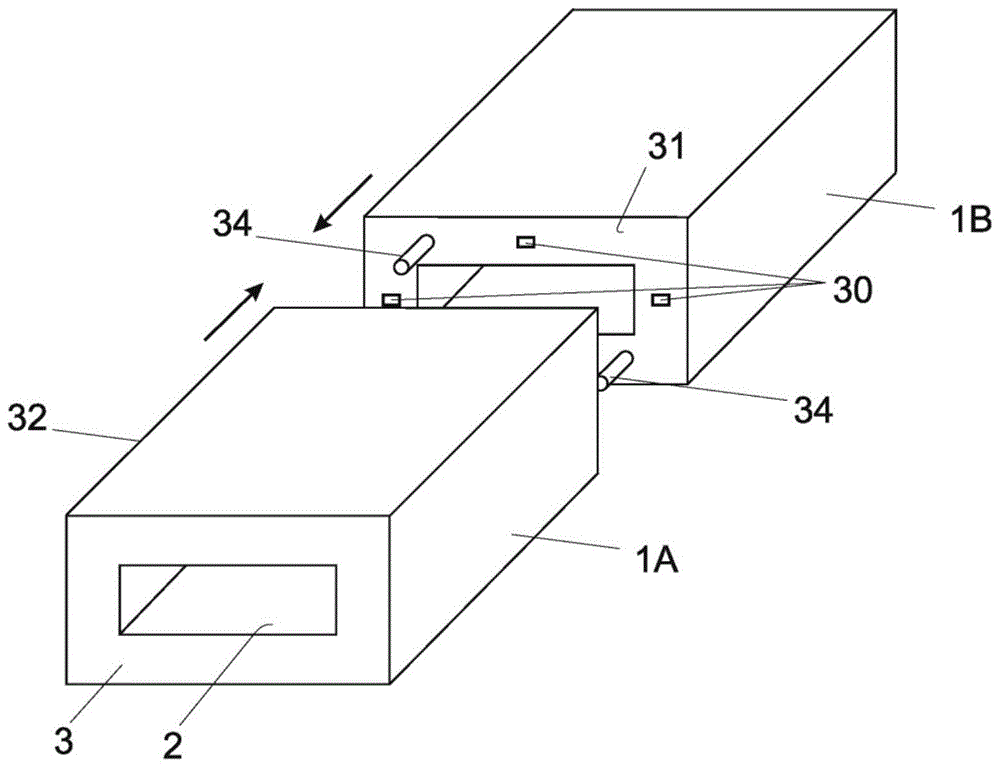
本发明涉及用于无源射频设备的增材制造的方法以及根据该方法所制造的无源射频设备。
背景技术:
:无源射频设备用于在不使用有源电子部件的情况下传播或操纵射频信号。无源射频设备例如包括基于中空金属通道中的波的引导的无源波导、滤波器、天线、模式转换器等。这些设备可以用于信号路由、频率滤波、信号分离或重组、在自由空间中或从自由空间的信号发送或接收等。作为示例,传统的无源射频设备包括由中空管形成的波导,其形状和比例确定给定电磁信号波长的传播特性。用于射频信号的传统波导具有矩形或圆形截面的内部孔。它们使得可以沿其截面传播对应于不同电磁场分布的电磁模式。在所示的示例中,波导具有沿轴y的高度b和沿轴z的宽度a。射频设备通常在户外使用,例如在航空航天(飞机、直升机、无人机)中以装备太空中的航天器、在海上的船上或在潜艇上、在沙漠中或在高山上运动的车辆上,每次都是在恶劣的甚至是极端的条件下。在这些环境中,射频设备尤其暴露于:-极端压力以及引起反复热冲击的变化很大的温度;-机械应力,波导被结合在经受冲击、振动和负荷的车辆中,所述冲击、振动和负荷会影响波导;-恶劣天气和环境条件,其中配备有波导的车辆到处(刮风、结冰、潮湿、沙地、盐地、真菌/细菌)运动。为了处理这些限制,已知通过组装先前加工的金属板来形成波导,这使得可以制造适于在恶劣环境中到处运动的波导。另一方面,这些波导的制造通常是困难的,昂贵的并且难以适应轻的但具有复杂形状的波导的制造。us2012/0033931a1描述了由具有u形截面的部件和覆盖该部件的盖形成的波导。这两个构件被组装并焊接在一起。最近的著作已经证明了使用增材制造方法例如通过3d打印来生产包括天线、波导、滤波器、转换器等的无源射频设备的可能性。特别公知的是包括例如聚合物或陶瓷的非导电材料以及导电金属的波导的增材制造。特别提出了包括通过增材方法制造然后通过金属镀层覆盖的陶瓷或聚合物壁的波导。实际上,波导的内表面必须是导电的才能进行工作。非导电芯的使用使得一方面可以减轻设备的重量和成本,另一方面可以实现适合于聚合物或陶瓷的3d打印方法并且使得能够生成具有低粗糙度的高精度部件。作为示例,mariod’auria等人的文章“3-dprintedmetal-piperectangularwaveguides”,2015年8月21日,ieeetransactionsoncomponents,packagingandmanufacturingtechnologies,第5卷第9期,1339-1349页,在第iii部分中描述了一种通过熔融沉积建模(fdm)来制造波导芯的方法。波导1例如通过增材制造来生产并且包括例如通过立体光刻、通过选择性激光熔化、通过选择性激光烧结或通过另外的增材方法制造的非导电芯。该芯通常包括用于传播射频信号的内部孔。围绕孔的芯的内壁可以涂覆有导电涂层,例如金属镀层。无源射频设备的增材制造使得可以生产难以或甚至不可能通过机械加工生产的复杂形状的设备。然而,增材制造确实具有其自身的限制并且不允许制造某些形状或大尺寸的部件。而且,难以在凹陷部件内部,例如在波导通道内部执行制造后的再加工操作,例如清洁、抛光、钻孔等。