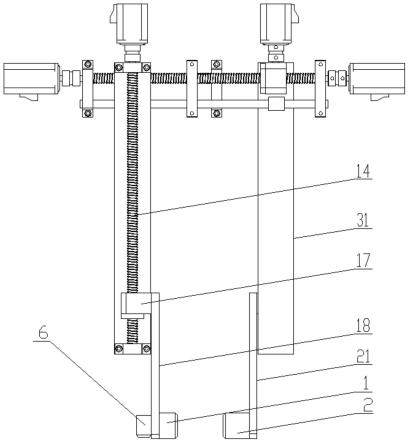
1.本发明属于铸造(探伤)缺陷检测技术领域,尤其涉及一种铸件缺陷自动检测设备及检测方法。
背景技术:2.随着高端装备的快速发展,对其铝合金关重铸件的内部质量要求越来越严格。由于铸造技术的缺陷和不可控因素,在铝合金铸件内部难免出现针孔、夹杂等各种内部缺陷,而且铝合金铸件需求量逐年呈爆发式增长,这对铸件内部质量检测技术提出了更高要求,要求实现连续、自动、快速、准确、高效检测。
3.x射线检测技术以其高灵敏度和高信息量,成本低、直观可靠及适于保存周期长等优点,非常适合铝合金铸件的内部质量检测,但目前铝合金铸件x射线检测设备在功能性能、关键参数控制、自动化程度等不高,存在检测效率低,成本高,周期长等问题。因此,开发一种铸件缺陷自动检测设备及检测方法十分必要。
4.随着工业智能化的发展,有关x射线自动检测设备也逐渐被开发出来。例如:桂林市南方检测有限责任公司开发的钢质大型立式储罐x射线自动化检测设备,包括数字探测器装置、x射线机装置、行走装置和升降装置,行走装置包括行走架和行走机构;烟台华科检测设备有限公司开发的x射线数字平板成像检测技术,整套检测系统主要由平板探测器,计算机及软件组成,当x射线穿过被检测物体到达平板探测器时,平板探测器将x射线不可见光信息转换成数字信号,然后由计算机软件处理成数字图像显示。
5.然而,前述储罐x射线自动化检测设备是应用于施工现场的检测设备,通用性差。而现有的x射线自动化检测设备,无法适用于生产车间对大批量的铸件缺陷进行快速、准确地检测,检测成本依然高昂,特别是对于较大的筒形件(直径大于2m、壁厚大于20mm、高度大于80cm)或异形板状件(壁厚大于20mm,表面积大于0.6
㎡
),对于较大的筒形件采用现有的人工贴胶片进行探伤至少需耗时一晚上(x射线探伤通常是在晚上进行,按8小时计,包含贴取胶片的时间在内每完成一次透照需10-20分钟)。更关键地是,目前在对板状样品进行检测时,须将板状样品放置在特定的工装夹具上,很不方便。
技术实现要素:6.本发明目的在于提供一种铸件缺陷自动检测设备及检测方法,能够用于生产车间对大批量的铸件缺陷进行快速、准确地检测并降低检测成本。
7.为实现前述目的,本发明采用如下技术方案。
8.一种铸件缺陷自动检测设备,包括设置在屏蔽房内的x射线发生器和x射线接收器,x射线接收器将接收到的信号转化为图像信号并通过显示终端进行显示,其特征在于:在屏蔽房内设置有可旋转的工件承载台,工件承载台及其旋转机构连接驱动机构,通过驱动机构驱动工件承载台及其旋转机构沿着轨道移动,轨道自屏蔽房内向外延伸至自动装卸料系统附近;x射线发生器设置在位置调节机构上,位置调节机构安装在屏蔽房
内的顶部;旋转机构、驱动机构、自动上料系统、位置调节机构分别连接控制器,控制器的存储模块上存储有能够在处理模块上运行的程序,所述处理模块执行所述程序时实现以下功能/步骤:控制工件承载台及其旋转机构沿着轨道移动至预设位置;控制工件承载台按照预设角度旋转;控制自动装卸料系统将工件转移到工件承载台上,控制自动装卸料系统将工件从工件承载台上移走;控制x射线发生器移动到目标探测位置并按照预设速度转动。
9.进一步地,所述位置调节机构包括竖直安装在屏蔽房顶部的转轴,转轴上端连接电机、转轴下端连接水平布置的横梁;在横梁上设置有两套二维移动机构,二维移动机构a上安装x射线发生器a,二维移动机构b上安装x射线接收器a,通过控制二维移动机构能够将x射线发生器a和x射线接收器a调节至同一高度且相向布置的状态,x射线接收器a的窗口朝向为水平方向,通过控制电机转动能够带动x射线发生器a和x射线接收器a同步旋转。
