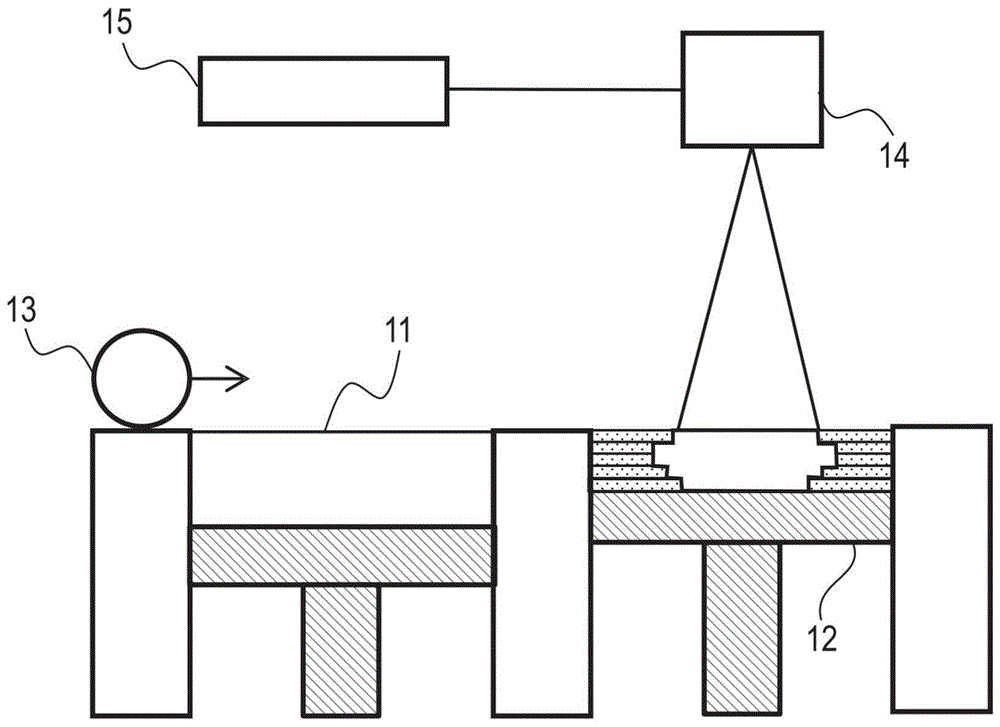
[
技术领域:
]本发明涉及在通过激光照射来形成陶瓷制造物时使用的粉体和使用该粉体的制造方法。[
背景技术:
:]近些年,增材制造技术已广泛传播,并且特别在金属领域中,在粉体床熔融方法中已实现了致密且多样的制造物。致密性归因于有效熔融且作为凝固组织群得到的制造物。在这样的状况下,还讨论了开发用于陶瓷制造的增材制造技术的可能性,并且报道了许多努力。为了采用与金属相同的方式熔融陶瓷,有必要注入相称的能量,但是与金属不同,状况是在粉体中发生光扩散,不可得到均匀的熔融,并且难以获得制造精度。因此,不熔融而简单地烧结陶瓷,并且因此追求确保制造精度来形成制造物,但是缺少致密性。在这样的状况下,例如npl1提出了使用了al2o3-zro2共晶系的方法,由此熔点降低,并且当共晶系熔融和凝固时,形成共晶系特有的细微结构,并且也实现了高的机械强度。然而,尽管事实是成功地满足了制造物的致密性改进,但是在制造物的表面上产生许多突起,状况是未能得到足够的制造精度。[引用列表][非专利文献]npl1:physicsprocedia5(2010)587至594[技术实现要素:][技术问题]激光的波长是nd:yag(大约1μm),并且即使当共晶系中沸点降低时,al2o3和zro2都没有明显地吸收光,需要相称的能量以便熔融和凝固材料体系。在这样的体系中,粉体中发生光散射,并且存在的问题是期望的制造部分不均匀地熔融,在期望的制造部分周围广泛产生不均匀的烧结区域等。此外,存在如下情况:通过吸收激光再次加工在激光扫描过程中已经加工的位置例如附近区域或层叠方向上的位置,存在不利地影响制造精度的问题。因此,为了改进制造精度,需要能够抑制粉体中的光扩散、吸收激光波长并且具有在制造位置降低或消失的吸收效果从而防止激光的再吸收及其影响的材料。[问题解决方案]本发明的陶瓷制造用粉体是用于通过在使用激光的照射部中重复地依次烧结或熔融并凝固粉体而获得制造物的陶瓷制造用粉体,其中该粉体包括多种组合物,所述多种组合物中的至少一种组合物是与其它组合物相比相对强地吸收激光的吸收体,并且该吸收体的至少一部分通过用激光照射而改变为相对弱地吸收激光的不同组合物。另外,用于通过在使用激光的照射部中重复地依次烧结或熔融并凝固粉体而获得制造物的陶瓷制造物的制造中,具有(i)在激光照射部中配置陶瓷制造用粉体的步骤,(ii)基于三维制造数据通过使用激光照射陶瓷制造用粉体来烧结或熔融并然后凝固该陶瓷制造用粉体的步骤,和(iii)通过重复步骤(i)和(ii)制造制造物的步骤。[发明有益效果]当使用本发明的陶瓷制造用粉体时,吸收体的一部分通过用激光照射而改变为相对弱地吸收激光的不同组合物,由此在随后的制造过程中激光照射不容易影响烧结或熔融区域。另外,吸收体与形成粉体的其它组合物相比相对强地吸收激光并因此也能够降低光扩散。结果是,能够实现具有高制造精度的陶瓷制造物的制造。[附图说明]图1是说明可应用本发明粉体的制造机的实例的示图。图2是说明可应用本发明粉体的制造机的另一实例的示图。图3是说明本发明的含有吸收体的粉体和不含有该吸收体的参照粉体的温度上升过程的概念图。