us2012/0084968a1描述了一种用于在通过3d打印生产然后在组装之前用金属涂层的多个部件中制造无源波导的方法。多个部件中的制造使得该方法更加灵活,并且使得可以生产在单个操作中不可能打印的复杂形式的部件。然而,该方法产生了在用金属涂层的不同部件之间的接合处的金属层的不连续性,其干扰了信号在波导中的传输。而且,难以保证不同部件的准确调整,并且几乎不能通过抛光或调整通常太薄的金属层来改善。技术实现要素:本发明的一个目的是提出一种免受已知设备的限制或使已知设备的限制最小化的无源射频设备。本发明的一个目的特别是提供一种通过增材制造来生产的无源射频设备,例如波导。根据本发明,这些目的特别地借助于无源射频设备来实现,该无源射频设备包括:-芯,其通过将若干个部件彼此直接接触地组装而形成,所述部件中的至少一个部件包括用于胶合剂的壳体,所述部件中至少一些部件通过增材制造来分别制造;-导电金属护套,其在不使所述部件彼此分离的情况下围绕所述芯。该设备提供了可以在部件的组装之后沉积的导电护套的优点,这保证了导电层不存在不连续性。形成芯的部件的胶合保证了其刚性固定。用于胶合剂的壳体的存在使得可以避免在组装的部件的主表面之间存在胶膜,这保证了准确的并且与胶膜的厚度或平坦度无关的相对定位。壳体可以由圆形、方形或矩形截面的凹口、凹槽或盲孔构成,以在意在组装期间被放置成与另一部件接触的部件的表面上形成凹腔。可以借助填充有金属或陶瓷颗粒的胶合剂将部件胶合在一起以便于组装。形成芯的不同部件可以使用至少一个螺钉或销来彼此对齐。一个或多个销可以与在组装期间要被放置成与另一部件接触的部件的表面呈直角地延伸,并且可以被插入设置在所组装的部件的相应表面中的盲孔中。一个或多个销可以是金属的或由其他材料制成。它们可以在增材制造之后被穿凿到部件中。形成芯的不同部件可以使用至少一个螺钉被固定到一起。一个或多个螺钉可以是金属的或由其他材料制成。螺钉可以在组装期间被插入。螺钉可以在胶合剂的硬化之后并且在导电护套的沉积之前被移除。这使得可以避免将导电层沉积在螺钉头上,因此保证导电护套的较好的平坦度。形成芯的不同部件可以被焊接在一起。形成芯的不同部件可以例如通过在组装之后结束其硬化来被熔融而不在它们之间增加材料。例如,在通过3d聚合物打印生产的部件的情况下,部件可以在其组装之后通过热或uv硬化而被接合。在一个实施方式中,导电金属护套无间断地覆盖芯的所有表面。在另一实施方式中,该设备包括设置有具有外表面和内表面的侧壁的波导,所述内表面限定通道,所述导电护套覆盖所述内表面但并未覆盖所有外表面。导电金属层的厚度有利地至少等于趋肤深度δ的五倍,优选地至少为趋肤深度δ的二十倍。该显著的厚度对于信号传输不是必需的,但是有助于设备的刚度,因此通过金属护套保证了所述刚度,尽管由多个部件制成的芯与整体芯相比可能不太坚硬。趋肤深度δ(δ)被定义为:其中μ(μ)是电镀金属的磁导率,f是要发送信号的射频并且σ(ρ)是电镀金属的电导率。直观地,它是在给定频率下电流被汇聚在导体中的区域的厚度。该解决方案提供了优于提供通过增材制造组装的波导的现有技术的以下特定优点:其对于它们被暴露于的应力(热、机械、气象和环境应力)具有更强的抗力。在根据现有方法的通过增材制造所组装的射频设备中,结构、机械、热和化学性质主要取决于芯的性质。