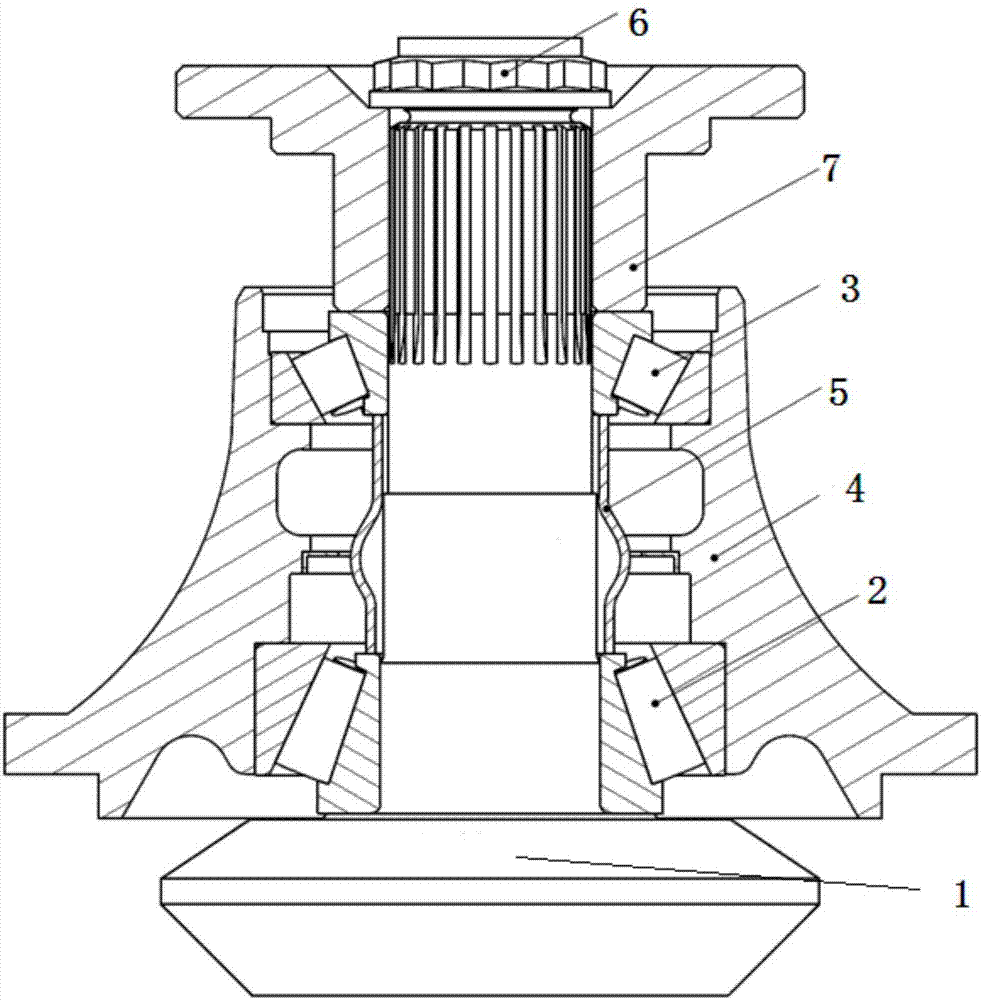
本发明涉及一种汽车关键零部件的优化设计方法,特别是一种驱动桥主锥总成波形套的优化设计方法,属于机械传动
技术领域:
。
背景技术:
:在汽车驱动桥主锥总成中,通常采用一对圆锥滚子轴承对主锥齿轮进行支承,为了保证轴承对主锥齿轮的支承刚度,在装配时必须对轴承进行适当的预紧。因为圆锥滚子轴承的外圈固定安装在主减速器壳轴承座上,轴承外圈之间的相对位置是固定的,所以可以通过改变轴承内圈之间的距离来调整轴承预紧量。现有驱动桥产品通常在两个轴承内圈之间安装有刚性套和垫片,当主锥总成锁紧后,轴承内圈之间的距离由刚性套轴向尺寸和垫片厚度确定,因为刚性套轴向尺寸通常是固定的,所以通过更换不同厚度的垫片,可以实现对轴承预紧量的调整。轴承预紧量必须满足空载状态下的主锥空转摩擦力矩要求,如果摩擦力矩超出了允许范围,即轴承预紧量过大,就需要换用更厚的垫片,以增加轴承内圈之间的距离,从而减小轴承预紧量,反之,应换用更薄的垫片。现有采用刚性套和垫片调整主锥轴承预紧量的方法主要存在以下不足:①由于轴承座、轴承、刚性套和垫片均存在加工误差,同一型号的主锥总成在轴承预紧量合适时对应的垫片厚度存在差异,所以需要提供满足预紧量调整范围的多种厚度系列的垫片,导致成本增加。②当主锥总成摩擦力矩不满足装配要求时,必须重新将主锥总成拆开,更换其他厚度的垫片。在实际装配过程中,生产线上的主锥总成装配人员通常需要对垫片厚度进行多次调整,即对主锥总成进行多次拆装,才能获得理想的轴承预紧效果,导致装配效率大大降低。为了提高驱动桥主锥总成的装配效率,节约人力物力成本,一种可变形的波形套被应用于主锥总成。目前市场上的波形套大多采用鼓肚的结构形式,从而实现波形套的轴向压缩变形特性。将波形套代替刚性套和垫片放置于主锥总成的两个轴承内圈之间,在对锁紧螺母进行拧紧的过程中,两个轴承内圈逐渐靠近,对波形套进行压缩,当波形套所承受的轴向压力达到一定程度时,波形套的鼓肚结构发生屈服变形,且在压缩变形过程中,波形套具有轴向力基本保持恒定的特点,从而保证锁紧螺母的锁紧力矩始终满足装配要求,如果同时对主锥总成的摩擦力矩进行监测,则可以在压缩波形套的同时实现对轴承预紧量的连续调整,克服刚性套和垫片方法需要多次拆装主锥总成的不足。波形套的设计参数对驱动桥主锥总成的性能具有重要影响,由于设计和加工水平的限制,波形套目前主要应用于国外少数大型车桥企业,国内对波形套的研究和应用还不成熟,尤其是有关波形套优化设计方法的研究,在国内外均鲜有报道。目前仍缺乏一种能够快速有效指导企业生产出满足驱动桥主锥总成装配要求波形套的设计、分析及优化方法。技术实现要素:针对上述问题,本发明的目的是提供一种汽车驱动桥主锥总成波形套的优化设计方法,该方法能够快速有效地指导企业生产出满足驱动桥主锥总成装配要求的波形套。为实现上述目的,本发明采用以下技术方案:一种汽车驱动桥主锥总成波形套的优化设计方法,其特征在于,包括以下步骤:1)确定波形套的结构形式和几何设计变量;2)确定波形套的优化设计变量和约束条件;3)确定波形套的性能参数和优化目标;4)进行波形套压缩过程的有限元模拟,快速准确地求得对应设计参数下的波形套性能参数;5)进行波形套优化设计的自动实现。