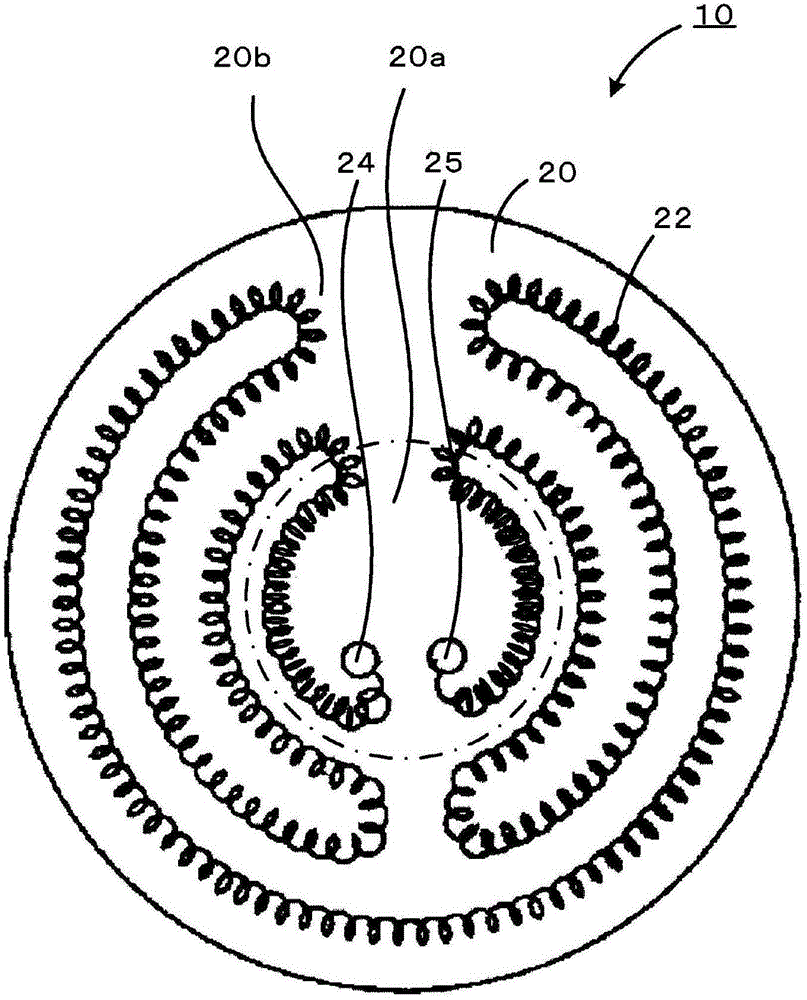
本发明涉及一种加热装置及半导体制造装置。
背景技术:对于半导体制造装置,在通过热CVD、等离子CVD等来由硅烷气等原料气体制造半导体薄膜的时候,采用用于加热晶片的加热装置。作为加热装置,已知一种包括具有晶片放置面的圆盘状的陶瓷基体、设在该陶瓷基体的内部或表面的电阻发热体、安装在该陶瓷基体中的晶片放置面的相反侧的面上的中空轴的装置。在这样的加热装置中,已知有各种用于使晶片放置面的温度均匀化的方法。例如,在将螺旋弹簧状的电阻发热体(缠绕体)埋设在陶瓷基体内的情况下,通过使缠绕体的圈数增多或使卷径变大,或使线径变小,能够使单位面积的晶片设置面的发热量增大。又,通过使缠绕体的圈数减少或使卷径变小,或使线径变大,能够降低每单位面积的晶片设置面的发热量(发热密度)。【现有技术文献】【专利文献】【专利文献1】特开2003-272805号公报
技术实现要素:【发明要解决的技术问题】然而,若在CVD工序的开始后立即导入原料气体,陶瓷基体的中央部的温度有可能会上升,基于这一点,有时对温度分布进行设计,以使得陶瓷基体的中央部预先达到比外周部低的低温。将这样的温度分布称为中冷型温度分布。中冷型温度分布例如在利用螺旋弹簧状的电阻发热体的情况下,通过与陶瓷基体的外周部相比使中央部的圈数变少(即使中央部的发热密度变小)能够很容易地实现。通常,陶瓷基体的温度控制是用热电偶测定陶瓷基体的温度,通过调节向电阻发热体供给的电量使该测定温度达到预先设定的目标温度来进行的。此时,热电偶被配置成能测定陶瓷基体的中央部(即中空轴的内侧)的温度。然而,在紧接着将晶片放置到晶片放置面后的情况下或在CVD工序中发生向晶片的等离子热量输入的情况下,可能会产生温度控制性降低、达到稳定的温度的时间变长、通过CVD得到的膜的厚度不均匀等的问题。以下对产生这样的问题的原因进行说明。陶瓷基体的中央部如上述那样,为了实现中冷型温度分布,与陶瓷基体的外周部相比发热密度变小。热电偶测定该发热密度小的部分的温度。因此,例如在由热电偶测定的温度没有达到目标温度而增加向电阻发热体的供电量的情况下,由于发热密度的差异,与外周部相比中央部的温度上升较晚。结果,当由热电偶测定的温度达到目标温度时,即中央部达到目标温度时,外周部可能会大幅地超过目标温度。这样的温度控制性的降低能够通过使发热密度在陶瓷基体的中央部与在外周部处没有多少差别来改善。然而,在该情况下,由于中冷型温度分布变小,当在CVD工序开始后立即导入原料气体时,中央部与外周部相比可能会变成高温。又,虽然考虑通过让陶瓷基体的热传导到中空轴来使中冷型温度分布相对变大,但若中空轴的温度变得过高,由于中空轴的下端通过O环进行密封的关系,O环可能会因为热而劣化从而密封性降低。由于这样,人们期望同时做到中冷型温度分布的实现和温度控制性的提高,还要防止中空轴的下端的高温化。本发明是为了解决这样的问题而提出的,其主要目的在于,在加热晶片的加热装置中,同时做到中冷型温度分布的实现和温度控制性的提高,还防止中空轴的下端的高温化。【解决问题的技术手段】本发明者们当初认为,为了实现中冷型温度分布,必须使中央部的发热密度与外周部相比变小。然而,通过这样的构成,在调节向电阻发热体的供电量使陶瓷基体的中央部的温度达到预先设定的目标温度的情况下,温度控制性降低了。因此,转换构思,考虑通过使中央部的发热密度与外周部相比变大,来实现中冷型温度分布。