通常,已知其中沉积在芯上的导电层非常薄,小于形成导电层的金属的趋肤深度的波导。因此,通常被接受的是,为了改善波导的结构和机械性能,必须增加芯的厚度和/或刚度。还被接受的是,必须减小导电表层的厚度以使结构减轻。通过增加导电层的厚度以使后者达到至少等于导电层金属的趋肤深度δ的五倍,优选地至少等于该深度的二十倍的厚度,波导的结构、机械、热和化学性质大部分地,甚至几乎完全地取决于导电层。即使导电层的厚度保持显著小于芯的厚度,也会观察到该不期望的特性。该实施方式使得可以减少甚至消除导电表面的粗糙度。这也使得可以增强设备的抗拉强度、抗扭强度、抗弯强度,例如波导的刚度。形成芯的至少两个不同部件可以在平面上彼此分离。这有助于通过制造两个平面表面来准确调整两个部件。形成芯的至少两个不同部件可以沿着非平面表面彼此分离。该表面可以例如用于例如使用榫眼型组装将两个部件固定在一起。芯的两个部件之间的分离平面可以与信号传播方向呈直角。因此例如可以从若干个连续的线性段来制造细长的波导。芯的两个部件之间的分离平面可以与信号传播方向平行。该设备可以包括平滑层,其意在至少部分地平滑芯的表面的不平整。导电护套沉积在平滑层之上。在芯的增材制造结束时,已经观察到增材制造工艺产生很大的粗糙度(例如凹陷和凸起),特别是在芯的边缘和表面上,特别是在有角度的边缘上。这些凹陷和凸起可以表现为阶梯式纹路的形式,每个纹路代表在增材制造中添加了一层非导电材料。已经观察到,在用薄导电层覆盖芯之后,芯的粗糙度仍然存在,使得用金属涂层之后的表面仍然表现出干扰rf信号传输的粗糙度。在这种情况下,在芯与导电层之间添加平滑层使得可以减少甚至消除这种粗糙度,其改善了rf信号的传输。平滑层可以由导电或非导电材料制成。该平滑层的厚度优选地在5到500微米之间,优选地在10到150微米之间,优选地在20到150微米之间。在通过立体光刻、通过选择性激光熔化或通过选择性激光烧结来制造芯的情况下,该厚度使得可以有效地平滑由于印刷方法而导致的表面不平整。平滑层的厚度优选地大于或等于芯的粗糙度(ra)。平滑层的厚度优选地大于或等于芯制造方法的分辨率。在平滑层包括弱导电材料例如镍的情况下,rf信号的传输基本上通过外导电金属层确保,平滑层的影响是可忽略不计的,并且在这种情况下外导电层的厚度必须至少等于所述趋肤深度δ的五倍,优选地至少等于该趋肤深度的20倍。在一个实施方式中,平滑层可以在不使所述部件彼此分离的情况下围绕芯。因此,可以在组装不同部件以形成芯之后并且在沉积金属护套之前沉积平滑层。在一个实施方式中,平滑层通过使所述部件彼此分离来围绕芯。然后在组装部件以形成芯之前沉积平滑层。其使得可以通过平滑部件在接合处的表面不平整来提高部件定位的准确度。平滑层可以由镍形成。设备可以包括粘合层(或底涂层),所述粘合层在芯的组装之后被沉积以无间断地覆盖芯,导电护套沉积在粘合层之上(以及平滑层之上)。粘合层可以由导电或非导电材料制成。粘合层使得可以改善导电层在芯上的粘合性。其厚度优选地小于芯的粗糙度ra,并且小于芯增材制造方法的分辨率。在一个实施方式中,设备的外护套包括连续的通过增材制造生产的非导电芯、粘合层、平滑层和导电层。因此,粘合层和平滑层使得可以减小波导通道表面的粗糙度。粘合层使得可以改善导电或非导电芯与平滑层和导电层的粘合性。