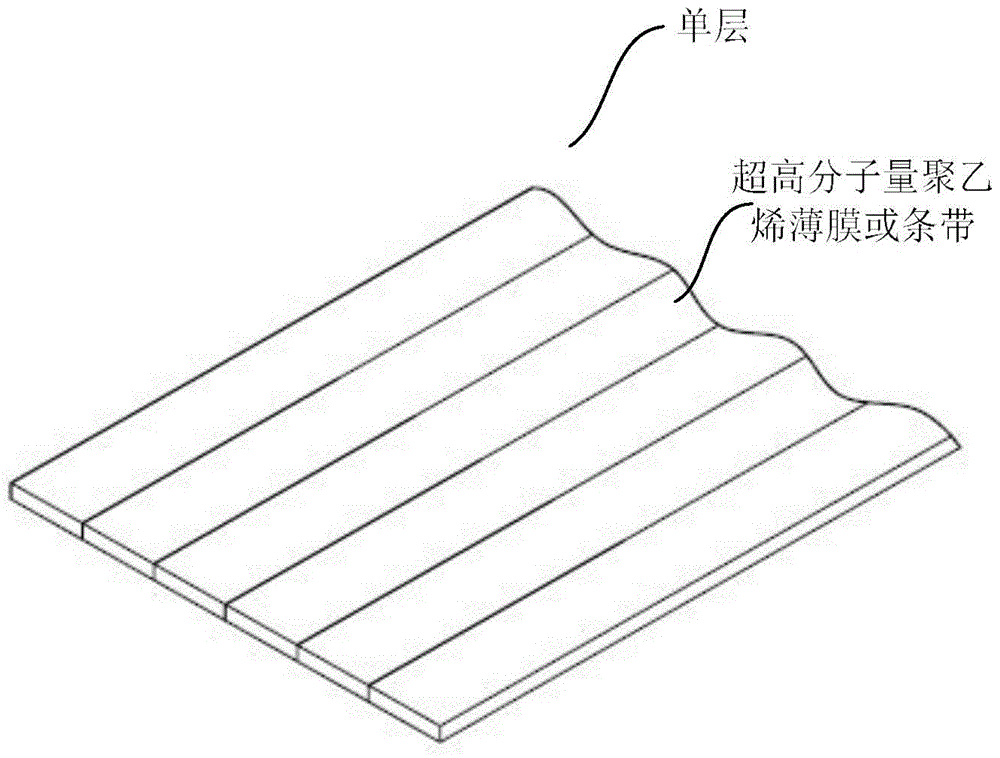
本申请涉及高分子材料应用技术领域,特别是涉及一种织物及其制备方法和一种防护制品。
背景技术:超高分子量聚乙烯(UltraHighMolecularWeightPolyethylene,简称UHMW-PE)是一种线型结构的具有优异综合性能的热塑性工程塑料,以这种材料为基础制成高强纤维是其最重要用途之一。超高分子量聚乙烯(UHMW-PE)纤维是一种合成纤维,其分子结构具有很高的伸直平行度和取向度,这种分子结构决定了超高分子量聚乙烯纤维具有极高的强度和模量,并具有良好的化学稳定性、耐腐蚀性等优点。超高分子量量聚乙烯(UHMW-PE)纤维的上述特性,已超越芳纶纤维平纹织物,广泛应用在军事、警用防弹防护领域,成为该领域替代传统钢结构防弹材料中的主流材料。以超高分子量聚乙烯纤维为带材的织物通常可采用如下工艺制备;将多根超高分子量聚乙烯纤维经过均匀、平行、挺直等处理使其沿一个方向排列整齐,用绑扎线作为经线或纬线绑扎形成一单层,绑扎线的熔融温度T1低于超高分子量聚乙烯纤维的熔点T2,之后采用介于T1和T2之间的一温度T3热压固结该单层。采用同样的方法制备多个单层,多个单层叠设即可制得所需的织物。上述技术对超高分子量聚乙烯纤维的处理工艺复杂、繁琐,在织物的形成过程中需要对每个单层都分别进行热压固结处理,效率较低,并且每次的热压处理对各单层的聚合物性能会造成一定程度的损害,由此降低多个单层所制备的织物的强度、防弹等性能。
技术实现要素:在下文中给出关于本申请的简要概述,以便提供关于本申请的某些方面的基本理解。应当理解,这个概述并不是关于本申请的穷举性概述。它并不是意图确定本申请的关键或重要部分,也不是意图限定本申请的范围。其目的仅仅是以简化的形式给出某些概念,以此作为稍后论述的更详细描述的前序。本申请实施例提供一种织物及其制备方法和一种防护制品。第一方面,本申请实施例提供了一种织物的制备方法,包括:依次连续平行铺展多片超高分子量聚乙烯薄膜或条带,形成一单层;在当前形成的所述单层上依次连续铺展多片超高分子量聚乙烯薄膜或条带,形成另一单层;重复此步骤,直至形成叠设的N个单层,其中,所述N个单层中至少二个相邻的单层交叉呈一定角度,N为大于或等于2的整数;采用捆绑纱将所述N个单层上下穿插捆绑为一个整体。结合本申请实施例提供的任一种织物的制备方法,可选的,在铺展多片所述超高分子量聚乙烯薄膜或条带形成一相应单层之前,所述方法还包括:在至少一片所述超高分子量聚乙烯薄膜或条带表面涂覆粘合剂;干燥涂覆的所述粘合剂。结合本申请实施例提供的任一种织物的制备方法,可选的,采用微凹辊在至少一片所述超高分子量聚乙烯薄膜或条带表面涂覆所述粘合剂。结合本申请实施例提供的任一种织物的制备方法,可选的,所述粘合剂包括以下一种或几种的混合物:聚苯乙烯异戊二烯共聚物、聚苯乙烯三嵌段共聚体、氢化聚苯乙烯三嵌段共聚体、乙烯醋酸乙烯酯共聚物、乙烯丙烯酸共聚物、水性聚氨酯。结合本申请实施例提供的任一种织物的制备方法,可选的,粘合剂含量为0.3%~20%,其中,所述粘合剂含量为:涂覆的所述粘合剂与涂覆有所述粘合剂的单张所述超高分子量聚乙烯薄膜或条带的重量比值。较佳的,所述粘合剂含量为1%~15%。优选的,所述粘合剂含量为3%~12%。结合本申请实施例提供的任一种织物的制备方法,可选的,在所述超高分子量聚乙烯薄膜或条带表面涂覆所述粘合剂之前,还包括:对待涂覆所述粘合剂的所述超高分子量聚乙烯薄膜或条带进行表面改性处理。较佳的,所述表面改性处理包括:电晕处理待涂覆所述粘合剂的所述超高分子量聚乙烯薄膜或条带的上表面和/或下表面。较佳的,所述电晕处理的功率为0.1Kw~3Kw。较佳的,所述电晕处理的功率为0.3Kw~2Kw。优选的,所述电晕处理的功率为0.5Kw~1Kw。结合本申请实施例提供的任一种织物的制备方法,可选的,形成任一单层过程中,在一所述超高分子量聚乙烯薄膜或条带的两端施加0.1克/旦~8克/旦的张力,以伸直铺展所述超高分子量聚乙烯薄膜或条带。