于是,钻研了各种中空轴的形状后,发现能够同时做到中冷型温度分布的实现和温度控制性的提高,并且能够防止中空轴的下端的高温化,直到完成本发明。本发明的加热装置包括:具有晶片放置面的圆盘状的陶瓷基体、设在该陶瓷基体的内部或表面的电阻发热体、安装在上述陶瓷基体中的上述晶片放置面的相反侧的面上的中空轴,上述陶瓷基体具有中央部和外周部,上述外周部为上述中央部外侧的环状区域,上述电阻发热体按在上述中央部处的发热密度高于在上述外周部处的发热密度来设置,上述中空轴包括从上述陶瓷基体到规定的中间位置的第1部位、和从上述中间位置到轴末端的第2部位,上述第1部位的厚度为上述第2部位的厚度的2~3.3倍,上述第1部位的长度为上述轴的全长的0.4~0.8倍。根据本发明的加热装置,能够同时做到中冷型温度分布的实现和温度控制性的提高,进而能够防止中空轴的下端的高温化。即,该加热装置中,中央部中的发热密度比外周部中的发热密度高。在此,发热密度是指每单位面积的晶片放置面的发热量。在调节向电阻发热体的供电量使陶瓷基体的中央部的温度达到预先设定的目标温度的温度控制中,对温度进行测定的中央部由于发热密度高,因而当供电量增加时会迅速地随之而温度上升。因此,陶瓷基体的温度控制性变得良好。另一方面,若按这样来设定发热密度,本来无法实现中冷型温度分布。然而,将其形状进行了设计的中空轴安装到中央部。具体地说,中空轴的第1部位的厚度为第2部位的厚度的2~3.3倍,第1部位的长度为轴的全长的0.4~0.8倍(第2部位的长度为全长的0.2~0.6倍)。这样,由于第1部位形成足够的厚度,中央部的热变得容易流出到中空轴的第1部位,从而实现中冷型温度分布。又,从第1部位到安装在中空轴的下端的冷却板的热的移动量受到厚度薄的第2部位限制。因此,中空轴的下端不会过于高温,不会损坏设在该下端与冷却板之间的O环的密封性。本发明的加热装置为了控制上述陶瓷基体的温度,也可以具有测定上述陶瓷基体的中央部的温度的热电偶。由于利用由这样的热电偶测定的温度来控制陶瓷基体的温度时的温度控制性的降低是一个问题,因而将本发明应用于具有这样的热电偶的加热装置的意义较大。本发明的加热装置中,上述电阻发热体优选按其上述中央部处的发热密度为上述外周部处的发热密度的1.4~2.0倍来设置。这样一来,陶瓷基体的温度控制性将变得更加良好。本发明的加热装置中,上述第1部位的直径优选大于上述第2部位的直径。这样一来,大量的热从第1部位的表面被散热掉。由此,中空轴也不会过于高温。本发明的加热装置中,上述第1部位的厚度也可以为6~10mm。这样一来,中央部的热更加容易流出到中空轴的第1部位,结果可靠地实现了中冷型温度分布。本发明的半导体制造装置包括:上述加热装置;从上述中空轴的所述中间位置除去热的除热单元。根据本发明的半导体制造装置,能够得到由上述加热装置得到的效果。又,由于能够从中空轴的中间位置除去热,能够较容易地防止中空轴的下端的温度过于高温。在本发明的半导体制造装置中,上述除热单元既可以作为吸入上述中间位置的周围的气体的单元,也可以作为向着上述中间位置喷射冷却气体的单元。这样一来,由于将通常设在半导体制造装置的单元作为除热单元来利用,因而装置构成不会变复杂。另外,除热单元不限于此,也可以是例如与中空轴的中间位置的周围相接触地被安装的散热器。附图说明图1是加热装置10的纵截面图。图2是加热装置10的俯视图(只是电阻发热体22及端子24、25由实线表示)。