在一个实施方式中,形成导电护套的金属层包括若干个金属子层。当导电层包括若干个连续的高导电性金属层,例如cu、au、ag时,趋肤深度δ由趋肤电流所汇聚的所有层的金属的性质确定。在一个实施方式中,粘合层可选地包括选自cu、au、ag、ni、al、不锈钢、黄铜的金属、锌酸盐、非导电材料例如聚合物或陶瓷或这些选项的组合。在一个实施方式中,平滑层可选地包括选自cu、au、ag、ni、al、不锈钢、黄铜的金属、非导电材料例如聚合物或陶瓷或这些选项的组合。设备的芯可以由聚合物材料形成。设备的芯可以由金属或合金例如铝、钛或钢形成。设备的芯可以由陶瓷形成。设备的芯可以通过立体光刻、通过选择性激光熔化或通过选择性激光烧结来生产。形成护套的金属层可以可选地包括选自cu、au、ag、ni、al、不锈钢、黄铜的金属或这些金属的组合。选自抗拉强度、抗扭强度或抗弯强度或这些强度的组合的设备强度可以大部分地由导电层赋予。选自抗拉强度,抗扭强度或抗弯强度或这些强度的组合的设备强度可以大部分地由导电层和平滑层赋予。本发明的另一目的是一种用于制造无源射频设备的方法,包括:对多个部件进行增材制造,至少一个部件包括壳体;将胶合剂插入所述壳体中;将部件组装在一起,以形成设备的芯,至少两个部件彼此直接接触;在不使所述部件彼此分离的情况下将导电层沉积在芯上。该方法使得能够通过组装通过增材制造生产的部件来制造复杂的设备。组装之后的用金属涂层保证了导电护套不存在不连续性。如将看到的,多个部件的制造还使得能够在部件的组装之前对部件进行清洁或抛光,这使得可以清洁或抛光设备的难以接近的部分。如将看到的,该多个部件的制造还使得能够在部件的组装之前对部件进行聚合,这使得要硬化的设备的难以接近的部分可以暴露于紫外线。根据一个实施方式,导电层在芯上的沉积通过电解沉积或电镀、化学沉积、真空沉积、物理气相沉积(pvd)、通过印刷的沉积,通过烧结的沉积来执行。在该方法的一个实施方式中,导电层包括连续沉积的若干个金属和/或非金属层。芯的制造包括增材制造步骤。“增材制造”应理解为意指基于存储在计算机介质上的计算机化数据通过增加材料来制造部件并定义部件的模型的任何方法。除了立体光刻和选择性激光熔化之外,该表达还描述了基于液体或粉末硬化或者特别是凝结的其他制造方法,包括但不限于基于喷绘(粘合剂喷射)、ded(直接能量沉积)、ebff(电子束自由成形制造)、fdm(熔融沉积成形)、pff(塑性自由成形)、气溶胶、bpm(弹道粒子制造)、粉末床、sls(选择性激光烧结)、alm(增材层制造)、聚合物喷射、ebm(电子束熔化)和光聚合等的方法。然而,通过立体光刻或通过选择性激光熔化的制造是优选的,因为它使得可以获得具有相对清洁的表面条件和低粗糙度的部件。该方法可以包括将平滑层沉积在芯周围的步骤。平滑层可以在组装之前被沉积,从而使所述部件彼此分离。平滑层可以在组装之后被沉积;在这种情况下,其因而不会使芯的部件彼此分离。芯的制造可以包括以下步骤:通过立体光刻、通过选择性激光熔化或通过选择性激光烧结来进行增材制造。芯的制造可以包括在组装之前进行抛光的步骤。芯的制造可以包括在组装之前的清洁步骤。芯的制造可以包括在组装之前的硬化步骤。芯的制造可以包括在组装之后的硬化步骤。芯的制造可以包括在组装之前的预硬化步骤和在组装之后的最终硬化步骤。