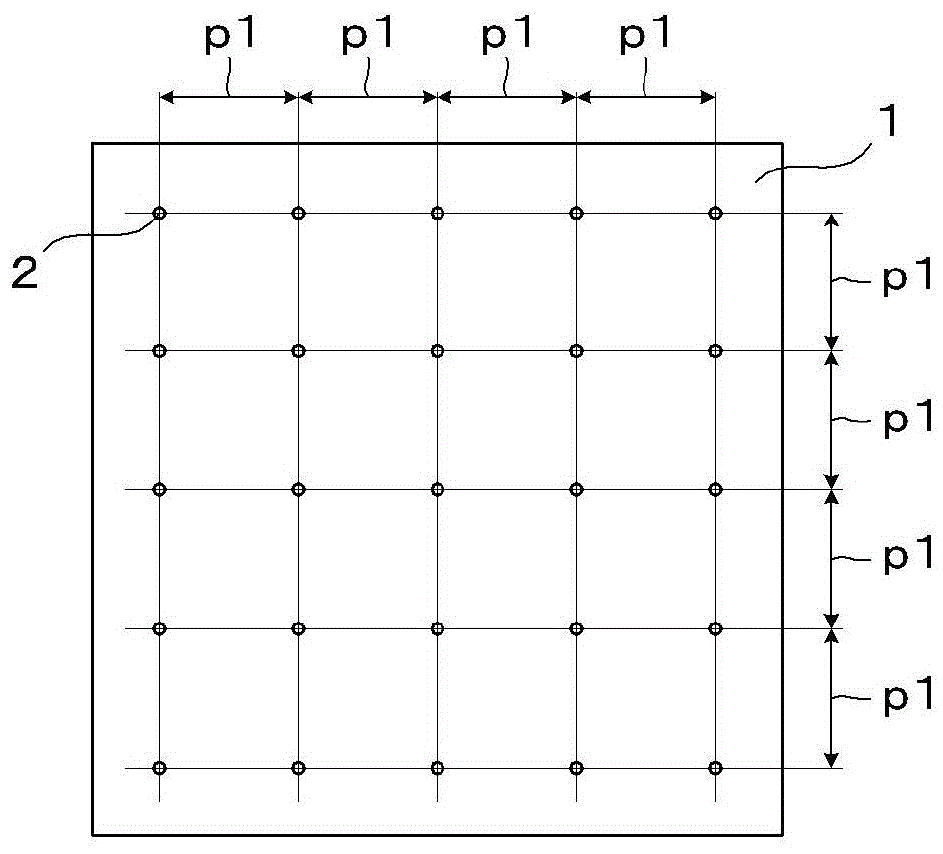
本发明涉及有效地使热从发热的半导体器件、车载用装置、电子设备中扩散、释放来消除因热产生的问题,并维持、改善其功能从而获得高可靠性。
背景技术:关于半导体器件、车载部件等,为了避免由于其高输出造成器件的一部分或全部变为高温而产生的功能下降或者停止,迄今一直在研究将其热量传导、释放到Cu制均热片、Al制散热片或者基片、壳体上。因此,使用金属或碳化物等热传导率高的物质作为热传导及散热的材料。专利文献1提出了一种用纳米碳作为第一层并在其上层层积非晶硅材料来作为第二层的结构。其记载了:在该结构中,第一层纳米碳的结晶性得到提高,膜内的热传导率得到改善,能够实现比现有的传热组件更小型化。该方法中,热传导率在膜内方向约为950~1600W/mk、在膜厚方向为1.5~3.0W/mk,高效地经由第一纳米碳层使来自发热部位的热传导到膜内来进行热扩散,纳米碳层和非晶硅层的厚度均薄至1~20nm,它们的厚度较薄,不足以将可能在局部大量产生的热传出。由于该结构的制造方法为薄膜工艺(真空装置),因此需要长时间来增加膜厚,不适用于传导大发热量。此外,在器件、电子设备驱动时的加热、冷却的热循环中、伴随着纳米碳层和非晶硅层之间的热膨胀系数的差所产生的应力会使纳米碳层的层间发生变形,其结果导致发生裂纹、剥离的危险性较高。特别是,结晶性高的纳米碳层间的密接强度比较弱,很有可能导致器件、电子设备的可靠性下降。专利文献2记载了在石墨的至少一个或两个表面上设置了金属薄膜的金属-石墨复合体,并提及了用于该金属薄膜的金属为镍、钴、钛中的任何一种金属或以该金属为主要成分的合金,由此改善了在碳原子结合面方向上的良好热传导性和在与之垂直的方向上的导电性以及在本金属膜上的焊接操作性。现有技术文献专利文献专利文献1:日本专利特开平10-330177号公报专利文献2:日本专利特开2008-270724号公报
技术实现要素:然而,并不认为这些方法能够解决上述因加热冷却时的应力所造成的石墨层间的剥离问题,可靠性问题依然存在。本发明的石墨结构体的特征在于,包括:石墨板,该石墨板以和基面(basalplane)平行地方式层叠而成;贯通孔,该贯通孔从所述石墨板的与所述基面平行的表面贯通到背面;以及覆盖层,该覆盖层通过与所述石墨板的碳原子形成化合物的金属来覆盖所述贯通孔的内周;在内周面被所述覆盖层覆盖的所述贯通孔的更内侧,形成有连通所述石墨板的所述表面和所述背面的连通孔。此外,本发明的电子器件的特征在于,在散热路径上设有所述石墨结构体。此外,本发明的设备的特征在于,使用所述电子器件。如果使用这种结构,就能够实现电子器件和其设备的小型化、薄型化、轻量化,并且能够解决因加热冷却时的应力造成的剥离问题,实现高可靠性。附图说明图1是本发明的实施方式1的石墨结构体的放大剖视图。图2是该实施方式中使用的石墨板的俯视图。图3是该实施方式的石墨结构体的制造工序图。图4是使用了本发明实施方式2的石墨结构体的电子器件的放大剖视图。图5是使用本发明实施方式3的石墨结构体的电子器件的放大剖视图。图6是使用本发明实施方式4的石墨结构体的电子器件的放大剖视图。图7是本发明实施方式5的石墨结构体的俯视图。图8是本发明实施方式6的石墨结构体的俯视图。具体实施方式以下,基于各实施方式对本发明的石墨结构体和使用该石墨结构体的电子器件进行说明。