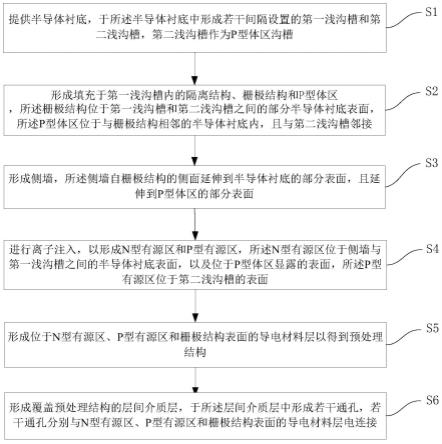
ldmos器件及其制备方法
技术领域
1.本发明涉及半导体制造技术领域,特别是涉及一种ldmos器件及其制备方法。
背景技术:2.bcd平台的ldmos(laterally diffused metal oxide semiconductor,横向扩散金属氧化物半导体)器件通常需要兼具低导通电阻与高击穿电压特性,但这两者在技术上是相矛盾的。为了使高击穿电压的器件在导通电阻上有较大的突破,一种解决思路是在ldmos器件的p型体区(pbody)形成沟槽(trench)结构,使得导通状态下的沟道变宽,从而使得导通电阻下降,提升器件的性能。
3.现有技术中主要包括采用类侧墙(spacer)结构的自对准工艺形成p型体区沟槽或使用额外光罩(mask)添加额外的干法刻蚀与清洗等步骤这两种工艺以达到需要的效果。这两种工艺中,第一种虽然不需要使用额外的光罩,但是会引入过多的热(thermo)过程,导致器件特性的偏移,易产生器件可靠性等方面的问题,在此不再赘述;以第二种工艺为例,形成p型体区沟槽的大致步骤如下(从p型体区离子注入到接触孔形成):
4.1.在栅极形成后进行p型体区刻蚀,并进行相应的离子注入;
5.2.形成侧墙阻挡层;
6.3.使用p型体区沟槽光罩进行光学掩膜处理,并进行干法刻蚀,得到p型体区沟槽;
7.4.进行后续的离子注入及生长导电材料;
8.5.生长介质层及形成接触孔。
9.该工艺方法的不足之处在于:1)需要使用一张额外的光罩,增加了工艺成本;2)由于一般情况下不希望ldmos源端过宽,步骤3的光学掩膜过程容易产生因侧壁与沟槽相距太近而导致的光刻胶倾倒,形成缺陷(defect)并影响后续的刻蚀;3)步骤3还会因光学对准的精度不够而使得沟槽的位置出现偏移,使得沟槽距离两边的位置不同,引起器件性能的失配(mismatch),并引起步骤5中的接触孔错位。
技术实现要素:10.鉴于以上所述现有技术的缺点,本发明的目的在于提供一种ldmos器件及其制备方法,用于解决现有技术中,在制造具有p型体区沟槽的ldmos器件时需要新加光罩,不仅增加成本,同时可能因对位不准使器件特性与设计存在偏差等问题。
11.为实现上述目的及其他相关目的,本发明提供一种ldmos器件的制备方法,包括步骤:
12.s1:提供半导体衬底,于所述半导体衬底中形成若干间隔设置的第一浅沟槽和第二浅沟槽,第二浅沟槽作为p型体区沟槽;
13.s2:形成填充于第一浅沟槽内的隔离结构、栅极结构和p型体区,所述栅极结构位于第一浅沟槽和第二浅沟槽之间的部分半导体衬底表面,所述p型体区位于与栅极结构相邻的半导体衬底内,且与第二浅沟槽邻接;
14.s3:形成侧墙,所述侧墙自栅极结构的侧面延伸到半导体衬底的部分表面,且延伸到p型体区的部分表面;
15.s4:进行离子注入,以形成n型源区和p型源区,所述n型源区位于侧墙与第一浅沟槽之间的半导体衬底表面,以及位于p型体区显露的表面,所述p型源区位于第二浅沟槽的表面;
16.s5:形成位于n型源区、p型源区和栅极结构表面的导电材料层以得到预处理结构;
