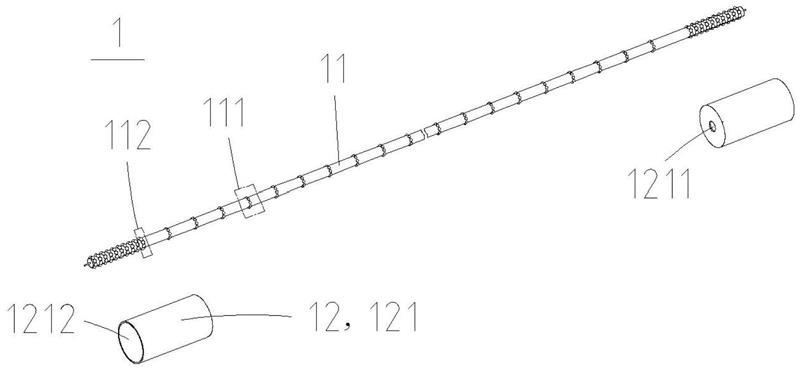
[0001]
本发明涉及风机技术领域,尤其涉及一种用于风机的降噪装置。
背景技术:[0002]
吸油烟机已成为现代家庭中不可或缺的厨房家电设备之一,风量、风压、噪声是吸油烟机的核心指标。最近几年,国内的烟机市场一直主推大风量、大吸力概念,随着风量的逐步提高,吸油烟机产生的噪声也越来越大。开启吸油烟机时便会听不到说话声、电话声、门铃声以及孩子声音,甚至吸油烟机工作产生的强噪音会使厨房操作人员产生烦躁,头痛,心悸等不良反应,长期使用,会对身心健康造成严重影响。
[0003]
随着人们对生活品质要求的提高,用户在选购吸油烟机时,越来越关注烟机噪音参数的大小,可见,烟机噪声性能的优劣是产品竞争力的一大关键因素。因此,噪音成为现有吸油烟机存在的亟待解决的技术问题。
技术实现要素:[0004]
本发明旨在至少在一定程度上解决现有相关技术中存在的问题之一,为此,本发明提出一种可消耗脱落涡能量的降噪装置,其结构简单、巧妙,能够消除脱落涡的能量,从而达到降噪的目的。
[0005]
本发明还提供了一种具有该降噪装置的离心风机,通过降噪装置,可显著降低离心风机工作产生的噪音,提升用户体验和公司产品竞争力。
[0006]
根据上述提供的一种可消耗脱落涡能量的降噪装置,其通过如下技术方案来实现:
[0007]
一种可消耗脱落涡能量的降噪装置,所述降噪装置包括旋转轴,所述旋转轴能够随脱落涡的转动而转动,在所述旋转轴外表面上设有若干沿长度方向间隔布置的第一凸起组,和/或在所述旋转轴的两端分别连接有用于消耗脱落涡能量的阻尼耗能结构,所述旋转轴与所述阻尼耗能结构可转动连接。
[0008]
在一些实施方式中,所述旋转轴为中空圆柱体,且所述旋转轴由塑料制成。
[0009]
在一些实施方式中所述第一凸起组包括沿所述旋转轴周向方向间隔布置的若干第一子凸起。
[0010]
在一些实施方式中,所述阻尼耗能结构包括壳体,所述壳体面向所述旋转轴的一面设有供所述旋转轴穿过的开孔,所述旋转轴的端部穿过所述开孔后伸入到所述壳体内。
[0011]
在一些实施方式中,所述阻尼耗能结构还包括若干弹性片,所述弹性片设置于所述壳体内且其连接端连接所述壳体的内侧壁,自由端延伸至所述旋转轴的侧壁外侧。
[0012]
在一些实施方式中,所述弹性片的数量为两个,两个所述弹性片的自由端分别位于所述旋转轴的相对两侧壁外侧。
[0013]
在一些实施方式中,在所述壳体内充填有粘性流体。
[0014]
在一些实施方式中,所述第一凸起组位于两个所述壳体之间,在所述旋转轴的外
表面还设有若干沿长度方向布置的第二凸起组,所述第二凸起组位于所述壳体内和/或两个所述壳体之间。
[0015]
在一些实施方式中,所述第二凸起组包括沿所述旋转轴周向方向间隔布置的若干第二子凸起。
[0016]
根据上述提供的一种离心风机,其通过如下技术方案来实现:
[0017]
一种离心风机,包括蜗壳和叶轮,所述蜗壳具有进风口和出风口,所述叶轮可转动设置于所述蜗壳内,其中还包括如上所述的降噪装置,在所述叶轮的出风孔处设有所述降噪装置,所述降噪装置的两端分别连接所述蜗壳的正面和背面。
[0018]
在一些实施方式中,所述蜗壳的正面具有环绕所述进风口布置的第一弧形区域和第二弧形区域,所述第一弧形区域靠近所述出风口布置,所述第二弧形区域远离所述出风口布置;位于所述第一弧形区域的所述旋转轴的直径为4mm~8mm,位于所述第二弧形区域的所述旋转轴的直径为1.5mm~5mm。
[0019]
与现有技术相比,本发明的至少包括以下有益效果:
[0020]
1、本发明的降噪装置,通过旋转轴将设计为与阻尼耗能结构可转动连接,从而使得旋转轴能够随脱落涡的转动而转动,并且在旋转轴外表面上设有若干第一凸起组,以实现更好地捕捉脱落涡以及耗散脱落涡的能量,有效消除了因脱落涡的能量而产生的噪音,进而实现显著降低离心风机的噪音;
[0021]
2、本发明的离心风机,通过在叶轮的出风孔处设置降噪装置,可实现消除脱落涡能量,显著降低风机的噪音,提升用户体验和公司产品竞争力。