在所述步骤1)中,波形套的结构形式为:孔径较小的一端称为小端直壁圆管,孔径较大的一端称为大端直壁圆管,波形区鼓肚圆弧分别与小端直壁圆管和大端直壁圆管连接;具体连接关系如下:①波形区鼓肚圆弧通过小端锥面段与小端圆弧过渡段相切连接;②波形区鼓肚圆弧通过大端锥面段与大端圆弧过渡段相切连接;③小端圆弧过渡段与小端直壁圆管相切连接;④大端圆弧过渡段与大端直壁圆管相切连接;基于上述波形套的结构形式,确定波形套的11个几何设计变量:总长度h、壁厚t、小端直壁圆管的内径d1、大端直壁圆管的内径d2、小端圆弧过渡段的外侧半径r1、波形区鼓肚圆弧的外侧半径r2、大端圆弧过渡段的外侧半径r3、小端锥面段的半锥角α1、大端锥面段的半锥角α2、波形区鼓肚圆弧的外圆弧相对大端直壁圆管外表面鼓出的高度b和波形区鼓肚圆弧的圆心到大端直壁圆管端面的距离hb。小端直壁圆管的内径d1与大端直壁圆管的内径d2相等时,将波形套任意一端作为小端直壁圆管;允许发生波形区无锥面段的情况,即波形区鼓肚圆弧直接与小端圆弧过渡段或大端圆弧过渡段相切。确定波形套在所述步骤2)中的优化设计变量包括:小端圆弧过渡段的外侧半径r1、波形区鼓肚圆弧的外侧半径r2、大端圆弧过渡段的外侧半径r3、小端锥面段的半锥角α1、大端锥面段的半锥角α2、波形区鼓肚圆弧的外圆弧相对大端直壁圆管外表面鼓出的高度b;根据波形套的具体连接关系和波形套几何模型的闭合条件,确定所述步骤2)中的约束条件如下:g1=r1-t>0g2=r2-t>0g3=r3-t>0g5=b-(r2+r3)×(1-cosα2)≥0上式中,g1~g7表示优化设计变量的约束条件。根据波形套在压缩过程中的轴向力-压缩量变化曲线体现所述步骤3)中的性能参数,包括如下:①波形套在压缩过程中的最大轴向力fmax;②轴向力平台区的轴向力变化量frange;③轴向力平台区的轴向力平均值④轴向力平台区起始点的波形套压缩量lstart;⑤轴向力平台区的波形套压缩量变化范围δl;⑥最大等效塑性应变peeqmax;综合考虑汽车驱动桥主锥总成的装配要求,确定以下指标作为所述步骤3)中的优化目标:①最小化轴向力平台区的轴向力变化量frange;②最小化轴向力平台区起始点的波形套压缩量lstart;③最小化最大等效塑性应变的最大值peeqmax。所述步骤4)中利用有限元分析软件abaqus实现对波形套压缩过程的模拟,具体步骤如下:①根据波形套的结构特点,采用轴对称模型对波形套进行建模,基于波形套的几何设计变量,建立波形套、上端压头、下端压头的几何模型,其中,上端压头和下端压头模型定义为刚体,分别用来模拟两个轴承内圈与波形套之间接触的端面;②定义波形套模型材料参数,包括弹性模量、泊松比和真实应力-应变数据;③对波形套几何模型进行网格划分,建立波形套的有限元模型;④分别在上端压头与波形套、下端压头与波形套之间建立面-面接触关系,并定义摩擦系数;⑤施加边界条件,即约束下端压头,在上端压头施加压缩波形套的位移,模拟装配过程中轴承内圈对波形套的压缩作用;⑥通过有限元分析软件abaqus进行分析求解,计算完成后,读取计算结果,包括波形套在压缩过程中的轴向力-压缩量变化曲线,以及所述步骤3)的波形套的性能参数。