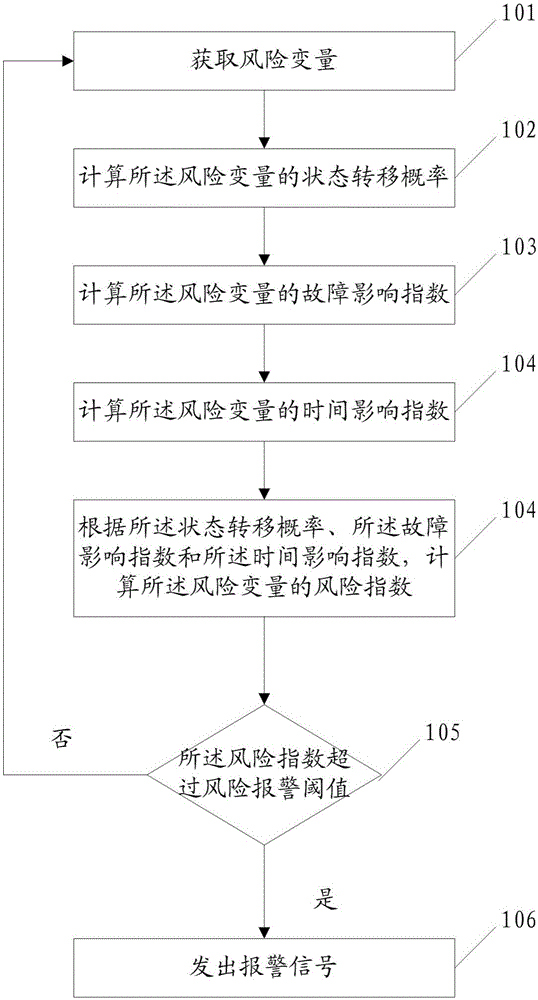
本发明涉及工业检测与报警
技术领域:
,特别是涉及一种基于风险评估的报警方法及系统。
背景技术:
:随着工业过程规模的扩大和工业过程本身复杂程度的增加,过程变量的数目已经达到了一个相当可观的数字。由于对过程变量的监控缺乏科学有效的方法,报警泛滥现象(报警数量在一段时间内超出操作人员处理能力的情况)时有发生。一旦出现报警泛滥,将致使操作员无法及时对过程故障进行有效分析、判断和处理,从而引发严重的后果。在现有技术中,有关故障诊断与报警的专利有专利号为CN104238545A的《一种石油炼化生产过程故障诊断和预警系统及其建立方法》、专利号为CN201522632U的《一种带风险评估功能的泄漏智能检测报警系统》、专利号为CN1838161的《利用计算机进行核电站的设备风险评估方法及装置》和专利号为CN104050528A的《一种基于大数据技术的核电厂人因风险分析监控报警系统》等。《一种石油炼化生产过程故障诊断和预警系统及其建立方法》主要是对石油炼化过程建立多级流模型进行故障诊断和预警,采用危险与可操作性HAZOP分析不同过程故障可能引发的后果;《一种带风险评估功能的泄漏智能检测报警系统》主要是对石油勘探过程中泄漏风险进行检测与评估,包括检测探头,用于风险评估的控制计算机和报警装置;《利用计算机进行核电站的设备风险评估方法及装置》主要是对核电站设备进行风险评估,如果风险指数达到预警值则发出报警;《一种基于大数据技术的核电厂人因风险分析监控报警系统》主要是使用大数据技术对核电厂人因风险进行分析、监控和报警。虽然上述专利提供的技术方案各自解决了一定的技术问题,但是均不能克服在报警泛滥时,操作员无法及时对过程故障进行有效分析、判断和处理的问题。技术实现要素:本发明的目的是提供基于风险评估的报警方法及系统,能够得到当前时刻所有风险变量的风险指数以及能够明显显现风险指数最高的风险变量,便于操作者有针对性的操作,避免了报警参数过多时,操作人员不能及时对过程故障进行有效分析、判断和处理的问题。为实现上述目的,本发明提供了如下方案:一种基于风险评估的报警方法,所述方法包括:获取风险变量,所述风险变量为工业过程中的反应物、生成物、中间产物的监控变量或者为工业过程中所用装置的监控变量或者为工作状态的监控变量;计算所述风险变量的状态转移概率,所述状态转移概率为所述风险变量由正常状态转移至故障状态的概率;计算所述风险变量的故障影响指数,所述故障影响指数用于表示所述风险变量发生故障导致整个工业过程发生故障的;计算所述风险变量的时间影响指数,所述时间影响指数用于表示所述风险变量发生故障的时间导致整个工业过程发生故障的;根据所述状态转移概率、所述故障影响指数和所述时间影响指数,计算所述风险变量的风险指数;判断所述风险指数是否超过风险报警阈值,所述风险报警阈值为系统所能承受的最大风险值;如果是,则发出报警信号。可选的,所述计算所述风险变量的状态转移概率,具体包括:获取所述风险变量的数据概率分布曲线;获取所述风险变量的阈值,所述风险变量的阈值为设定值,当所述风险变量大于所述阈值时,确定所述风险变量发生故障;根据所述阈值,对所述风险变量的数据概率分布曲线进行积分变换,得到所述风险变量的状态转移概率。可选的,所述计算所述风险变量的故障影响指数,具体包括:根据风险变量的故障影响指数公式I(x)=αCSMB(ix)计算所述风险变量的故障影响指数,其中,α为故障指数重要程度调整因子,n为所有风险变量的数量,x为所述风险变量,ix为所述风险变量x在所有的风险变量构成的网络中的编号,bjk(ix)风险变量的联通情况,在所有的风险变量构成的网络中,如果所述风险变量x位于风险变量k与风险变量j的连接通路上,则bjk(ix)=1,否则bjk(ix)=0。