超高的比表面积,为确保还原性氢气与其充分接触,本申请建议采用直径较大的石英管使前驱体充分铺展。为确保反应可控,在具体的实施例中,本实验采用直径2.5cm石英管进行反应,控制前驱体moo2的质量为5mg,混合气体总流量为100sccm,以制备前驱物mo/moo2面内结。
61.为说明以上参数对反应的影响,本申请设计如下实验:将称好的前驱体moo2纳米片置于瓷舟,在滑轨管式炉中于400℃在20/80sccm的氢氩混合气氛下反应300min,收集产物;将称好的前驱体moo2纳米片置于瓷舟,在滑轨管式炉中于550℃在20/80sccm的氢氩混合气氛下反应90min,收集产物;将称好的前驱体moo2纳米片置于瓷舟,在滑轨管式炉中于700℃在20/80sccm的氢氩混合气氛下反应10min,收集产物。如图9所示,三个样品的衍射花样均含有moo2和mo这两种物相的衍射信号。其中400℃反应300min样品仅含有极微量的mo,这说明400℃这个边界温度比较低,还原反应特别慢,该样品仅发生了极轻度的还原。由于此时得到的mo/moo2面内结的主体物相为moo2,该样品的电催化产氢性能仅有程度较小的提升。而同样在适中的550℃下,反应较为可控,仅需通过调控反应时间即可控制面内结含量,优选的样品在550℃下反应90min后得到了理想的mo/moo2面内结材料,此时主体物相为mo,同样表现出了安培级的电催化析氢性能。而在700℃这个相对较高的反应温度下,还原速度很快,仅需10min便得到了与优选条件还原程度相当的面内结合材料,该材料的性能提升幅度适中。可能是高温下样品的晶格会发生重构,导致面内应力较小。
62.本领域的技术人员容易理解,以上所述仅为本发明的较佳实施例而已,并不用以限制本发明,凡在本发明的精神和原则之内所作的任何修改、等同替换和改进等,均应包含在本发明的保护范围之内。