图4是说明在激光照射区域和未照射区域之间边界部轮廓的偏差宽度(deflectionwidth)测量结果的示图。图5a是说明用激光照射本发明实施例8至25的粉体的过程的示图。图5b是说明用激光照射本发明实施例8至25的粉体的过程的示图。图6a是说明其中使用了本发明实施例8至25的粉体的制造物的示图。图6b是说明其中使用了本发明实施例8至25的粉体的制造物的示图。[具体实施方案]下文中,将参考附图描述本发明的实施方案。首先,将描述本发明中的粉体、组合物和吸收体。粉体是可被识别为独立微粒的颗粒的聚集体。另外,该粉体由多种组合物形成。组合物由多种组分(元素或化合物)构成。另外,粉体由多种组合物形成意味着以混合的方式存在由一种组合物形成的许多种颗粒的情况或者以混合的方式存在由多个种类的组合物形成的一种或许多种颗粒的情况。吸收体被定义为对于使用的激光而言比形成粉体的其他组合物具有相对强的吸收能力的组合物。换句话说,在粉体中包括的组合物中,吸收体具有对于激光而言最强的吸收能力。形成本发明粉体的至少一种组合物是具有激光吸收能力的吸收体。吸收体的吸收能力对于具有所用波长的激光而言优选为10%或更大的吸收率。另外,吸收率为40%或更大的情况是更优选的,并且此外吸收率为60%或更大的情况是最优选的。作为用于测量吸收体单一物质的吸收率的方法,可使用普通的分光计,并且通过使用假定波长(接近在制造过程中使用的激光波长)照射试样盘上装载的吸收体单一物质来测量吸收率。将不存在试样的情况下的吸收率视为参照数据,并且从其比率计算吸收率。(粉体)本发明的粉体由多种(两种或更多种)组合物构成,并且该多种组合物包括作为吸收体的至少一种组合物。形成粉体的各颗粒可由单一组合物形成,并且一个颗粒可由多种组合物形成。下文中,将顺序描述每种情况。第一种情况是粉体是由单一组合物形成的颗粒构成的状态的情况。例如,例示以下状态:其中多种组合物由al2o3、zro2和tb4o7(吸收体)的三种构成,分别存在al2o3颗粒、zro2颗粒和tb4o7颗粒,并且作为这些颗粒的混合物形成粉体。第二种情况是粉体包括由两种或更多种的组合物构成的颗粒的状态的情况。例如,在组合物由al2o3、zro2和tb4o7(吸收体)的三种构成的情况下,例示粉体单独由al2o3-zro2-tb4o7形成的颗粒构成的状态,或者al2o3-zro2形成相同颗粒使得颗粒被称作al2o3-zro2颗粒和tb4o7颗粒的状态。特别地,在相同的颗粒中与其它组合物一起含有吸收体的构成的情况下,优选通过在tb4o7(其为本发明吸收体的实例)中维持tb4o7状态来形成粉体。此外,不管其它组合物如何形成,作为吸收体的组合物单独形成颗粒的状况是优选的。另外,对于本发明的粉体而言,在粉体床熔融方法中使用再涂覆器构造粉体床层的情况下或者在包覆方法(claddingmethod)中从喷嘴喷射粉体的情况下,粉体的流动性是重要的。作为粉体,优选使用具有满足40[sec/50g]或更小的流动性指数的粉体。为了使流动性持续,颗粒优选具有球形形状。然而,只要满足了流动性指数,颗粒不必须具有球形形状。此外,形成吸收体的组合物的颗粒的粒径(粒径是指形成相同组成的不是单一颗粒而是颗粒群的中值)优选为不是吸收体的组合物的颗粒的粒径的1/5或更小。