可选的,所述计算所述风险变量的时间影响指数,具体包括:记录所述风险变量进入故障状态的时间,标记为t;获取安全阈值,标记为tsafe;根据时间影响指数计算公式计算所述时间影响指数,其中,β为调整因子。可选的,所述根据所述状态转移概率、所述故障影响指数和所述时间影响指数,计算所述风险变量的风险指数,具体包括:根据风险指数计算公式R(x)=P(x)·I(x)·T(x)计算所述风险变量x的风险指数,其中,P(x)为所述风险变量的状态转移概率,I(x)为所述风险变量的故障影响指数,T(x)为所述风险变量的时间影响指数。本发明还提供了一种基于风险评估的报警系统,所述系统包括:风险变量获取单元,用于获取风险变量,所述风险变量为工业过程中的反应物、生成物、中间产物的监控变量或者为工业过程中所用装置的监控变量或者为工作状态的监控变量;状态转移概率计算单元,用于计算所述风险变量的状态转移概率,所述状态转移概率为所述风险变量由正常状态转移至故障状态的概率;故障影响指数计算单元,用于计算所述风险变量的故障影响指数,所述故障影响指数用于表示所述风险变量发生故障导致整个工业过程发生故障的概率;时间影响指数计算单元,用于计算所述风险变量的时间影响指数,所述时间影响指数用于表示所述风险变量发生故障的时间导致整个工业过程发生故障的概率;风险指数计算单元,用于根据所述状态转移概率、所述故障影响指数和所述时间影响指数,计算所述风险变量的风险指数;风险指数判断单元,用于判断所述风险指数是否超过风险报警阈值,所述风险报警阈值为系统所能承受的最大风险值;报警信号发出单元,用于当所述风险指数超过风险报警阈值时,发出报警信号。可选的,所述状态转移概率计算单元,具体包括:概率分布曲线获取子单元,用于获取所述风险变量的数据概率分布曲线;阈值获取子单元,用于获取所述风险变量的阈值,所述风险变量的阈值为设定值,当所述风险变量大于所述阈值时,确定所述风险变量发生故障;状态转移概率计算子单元,用于根据所述阈值,对所述风险变量的数据概率分布曲线进行积分变换,得到所述风险变量的状态转移概率。可选的,所述故障影响指数计算单元,具体包括:故障影响指数计算子单元,用于根据风险变量的故障影响指数公式I(x)=αCSMB(ix)计算所述风险变量的故障影响指数,其中,α为故障指数重要程度调整因子,n为所有风险变量的数量,x为所述风险变量,ix为所述风险变量x在所有的风险变量构成的网络中的编号,bjk(ix)风险变量的联通情况,在所有的风险变量构成的网络中,如果所述风险变量x位于风险变量k与风险变量j的连接通路上,则bjk(ix)=1,否则bjk(ix)=0。可选的,所述时间影响指数计算单元,具体包括:故障状态时间记录子单元,用于记录所述风险变量进入故障状态的时间,标记为t;安全阈值获取子单元,用于获取安全阈值,标记为tsafe;时间影响指数计算子单元,用于根据时间影响指数计算公式计算所述时间影响指数,其中,β为调整因子。可选的,所述风险指数计算单元,具体包括:风险指数计算子单元,用于根据风险指数计算公式R(x)=P(x)·I(x)·T(x)计算所述风险变量x的风险指数,其中,P(x)为所述风险变量的状态转移概率,I(x)为所述风险变量的故障影响指数,T(x)为所述风险变量的时间影响指数。根据本发明提供的具体实施例,本发明公开了以下技术效果:本发明提供的方案选取工业过程中主要的参数作为风险变量,通过计算风险变量的状态转移概率、故障影响指数和时间影响指数以及将三者的结合,得到风险变量的风险指数,使得各风险变量具有统一的评价标准(即风险指数),进而,使各风险变量具有可比性,得到当前风险指数最大的风险变量,以供操作人员参考,能够使操作员及时对过程故障进行有效的分析、判断和处理。