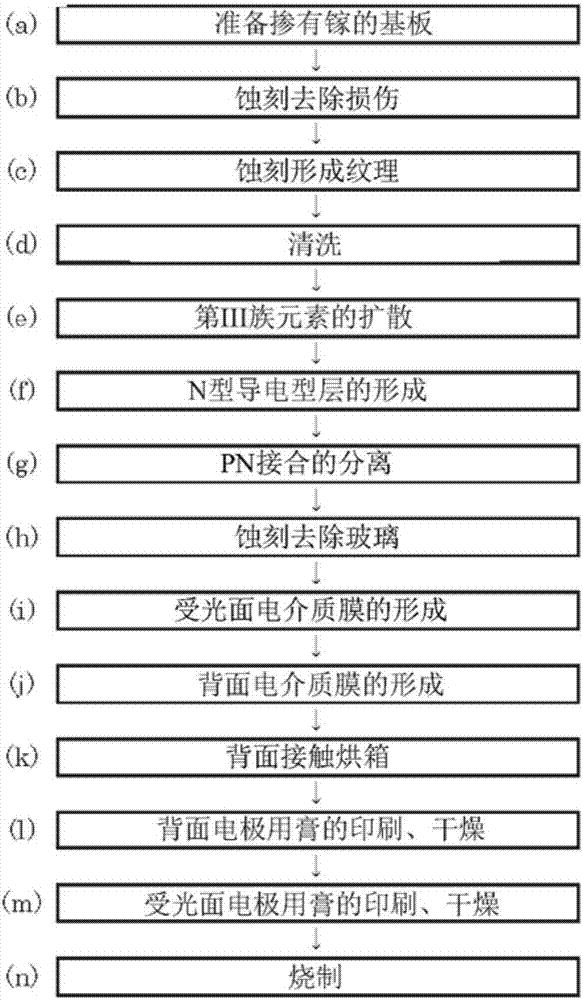
本发明涉及一种太阳能电池及其制造方法。
背景技术:
:太阳能电池用半导体基板通常利用提拉法(czochraskimethod,cz法)制造,所述cz法可以用相对低的成本来制造大直径的单晶。例如,根据利用cz法制作掺有硼的硅单晶,并将此单晶切成薄片,可以获得p型半导体基板。如此获得的掺有硼的硅基板存在以下问题:由于基板中存在的硼与氧所造成的影响,当太阳能电池受到强光照射后,寿命会下降并产生光劣化。为了解决此种光劣化的问题,在专利文献1中,提出使用镓来代替硼作为p型掺杂剂。此处,作为太阳能电池的背面结构,可以列举具有背面场(backsurfacefield,bsf)区域的结构。根据将铝浆印刷到基板的背面的几乎整个区域并进行烧制,可以在背面的几乎整个面提供bsf区域。此外,为了进一步提高效率,还有以下结构,所述结构使基板与背面的电极的接触区域为部分区域,并利用作为钝化膜发挥作用的电介质膜(dielectricfilm)来保护大部分的背面。这些太阳能电池结构被称作钝化发射极背面接触太阳能电池(passivatedemitterandrearcontactsolarcell,perc)结构、钝化发射极背面局部扩散太阳能电池(passivatedemitterandrearlocallydiffusedsolarcell,perl)结构。图6为示意性地表示以往的具有perl结构的太阳能电池的剖面图。如图6所示,太阳能电池110在p型硅基板111的受光面侧具备n型导电型层(发射极层)112。在此n型导电型层112上具备受光面电极116。多数情况下,受光面上设置有抗反射膜114。另外,在背面上具备起到钝化膜或者保护膜作用的电介质膜115。另外,在背面上具备背面电极117。在背面电极117与p型硅基板111接触的接触区域上具备bsf层113。现有技术文献专利文献专利文献1:国际公开第wo2000/073542号说明书。技术实现要素:发明所要解决的问题在制造上述具有perc结构或者perl结构等结构的太阳能电池的过程中,存在下述问题:在背面形成电介质膜时,尤其是当使用掺有镓的硅基板(以下也记载为掺镓基板)时,掺杂的镓原子扩散到电介质膜侧,从而导致基板侧的背面的镓(p型掺杂剂)的表面浓度下降。如上所述,如果基板侧的背面的镓的表面浓度下降,则会导致以下问题:i)接触电阻增大;ii)当形成具有正电荷的电介质膜时,如图6所示,在基板背面形成反转层118,在触点附近(接触区域)产生泄露电流,太阳能电池的特性会大幅度下降。本发明是鉴于上述问题而完成,其目的在于,提供一种太阳能电池及其制造方法,所述太阳能电池具备掺镓基板且转换效率优异。解决问题的技术方案为了实现上述目的,本发明提供一种太阳能电池,所述太阳能电池具备p型硅基板,所述p型硅基板以一个主表面为受光面并以另一个主表面为背面,在所述背面上具备电介质膜,并且,所述p型硅基板在所述受光面的至少一部分具有n型导电型层,所述太阳能电池的特征在于,所述p型硅基板为掺有镓的硅基板,在所述p型硅基板的所述背面含有扩散的第iii族元素。如果为此种太阳能电池,由于在基板的背面含有扩散的第iii族元素,因此即使在掺有镓的基板的背面上形成电介质膜,在基板背面的p型掺杂剂的浓度也很充分。