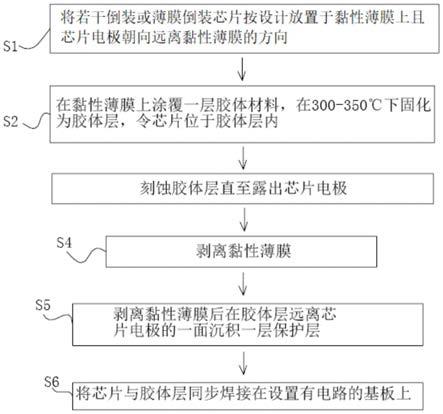
一种深紫外led封装方法
技术领域
1.本发明涉及led封装领域,更具体地,涉及一种深紫外led封装方法。
背景技术:2.目前常规led封装方法是将led芯片通过共晶工艺或固晶工艺固定在基板或者支架上面,先实现电连接,再将荧光粉和环氧树脂或者硅胶的混合物涂覆到led芯片周围,形成荧光粉层。在深紫外led封装过程中由于光子能量高,有机封装材料会对紫外光产生强吸收,造成材料老化变性,紫外光无法出射等问题,所以一般采用石英玻璃材料进行深紫外封装。
3.如公开号为“cn104393154a”,公开日为2015年3月4日的中国专利申请公开了一种led芯片级白光光源的晶圆级封装方法,倒装led的封装方法首先将芯片转移到晶圆基板片(膜)上,随后通过模具获得薄膜真空压印的方法在晶圆片上实施荧光粉涂覆,最后将晶圆片上进行切割获得单颗芯片级的led直接白光光源芯片。正装led的封装方法归纳为首先将led芯片在晶圆基板上片上完成固晶和金线键合工艺,随后对每颗led芯片通过点涂方法形成一硅胶保护透镜,接下来通过薄膜真空压印的方法将硅胶保护透镜上涂覆均匀的荧光粉层。如公开号为“cn104037306a”,公开日为2014年9月10日的中国专利申请公开了一种全无机集成led封装方法和结构,采用三维支架与玻璃盖板实现深紫外的全无机封装。
4.采用石英玻璃封装存在封装成本高,不易完全气密性封装等问题。旋涂玻璃材料由于基本成分为无机材料sio2在紫外波段透过率较高,是一种可能的解决方案。但是深紫外led芯片与基板一般通过金锡共晶工艺焊接,金锡共晶合金的熔点普遍在280℃附近,而旋涂玻璃材料固化则需在300~350
°
温度范围固化30min以上,已超出金锡共晶合金熔点,会造成led芯片与基板片之间焊接点的熔化脱焊,影响产品的可靠性。另外胶体层厚度是影响器件紫外光出射率的一个重要因素,在芯片表面即可形成保护也要保证紫外光尽可能高的出射是深紫外封装需解决的另一个问题。
技术实现要素:5.本发明为克服上述现有技术中固化过程中led芯片焊接点熔化脱焊、封装成本高、不易完全气密性封装等问题,提供一种深紫外led封装方法,先将led芯片固化在与芯片相同厚度的胶体材料内,对器件进行保护层沉积保护,再将芯片与胶体层同步固定到基板上。
6.为解决上述技术问题,本发明采用的技术方案是:一种深紫外led封装方法,包括以下步骤:
7.步骤一:将若干倒装或薄膜倒装芯片按设计放置于黏性薄膜上且芯片电极朝向远离黏性薄膜的方向;
8.步骤二:在黏性薄膜上涂覆一层胶体材料,在300
‑
350℃下固化为胶体层,令芯片位于胶体层内;
9.步骤三:刻蚀减薄胶体层直至露出芯片电极
10.步骤四:剥离黏性薄膜;
11.步骤五:剥离黏性薄膜后在胶体层远离芯片电极的一面沉积一层保护层;
12.步骤六:将芯片与胶体层同步焊接在设置有电路的基板上。
13.在上述的技术方案中,黏性薄膜通过胶粘力固定led芯片,胶体材料涂覆在黏性薄膜上并完成固化后再进行led芯片和基板的焊接,在完成焊接之后就无需进行高温的胶体固化,避免了胶体固化的高温造成led芯片焊接点熔化。
14.优选的,在所述步骤一中,黏性薄膜为耐高温黏性薄膜,能够在300
‑
350℃下保持其性能或形态,可以是铁氟龙高温胶带、聚酰亚胺高温胶带,在胶体层形成后,能够从胶体层上撕下并且不会发生残留,影响后续的步骤。
15.优选的,所述步骤六的具体流程如下:
16.s1:在胶体层的边缘蒸镀一层金或金锡合金;
17.s2:在基板上制作电路,并在基板的边缘蒸镀一层金或金锡合金;
18.s3:将芯片led与胶体层采用共晶工艺焊接在基板上,胶体层的边缘和基板的边缘焊接。
19.胶体层和基板边缘焊接在一起,增强两者之间的连接强度。
20.优选的,胶体层边缘的一层金或金锡合金的厚度为1
‑
5um,优选为3um。基板的边缘蒸镀一层金或金锡合金的厚度为1
‑
10um,优选5um。两者具有足够的厚度焊接在一起,也避免了整体器件的厚度过厚。