此外,对于具有相同作用的部分附加相同的标号加以说明。(实施方式1)图1是在半导体芯片或其封装件与散热板之间安装使用的实施方式1的石墨结构体的放大剖视图,图2是表示石墨结构体制作中使用的石墨板1的加工过程中的一个示例的俯视图,图3是制造工序的图。在用于形成石墨结构体25的板状的石墨板1上,以间距p1将贯通孔2贯穿设置成矩阵状(参照图2)。在该石墨板1的表面和背面以及贯通孔2的内周面上覆盖有对石墨板1的碳原子有反应性的Ti层3来作为覆盖层。t1为石墨板1的厚度,t2为石墨板1的表面和背面上的Ti层3的膜厚。在贯通孔2的内侧有连接上下两侧并开口的连通孔4。图2表示被Ti层3覆盖前的石墨板1。该连通孔4在使用该石墨结构体25时起到对将石墨结构体25夹持并配置在上下两侧的部件进行吸附并保持的作用。将在实施方式2中对其作详细说明。石墨板1以厚度50μ以下的高分子膜为原料,对通过在超过2500℃的高温、加压、还原气氛中处理所得到的薄板状(图3(a))进行加工而制成。因此,该石墨板1是以和碳的六元环所构成的面即基面相平行的方式层叠得到的石墨板。石墨板1的表面和背面的面间厚度为:t1=15μm以下。如果厚度超过15μm,则结晶性会下降,使热传导率降低。而且,这也限制了对于推进小型化和薄型化的器件、设备的适用性。此外,该石墨板1的表面和背面大致平行于由碳的六元环构成的面(基面),该平行方向上的石墨板1的热传导率为1000W/mk以上,而石墨板1的垂直方向上的热传导率为5W/mk以下,比重为2.25g/cm3以下,且导电率和杨氏模量分别为106S/m以上、750GPa以上。石墨板1的表面粗糙度以1~4μm为优选,这里将表面粗糙度设为2μm。如果表面粗糙度小于1μm,则石墨板1上设置的Ti层3的密接性下降,在热循环时会发生剥离。相反地,如果表面粗糙度超过4μm,Ti层3的密接性也会下降。此外,如果石墨板1的表面粗糙度超过4μm,则半导体器件与石墨结构体的密接性会下降,使热传导性降低。对于垂直地穿过石墨板1的平面膜内的贯通孔2,在石墨板1的表面和背面设有Ti层3的情况下,经由该贯通孔2与表面侧的Ti层和背面侧的Ti层3连续地结合而形成。Ti与C的相容性良好,而且与用于半导体封装的阻挡层金属(主要为Ni)材料的相容性也良好。这里,相容性意指密接性和界面的热阻低。贯通孔2的位置可以任意设置,但是为了使石墨板1的可靠性提高,理想的是,包含适用于器件的石墨板1的最大尺寸的周围在内,设置成矩阵状。需要使贯通孔2的开口比例(密度)对于石墨板1的总平面面积在10%以下。优选地为7%以下。如果面积大于10%,则贯通孔2会阻碍平面方向的热传导,但小于0.1%,则对于石墨层间剥离的抑制力不足,从而也不好。热传导性会下降,层间的剥离也会发生。贯通孔2的形状为圆形,但并不限于圆形。关于贯通孔2的形成方法,例如可以利用使用了汤姆逊刀的机械加工方法。将汤姆逊刀埋置于橡胶而成为版状工具,用该版压入石墨板1来进行穿孔。还可举出利用高压水进行的加工等,但是并不限于这些。图3(b)示出了形成有贯通孔2的石墨板1。Ti层3通过气相沉积、溅射、镀敷中的任一方法设置,其厚度t2=0.01μm~0.2μm。如果厚度小于t2=0.01μm,会产生空隙等问题,相反地,如果厚度大于t2=0.2μm,则难以实现器件、电子设备的小型化、薄型化。