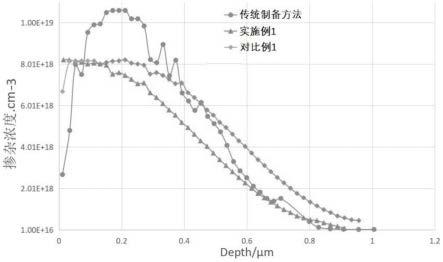
1.本发明涉及太阳能电池技术领域,具体涉及一种硼掺杂发射极的制备方法。
背景技术:2.传统制备硼掺杂发射极的方法(即传统制备方法)是管式硼扩散法:即在管式炉中,通入氮气作为管内气氛,通入三氯化硼或者三溴化硼作为掺杂源,经高温扩散来使硼扩散至硅片中形成硼掺杂发射极。在硼扩散的过程中,硅片(硅片一般采用单晶硅片或多晶硅片)上生成硼硅玻璃层(硼硅玻璃层的主要成分包括二氧化硅,且在电池制作过程中,硼硅玻璃层需去除),而由于硼在二氧化硅中的固溶度大于硼在硅中的固溶度,所以在硼扩散的过程中会导致硅片与二氧化硅的界面分凝系数的差异;这样,更多的硼原子会进入二氧化硅中,所以,制得硼掺杂发射极后,二氧化硅中的硼掺杂浓度高于硅片中的硼掺杂浓度,且硅片中硼掺杂浓度从硅片表层(即硼掺杂发射极表层)至硅片体区(即硅片内部)呈现先逐渐增加后逐渐降低的趋势。因此,传统制备方法的硼掺杂发射极的硼掺杂ecv(电化学微分电容电压)曲线为拱形抛物线型,而这样的硼掺杂ecv曲线决定了制备硼掺杂发射极后,硼掺杂浓度最大值不在硅片表层而在硅片内部一定深度(>150nm),而由于硅片体区的硼掺杂浓度相比硅片表层的硼掺杂浓度更高,所以会导致硅片体区的srh复合和俄歇复合更大;同时,后续的电极金属浆料也需要烧结更深的深度才能与硼掺杂发射极形成更好的接触,然而,烧结深度越深,则电极金属浆料对发射极区域的腐蚀损伤越大,电极金属浆料中的重金属元素在硅片中的分布也更深,对其空间电荷区的破坏更大,故而会导致硼掺杂发射极的表面复合,且电极金属浆料匹配难。
3.而现有硼掺杂发射极的制备方法,如公开号cn114023635a所示,其采用先沉积硼掺杂非晶硅再退火扩散的方法,将硼掺杂非晶硅(在退火过程中会高温晶化成硼掺杂多晶硅)作为硼掺杂发射极的掺杂源,以避免b2o3中间物的产生,从而使非激活硼的含量较少,进而能获得更好的硼掺杂均匀性,同时能避免b2o3对石英件的腐蚀破坏。尽管现有的这种制备方法能改善硼掺杂发射极的硼掺杂的均匀性,故而能减少复合;但是,现有这种制备方法的硼掺杂发射极的硼掺杂ecv曲线中,硼掺杂浓度最大值也并不在硅片表层,所以,这种改善硼掺杂的均匀性来减少复合的复合改善效果有限,制得硼掺杂发射极后的硅片仍然存在较大的表面复合和体区复合。
技术实现要素:4.本发明的目的在于克服现有技术的不足,提供一种硼掺杂发射极的制备方法,以实现区别于传统制备方法形成的硼掺杂发射极的硼掺杂ecv曲线,以实现更低表面复合和更优界面金属电极接触,并实现更低的体区复合。
5.基于此,本发明公开了一种硼掺杂发射极的制备方法,包括如下制备步骤:
6.s1、对n型的硅片进行清洗和制绒处理,以去除硅片表面的损伤层,并使硅片的正面和背面形成金字塔状的绒面;
7.s2、在硅片正面的绒面制备硼掺杂的非晶硅层;
8.s3、对硼掺杂的非晶硅层进行退火处理,先使硼掺杂的非晶硅层的硼原子向硅片内扩散,以在硅片的正面形成硼掺杂发射极,而非晶硅层晶化转变为位于硼掺杂发射极正面的多晶硅层,然后,在降温过程中通入氧气,以在多晶硅层的正面形成硼硅玻璃层,而硅片的背面形成二氧化硅层;
