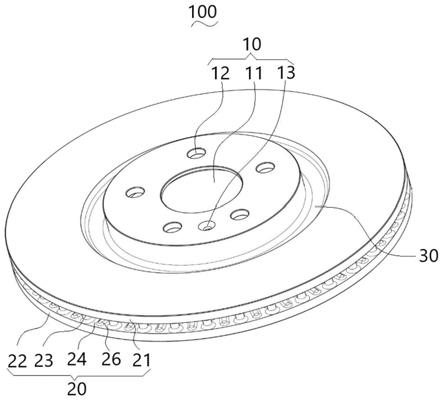
[0001]
本发明涉及汽车制动系统技术领域,尤其是涉及一种内通风式制动盘。
背景技术:[0002]
制动盘是一种车辆的旋转原件,制动是利用制动片等固定元件和旋转元件的表面摩擦从而产生制动力,阻碍车辆运动或者减缓车辆的运动趋势。通过制动盘内部产生的摩擦力,使得车辆减速、停止或者保持静止的状态。正是基于这个原理,车辆运行时,通过制动使得车辆的动能转化为热能,实现制动的效果。在制动过程中,摩擦所产生的热量使得制动盘温度升高,制动盘容易产生形变、存在制动抖动的隐患。因此,制动盘的散热效率不高,在频繁制动的情况下会过早产生裂纹,从而影响车辆使用的安全性和舒适性。
[0003]
为了能够改善制动盘在使用过程中的温度升高的情况,提高制动盘的散热效率,保证制动器的稳定制动性能。现有很多的制动盘都在内部设置相互独立的通风道以改善制动盘的通风效果。但是在制动盘内部所设置的相邻的通风道都是相互独立的,冷却空气只能沿着单一通道流通,相邻通道之间无法互通,难以形成较大流量以及有利于对流换热的气流。并且相互独立的通风道使得冷却空气在通风道内停留的时间较短,导致热交换效率偏低,使得散热效果不理想。同时,现有的制动盘内所设置通风道结构中为了保证连接强度,而未考虑制动盘轻量化的需求,导致连接强度过剩从而使制动盘的质量增大的问题。
技术实现要素:[0004]
本发明的目的在于解决现有制动盘内的通风道相互独立设置,使得热交换效率低,散热效果不理想以及未考虑制动盘轻量化的需求而使得连接强度过剩的缺点,提供一种内通风式制动盘。
[0005]
本发明解决其技术问题采用的技术方案是:一种内通风式制动盘,包括安装盘、环状摩擦盘以及用于连接所述安装盘和所述环状摩擦盘的支撑架,所述环状摩擦盘包括同轴设置的第一摩擦盘和第二摩擦盘,所述第一摩擦盘与所述第二摩擦盘之间设置有若干个沿圆周径向设置的连接部,相邻的所述连接部之间形成由所述环状摩擦盘的中心连通至所述环状摩擦盘外侧的主风道,所述连接部包括至少两个在圆周径向上间隔设置的加强筋,相邻的所述加强筋之间形成与所述主风道连通的侧风道。
[0006]
进一步地,所述连接部在圆周方向上的宽度由所述圆周的中心处向外逐渐增大。
[0007]
进一步地,所述环状摩擦盘的第一摩擦盘通过所述支撑架与所述安装盘固定连接,所述第一摩擦盘的厚度大于所述第二摩擦盘的厚度。
[0008]
进一步地,所述环状摩擦盘在所述主风道上还设置散热部,所述散热部包括设置于所述第一摩擦盘上的至少一个沿着圆周径向设置的第一散热凸起。
[0009]
具体地,所述散热部还包括设置于所述第二摩擦盘上的至少一个沿着圆周径向设置的第二散热凸起。
[0010]
具体地,所述第一摩擦盘和所述第二摩擦盘均具有相对设置的通风面以及相背设
置的摩擦面,所述第一散热凸起和所述第二散热凸起均设置于所述通风面上。
[0011]
具体地,所述第一散热凸起和所述第二散热凸起均具有由所述通风面凸起的圆弧状散热面。
[0012]
具体地,所述散热面距离所述通风面的高度小于等于两个所述通风面间距的1/4。
[0013]
具体地,相邻的所述第一散热凸起在圆周径向上间隔设置,相邻的所述第二散热凸起在圆周径向上间隔设置。
[0014]
进一步地,所述支撑架包括垂直于所述安装盘外圆周设置的第一支撑部和由所述第一支撑部的端部延伸至所述环状摩擦盘内圆周的第二支撑部,所述第一支撑部与所述第二支撑部之间形成的夹角呈锐角。
[0015]
