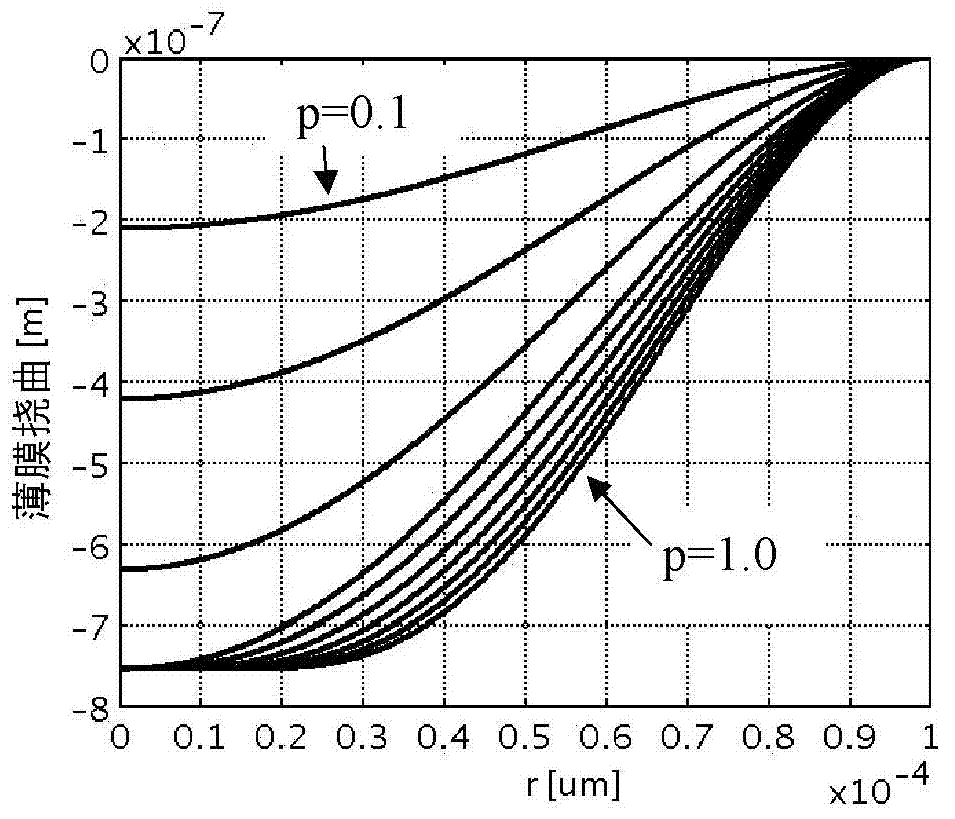
本发明涉及MEMS电容式压力传感器。
背景技术:MEMS压力传感器典型地具有压阻式或者电容式读出,并且是本领域公知的。在图1中示出了电容式MEMS压力传感器一个示例的SEM横截面。该图示出了在牺牲层刻蚀以及用2μm厚PECVDSiN膜封闭所述刻蚀孔作为最后一级薄膜制造步骤之一之后的器件。所述传感器具有悬置SiN薄膜。通过采用PEVCDSiN工艺气密性地封闭在所述SiN薄膜下方的腔体。所述最终器件性能很大程度上由这个薄膜的几何、物理、机械和结构特性决定。该薄膜的密度和组成确定所述气密性、放气行为和内部应力。所述应力与所述SiN厚度一起确定所述薄膜的刚度以及因此所述压力传感器的灵敏度。在医疗应用中的关键系统、替代能源、智能楼宇、引擎控制(例如燃气和燃料进口压力)和诸如轮胎监测系统的汽车安全应用需要压力传感器在其生命周期上提供准确且可预测的输出,以便在这些变化变成临界之前跟踪操作变化。在20世纪70年代末,硅作为感测材料的出现开始影响工业和商业应用中的压力测量。硅基传感器使用后来被称为MEMS(微机电系统)的技术。MEMS传感器迅速地被应用在良好环境下的汽车和医疗应用中。由于体积小,在大量生产下它们相对低廉。尽管其他压力感测技术,诸如薄膜、厚膜和陶瓷电容的发展,MEMS仍然是最广泛使用的技术,并且注定成为新兴市场,诸如替代能源、汽车和/或医疗应用中驱动力。随着不断的小型化,MEMS压力传感器在某种意义上也开始受到其小尺寸和制造方式的影响。例如,出现与不灵敏、不准确和信号漂移相关的问题。尽管正在采用现有技术的沉积工具和光刻技术,但是不能保证所有MEMS器件都被均匀地沉积或者具有相同的几何尺寸。由于没有两个MEMS器件是完全相同的,需要有一些手段来校准它们,以便抵消那些不一致。因为在工业制造环境下测量单个器件参数是非常不切实际的,例如与外部施加力相关的挠曲(deflection)形状,希望开发用于内部校准的方法,以便保证两个MEMS器件以完全相同的方式作用或者测量。此外,需要自校准,因为微型器件可能会外露在恶劣的环境中或者长时间处于休眠状态。在一些情况下,所述器件应当唤醒并且重新校准自己,以便将因温度差异、所述气体或者液体环境中的变化或者可能影响所述传感器特性的其他条件造成的变化考虑在内。目前,大多数微机械压力传感器使用气密性薄膜,所述薄膜密封参考腔体(referencecavity),所述参考腔体处在某个表压(gaugepressure)(在一些情况下,表压是真空)。测量外部压力,因为外部压力与表压之间的压力差在薄膜上产生作用力,造成了薄膜挠曲。然后由压阻式、电容式或者光学传感器测量这种挠曲。存在一些与这种常规的压力传感器设计相关的困难:参考腔体中的气体压力需要非常稳定,以便避免信号漂移。这要求非常高等级的气密性,薄膜没有释气。为了具有大的挠曲幅度和最佳的灵敏度,薄膜的厚度应当较小(或者它应当具有大的面积)。由于难以使非常薄的薄膜是气密的,这些是矛盾的要求,并且导致较大的传感器尺寸。如果参考腔体处在某个压力,根据波义耳定律(Boyle’s)(P×V=n×R×T),这个压力将是温度依赖的。因此,传感器变成温度依赖的。压力传感器的灵敏度由薄膜变形的幅度确定,所述幅度进而由薄膜的厚度、直径和屈服强度限定。对于具有电容式读出的仪表,灵敏度还依赖于极板的分离。