图3是半导体制造装置100的概略说明图。图4是示出加热装置10的尺寸的说明图。图5是示出实验例1~6的温度控制性的图表。图6是示出实验例8~11的温度控制性的图表。【符号说明】10加热装置,20陶瓷基体,20a晶片放置面,20a中央部,20b外周部,20c厚壁部,22电阻发热体,24正极端子,25负极端子,26、27供电元件,30热电偶,40中空轴,40L下端,40M中间位置,40U上端,40a第1凸缘,40b第2凸缘,41第1部位,42第2部位,44冷却板,46O环,48电源电路,50控制器,60腔室,62供给口,64真空口,100半导体制造装置,L中空轴的全长,L1第1部位的长度,S晶片放置面,tb1第1部位的厚度,tb2第2部位的厚度具体实施方式以下参照附图对本发明的优选的实施方式进行说明。图1是加热装置10的纵截面图,图2是加热装置10的俯视图(只是电阻发热体22及端子24、25由实线表示)。加热装置10是在半导体的制造工序中作为用于加热半导体晶片的台座来利用的,包括:表面为晶片放置面S的圆盘状的陶瓷基体20;埋设在该陶瓷基体20的内部的电阻发热体22;测定陶瓷基体20的温度的热电偶30;安装在陶瓷基体20中晶片放置面S的相反侧的面上的中空轴40。陶瓷基体20是由以氮化铝或碳化硅、氮化硅、氧化铝等为代表的陶瓷材料构成的圆盘状的平板。该陶瓷基体20的厚度为例如0.5mm~30mm。又,陶瓷基体20的晶片放置面S既可以由模压加工来形成多个凹凸,也可以形成多条沟槽。陶瓷基体20有中央部20a和外周部20b。中央部20a为由与陶瓷基体20同心的圆围成的圆形区域,该区域直径约为陶瓷基体20的直径的40%。外周部20b为陶瓷基体20中的中央部20a的外侧的环状区域。另外,陶瓷基体20的晶片放置面S的相反侧的面的中央附近形成有厚壁部20c。厚壁部20c形成为圆形的台那样凸起的形状,其外径与中空轴40的第1凸缘40a的外径大致一致。该厚壁部20c的厚度与其它部分相比厚10%左右。电阻发热体22如图2所示,按如下方式来形成:从配设在陶瓷基体20的中央附近的正极端子24出发,以一笔延伸的方式在晶片放置面S的整个区域布线后,到达设在正极端子24旁边的负极端子25。两个端子24、25分别通过供电元件26、27连接到电源电路48。该电源电路48由控制器50控制。该电阻发热体22为螺旋弹簧状,设定每单位长度的圈数,使陶瓷基体20的中央部20a与外周部20b相比发热密度(每单位面积的晶片放置面的发热量)变高,具体地说变为1.4~2.0倍。又,电阻发热体22的材质可列举出例如,钼,钨或钼/钨化合物等。供电元件26、27优选为金属制,更加优选为Ni制。又,作为供电元件26、27的形状可列举出棒形、线形等。各端子24、25与各供电元件26、27的连接可应用螺丝钉、铆接、嵌合、钎焊、焊接、共晶焊接等。热电偶30测定陶瓷基体20的中央部20a的温度,被插入到设在陶瓷基体20的晶片放置面20a的相反侧的面的中央的凹部。该热电偶30将测定到的温度作为电信号输出到控制器50。控制器50调节由电源电路48向电阻发热体22供给的电量,使从热电偶30输入的温度与预先设定的目标温度之差为零。中空轴40为由与陶瓷基体20相同的陶瓷材料构成的圆筒体,与陶瓷基体20的厚壁部20c一体接合。在该中空轴40的内部配置有供电元件26、27和热电偶30等。在中空轴40中的陶瓷基体20侧的端部设有第1凸缘40a,在中空轴40中的陶瓷基体20的相反侧的端部设有第2凸缘40b。