较佳的,所述张力为0.4克/旦~5克/旦。优选的,所述张力为0.5克/旦~3克/旦。结合本申请实施例提供的任一种织物的制备方法,可选的,形成任一单层过程中,任二片相邻的所述超高分子量聚乙烯薄膜或条带之间无间隙、或有间隙且间隙小于或等于10mm。较佳的,所述间隙小于或等于5mm。较佳的,所述间隙小于或等于3mm。优选的,所述间隙小于或等于2mm。结合本申请实施例提供的任一种织物的制备方法,可选的,所述方法还包括:热压所述N个单层经所述捆绑纱上下穿插捆绑成的所述整体。结合本申请实施例提供的任一种织物的制备方法,可选的,所述热压的控制条件包括:温度40℃~160℃,和/或,压力0.5MPa~30MPa。结合本申请实施例提供的任一种织物的制备方法,可选的,所述捆绑纱包括以下一种或多种的组合:聚酯纤维、聚烯烃纤维、聚酰胺纤维、超高分子量聚乙烯纤维或条带。结合本申请实施例提供的任一种织物的制备方法,可选的,所述超高分子量聚乙烯薄膜的相关参数至少满足以下一种或多种:线密度在5000旦以上;宽度100mm以上;厚度0.2mm以下;断裂强度在10克/旦以上;拉伸模量在800克/旦以上;断裂伸长率在6%以下。结合本申请实施例提供的任一种织物的制备方法,可选的,所述超高分子量聚乙烯条带的相关参数至少满足以下一种或多种:线密度在100旦以上;宽度1-100mm;厚度0.2mm以下;断裂强度在10克/旦以上;拉伸模量在800克/旦以上;断裂伸长率在6%以下。结合本申请实施例提供的任一种织物的制备方法,可选的,任一片所述超高分子量聚乙烯薄膜或条带的铺展方向为其宽度方向。较佳的,所述超高分子量聚乙烯薄膜或条带的宽度方向为垂直所述超高分子量聚乙烯薄膜或条带的分子链伸直方向。第二方面,本申请实施例提供了一种采用本申请实施例提供的任一种织物的制备方法制备得到的织物。第三方面,本申请实施例提供了一种织物,所述织物由捆绑纱将N个单层上下穿插捆绑而成,其中,任一所述单层包括依次连续平行铺展多片超高分子量聚乙烯薄膜或条带,所述N个单层中至少二个相邻的单层交叉呈一定角度,N为大于或等于2的整数。结合本申请实施例提供的任一种织物,可选的,至少一片所述超高分子量聚乙烯薄膜或条带表面涂覆有粘合剂。结合本申请实施例提供的任一种织物,可选的,所述粘合剂包括以下一种或几种的混合物:聚苯乙烯异戊二烯共聚物、聚苯乙烯三嵌段共聚体、氢化聚苯乙烯三嵌段共聚体、乙烯醋酸乙烯酯共聚物、乙烯丙烯酸共聚物、水性聚氨酯。结合本申请实施例提供的任一种织物,可选的,粘合剂含量为0.3%~20%,其中,所述粘合剂含量为:涂覆的所述粘合剂与涂覆有所述粘合剂的单张所述超高分子量聚乙烯薄膜或条带的重量比值。较佳的,所述粘合剂含量为1%~15%。优选的,所述粘合剂含量为3%~12%。结合本申请实施例提供的任一种织物,可选的,任一所述单层中,任二片相邻的所述超高分子量聚乙烯薄膜或条带之间无间隙、或有间隙且间隙小于或等于10mm。较佳的,所述间隙小于或等于5mm。较佳的,所述间隙小于或等于3mm。优选的,所述间隙小于或等于2mm。结合本申请实施例提供的任一种织物,可选的,所述捆绑纱包括以下一种或多种的组合:聚酯纤维、聚烯烃纤维、聚酰胺纤维、超高分子量聚乙烯纤维或条带。结合本申请实施例提供的任一种织物,可选的,所述超高分子量聚乙烯薄膜的相关参数至少满足以下一种或多种:线密度在5000旦以上;宽度100mm以上;厚度0.2mm以下;断裂强度在10克/旦以上;拉伸模量在800克/旦以上;断裂伸长率在6%以下。结合本申请实施例提供的任一种织物,可选的,所述超高分子量聚乙烯条带的相关参数至少满足以下一种或多种:线密度在100旦以上;宽度1-100mm;厚度0.2mm以下;断裂强度在10克/旦以上;拉伸模量在800克/旦以上;断裂伸长率在6%以下。结合本申请实施例提供的任一种织物,可选的,任一片所述超高分子量聚乙烯薄膜或条带的铺展方向为其宽度方向。