基于挠曲压力传感器的总动态范围也由薄膜的最大挠曲限制。薄膜厚度、直径和应力中的任何变化都会对所得到的薄膜挠曲轮廓具有显著的影响,不仅影响绝对电容读数,而且影响读出的准确度和精确度。由于在制造期间的工艺变化,没有两个微观结构具有相同的几何尺寸和材料特性,这将会导致尺寸、质量、刚度中的小变化,而这将会显著地影响性能。例如,如果薄膜包含压缩和伸张层,薄膜厚度中10%的变化会造成微观结构刚度和压力灵敏度中50%-100%的变化。工艺变化使得企业难以准确地预测MEMS的性能并且在没有逐个测量它们的情况下详细说明性能。要求校准和频繁的重新校准以便保证准确、可靠的输出。目前,没有方法在工业环境中执行自校准并且校正信号漂移。
技术实现要素:根据本发明,提供了一种压力传感器,包括:第一压力传感器元件,包括具有可变形上电极的电容式MEMS压力传感器,以及由第一腔体部分隔开的固定下电极,其中所述上电极响应于待感测的压力而变形;以及第二压力传感器元件,包封在第二腔体部分内,其中所述第二腔体部分具有刚性的顶盖,其中连接所述第一和第二腔体部分来限定组合的密封腔体,其中,所述传感器还包括用于对所述第一和第二压力传感器元件输出进行组合的装置,使得所述第二压力传感器元件输出提供所述第一压力传感器输出的校准。这种结构提供了连接至所述电容式传感器腔体的第二压力传感器。一个压力传感器是基于变形的检测,而另一个是基于内部压力。这个内部压力变化远小于所述外部压力,并且所述内部压力变化是体积变化的函数,所述体积变化由所述电容式传感器电极的移动导致。因此,所述第二压力传感器同样没有测量外部压力,但是它仍然可被用于提供所述主电容式传感器的自动校准。更具体地,所述第二压力传感器元件性能将依赖于所述腔体的释气级别,并且因此可用于补偿所述电容式压力传感器性能随时间的变化。它也可以补偿温度的变化。所述第一和第二腔体部分可以并排地位于SOI衬底结构上,所述SOI衬底结构包括晶片、在所述晶片上的绝缘体层和在所述绝缘体层上的半导体层,并且所述腔体部分可以由在所述绝缘体层中形成的沟道连接。这样,两个压力传感器都可以利用共享的工艺步骤成为集成电路的一部分。每一个腔体部分均可以例如通过在所述硅层中形成的相应的通孔连接至所述沟道。所述第一腔体部分可以在所述半导体层上,以及所述第二腔体部分可以形成在所述半导体层中。然后所述压力感测元件可以成为所述半导体层的一部分。在另外一种构造中,可以将所述第一和第二腔体部分组合在SOI衬底结构上相同的腔体中,所述SOI衬底结构包括晶片、在所述晶片上的绝缘体层和在所述绝缘体层上的半导体层。这样,可以减小所述形状因数(formfactor),同时两个压力传感器都可以利用共享的工艺步骤成为集成电路的一部分。在另外一种构造中,可以将所述第一和第二腔体部分形成在CMOS电路上,例如读出电路。这样,由于在所述集成电路顶部的所述压力传感器功能的集成,可以减小所述形状因数,同时两个压力传感器都可以利用共享的工艺步骤成为集成电路的一部分。然后所述第一和第二腔体部分可以并排地位于所述CMOS集成电路上。所述CMOS集成电路的上金属层可用于形成外部压力传感器接触与所述内部压力传感器电极之间的电连接。在第一示例中,所述第二压力传感器元件包括皮拉尼压力计(Piranigauge)。在第二示例中,所述第二压力传感器元件包括MEMS谐振器,其中使用所述谐振频率或者所述谐振频率的品质因数来确定压力。