由此,可以防止接触电阻增大及在接触点附近产生泄露电流等,可以制成转换效率较高的太阳能电池。另外,优选为,所述背面中的所述第iii族元素的扩散表面浓度为5.0×1017atom/cm3以上且2.0×1019atom/cm3以下。如果为第iii族元素以此种浓度在背面表面扩散而成的太阳能电池,可以抑制背面中的p型掺杂剂的浓度下降,并且抑制电池特性变差。另外,优选为,所述第iii族元素为硼、镓或者铝。本发明的太阳能电池的基板背面所含有的元素特别优选为这些。本发明还提供一种太阳能电池的制造方法,其制造一种具备p型硅基板的太阳能电池,所述p型硅基板的一个主表面为受光面且另一个主表面为背面,所述制造方法的特征在于,具有以下步骤:准备同样掺有镓的硅基板作为所述p型硅基板;使第iii族元素在所述背面扩散;在所述受光面形成n型导电型层;及,在所述背面上形成电介质膜。如果为此种太阳能电池的制造方法,可以向背面导入第iii族元素扩散而成的p-层,根据补偿p型掺杂剂量,即使在掺镓基板的背面形成电介质膜作为保护膜等,也可以防止与该电介质膜接触的基板背面的表面附近的p型掺杂剂的浓度下降。结果,可以避免泄露电流引起的电压降低,可以维持高效率。另外,优选为,利用一次热处理来进行所述第iii族元素的扩散及所述n型导电型层的形成。如果为此种太阳能电池的制造方法,可以利用低成本容易地形成含有第iii族元素的层。发明的效果如果为本发明的太阳能电池,由于在基板的背面含有扩散的第iii族元素,因此即便在掺镓基板的背面上形成电介质膜,在基板背面的p型掺杂剂的浓度也很充分。另外,如果为本发明的太阳能电池的制造方法,根据向背面导入硼等第iii族元素来补偿p型掺杂剂量,即使在掺镓基板的背面形成电介质膜作为保护膜等,也可以防止与该电介质膜接触的基板背面的表面附近的p型掺杂剂的浓度下降。结果,可以避免泄露电流引起的电压降低,可以维持高效率。附图说明图1是表示本发明的太阳能电池的一个实例的剖面图。图2是表示本发明的太阳能电池的制造方法的一个实例的流程图。图3是表示利用二次离子质量分析(secondaryionmassspectroscopy,sims)获得的实施例2的扩散轮廓的图。图4是表示实施例1及比较例的内部量子效率的图。图5是概念性地表示图1及图6的虚线所表示的横截面的能带图的图。图6是示意性地表示以往的具有perl结构的太阳能电池的剖面图。具体实施方式以下,更详细地说明本发明。如上所述,需要一种具备掺镓基板且转换效率优异的太阳能电池及其制造方法。但是,当使用掺镓基板作为太阳能电池用基板时,存在以下问题:如果在基板表面形成电介质膜作为保护膜或钝化膜,如上所述,在与该电介质膜接触的区域及其附近,掺杂剂也就是镓的量减少等。本发明人进行了潜心研究以解决上述问题。结果发现,以下太阳能电池可以解决上述问题,所述太阳能电池在掺镓基板的背面上具备电介质膜,并含有扩散至此基板的背面的第iii族元素,从而完成了本发明的太阳能电池及其制造方法。以下,参照附图具体地对本发明的实施方式进行说明,但本发明并不限定于这些。图1是表示本发明的太阳能电池的一个实例的剖面图。如图1所示,本发明的太阳能电池10具备p型硅基板11,所述p型硅基板以一个主表面为受光面并以另一个主表面为背面。