较佳的,所述超高分子量聚乙烯薄膜或条带的宽度方向为垂直所述超高分子量聚乙烯薄膜或条带的分子链伸直方向。第四方面,本申请实施例提供了一种防护制品,包括本申请实施例提供的任一种所述织物。本申请实施例提供的织物的制备方法,工艺简单易行,生产效率高,对设备精度要求较低,有利于降低设备购置成本。采用本申请实施提供的制备方法进行织物的制备过程中,各单层中各片超高分子量聚乙烯薄膜或条带处于同一排列方向的伸直状态,层间无交织或穿插,在完成一单层的制备之后,在该单层的基础上以一定角度重叠铺设另一单层,由此制备得到的N个单层再通过捆绑纱上下穿插捆绑成一个整体,整个制备工艺无需对各个单层的热压等处理,由此在织物的制备过程中减少了对各个单层的超高分子量聚乙烯薄膜或条带性能的损伤概率;此外,由于多个呈一定角度堆叠铺设的单层以及捆绑纱的存在,能够有效提高织物层间性能、充分利用超高分子量聚乙烯薄膜或条带的性能,改善织物拉伸、抗拉、抗冲击等力学性能。本申请实施例提供的织物,可由本申请实施例提供的织物制备方法制得,或者,可采用其他方法制得,所述织物包括的各单层中每片超高分子量聚乙烯薄膜或条带层完全伸直且平行排列,不同单层通过捆绑纱上下穿插连接,形成具有一定角度叠置的双层或多层织物,其可设计性好,具有柔软的手感和较高的抗拉强度,织物的结构整体性好,有利于后道应用加工。本申请实施例提供的防护制备,包括本申请实施例提供的任一种所述织物,具有重量轻、抗冲击性能和防弹性能好等优点,应用广泛。附图说明为了更清楚地说明本申请实施例或现有技术中的技术方案,下面将对实施例或现有技术描述中所需要使用的附图作简单地介绍,显而易见地,下面描述中的附图仅仅是本申请的一些实施例,对于本领域普通技术人员来讲,在不付出创造性劳动性的前提下,还可以根据这些附图获得其他的附图。图1为本申请实施例提供的织物的制备方法的流程图;图2为本申请实施例多片超高分子量聚乙烯薄膜或条带平行铺展形成的单层的结构示例;图3a为本申请实施例基于超高分子量聚乙烯薄膜或条带制得的经编双轴向织物结构示例一;图3b为本申请实施例基于超高分子量聚乙烯薄膜或条带制得的经编双轴向织物结构示例二。本领域技术人员应当理解,附图中的元件仅仅是为了简单和清楚起见而示出的,而且不一定是按比例绘制的。例如,附图中某些元件的尺寸可能相对于其他元件放大了,以便有助于提高对本申请实施例的理解。具体实施方式为使本申请实施例的目的、技术方案和优点更加清楚,下面将通过文字和/或结合附图对本申请实施例中的技术方案进一步进行清楚、完整地描述,显然,所描述的实施例是本申请一部分实施例,而不是全部的实施例。为了清楚和简明起见,在说明书中并未描述实际实施方式的所有特征。然而,应该了解,在开发任何这种实际实施例的过程中必须做出很多特定于实施方式的决定,以便实现开发人员的具体目标,例如,符合与系统及业务相关的那些限制条件,并且这些限制条件可能会随着实施方式的不同而有所改变。此外,还应该了解,虽然开发工作有可能是非常复杂和费时的,但对得益于本公开内容的本领域技术人员来说,这种开发工作仅仅是例行的任务。在此,还需要说明的一点是,在本申请的一个附图或一种实施方式中描述的元素和特征可以与一个或更多个其它附图或实施方式中示出的元素和特征相结合,为了避免因不必要的细节而模糊了本申请,在附图和说明中仅仅描述了与根据本申请的方案密切相关的装置结构和/或处理步骤,而省略了对与本申请关系不大的、本领域普通技术人员已知的部件和处理的表示和描述。基于本申请中的实施例,本领域普通技术人员在没有付出创造性劳动前提下所获得的所有其他实施例,都属于本申请保护的范围。本领域技术人员可以理解,本申请中的“第一”、“第二”等术语仅用于区别不同步骤、设备或模块等,既不代表任何特定技术含义,也不表示它们之间的必然逻辑顺序。本申请实施例提供了一种织物的制备方法,如图1所示,所述织物的制备方法包括:S101:依次连续平行铺展多片超高分子量聚乙烯薄膜或条带,形成一单层。超高分子量聚乙烯薄膜是一种由超高分子量聚乙烯制成的、具有一定宽度和厚度的薄片,且宽度远远大于厚度。