最终硬化可以用于将部件熔融在一起。该方法可以包括将粘合层沉积在芯周围。在本发明的上下文中,术语“导电层”、“导电涂层”、“导电金属层”和“金属层”是同义的且可互换的。附图说明在附图所示的描述中指示了本发明的实现示例,在附图中:·图1a示出了意在沿与信号传播方向呈直角的接合平面被组装以形成波导芯的两个部件的立体图。·图1b示出了图1a的两个部件在组装以形成波导芯之后的立体图。·图1c示出了包括由组装的两个部件制成且在内壁和外壁上由导电护套覆盖的芯的设备的立体图。·图1d示出了包括以组装的两个部件形式的且在内壁和外壁上覆盖有导电护套的芯的设备的纵向截面图。·图2a示出了意在沿与信号传播方向平行的接合平面被组装以形成波导芯的两个部件的立体图。·图2b示出了图2a的两个部件在组装以形成波导芯之后的立体图。·图2c示出了包括以组装的两个部件的形式的且在内壁和外壁上由导电护套覆盖的芯的设备的横向截面图。·图3a示出了根据本发明的包括涂覆有平滑层和导电护套的以两个部件的形式的芯的设备的横向截面图。·图3b示出了包括以组装的两个部件的形式的且在内壁和外壁上覆盖有平滑层和导电护套的芯的设备的纵向截面图。具体实施方式图1a示出了意在被组装在一起以形成在这里为波导的无源射频设备的芯3的两个部件1a和1b。部件设置有限定了用于传输射频信号的通道的矩形截面的纵向孔2。根据要发送的电磁信号的频率确定孔的截面。该内部通道的尺寸及其形状根据设备1的操作频率,也就是制造该设备并且获得稳定的且可选地具有最小衰减的传输模式的电磁信号的频率来确定。在该示例中,两个部件1a和1b意在沿信号的传输方向一个接一个地被并置,因此形成连续的纵向通道。意在被放置以接触的表面31是平面的并且与射频信号的传输方向呈直角。这些表面中的至少一个包括一个或更多个壳体30以在其中容纳胶合剂,以将两个部件1a、1b固定成彼此胶合。壳体30被设置在部件(这里是部件1b)的表面31上,该表面31意在在组装期间被放置成与另一部件(1a)接触。这些壳体优选地不暴露在意在用金属沉积物覆盖的外表面或内表面上。因此,金属层仅沉积在芯上,而不沉积在胶合剂上,这保证了平整的沉积。该芯3界定了用于引导波的内部通道2。意在形成芯3的部件1a、1b可以例如由聚合物、环氧树脂、陶瓷、有机材料或金属(优选地为铝、钛、钢或因瓦合金)制成。部件1a和1b通过增材制造,优选通过立体光刻或通过选择性激光熔化来制造,以减小表面的粗糙度。芯的材料可以是非导电的或导电的。壁的厚度例如在0.5到3mm之间,优选地在0.8到1.5mm之间。部件1a、1b的形状可以由存储在计算机数据介质中并且使得可以控制增材制造设备的计算机文件确定。在制造之后并且在组装之前,部件1a、1b中的每一个可以被干燥、清洁和/或抛光以改善表面条件。其还至少部分地被硬化。在组装之前的干燥、清洁、抛光和/或硬化使得可以更容易地接近设备中的在组装之后难以接近的部分,例如在通道2的中心处。如将看到的,可以在组装之前沉积平滑层。图1b示出了在组装以形成芯3之后的两个部件1a、1b。部件借助于沉积在胶合剂壳体30中的胶合剂通过胶合来固定。接触表面31上的胶合剂的存在优选地被避免,这提高了组装的准确性。然而,胶合剂被优选地选择成使得利用沉积方法沉积的金属能够被保留;因此,靠近两个胶合剂之间的接合处的胶合剂的痕迹的可能存在不会导致沉积中的不平整。