附图说明为了更清楚地说明本发明实施例或现有技术中的技术方案,下面将对实施例中所需要使用的附图作简单地介绍,显而易见地,下面描述中的附图仅仅是本发明的一些实施例,对于本领域普通技术人员来讲,在不付出创造性劳动的前提下,还可以根据这些附图获得其他的附图。图1为本发明实施例基于风险评估的报警方法的流程示意图;图2为本发明实施例风险变量的状态转移概率曲线示意图;图3为本发明提供的化工过程田纳西-伊斯特曼过程的流程示意图;图4为本发明实施例风险变量关系示意图;图5为本发明实施例各风险变量的变化示意图;图6为本发明实施例各风险变量的风险指数示意图;图7为本发明实施例风险指数最大变量显示图;图8为本发明实施例风险变量数值随时间的变化示意图;图9为本发明实施例风险变量的报警情况示意图;图10为本发明实施例三个风险变量的风险数值计算结果示意图;图11为本发明实施例三个风险变量的报警情况示意图;图12为本发明实施例风险指数最大变量显示示意图;图13为本发明实施例基于风险评估的报警系统的结构示意图。具体实施方式下面将结合本发明实施例中的附图,对本发明实施例中的技术方案进行清楚、完整地描述,显然,所描述的实施例仅仅是本发明一部分实施例,而不是全部的实施例。基于本发明中的实施例,本领域普通技术人员在没有做出创造性劳动前提下所获得的所有其他实施例,都属于本发明保护的范围。本发明的目的是提供一种基于风险评估的报警方法及系统,能够得到当前时刻所有风险变量的风险指数以及能够明显显现风险指数最高的风险变量,便于操作者有针对性的操作。为使本发明的上述目的、特征和优点能够更加明显易懂,下面结合附图和具体实施方式对本发明作进一步详细的说明。图1为本发明实施例基于风险评估的报警方法的流程示意图,如图1所示,本发明提供的基于风险评估的报警方法步骤如下:步骤101:获取风险变量,所述风险变量为工业过程中的反应物、生成物、中间产物的监控变量或者为工业过程中所用装置的监控变量或者为工作状态的监控变量;风险变量的选取应基于实际过程,具体情况具体分析。通常来说,我们选取风险变量基于以下三方面的考量:(1)是否为过程主要反应物/生成物/中间产物的监控变量(如反应物的浓度、温度、密度等等);(2)是否为过程主要装置的监控变量(如反应炉的温度、压力等等);(3)是否为过程主要状态的监控变量(化工过程可能需要根据过程进行的具体情况在不同的工作状态间进行切换,主要状态的监控变量即用来监控过程当前的工作状态)。步骤102:计算所述风险变量的状态转移概率,所述状态转移概率为所述风险变量由正常状态转移至故障状态的概率;具体包括:根据历史数据和过程知识,获取所述风险变量的数据概率分布曲线;获取所述风险变量的阈值,所述风险变量的阈值为设定值,当所述风险变量大于所述阈值时,确定所述风险变量发生故障;根据所述阈值,对所述风险变量的数据概率分布曲线进行积分变换,得到所述风险变量的状态转移概率,具体的,以所述风险变量的数据概率分布遵循正态分布N(μ,σ)为例,我们设定故障发生的判断阈值为μ±3σ。首先,将N(μ,σ)平移,得到N(μ+3σ,σ)和N(μ-3σ,σ);然后对N(μ+3σ,σ)和N(μ-3σ,σ)进行积分,将以及合并,即得到状态转移概率曲线。图2为本发明实施例风险变量的状态转移概率曲线示意图,如图2所示,实线201、实线202和实线203分别对应N(μ,σ)、N(μ-3σ,σ)和N(μ+3σ,σ),虚线204和虚线205分别对应将和可以观察到,在x=μ±3σ处,状态转移概率均为0.5,意味着风险变量有50%的概率发生故障,有50%的概率不发生故障。记变量x的状态转移概率为P(x),其中,Ax∈U(x)为示性函数,只有当x∈U,Ax∈U(x)=1,否则为0。