17.s6:形成覆盖预处理结构的层间介质层,于所述层间介质层中形成若干接触孔,若干接触孔分别与n型源区、p型源区和栅极结构表面的导电材料层电连接。
18.可选地,第一浅沟槽和第二浅沟槽的深度一致,所述第一浅沟槽为多个,第二浅沟槽位于多个第一浅沟槽之间。
19.可选地,形成栅极结构、p型体区和填充于第一浅沟槽内的隔离结构的步骤包括:
20.形成隔离材料层,所述隔离材料层填充第一浅沟槽、第二浅沟槽且覆盖第一浅沟槽和第二浅沟槽之间的半导体衬底,位于第一浅沟槽内的隔离材料层构成隔离结构;
21.进行表面平坦化处理,以显露出位于第一浅沟槽和第二浅沟槽之间的半导体衬底;
22.于第一浅沟槽和第二浅沟槽之间的半导体衬底表面形成牺牲氧化层;
23.进行离子注入以形成p型阱区和n型阱区,第二浅沟槽位于p型阱区内,之后去除所述牺牲氧化层;
24.形成栅氧化层和位于栅氧化层表面的多晶硅栅层,对所述多晶硅栅层和栅氧化层进行刻蚀以形成由栅氧化层和多晶硅栅层构成的栅极结构,所述栅极结构延伸到p型阱区和n型阱区的部分表面;
25.形成覆盖栅极结构、第一浅沟槽和第二浅沟槽的光刻胶层,进行曝光显影以显露出对应p型体区的区域,进行离子注入以形成位于p型阱区内的所述p型体区;
26.去除位于所述第二浅沟槽内的隔离材料层。
27.可选地,所述隔离材料层的材质包括氧化硅,形成所述隔离材料层的方法为化学气相沉积法,去除所述第二浅沟槽内的隔离材料层的方法为湿法刻蚀法。
28.可选地,所述牺牲氧化层和栅氧化层均为氧化硅层,均通过热氧化法形成,去除所述牺牲氧化层的方法为湿法刻蚀法。
29.可选地,所述多晶硅栅层的形成方法为化学气相沉积法,对所述栅氧化层和多晶硅栅层进行刻蚀的方法为干法刻蚀法。
30.可选地,所述p型阱区和n型阱区相互间隔。
31.可选地,形成侧墙的方法为,
32.采用化学气相沉积工艺形成侧墙材料层,所述侧墙材料层覆盖步骤s2后得到的结构,所述侧墙材料层的材质包括氮化硅;
33.刻蚀去除除侧墙外的侧墙材料层。
34.可选地,所述导电材料层为金属硅化物层,位于p型体区表面的导电材料层延伸至与位于p型源区表面的导电材料层相连接;所述层间介质层包括氧化物层。
35.本发明还提供一种ldmos器件,所述ldmos器件采用如上述任一方案中所述的制备方法制备而成。
36.如上所述,本发明的ldmos器件及其制备方法,具有以下有益效果:本发明经改善的流程和工艺设计,省去了大部分单独形成p型体区沟槽所需的工艺步骤,降低了工艺的复杂性,且整个制备流程与现有的bcd工艺相兼容;本发明中,只需保证接触孔光刻时对有源区的对准,对准难度大大下降,可显著降低因对位不准导致器件特性偏移的可能性,且可以减少光罩使用,降低生产成本。
附图说明
37.图1显示为本发明提供的ldmos器件的制备方法的流程图。
38.图2-6显示为依本发明提供的制备方法制备ldmos器件的各步骤中所呈现出的例示性结构示意图。
39.元件标号说明
40.11
ꢀꢀꢀꢀꢀꢀꢀꢀꢀꢀꢀꢀꢀꢀꢀꢀꢀꢀꢀꢀꢀꢀ
半导体衬底
41.12
ꢀꢀꢀꢀꢀꢀꢀꢀꢀꢀꢀꢀꢀꢀꢀꢀꢀꢀꢀꢀꢀꢀ