第1凸缘40a接合到陶瓷基体20的中央部20a。第2凸缘40b通过O环46密封地安装到金属铝制的冷却板44。冷却板44起到散热器的作用,内部设有使制冷剂循环的通路。中空轴40有第1部位41和第2部位42。第1部位41为从上端40U到中间位置40M的部位。该第1部位41的厚度tb1为6~10mm。第1部位41的长度L1为中空轴40的全长L的0.4~0.8倍。第2部位42为从中间位置40M到下端40L(轴末端)的部位。该第2部位42的厚度tb2为第1部位41的厚度tb1的0.3~0.5倍,换而言之,第1部位41的厚度tb1为第2部位42的厚度的2~3.3倍。另外,中空轴40被配置为:在俯视时,除了第1及第2凸缘40a、40b,都进入陶瓷基体20的中央部20a的范围。然后,对加热装置10的制造例进行说明。首先,准备作为陶瓷基体20的原料的陶瓷原料粉,将电阻发热体22及各端子24、25埋设到陶瓷原料粉中,对该陶瓷原料粉进行加压形成陶瓷成形体。接着,对该陶瓷成形体进行热压烧成形成陶瓷基体20。陶瓷基体20的直径与陶瓷成形体相同,但厚度为陶瓷成形体的一半左右。接着,从陶瓷基体20的背面向着各端子24、25开孔,使各端子24、25在孔内露出。又,在陶瓷基体20的背面中央形成用于插入热电偶30的凹部。另一方面,与陶瓷基体20相分离地制作中空轴40。首先,将与陶瓷基体同样的AlN原料粉装入到模具中,通过CIP(冷等静压制)成型,形成厚壁的圆筒型成形体。对该圆筒型成形体进行烧成,形成圆筒型烧成体。然后,通过对得到的圆筒型烧成体进行研磨,得到中空轴40。接着,使陶瓷基体20与中空轴40同轴,并且使陶瓷基体20的背面与中空轴40的第1凸缘40a相接,以该状态来接合两者。另外,接合可以是钎焊接合,也可以是固相连接,也可以是固液连接。其后,在中空轴40的内部,将各供电元件26、27连接到各端子24、25,将热电偶30的测温部插入到陶瓷基体20的凹部。最后,将中空轴40的下端通过O环46安装到冷却板44。另外,组装各供电元件26、27及热电偶30,以保持密封状态并在上下方向上贯通冷却板44。然后,对加热装置10的使用例进行说明。在此,对利用加热装置10通过等离子CVD在晶片上形成半导体薄膜的工序进行说明。加热装置10作为图3所示的半导体制造装置100的构成部件来被利用。半导体制造装置100在密闭的腔室60的内部具有加热装置10。在腔室60内装备有供给硅烷气等的原料气体的供气口62和将腔室60内的气体排出的真空口64等。真空口64设在中空轴40的中间位置40M的周边,与未图示的真空泵相连接。等离子CVD中,首先,将目标温度设定为350℃,由控制器50进行陶瓷基体20的温度控制。控制器50输入来自热电偶30的陶瓷基体20的中央部20a的温度,通过介由电源电路48调节向电阻发热体22的供电量使该温度达到目标温度,来进行陶瓷基体20的温度控制。又,从供气口62供给原料气体,并且从真空口64将腔室60内的气体排出。然后,在从热电偶30输入的温度与目标温度大致一致后,继续陶瓷基体20的温度控制,并将晶片放置到陶瓷基体20的晶片放置面S上。紧接着放置晶片后,虽然由于晶片自身的温度低于目标温度,测定温度降低数℃,但通过由控制器50进行的温度控制而再次上升到目标温度。该状态下使等离子产生,在晶片上由原料气体来形成半导体薄膜。在此,在加热装置10中,中央部20a中的发热密度为外周部20b中的发热密度的1.4~2.0倍。