步骤103:计算所述风险变量的故障影响指数,所述故障影响指数用于表示所述风险变量发生故障导致整个工业过程发生故障的概率;具体为根据风险变量的故障影响指数公式I(x)=αCSMB(ix)计算所述风险变量的故障影响指数,其中,α为故障指数重要程度调整因子,n为所有风险变量的数量,x为所述风险变量,ix为所述风险变量x在所有的风险变量构成的网络中的编号,bjk(ix)风险变量的联通情况,在所有的风险变量构成的网络中,如果所述风险变量x位于风险变量k与风险变量j的连接通路上,则bjk(ix)=1,否则bjk(ix)=0。风险变量所对应的故障影响指数有多种评价方法,本文采用改进的中间中心度作为其评价指标。中间中心度用来描述某点是否处于较多相连网络的路径上,数值越高,该点控制其他点之间关联的能力越强。该指标的计算公式如表1所示。表1其中,n为网络中总的节点数;如果节点i位于节点j与节点k的连接通路上,bjk(i)=1。为了避免CSB=0的情况出现,我们认为每个点都在自己到自己的连接通路上,得到改进的中间中心度如表2所示:表2因此,对于风险变量x,其所对应的故障影响指数I(x)为I(x)=αCSMB(ix),其中,ix为变量x在所有风险变量构成的网络中的编号,参数α用来调节故障影响指数的重要程度。在实际操作过程中,我们首先需要获得过程风险变量之间的有向连接关系,然后根据连接网络计算各变量的故障影响指数。由于故障影响指数在风险变量确定之后一般不再发生改变,因此可以考虑在开始监控前将此部分信息处理并保存下来,方便时时监控中进行调用。步骤104:计算所述风险变量的时间影响指数,所述时间影响指数用于表示所述风险变量发生故障的时间导致整个工业过程发生故障的概率;步骤105:根据所述状态转移概率、所述故障影响指数和所述时间影响指数,计算所述风险变量的风险指数;具体为记录所述风险变量进入故障状态的时间,标记为t;获取安全阈值,标记为tsafe;根据时间影响指数计算公式计算所述时间影响指数,其中,β为调整因子。风险变量进入故障状态时间越久,相应引发故障的可能性越大,因此风险也越大。我们引入安全时间阈值,记为tsafe。一旦变量进入故障状态,计数器开始从零计时;t时刻变量x对应的时间影响指数T(x)为其中,参数β用来调节T(x)的整体趋势。步骤106:判断所述风险指数是否超过风险报警阈值,所述风险报警阈值为系统所能承受的最大风险值;具体为根据风险指数计算公式R(x)=P(x)·I(x)·T(x)计算所述风险变量x的风险指数,其中,P(x)为所述风险变量的状态转移概率,I(x)为所述风险变量的故障影响指数,T(x)为所述风险变量的时间影响指数。步骤107:如果是,则发出报警信号。图3为本发明实施例化工过程田纳西-伊斯特曼过程(TEP)的流程示意图,这个过程由开源仿真实现,在过程控制领域用作基准模型,如图3所示,TEP反应装置由五个基本单元构成:反应器、冷凝器、气液分离器、压缩机和汽提塔。反应涉及八种成分,包括四种气态反应物A、C、D、E,气态催化剂B,副产物F和两种液态生成物G、H。TEP的具体反应过程为:反应物A、C、D、E与催化剂B加入反应器中反应,将初步生成物在冷凝器中冷却后送入气液分离器,分离出的没有反应完全的原料气体通过压缩机压缩至高温高压再送回反应器中继续反应,剩余液态产物则送入汽提塔。汽提塔中,以A、C为主要成分的气体反应物被再次分离,未反应物经压缩机送回反应器,最终生成产品G和H以及副产物F。TEP共有12个可操控变量(其中一个为常量,通常不考虑)和41个观测变量(包括22个连续测量变量和19个成分测量变量)。表3至5为52个变量在本体模型中的名称对照表,其中,表3为22个连续测量变量名称对照表,表4为19个成分测量变量名称对照表,表5为11个控制变量名称对照表。