10.进一步地,二维移动机构a包括第一水平丝杠和第一竖直丝杠,第一水平丝杠上配合有第一活动座,第一竖直丝杠连接在第一活动座上,第一竖直丝杠上配合有第二活动座,第二活动座上设置有竖直布置的第一连杆,x射线发生器a安装在第一连杆下部;二维移动机构b包括第二水平丝杠和第二竖直丝杠,第二水平丝杠上配合有第三活动座,第二竖直丝杠连接在第三活动座上,第二竖直丝杠上配合有第四活动座,第四活动座上设置有竖直布置的第二连杆,x射线接收器a安装在第二连杆下部;x射线发生器a中心、x射线接收器a中心、第一竖直丝杠轴线、第二竖直丝杠轴线与转轴轴线位于同一竖直平面。
11.为了使得本发明检测设备能够对板状异形工件进行快速、准确地检测,在第一连杆下部还设置有x射线发生器b,x射线发生器b的窗口朝向为竖直向下,在工件承载台上设置有x射线接收器b,x射线接收器b直径大于工件长度,x射线接收器b表面设置有用于搁放工件的亚克力板和/或泡沫垫。
12.进一步地,工件承载台呈圆形,工件承载台和转轴同轴布置。
13.本发明中,一种采用前述铸件缺陷自动检测设备的检测方法,其特征在于步骤包括:步骤11,控制屏蔽房的门打开,控制工件承载台及其旋转机构沿着轨道移动至自动上料系统附近;步骤12,控制自动上料系统运行,将待检测的筒形铸件转移至工件承载台上,使筒形铸件中心与工件承载台中心重合;步骤13,控制工件承载台及其旋转机构沿着轨道回到屏蔽房的检测区域;步骤14,调节二维移动机构a和二维移动机构b的竖直丝杠间距,使第一活动座和第三活动座位于电机同一侧,使x射线发生器a与x射线接收器a之间的间距大于筒形铸件壁厚且小于筒形铸件直径;步骤15,初步调节第一活动座和第三活动座的高度,使x射线发生器a位于筒形铸件外侧,使x射线接收器a位于筒形铸件内腔;步骤16,精确调节第一活动座和第三活动座的位置,使x射线发生器a和x射线接收
器a均位于检测起始点;步骤17,开启x射线发生器a和x射线接收器a,控制电机转动,直到x射线发生器a和x射线接收器a刚好转动一圈后暂定;步骤18,控制第一活动座和第三活动座同步上升一个标准高度,继续控制电机转动,直到x射线发生器a和x射线接收器a刚好转动一圈后暂定;步骤19,多次重复执行步骤18,直到完成检测。
14.本发明中,一种采用前述铸件缺陷自动检测设备的检测方法,其特征在于步骤包括:步骤21,控制屏蔽房的门打开,控制工件承载台及其旋转机构沿着轨道移动至自动上料系统附近;步骤22,控制自动上料系统运行,将待检测的板状铸件转移至工件承载台上,使板状铸件中心与工件承载台中心基本重合;步骤23,控制工件承载台及其旋转机构沿着轨道回到屏蔽房的检测区域;步骤24,控制二维移动机构b移动至横梁端部,控制第一活动座移动至与转轴轴线基本重合的位置;步骤25,控制第一活动座下移至目标高度;步骤26,开启x射线发生器b和x射线接收器b,控制电机转动,直到x射线发生器b刚好转动一圈后暂定;步骤27,控制x射线发生器b水平移动一个标准长度,继续控制电机转动,直到x射线发生器b刚好转动一圈后暂定;步骤28,多次重复执行步骤27,直到完成检测。