21.优选的,所述步骤二中的胶体材料为旋涂玻璃。
22.优选的,在所述步骤三中,在刻蚀胶体层从而减薄胶体层的厚度,直至芯片电极较胶体层高1~5um,以便于芯片电极与基板焊接。
23.优选的,在所述步骤五中,在胶体层远离芯片电极的一面以蒸镀方式制备一层sio2钝化层或以旋涂方式制备一层旋涂玻璃层形成保护层。sio2不会吸收紫外线老化,紫外透过性较高,可实现良好的深紫外led芯片封装。
24.优选的,保护层的厚度为0.2
‑
2um,更优选为0.5um。较薄的保护层保证紫外透过性高。
25.与现有技术相比,本发明的有益效果是:将若干芯片按设计封置胶体层内,可实现深紫外led的集成封装。芯片与胶体层同步焊接,提高深紫外封装可靠性与气密性,同时芯片表面仅沉积一层保护层,紫外光出射经过的介质层距离短,提高光的出射率。
附图说明
26.图1是本发明的一种深紫外led封装方法的流程图。
具体实施方式
27.附图仅用于示例性说明,不能理解为对本专利的限制;为了更好说明本实施例,附图某些部件会有省略、放大或缩小,并不代表实际产品的尺寸;对于本领域技术人员来说,附图中某些公知结构及其说明可能省略是可以理解的。附图中描述位置关系仅用于示例性说明,不能理解为对本专利的限制。
28.本发明实施例的附图中相同或相似的标号对应相同或相似的部件;在本发明的描
述中,需要理解的是,若有术语“上”、“下”、“左”、“右”“长”“短”等指示的方位或位置关系为基于附图所示的方位或位置关系,仅是为了便于描述本发明和简化描述,而不是指示或暗示所指的装置或元件必须具有特定的方位、以特定的方位构造和操作,因此附图中描述位置关系的用语仅用于示例性说明,不能理解为对本专利的限制,对于本领域的普通技术人员而言,可以根据具体情况理解上述术语的具体含义。
29.下面通过具体实施例,并结合附图,对本发明的技术方案作进一步的具体描述:
30.实施例1
31.如图1所示为一种深紫外led封装方法的实施例1,包括如下步骤:
32.步骤一:将若干倒装或薄膜倒装芯片按设计放置于耐高温的黏性薄膜上且芯片电极朝向远离黏性薄膜的方向;
33.步骤二:在黏性薄膜上涂覆一层旋涂玻璃,在300
‑
350℃下固化为胶体层,令芯片位于胶体层内;
34.步骤三:刻蚀胶体层直至露出芯片电极,芯片电极露出胶体层高度为1~5um,以便于芯片电极与基板焊接;
35.步骤四:剥离黏性薄膜;
36.步骤五:剥离黏性薄膜后在胶体层远离芯片电极的一面沉积一层保护层,保护层的厚度为0.5um;
37.步骤六:将led芯片焊接在设置有电路的基板上,具体的流程如下:s1:在胶体层的边缘蒸镀一层厚度为3um的金锡合金;s2:在基板上制作电路,并在在基板的边缘蒸镀一层厚度为5um的金锡合金;s3:将芯片led与胶体层采用共晶工艺焊接在基板上,胶体层的边缘和基板的边缘焊接。
38.本实施例的工作原理或工作流程:黏性薄膜通过胶粘力固定led芯片,胶体材料涂覆在黏性薄膜上并完成固化后再进行led芯片和基板的焊接,在完成焊接之后就无需进行高温的胶体固化,避免了胶体固化的高温造成led芯片焊接点熔化。
39.本实施例的有益效果:将若干芯片按设计封置胶体层内,可实现深紫外led的集成封装。芯片与胶体层同步焊接,提高深紫外封装可靠性与气密性,同时芯片表面仅沉积一层保护层,紫外光出射经过的介质层距离短,提高光的出射率。
40.实施例2
41.一种深紫外led封装方法的实施例2,与实施例1的区别在于,在步骤五中,在胶体层远离芯片电极的一面以蒸镀方式制备一层sio2钝化层或以旋涂方式制备一层旋涂玻璃层形成保护层。保护层的厚度为1.5um。
42.本实施例的工作原理与实施例1一致。
43.显然,本发明的上述实施例仅仅是为清楚地说明本发明所作的举例,而并非是对本发明的实施方式的限定。对于所属领域的普通技术人员来说,在上述说明的基础上还可以做出其它不同形式的变化或变动。这里无需也无法对所有的实施方式予以穷举。凡在本发明的精神和原则之内所作的任何修改、等同替换和改进等,均应包含在本发明权利要求的保护范围之内。