此p型硅基板11为掺镓硅基板,在背面上具备电介质膜(背面电介质膜)15。另外,p型硅基板11在受光面的至少一部分具有n型导电型层12。此处,掺有镓的p型硅基板11的电阻率并无特别限定,可以设为例如0.1~5ω·cm的范围内。p型硅基板11的厚度也无特别限定,可以设为例如100~200μm的厚度。p型硅基板11的主面的形状及面积并无特别限定。如图1所示,背面上通常具有背面电极17。背面电极17如图1所示,可以将背面电介质膜15的一部分开口而使所述背面电极17与p型硅基板11的背面接合。在n型导电型层12上通常具备受光面电极16。另外,在受光面上可以设置作为抗反射膜等发挥作用的受光面电介质膜14。在背面电极17与p型硅基板11接触的接触区域可以设置bsf层13。此时,形成具有perl结构的太阳能电池。也可以不设置bsf层13而制成具有perc结构的太阳能电池。此处,所谓具有perc结构的太阳能电池,是指具备局部地形成于基板背面上的背面电极,并具有p型硅基板与背面电极接触的接触区域的太阳能电池。所谓具有perl结构的太阳能电池,是指此接触区域中的p型掺杂剂的浓度高于接触区域以外的区域中的p型掺杂剂的浓度的太阳能电池。这些时候,背面电极17与p型硅基板11直接接合的区域的间距可以设为例如1mm以上且10mm以下。如上所述,受光面电介质膜可以作为抗反射膜发挥作用。另外,也可以作为钝化膜、保护膜发挥作用。背面电介质膜可以作为钝化膜、保护膜发挥作用。作为这些电介质膜,可以使用sinx膜(硅氮化膜)和sio2膜等,所述sinx膜(硅氮化膜)和sio2膜等可以使用等离子化学气相沉积(chemicalvapordeposition,cvd)装置形成,也可以使用热氧化膜。作为抗反射膜,电介质膜的膜厚优选为反射率降低效果最大的85~105nm。此处,在本发明中,p型硅基板11为掺有镓的硅基板。另外,在p型硅基板11的背面含有扩散的第iii族元素(13族元素)。图1中以参照编号19示出扩散有第iii族元素的层。此处,作为n型导电型层12所含的n型掺杂剂,可以列举:p(磷)、sb(锑)、as(砷)、bi(铋)等。作为扩散的第iii族元素,可以列举:b(硼)、ga(镓)、al(铝)、in(铟)等。第iii族元素优选为硼、镓或者铝。另外,背面中的第iii族元素的扩散表面浓度并无特别限定。扩散表面浓度可以设为例如1.0×1015atom/cm3以上且1.0×1020atom/cm3以下。优选为5.0×1017atom/cm3以上且2.0×1019atom/cm3以下。如果扩散表面浓度为5.0×1017atom/cm3以上,可以充分抑制背面中的p型掺杂剂的浓度下降。如果为2.0×1019atom/cm3以下,可以在不降低电压、不降低转换效率的情况下,降低电池特性的恶化。此外,此处所说的扩散表面浓度是指背面的追加掺杂的第iii族元素的浓度,并不包含原本含有的镓的浓度。只要在背面侧的特定厚度中满足此扩散表面浓度的规定即可。所谓特定厚度,可以设为0.1μm。更优选为至0.5μm的深度为止满足此规定。第iii族元素的背面的扩散深度并无特别限定。扩散深度可以设为例如0.1μm~3μm的范围内。使第iii族元素扩散的面积并无特别限定。