9.s4、去除所述二氧化硅层,再对硅片的背面进行抛光处理,以使硅片的背面形成平坦形貌;
10.s5、依次去除所述硼硅玻璃层和多晶硅层,以使硼掺杂发射极露出并位于硅片的正表面,且硼掺杂发射极的正表面的硼掺杂浓度不小于其硼掺杂浓度最大值的95%。
11.优选地,步骤s5中,所述硼掺杂浓度最大值是在距离硼掺杂发射极的正表面50nm深度以内的硅片表层。
12.优选地,步骤s3中,所述退火处理过程为:先在900-1050℃的高温下于硅片的正面依次形成所述硼掺杂发射极和多晶硅层,然后,进行降温,并在降温过程中通入氧气来使多晶硅层的正面形成厚度为40-60nm的硼硅玻璃层。
13.进一步优选地,步骤s4中,对硅片的背面进行单面hf清洗,以去除所述二氧化硅层而保留硅片正面的硼硅玻璃层,再采用碱溶液对硅片的背面进行抛光处理,以使硅片的背面形成平坦形貌。
14.优选地,步骤s2为:在所述硅片正面的绒面制备原位硼掺杂的非晶硅层。
15.优选地,步骤s2为:先在所述硅片正面的绒面制备本征非晶硅层,再对本征非晶硅层进行离子注入或硼扩散掺杂处理,以制得硼掺杂的非晶硅层。
16.进一步优选地,对所述本征非晶硅层进行离子注入处理时,以bf2作为硼掺杂的非晶硅层的掺杂源,bf2的掺杂剂量为1-10e15.cm-2
。
17.进一步优选地,对所述本征非晶硅层进行硼扩散掺杂处理时,以bcl3或bbr3作为硼掺杂的非晶硅层的掺杂气,在800-850℃下通入掺杂气和氧气,保温,即得所述硼掺杂的非晶硅层。
18.优选地,步骤s2中,所述非晶硅层的制备方法为pvd法或pecvd法;所述非晶硅层的厚度为50-200nm。
19.优选地,步骤s1中,使用naoh溶液或koh溶液对所述硅片进行清洗和制绒处理,所得金字塔状的绒面的反射率为10-12%。
20.优选地,步骤s5中,将硅片放入hf溶液中,以去除硅片正面的硼硅玻璃层,再采用hf与hno3的混合酸溶液、氨水溶液、四甲基氢氧化铵溶液、氢氧化钠溶液或氢氧化钾溶液来去除所述多晶硅层。
21.现有的硼掺杂发射极的制备方法(简称现有方法,例如cn114023635a)中,由于其并没有将硼掺杂的非晶硅层(或多晶硅层)作为硼掺杂发射极的牺牲层,所以其硼掺杂发射极包括由硼掺杂的非晶硅层晶化形成的硼掺杂的多晶硅层。而多晶硅和单晶硅均不是二氧化硅,硼在单晶硅或多晶硅中的固溶度几乎没有差异,因此,理论上,硼在硼掺杂的多晶硅层与单晶硅片的界面结构的扩散基本不存在界面分凝系数差异,故而,理论上,在现有的硼掺杂发射极的硼掺杂ecv曲线上的硼掺杂浓度分布不会如传统制备方法的硼掺杂发射极的硼掺杂ecv曲线一样:呈现先上升后降的分布趋势。
22.然而,申请人经测试发现,在现有方法的硼掺杂发射极的硼掺杂ecv曲线中,其硼掺杂发射极表层的硼掺杂浓度也不是硼掺杂浓度最大值。而本发明的制备方法,将硅片正面的硼掺杂的非晶硅层(或多晶硅层)作为硼掺杂发射极的掺杂源和牺牲层,在步骤s5中去除多晶硅层而使硼掺杂发射极露出并位于硅片的正表面后,所得的硼掺杂发射极的硼掺杂ecv曲线中,其硼掺杂浓度最大值位于距离硼掺杂发射极正表面50nm深度以内的区域,由于这个区域距离经步骤s5处理后的硅片(或硼掺杂发射极)的正表面比较浅,故而这个区域称为硅片表层(或硼掺杂发射极表层);所以,本发明的硼掺杂发射极的硼掺杂ecv曲线中,其硼掺杂浓度最大值即位于硅片表层。