在一个实施方式中,形成芯的不同部件在其组装之前例如通过加热和/或暴露于紫外线辐射被预硬化。它们然后被并置,然后通过再次将部件置于紫外线辐射下或置于烘箱中来执行最终硬化步骤。该解决方案使得可以将部件1a、1b熔融在一起以便于其组装。至少一个销34优选地被插入接触表面31中之一中的用于销的壳体中,以与该接触表面呈直角地延伸。该销优选地被穿凿到壳体中,并且意在被插入设置在面向部件1a的接触面中的壳体中。这个或这些销保证将部件1a,1b彼此对齐。还可以提供螺钉(未示出)以至少在胶合期间将两个部件固定在一起。还可以采用通过以夹紧组装或榫眼型组装来装配的机械组装将部件1a,1b彼此固定。图1c示出了在芯3的内表面和外表面上通过形成导电护套4、5的金属沉积来涂覆该芯3而形成的设备。该图示出了在设备前面的横向面32上的不同层;在另一实施方式中,该前面也被用金属涂层,使得内层3、4是不可见的。在所示的该实施方式中,芯3的内表面和外表面覆盖有通过无电流的化学沉积所镀覆的导电金属层4,例如铜、银、金、镍等。该层的厚度例如在1到20微米之间,例如在4到10微米之间。该导电涂层4的厚度必须足以使表面在所选择的射频下导电。这通常使用其厚度大于趋肤深度δ的导电层获得。该厚度优选地在所有内表面上基本恒定,以获得具有用于通道的精确尺寸容限的成品部件。导电金属4、5在内表面和可能的外表面上的沉积通过以下操作来完成:在将部件1a、1b组装之后将芯3浸入连续的一系列的槽,通常为1至15个槽。每个槽包含具有一种或更多种试剂的流体。沉积使得不需要向要覆盖的芯施加电流。通过搅拌流体,例如通过将流体泵送到传输通道和/或设备周围或通过例如利用超声振动设备产生超声波来振动芯3和/或流体罐来获得经搅拌的平整的沉积。在一个实施方式中,该层4的厚度比趋肤深度大至少20倍,以改善设备的结构、机械、热和化学性质。因此,表面电流大部分地,甚至几乎完全地被汇聚在该层中。在外表面上施加金属沉积不会有助于在通道2中的射频信号的传播,但是确实具有保护设备免受热、机械或化学侵害的优点。在未示出的实施方式中,仅围绕通道2的芯的内表面覆盖有金属护套;外表面是裸露的,或覆盖有不同的涂层。图1d示出了沿图1c的平面a-a的金属设备的纵向截面图。特别可见的是两个部件1a、1b通过胶合剂壳体30中的胶合而彼此固定。通过芯的内表面和外表面上的连续金属护套4也确保了固定。图2a至图2c示出了变型设备;除非另有说明,否则以上关于图1a至1d描述的所有特征和步骤也适用于该变型。图2a示出了变型设备,其中通过沿分离平面组装两个部件1a和1b来形成芯,该分离平面在信号通过通道2传播的方向上纵向延伸。在该示例中,部件1a具有u形截面并且部件1b具有形成部件1a的顶部的盖的矩形截面。还可以产生具有矩形截面的波导,其中两个u形部件头对尾地一个安装在另一个的顶部上。部件1a之一的接触表面31包括壳体30以在其中容纳意在将部件固定在一起的胶合剂。两个部件1a、1b借助于销34彼此对齐,销34从部件1a中之一的表面延伸,换言之,突出并且穿透到另一部件1b中的盲孔中。因此销在组装之后被隐藏。图2b示出了在两个部件1a和1b的组装和胶合之后的设备的芯。