表3表4表5我们选取TEP过程关键变量F1、F6、F5、F10、F14、F17作为风险变量,如图3所示,根据各风险变量所在流1、6、8、9、10、11(图3的附图标记),分别将各风险变量记为x1、x6、x8、x9、x10、x11。根据图3所示的流程图,各风险变量之间的关系如图4所示(图4为本发明实施例风险变量关系示意图),箭头方向表示施加影响的方向。由改进中间中心度计算公式,α=1,故障影响指数的计算结果如表6所示。表6风险变量x1x6x8x9x10x11CSMB0.08338.33332.08332.08338.33330.0833根据步骤101至107分别计算风险变量x1、x6、x8、x9、x10、x11的风险指数。在风险变量x1出现阶跃变化时,如图5所示,由上至下依次为风险变量x1、x6、x8、x9、x10、x11归一化的数值的变化情况(图5为本发明实施例各风险变量的变化示意图),风险变量x1、x6、x8、x9、x10、x11的风险指数变化如图6所示(图6为本发明实施例各风险变量的风险指数示意图)。如图6所示,参数β=0.01,在风险变量x1出现阶跃变化时,图6中从上到下依次为风险变量x1、x6、x8、x9、x10、x11的风险指数的变化情况,黑色虚线为风险指数阈值,红色区域表示相应时刻风险变量的风险指数超过阈值,青色区域表示相应时刻风险变量的风险指数超过阈值,且为所有风险变量同时刻的最大值。由图5、图6,我们可以得出:在变量数值图中,比较不同变量的数值大小缺乏物理意义;在图6中,变量风险指数可以直接进行比较,且易得出当前风险较大的变量,便于操作员有针对性的进行监控。图7为本发明实施例风险指数最大变量显示图,图7显示了在不同时刻六个风险变量中风险指数最大的变量。作为本发明又一具体的实施例,在一输料管道系统中,存在x1、x2、x3三个变量,这三个变量分别监控不同位置的物料流量,变量之间的物理连接关系为x1→x2→x3,即上中下游的关系,箭头表示单向连接。某一时段内,变量数值随时间变化如图8所示,图8为本发明实施例风险变量数值随时间的变化示意图,当变量数值超过报警阈值,则发出报警,本实施例中,报警阈值为±3。图9为本发明实施例风险变量的报警情况示意图,如图9所示,报警对应值为1,正常状态对应值为0。由于三个变量分布在不同位置,设备维护员在同一时刻仅能对其中一个变量发出的报警进行诊断。因此在当前情况下,维护员无法对同时刻多个报警的重要性进行评估,进而选取最为重要的报警优先处理。对此,本发明基于变量的风险指数值,考虑了故障发生的概率,变量的故障影响指数和时间影响指数,能够使操作员定位重要报警,从而避免上述问题的发生。具体方法为:获取风险变量,所述风险变量为不同位置的物料流量x1、x2、x3;分别计算所述风险变量x1、x2、x3的状态转移概率,所述状态转移概率为所述风险变量由正常状态转移至故障状态的概率;分别计算所述风险变量的故障影响指数,所述故障影响指数用于表示所述风险变量发生故障导致整个工业过程发生故障的概率;计算所述风险变量x1、x2、x3的时间影响指数,所述时间影响指数用于表示所述风险变量发生故障的时间导致整个工业过程发生故障的概率;根据所述状态转移概率、所述故障影响指数和所述时间影响指数,分别计算所述风险变量x1、x2、x3的风险指数;判断所述x1、x2、x3的风险指数是否超过风险报警阈值,所述风险报警阈值为系统所能承受的最大风险值;如果是,则发出报警信号。所述分别计算所述风险变量x1、x2、x3的状态转移概率,具体包括:获取所述风险变量的数据概率分布曲线;获取所述风险变量的阈值,所述风险变量的阈值为设定值,当所述风险变量大于所述阈值时,确定所述风险变量发生故障;对所述风险变量的数据概率分布曲线进行平移,根据平移后的所述风险变量的数据概率分布曲线与所述风险变量的阈值进行积分,得到所述风险变量的状态转移概率。