陶瓷基体20的温度控制中,测定陶瓷基体20的中央部20a的温度,并调节向电阻发热体22的供电量使该温度达到目标温度。在对温度进行测定的中央部20a中,由于发热密度高,当供电量增加时会迅速地随之而温度上升。因此,陶瓷基体20的温度控制性变得良好。另一方面,若电阻发热体22这样构成,本来是无法实现中冷型温度分布。然而,中央部20a中安装有其形状经过设计的中空轴40。具体地说,中空轴40的第1部位41的厚度tb1达到6~10mm(通常的轴厚为3mm左右)。这样,由于第1部位41形成足够的厚度,中央部20a的热很容易地流出到中空轴40的第1部位41,结果实现了中冷型温度分布。另外,当在等离子CVD的开始时将原料气体供给到腔室60内,中冷型温度分布大体上变成平坦的温度分布,晶片整体达到几乎相同的温度。又,第2部位42的厚度tb2为厚度tb1的0.3~0.5倍,第1部位41的长度L1达到中空轴40的全长L的0.4~0.8倍(第2部位42的长度为全长L的0.2~0.6倍)。因此,从第1部位41到冷却板44的热的移动量受到厚度薄的第2部位42限制。因此,中空轴40的下端不会变得过于高温,不损坏O环46的密封性。又,真空口64由于吸入中空轴40的中间位置40M的周围的气体,能将来自中空轴40的中间位置M的热除去。通过这点,中空轴40的下端也不会过于高温。进一步地,由于第1部位41的直径大于第2部位42的直径,因而第1部位41的表面积大于第2部位42的表面积。因此,大量的热从第1部位41的表面被散热了。通过这点,中空轴40的下端也不会过于高温。另外,若中央部20a中的发热密度不足外周部20b中的发热密度的1.4倍,由于温度控制性降低故不优选,若超过2.0倍,由于与外周部20b相比中央部20a的温度变得过高故也不优选。若第1部位41的厚度tb1不足6mm,由于无法实现中冷型温度分布故不优选,若超过10mm,由于与外周部20b相比中央部20a的温度变得过低故也不优选。第2部位42的厚度tb2不足第1部位41的厚度tb1的0.3的话,由于无法实现中冷型温度分布故不优选,若超过0.5,由于O环46过于高温故不优选。若第1部位41的长度L1不足中空轴40的全长L的0.4倍,中冷型温度分布和温度控制性都变得不充分,若超过0.8倍,由于中空轴40的下端过于高温有可能损坏O环46的密封性,故不优选。根据以上说明的本实施方式的加热装置10,能够同时做到中冷型温度分布的实现和温度控制性的提高,进而能够防止中空轴40的下端的高温化。另外,本发明不受上述的实施方式任何限定,毫无疑问,只要属于本发明的技术的范围,可以以各种的形态来实施。例如,虽然在上述的实施方式中,将真空口64设在中空轴40的中间位置40M的周边,但在将真空口64设在别的位置的情况下,也可以设置将冷却气体往中间位置M喷射的喷射口。这样一来,由于通过从喷射口喷射的冷却气体来从中间位置M除去热,因而中空轴40的下端不会过于高温。或者,也可以使中空轴40的中间位置40M的周围与散热器相接触地固定。这种情况下,由于通过散热器也能从中间位置M除去热,因而中空轴40的下端不会过于高温。在上述的实施方式中,对于使陶瓷基体20的中央部20a的发热密度与外周部20b相比增大,虽然是变更了单位长度螺旋弹簧状的电阻发热体22的圈数,但也可以不那样做,而是变更卷径或变更线间距离(相邻的螺旋弹簧的间隔)。