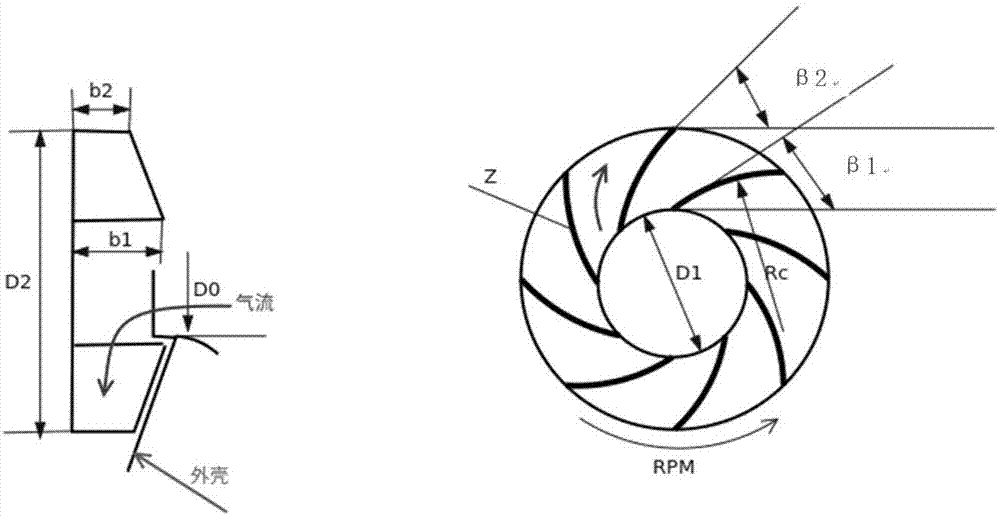
本发明属于离心风机设计领域,特别涉及了一种中小型离心风机空气动力学工程优化方法。
背景技术:
本发明的主要应用对象为离心风机。尤其是民用领域内如空调、空气净化器、电子设备散热器等所产品所使用的中小型离心风机。该类风机一般关注于噪音的控制,而对于效率的问题则不甚考虑。同时,相比于工业领域,该类产品往往追求外型设计,这对于其内部动力提供者——离心风机的设计造成了诸多的几何限制。依赖于流体机械相似定律的传统设计方法由于没有可以参照的成熟风机型号在此无法应用,而完成一个新型风机的空气动力学设计则完全超出了一般生产商的能力范围。大型科研单位则由于此类风机经济价值低廉,而研发费用相对较高则不愿为此付出太多精力。此外,此类多叶离心通风机的工程设计方法并不是非常成熟,经常在多次试算后才能达成设计指标,甚至无法完成设计指标,费时且费力。技术实现要素:为了解决上述
背景技术:
提出的技术问题,本发明旨在提供一种离心风机空气动力学设计方法并以计算机软件方式实现。该方法不但可以根据客户给定的通风机基础设计指标(流量、压力)迅速提供一种推荐方案,同时在存在几何约束的条件下,如限定通风机的最大叶轮外径,或者限定通风机的最大宽度,或者限定叶轮的最小内径等情形下,也可以提供满足要求的设计方案。还可以发现现有风机型号的某些不合理设计。并且,对于大型离心通风机设计,本发明也可以提供优良的初始设计,大大减少了研发费用。为了实现上述技术目的,本发明的技术方案为:一种离心风机设计优化方法,包括以下步骤,步骤1,确定离心风机设计指标:设计流量qn,设计总压pn;步骤2,建立离心风机的空气动力学性能函数:其中,表示标准状态下该型风机的空气动力学性能参数,其包括总压pt,静压ps,动压p,静压效率ηs,总压效率ηi;q为流量,n为转速,为几何参数;步骤3,通过优化算法使总压pt达到设计总压pn,由此确定几何参数其中,优化算法如下:1)对离心风机某一几何参数g施加一个扰动δg,该几何参数g属于的某一分量;2)获取该几何参数g的扰动产生的总压扰动δp;3)获取梯度信息:t=δp/δg;4)对所述几何参数g施加增量δg=(pn-pt)/t;5)计算施加所述增量δg后的总压pt;6)重复步骤1)-5),直至所述总压pt达到所述设计总压pn。进一步地,几何参数包括,叶轮外径d2,叶片出口安装角β2,叶片出口宽度b2,叶轮内径d1,叶片入口安装角β1,叶片入口宽度b1,叶片数目z,叶片形状,叶片厚度h。上述空气动力学性能函数获取方式如下,离心风机的空气动力学的工程设计表示为:其中,pi为通过计算得到的总压;对于任一设计所得的几何外形,首先要通过迭代计算其实际总压:其中,i=0,1,2…;初始条件:p0=pn;当迭代计算满足退出条件:时(ε为一小量,工程上取ε=0.001即可满足要求。有时甚至可放宽至3%~1%),即认为该计算收敛,从而获得了该外形下空气动力学性能函数:进一步地,在预设转速n下,通过所述优化算法,调整叶片出口宽度b2以实现所述设计指标。进一步地,限定叶片等宽b1=b2,并预设转速n下,通过所述优化算法,调整叶轮外径d2以达到所述设计指标。