因此,形成吸收体的颗粒的粒径优选为1μm或更大且10μm或更小,因此重要的是除吸收体之外的组合物的粒径为5μm或更大并满足以上所述情况。另外,本发明的粉体优选不含有树脂粘合剂。这是因为在粉体含有树脂粘合剂的情况下,有时通过激光照射发生树脂粘合剂剧烈消失的过程,并且有可能树脂粘合剂可引起制造的区域中存在的孔隙等。此外,当含有碳时,碳键合至氧并变为气体,因此担心碳组分所占据的体积可变为孔隙,并因此碳的量优选是小的。因此,含有的碳以摩尔比计优选为形成粉体的多种组合物的金属元素的1000ppm或更少。另外,当含有碳时,碳被激光照射氧化并汽化,由此不利地影响制造,并因此与本发明的吸收体类似,碳优选被激光照射而改变为另一种组合物且并入制造物中。至此,已经描述了吸收体、组合物和颗粒,本发明中的陶瓷制造用粉体是否处于结晶状态或非晶状态、为它们的混合物等都没有关系。另外,粉体和制造物的组成不需要完全一致,并特别地可在氧化状态、氮化状态等方面不同。因此,优选控制制造过程中的气氛,并且还优选将气氛设定为不仅是大气条件还设定为氮或其它稀有气体气氛的不活泼状态,其中通过部分含有氢、减小压力等来促进还原的状态,以及进一步地氧气氛。这样的气氛控制没有排除包括处于部分金属状态的组合物作为原材料的粉体。本发明是陶瓷制造用粉体,但不限于由100%晶体制成的陶瓷来形成制造物的状态,并且在可获得期望的特性值的情况下,可在制造物的一部分或大部分中形成处于非晶态状态的区域、被还原为处于接近金属状态的区域等。(吸收体)本发明中优选的吸收体吸收激光,使用激光通过激光的热量烧结或熔融照射部位中的粉体以转化为凝固体,并保留在制造物中。此时,吸收体的一部分改变为具有相对弱的激光吸收能力的不同组合物且并入制造物中。因此,在吸收体转化为凝固体的区域中,比在用激光照射前的粉体中吸收了更小量的激光。将详细地描述本发明的吸收体的作用和效果。第一作用效果是吸收体高效地吸收在制造过程中使用的激光并提高温度,由此影响与激光的焦点尺寸一样大的区域中存在的其它组合物并提高温度。因此,实现了更有效的局部加热,使在加工区域(使用激光照射的区域)和未加工区域(未使用激光照射的区域)之间的边界部变得明晰,并且制造精度改进。第二作用效果是使用激光照射由此完成制造过程的区域吸收较少的光,因此能够抑制层内相邻区域(在其上即将执行工艺的部分中)或者下层中的区域再次吸收激光并改性。另外,抑制对完成制造的相邻区域或下层中的区域的影响,因此广泛地建立例如激光照射条件的工艺裕度,并且还能够减少照射条件的波动对制造精度的不利影响。在通过选择激光并使用激光照射本发明的陶瓷制造用粉体来进行制造的情况下,由于第一作用效果和第二作用效果可实现具有较高精度的制造。将参考作为概念图的图3来描述这样的状况。横轴表示激光照射时间,并且纵轴表示激光照射区域的温度。在图3中的线a和b中,线a表示不包括吸收体的粉体的特性。在线a中,通过激光照射温度开始提高,线性地超过熔点(这使粉体熔解)并达到由虚线表示的制造温度。在另一方面,线b表示本发明的包括吸收体的粉体的特性。在线b中,由于吸收体的光吸收效果、通过激光照射温度开始急剧提高,在粉体熔解之前吸收体的效果即刻弱化,并且温度升高速率变得接近粉体不包括吸收体的情况的线a的温度升高速率。