在上述的实施方式中,虽然是在晶片放置面S的整个面内以一笔延伸的方式来形成电阻发热体22,但也可以不那样做,而是将晶片放置面S分割成多个区域,分别在各区域以一笔延伸的方式来形成。在分割成多个区域时,也可以以与陶瓷基体20同心的一个以上的圆作为边界线来分割。或者,也可以以两个以上的半径作为边界线来分割圆盘状的陶瓷基体20,在该情况下,分割成中心角为360°/n(n为2以上的整数)的扇形。在上述的实施方式中,虽然将电阻发热体22的形状做成螺旋弹簧状,但也可以不限于此,例如,可以是网状(网眼状)或膜状(片状)。在采用网状的发热体的情况下,要变更发热密度,可以例如变更网眼的大小或变更线径或变更发热体的面积,在采用膜状的发热体的情况下,要变更发热密度,可以例如变更面积。在上述的实施方式中,虽然在陶瓷基体20的晶片放置面S的相反侧的面设有厚壁部20c,但也可以不设这样的厚壁部20c而是使陶瓷基体20的厚度保持一致。在上述的实施方式中,虽然在陶瓷基体20中埋设电阻发热体22,但也可以进一步地埋设静电卡盘用的静电电极或等离子发生用的高频电极。又,也可以不埋设电阻发热体22而是将其设在陶瓷基体20的表面。在上述的实施方式中,虽然陶瓷基体20与中空轴40由相同的陶瓷材料而形成,但也可以由不同的陶瓷材料而形成。【实施例】[实验例1~11]对于各实验例,制作了如图1所示的加热装置10。各实验例的加热装置10的尺寸如图4及表1所示。以下对具体的制作次序进行说明。首先,制作AlN成形体。AlN原料粉用纯度99%的原料粉。在该AlN成形体中,以遍布AlN成形体的整个面的方式埋设由Mo制的螺旋弹簧构成的电阻发热体。此时,按如下方式来埋设电阻发热体:从中心的附近出发,以一笔延伸的方式遍布整个面地配置后,再返回到中心的附近。又,电阻发热体的一端安装正极端子,另一端安装负极端子。又,将AlN成形体的外径的40%以内的圆形区域作为AlN成形体的中央部,将中央部的外侧的环状区域作为外周部。然后,设定中央部及外周部的螺旋弹簧的单位长度的圈数,使发热密度的比率达到表1的各实验例的发热密度的比率。另外,发热密度的比率是指埋设在中央部的电阻发热体的每单位面积的发热量相对于埋设在外周部的电阻发热体的每单位面积的发热量的比率。然后,将该AlN成形体装入到烧成炉的模具,用热压法来烧成,形成陶瓷基体。烧成在约2000℃下进行。接着,从陶瓷基体的背面向着各端子开孔使各端子在孔内露出。又,在陶瓷基体的背面中央形成用于插入热电偶的凹部。另一方面,另外制作中空轴。首先,将与陶瓷基体同样的AlN原料粉装入到模具中,通过CIP(冷等静压制)来成型,得到厚壁的圆筒型成形体。将该圆筒型成形体由常压炉在约2000℃下烧成,得到圆筒型烧成体。然后,通过研磨得到的圆筒型烧成体的外表面,得到中空轴。另外,中空轴按如图4及表1所示的各实验例的尺寸来制作。接着,使陶瓷基体与中空轴同轴并且使陶瓷基体的背面与中空轴的第1凸缘相接,以该状态升温到约2000℃来接合两者(固相连接)。接合后,加工陶瓷基体的表面,使陶瓷基体达到如图3所示的尺寸。其后,将供电元件通过钎焊接合分别接合到电阻发热体的各端子,将该供电元件连接到电源电路。又,将热电偶插入并固定到设在陶瓷基体的背面中央的凹部。最后,通过O环(耐热温度200℃)在中空轴的下端安装金属铝制的冷却板。另外,组装各供电元件及热电偶以保持密封的状态并在上下方向上贯通冷却板。电源电路及热电偶连接到控制器50。