本发明还提供了一种操作压力传感器的方法,包括:利用第一压力传感器元件测量外部压力,所述第一压力传感器元件包括电容式MEMS压力传感器,所述电容式MEMS压力传感器具有可变形的上电极、以及由第一腔体部分隔开的固定下电极,其中所述上电极响应于待感测的压力而变形;利用第二压力传感器元件测量内部腔体压力,所述第二压力传感器包封在第二腔体部分内,其中连接第一和第二腔体部分来限定组合的密封腔体;对所述外部压力和内部压力测量进行组合,使得所述第二压力传感器元件输出提供所述第一压力传感器输出的校准。本发明还提供了一种制造压力传感器的方法。第一示例包括:提供SOI衬底结构,所述SOI衬底结构包括晶片、在所述晶片上的绝缘体层和在所述绝缘体层上的半导体层,形成第一压力传感器元件,所述第一压力传感器元件包括电容式MEMS压力传感器,所述电容式MEMS压力传感器具有可变形的上电极以及由第一腔体部分隔开的固定下电极,所述第一腔体部分在所述半导体层上;形成包封在第二腔体部分内的第二压力传感器元件,并且在所述第二腔体部分上形成刚性的顶盖和在所述半导体层中形成第二腔体部分;以及通过在所述绝缘体层中形成的沟道连接所述第一和第二腔体部分来限定组合的密封腔体。第二示例包括:提供CMOS电路,所述CMOS电路包括具有多级互连结构的晶片;形成第一压力传感器元件,所述第一压力传感器元件包括电容式MEMS压力传感器,所述MEMS压力传感器具有可变形的上电极,以及由第一腔体部分隔开的固定的下电极,所述第一腔体部分在所述金属互连结构上;形成包封在第二腔体部分内的第二压力传感器元件,以及在所述第二腔体部分上形成刚性的顶盖;以及通过沟道连接所述第一和第二腔体部分来限定组合的密封腔体,其中所述互连结构用于形成至所述压力传感器元件的电连接的一部分。附图说明现在将参考附图详细描述本发明的示例,其中:图1示出了电容式MEMS压力传感器的一个示例的SEM截面图;图2示出了电容压力传感器的薄膜挠曲轮廓;图3示出了作为所施加压力函数的所述电容;图4示出了作为所施加外部压力函数的所述腔体体积减小和压力增加;图5示出了作为所施加外部压力函数的电容和灵敏度的FEM仿真;图6示出了对于皮拉尼传感器三种不同构造的归一化电阻变化;图7示出了作为谐振器压力函数的谐振频率;图8示出了在SOI中制造的具有压阻读出的狗骨头状谐振器的示意性顶视图;图9示出了在SOI中制造的具有压阻读出的狗骨头状谐振器的SEM横截面;图10示出了作为压力函数的谐振器谐振频率的品质因数;图11示出了狗骨头状谐振器平面外运动;图12A至12K示出了用于制造电容式压力传感器的示范性工艺流程的连续步骤,所述电容式压力传感器包括皮拉尼压力计或者谐振器;图13示出了作为退火温度函数的从PECVDSiNx:Hy膜的氢水渗出;图14示出了在封装之后具有PVDAl插头SiN覆盖腔体中压力的累积分布;图15A至15G示出了用于制造电容式压力传感器的示范性工艺流程的连续步骤,所述电容式传感器包括在CMOS电路顶部上的皮拉尼压力计;以及图16示出了具有所施加压力并且对于皮拉尼压力计版本的图12K的设计。具体实施方式本发明提供了一种能够执行自校准并且校正信号漂移的压力传感器。通过利用电容式读出方法测量薄膜的挠曲,来感测外部介质与腔体之间的压力差。存在两种方式实施本发明。一种方式涉及集成皮拉尼传感器的使用,以及另一种方式涉及集成谐振器的使用,用作参考压力传感器。