在显示线a特性的粉体中,加热效率差,在用激光照射的区域中在已熔融和凝固的部分和粉体之间的边界中产生宽的低密度烧结部分,即使相邻的粉体部分也被广泛地影响,并且无法获得空间制造精度。在另一方面,在显示线b特性的粉体中,加热效率良好,并且实现了局部加热。因此,当形成了激光照射区域时,可充分地确保与相邻区域的温度差,因此在已熔融和凝固的部分和粉体之间的边界中仅产生窄的烧结部分,获得了良好的制造精度。此外,已用激光照射的完全制造部分不吸收光并显示与线a的特性类似的特性,并因此即使当工艺条件波动并且激光影响已有的制造区域时,通过激光温度提高相对小,并且能够避免温度提高的影响。同时,正在用激光照射的区域和已照射的区域通过由于两个区域之间的热传导而引起的熔融而结合在一起,并因此维持在激光描画的线之间的边界部分的连接或强度。以这样的方式,在具有本发明线b的特性的情况下,可获得以上所述的两种效果。作为本发明的吸收体,只要吸收体的至少一部分通过激光照射改变为相对弱地吸收光的不同组合物,可在没有任何限制的情况下使用任何吸收体,但是吸收体优选选自金属氧化物。原因是在金属氧化物中由于温度提高引起的氧分离改变金属元素的价态,并且存在这样的金属氧化物,其容易改变为相对弱地吸收激光的不同金属氧化物(例如tb4o7→tb2o3,gdalo3中的钆(gd)位点被tb3+取代等)。另外,原因是金属氧化物还具有与形成陶瓷的其它组合物的高亲和力并且可并入制造物中。作为其中相对各种激光波长的价态改变作为吸收率的改变而起作用的金属氧化物,优选使用选自以下的金属的氧化物:ti、v、cr、mn、fe、co、ni、cu、zn、zr、nb、mo、hf、ta、w、in、sn、bi、ce、pr、sm、eu、tb和yb。对于nd:yag激光(1,070nm)(其为用于制造的典型激光)而言,优选使用tb或pr的氧化物,并且其氧化状态更优选为tb4o7或pr6o11。然而,金属氧化物不限于以上所述分子式的比率(组成比)的情况,只要可获得期望的吸收效果,还可使用具有不同比率或处于与其混合状态的金属氧化物。接下来,将作为实例详细地描述作为本发明吸收体的组合物最优选的氧化铽。氧化铽可处于不同状态,通常的实例为被称作tb4o7的状态和被称作tb2o3的状态。在分子式中,tb4o7的表示没有严格限制4:7的比率。此时,tb4o7是一半由tb4+形成并且另一半由tb3+形成的物质,但是tb2o3仅由tb3+形成。tb4o7的高红外吸收率在nd:yag激光的1,070nm附近显著,超过60%,并且在一些情况下达到70%。同时,当tb4+逐渐减少时,吸收率降低,并且在仅由tb3+形成的tb2o3状态下达到大约7%。因此,清楚的是tb4+的减少降低吸收率,这样地,作为吸收体,包括四价铽的氧化铽(tb4o7)优选作为实现本发明的组合物之一。另外,为了获得10%的吸收率(在测量吸收体单一物质时),tb4+的量需要为tb3+和tb4+总量的大约10%。这里,作为用于评价价态的方法,可应用x-射线吸收精细结构(xafs)。吸收端的升高能量(risingenergy)随着价态变化,因此可从其比率来评价价态。额外地,可通过驱使作为普通评价方法的x-射线光电子能谱法(xps)或化学分析电子能谱法(esca)、电子自旋共振(esr)等来评价价态。