附图说明
[0022]
图1是本发明实施例1中降噪装置的结构分解示意图;
[0023]
图2是本发明实施例1中降噪装置的结构示意图;
[0024]
图3是本发明实施例1中离心风机的结构示意图;
[0025]
图4是本发明实施例1中离心风机的剖视图。
[0026]
图5是本发明实施例2中降噪装置的局部结构示意图;
[0027]
图6是本发明实施例3中降噪装置的结构示意图
[0028]
图7是本发明实施例3中降噪装置另一种结构的结构示意图;
[0029]
图8是本发明实施例4中降噪装置的结构示意图;
具体实施方式
[0030]
以下实施例对本发明进行说明,但本发明并不受这些实施例所限制。对本发明的具体实施方式进行修改或者对部分技术特征进行等同替换,而不脱离本发明方案的精神,其均应涵盖在本发明请求保护的技术方案范围当中。
[0031]
实施例1
[0032]
当离心风机的叶轮旋转时,会在叶轮的迎风面和背风面形成很强的压力梯度,从而造成严重的边界层流体分离现象。因此,在叶轮背压区存在很多的流动分离,这些流动分离以脱落涡的形式分布于叶轮出风孔处,并且这些脱落涡的能量是离心风机噪音的重要贡献来源。
[0033]
参见图1-2,本实施例提供了一种可消耗脱落涡能量的降噪装置,该降噪装置1包括旋转轴11和阻尼耗能结构12,其中旋转轴11能够随脱落涡的转动而转动,在旋转轴11外表面上设有若干沿长度方向间隔布置的第一凸起组111,该第一凸起组111用于更好地捕捉脱落涡。在旋转轴11的两端分别连接有用于消耗掉脱落涡能量的阻尼耗能结构12,旋转轴11与阻尼耗能结构12可转动连接,以保证旋转轴11能够在脱落涡的带动下进行自转。
[0034]
可见,本实施例的降噪装置,通过旋转轴11将设计为与阻尼耗能结构12可转动连接,从而使得旋转轴11能够随脱落涡的转动而转动,并且在旋转轴11外表面上设有若干第一凸起组111,以实现更好地捕捉脱落涡以及耗散脱落涡的能量,有效消除了因脱落涡的能量而产生的噪音,进而实现显著降低离心风机的噪音,提升用户体验和公司产品竞争力。
[0035]
优选地,旋转轴11为中空圆柱体,且旋转轴11由塑料制成,如此,可使得旋转轴11的质量更轻,更加便于转轴11随脱落涡的转动而转动,进而提高捕捉脱落涡以及耗散脱落涡能量的效果。
[0036]
优选地,第一凸起组111包括沿旋转轴11周向方向间隔布置的若干第一子凸起,如此沿旋转轴11周向方向间隔布置的若干第一子凸起(图中未示出),一方面,实现了增大旋转轴11的局部表面积,从而能够更好地捕捉脱落涡;另一方面,增加了第一子凸起的增加旋转轴11与脱落涡之间的摩擦力,使得脱落涡之能量进一步降低,进而实现显著降低风机的噪音。在本实施例中,第一子凸起可以为圆点、尖刺、锯齿或其他不规则形状,如此,流经第一子凸起的脱落涡,其频谱变得更加离散,从而实现自动调节噪音频谱。
[0037]
更优选地,在旋转轴11的外表面还设有若干沿长度方向布置的第二凸起组112,第二凸起组112位于阻尼耗能结构12内部,用于消除进入到阻尼耗能结构12内部的脱落涡能量。在本实施例中,第二凸起组112包括沿旋转轴11周向方向间隔布置的若干第二子凸起,该第二子凸起可以为圆点、尖刺、锯齿或其他不规则形状。
[0038]
参见图1-2,优选地,阻尼耗能结构12包括壳体121,壳体121面向旋转轴11的一面设有供旋转轴11穿过的开孔1211,旋转轴11的端部穿过开孔1211后伸入到壳体121内,如此,通过在旋转轴11的两端设置壳体121,便于通过壳体121,将旋转轴11可转动地安装于风机叶轮的出风孔处。
[0039]
更优选地,在壳体121内充填有粘性流体,该粘性流体作为9.摩擦阻尼耗能结构,用于消耗掉脱落涡的能量,以实现进一步减少脱落涡产生的噪音。
[0040]
在本实施例中,壳体121背离开孔1211的一端具有开口1212,该开口1212在降噪装置1安装于风机内时抵接风机蜗壳的内侧壁,以节省制造材料,并且方便粘性流体的充填。在其他实施例中,还可以将壳体121背离开孔1211的一端封闭,以防止粘性流体从开口1212处流出。