本发明所提供的一种内通风式制动盘的有益效果在于:在环状摩擦盘内部设置有相互间隔的连接部,通过间隔的连接部形成了由环状摩擦盘中心连通至外侧的主风道,连接部由多个加强筋间隔设置形成侧风道,该侧风道的设置不仅可以起到相邻主风道之间的连通,还可以在满足第一摩擦盘与第二摩擦盘连接和支撑强度的同时降低环状摩擦盘整体的重量,符合制动盘整体轻量化设计的需求,并且通过在连接部上所设置的侧风道与主风道连通,形成较大流量以及利于对流换热的冷却空气,增加冷却空气在环状摩擦盘内停留的时间,可以大幅提高环状摩擦盘内部的散热性能和散热效率,能够将环状摩擦盘外部摩擦产生的热量即使通过主风道和侧风道之间热对流而散发出去,从而能够有效改善车辆制动时制动盘的温升。
附图说明
[0016]
图1是本发明提供的一种内通风式制动盘的立体结构示意图;
[0017]
图2是本发明提供的一种内通风式制动盘的沿轴向的全剖视图;
[0018]
图3是本发明提供的一种内通风式制动盘的侧视图;
[0019]
图4是本发明提供的一种内通风式制动盘的立体结构示意图,为了能够展示第一摩擦盘的内部结构,去除了第二摩擦盘的一部分;
[0020]
图5是本发明提供的一种内通风式制动盘的立体结构示意图,为了能够展示第二摩擦盘的内部结构,去除了第一摩擦盘的一部分。
[0021]
图中:100-内通风式制动盘、10-安装盘、11-安装孔、12-固定孔、13-定位孔、20-环状摩擦盘、21-第一摩擦盘、211-第一摩擦盘的通风面、212-第一摩擦盘的摩擦面、22-第二摩擦盘、221-第二摩擦盘的通风面、222-第二摩擦盘的摩擦面、23-连接部、231-加强筋、2311-条状筋、2312-柱状筋、24-主风道、25-侧风道、26-散热部、261-第一散热凸起、2611-第一散热凸起的散热面、262
-ꢀ
第二散热凸起、2621-第二散热凸起的散热面、30-支撑架、31-第一支撑部、32
-ꢀ
第二支撑部、h-环状摩擦盘的厚度、h1-第一摩擦盘的厚度、h2-第二摩擦盘的厚度、h3-散热面距离通风面的高度、h4-两个通风面之间的间距、l1-连接部靠近圆周的中心处的宽度、l2-连接部远离圆周的中心处的宽度。
具体实施方式
[0022]
为了使本发明的目的、技术方案及优点更加清楚明白,以下结合附图及实施例,对本发明进行进一步详细说明。应当理解,此处所描述的具体实施例仅仅用以解释本发明,并
之间形成了可供气体流通的侧风道25。当然,本发明所提供的内通风式制动盘 100中,该连接部23还可以设置为多条沿着轴向间隔设置的条状加强筋,相邻的条状加强筋之间的间隔形成了可供气流通过的侧风道。该每个连接部23上均具有侧风道25,使得相邻的主风道24之间通过侧风道25实现了空气流通。本发明所提供的一种内通风式制动盘100中,相邻的主风道24之间通过连接部 23上所设置的侧风道25而实现了相互连通。通过侧风道25的设置,增加了第一摩擦盘21和第二摩擦盘22之间空气可流通的空间,从而提高了环状摩擦盘 20内的空气流通量,这样有利于对流换热,并且可以增加冷却空气在第一摩擦盘21和第二摩擦盘22内部停留的时间,从而大幅度的提高环状摩擦盘20的散热效果和热交换效率。
[0026]