从1906年发明至今,皮拉尼压力计已经被广泛地用于真空测量。具有高电阻温度系数的加热导线被放置在真空环境下。导线(其电阻与其温度成正比,)形成平衡惠斯通电桥的一个臂。气体分子与导线碰撞,从导线传递热量并且使电桥相对于参考状态不平衡。由于分子碰撞频率与气体压力成正比,因此维持电桥平衡所需的电压与压力成正比。由于其可靠性、低成本和相对广泛的压力范围,皮拉尼压力计已经成为一个行业标准。能够监测真空等级的微皮拉尼传感器已经是深入的研究工作的主题。与基于皮拉尼压力计的传统细丝相比,它们具有尺寸小、成本低、响应快和压力感测范围大的优势。基于SOI的工艺过程允许长且薄的结构,对测量低气压是必要的。传感器例如可以设置作为导线,在导线与侧面热沉之间具有间隙。在根据本发明的第一示例中,将具有气密性密封腔体的电容式压力传感器与连接至相同腔体或者在相同腔体内的微皮拉尼压力计组合。然后利用自由悬挂结构(即具有或者没有散热片的导线或者Si梁)的电阻来测量内部压力。从这个结构至周围气体的热传导依赖于结构周围的气体压力。如果由于释气或者由于气密性密封腔体内部气体的压缩导致内部压力有变化,那么可以通过电阻变化来感测。利用腔体内部皮拉尼压力计的目的是针对内部压力变化(例如由于释气、温度或者由于压缩)而校正薄膜电容测量。可以利用惠斯通电桥构造作为读出来校正由于外部温度变化所导致的皮拉尼压力计内电阻变化。如果独立地测量芯片上温度,不仅可以补偿导线的电阻变化,还可以补偿腔体内的体积膨胀/压力增加。在根据本发明的第二示例中,将具有气密性密封腔体的电容式压力传感器与在相同腔体内的谐振器组合。然后利用谐振结构的频率偏移/品质因数测量内部压力。如果由于释气或者由于气密性密封腔体内部气体的压缩内部压力有变化,那么可以通过谐振频率的峰加宽来感测。利用内部谐振器的目的再次是针对内部压力变化(例如由于释气、温度或者由于压缩)来校正薄膜电容测量。如果将参考谐振器构建在独立的腔体中,那么可以差分地测量主谐振器的谐振频率,使得谐振频率的环境温度依赖性不会限制准确度。在这两种情况下,由于例如不均匀的薄膜厚度、应力和释气所造成的工艺过程条件变化将导致挠曲轮廓中的较大展宽,并且因此可以利用芯片上加工分别地确定和校准。目前,大多数微机械压力传感器利用气密性密封参考腔体的薄膜,腔体处在某个表压下。测量外部压力,因为在外部压力与内部表压之间的压力差在薄膜上产生一个作用力,造成了薄膜挠曲。理想地,内部参考压力是真空,这样可以抵消内部腔体压力的影响。然后利用反电极以电容的方式测量薄膜挠曲。在图2中,根据有限元模型(FEM)仿真,将用于电容式压力传感器的薄膜挠曲轮廓表示为压力的函数。压力从上到下以0.1巴的步长从0.1巴增加至1巴(以10kPa的步长从10kPa增加至100kPa)。对于750nm的间隙,薄膜“倒塌”发生在0.35巴(35kPa)。腔体内的压力为零并且假定没有残余应力。在某个压力下,上薄膜将开始接触腔体的底部。对于所建模的半径为100μm、厚度为1.5μm的SiN薄膜,在0.35巴(35kPa)下已经发生这种情况。在图3中,描述了电容作为所施加压力的函数,表示出当挠曲薄膜接近下电极时非线性的C~1/P行为以及在下降阶段薄膜“向下接触”之后差不多线性的C~P行为。从该图可以明显看出,就在“向下接触”之前压力灵敏度最大(较大C-P斜率)。