15.本发明中,一种采用前述铸件缺陷自动检测设备的检测方法,其特征在于步骤包括:步骤31,控制屏蔽房的门打开,控制工件承载台及其旋转机构沿着轨道移动至自动上料系统附近;步骤32,控制自动上料系统运行,将待检测的筒形铸件转移至工件承载台上,使筒形铸件中心与工件承载台中心重合;步骤33,控制工件承载台及其旋转机构沿着轨道回到屏蔽房的检测区域;步骤34,调节二维移动机构a和二维移动机构b的竖直丝杠间距,使第一活动座和第三活动座位于电机两侧且以转轴轴线为对称轴进行对称布置,使x射线发生器a与x射线接收器a之间的间距大于筒形铸件的最大外径;步骤35,初步调节第一活动座和第三活动座的高度,使x射线发生器a和x射线接收器a均位于筒形铸件外侧;步骤36,精确调节第一活动座和第三活动座的位置,使x射线发生器a和x射线接收器a均位于检测起始点;步骤37,开启x射线发生器a和x射线接收器a,控制电机转动,直到x射线发生器a和x射线接收器a刚好转动一圈后暂定;步骤38,控制第一活动座和第三活动座同步上升一个标准高度,继续控制电机转动,直到x射线发生器a和x射线接收器a刚好转动一圈后暂定;
步骤39,多次重复执行步骤38,直到完成检测。
16.为进一步地提高检测结果的准确性,所述的标准高度和标准长度均为有效探测区域宽度的1/4-1/3。
17.有益效果:1、采用本发明,不仅能够在生产车间对较大的回转式筒形铸件、异形板状件的缺陷进行快速、准确地检测,而且能够实现对复杂铸件的单壁透照,对于直径2.5m*2.7m的锥形铸件也能够快速、准确地进行检测,以及对小型铸件的双壁透照,具有很好地通用性;2、采用本发明,能够大幅降低检测成本,特别是对于较大的回转式筒形铸件和异形板状件,检测成本不到现有人工贴胶片探伤检测方式成本的1/10,而采用现有的x射线自动检测设备根本无法对其进行检测;3、采用本发明,自动化程度高,操作过程简单,只需一名操作人员便能对大批量的工件进行检测,大幅降低了人员劳动强度;4、采用本发明,无需使用特定的工装夹具就能够对异形板状件进行快速检测,非常方便。
附图说明
18.图1为实施例1中铸件缺陷自动检测设备外部结构示意图;图2为实施例1中铸件缺陷自动检测设备内部结构局部示意图(省略了x射线发生器b);图3为实施例1中铸件缺陷自动检测设备的位置调节机构示意图一(省略了x射线发生器b);图4为实施例1中铸件缺陷自动检测设备的位置调节机构示意图二(省略了x射线发生器b);图5为实施例1中铸件缺陷自动检测设备的位置调节机构示意图三(省略了x射线发生器b);图6为实施例2中铸件缺陷自动检测设备工作状态示意图(内部结构局部);图7为实施例3中铸件缺陷自动检测设备工作状态示意图(内部结构局部);图8为实施例4中铸件缺陷自动检测设备工作状态示意图(内部结构局部);图9为实施例3中检测路径区域示意图。
具体实施方式
19.下面结合附图和实施例对本发明作进一步说明。
20.实施例1本实施例先对铸件缺陷自动检测设备进行说明。如图1至图4所示,该铸件缺陷自动检测设备,包括带有自动控制门的屏蔽房3,设置在屏蔽房3内的x射线发生器1和x射线接收器2,x射线发生器1和x射线接收器2都连接与之配套的计算机控制系统,x射线接收器2将接收到的信号转化为图像信号并通过显示终端进行显示,技术人员即可通过观测显示的图像进行缺陷评定,x射线发生器1、x射线接收器2和计算机控制系统属于市售的成套设备,其原理和具体结构不再赘述。该铸件缺陷自动检测设备的创新部分如下。