采用有限元分析软件abaqus和优化设计软件isight自动实现波形套的优化设计,具体过程如下:①在优化设计软件isight中定义所述步骤1)给出的11个设计变量,并选取r1、r2、r3、α1、α2、b为优化设计变量,定义各优化设计变量的初值和设计空间;②在优化设计软件isight中定义优化设计变量的约束条件g1~g7;③在优化设计软件isight中定义优化目标,分别为最小化轴向力平台区的轴向力变化量frange、最小化轴向力平台区起始点的波形套压缩量lstart和最小化最大等效塑性应变peeqmax;④定义所述步骤③中的各优化目标的比例系数和权重系数;通过无量纲形式公式将多目标优化问题转换为单目标优化问题,使目标k最小,无量纲形式公式如下:式中,f1、l1、p1分别对应为frange、lstart、peeqmax的权重系数,f2、l2、p2分别对应为frange、lstart、peeqmax的比例系数;⑤在优化设计软件isight中选择优化算法;⑥利用优化设计软件isight首先计算步骤②中定义的约束条件g1~g7,并判断g1~g7是否全部满足;⑦若约束条件不全部满足,即基于该组优化设计变量无法建立波形套模型,此时优化设计软件isight直接跳过波形套的有限元分析过程,并根据步骤⑤的优化算法,自动修改优化设计变量的参数值后,重复进行步骤⑥和⑦直至优化设计变量的参数值满足约束条件g1~g7;⑧将满足约束条件的波形套的优化设计变量的参数值用优化设计软件isight写入指定的文本文件,并自动调用有限元分析软件abaqus读取包含优化设计变量的参数值的文本文件,有限元分析软件abaqus按照所述步骤4)的过程,对该组优化设计变量的参数值下的波形套自动进行建模、有限元分析和后处理,求得波形套压缩过程的轴向力-压缩量曲线,并计算波形套的性能参数;⑨有限元分析软件abaqus在有限元分析过程中,需要对波形套壁厚t进行自动修改,以保证波形套的最大轴向力fmax满足驱动桥主锥总成的装配要求,首先设定期望得到的轴向力最大值fmax,target,如果有限元分析软件abaqus求得步骤⑧中的优化设计变量的参数值对应的最大轴向力fmax比fmax,target小,则适当增大壁厚t;反之,则适当减小壁厚,重新进行有限元分析,直到求得波形套的最大轴向力fmax与期望值fmax,target之差小于容差;⑩有限元分析软件abaqus在有限元分析完成后,会将计算结果输出到指定的文本文件中,优化设计软件isight从有限元分析软件abaqus输出的文本文件中读取优化目标的计算结果,并根据步骤④中定义的无量纲形式公式计算单目标结果,然后根据步骤⑤中的优化算法,自动修改优化设计变量的参数值,对新一组优化设计变量的参数值下的波形套重复步骤⑥~⑨的过程,直到找到最优结果或达到设定的最大迭代次数,优化设计过程结束,最后获得波形套的优化设计方案。在所述步骤⑧中优化设计软件isight调用有限元分析软件abaqus的过程通过windows批处理文件实现,有限元分析软件abaqus的自动建模分析过程通过python语言编写的脚本文件实现。