超高分子量聚乙烯条带可独立制备或可由该薄膜拉伸前后进行分切工序形成的条状薄片,条带的宽度小于薄膜的宽度,厚度与薄膜相当或小于薄膜的厚度。本申请提供的超高分子量聚乙烯薄膜或条带,与超高分子量聚乙烯纤维不同,与由多根超高分子量聚乙烯纤维胶接形成的平面也不同,它们的显著区别在于:本申请提供的超高分子量聚乙烯薄膜或条带本身具有一定的宽度和厚度,是一种没有结合点或裁切线的整体结构。可将多片超高分子量聚乙烯薄膜或条带按照某一方向依次连续平行铺展,使得所述多片超高分子量聚乙烯薄膜或条带处于沿同一方向的伸直状态,如此可形成一单层,如图2所示。S102:在当前形成的所述单层上依次连续铺展多片超高分子量聚乙烯薄膜或条带,形成另一单层;重复此步骤,直至形成叠设的N个单层,其中,所述N个单层中至少二个相邻的单层交叉呈一定角度,N为大于或等于2的整数。不同单层的制备方式相似,其中,上一单层是在下一单层上铺展的,二个相邻单层的超高分量聚乙烯薄膜或条带的伸直方向交叉呈一定角度,所述角度可为0-±180度之间的任一角度,可根据织物的用途选择不同的角度铺设相邻单层,本申请实施例对此并不限制,实现方式非常灵活,例如可为±30度、±45度、±90度等等。不同相邻单层之间的交叉角度可根据实际需要确定,例如,N个单层可依次呈“0度—90度—0度—90度……”交替变化,也可依次呈“0度—30度—45度—90度……”依次递增,由此提高织物抗冲击、防弹等性能。制备好的N个单层,层间没有交织或穿插,相当于是以一定角度交叉堆叠的N个单层。S103:采用捆绑纱将所述N个单层上下穿插捆绑为一个整体。以一定角度交叉堆叠的N个单层制备完成之后,可用捆绑纱将所述N个单层上下穿插捆绑为一个整体,由此将N个单层固结以形成所述织物。形成的所述织物可以为机织物,或者,可为经编双轴向织物(如图3a和图3b所示),或者,可为经编多轴向织物,等等,织物的具体结构形态多样化,本申请实施例对此并不限制。本申请实施例提供的织物的制备方法,工艺简单易行,生产效率高,对设备精度要求较低,有利于降低设备购置成本。采用本申请实施提供的制备方法进行织物的制备过程中,各单层中各片超高分子量聚乙烯薄膜或条带处于同一排列方向的伸直状态,层间无交织或穿插,在完成一单层的制备之后,在该单层的基础上以一定角度重叠铺设另一单层,由此制备得到的N个单层再通过捆绑纱上下穿插捆绑成一个整体,整个制备工艺无需对各个单层的热压等处理,由此在织物的制备过程中减少了对各个单层的超高分子量聚乙烯薄膜或条带性能的损伤概率;此外,由于多个呈一定角度堆叠铺设的单层以及捆绑纱的存在,能够有效提高织物层间性能、充分利用超高分子量聚乙烯薄膜或条带的性能,改善织物拉伸、抗拉、抗冲击等力学性能。此外,本申请实施例织物制备的每个单层制备过程中,是将超高分子量聚乙烯薄膜或条带作为一个整体进行处理,结构整体性好、制备工艺简单,省去了对多根纤维丝进行分别整理的复杂工艺,明显降低了薄膜或条带的表面产生毛刺的概率,也明显降低薄膜或条带内部出现断丝、扭曲、缠绕等现象的概率,由此有利于保证所制备的织物获得强度、防弹等方面的较高性能。可选的,在铺展多片所述超高分子量聚乙烯薄膜或条带形成一相应单层之前,所述方法还包括:在至少一片所述超高分子量聚乙烯薄膜或条带表面涂覆粘合剂;干燥涂覆的所述粘合剂。本申请实施例在所述超高分子量聚乙烯薄膜或条带表面涂覆粘合剂,涂覆的粘合剂在织物的制备过程中几乎不起作用,即在所述织物制备过程中不同单层之间并非主要靠超高分子量聚乙烯薄膜或条带表面涂覆的粘合剂粘结的(是由捆绑纱将所述N个单层上下穿插为一整体),而是在后续应用中发挥主要作用,具体的,由于超高分子量聚乙烯薄膜或条带表面涂覆的粘合剂的存在,使得制备得到的织物在受到外界冲击,如受到外界子弹的冲击时,所述粘合剂可有效减小织物受弹击而造成分层的概率,由此提高织物制品的整体防弹等性能。所述粘合剂取材方便,可包括但不限于以下一种或几种的混合物:聚苯乙烯异戊二烯共聚物、聚苯乙烯三嵌段共聚体、氢化聚苯乙烯三嵌段共聚体、乙烯醋酸乙烯酯共聚物、乙烯丙烯酸共聚物、水性聚氨酯。