21.在屏蔽房3内设置有可旋转的工件承载台4,工件承载台4及其旋转机构连接驱动机构,通过驱动机构驱动工件承载台4及其旋转机构沿着轨道5移动,轨道5自屏蔽房3内向外延伸至自动装卸料系统附近;x射线发生器1设置在位置调节机构上,位置调节机构安装在屏蔽房3内的顶部;旋转机构、驱动机构、自动上料系统(自动上料系统采用六轴机器人8)、位置调节机构分别连接控制器,控制器的存储模块上存储有能够在处理模块上运行的程序,所述处理模块执行所述程序时至少能够实现以下功能/步骤:控制工件承载台4及其旋转机构沿着轨道5移动至预设位置;控制工件承载台4按照预设角度旋转;控制自动装卸料系统将工件转移到工件承载台4上,控制自动装卸料系统将工件从工件承载台4上移走;控制x射线发生器1移动到目标探测位置并按照预设速度转动。
22.其中,位置调节机构包括竖直安装在屏蔽房3顶部的转轴10,转轴10上端连接电机11、转轴10下端连接水平布置的横梁12中部;在横梁12上设置有两套二维移动机构,二维移动机构a上安装x射线发生器a1,二维移动机构b上安装x射线接收器a2,通过控制二维移动机构能够将x射线发生器a1和x射线接收器a2调节至同一高度且相向布置的状态,x射线接收器a2的窗口朝向为水平方向,通过控制电机11转动能够带动x射线发生器a1和x射线接收器a2同步旋转。
23.其中,二维移动机构a包括第一水平丝杠13和第一竖直丝杠14,第一水平丝杠13上配合有第一活动座22,第一竖直丝杠14连接在第一活动座22上,第一竖直丝杠14上配合有第二活动座17,第二活动座17上设置有竖直布置的第一连杆18,x射线发生器a1安装在第一连杆18下部;二维移动机构b包括第二水平丝杠15和第二竖直丝杠16,第二水平丝杠15上配合有第三活动座19,第二竖直丝杠16连接在第三活动座19上,第二竖直丝杠16上配合有第四活动座20,第四活动座20上设置有竖直布置的第二连杆21,x射线接收器a2安装在第二连杆21下部;x射线发生器a1中心、x射线接收器a2中心、第一竖直丝杠14轴线、第二竖直丝杠16轴线与转轴10轴线位于同一竖直平面。其中,第一水平丝杠13旋转通过电机35驱动,第一竖直丝杠14旋转通过电机34驱动,第二水平丝杠15旋转通过电机30驱动,第二竖直丝杠16旋转通过电机33驱动;第一竖直丝杠14安装在安装板32上,第二竖直丝杠16安装在安装板31上。
24.其中,参照图5所示,第一连杆18下部还设置有x射线发生器b6,x射线发生器b6的窗口朝向为竖直向下,x射线发生器b 6的窗口不低于第一连杆18下端,在工件承载台4上设置有x射线接收器b7,x射线接收器b7上表面(有效探测面)为圆形,x射线接收器b7直径大于工件长度,x射线接收器b7表面设置有用于搁放工件的亚克力板或泡沫垫(亚克力板或泡沫垫见附图中编号23),或者在x射线接收器b 7表面先设置有亚克力板,再在亚克力板上放置泡沫垫。亚克力板或泡沫垫的厚度和强度可根据工件规格选择,要满足放置工件时不被压裂,亚克力板的上表面积与工件承载台4的上表面积相同。其中,工件承载台4呈圆形,工件承载台4和转轴10同轴布置。
25.使用过程中:通过调节电机35和/或电机30的转动情况来调节第一活动座22与第三活动座19之间的间距,从而实现调节“安装板32、第一竖直丝杠14、第二活动座17、第一连
杆18、x射线发生器a 1”整体结构与“安装板31、第二竖直丝杠16、第四活动座20、第二连杆21、x射线接收器a 2
”ꢀ
整体结构之间的间距;通过调节电机34的转动情况来调节第二活动座17的高度,进而实现调节x射线发生器a 1的高度;通过调节电机33的转动情况来调节第四活动座20的高度,进而实现调节x射线接收器a 2的高度。在使用x射线发生器a 1与x射线接收器a 2进行透照时,应当始终确保x射线发生器a 1与x射线接收器a 2同步移动且面对面布置;在使用x射线发生器b 6与x射线接收器b7进行透照时,只需要将x射线发生器b 6调节到合适位置并按照预设路径和预设速度进行移动,由于x射线接收器b7位于工件承载台4上,只要工件不大于x射线接收器b7的有效探测面,x射线接收器b7就能够始终显示对应的部位的透照图像。