第一浅沟槽
42.13
ꢀꢀꢀꢀꢀꢀꢀꢀꢀꢀꢀꢀꢀꢀꢀꢀꢀꢀꢀꢀꢀꢀ
p型体区沟槽
43.14
ꢀꢀꢀꢀꢀꢀꢀꢀꢀꢀꢀꢀꢀꢀꢀꢀꢀꢀꢀꢀꢀꢀ
栅极结构
44.15
ꢀꢀꢀꢀꢀꢀꢀꢀꢀꢀꢀꢀꢀꢀꢀꢀꢀꢀꢀꢀꢀꢀ
p型体区
45.16
ꢀꢀꢀꢀꢀꢀꢀꢀꢀꢀꢀꢀꢀꢀꢀꢀꢀꢀꢀꢀꢀꢀ
隔离结构
46.17
ꢀꢀꢀꢀꢀꢀꢀꢀꢀꢀꢀꢀꢀꢀꢀꢀꢀꢀꢀꢀꢀꢀ
侧墙
47.18
ꢀꢀꢀꢀꢀꢀꢀꢀꢀꢀꢀꢀꢀꢀꢀꢀꢀꢀꢀꢀꢀꢀ
n型源区
48.19
ꢀꢀꢀꢀꢀꢀꢀꢀꢀꢀꢀꢀꢀꢀꢀꢀꢀꢀꢀꢀꢀꢀ
p型源区
49.20
ꢀꢀꢀꢀꢀꢀꢀꢀꢀꢀꢀꢀꢀꢀꢀꢀꢀꢀꢀꢀꢀꢀ
导电材料层
50.21
ꢀꢀꢀꢀꢀꢀꢀꢀꢀꢀꢀꢀꢀꢀꢀꢀꢀꢀꢀꢀꢀꢀ
层间介质层
51.22
ꢀꢀꢀꢀꢀꢀꢀꢀꢀꢀꢀꢀꢀꢀꢀꢀꢀꢀꢀꢀꢀꢀ
接触孔
52.23
ꢀꢀꢀꢀꢀꢀꢀꢀꢀꢀꢀꢀꢀꢀꢀꢀꢀꢀꢀꢀꢀꢀ
光刻胶层
具体实施方式
53.以下通过特定的具体实例说明本发明的实施方式,本领域技术人员可由本说明书所揭露的内容轻易地了解本发明的其他优点与功效。本发明还可以通过另外不同的具体实施方式加以实施或应用,本说明书中的各项细节也可以基于不同观点与应用,在没有背离本发明的精神下进行各种修饰或改变。如在详述本发明实施例时,为便于说明,表示器件结构的剖面图会不依一般比例作局部放大,而且所述示意图只是示例,其在此不应限制本发明保护的范围。此外,在实际制作中应包含长度、宽度及深度的三维空间尺寸。
54.为了方便描述,此处可能使用诸如“之下”、“下方”、“低于”、“下面”、“上方”、“上”等的空间关系词语来描述附图中所示的一个元件或特征与其他元件或特征的关系。将理解到,这些空间关系词语意图包含使用中或操作中的器件的、除了附图中描绘的方向之外的其他方向。此外,当一层被称为在两层“之间”时,它可以是所述两层之间仅有的层,或者也可以存在一个或多个介于其间的层。
55.在本技术的上下文中,所描述的第一特征在第二特征“之上”的结构可以包括第一和第二特征形成为直接接触的实施例,也可以包括另外的特征形成在第一和第二特征之间
的实施例,这样第一和第二特征可能不是直接接触。
56.需要说明的是,本实施例中所提供的图示仅以示意方式说明本发明的基本构想,遂图式中仅显示与本发明中有关的组件而非按照实际实施时的组件数目、形状及尺寸绘制,其实际实施时各组件的型态、数量及比例可为一种随意的改变,且其组件布局型态也可能更为复杂。为使图示尽量简洁,各附图中并未对所有的结构全部标示。
57.请参阅图1至图6。
58.如图1所示,本发明提供一种ldmos器件的制备方法,包括步骤:
59.s1:提供半导体衬底11,于所述半导体衬底11中形成若干间隔设置的第一浅沟槽12(sti)和第二浅沟槽,第二浅沟槽作为p型体区15(pbody)沟槽,可以有效提高器件的击穿电压;所述半导体衬底11包括但不限于硅衬底、锗衬底、锗硅衬底、绝缘体上硅衬底、碳化硅衬底、砷化镓衬底或上述多种衬底的结合,即所述半导体衬底11可以为单层结构,例如为硅晶圆,也可以为复合结构,例如为硅晶圆表面形成有外延层(这种情况下,则各沟槽形成于外延层中),