所述分别计算所述风险变量x1、x2、x3的故障影响指数,具体包括:根据风险变量的故障影响指数公式I(x)=αCSMB(ix)分别计算所述风险变量x1、x2、x3的故障影响指数,其中,α为故障指数重要程度调整因子,n为所有风险变量的数量,x为所述风险变量,ix为所述风险变量x在所有的风险变量构成的网络中的编号,bjk(ix)风险变量的联通情况,在所有的风险变量构成的网络中,如果所述风险变量x位于风险变量k与风险变量j的连接通路上,则bjk(ix)=1,否则bjk(ix)=0。所述分别计算所述风险变量x1、x2、x3的时间影响指数,具体包括:记录所述风险变量x1进入故障状态的时间、x2进入故障状态的时间、x3进入故障状态的时间,标记为t;获取x1的安全阈值、x2的安全阈值、x3的安全阈值,标记为tsafe;根据时间影响指数计算公式分别计算x1、x2、x3时间影响指数,其中,β为调整因子。所述根据所述状态转移概率、所述故障影响指数和所述时间影响指数,计算所述风险变量的风险指数,具体包括:根据风险指数计算公式R(x)=P(x)·I(x)·T(x)分别计算所述风险变量x1、x2、x3的风险指数,其中,P(x)为所述风险变量的状态转移概率,I(x)为所述风险变量的故障影响指数,T(x)为所述风险变量的时间影响指数。通过计算,图10为本发明实施例三个风险变量的风险数值计算结果示意图,图10是在α=1,x1的故障影响指数GSMB为1,x2的故障影响指数GSMB为2,x3的故障影响指数GSMB为1,时间影响指数的参数β=0.1,tsafe=20的情况下得到三个风险变量的风险数值。图11为本发明实施例三个风险变量的报警情况示意图,风险报警情况如图11所示,设定的风险报警阈值为1.5。由上方两图可以得:(1)由于变量x2对应的故障影响指数较大,所以x2的风险数值整体上比x1和x3大。x2对应的风险报警较多,而另两个变量对应的风险报警较少,因此操作员能够针对x2发出的报警进行重点诊断。(2)虽然从总的时间长度上来看,变量x1和x3超出自身报警阈值的时长相同,但由于变量x1超出阈值的连续时间较长,即x1处于故障状态的时间较长,更易造成不利后果,因此x1对应的风险报警比x3多。(3)如果存在同一时刻多个变量发出风险报警,则可以选取风险值最高的报警进行诊断,图12为本发明实施例风险指数最大变量显示示意图,图12显示了在不同时刻风险指数最大的变量,这样解决了设备维护员无法从多个报警中找出重要报警的问题。本发明提供的基于风险评估的工业过程实时报警方法,克服了传统基于变量测量值的工业过程报警管理方式的不足之处,本方法通过设立风险变量,结合风险变量的状态转移概率、故障影响指数和时间影响指数三个方面,实现对过程风险状态的实时评估与监控。该方法能够有效避免因报警泛滥导致操作员无法及时有效处理过程故障的情况,便于其关注风险值较大的报警信息,从而优先解决风险最高的异常。可通过风险变量的选取与风险指数的实时计算,产生基于风险的报警,对操作员寻找风险最高的报警、及时给出消除故障的措施有很大的指导作用。通过这种先进报警方法,实现了智能报警管理系统对报警简洁性和实用性的要求,对提高系统的安全性能和操作效率、保证企业效益都有着重要意义。