本发明采用以上技术方案,其具有如下优点:1、本发明提供了一种汽车驱动桥主锥总成波形套的优化设计方法,通过abaqus和isight软件自动实现波形套的建模分析和优化设计,克服了传统方法人为修改波形套设计参数、多次建模和计算效率较低的不足,能够快速获得满足驱动桥主锥总成装配要求的波形套设计方案,大大节约波形套的设计分析成本,缩短波形套的研发周期。2、本发明提供了一种汽车驱动桥主锥总成波形套的优化设计方法,该方法明确了波形套优化设计的设计变量、设计空间、约束条件和优化目标,为波形套的设计分析提供了技术手段和理论依据。3、本发明提供了一种汽车驱动桥主锥总成波形套的优化设计方法,该方法除应用于鼓肚形式的波形套的优化设计外,还可广泛应用于其他形式波形套的建模分析和优化设计。附图说明图1是本发明的整体流程示意图;图2是某驱动桥主锥总成的结构示意图;图3是波形套几何设计变量示意图;图4是波形套轴向力-压缩量变化曲线示意图;图5是波形套有限元模型示意图;图6是本发明实施例中波形套优化设计方案对应的几何设计参数示意图;图7是本发明实施例中波形套优化设计方案对应的轴向力-压缩量变化曲线。具体实施方式下面结合附图和实施例对本发明进行详细的描述。在本实施例中,以驱动桥主锥总成为例(如图2所示),主动锥齿轮1由一对圆锥滚子轴承支撑,分为大端圆锥滚子轴承2和小端圆锥滚子轴承3;大端圆锥滚子轴承2和小端圆锥滚子轴承3的外圈均安装在主减速器壳轴承座4上,大端圆锥滚子轴承2的内圈固定在主动锥齿轮1背锥一侧,波形套5安装在大端圆锥滚子轴承2和小端圆锥滚子轴承3的内圈之间,当拧紧锁紧螺母6时,锁紧螺母6带动法兰7和小端圆锥滚子轴承3的内圈压缩波形套5。如图1所示,基于上述实施例中的驱动桥主锥总成,本实施例提出了一种汽车驱动桥主锥总成波形套的优化设计方法,包括以下步骤:1)确定波形套的结构形式和几何设计变量如图3所示,波形套5的结构形式为:孔径较小的一端称为小端直壁圆管f,孔径较大的一端称为大端直壁圆管j,波形区鼓肚圆弧a分别与小端直壁圆管f和大端直壁圆管j连接,具体连接关系如下:①波形区鼓肚圆弧a通过小端锥面段b与小端圆弧过渡段c相切连接;②波形区鼓肚圆弧通过大端锥面段d与大端圆弧过渡段e相切连接;③小端圆弧过渡段c与小端直壁圆管f相切连接;④大端圆弧过渡段e与大端直壁圆管j相切连接。基于上述波形套5的结构形式,确定波形套的11个几何设计变量:总长度h、壁厚t、小端直壁圆管f的内径d1、大端直壁圆管j的内径d2、小端圆弧过渡段c的外侧半径r1、波形区鼓肚圆弧a的外侧半径r2、大端圆弧过渡段e的外侧半径r3、小端锥面段b的半锥角α1、大端锥面段d的半锥角α2、波形区鼓肚圆弧a的外圆弧相对大端直壁圆管j外表面鼓出的高度b和波形区鼓肚圆弧a的圆心到大端直壁圆管j端面的距离hb。其中,上述设计参数允许以下特殊情况:若d1=d2,则可将波形套任意一端作为小端直壁圆管f;允许发生波形区无锥面段的情况,即波形区鼓肚圆弧a直接与小端圆弧过渡段c或大端圆弧过渡段e相切。2)确定波形套的优化设计变量和约束条件①确定波形套的优化设计变量在步骤1)列出的波形套11个几何设计变量中,因为波形套总长度h受到驱动桥主锥总成轴承内圈之间的装配距离限制,且对波形套的性能影响很小,d1、d2、hb受到轴承内圈尺寸和传动轴尺寸的限制,设计空间较为有限,所以h、d1、d2、hb不作为优化设计变量。