23.申请人认为,之所以会存在现有方法与本发明方法的硼掺杂发射极的硼掺杂ecv曲线的上述差异,其原因主要在于:由于硼掺杂的非晶硅层(或多晶硅层)作为硼掺杂发射极的掺杂源,所以多晶硅层中的硼掺杂量较大,故而硼在硼掺杂的多晶硅层中的扩散可以认为是无限源扩散,其扩散分布符合余误差函数分布),因此在现有方法的硼掺杂发射极的硼掺杂ecv曲线中,其硼掺杂发射极表层的硼掺杂浓度不是硼掺杂浓度最大值。而本发明的硼掺杂发射极的制备方法,将硼掺杂的非晶硅层作为硼掺杂发射极的掺杂源和牺牲层,去除多晶硅层后,硼在硅片(例如单晶硅片)表面向硅片内部的扩散分布可以认为是有限源扩散分布(即恒定源扩散分布),本发明的硼掺杂发射极中硼原子的扩散分布符合高斯函数分布,故而,硼原子在本发明的硼掺杂发射极的表面至内部的扩散分布基本满足逐渐降低的趋势,也即本发明的硼掺杂发射极的硼掺杂ecv曲线中,其硼掺杂浓度最大值即位于硅片表层。
24.与现有技术相比,本发明至少包括以下有益效果:
25.本发明的硼掺杂发射极的制备方法,将硅片正面的硼掺杂的非晶硅层作为硼掺杂发射极的掺杂源和牺牲层,在完成硼掺杂后,去除了晶化的多晶硅层,所以本发明方法所形成的硼掺杂发射极的硼掺杂ecv曲线区别于传统制备方法的硼掺杂发射极的的硼掺杂ecv曲线,故而硼掺杂浓度最大值在该硅片表层,而非在硅片的体区内,因此能大大降低硅片体区的俄歇复合和srh复合;而且,由于硅片表层的硼掺杂浓度即为硼掺杂浓度最大值,所以,电极金属浆料的最佳烧结深度会明显减小,故而电极金属浆料对发射极区域的腐蚀损伤更小,电极金属浆料中的重金属元素对硅片的空间电荷区的破坏也更小,故而能降低硼掺杂发射极的表面复合;同时,电极金属浆料与硼掺杂发射极能形成较好的接触,故而有利于降低接触电阻率,能实现较低的金属复合,且电极金属浆料的匹配难度更低。
26.另外,现有方法(例如cn114023635a)中,由于并没有将硼掺杂的非晶硅层作为硼掺杂发射极的牺牲层,所以其硼掺杂发射极包括由硼掺杂的非晶硅层晶化形成的硼掺杂的多晶硅层,经测试发现,这种现有方法的硼掺杂发射极的硼掺杂ecv曲线中,其硅片表层的硼掺杂浓度也不是硼掺杂浓度最大值,因此采用现有方法制得的这种硅片仍然存在较大的体区复合、表面复合及金属复合;而且,由于其硅片正面存在硼掺杂的多晶硅层会带来寄生光吸收损耗,使短波段(300-600nm波段)的光吸收受限,影响正面的光利用率,进而还会导致其电池出现短路电流损失。
附图说明
27.图1为实施例1的一种硼掺杂发射极的制备方法中硅片经步骤1后的截面结构示意
图。
28.图2为实施例1-3的一种硼掺杂发射极的制备方法中硅片经步骤2后的截面结构示意图。
29.图3为实施例1-2的一种硼掺杂发射极的制备方法中硅片经步骤3后的截面结构示意图。
30.图4为实施例3的一种硼掺杂发射极的制备方法中硅片经步骤3后的截面结构示意图。
31.图5为实施例1-3的一种硼掺杂发射极的制备方法中硅片经步骤4后的截面结构示意图。