[0041]
参见图3-4,本实施例还提供了一种离心风机,该离心风机包括蜗壳2和叶轮3,蜗壳2具有进风口21和出风口22,叶轮3可转动设置于蜗壳2内,其中还包括如上所述的降噪装置1,在叶轮3的出风孔31处设有降噪装置1,降噪装置1的两端分别连接蜗壳2的正面201和背面202。由此,风机工作产生的脱落涡流经降噪装置1,其能量会被降噪装置1消耗掉,从而实现显著降低风机的噪音,提升用户使用体验。
[0042]
具体地,降噪装置1的旋转轴11可转动设置于出风孔31的出口处,旋转轴11的两端分别通过壳体121连接蜗壳2的正面201和背面202。在本实施例中,壳体121具有开口1212的
一端可以粘接、焊接固定在蜗壳2的内侧壁上,或者壳体121可以采用螺钉固在在蜗壳2的内侧壁上。
[0043]
优选地,蜗壳2的正面201具有环绕进风口21布置的第一弧形区域23和第二弧形区域24,对应的,蜗壳2的背面202具有相应的第一弧形区域23和第二弧形区域24,其中,第一弧形区域23靠近出风口22布置,第二弧形区域24远离出风口22布置。由于第一弧形区域23靠近出风口22布置,处于第一弧形区域23的脱落涡尺寸较大,而处于第二弧形区域24的脱落涡尺寸相对较小。
[0044]
为更好地捕捉不同区域、不同尺寸的脱落涡,本实施例将位于第一弧形区域23的旋转轴11的直径设计为4mm~8mm,而位于第二弧形区域24的旋转轴11的直径设计为1.5mm~5mm,如此,实现了根据不同区域设计不同尺寸的旋转轴11,进而保证降噪装置1能够捕捉不同尺寸的脱落涡,提高产品的适应性。
[0045]
实施例2
[0046]
参考图5,本实施例与实施例1的不同点在于,阻尼耗能结构12的结构不同。具体地,本实施例的阻尼耗能结构12还包括若干弹性片122,弹性片122作为摩擦阻尼耗能结构,其设置于壳体121内且其连接端连接壳体121的内侧壁,自由端延伸至旋转轴11的侧壁外侧。
[0047]
优选地,本实施例的弹性片122的数量为两个,两个弹性片122的自由端分别位于旋转轴11的相对两侧壁外侧,其它部位均与实施例1相同。
[0048]
可见,本实施例通过采用若干弹性片122替代粘性流体,在实现消耗掉脱落涡的能量,减少脱落涡产生的噪音的同时,无需考虑粘性流体的泄漏以及壳体1的密封性问题,从而使降噪装置1的工艺要求更低。
[0049]
实施例3
[0050]
参考图6,本实施例与实施例1的不同点在于,降噪装置1的结构不同。具体地,本实施例的降噪装置1仅包括中空的旋转轴11,在旋转轴11的长度方向上设有若干第一凸起组111和第二凸起组112。本实施例三个第一凸起组111构成第一凸起大组,十个第二凸起组112构成第二凸起大组,并且第一凸起大组和第二凸起大组沿旋转轴11长度方向交错布置。降噪装置1安装于蜗壳2时,旋转轴11的两端分别与蜗壳2的正面和背面可转动连接。
[0051]
在其他实施例中,参见图7,可以将全部第一凸起组111设置于两个第二凸起组112之间,其它部位均与实施例相同。
[0052]
可见,本实施例在实现消耗脱落涡能量,显著降低风机工作噪音的同时,省去了阻尼耗能结构12,使得本实施例降噪装置1的整体结构更加简单,优化加工工序,制造成本更低。
[0053]
实施例4
[0054]
参考图8,本实施例与实施例1或2的不同点在于,旋转轴11的结构不同。具体地,在旋转轴11的两端分别设有阻尼耗能结构12,且旋转轴11通过阻尼耗能结构12可转动地连接蜗壳2的正面和背面,并位于叶轮出风孔处。在旋转轴11的表面上只设有位于其两端的第二凸起组112,该第二凸起组112位于阻尼耗能结构12内部,其它部位均与实施例1或2相同。
[0055]
可见,本实施例通过省去旋转轴11表面的第一凸起组111,使得旋转轴11的整体结构更简单,更加便于旋转轴11快速加工成型,使制造成本更低。
[0056]
以上所述的仅是本发明的一些实施方式。对于本领域的普通技术人员来说,在不脱离本发明创造构思的前提下,还可以做出若干变形和改进,这些都属于本发明的保护范围。