26.实施例2一种采用实施例1中铸件缺陷自动检测设备的检测方法,用于检测外径为2.5m、壁厚为30mm的圆筒形铝合金铸件36的铸造缺陷,步骤包括:步骤11,控制屏蔽房3的门9打开,控制工件承载台4及其旋转机构沿着轨道5移动至自动上料系统附近;步骤12,控制自动上料系统运行,将待检测的筒形铸件转移至工件承载台4上,使筒形铸件中心与工件承载台4轴线重合(即将筒形铸件放置到工件承载台4中心,此工序可以通过多种方案实现:一是依据标记点进行人工对中;二是借助于六轴机器人直接将筒形铸件放置到位并通过传感器判断是否放置到位,例如,在放置到位的筒形铸件外轮廓正上方设置至少3个红外测距传感器,当监测到3个相同距离信号时表示筒形铸件放置到位,通过六轴机器人将产品放置到预设点位属于常规技术,本领域普通技术人员即可编设相应的程度);步骤13,控制工件承载台4及其旋转机构沿着轨道5回到屏蔽房3的检测区域;步骤14,调节二维移动机构a和二维移动机构b的竖直丝杠间距,使第一活动座22和第三活动座19位于电机11同一侧,使x射线发生器a1与x射线接收器a2之间的间距大于筒形铸件壁厚且小于筒形铸件直径,本例中将x射线发生器a1与x射线接收器a 2之间的间距控制为1m为佳;步骤15,初步调节第一活动座22和第三活动座19的高度,使x射线发生器a1位于筒形铸件外侧,使x射线接收器a2位于筒形铸件内腔,此时的状态如图6所示;步骤16,精确调节第一活动座22和第三活动座19的位置,使x射线发生器a1和x射线接收器a2均位于检测起始点,此时第一活动座22和第三活动座19均位于下极限位置,检测起始点对应筒形铸件最下段;步骤17,开启x射线发生器a1和x射线接收器a2,控制电机11按照预设速度转动,直到x射线发生器a1和x射线接收器a2刚好转动一圈后暂定,此时就对筒形铸件最下段完成了检测;步骤18,控制第一活动座22和第三活动座19同步上升一个标准高度,继续控制电机11转动,直到x射线发生器a1和x射线接收器a2刚好转动一圈后暂定;步骤19,多次重复执行步骤18,直到完成检测。
27.实施例3一种采用实施例1中铸件缺陷自动检测设备的检测方法,用于检测铝合金板状铸
件37(最大长度为1.5m、最短长度为0.6m、宽度为0.5m,厚度为32mm)的铸造缺陷,步骤包括:步骤21,控制屏蔽房3的门打开,控制工件承载台4及其旋转机构沿着轨道5移动至自动上料系统附近;步骤22,控制自动上料系统运行,将待检测的板状铸件37转移至工件承载台4上的,并调节板状铸件37中心与工件承载台4中心基本重合;步骤23,控制工件承载台4及其旋转机构沿着轨道5回到屏蔽房3的检测区域;步骤24,控制二维移动机构b移动至横梁12端部,控制第一活动座22移动至与转轴10轴线基本重合的位置;步骤25,控制第一活动座22下移至目标高度,此时的状态如图7所示;步骤26,开启x射线发生器b6和x射线接收器b7,控制电机11按照预设速度转动,直到x射线发生器b6刚好转动一圈后暂定,此时相当于对第一圆状区域(图9中圆周线40内侧区域)完成了检测;步骤27,控制x射线发生器b6水平移动一个标准长度,继续控制电机11转动,直到x射线发生器b6刚好转动一圈后暂定,此时相当于对第一带状区域(图9中圆周线40与圆周线41之间的带状区域)完成了检测;步骤28,多次重复执行步骤27,直到完成检测,即对第二带状区域(图9中圆周线41与圆周线42之间的带状区域)、第三带状区域(图9中圆周线42与圆周线43之间的带状区域)、第四带状区域(图9中圆周线44与圆周线44之间的带状区域)分别完成检测。