但是,理想为使第iii族元素在背面的整个区域扩散,以充分抑制背面中的p型掺杂剂的浓度下降。n型导电型层12中的n型掺杂剂的浓度并无特别限定。此浓度可以设为例如1.0×1018atom/cm3以上且1.0×1020atom/cm3以下。n型导电型层12也可以形成于受光面的整个区域。n型导电型层12的形状可以配合受光面电极16的形状适当变更。接着,参照图2对本发明的太阳能电池的制造方法进行说明。图2是表示本发明的太阳能电池的制造方法的一个实例的流程图。以下说明的方法为典型例,本发明并不限定于此。首先,如图2(a)所示,准备同样掺有镓的硅基板作为一个主表面为受光面,另一个主表面为背面的p型硅基板。此外,同样掺有镓的硅基板是指像从利用cz法制造的硅单晶切出的基板那样,在基板的整个区域(厚度方向及长度方向)均匀地掺有p型掺杂剂也就是镓的硅基板。其中,同样掺有镓的硅基板也可以具有由偏析等引起的固有的若干浓度分布。切出掺镓基板的硅单晶,例如可以如上所述使用cz法来制造。此时,只要将镓与多晶原料一起放入坩埚中并作成原料熔液即可。尤其是量产时需要精细的浓度调整,因此理想为先制作高浓度的掺镓硅单晶,然后将其细细粉碎而制作掺杂剂,并以成为所需浓度的方式将所述掺杂剂投入将多晶硅熔融后的融液中。根据将如此地获得的掺有镓的硅单晶切成薄片,可以获得掺镓基板。接着,如图2(b)所示,可以使用浓度5~60%的氢氧化钠或氢氧化钾之类的高浓度的碱或者氟酸与硝酸的混酸等,蚀刻去除基板表面的切片损伤。紧接着,如图2(c)所示,可以在基板表面形成被称作纹理的微小凹凸。纹理是用于降低太阳能电池的反射率的有效方法。利用在加热过的氢氧化钠、氢氧化钾、碳酸钾、碳酸钠、碳酸氢钠等碱溶液(浓度1~10%,温度60~100℃)中浸渍10分钟至30分钟左右来制作纹理。多数情况下,在上述溶液中溶解特定量的2-丙醇(ipa:异丙醇),以在面内均匀地形成纹理。蚀刻去除损伤及形成纹理后,优选为如图2(d)所示地清洗基板。清洗可以在例如盐酸、硫酸、硝酸、氟酸等或者这些的混合液的酸性水溶液中进行,或者使用纯水进行。接着,如图2(e)所示,使第iii族元素在掺镓基板的背面扩散。另外,如图2(f)所示,在掺镓基板的受光面形成n型导电型层。进行步骤(e)及步骤(f)的顺序并无特别限定,另外,如下所示,也可以同时进行步骤(e)及步骤(f)。在步骤(e)中使第iii族元素扩散的方法及在步骤(f)中形成n型导电型层的方法,并无特别限定。可以列举例如使掺杂剂热扩散的方法。此时,可以使用气相扩散法和涂布扩散法等,所述气相扩散法为将pocl3(氧氯化磷)或bbr3(三溴化硼)等与载气一起导入至热处理炉内进行扩散,所述涂布扩散法为将含有磷或硼的材料涂布至基板上后进行热处理。作为涂布扩散法中的涂布方法,可以列举:旋转涂布法、喷雾涂布法、喷墨法、丝网印刷法等。当使用涂布扩散法时,根据先在背面涂布含有第iii族元素的材料后进行热处理,可以进行第iii族元素的扩散。另外,根据在受光面涂布含有n型掺杂剂的材料后进行热处理,可以形成n型导电型层。此外,理想为在背面整个区域涂布含有第iii族元素的材料,以充分抑制背面中的p型掺杂剂的浓度下降。此时,优选为同时进行步骤(e)及步骤(f),即利用一次热处理来扩散第iii族元素及形成n型导电型层。