32.图6为实施例1-3的一种硼掺杂发射极的制备方法中硅片经步骤5后的截面结构示意图。
33.图7为实施例1、对比例1和传统制备方法的硼掺杂发射极的硼掺杂ecv曲线对比图。
34.图8为实施例2和传统制备方法的硼掺杂发射极的硼掺杂ecv曲线对比图。
35.图9为实施例3和传统制备方法的硼掺杂发射极的硼掺杂ecv曲线对比图。
36.附图标号说明:硅片1,非晶硅层2,多晶硅层21,硼掺杂发射极3,硼硅玻璃层4,二氧化硅层5。
具体实施方式
37.为使本发明的上述目的、特征和优点能够更加明显易懂,下面结合附图和具体实施方式对本发明作进一步详细的说明。
38.实施例1
39.本实施例的一种硼掺杂发射极的制备方法,包括依次进行的以下步骤:
40.步骤1、选择n型单晶硅片1作为衬底,对硅片1进行清洗和制绒处理,以去除硅片1表面的损伤层,并使硅片1的正面和背面均形成减反射的金字塔状的绒面。经步骤1处理后的结构如图1所示。其中,n型单晶硅片1的电阻率为0.5-1.5ω/sq;金字塔状的绒面的反射率控制在10-12%范围内。
41.具体地,使用naoh溶液对硅片1进行清洗和制绒处理,naoh的浓度为1-2%,处理的温度为78-84℃,处理的时间为5-10min。
42.当然,在其他示例中,还可使用koh溶液对硅片1进行清洗和制绒处理。
43.步骤2、在步骤1处理后的硅片1正面的绒面上沉积原位硼掺杂的非晶硅层2。经步骤2处理后的结构如图2所示。其中,硅片1正面的绒面沉积的非晶硅层2的厚度控制在50-200nm范围内、优选为100-200nm。
44.具体地,采用pvd法在硅片1正面的绒面上沉积原位硼掺杂的非晶硅层2。具体地,在磁控溅射反应腔中固定本征硅靶材,保持硅片1正面与靶材之间的距离为10-50cm;然后,在氩气氛围中,调整反应气压为0.5-1.0pa,通入氟化硼气体,控制氟化硼与氩气的比例为8-10%,沉积的工艺温度为250-300℃,沉积的反应时间为3-6min。
45.当然,在其他示例中,还可采用如pecvd法的其他方法在硅片1正面的绒面上沉积硼掺杂的非晶硅层2。
46.此外,在本实施例中,由于采用沉积原位硼掺杂非晶硅层2的方法,所以无需再额外进行离子注入或者扩散掺杂工序来实现非晶硅层2的硼掺杂源的加入,所以,本实施例的制备工序更简单。
47.步骤3、对硅片1的非晶硅层2进行退火处理:先使非晶硅层2的原位硼掺杂的硼原子在高温(如900-1050℃)下得到激活并向硅片1体内扩散,以在硅片1的正面形成硼掺杂发射极3,而非晶硅层2在该高温下晶化转变为多晶硅层21,该多晶硅层21位于硼掺杂发射极3的正面,然后在降温过程中通入氧气,以在硅片1的正面形成厚度为40-60nm的硼硅玻璃层4,该硼硅玻璃层4位于多晶硅层21的正面。经步骤3处理后的结构如图3所示。
48.具体地,将沉积非晶硅层2的硅片1放置于石英舟中,并将石英舟送入管式炉中,通入氮气作为退火气氛,升温至960℃,在960℃下恒温1h,此时,非晶硅层2的硼掺杂的硼原子得到激活并向硅片1体内扩散,以使硅片1的正面形成硼掺杂发射极3,而非晶硅层2经高温晶化转变为多晶硅层21,然后开始降温,降温过程中通入氧气气氛,以在硅片1的正面形成较厚的硼硅玻璃层4,此时硅片1的背面也会氧化形成二氧化硅层5;如此即完成对沉积非晶硅层2的硅片1的退火处理。