本发明所提供的一种内通风式制动盘100中,在制作之前先通过模态分析制动盘的固有频率和振型,分析之后可通过调节条状加强筋2311和柱状加强筋 2312的尺寸或数量,从而改变制动盘100的固有频率并满足设计要求,降低制动噪音发生的频率。通过这种方式加工的内通风式制动盘100与现有技术中通过改变材料成分含量来改变制动盘固有频率的方式更为简单有效、成本低。同时,本发明所提供的一种内通风式制动盘100中,该连接部23设置了间隔的加强筋231结构,即能够提高散热效率,还可以在保证第一摩擦盘21和第二摩擦盘22的连接强度以及支撑强度的同时,减少加强筋231处的质量。在保证环状摩擦盘20的连接稳定性的前提下,可以设置多个间隔,即在连接部23上设置多个侧风道25,就可以减轻整个环状摩擦盘20的重量,更加利于制动盘100 的轻量化设计的需求。
[0027]
进一步地,如图4所示,本发明所提供的一种内通风式制动盘100中,该连接部23在圆周方向上的宽度由圆周的中心处向外逐渐增大。在本实施例中,该条状加强筋2311为不等宽设计,使得位于环状摩擦盘20中的主风道24呈喇叭性结构,其中靠近圆心一侧的主风道24的截面面积较大,远离圆心一侧的主风道24的截面面积较小。对应的,在本实施例中,条状加强筋2311的远离圆周中心处一侧的宽度l2大于靠近圆周中心处一侧的宽度l1。这样设计的目的是可以增加空气的接触面积,以及利于导风,使得冷空气可以由环状摩擦盘20 的中心向外流通。并且,该在本实施例中,连接部23远离圆周中心处的宽度 l2比靠近圆周中心处的宽度l1大1-2mm。该连接部23的不等宽设计,可以增加主风道24和侧风道25处的散热面积,通过提高冷空气与环状摩擦盘20内部的接触面积而达到提高散热效率的作用。
[0028]
进一步地,如图2所示,本发明所提供的一种内通风式制动盘100中,该环状摩擦盘20第一摩擦盘21的厚度h1大于第二摩擦盘22的厚度h2。该环状摩擦盘20在保证其整体厚度h不变的前提下,第一摩擦盘21的厚度h1大于第二摩擦盘22的厚度h2,这样使得第一摩擦盘21的通风面211和第二摩擦盘22 的通风面212之间的间距h4缩小。具体地,第一摩擦盘21的厚度h1与第二摩擦盘22之间的厚度h2之间的厚度差小于等于1mm。即该第一摩擦盘21的厚度 h1比第二摩擦盘22的厚度h2略大,这样设计不仅可以有效地增大整个制动盘 100的强度和刚度,还可以有效地抑制热胀冷缩而导致的热变形的问题。
[0029]
进一步地,本发明所提供的一种内通风式制动盘100中,该环状摩擦盘20 在主风道24上还设置有散热部26,散热部26包括设置于第一摩擦盘21上的至少一个沿着圆周径向设置的第一散热凸起261。该散热部26设置于主风道24 上,可以有效地增加主风道24处环状摩擦盘20与冷空气的接触面积,从而提高散热效率。并且,该第一散热凸起261的设置数量可以根据实际散热的需求而增加或者减少。如图4所示,相邻的第一散热凸起261在圆周径向上间隔设置。在本实施例中,该第一摩擦盘21的主风道24上设置有第一散热凸起261,
且沿着圆周径向设置有两个间隔设置的第一散热凸起261。该第一散热凸起261 设置的数量与散热需求有关,若制动所产生的散热需求大,可以适应的沿圆周径向上增加间隔设置的第一散热凸起261的数量,主要是通过增加的第一散热凸起261增加接触面积达到热交换的目的。
[0030]
具体地,如图5所示,该散热部26还包括设置于第二摩擦盘22上的至少一个沿着圆周径向设置的第二散热凸起262。并且相邻的第二散热凸起262在圆周径向上间隔设置。该第二散热凸起262与第一散热凸起261相对设置,且数量和结构完全相同。该第二散热凸起262的设置目的与第一散热凸起261的目的一致,并且两者分别设置于第一摩擦盘21和第二摩擦盘22的相对设置的通风面(211、221)上。
[0031]