进一步地,限定叶片等宽b1=b2,并限定最大叶轮外径d2及最大转速下,通过所述优化算法,调整叶片出口角β2以达到所述设计指标。本发明主要具有以下的技术优点:(1)对于几何外形确定的多叶离心风机,通过计算机程序实现了一种快速估算其气动性能的工程方法。该方法在精度上优于传统的工程方法,同时在计算代价上远小于采用cfd(计算流体动力学)的方式。(2)在给定的设计指标:流量q,总压p,在预设转速rpm下,通过最优化算法,自动调整叶片出口宽度b2以实现设计指标。(3)在给定的设计指标:流量q,总压p,限定叶片等宽(b1=b2),在预先设定的转速rpm下,通过最优化算法,自动调整叶轮外径d2以达到设计指标。(4)在给定的设计指标:流量q,总压p,限定叶片等宽(b1=b2),并限定最大叶轮外径及最大转速,通过最优化算法,自动调整叶片出口角β2以逼近设计指标。附图说明图1为表示本发明的离心风机空气动力学略图。图2为本发明的通用离心风机的设计流程图。图3为本发明的多叶离心风机的设计流程图。图4为本发明的调整离心风机叶片出口宽度的设计流程图。图5为本发明的调整离心风机叶轮外径的设计流程图。图6为本发明的调整离心风机叶片出口安装角的设计流程图。具体实施方式下面结合附图实施例对本发明作进一步说明,对本发明的实施例所涉及的离心风机设计方案进行详细说明,但这些说明不构成对本发明的保护范围的限制。图1为表示本发明的离心风机空气动力学略图。其主要的设计指标包括:·流量q(单位:m3/h)·总压pt(单位:pa)与空气动力学性能相关的几何参数主要包括:·叶轮外径d2·叶片出口安装角β2·叶片出口宽度b2·叶轮内径d1·进风口直径d0·叶片入口安装角β1·叶片入口宽度b1·叶片数目z·叶片形状(简单的圆弧叶片用半径rc及弧心角α表示)·叶片厚度δ(机翼型叶片使用迎风面及背风面坐标表示)离心风机的空气动力学性能可以表示为函数:表示标准状态下该型风机的空气动力学性能参数(包括总压pt,静压ps,动压p,静压效率ηs,总压效率ηi等)。n即转速rpm。对离心风机叶轮进行优化设计,其空气动力学性能计算模型如下:本发明的离心风机的空气动力学的工程设计可以表示为:其中qn为设计流量,pn为设计总压,或目标压力。n为转速,为几何参数,p为通过计算得到的总压,其值可能与目标压力不一致。由此看出,对于任一根据工程经验设计所得的几何外形,首先要通过迭代计算其实际总压:其中,i=0,1,2…;初始条件:p0=pn;当迭代满足退出条件时,即认为该计算收敛,从而获得了该外形下的气动性能:一般而言,此时得到的总压pt与目标压力pn并不一致。传统设计方法通过调整几何参数,并经过多次试算后才可能达到一个比较满意的结果。本发明则采用优化算法在各种不同的设计约束下来达到设计目标。使用优化算法的基本思路如下:1)首先,对某一几何参数g(属于的某一分量)施加一个扰动(微小增量)δg;2)该几何扰动产生的总压扰动(微小的增量或减量)为δp;3)据此获得了当前几何构型(设计状态)下的梯度信息:t=δp/δg;4)对该几何参数施加增量δg=(pn-pt)/t;5)计算新的几何构型下的气动性能其中包括总压pt;6)重复1)~5),直至总压pt达到设计总压pn。