第一浅沟槽12和第二浅沟槽优选在同一刻蚀工艺中同步形成,因而两者通常具有相同的深度,两者的形貌不限,例如可以完全一样,本实施例中只是出于描述的方便将不同作用的沟槽定义为“第一浅沟槽”和“第二浅沟槽”,且在本实施例中,第一浅沟槽12为2个以上,第二浅沟槽位于多个第一浅沟槽12之间,当然,第二浅沟槽也可以为多个,当形成包括多个ldmos器件的阵列时,实质就形成了第一浅沟槽中包围多个第二浅沟槽的结构,该步骤得到的结构如图2所示;s2:形成填充于第一浅沟槽12内的隔离结构16、栅极结构14和p型体区15,所述栅极结构14位于第一浅沟槽12和第二浅沟槽之间的部分半导体衬底11表面,即栅极结构14并未完全覆盖第一浅沟槽12和第二浅沟槽之间的半导体衬底11,所述p型体区15位于与栅极结构14相邻的半导体衬底11内,且与第二浅沟槽邻接,p型体区15通常通过对对应区域进行p型离子注入而成;在本实施例提供的较佳示例中,该步骤的具体过程为:形成隔离材料层,所述隔离材料层填充第一浅沟槽12、第二浅沟槽且覆盖第一浅沟槽12和第二浅沟槽之间的半导体衬底11,位于第一浅沟槽12内的隔离材料层构成隔离结构16;所述隔离材料层包括但不限于氧化硅层,还可以为其他高k介质材料层,形成方法优选化学气相沉积法,本示例中采用氧化硅材料作为隔离材料;之后进行表面平坦化处理,例如进行化学机械研磨(cmp),将第一浅沟槽12和第二浅沟槽之间的半导体衬底11表面的隔离材料层去除,直至显露出位于第一浅沟槽12和第二浅沟槽之间的半导体衬底11;于第一浅沟槽12和第二浅沟槽之间的半导体衬底11表面形成牺牲氧化层,牺牲氧化层优选氧化硅层,形成方法优选热氧化法,具有形成速度快,且生成的氧化硅层具有细小的孔洞,便于后续的离子注入,且在后续步骤中容易去除;对显露的半导体衬底11进行离子注入以形成p型阱区(pwell)和n型阱区(nwell),该掺杂过程通常为轻掺杂,p型阱区和n型阱区之间通常具有一定间距,当然根据器件需要也可以没有间距,第一浅沟槽12可以位于n型阱区内,也可以是n型阱区占据第一浅沟槽的一部分,而第二浅沟槽位于p型阱区内,第二浅沟槽的深度通常小于p型阱区的深度,之后去除所述牺牲氧化层,较佳地为采用湿法清洗去除所述牺牲氧化层,可以有效减少对半导体衬底11的表面损伤,清除杂质;接下来,形成栅氧化层和位于栅氧化层表面的多晶硅栅层(即栅氧化层位于半导体衬底11表面),栅氧化层具体为氧化硅层,优选采用热氧化工艺形成,多晶硅栅层较佳地为采用化学气相沉积工艺形成,对所述多晶硅栅层和栅氧化层进行刻蚀,例如在掩膜层作用下,采用干法刻蚀进行刻蚀,以形成由栅
氧化层和多晶硅栅层构成的栅极结构14,所述栅极结构14延伸到p型阱区和n型阱区的部分表面,或者说,栅极结构14位于半导体衬底11表面,并向外延伸到p型阱区和n型阱区的部分表面(但未完全将n型阱区和p型阱区覆盖);采用包括但不限于旋涂工艺形成覆盖栅极结构14、第一浅沟槽12和第二浅沟槽的光刻胶层23,进行曝光显影以显露出对应p型体区15的区域,该区域为位于栅极结构14和第二浅沟槽之间的半导体衬底11区域,对该区域进行离子注入以形成位于p型阱区内的所述p型体区15,p型体区15和p型阱区的离子掺杂类型一致,但p型体区15的掺杂浓度可以高于p型阱区的掺杂浓度,也可以相同,对此不做严格限制,该步骤可以参考图3所示;去除位于所述第二浅沟槽内的隔离材料层,例如采用湿法刻蚀去除,且之后去除残余的光刻胶层23以显露出栅极结构14、第一浅沟槽12和第二浅沟槽;