具体地,为了能够尽量增加接触面积,该第一散热凸起261和第二散热凸起262均具有由通风面(211、221)凸起的圆弧状散热面(2611、2621)。第一散热凸起261和第二散热凸起262的散热面(2611、2621)均是由通风面(211、221) 凸起而形成的弧状结构,能够在增加凸起数量相同的前提下,尽可能多的增大散热部26的面积,从而提高热交换的效率。
[0032]
具体地,如图2所示,本实施例中,该散热面2621距离通风面221的高度 h3小于等于两个通风面(211、221)间距h4的1/4。该散热面2621的高度h3 若太高将会影响整个主风道24的冷空气流通效果,反而不利于该环状摩擦盘 20内部的热交换效果。而该散热面2621的高度h3若太小,也无法起到增加接触面积的技术效果,就无法实现提高热交换效率的目的。因此,当该散热面2621 距离通风面221的高度h3为两个通风面(211、221)高度h4的1/4的时候,该第一散热凸起261和第二散热凸起262能够兼顾重量和散热效率而达到的增大散热效果最佳。
[0033]
在本实施例中,该散热部26中的第一散热凸起261和第二散热凸起262 分别设置于第一摩擦盘21和第二摩擦盘22上,但是两者无论是从设置数量还是设置方向,以及设置结构上均是相同的。且第一散热凸起261和第二散热凸起262在圆周径向上的间隔也是等宽等距的。该散热部26能够在整个环状摩擦盘20中沿着通风面(211、221)均匀分布,保证整个内通风式制动盘100的动平衡性。并且该第一散热凸起261和第二散热凸起262上的圆弧状结构设计,能够最大限度的增加第一摩擦盘21和第二摩擦盘22在主风道24内与冷空气接触的表面积,有效地提升热交换率,增加散热速度。
[0034]
进一步地,如图2所示,本发明所提供的一种内通风式制动盘100中,该支撑架30用于连接安装盘10和环状摩擦盘20。具体地,该支撑架30用于连接安装盘10与环状摩擦盘20中的第一摩擦盘21。该支撑架30包括垂直于安装盘10外圆周设置的第一支撑部31和由第一支撑部31的端部延伸至环状摩擦盘20内圆周的第二支撑部32,第一支撑部31与第二支撑部32之间形成的夹角α呈锐角。在本实施例中,该第二支撑部32由第一支撑部31的端部延伸至第一摩擦盘21的内圆周处。作为优选的方案,该第一支撑部31与第二支撑部 32之间的夹角α为30
°-
70
°
之间。这样该夹角α能够在制动过程中,用以抵消因为热胀冷缩而导致的第一摩擦盘21所产生的热变形,从而可以有效地抑制因为制动升温而导致的制动盘100变形的问题。
[0035]
本发明所提供的一种内通风式制动盘100,在环状摩擦盘20内部设置有相互间隔的连接部23,通过间隔的连接部23形成了由环状摩擦盘20中心连通至外侧的主风道24,连接部23由多个加强筋231间隔设置形成侧风道25,该侧风道25的设置不仅可以起到相邻主
风道24之间的连通,还可以在满足第一摩擦盘21与第二摩擦盘22连接和支撑强度的同时降低环状摩擦盘20整体的重量,符合制动盘100整体轻量化设计的需求,并且通过在连接部23上所设置的侧风道25与主风道24连通,形成较大流量以及利于对流换热的冷却空气,增加冷却空气在环状摩擦盘20内停留的时间,可以大幅提高环状摩擦盘20内部的散热性能和散热效率,能够将环状摩擦盘20外部摩擦产生的热量即使通过主风道24和侧风道25之间热对流而散发出去,从而能够有效改善车辆制动时制动盘的温升。
[0036]
以上仅为本发明的较佳实施例而已,并不用以限制本发明,凡在本发明的精神和原则之内所作的任何修改、等同替换和改进等,均应包含在本发明的保护范围之内。