这些粘合剂不会影响超高分子量聚乙烯薄膜或条带本身的性能,还有利于相邻单层的超高分子量聚乙烯薄膜或条带一定条件下粘合。优选粘合剂为KratonD1161、G1650、Estane5703和水性聚氨酯,取材方便,且涂胶过程中不会损坏超高分子量聚乙烯薄膜或条带的性能。所述粘合剂的涂覆方式可采用但不限于刮刀、喷涂、浸渍、热熔胶转移或微凹辊涂(microgravure)等,实现方式非常灵活。其中,微凹辊涂可采用直径一般在Φ20mm~Φ50mm之间的网纹涂布辊进行粘合剂的反向、接触式涂布,即微型涂布辊的旋转方向与超高分子量聚乙烯薄膜或条带的走料方向相反,微凹辊涂方式相对传统凹版涂布方式而言,无需背压辊,因此在涂布面上不会形成胶印、褶皱等缺陷,还可以对涂布料膜的边缘上胶,可精密控制超高分子量聚乙烯薄膜或条带表面粘合剂的含量。所述粘合剂含量是指涂覆的所述粘合剂与涂覆有所述粘合剂的单张所述超高分子量聚乙烯薄膜或条带的重量比值,可选的,所述粘合剂含量为0.3%~20%,较佳的,粘合剂含量为1%~15%,进一步较佳的,粘合剂含量为3%~12%,通过将所述超高分子量聚乙烯薄膜或条带的表面涂覆的粘合剂的含量控制在上述尽可能优选的范围,有利于实现在尽可能少的粘合剂的情况下,织物间的粘结力达到最佳效果,其织物制品在弹击后的分层概率尽可能降到最小。可选的,在所述超高分子量聚乙烯薄膜或条带表面涂覆所述粘合剂之前,还包括:对待涂覆所述粘合剂的所述超高分子量聚乙烯薄膜或条带进行表面改性处理。通过表面改性处理可有效降低超高分子量聚乙烯薄膜或条带的表面惰性,提高粘合剂与超高分子量聚乙烯薄膜或条带之间的粘结力。对所述超高分子量聚乙烯薄膜或条带表面改性处理的方式,可根据实际需要确定,例如可采用但不限于离子体处理法、辐照表面接枝法、电晕放电处理法、化学交联处理法等,实现方式非常灵活。其中,采用电晕放电处理法对超高分子量聚乙烯薄膜或条带进行表面改性处理,即电晕处理待涂覆所述粘合剂的所述超高分子量聚乙烯薄膜或条带的上表面和/或下表面,处理方法简单,便于控制,且表面改性效果好。可选的,所述电晕处理的功率为0.1Kw~3Kw,采用该功率范围对超高分子量聚乙烯薄膜或条带进行表面改性处理,可有效在不损伤超高分子量聚乙烯薄膜或条带表面性能的基础上,降低超高分子量聚乙烯薄膜或条带的表面惰性,提高其与粘合剂的粘结力。进一步的,所述电晕处理的功率为0.3Kw~2Kw,优选的,所述电晕处理的功率为0.5Kw~1Kw,通过对电晕处理的功率控制参数的不断优化,可进一步改善超高分子量聚乙烯薄膜或条带表面处理的效率和效果,由此进一步提高超高分子量聚乙烯薄膜或条带与其表面涂覆的粘合剂的粘结力,也有利于提高织物各单层间的粘结力。采用本申请实施例提供的任一技术方案形成任一单层过程中,可选的,可通过一定的张力控制使得各超高分子量聚乙烯薄膜或条带处于伸直且无褶皱的状态,例如,形成任一单层过程中,可在一所述超高分子量聚乙烯薄膜或条带的两端施加0.1克/旦~8克/旦的张力,以在不损伤超高分子量聚乙烯薄膜或条带性能的基础上,伸直铺展所述超高分子量聚乙烯薄膜或条带,由此避免因超高分子量聚乙烯薄膜或条带未伸直或发生褶皱而影响织物各层间的结合。进一步的,所述张力为0.4克/旦~5克/旦,优选的,所述张力为0.5克/旦~3克/旦,通过对张力控制参数不断优化,可进一步改善超高分子量聚乙烯薄膜或条带表面处理的铺设质量,由此实现织物至少二个单层相互间无松弛、无滑移、无褶皱铺层的效果,提高所制备的织物的整体性能。采用本申请实施例提供的任一技术方案形成任一单层过程中,可选的,任二片相邻的所述超高分子量聚乙烯薄膜或条带之间无间隙或者有很小的间隙,所述无间隙包括二片相邻的超高分子量聚乙烯薄膜或条带边缘紧密相邻或边缘处局部重叠等情形。由于超高分子量聚乙烯薄膜或条带存在一定的偏差,所谓的边缘紧密相邻而无缝隙是指在一定偏差允许范围内,边缘紧密相邻而无缝隙。