60.s3:形成侧墙17,所述侧墙17自栅极结构14的侧面延伸到半导体衬底11的部分表面,且延伸到p型体区15的部分表面;该步骤具体可以为,先采用化学气相沉积工艺形成侧墙17材料层,所述侧墙17材料层较佳地包括氮化硅层和/或氧化硅层,例如可以为单一的氮化硅层,也可以是氮化硅层和氧化硅层的复合层,而氧化硅层位于氮化硅层和栅极结构14之间,所述侧墙17材料层覆盖步骤s2后得到的结构,即覆盖栅极结构14、第一浅沟槽12、第二浅沟槽和p型体区15,之后进行光刻刻蚀去除除侧墙17外的侧墙17材料层,即去除位于第一浅沟槽12、第二浅沟槽以及部分半导体衬底11表面的侧墙17材料层;该步骤后得到的结构如图4所示;
61.s4:进行离子注入,以形成n型源区18和p型源区19,该步骤通常为重掺杂,可以大于阱区掺杂时的浓度,所述n型源区18位于侧墙17与第一浅沟槽12之间的半导体衬底11表面,该n型源区18与第一浅沟槽12和侧墙17均邻接,以及位于p型体区15显露的表面(包括p型体区15的上表面及斜面),所述p型源区19位于第二浅沟槽的表面,包括第二浅沟槽的底面和侧面,本实施例中主要以位于底面为例;该步骤后得到的结构如图5所示;
62.s5:形成位于n型源区18、p型源区19和栅极结构14表面的导电材料层20以得到预处理结构;本实施例提供的较佳示例中,所述导电材料层20为金属硅化物(salicide),其形成方法为在对应的结构层(这些结构层都是半导体材料,例如硅)表面形成较薄的金属层,之后经高温退火使硅和金属反应形成金属硅化物,而位于p型体区15表面的导电材料层20将延伸至与位于p型源区19表面的导电材料层20相连接;
63.s6:形成覆盖预处理结构的层间介质层21,于所述层间介质层21中形成若干接触孔22,若干接触孔22分别与n型源区18、p型源区19和栅极结构14表面的导电材料层20电连接;所述层间介质层21优选但不仅限于氧化硅层,其形成方法优选化学气相沉积法,之后采用光刻刻蚀工艺于层间介质层21中形成若干通孔,并对通孔进行金属填充而形成接触孔22,以将相应的各结构电性引出,该步骤后得到的结构如图6所示。
64.现有技术中在制备具有p型体区沟槽的ldmos器件时,需要同时保证接触孔光刻时对有源区(active area)、栅极和p型体区沟槽的对准,对准精度控制难度大,且花费成本巨大。而本发明经改善的流程和工艺设计,省去了大部分单独形成p型体区沟槽所需的工艺步骤,降低了工艺的复杂性,且整个制备流程与现有的bcd工艺相兼容;本发明中,只需保证接触孔光刻时对有源区的对准,对准难度大大下降,可显著降低因对位不准导致器件特性偏移的可能性,且可以减少光罩使用,降低生产成本。