实施例一(图2)图2为表示本发明的实施例一所涉及的通用离心风机的设计流程图。如图2所示,通用离心风机的设计流程具体步骤如下:步骤1,确定离心风机设计流量qn(m3/s)和设计总压pn(pa);步骤2,设定转速rpm;步骤3,计算比转速ns;步骤4,预选压力系数ψ;步骤5,确定出口安装角β2;步骤6,确定叶轮外径d2;步骤7,设计进风口直径d0;步骤8,确定叶轮内径d1;步骤9,确定入口宽度b1;步骤10,确定入口安装角β1;步骤11,优选叶片数z;步骤12,确定出口宽度b2;步骤13,验证总压pt;步骤13,设计轮盖与蜗壳;最后,结束离心风机的设计流程。实施例二(图3)图3为表示本发明的实施例二所涉及的多叶离心风机的设计流程图。对于多叶离心风机的空气动力学模型不同于普通风机,不能采用实施例一中所述的设计流程。其可行的设计流程如图3所示,具体步骤如下:步骤1,确定离心风机设计流量qn(m3/s)和设计总压pn(pa);步骤2,设定转速rpm;步骤3,计算比转速ns;步骤4,预选叶片安装角β1及β2;步骤5,预选压力系数ψ;步骤6,确定叶轮外径d2;步骤7,确定叶轮内径d1;步骤8,确定叶片宽度b;步骤9,优选叶片数z;步骤10,验证总压pt;步骤11,设计轮盖;步骤12,设计蜗壳;最后,结束多叶离心风机的设计流程。实施例三(图4)图4为表示本发明的调整离心风机叶片出口宽度的设计流程图。对于非等宽叶片,调整出口宽度可以改变离心风机叶轮出口压力。使用最速下降法,一般可以得到比较满意的结果。此时使用的梯度信息为:对于等宽叶片,定义其宽度为b=b1=b2,梯度信息定义为:其可行的设计流程如图4所示,具体步骤如下:步骤1,确定离心风机设计流量qn(m3/s)和设计总压pn(pa);步骤2,设定转速rpm;步骤3,预选叶片安装角β1及β2;步骤4,确定叶轮外径d2及叶轮内径d1;步骤5,优选叶片数z;步骤6,确定叶片宽度b;步骤7,判断总压pt是否达标;如果达标,则结束离心风机的设计流程;如果不达标,则进入步骤8;步骤8,计算δb,并对该几何参数叶片宽度b施加上述增量δb,重复上述步骤7,直至总压pt达标,结束离心风机的设计流程。实施例四(图5)图5为表示本发明的调整离心风机叶轮外径的设计流程图。对于离心风机,增大叶轮外径是增大风机总压最直接的方法。但很多时候,叶轮外径存在尺寸限制的。对于调整叶轮外径所使用的梯度信息为:其可行的设计流程如图5所示,具体步骤如下:步骤1,确定离心风机设计流量qn(m3/s)和设计总压pn(pa);步骤2,设定转速rpm;步骤3,计算比转速;步骤4,确定叶轮外径d2;步骤5,确定各几何参数:风机入口直径d0,叶轮内径d1,叶片入口宽度b1,叶片入口安装角β1,叶片数z;步骤6,判断总压pt是否达标;如果达标,则结束离心风机的设计流程;如果不达标,则进入步骤7;步骤7,计算δd2,并对该几何参数d2施加上述增量δd2,重复上述步骤6,直至总压pt达标,结束离心风机的设计流程。实施例五(图6)图6为表示本发明的调整离心风机叶片出口安装角的设计流程图。