通过将多片超高分子量聚乙烯薄膜或条带铺设呈无缝隙的单层,有利于提高织物的紧密性。可选的,任二片相邻的所述超高分子量聚乙烯薄膜或条带之间也可以留有很小的间隙,所述间隙小于或等于10mm,这样的间隙可使织物具有一定的紧密性的同时,还有利于降低制备工艺的精度要求。进一步的,所述间隙小于或等于5mm,较佳的,所述间隙小于或等于3mm,优选的,所述间隙小于或等于2mm,通过对任二片相邻的超高分子量聚乙烯薄膜或条带的间隙允许参数的设置,可在制备工艺精度和织物性能之间获得较好的平衡点。由于超高分子量聚乙烯薄膜或条带尺寸有一定的偏差,如所述超高分子量聚乙烯薄膜或条带的宽度存在一定的偏差,本申请实施例在某一单层中所述的任二片相邻的超高分子量聚乙烯无间隙或有很小的间隙,都是相对超高分子量聚乙烯薄膜或条带的宽度偏差容许范围而言,所述宽度偏差容许低于2mm,较佳的,所述宽度偏差容许低于1mm,优选的,所述宽度偏差容许低于0.2mm,通过对超高分子量聚乙烯薄膜或条带的织物制备原材料的严格筛选,有利于提高工艺的精度控制。本申请实施例提供的任一种技术方案中,在采用捆绑纱将所述N个单层上下穿插捆绑呈一个整体之后,还可热压所述N个单层经所述捆绑纱上下穿插捆绑成的所述整体,以提高织物层间的粘合力。可选的,所述热压的控制条件包括:温度40℃~160℃,和/或,压力0.5MPa~30MPa,采用上述参数对所述整体进行热压处理,可有效减小热压处理对所述N个单层中各单层的超高分子量聚乙烯薄膜或条带的性能损伤,由此保证织物的性能。所述捆绑纱可根据实际应用需要进行选材,可以是单纱,也可以是复丝,本申请实施例对此并不限制。例如,所述捆绑纱可包括但不限于以下一种或多种的组合:聚酯纤维、聚烯烃纤维、聚酰胺纤维。上述材料的熔点都不高于本申请实施例上述的超高分子量聚乙烯薄膜或条带,由此在热压过程中选择的温度参数不会高于超高分子量聚乙烯薄膜或条带的熔点。或者,所述捆绑纱还可包括但不限于超高分子量聚乙烯纤维或条带,采用超高分子量聚乙烯纤维或条带作为多个所述单层的捆绑纱,由于材料特性相同或相似,可达到更佳的捆绑效果。可选的,所述超高分子量聚乙烯薄膜的相关参数满足以下一个或多个条件:线密度大于或等于5000旦;宽度大于或等于100mm;厚度小于或等于0.2mm;断裂强度大于或等于10克/旦;拉伸模量大于或等于800克/旦;断裂伸长率小于或等于6%。较佳的,所述超高分子量聚乙烯薄膜满足以下一个或多个条件:厚度为0.001-0.2mm,断裂强度为10-50克/旦,拉伸模量为800-2600克/旦,断裂伸长率为0.5-6%。进一步,较佳的,所述超高分子量聚乙烯薄膜的线密度为6000-80000旦,宽度为100-400mm,厚度为0.005-0.15mm,断裂强度为12-48克/旦,拉伸模量为1000-2500克/旦,断裂伸长率为0.8-4%。较佳的,所述超高分子量聚乙烯薄膜满足以下一个或多个条件:线密度为7000-60000旦,宽度为105-300mm,厚度为0.008-0.12mm,断裂强度为15-45克/旦,拉伸模量为1200-2500克/旦,断裂伸长率为1-3%。较佳的,所述超高分子量聚乙烯薄膜满足以下一个或多个条件:线密度为8000-40000旦,宽度为110-220mm,厚度为0.01-0.1mm,断裂强度为16-42克/旦,拉伸模量为1400-2400克/旦,断裂伸长率为1.5-2.5%。通过对所述超高分子量聚乙烯薄膜参数的优化设置,可获得用于制备织物的较高性能的带材,由此提高织物的整体性能。可选的,所述超高分子量聚乙烯条带的相关参数满足以下一种或多种要求:线密度大于或等于100旦、小于5000旦;宽度1-100mm;厚度小于或等于0.2mm;断裂强度大于或等于10克/旦;拉伸模量大于或等于800克/旦;断裂伸长率小于或等于6%。较佳的,所述超高分子量聚乙烯条带满足以下一种或多种要求:厚度为0.001-0.2mm,断裂强度为10-50克/旦,拉伸模量为800-2600克/旦,断裂伸长率为0.5-6%。