49.步骤3中,硅片1正面的硼硅玻璃层4的厚度优选为控制在40-60nm范围内,此时硅片1正面的硼硅玻璃层4较厚,能在后续步骤4的抛光处理过程中对硅片1正面起到很好的保护作用,从而有利于后续步骤5的硅片1正面的多晶硅层21的精确去除,进而能提升所制得的硼掺杂发射极3的品质。这是因为,如果硅片1正面的硼硅玻璃层4较薄,则在后续步骤4的抛光处理过程中硅片1正面的硼掺杂发射极3和多晶硅层21会存在被刻蚀的风险,这不利于后续步骤5中对硅片1正面的多晶硅层21的精确去除操作,从而会导致硼掺杂发射极3受损伤,使其复合变大,进而影响硅片1正面的硼掺杂发射极3的品质。
50.步骤4、将硅片1的背面放置于hf溶液之上,而硅片1的正面不与hf溶液接触,以去除硅片1背面的二氧化硅层5;然后将硅片1置于加热的碱溶液中,以对硅片1的背面进行抛光处理,使硅片1的背面形成平坦的背面形貌。经步骤4处理后的结构如图5所示。
51.具体地,将硅片1的背面放置并漂浮于浓度1-5%的hf溶液上,以去除硅片1背面的二氧化硅层5;然后将硅片1的背面浸入温度为60-70℃、浓度为2-2.5%的naoh溶液中,以对硅片1的背面进行抛光处理,使硅片1的背面形成平坦的背面形貌。
52.步骤4中,仅去除了硅片1背面的二氧化硅层5,而硅片1正面的硼硅玻璃层4被保留下来,这样,硅片1正面的较厚的硼硅玻璃层4在抛光处理的过程中能对硅片1的正面起到很好的保护作用,有利于后续步骤5对硅片1正面的多晶硅层21的精确去除,进而能提升所制得的硼掺杂发射极3的品质。
53.步骤5、将硅片1正面置于hf溶液中,以去除硅片1正面的硼硅玻璃层4,然后将硅片1正面浸入酸溶液或碱溶液中,以去除硅片1正面的多晶硅层21,烘干硅片1,即制得正面具有硼掺杂发射极3的硅片1。经步骤5处理后的结构如图6所示。其中,该酸溶液为hf与hno3的混合溶液。该碱溶液为氨水溶液或四甲基氢氧化铵溶液或氢氧化钠溶液或氢氧化钾溶液。
54.具体地,将硅片1正面放入1-5%浓度的hf溶液中,以去除硅片1正面的硼硅玻璃层4,然后将硅片1正面浸入温度为30-70℃、浓度为0.03-1.2%的naoh溶液中;该naoh溶液中优选为加入体积比为1%-10%的辅助添加剂(如拓邦科技的绕镀poly层的清洗添加剂),以稳定地控制naoh溶液对硅片1正面的多晶硅层21的刻蚀速度;进而去除硅片1正面的多晶硅
层21。
55.本发明的硼掺杂发射极的制备方法,是将硅片1正面的硼掺杂的非晶硅层2作为硼掺杂发射极3的掺杂源和牺牲层;具体为:在制绒后的硅片1正面沉积非晶硅层2,以硼掺杂的非晶硅层2作为硼掺杂进行退火处理(退火处理后,非晶硅层2转换为多晶硅层21),然后,在完成硼掺杂后,去除晶化后的多晶硅层21,以使硼掺杂发射极3露出并位于硅片1的正表面,此时,硼掺杂发射极3的正表面即为硅片1的正表面,硼掺杂发射极3的正表面的硼掺杂浓度不小于硼掺杂发射极3的硼掺杂浓度最大值的95%;参见图6,本发明中,该硼掺杂发射极3的硼掺杂浓度最大值是在距离硼掺杂发射极3的正表面50nm深度以内的经步骤1-5处理后的硅片1表层(也即硼掺杂发射极3表层)。