Ti层3的密接性非常高,赛璐玢胶带剥离测试时的破坏模式为石墨板1的材料破坏。这样制作成的石墨结构体25如图3(c)所示。实施方式1中,Ti层3形成后贯通孔2未被填埋,在贯通孔2的内侧存在连通孔4。连通孔4的直径d2为“d1﹣2·t2”。如此,通过在石墨板1上设置贯通孔2、Ti层3、连通孔4,使得在装入半导体器件时与裸芯片(chipdie)的阻挡金属层或金属制均热片的密接性提高。此外,对于半导体器件驱动时发热-冷却循环时产生的石墨板1上的剪切应力,由于贯通孔2的Ti层3的效果,因热膨胀差造成的平面方向的剪切变形得以缓和,不会产生石墨板1的裂纹、剥离。因此,如果将高热传导性复合材料、即该石墨结构体作为热对策部件应用于半导体封装件、车载设备、功率设备或LED照明用设备上,则能实现设备的小型化、薄型化、轻量化。例如在半导体器件中,特别是对于高端机型的电脑的CPU用半导体器件,伴随着高工作频率会产生大量的热,结果为了确保安全驱动,其工作频率及驱动电压自动下降,从而使响应速度、处理速度下降。并且,如果即使如此温度也不下降,就会进入自动停止的状态。为了避免出现这样的问题,使裸芯片内产生的热传到铜制的均热片上来作为半导体封装件,之后,热量经由铝散热片那样的散热部件逸出到空气中。或者,经由接合点将热传给安装的基片来实现低温化。然而,半导体的集成度在飞跃上升,CPU的发热温度、发热速度随之增大,在如上所述的散热对策中,从发热部位到散热部件的热扩散、热传导速度缓慢,该问题已经不可回避。在这样的状况下使用本发明可取得较大效果。即,通过以该石墨结构体来取代将裸芯片内产生的热传到均热片上时所使用的、含有铝粉那样的金属粉的热传导性润滑脂、铟那样的低熔点金属、其合金,具体而言,通过在裸芯片和均热片之间设置石墨结构体,使得裸芯片所产生的热更快地在石墨板1的平面内扩散,随后传导至均热片上,从而使裸芯片的发热部位冷却,温度下降,从而可不降低CPU的处理速度、响应速度,能够维持高工作频率。此外,通过使用该石墨结构体,不仅能够维持并确保高的工作频率,而且能够制作迄今一直小型且轻薄的器件。在3000℃的还原气氛中处理东丽·杜邦制聚酰亚胺膜(厚25μm),制成大小为60mm×60mm、厚度t1=10μm、表面粗糙度为2μm的实施方式1的石墨板1。其特性是,面方向上的热传导率为1500W/m·k,与该面垂直的方向上的热传导率为3W/m·k,比重为2.3,弹性模量为750Gpa。如图2所示,用汤姆逊刀在60mm×60mm见方的石墨板1上形成25个直径d1=1mm的圆形贯通孔2后,利用溅射在石墨板1的表面、背面以及贯通孔2的侧面形成t2=0.2μm的连续的Ti层3。此时的贯通孔2处于通孔状态,其中心部分形成有未充填Ti层3的连通孔4。另外,此例中贯通孔2的总面积为19.6mm2,该面积占石墨板1整个面积的0.5%。<评价>对于实施方式的情况,以﹣65℃~120℃作为一个循环进行了500循环、1000循环、2000循环的冷热冲击试验。试验结束后未发现层间剥离和/或外观异常。(实施方式2)图4表示实施方式2。实施方式2是使用了实施方式1的石墨结构体的电子器件26的放大剖视图。石墨板1的表面上配置有第一部件11。石墨板1的背面上配置有第二部件12。第一部件11是散热部件、冷却部件等。第二部件12是半导体元件、电子部件等。图4中未作说明的部分与实施方式1相同。