图3再次涉及厚度为1.5μm、间隙为750nm、半径为100μm的SiN薄膜(杨氏模量为250GPa、泊松比为0.23)。在电极之间是εr=6的200nm的SiN电介质层。可以设计膜片尺寸,以便设定压力范围。下面给出了对于圆形薄膜的挠曲作为压力、薄膜厚度、薄膜半径和间隙高度的函数的关系式。在抗挠刚度支配机制中作为压力P的函数的圆形薄膜的挠曲w(r)由下式给出:其中,R是薄膜的半径,r是从边缘至实际挠曲点的距离,v是泊松比,E是杨氏模量,h是薄膜厚度。从上述关系式中可以看出,挠曲与R4和1/h3成正比。薄膜厚度和/或尺寸中的较小变化已经对挠曲轮廓产生巨大影响。这个关系对没有任何内部应力的薄膜是有效的。如果考虑内部应力,薄膜变得更硬并且达到接触点的压力变得更大。如果在腔体内部存在某个残余压力,根据波义耳定律内部压力将与体积变化成反比变化。例如考虑直径为75μm、高度为500nm的腔体,腔体由2.2μm厚的SiN薄膜覆盖。其体积为~9000μm3,在1巴(100kPa)的外部压力下(假定腔体真空),体积减小至~7600μm3。这由图4中的圆圈表示,示出了对于腔体真空腔体体积减小作为所施加外部压力的函数。输入参数为厚度为2.2μm、半径为75μm的SiN薄膜(杨氏模量为220GPa、泊松比为0.3),间隙高度为500nm。如果在腔体中的残余气体压力是100毫巴(10kPa)而不是真空(用外部真空测量),那么如果施加1巴(100kPa)的外部压力,该气压将上升至120毫巴(12kPa)。这也在图4中利用三角形点示出,表示了对于100毫巴的初始压力(10kPa,并且是对于所施加外部压力为0.0巴的压力)的内部压力变化。如果在腔体中的压力随时间变化不是恒定的,例如由于释气,那么薄膜将经受对抗外部施加压力的额外的但是未知的作用力。如果在校准期间不考虑腔体内部的压力增加(在上述示例中为100毫巴(10kPa))的影响,那么误差随压力而增大。例如,由于薄膜挠曲,内部压力在1巴下增加至120毫巴(12kPa)以及在2巴(200kPa)下增加至145毫巴(14.5kPa)。如果没有在受控环境中规律地校准传感器,那么这会导致随时间变化的不可接受的信号漂移。在实际日常生活的情况下,难以执行传感器校准,因为通常不能将传感器从其环境中取出(例如医学植入、汽车压力传感器等)。此外,如果腔体内部的气体由于温度增加而膨胀,那么如果内部压力是未知的,将不能校正影响。校准为潜在的信号漂移提供了解决方法。出于这个原因,在校准程序中确定薄膜的初始状态和挠曲行为并且时常检查是否发生任何变化是重要的。在标准校准期间,会向薄膜施加几个参考压力,并且会测量电容。校正和校准参数会从测量结果中提取并且被存储在芯片上的存储器中或者会修整(trim)电路元件。这些校准数据例如可以由在适当的压力感测范围内获取的电容-电压(C-P)数据点组成。典型地,需要三个或者更多的C-P点,以便通过数据点推导高阶多项式拟合。因为C-P关系是非线性的(参见下面的公式),那么校准点越多,多项式拟合就会越准确。其他的校准可能性例如是电容电压(C-V)扫描。这种扫描包括在不同偏置电压下准确的电容测量。通常,在+20与-20V之间以1V的间隔绘制C-V曲线。由于静电引力,薄膜朝向另一个电极挠曲,随着电压偏置增大(负或正)而增大电容。可以利用通过C-V数据拟合来推导薄膜柔量,薄膜柔量是薄膜压力灵敏度的一个量度。C-V校准方法是一种相对快速的校准方法,可以在不使用专...