因为壁厚t对波形套最大轴向力的影响最大,所以将t作为用于调整最大轴向力fmax的中间变量。最终确定其他6个对波形套性能起主要影响的参数作为优化设计变量:r1、r2、r3、α1、α2、b。②确定波形套的优化设计变量的约束条件波形套的优化设计变量必须满足波形区鼓肚圆弧、两端直壁管、两端锥面段、两端圆弧过渡段之间的相切关系和波形套几何模型的闭合条件,优化设计变量需满足的约束条件如下:g1=r1-t>0(1)g2=r2-t>0(2)g3=r3-t>0(3)g5=b-(r2+r3)×(1-cosα2)≥0(5)上式中,g1~g7表示优化设计变量的约束条件。3)确定波形套的性能参数和优化目标波形套在压缩过程中的轴向力-压缩量变化曲线是波形套性能的主要体现(如图4所示),波形套的性能参数包括:①波形套在压缩过程中的最大轴向力fmax;②轴向力平台区的轴向力变化量frange;③轴向力平台区的轴向力平均值④轴向力平台区起始点的波形套压缩量lstart;⑤轴向力平台区的波形套压缩量变化范围δl;⑥最大等效塑性应变peeqmax。其中,轴向力平台区表示轴向力f在最大轴向力fmax附近变化梯度近似为零的波形套压缩范围,轴向力平台区内的轴向力平均值越大,主锥总成锁紧螺母力矩也越大,在装配时,应保证波形套轴向力对应的锁紧螺母锁紧力矩满足防松要求;希望frange越小越好,即轴向力在轴向力平台区的波动小;δl越大越好,即轴向力平台区的压缩量充足;lstart应满足装配要求,确保当波形套压缩到对应轴承预紧量的理想位置时,锁紧螺母仍然处于有效线程范围内。综合考虑汽车驱动桥主锥总成的装配要求,确定以下指标作为优化目标:①最小化轴向力平台区的轴向力变化量frange;②最小化轴向力平台区起始点的波形套压缩量lstart;③最小化最大等效塑性应变peeqmax。4)波形套压缩过程的有限元模拟利用有限元分析软件abaqus实现对波形套压缩过程的模拟,能够快速准确地求得对应设计参数下的波形套性能参数,有限元分析过程如下:①根据波形套的结构特点,采用轴对称模型对波形套进行建模,可以大大提高建模和计算效率。基于波形套的几何设计变量,建立波形套、上端压头、下端压头的几何模型,其中,上端压头和下端压头模型定义为刚体,分别用来模拟两个轴承内圈与波形套之间接触的端面;②定义波形套模型材料参数,包括弹性模量、泊松比和真实应力-应变数据,其中,材料的真实应力-应变数据可以由材料性能试验获得;本实施例中波形套材料为10钢,弹性模量e=209gpa、泊松比ε=0.29,材料的真实应力-塑性应变数据由材料性能试验获得,如表1所示;表1波形套材料的真实应力-塑性应变数据塑性应变真实应力/mpa塑性应变真实应力/mpa02320.1284360.01172320.1384440.0132450.1484510.0182680.1584570.0282980.1684630.0383220.1784690.0483430.1884740.0583600.1934770.0683750.1984790.0783880.2034820.0884000.2134860.0984110.2234900.1084