同时,在金属元素和氧之间的比率为2:3的氧化物中,金属元素稳定为3+价态,因此在转化为凝固体之后,氧化物以固溶状态存在于其他组合物中(例如y2o3或gd2o3,额外地r2o3(r:金属元素))。因此,已转化为制造凝固体的区域不显著吸收光。另外,还在多元素氧化物等中,在r3+是稳定的化合物中,r位点被tb取代,由此可实现相同的状态。另外,在zro2中,形成固溶体以有助于萤石结构的稳定化,并且也在此时,价态变为3+。如此,本发明的吸收体还充当形成制造物的材料。另外,为了获得本发明的效果,在通过使用激光照射来进行工艺之前和之后吸收率优选相差1.2倍或更大且更优选相差2倍或更大。供选择地,吸收率在进行工艺之前优选为50%或更大并且在进行了工艺之后为40%或更小。供选择地,吸收率在进行工艺之前优选为60%或更大并且在进行了工艺之后为20%或更小。从获得这种状况的观点优选使用tb4o7(其为吸收体实例)作为组合物。同时,该吸收率是吸收体单一物质的吸收率。只要在多种组合物中含有吸收体,就可获得其效果,但是作为吸收体的组合物的含量优选为粉体的0.5体积%或更大且53体积%或更小。这里,使用“体积%”的原因是由吸收体占据面积的尺寸相对于激光的照射尺寸(焦点尺寸)是重要的并且通过“摩尔%”的表示无法处理形成粉体的组合物中的改变。由在激光焦点尺寸中包括至少一个吸收体颗粒的必要性来确定以上描述的吸收体含量的下限值。由对形成制造物的主要组合物的影响来确定上限值。当激光焦点尺寸为10μm时,通过激光熔融的区域被认为是具有10μm直径的半球形形状,并且在该区域中存在具有1μm直径的吸收体的一个颗粒的状态下,吸收体的含量为大约0.5体积%,因此吸收体组合物的下限值优选设定为0.5体积%或更大。另外,关于上限值,当将tb4o7添加至通用为结构陶瓷的al2o3时,形成tb3al5o12。为了使用al2o3陶瓷的特性来形成具有tb3al5o12的复合体系,tb4o7的含量需要设定为53体积%或更小,并且在这种情况下,为少量的al2o3分散在tb3al5o12主相的晶界中的状况,并因此上限值优选为53体积%。另外,吸收体的粒径也是重要的,优选10μm或更小、更优选1μm或更大且10μm或更小、和最优选1μm或更大且5μm或更小。这里,本发明中的粒径限定由相同组合物形成的颗粒的颗粒尺寸分布的中值范围并且不意味着不包括该范围以外的粒径。另外,粒径的测量不仅适用于处于单晶状态的颗粒而且适用于多晶状态或聚集状态。作为吸收体的组合物可作为单一物质形成颗粒。在作为吸收体的组合物作为单一物质形成颗粒的情况下,当含有0.5体积%的吸收体,粒径为1μm,并且粉体层的装填密度为真密度的50%时,在10μm的激光焦点尺寸加热的区域(由焦点尺寸直径形成的半球形状的体积)中包括一个颗粒,并且获得吸收体效果。另外,在粒径为10μm的情况下,在100μm的激光焦点尺寸加热的区域中包括一个颗粒,因此按照激光焦点尺寸选择吸收体的粒径变得重要。从均一性的观点,在激光焦点尺寸中包括至少两个吸收体颗粒的状态是更优选的。在单个吸收体颗粒之间的间隔优选为100μm或更小且更优选50μm或更小。另外,还优选调节激光焦点尺寸使得可实现这样的状况。