两个部件1a、1b优选地借助于螺钉35被彼此夹紧地固定,螺钉35穿过通过部件1a中之一的通孔36并且在另一部件中的螺纹孔37中接合。这些螺钉可以在胶合之前被插入,并在胶合剂硬化后被移除。在变型中,可以保留不干扰金属护套的沉积的螺钉。图2c示出了在用金属护套涂覆芯3的内表面和外表面之后的设备的横向截面图。可以通过组装两个以上的部件来产生无源射频设备芯。可以沿既非纵向也非横向的平面或沿非平面表面来组装部件。图3a和图3b示出了变型设备;除非另有说明,否则以上关于图1a至1d和图2a至图2c描述的所有特征和步骤也适用于该变型。图3a示出了另一变型设备的横向截面图,其中芯3由第一平滑层9、6涂覆,然后由导电层4、5涂覆。图3a示出了该设备的纵向截面图。在图3a所示的实施方式中,在组装之后,用平滑层9例如ni层覆盖芯3的表面。平滑层9的厚度至少等于芯的表面的粗糙度ra,或者至少等于用于制造芯的3d打印方法的分辨率(确定表面的粗糙度ra的3d打印方法的分辨率)。在一个实施方式中,该层的厚度在5到500微米之间,优选地在10到150微米之间,优选地在20到150微米之间。该平滑层还确定了设备1的机械和热性能。然后,用例如铜、银、金等的导电层4覆盖ni层9。平滑层使得可以平滑芯的表面并因而减少由于内表面的粗糙度而导致的传输损耗。在该实施方式中,芯3因而被覆盖有由平滑层9和导电层4形成的金属层4+9。该层4+9的总厚度优选地大于或等于趋肤深度δ的五倍,优选地为趋肤深度δ的二十倍。设备1的杨氏模量的值大部分由该导电层4+9赋予。导电层4的厚度本身也可以大于或等于趋肤深度δ的二十倍。大多数导电层优选地被最后沉积在周边。在该示例中所示的平滑层在组装不同部件1a,1b以形成芯之后被沉积;其因而不会使部件分离,并且不会沉积在部件之间的接合表面31上。在未示出的实施方式中,平滑层在组装不同部件1a、1b以形成芯之前被沉积;其因而通过覆盖部件之间的接合表面31使部件分离。该实施方式使得可以获得芯的部件1a、1b之间的更平滑的接合表面31,因而提高了组装的准确度和刚度。在未示出的实施方式中,设备1包括粘合层,例如,在芯3的内表面和可能的外表面之上的由cu制成的涂层;如果提供了该粘合层,则这样的层便于平滑层9的后续沉积,或导电层4的后续沉积。该涂层的厚度有利地小于30微米。该粘合层优选地在组装之后被沉积,因而不覆盖部件之间的接合表面31。还可以产生以下无源射频设备,该无源射频设备包括:通过无胶合地组装多个部件而形成的芯,所述部件中的至少一些部件通过增材制造来分别制造并使用销来对齐;在不使所述部件彼此分离的情况下沉积在所述芯上的导电金属护套。除了胶合之外,上述本发明的其他特征也可以应用于这些设备。还可以产生以下无源射频设备,该无源射频设备包括:通过组装多个部件而形成的芯,所述部件中的至少一些部件通过增材制造来分别制造并使用销来对齐;在不使所述部件彼此分离的情况下沉积在所述芯上的导电金属护套;在所述部件的组装之前沉积在所述部件上的平滑层。包括或不包括胶合的上述本发明的其他特征也可以应用于这些设备。附图中使用的附图标记1无源射频设备2波导通道3芯30用于胶合剂的壳体31接触表面32外表面34销35螺钉36通孔37盲孔,例如螺纹孔4内导电涂层5外导电涂层6平滑或结构层9平滑层当前第1页12