200.2334940.1184280.243497③对波形套几何模型进行网格划分,建立波形套的有限元模型,本实施例中单元网格尺寸取0.2mm,如图5所示;④分别在上端压头与波形套、下端压头与波形套之间建立面-面接触关系,并定义摩擦系数,本实施例中摩擦系数取为0.15;⑤施加边界条件,即约束下端压头,在上端压头施加压缩波形套的位移,模拟装配过程中轴承内圈对波形套的压缩作用,本实施例中,取波形套的压缩位移大小为5mm;⑥通过有限元分析软件abaqus进行分析求解,计算完成后,读取计算结果,包括波形套在压缩过程中的轴向力-压缩量变化曲线,以及步骤3)的波形套的性能参数。5)波形套优化设计的自动实现传统的波形套设计方法通常需要人为反复多次调整设计参数进行建模和试算,计算效率较低,且往往难以获得理想的设计方案。为了克服该问题,本发明采用有限元分析软件abaqus和优化设计软件isight自动实现波形套的优化设计,能够快速准确地获得波形套的优化设计方案,优化设计过程如下:①在优化设计软件isight中定义步骤1)给出的11个设计变量,并选取r1、r2、r3、α1、α2、b为优化设计变量,定义各优化设计变量的初值和设计空间。本实施例中,根据驱动桥主锥总成的结构特点,确定波形套5的小端直壁圆管f的内径d1=69mm,大端直壁圆管j的内径d2=73mm,波形区鼓肚圆弧a的外圆弧相对大端直壁圆管j的外表面鼓出的高度b≤6mm,波形区鼓肚圆弧a的圆心到大端直壁圆管j的端面的距离hb=30mm。r1、r2、r3取值过小不利于降低其所在位置的应力,其中一个取值过大就将会使g1~g7的约束条件得不到满足,因而在优化时r1、r2、r3采用的上下限分别为:6mm≤r1≤10mm,初值取8mm(8)8mm≤r2≤20mm,初值取12mm(9)6mm≤r3≤10mm,初值取8mm(10)α1和α2取值过小将导致波形区过长,取值过大将造成波形套加工困难,因而在优化时采用的上下限为:25°≤α1,α2≤40°,初值均取30°(11)b取值过小则波形区不明显,波形套难以承受较大的压缩量,受轴承外圈最小内径、挡油环内径的限制,b的取值应当小于6mm,在优化时采用的上下限为:4mm≤b≤6mm,初值取5mm(12)综上,本实施例中,波形套各设计变量初值如表2所示:表2波形套的各几何设计变量初值②在优化设计软件isight中定义式(1)~式(7)所示的约束条件g1~g7。③在优化设计软件isight中定义优化目标,分别为最小化轴向力平台区的轴向力变化量frange、最小化轴向力平台区起始点的波形套压缩量lstart和最小化最大等效塑性应变peeqmax。④定义步骤③中的各优化目标的比例系数和权重系数,本实施例中,frange、lstart和peeqmax的比例系数分别为1000、2.1和0.25,其作用是将不同单位制的优化目标转化为相同量级的无量纲水平,以便采用权重系数体现优化目标的重要程度,对应的权重系数分别取为0.2、0.5和0.3。通过无量纲形式的式(13)将多目标优化问题转换为单目标优化问题,使目标k最小:⑤在优化设计软件isight中选择优化算法,本实施例采用改良的序列二次规划算法,最大迭代次数和优化步长分别取为100和0.02。