较佳的,所述超高分子量聚乙烯条带满足以下一种或多种要求:线密度为150-4000旦,宽度为2-90mm,厚度为0.003-0.1mm,断裂强度为12-48克/旦,拉伸模量为1000-2500克/旦,断裂伸长率为0.8-4%。较佳的,所述超高分子量聚乙烯条带满足以下一种或多种要求:线密度为200-3500旦,宽度为3-80mm,厚度为0.005-0.06mm,断裂强度为15-45克/旦,拉伸模量为1200-2400克/旦,断裂伸长率为1-3%。较佳的,所述超高分子量聚乙烯条带满足以下一种或多种要求:线密度为300-3000旦,宽度为5-60mm,厚度为0.008-0.03mm,断裂强度为16-42克/旦,拉伸模量为1400-2400克/旦,断裂伸长率为1.5-2.5%。通过对所述超高分子量聚乙烯条带参数的优化设置,可获得用于制备织物的较高性能的带材,由此提高织物的整体性能。可选的,任一片所述超高分子量聚乙烯薄膜或条带的铺展方向为其宽度方向,较佳的,所述超高分子量聚乙烯薄膜或条带的宽度方向为垂直所述超高分子量聚乙烯薄膜或条带的分子链伸直方向。所述超高分子量聚乙烯薄膜或条带的分子链伸直方向为超高分子量聚乙烯的纵向拉伸方向,是指超高分子量聚乙烯纵向被拉伸后,其大分子链自觉的沿着纵向受力方向而排列的方向。由于超高分子量聚乙烯具有线性结构,超高分子量聚乙烯薄膜或条带沿其分子链伸直方向的强度最大,故沿其分子链伸直方向铺设超高分子量聚乙烯薄膜或条带,有利于提高超高分子量聚乙烯薄膜或条带的强度利用率,进而提高织物的强度等性能。本申请实施例提供的任一种织物或采用任一种制备方法制备得到的织物,各单层中每片超高分子量聚乙烯薄膜或条带层完全伸直且平行排列,不同单层通过捆绑纱上下穿插连接,形成具有一定角度叠置的双层或多层织物,其可设计性好,具有柔软的手感和较高的抗拉强度,织物的结构整体性好,有利于后道应用加工。所述织物的应用可包括但不限于用于制备防护制品,所述防护制品可包括但不限于以下一种或多种:防弹插板、防弹头盔、装甲背衬、直升机座椅、舱门或其他类型的防弹制品等,测试表明,采用所述织物制备的防制品具有优良的抗冲击性能和防弹性能。实施例1采用超高分子量聚乙烯薄膜来制备织物,其中超高分子量聚乙烯薄膜宽度为120mm,厚度为0.025mm,线密度为19000D,断裂强度为27克/旦,拉伸模量为1600克/旦,断裂伸长率为1.9%。单层所需的超高分子量聚乙烯薄膜的片数可根据所需的单层的宽度以及单根超高分子量聚乙烯薄膜的宽度确定,如可将32片上述超高分量聚乙烯薄膜紧密相邻平行铺展形成一单层,在该单层上依次连续铺设32片上述超高分量聚乙烯薄膜形成另一单层,相邻两个单层的超高分子量聚乙烯薄膜的铺设角度成90度,二个单层都铺设完成之后,采用线密度为300D的超高分子量聚乙烯条带作为捆绑纱将二层所述单层上下穿插为一个整体,由此形成的织物为经编双轴向织物。将216层上述经编双轴向织物进行堆叠,堆叠之后在温度125℃、压力20MPa的控制条件下进行热压成板材,由此制得防护制品A。经测试,该防护制品A的面度为6.5kg/m2。采用7.62mm专用发射器配1.1g破片,对该防护制品A进行检测,测得V50(穿透概率为50%)弹道极限值为725m/s。将900层上述经编双轴向织物进行堆叠,堆叠之后进行热压成板材,由此制得防护制品B。经测试,该防护制品B的面度为21kg/m2。按照GA141-2010标准对防护制品B进行性能测试,测试弹速为736m/s,经过测试,测得防护制品B的防弹性能能够满足GA1415级标准。实施例2采用超高分子量聚乙烯条带来制备织物,其中超高分子量聚乙烯条带宽度为50mm,厚度为0.012mm,线密度为5000D,断裂强度为29克/旦,拉伸模量为1800克/旦,断裂伸长率为1.8%。