65.本发明还提供一种ldmos器件,所述ldmos器件采用如上述任一方案中所述的制备
方法制备而成,故前述内容可以全文引用至此。参考图6及前文所述,所述ldmos器件包括半导体衬底11、位于半导体衬底11内的第一浅沟槽12和第二浅沟槽、栅极结构14、侧墙17、n型源区18、p型源区19、p型体区15、导电材料层20、层间介质层21和接触孔22,第二浅沟槽作为p型体区沟槽13,其被层间介质层填充,第一浅沟槽12内填充有隔离结构16,栅极结构14位于第一浅沟槽12和第二浅沟槽之间的半导体衬底11表面,侧墙17位于栅极结构14侧面且延伸到半导体衬底11的部分表面,n型源区18位于第一浅沟槽12和侧墙17之间的半导体衬底11内和p型体区15内表面,p型体区15位于第二浅沟槽和侧墙17之间的半导体衬底11内,p型源区19位于第二浅沟槽的表面,包括底面,导电材料层20位于栅极结构14、n型源区18和p型源区19表面,层间介质层21覆盖前述各结构,而接触孔22贯穿层间介质层21,且与n型源区18、p型源区19和栅极结构14表面的导电材料层20接触,以将对应各结构电性引出。对所述ldmos器件的更多介绍还请参考前述内容,出于简洁的目的不赘述。由于采用前述方法制备而成,使得本发明提供的ldmos器件在兼具低导通电阻与高击穿电压特性的同时,其制造难度和制造成本可以显著降低。
66.综上所述,本发明提供一种ldmos器件及其制备方法。制备方法包括步骤:s1:提供半导体衬底,于所述半导体衬底中形成若干间隔设置的第一浅沟槽和第二浅沟槽,第二浅沟槽作为p型体区沟槽;s2:填充于第一浅沟槽内的隔离结构、形成栅极结构和p型体区,所述栅极结构位于第一浅沟槽和第二浅沟槽之间的部分半导体衬底表面,所述p型体区位于与栅极结构相邻的半导体衬底内,且与第二浅沟槽邻接;s3:形成侧墙,所述侧墙自栅极结构的侧面延伸到半导体衬底的部分表面,且延伸到p型体区的部分表面;s4:进行离子注入,以形成n型源区和p型源区,所述n型源区位于侧墙与第一浅沟槽之间的半导体衬底表面,以及位于p型体区显露的表面,所述p型源区位于第二浅沟槽的表面;s5:形成位于n型源区、p型源区和栅极结构表面的导电材料层以得到预处理结构;s6:形成覆盖预处理结构的层间介质层,于所述层间介质层中形成若干接触孔,若干接触孔分别与n型源区、p型源区和栅极结构表面的导电材料层电连接。本发明经改善的流程和工艺设计,省去了大部分单独形成p型体区沟槽所需的工艺步骤,降低了工艺的复杂性,且整个制备流程与现有的bcd工艺相兼容;本发明中,只需保证接触孔光刻时对有源区的对准,对准难度大大下降,可显著降低因对位不准导致器件特性偏移的可能性,且可以减少光罩使用,降低生产成本。所以,本发明有效克服了现有技术中的种种缺点而具高度产业利用价值。
67.上述实施例仅例示性说明本发明的原理及其功效,而非用于限制本发明。任何熟悉此技术的人士皆可在不违背本发明的精神及范畴下,对上述实施例进行修饰或改变。因此,举凡所属技术领域中具有通常知识者在未脱离本发明所揭示的精神与技术思想下所完成的一切等效修饰或改变,仍应由本发明的权利要求所涵盖。