为达到上述目的,本发明还提供了一种基于风险评估的报警系统,图13为本发明实施例基于风险评估的报警系统的结构示意图,如图13所示,该报警系统包括:风险变量获取单元1301,用于获取风险变量,所述风险变量为工业过程中的反应物、生成物、中间产物的监控变量或者为工业过程中所用装置的监控变量或者为工作状态的监控变量;状态转移概率计算单元1302,用于计算所述风险变量的状态转移概率,所述状态转移概率为所述风险变量由正常状态转移至故障状态的概率;故障影响指数计算单元1303,用于计算所述风险变量的故障影响指数,所述故障影响指数用于表示所述风险变量发生故障导致整个工业过程发生故障的概率;时间影响指数计算单元1304,用于计算所述风险变量的时间影响指数,所述时间影响指数用于表示所述风险变量发生故障的时间导致整个工业过程发生故障的概率;风险指数计算单元1305,用于根据所述状态转移概率、所述故障影响指数和所述时间影响指数,计算所述风险变量的风险指数;风险指数判断单元1306,用于判断所述风险指数是否超过风险报警阈值,所述风险报警阈值为系统所能承受的最大风险值;报警信号发出单元1307,用于当所述风险指数超过风险报警阈值时,发出报警信号。其中,所述状态转移概率计算单元1302,具体包括:概率分布曲线获取子单元,用于获取所述风险变量的数据概率分布曲线;阈值获取子单元,用于获取所述风险变量的阈值,所述风险变量的阈值为设定值,当所述风险变量大于所述阈值时,确定所述风险变量发生故障;状态转移概率计算子单元,用于对所述风险变量的数据概率分布曲线进行平移,根据平移后的所述风险变量的数据概率分布曲线与所述风险变量的阈值进行积分,得到所述风险变量的状态转移概率。所述故障影响指数计算单元1303,具体包括:故障影响指数计算子单元,用于根据风险变量的故障影响指数公式I(x)=αCSMB(ix)计算所述风险变量的故障影响指数,其中,α为故障指数重要程度调整因子,n为所有风险变量的数量,x为所述风险变量,ix为所述风险变量x在所有的风险变量构成的网络中的编号,bjk(ix)风险变量的联通情况,在所有的风险变量构成的网络中,如果所述风险变量x位于风险变量k与风险变量j的连接通路上,则bjk(ix)=1,否则bjk(ix)=0。所述时间影响指数计算单元1304,具体包括:故障状态时间记录子单元,用于记录所述风险变量进入故障状态的时间,标记为t;安全阈值获取子单元,用于获取安全阈值,标记为tsafe;时间影响指数计算子单元,用于根据时间影响指数计算公式计算所述时间影响指数,其中,β为调整因子。所述风险指数计算单元1305,具体包括:风险指数计算子单元,用于根据风险指数计算公式R(x)=P(x)·I(x)·T(x)计算所述风险变量x的风险指数,其中,P(x)为所述风险变量的状态转移概率,I(x)为所述风险变量的故障影响指数,T(x)为所述风险变量的时间影响指数。本发明提供的基于风险评估的工业过程实时报警系统,克服了传统基于变量测量值的工业过程报警管理方式的不足之处,本方法通过设立风险变量,结合风险变量的状态转移概率、故障影响指数和时间影响指数三个方面,全面评价风险发生的可能性、影响程度和持久度,实现对过程风险状态的实时评估与监控。该方法能够有效避免因报警泛滥导致操作员无法及时有效处理过程故障的情况,便于其关注风险值较大的报警信息,从而优先解决风险最高的异常。可通过风险变量的选取与风险指数的实时计算,产生基于风险的报警,对操作员寻找风险最高的报警、及时给出消除故障的措施有很大的指导作用。通过这种先进报警方法,实现了智能报警管理系统对报警简洁性和实用性的要求,对提高系统的安全性能和操作效率、保证企业效益都有着重要意义。本说明书中各个实施例采用递进的方式描述,每个实施例重点说明的都是与其他实施例的不同之处,各个实施例之间相同相似部分互相参见即可。对于实施例公开的系统而言,由于其与实施例公开的方法相对应,所以描述的比较简单,相关之处参见方法部分说明即可。本文中应用了具体个例对本发明的原理及实施方式进行了阐述,以上实施例的说明只是用于帮助理解本发明的方法及其核心思想;同时,对于本领域的一般技术人员,依据本发明的思想,在具体实施方式及应用范围上均会有改变之处。综上所述,本说明书内容不应理解为对本发明的限制。当前第1页1 2 3