控制器50进行陶瓷基体的温度控制,具体地说,输入由热电偶测定的温度,操作从电源电路向电阻发热体供给的电量,使该温度达到预先设定的目标温度。[评价]1.温度分布准备温度测定用晶片。该温度测定用晶片在直径300mm的硅晶片的中心点、直径140mm的圆周上的8个点(各点等间隔地设在圆周上)、直径280mm的圆周上的8个点(各点等间隔地设在圆周上)这合计17处埋入热电偶。将该温度测定用晶片放在晶片放置面上,设定目标温度为350℃,通过控制器进行陶瓷基体的温度控制。从开始温度控制起的15分后读取温度测定用晶片的各点的温度,将从最外周的8点的温度的平均值中减去中心点的温度得到的值作为中冷型温度分布。各实验例的中冷型温度分布如表1所示。2.温度控制性在等离子CVD工序中,设定目标温度为350℃,通过控制器进行陶瓷基体的温度控制。插入到陶瓷基体的背面中央的热电偶的测定温度达到约350℃后,继续陶瓷基体的温度控制,将硅晶片放置到晶片放置面上,通过等离子CVD在硅晶片的表面上形成半导体薄膜。完成以此时的经过时间为横轴,以热电偶的测定温度为纵轴的表示温度控制性的图表。时间计测从放置硅晶片并开始等离子CVD的时刻起开始。又,求出经过120秒后的测定温度与目标温度之差,将其作为温度控制性的指标。图5及图6中示出了表示各实验例的温度控制性的图表。又,各实验例的温度控制性的指标如表1所示。表示温度控制性的图5及图6中,任一个实验例都是,紧接着放置硅晶片之后,即在计时开始后数秒到数十秒内测定温度降低,实验例3~6、8~10在120秒后通过控制器的温度控制测定温度基本上稳定到350℃。与此相对,实验例1、2、11即使在120秒后测定温度也比350℃高出4.5~10℃。3.轴末端温度在上述“2.”的温度控制性的评价实验中测定了经过120秒后的中空轴的下端的温度(轴末端温度)。轴末端温度是通过在中空轴的最下端内周部安装热电偶来测定的。各实验例的轴末端温度如表1所示。【表1】[结果]根据实验例3~5、9、10(相当于本发明的实施例),中冷型温度分布为4~7℃,温度控制性的指标为3℃以下的上升,轴末端温度为200℃以下。即,能够同时做到中冷型温度分布的实现和温度控制性的提高,进而能够将中空轴的下端的温度控制在低于O环的耐热温度的范围内。能够得到这样的效果是由于发热密度的比率为1.4~2.0,第1部位的厚度tb1为6~10mm,第2部位的厚度tb2为3mm(tb2/tb1为0.3~0.5,tb1/tb2为2~3.3),第1部位的长度L1与中空轴的全长L的比(L1/L)为0.4~0.8。另一方面,实验例1、2、6~8、11(相当于本发明的比较例)无法完成中冷型温度分布的实现、温度控制性的提高及中空轴的下端的高温化防止中的至少一个。实验例1中,由于将发热密度的比率设定为0.6因而温度控制性降低。实验例2中,由于将发热密度的比率设定为1.0因而无法实现中冷型温度分布。实验例6将实验例3的L1/L设定为1.0。该实验例6中虽然能够同时做到中冷型温度分布的实现和温度控制性的提高,但中空轴的下端的温度超过了200℃。实验例7中,由于将发热密度的比率设定为2.4,将tb2/tb1设定为0.2,因而在制造过程中发生了破损。实验例8将实验例9、10的L1/L设定为1.0。该实验例8中虽然能够同时做到中冷型温度分布的实现和温度控制性的提高,但中空轴的下端的温度超过200℃。实验例11将实验例5的L1/L设定为0.2。该实验例11中,无法充分实现中冷型温度分布,温度控制性没有提高。