如果为此种方法,在背面导入p型层时,可以减少制造步骤数,工序不会费工夫,可以削减成本。如此地,根据同时进行步骤(e)及步骤(f),可以在背面容易地导入所需表面浓度的p型层。当同时进行步骤(e)及步骤(f)时,例如,首先,利用在受光面涂布含有n型掺杂剂的材料,并将基板投入到干燥炉中使材料干燥,形成含有n型掺杂剂的膜,接着,利用同样的方法在背面形成含有第iii族元素的膜。然后,实施热处理,可以利用一次热处理同时扩散第iii族元素及形成n型导电型层。此外,也可以利用涂布扩散法进行扩散第iii族元素及形成n型导电型层中的任一个,利用气相扩散法进行另一个。此处,作为含有n型掺杂剂的材料,可以使用根据热处理而玻璃化的磷扩散剂(磷扩散源)。此磷扩散剂可以使用公知的磷扩散剂,也可以根据将例如p2o5、纯水、聚乙烯醇(polyvinylalcohol,pva)、原硅酸四乙酯(tetraethylorthosilicate,teos)混合来获得。作为含有第iii族元素的材料,可以使用根据热处理而玻璃化的硼扩散剂(硼扩散源)。此硼扩散剂可以使用公知的硼扩散剂,也可以根据将例如b2o3、纯水、pva混合来获得。在基板的受光面涂布上述磷扩散剂,在背面涂布上述硼扩散剂,如果能以磷扩散温度进行同时扩散,由于硼原子比磷原子扩散系数小,因此可以形成表面浓度相对低的硼层。由此,与分别形成硼层与磷扩散层的方法相比,可以削减成本。此外,磷扩散温度并无特别限定,通常为830~950℃的范围内。硼扩散温度通常为900~1100℃的范围内。这些热处理时间通常为1~60分钟左右。根据对例如硼扩散剂中的b2o3的含量、热处理温度、热处理时间等进行调整,可以使第iii族元素的扩散表面浓度和扩散深度成为符合目的又适当的值。接着,如图2(g)所示,使用等离子蚀刻器来进行pn接合的分离。在此工序中堆叠样品以使等离子和自由基不会侵入到受光面和背面,在此状态下,将端面削去数微米。此利用等离子蚀刻而实行的pn接合的分离,可以在去除硼玻璃及磷玻璃前进行,也可以在去除后进行。作为pn接合的分离的代替方法,也可以利用激光形成槽。进行上述步骤(e)及步骤(f)后,在基板的表面形成相当多的玻璃层。因此,如图2(h)所示,利用氟酸等来去除表面的玻璃。接着,如图2(i)所示,可以在掺镓基板的受光面上形成电介质膜。作为电介质膜,可以使用与上述太阳能电池的项中记载相同的电介质膜。接着,如图2(j)所示,在掺镓基板的背面上形成电介质膜。作为电介质膜,可以使用与上述太阳能电池的项中记载相同的电介质膜。如果为本发明的太阳能电池的制造方法,由于在步骤(e)中使第iii族元素在基板的背面扩散,因此当形成硅氮化膜等具有正电荷的电介质膜时,可以防止在基板背面的表面区域形成反转层。步骤(i)与(j)可以颠倒顺序,也可以同时进行。接着,如图2(k)所示,仅在形成背面电极的部分去除电介质膜。可以使用例如光刻法和激光烧蚀法、蚀刻膏等去除电介质膜。此蚀刻膏含有例如选自由磷酸、氟化氢、氟化铵及氟化氢铵组成的群中的至少1种作为蚀刻成分,并含有水、有机溶剂及增粘剂。另外,即使不特意去除电介质膜,在利用丝网印刷等在此区域形成后述具有烧成贯通(fire-through)性能的电极的过程中,也可以根据利用烧制贯穿电介质膜来形成该结构。