⑥利用优化设计软件isight首先计算步骤②中定义的约束条件g1~g7,并判断g1~g7是否全部满足。⑦若约束条件不全部满足,即基于该组优化设计变量无法建立波形套模型,此时优化设计软件isight直接跳过波形套的有限元分析过程,并根据步骤⑤的优化算法,自动修改优化设计变量的参数值后,重复进行步骤⑥和⑦直至优化设计变量的参数值满足约束条件g1~g7。⑧将满足约束条件的波形套的优化设计变量的参数值用优化设计软件isight写入指定的文本文件,并自动调用有限元分析软件abaqus读取包含优化设计变量的参数值的文本文件,有限元分析软件abaqus按照步骤4)的过程,对该组优化设计变量的参数值下的波形套自动进行建模、有限元分析和后处理,求得波形套压缩过程的轴向力-压缩量曲线,并计算波形套的性能参数。其中,优化设计软件isight调用有限元分析软件abaqus的过程通过windows批处理文件实现,有限元分析软件abaqus的自动建模分析过程通过python语言编写的脚本文件实现。⑨有限元分析软件abaqus在有限元分析过程中,需要对波形套壁厚t进行自动修改,以保证波形套的最大轴向力fmax满足驱动桥主锥总成的装配要求,首先设定期望得到的轴向力最大值fmax,target,如果有限元分析软件abaqus求得步骤⑧中的优化设计变量的参数值对应的最大轴向力fmax比fmax,target小,则适当增大壁厚t;反之,则适当减小壁厚,重新进行有限元分析,直到求得波形套的最大轴向力fmax与期望值fmax,target之差小于容差,在本实施例中容差为10n。⑩有限元分析软件abaqus在有限元分析完成后,会将计算结果输出到指定的文本文件中,优化设计软件isight从有限元分析软件abaqus输出的文本文件中读取优化目标的计算结果,并根据步骤④中定义的式(13)计算单目标结果,然后根据步骤⑤中的优化算法,自动修改优化设计变量的参数值,对新一组优化设计变量的参数值下的波形套重复步骤⑥~⑨的过程,直到找到最优结果或达到设定的最大迭代次数,优化设计过程结束,最后获得波形套的优化设计方案。本实施例中获得波形套的优化设计方案如表3所示,对应的几何设计参数示意图如图6所示,对应的波形套在压缩过程中的轴向力-压缩量变化曲线如图7所示,其中,优化设计方案对应的优化目标计算结果分别为:frange=996n;lstart=2.31mm;peeqmax=0.217。表3本实施例中波形套的优化设计方案设计参数数值波形套的轴向尺寸h/mm79.1波形套的壁厚t/mm3.03波形套小端内径d1/mm69.0波形套大端内径d2/mm73.0小端圆弧过渡段外侧半径r1/mm8.42鼓肚圆弧外侧半径r2/mm18.0大端圆弧过渡段外侧半径r3/mm7.06小端锥面段半锥角α1/(°)29.6大端锥面段半锥角α2/(°)28.6鼓肚圆弧段外圆弧相对大端外表面鼓出的高度b/mm4.02鼓肚圆弧圆心到大端端面的距离hb/mm30.0本发明仅以上述实施例进行说明,各部件的结构、设置位置及其连接都是可以有所变化的。在本发明技术方案的基础上,凡根据本发明原理对个别部件进行的改进或等同变换,均不应排除在本发明的保护范围之外。当前第1页12