调整叶片出口角安装角β2所使用的梯度信息为:如图6所示,调整离心风机叶片出口角安装角β2的设计流程具体步骤如下:步骤1,确定离心风机设计流量qn(m3/s)和设计总压pn(pa);步骤2,设定转速rpm;步骤3,计算比转速;步骤4,预选压力系数;步骤5,确定出口安装角β2;步骤6,确定各几何参数:叶轮外径d2,风机入口直径d0,叶轮内径d1,叶片入口宽度b1,叶片入口安装角β1,叶片数z;步骤7,判断总压pt是否达标;如果达标,则结束离心风机的设计流程;如果不达标,则进入步骤8;步骤8,计算δβ2,并对该几何参数β2施加上述增量δβ2,重复上述步骤7,直至总压pt达标,结束离心风机的设计流程。实施例六:最优叶片数z的设计传统工程方法一般使用叶片出口安装角β2来确定最优叶片数范围。最终的叶片数则取决于工程经验及空气动力学实验。本发明对于最优叶片数则直接根据直列叶栅理论来确定。设计实例1(某型通用离心风机设计)某小型风机的设计要求如下:对此风机无几何约束条件。采用通用风机设计流程,所得设计结果如下:设计实例2(某型多叶离心风机设计-叶轮宽度优化)某小型风机(tr2866)的设计要求如下:实际应用中,对应于该设计的原型风机参数如下:该型风机在转速上升到1100转/分后,流量即无法达到工况要求。在限定叶轮外径d2<212mm的几何约束条件下,采用多叶离心通用风机设计流程,所得设计结果如下:有设计结果可见,原有设计除叶片形状不合理外,主要问题在于叶轮宽度不足。实际工况要求该风机叶轮宽度需增大至84mm。设计实例3(叶轮外径d2优化设计实例)某小型风机(tr2809)原始几何参数如下:外径d2=91mm内径d1=73mm出口安装角β2=67°入口安装角β1=70°叶片宽度b=22mm叶片数z=45该型风机在达到rpm=1900转/分时,流量为q=33.5m3/小时。现希望该型风机在其他条件不变的情况下,其流量q>=37m3/h。根据计算,将其设计指标定为:在确保新风机外形尺寸不大于原风机的情况下,预设β2=26°,使用调整叶轮外径的方法,新风机设计结果如下:由上可见,新风机在满足设计要求的情况下,整体尺寸反而缩小了约5.5%。设计实例4(叶片出口安装角β2优化实例)某小型风机(tr2826)原始几何参数如下:外径d2=240mm内径d1=73mm出口安装角β2=28°入口安装角β1=87°叶片宽度b=64mm叶片数z=45该型风机在达到rpm=1000转/分时,出现流量不足的现象。分析表明,此现象由于风机压力不足导致。现拟将该风机总压指标提高15pa,从而将其设计指标定为:在其他几何参数不变的情况下,使用调整叶片出口安装角β2的方法,新风机设计结果如下:新设计将叶片出口安装角从28度增大到38度(相应地,叶片数也发生了变化),从而满足了实际风机工作需要。以上对本发明所提供的一种离心风机设计优化方法进行了详尽介绍,本文中应用了具体个例对本发明的原理及实施方式进行了阐述,以上实施的说明只是用于帮助理解本发明的方法及其核心思想;同时,对于本领域的一般技术人员,依据本发明的思想,在具体实施方式及应用范围上均会有改变之处,对本发明的变更和改进将是可能的,而不会超出附加权利要求所规定的构思和范围,综上所述,本说明书内容不应理解为对本发明的限制。当前第1页12