56.。如此,采用本发明的制备方法所形成的硼掺杂发射极的硼掺杂ecv曲线区别于传统制备方法的硼掺杂发射极的硼掺杂ecv曲线(参见图7-9),这使得硅片1表层的硼掺杂浓度即为硼掺杂浓度最大值,也即硼掺杂浓度最大值在该硅片1表层,而非在硅片1的体区内,故而能大大降低硅片1体区的俄歇复合和srh复合。
57.而且,由于硅片1表层的硼掺杂浓度即为硼掺杂浓度最大值,所以,在后续的金属化过程中,电极金属浆料的最佳烧结深度会明显减小,故而电极金属浆料对发射极区域的腐蚀损伤更小,电极金属浆料中的重金属元素在硅片1中的分布更浅,这些重金属元素对硅片1的空间电荷区的破坏更小,故而能降低硼掺杂发射极3的表面复合;同时,即便电极金属浆料的烧结深度减小也能确保电极金属浆料与硼掺杂发射极3形成较好的接触,故而有利于降低接触电阻率,进而能实现较低的金属复合;且由于电极金属浆料的最佳烧结深度变浅,所以电极金属浆料的匹配难度更低。
58.另外,现有硼掺杂发射极的制备方法(如cn114023635a)中,由于其仅将硼掺杂的非晶硅层作为硼掺杂发射极的掺杂源,并没有将硼掺杂的非晶硅层作为硼掺杂发射极的牺牲层,也即该硼掺杂发射极包括由硼掺杂的非晶硅层晶化所形成的硼掺杂的多晶硅层,经测试发现,这种现有方法的硼掺杂发射极的硼掺杂ecv曲线中,其硅片表层的硼掺杂浓度也不是硼掺杂浓度最大值,因此采用现有方法制得的这种硅片,故而其硅片仍然具有较大的体区复合、表面复合及金属复合。而且,现有硼掺杂发射极的制备方法中,由于其硅片正面存在硼掺杂的多晶硅层会带来寄生光吸收损耗,使短波段(300-600nm波段)的光吸收受限,从而会影响正面的光利用率,进而会导致其电池出现短路电流损失。而本发明的硼掺杂发射极的制备方法不会有这方面的损失。
59.实施例2
60.本实施例的一种硼掺杂发射极的制备方法,具体参照实施例1,其与实施例1的区别仅在于:
61.步骤2中,采用pvd法在硅片1正面的绒面上沉积本征非晶硅层2。经本实施例的步骤2处理后的结构如图2所示。具体地,在磁控溅射反应腔中固定本征硅靶材,保持硅片1正面与靶材之间的距离为10-50cm;然后,在氩气氛围中,调整反应气压为0.5-1.0pa,沉积的工艺温度为250-300℃,沉积的反应时间为3-6min,即在硅片1正面的绒面上沉积该本征非晶硅层2。
62.步骤3中,在进行退火处理之前,预先对沉积本征非晶硅层2的硅片1正面进行离子注入处理,以获得硼掺杂的非晶硅层2。其中,离子注入处理的工艺参数包括:制备硼掺杂的
非晶硅层2所用的掺杂源为bf2,掺杂剂量为1-10e15.cm-2
。经本实施例的步骤3处理后的结构如图3所示。
63.具体地,离子注入处理的工艺参数为:bf2的掺杂剂量为8e15.cm-2
,离子注入的电压为2kev。
64.实施例3
65.本实施例的一种硼掺杂发射极的制备方法,具体参照实施例2,其与实施例2的区别仅在于:
66.步骤3中,在进行退火处理之前,预先对沉积本征非晶硅层2的硅片1正面进行硼扩散掺杂处理,以获得硼掺杂的非晶硅层2。其中,硼扩散掺杂处理的工艺参数包括:以bcl3或bbr3作为制备硼掺杂的非晶硅层2的掺杂气,在800-850℃下通入掺杂气和氧气,保温,即得硼掺杂的非晶硅层2。