贯通孔2具有连通孔4。贯通孔2的直径为d1=1mm,Ti层3的厚度为0.2μm。石墨板1的表面凹凸小至3μm以下,接近于镜面。因此,表面和背面被Ti层3覆盖的石墨板1与第一部件11和第二部件12的密接性良好。这样,在第一部件11和第二部件12经由Ti层3大致密接于石墨板1的状态下,若第一部件11的温度上升,则连通孔4内的气体膨胀,连通孔4的内部压力上升而超过连通孔4的外部压力。伴随连通孔4的内部压力上升,已进入连通孔4的气体通过第一部件11与Ti层3之间、第二部件12与Ti层3之间排出。在这种状态下,如果第一部件11的温度下降,则连通孔4的内部接近真空状态,于是石墨板1、第一部件11、第二部件12通过连通孔4而一体化。不在接触面上使用润滑脂、热传导性粘接剂等也可以。(实施方式3)图5表示实施方式3。实施方式2中,贯通孔2的形状是从石墨板1的表面到背面均为单一直径d1的孔,连通孔4的形状也是从石墨板1的表面到背面均为单一直径的孔,然而,该实施方式3的电子器件26中使用的石墨结构体25的连通孔4的形状与实施方式2的不同。对于实施方式3的石墨结构体25的连通孔4的形状,连通孔4的开口形成为向外扩展。具体而言,连通孔4的开口形成为向外扩展的锥形形状27。为了形成这种结构,贯通孔2的开口也形成为向外扩展的锥形形状。对于如此将连通孔4的开口形成为向外扩展的锥形形状27的情况,由于连通孔4的内部压力降低而产生的与第一、第二部件11、12的吸附性要优于实施方式2的情况。另外,为了确保热传导,贯通孔2的总面积最好占石墨板1的整个面积的10%以下。如果面积小于0.1%,则石墨板1的层间不能压紧,从而阻碍热传导。这里,贯通孔2的面积不是由端部(上下表面)的扩展部分来定义,而是由内部的中心部分的截面积来定义。也就是说,由截面面积最小处的直径来定义,这是因为该部分决定了热传导能力。另外,Ti层3的厚度为t2时,贯通孔2减去2·t2后的尺寸即为连通孔4的直径,由于t2=0.2μm左右,故贯通孔2的总面积与连通孔4的总面积大致相等。(实施方式4)图6表示实施方式4。实施方式2中,贯通孔2的形状是从石墨板1的表面到背面均为单一直径d1的孔,连通孔4的形状也是从石墨板1的表面到背面均为单一直径的孔,然而,该实施方式4的电子器件26所使用的石墨结构体25的连通孔4的形状与实施方式2不同。对于实施方式4的石墨结构体25的连通孔4的形状,上述连通孔4的开口形成为向外扩展。具体而言,连通孔4的开口形成为截面积从内侧向外侧逐渐变大的R形状28。为了形成这种结构,贯通孔2的开口也形成为向外扩展的R形状。对于如此将连通孔4的开口形成为向外扩展的R形状28的情况,由于连通孔4的内部压力降低而产生的第一、第二部件11、12之间的吸附性要优于实施方式2的情况。连通孔4的面积比例和面积的定义与实施方式3相同。(实施方式5)图7(a)和图7(b)分别表示实施方式5的石墨结构体25。实施方式1中石墨板1上的贯通孔2的分布是如图2所示,在平面内均匀地进行配置,因此,石墨结构体25的连通孔4也在平面内均匀分布。图7(a)与之的不同点在于,连通孔4的分布在平面内呈不均匀地配置。如果石墨板1上贯通孔2和经由Ti层3形成在贯通孔2的内侧的连通孔4的数量较多,则通过Ti层3在石墨板1的厚度方向上可靠地压紧、固定,热传导率得以确保。