单层所需的超高分子量聚乙烯条带的片数可根据所需的单层的宽度以及单根超高分子量聚乙烯条带的宽度确定,如可将24片上述超高分量聚乙烯条带以很小间隙(小于2mm)依次平行铺展形成一单层,在该单层上依次连续铺设24片上述超高分量聚乙烯条带形成另一单层,相邻两个单层的超高分子量聚乙烯条带的铺设角度成90度,二个单层都铺设完成之后,采用线密度为300D的超高分子量聚乙烯条带作为捆绑纱将二层所述单层上下穿插为一个整体,由此形成的织物为经编双轴向织物。将96层上述经编双轴向织物进行堆叠,由此制得防护制品C。经测试,该防护制品C的面度为6kg/m2。采用7.62mm专用发射器配51式7.62mm增减药弹,对该制品进行检测,测得V50(穿透概率为50%)弹道极限值为630m/s。将55层上述经编双轴向织物进行堆叠,由此制得防护制品D。经测试,该防护制品D的面度为3.5kg/m2。按照NIJ0101.04中ⅢA级要求进行测试,弹速为436m/s。经过测试,测得该防护制品D防弹性能能够满足NIJ0101.04ⅢA级要求。实施例3采用超高分子量聚乙烯薄膜来制备织物,其中超高分子量聚乙烯薄膜宽度为120mm,厚度为0.025mm,线密度为19000D,断裂强度为27克/旦,拉伸模量为1600克/旦,断裂伸长率为1.9%。对待使用的各单片超高分子量聚乙烯薄膜进行上胶,粘合剂选用水性聚氨酯乳液,通过微凹涂布方式进行涂覆,上胶量为6.5%。将上完胶的5片超高分子量聚乙烯薄膜紧密相邻平行铺展形成一单层,在该单层上依次连续铺设5片上述超高分量聚乙烯薄膜形成另一单层……采用同样的方法完成四个单层的铺设,这四个单层中超高分子量聚乙烯薄膜的铺设角度为“0度—30度—45度—90度”。四个单层都铺设完成之后,采用线密度为300D的超高分子量聚乙烯条带作为捆绑纱将二层所述单层上下穿插为一个整体,并对形成的整体在温度100℃、压力10MPa的控制条件下进行热压处理,由此形成的织物为经编双轴向织物。将100层上述经编双轴向织物进行堆叠,由此制得防护制品E。经测试,该防护制品E的面度为6kg/m2,防护制品可制成但不限于防弹头盔。采用GA141-2010警用防弹衣的测试标准进行弹击检测,防护制品E能够满足GA141-2010中2级要求。将175层上述经编双轴向织物进行堆叠,由此制得防护制品F。经测试,该防护制品F的面度为10.5kg/m2。采用GA141-2010警用防弹衣的测试标准和GA68-2008防弹防刺服技术要求分别进行弹击及穿刺检测,防护制品F防弹、防刺性能分别能够满足GA141-2010中3级要求和GA68-2008中的2级要求。总之,本申请实施例提供的基于超高分子量聚乙烯薄膜或条带的织物及其制品显示出极佳的防弹效果,可以有效的抵御子弹威胁。这种织物以重量轻、防弹效果好的优势可广泛用于防弹插板、防弹头盔、装甲背衬、直升机座椅等防护制品。在本申请上述各实施例中,实施例的序号仅仅便于描述,不代表实施例的优劣。对各个实施例的描述都各有侧重,某个实施例中没有详述的部分,可以参见其他实施例的相关描述。在本申请的装置和方法等实施例中,显然,各部件或各步骤是可以分解、组合和/或分解后重新组合的。这些分解和/或重新组合应视为本申请的等效方案。同时,在上面对本申请具体实施例的描述中,针对一种实施方式描述和/或示出的特征可以以相同或类似的方式在一个或更多个其它实施方式中使用,与其它实施方式中的特征相组合,或替代其它实施方式中的特征。应该强调,术语“包括/包含”在本文使用时指特征、要素、步骤或组件的存在,但并不排除一个或更多个其它特征、要素、步骤或组件的存在或附加。最后应说明的是:虽然以上已经详细说明了本申请及其优点,但是应当理解在不超出由所附的权利要求所限定的本申请的精神和范围的情况下可以进行各种改变、替代和变换。而且,本申请的范围不仅限于说明书所描述的过程、设备、手段、方法和步骤的具体实施例。本领域内的普通技术人员从本申请的公开内容将容易理解,根据本申请可以使用执行与在此所述的相应实施例基本相同的功能或者获得与其基本相同的结果的、现有和将来要被开发的过程、设备、手段、方法或者步骤。因此,所附的权利要求旨在在它们的范围内包括这样的过程、设备、手段、方法或者步骤。