接着,如图2(l)所示,在掺镓基板的背面上印刷背面电极用膏并进行干燥。例如,对上述基板的背面进行丝网印刷下述膏,所述膏是在有机物粘合剂中混合al粉末而成。背面电极材料也可以使用ag等。接着,如图2(m)所示,在掺镓基板的受光面上印刷受光面电极用膏并进行干燥。例如,对上述基板的受光面进行丝网印刷将ag粉末和玻璃料与有机物粘合剂混合而成的ag膏。也可以颠倒步骤(l)与步骤(m)的顺序。进行以上电极印刷后,如图2(n)所示,烧制受光面电极用膏及背面电极用膏。如此地,利用印刷膏后进行烧制,形成受光面电极及背面电极。通常利用以700~800℃的温度进行5~30分钟热处理来进行烧制。根据此热处理使ag粉末贯穿至受光面侧的电介质膜(烧成贯通),导通受光面电极与掺镓基板。背面电极及受光面电极的烧制也可以分别进行。如此地,可以制作图1所示的太阳能电池。本发明的太阳能电池的制造方法具有下述主要特征,所述主要特征为使用掺镓基板及在形成电介质膜前使第iii族元素扩散至背面,从而可以应用于各种太阳能电池的制造方法。实施例以下,示出实施例及比较例更具体地说明本发明,但本发明并不限定于此实施例。(实施例1)首先,准备厚度200μm、基板电阻率1ω·cm的156mm见方的像切片一样的cz基板作为同样掺有镓的硅基板(图2(a))。接着,使此掺镓基板在硝酸氢氟酸溶液中浸渍15秒来蚀刻去除损伤,(图2(b))。进一步,在含有2%的koh与2%的ipa的70℃的水溶液中进行5分钟化学蚀刻(图2(c))。然后利用纯水进行清洗并干燥,由此在掺镓基板的受光面形成纹理结构(图2(d))。接着,使用旋转涂布法在背面涂布含有硼酸的硼扩散剂后,投入到干燥炉中,以120℃干燥1分钟左右,在背面整个区域形成含硼膜。接着,将形成有含硼膜的掺镓基板投入到热处理炉中,以温度850℃、热处理时间40分钟进行热处理,使第iii族元素扩散至掺镓基板的背面(图2(e))。此时,以硼涂布面为外侧的方式在石英舟的一槽中放置两片,尽量在未涂布硼的面上实施以使硼扩散层不会成长。接着,在氧氯化磷环境下,以850℃对掺镓基板热处理30分钟,在受光面形成n型导电型层(图2(f))。此时,根据将硼扩散面彼此重合,并插入至石英舟的一槽中来进行扩散,尽可能防止磷扩散至硼扩散层。接着,使用等离子蚀刻器来实行pn接合的分离(图2(g))。然后,将残存于上述基板表面上的扩散玻璃在25%氟酸水溶液中浸渍5分钟,然后根据利用纯水进行5分钟冲洗来去除(图2(h))。接着,将实施过扩散的本掺镓基板放到氧化炉中,以900℃在氧环境下热处理30分钟,在基板两面形成膜厚20nm的氧化膜作为电介质膜。进一步,分别使用等离子cvd装置,在掺镓基板的受光面上及背面上形成硅氮化膜作为电介质膜(图2(i)、图2(j))。受光面侧的电介质膜的膜厚设为90nm。另外,背面侧的电介质膜的膜厚也设为90nm。此时刻,利用氟酸蚀刻氧化膜并测定表面电阻的结果为250ω/□,由此推测表面浓度为约1.5×1018atom/cm3。接着,使用蚀刻膏仅在背面侧的形成背面电极的部分去除电介质膜(第2(k)图)。接着,利用丝网印刷法在掺镓基板的背面上印刷以银为主成分的导电性膏,并以150℃进行干燥(图2(l))。接着,利用丝网印刷法也在掺镓基板的受光面上印刷以银为主成分的导电性膏,并以150℃进行干燥(图2(m))。