67.具体地,步骤3的具体操作如下:将沉积非晶硅层2的硅片1放置于石英舟中,并将石英舟送入管式炉中,通入氮气作为管内气氛,升温至820℃,通入400sccm的bcl3和600sccn的氧气,在820℃下保持800s,如此,通过这样的硼扩散掺杂方式来获得硼掺杂的非晶硅层2,然后结束通源,再参照实施例2的步骤3对硅片1进行退火处理。本实施例中,在通过上述硼扩散掺的方式来获得硼掺杂的非晶硅层2的过程中,硅片1背面的边缘处会发生绕镀,所以,在退火处理后,硅片1背面的边缘处会依次形成硼掺杂发射极3和硼硅玻璃层4,而硅片1背面的中间位置则仍然会氧化形成二氧化硅层5。经本实施例的步骤3处理后的结构如图4所示。
68.对比例1
69.本对比例的一种硼掺杂发射极的制备方法,具体参照实施例1,其与实施例1的区别仅在于:
70.步骤5中,将硅片正面置于hf溶液中以去除硅片正面的硼硅玻璃层之后,省略了去除硅片正面的多晶硅层的相关操作,烘干硅片,即制得本对比例的正面具有硼掺杂发射极的硅片。由于本对比例与现有技术相似,均没有将硼掺杂的非晶硅层作为牺牲层,所以,本对比例的硼掺杂发射极包括了由硼掺杂的非晶硅层晶化所形成的硼掺杂的多晶硅层。
71.性能测试
72.1、采用德国wep公司的ecv测试仪,测试并获得实施例1-3、对比例1和传统制备硼掺杂发射极的方法(简称传统制备方法)所得的硅片(由于硼硅玻璃层在电池制作过程中需去除,所以,测试的硼掺杂发射极并不包括硼硅玻璃层,故而,制备完硼掺杂发射极后的硅片的表面也不含硼硅玻璃层)从硅片表层(即硼掺杂发射极表层)至硅片内部一定深度的硼掺杂ecv曲线,所得硼掺杂ecv曲线如图7-9所示。图7-9中,实施例1-3和传统制备方法的硼掺杂ecv曲线的深度是从硼掺杂发射极正表面至硅片体区内。而对比例1的硼掺杂ecv曲线的深度是从其硼掺杂的多晶硅层正表面至硅片体区内。
73.从图7-9可以看出,本发明实施例1-3的硼掺杂发射极的制备方法所形成的硼掺杂ecv曲线区别于传统制备方法的硼掺杂ecv曲线(参见图7-9),显然,本发明实施例1-3的硼掺杂发射极的制备方法所得硅片的硅片表层(即硼掺杂发射极表层)的硼掺杂浓度即为硼掺杂浓度最大值。
74.2、将实施例1、对比例1和传统制备方法所得的硅片的发射极区域进行方阻和俄歇
复合测试;将实施例1、对比例1和传统制备方法所得的硅片分别制成太阳能电池,对太阳能电池的金属复合、接触电阻及短路电流进行测试。以上测试结果参见如下表1。
75.表1
[0076][0077]
尽管已描述了本发明实施例的优选实施例,但本领域内的技术人员一旦得知了基本创造性概念,则可对这些实施例做出另外的变更和修改。所以,所附权利要求意欲解释为包括优选实施例以及落入本发明实施例范围的所有变更和修改。
[0078]
以上对本发明所提供的技术方案进行了详细介绍,本文中应用了具体个例对本发明的原理及实施方式进行了阐述,以上实施例的说明只是用于帮助理解本发明的方法及其核心思想;同时,对于本领域的一般技术人员,依据本发明的思想,在具体实施方式及应用范围上均会有改变之处,综上所述,本说明书内容不应理解为对本发明的限制。