如以上所述,从制造精度的观点,当假定激光焦点尺寸的上限为100μm时,如以上所述,吸收体的粒径优选为1μm或更大且10μm或更小。然而,根据期望的制造精度,激光焦点尺寸可为100μm或更大。同时,从确保粉体流动性的观点,作为制造物的基材而不是吸收体的组合物的颗粒的颗粒尺寸分布的中值和形状期望为5μm或更大的球形形状。另外,吸收体的粒径在1μm或更大且10μm或更小的范围内并优选粒径尽可能小。其原因是出于吸收体在粉体中的分散性或者高填充密度的观点。另外,在本发明中,吸收体的粒径优选为除吸收体之外的组合物的粒径的1/5或更小。(除吸收体之外的组合物)作为除吸收体之外的组合物,例示作为陶瓷结构形成主要组分的组合物。这样的组合物显著有助于在最终制造物中的例如强度的特性,因此应该取决于用途而适当选择该组合物。因此,优选对于在制造过程中使用的激光的波长确定吸收体,由此从具有相对弱的吸收效果的金属氧化物选择作为一种或多种主要组分的组合物,并且还优选选择化合物或其混合物。特别地,作为通用的结构陶瓷,可使用氧化铝或氧化锆(稳定化和准稳定化)。此外,还能够使用氧化硅、氮化硅和氮化铝。氮化硅表现出激光吸收效果,但是具有在工艺前后没有改变的吸收率,因此不充当本发明的吸收体。此外,还能够选择陶瓷材料例如堇青石(2mgo·2al2o3·5sio2)、锆石(zro2·sio2)、莫来石(3al2o3·2sio2)、氧化钇、或钛酸铝。另外,组合物可为以上所述各种材料的混合物。另外,用作主要组分的组合物还可包括具有小于5μm的小直径的氧化硅颗粒。以下将详细描述氧化硅颗粒的功能。当使用激光照射陶瓷制造用粉体时,照射部中的吸收体吸收能量并产生热。小直径氧化硅具有小至低于5μm的粒径并且容易熔融,因此来自吸收体的热首先熔融在吸收体周围存在的小直径氧化硅颗粒。另外,熔融的小直径氧化硅颗粒将热传递至具有相对大粒径的其它颗粒,并且这些颗粒熔融。在使用激光照射的区域中熔融的小直径氧化硅颗粒软化、变形并在大面积中与具有相对大粒径的其它颗粒接触,由此高效地将热传递至颗粒的表面。因此,与不包括小直径氧化硅颗粒的情况相比,能够更均匀地将热传递至具有相对大粒径的其它颗粒。结果是,在熔融过程中陶瓷制造用粉体中的温度分布变小,取决于位置,在凝固过程中冷却速率变得均匀。因此,热应力降低,在凝固过程中微裂纹的产生受抑制,获得了具有少量微裂纹的陶瓷制造物。另外,作为不同的效果,在凝固过程中粉体中含有氧化硅组分或者氧化硅组分与用作主要组分的其它组合物形成化合物的情况下,热导率变得相对低,缓和在凝固过程中的急冷,并且微裂纹的产生受抑制。具有少量微裂纹的陶瓷制造物具有高的机械强度和低的水吸收比,因此可应用于需要强度和低的水吸收比的部件如真空装置组件。如上所述,小直径氧化硅颗粒的粒径小于由其它组合物形成的颗粒的粒径,并且直径优选小于5μm。在粉体由多个种类的颗粒构成的情况下,小直径氧化硅颗粒的粒径优选小于多个种类的颗粒中每种的粒径。其原因是当粒径小时,小直径氧化硅颗粒易于导致与吸收体一起熔融,并且软化的小直径氧化硅颗粒比其它颗粒分布更均匀,因此能够进一步使熔融过程中陶瓷制造用粉体中的温度分布变窄。从流动性的观点,小直径氧化硅颗粒优选具有球形形式,但是可具有各向异性的形状例如不规则形状、板状或针状。