28.本实施例中,x射线发生器b6每旋转一圈,就会对一个带状区域进行检测,当所有带状区域完全覆盖板状铸件37表面时,表示完成检测,整个检测过程巧妙地利用了圆形检测带去覆盖板状表面,适用于绝大多数异形板状铸件37的铸造缺陷检测。检测过程中,只需要将板状铸件37放置在亚克力板和/或泡沫垫上,省去了定制的工装夹具,非常方便。
29.实施例4一种采用实施例1中铸件缺陷自动检测设备的检测方法,用于检测外径为0.3m、壁厚为10mm的筒形铝合金铸件的铸造缺陷,步骤包括:步骤31,控制屏蔽房3的门打开,控制工件承载台4及其旋转机构沿着轨道5移动至自动上料系统附近;步骤32,控制自动上料系统运行,将待检测的筒形铸件转移至工件承载台4上,使筒形铸件中心与工件承载台4中心重合;步骤33,控制工件承载台4及其旋转机构沿着轨道5回到屏蔽房3的检测区域;步骤34,调节二维移动机构a和二维移动机构b的竖直丝杠间距,使第一活动座22和第三活动座19位于电机11两侧且以转轴10对称布置,使x射线发生器a1与x射线接收器a2之间的间距大于筒形铸件的最大外径,本例中第一活动座22与第三活动座19之间的间距控制为0.5m为佳;步骤35,初步调节第一活动座22和第三活动座19的高度,使x射线发生器a1和x射线接收器a2均位于筒形铸件外侧;步骤36,精确调节第一活动座22和第三活动座19的位置,使x射线发生器a1和x射线接收器a2均位于检测起始点;步骤37,开启x射线发生器a1和x射线接收器a2,控制电机11转动,直到x射线发生
器a1和x射线接收器a2刚好转动一圈后暂定;步骤38,控制第一活动座22和第三活动座19同步上升一个标准高度,继续控制电机11转动,直到x射线发生器a1和x射线接收器a2刚好转动一圈后暂定;步骤39,多次重复执行步骤38,直到完成检测。
30.本实施例中,相当于对工件实施双壁透照。
31.实施例5一种采用实施例1中铸件缺陷自动检测设备的检测方法,用于检测外径为2.5~2.7m、壁厚为30mm的圆锥筒形铝合金铸件38(实质上是锥台形,其大径端的外径为2.7m、小径端的外径为2.5m),步骤参照实施例2,其检测状态如图8所示。
32.前述各实施例中,所述的标准高度和标准长度均为有效探测区域宽度的1/4-1/3,以免出现漏检区。
33.对于实施例2至实施例4的步骤,可以通过编程控制执行,实现全自动的智能化检测。
34.采用本发明,不仅能够在生产车间对较大的回转式筒形铸件、异形板状件的缺陷进行快速、准确地检测,而且能够实现对复杂铸件的单壁透照,对于直径2.5m*2.7m的锥形铸件也能够快速、准确地进行检测,以及对小型铸件的双壁透照,具有很好地通用性;采用本发明,能够大幅降低检测成本,特别是对于较大的回转式筒形铸件和异形板状件,检测成本不到现有人工检测方式成本的1/10(对于实施例2和实施例3中的方案,只需要一名操作人员,平均每5-10秒钟可完成一张透照图像对应区域的检测),而采用现有的x射线自动检测设备根本无法对其进行检测;采用本发明,自动化程度高,操作过程简单,只需一名操作人员便能对大批量的工件进行检测,大幅降低了人员劳动强度;采用本发明,无需使用特定的工装夹具就能够对异形板状件进行快速检测,非常方便。