将此已经涂布导电性膏的基板投入至烧制炉中,以最高温度800℃对导电性膏烧制5秒,形成背面电极及受光面电极,制作图1所示的太阳能电池(图2(n))。(实施例2)除同时处理图2的(e)(f)所示的步骤以外,进行与实施例1相同的处理制作图1所示的太阳能电池。也就是在本步骤中,首先,使用旋转涂布法在背面涂布含有硼酸的硼扩散剂,然后以120℃在热板上干燥1分钟左右,在背面的整个区域形成含硼膜,紧接着,使用旋转涂布法在表面涂布含有磷酸的磷扩散剂后,以150℃在热板上干燥1分钟左右,在表面的整个区域形成含磷膜。接着,将此基板投入至炉中后以850℃进行30分钟热处理,同时在表面形成n型导电型层,在背面形成p型导电型层。此时,根据将硼涂布面彼此或者磷扩散面彼此重合,并插入至石英舟的一槽中,来进行扩散,尽可能防止硼与磷相互扩散。图3是表示表示利用sims(二次离子质量分析)获得的实施例2的扩散轮廓的图。此外,其对步骤(h)后的时刻的基板进行测定。可知如图3所示,与制作意图相同,硼在掺镓基板的背面扩散,磷在受光面扩散。(比较例)除了不进行图2的(e)所示的步骤(在掺镓基板的背面形成含硼膜,使第iii族元素扩散的步骤)以外,进行与实施例一样的处理来制作图6所示的太阳能电池。利用太阳模拟器(25℃的环境中,照射强度:1kw/m2,光谱:am1.5global)对如此制作的太阳能电池共300片(实施例1:100片,实施例2:100片,比较例:100片)进行评价(电流电压特性检查)。表1示出实施例1、2及比较例的结果。表1中的转换效率等是表示实施例1、2、比较例各自的各100片太阳能电池的平均值。[表1]短路电流密度开放电压填充因子转换效率实施例139.5ma/cm2653mv0.78820.3%实施例239.1ma/cm2651mv0.79220.2%比较例37.9ma/cm2651mv0.76618.9%如表1所示,使第iii族元素在掺镓基板的背面扩散的实施例1及2,短路电流密度、开放电压、填充因子(fillfactor)、转换效率均显示良好的结果。另一方面,未使第iii族元素在基板的背面扩散的比较例,如图6所示,在基板背面形成反转层118,短路电流密度等的结果变差。图4是示出实施例1及比较例的内部量子效率的图。根据分光感度测定装置测定图4中的内部量子效率。如图4所示,实施例1与比较例相比,尤其是在波长800nm~1100nm中,内部量子效率良好。此外,实施例2的内部量子效率与实施例1的内部量子效率几乎相同。图5是概念性地表示图1(实施例的结构)及图6(比较例的结构)的以虚线表示的横截面的能带图的图。如图5所示,在使第iii族元素扩散的实施例中,由于背面侧的p型掺杂剂的浓度高于基板内部的p型掺杂剂的浓度,因此背面侧的导带的下端变得高于基板内部的导带。由此,防止载子在背面侧再结合。另一方面,在未使第iii族元素扩散的比较例中,由于背面侧的p型掺杂剂的浓度低于基板内部的p型掺杂剂的浓度,因此导带的下端变低。因此,载子在背面侧再结合。由此,转换效率等变差。此外,本发明并不限定于上述实施方式。上述实施方式为示例,具有本发明的权利要求书所记载的技术思想实质相同的构成,发挥相同作业效果的一切技术方案均包含在本发明的技术范围内。当前第1页12