但是,在贯通孔2、连通孔4处热传导中断,因此横向(石墨板1的平面方向)的热传导性降低。图7(a)中,在实施方式2中的配置第一、第二部件11、12的配置区域13和不配置第一、第二部件11、12的周边区域23,石墨板1上的贯通孔2和连通孔4的密度不同。具体而言,配置区域13和周边区域23中的所有贯通孔2和连通孔4的直径相同,为了不阻碍配置区域13的热传导,周边区域23的贯通孔2和连通孔4的总面积密度设为高于配置区域13中的密度。这样的话,将第二部件12所产生的热首先从配置区域13内迅速地传导至周边区域23,能够立即使第二部件12冷却。周边区域23的贯通孔2和连通孔4较多,因此其热传导性比配置区域13差,但是防止了石墨板1整体的层间剥离,并确保了上下方向的热传导。此例中,配置区域13的贯通孔2和连通孔4的总面积的密度大约为周边区域23的密度的一半。优选的是,若设置2倍以上的密度差异,则能确保热传导率以及防止石墨层之间的剥离。在图7(b)所示的情况下,通过在配置区域13和周边区域23变更贯通孔2和连通孔4的直径,从而使石墨结构体25的贯通孔2和连通孔4的分布在平面内不均匀。具体而言,为了不阻碍热传导性,配置区域13的贯通孔2和连通孔4的直径小于周边区域23的贯通孔2和连通孔4的直径。对于贯通孔2和连通孔4的总面积的密度,第一部件11的配置区域13为周边区域23的一半。在这种情况下,无需在周边区域23设置较多的贯通孔2和连通孔4并能实现热传导性良好的石墨结构体。(实施方式6)图8表示实施方式6的石墨结构体25中所使用的石墨板1的俯视图。对于该石墨板1,贯通孔2的数量最少,贯通孔2的直径为最大,贯通孔2的比例为占石墨板1的面积的10%以下。为了固定并保护石墨板1的整体层间,需要在最少三处设置相同大小的贯通孔2。其结果是,每个贯通孔2的最大面积需要设为石墨板1的整体面积的3.3%以下。另一方面,为了通过降低之后在贯通孔2的内侧形成Ti膜3所形成的连通孔4的内部压力,从而将第一、第二部件11、12固定在石墨板1上,需要在石墨结构体25的配置了第一、第二部件11、12的配置区域13中设置1个以上的贯通孔2。为此,图8中,在配置区域13的中央设置了1个贯通孔2,在周边区域23的端部设置了两个贯通孔2。当然,在周边区域23均匀地设置多个较小直径的贯通孔2较好。此外,Ti层3最小厚度需要为t2=0.01mm,因此,为了在贯通孔2的内周形成Ti膜3,并确保其内侧有d2=0.01mm的连通孔4,贯通孔2的最小直径需为d1=0.03mm。上述的各实施方式中,在Ti层3上没有设保护膜,但可以使用用于改善Ti层3的耐久性的抗氧化膜,例如WN、TiN等的氮化物、碳氟化合物等氟化物、对二甲苯和丙烯酸等有机高分子。也可以根据电绝缘的需要设置类金刚石碳(Diamond-likeCarbon)层、高分子层等绝缘层。上述的各实施方式中,以使用Ti层3的情况为例作了说明,但是,作为与碳原子具有反应性的该覆盖层,也可以使用镍、钴、钛等易与碳发生反应的金属,即,与碳形成化合物的金属,以及包含这些金属元素来作为主要成分的合金。上述的各实施方式中,贯通孔2、连通孔4的形状为圆形,但也可以不是圆形而为三角形、椭圆等。另外,只要没有阻碍因素,可以对上述实施方式进行组合。本发明适用于半导体、太阳能电池、电动汽车、照明设备等使用大功率的需采取热对策的各种用途,有助于改善可靠性和实现设备的薄型化。