小直径氧化硅颗粒优选具有窄的颗粒尺寸分布。这是因为当颗粒尺寸彼此类似时,能够在陶瓷制造用粉体中较均匀地分布小直径氧化硅颗粒,并且当软化时,在由其它组合物形成的颗粒的表面上较均匀地分布小直径氧化硅颗粒。在陶瓷制造用粉体中包括的小直径氧化硅颗粒的质量优选为吸收体的颗粒质量的0.04%或更大且5.0%或更小。当包括0.04%或更多的sio2颗粒时,水吸收比可设为1.0%或更小,这是期望的。另外,当小直径氧化硅颗粒的质量为吸收体的颗粒质量的5.0%或更小时,在用作主要组分的组合物等的颗粒之间存在的几乎所有的小直径氧化硅颗粒熔融。不存在保持未熔融的小直径氧化硅颗粒(其可引起陶瓷制造物的机械强度降低),这是更期望的。另外,小直径氧化硅颗粒通过使用激光的照射而熔融并起加热介质的作用,然后小直径氧化硅颗粒中的一些变为玻璃并分布在陶瓷制造物的表面上和陶瓷制造物中。当在陶瓷制造用粉体凝固时在该粉体中包括大量的小直径氧化硅颗粒时,存在在陶瓷制造物中形成来源于小直径氧化硅颗粒的许多玻璃区域并且陶瓷制造物的机械强度降低的可能性。因此,小直径氧化硅颗粒的质量更优选为由作为主要组分的组合物形成的颗粒质量的1.0%或更小。本发明的粉体由多种组合物组成并且优选包括至少一种组分作为吸收体和氧化铝、氧化锆和氧化硅中至少任一种组分作为形成陶瓷结构的主要组分。由于它们的吸收能力比吸收体弱,氧化铝、氧化锆和氧化硅是优选的并且能够与许多材料体系一起形成共晶系,通过精细结构的发展而维持高强度,并获得降低熔点的效果。例如,在氧化铝中,在两种氧化物与作为吸收体的tb4o7的混合物的情况下,在制造过程中从tb4o7的改变产生与tb3al5o12或tbalo3相关的组合物。同时,在氧化锆中,tb4o7在tb3+状态下起稳定氧化锆为正方晶的作用。另外,还优选的是氧化铝和氧化锆同时被包括作为组合物并与吸收体一起形成三组分粉体。还能够不仅选择共晶组成还能够选择al2o3:zro2=85:15重量%、70:30重量%等。另外,无论状态(结晶或非晶)氧化硅优选形成为制造物。此外,氧化硅还优选不仅与吸收体一起形成两种氧化物的组合物,还形成包括氧化锆、氧化铝等的三组分或四组分粉体。此外,在含有氧化硅的制造物中,可包括锆石、莫来石、与吸收体的硅酸盐等。虽然本发明中没有限制,但是优选以形成共晶组成的关系含有多种组合物。共晶组成是处于共晶相图中所示的共晶点的组成;然而,在本发明的制造工艺中(其中使用激光),以极快的速度重复加热和冷却状态,并且该状态远离平衡状态。因此,共晶组成优选定义为形成共晶结构的组成范围,并且允许的裕度是从被称作共晶相图中的共晶组成的点的±10mol%的范围。接下来,优选包括不是吸收体的至少一种稀土氧化物。稀土氧化物的金属元素优选选自sc、y、la、ce、nd、sm、eu、gd、dy、ho、er、tm、yb和lu。在这种情况下,取决于组成,对于r2o3(根据情况为ro2)而言可形成ralo3、r3al5o12等,并且在组合物能够形成新的组合物的情况下,还优选使用该组合物。根据情况,组合物还优选为共晶组成。另外,由tb3+或pr3+形成的材料体系也是可应用的。(本发明的陶瓷制造用粉体的用途)在通过使用激光照射的制造物的制造工艺(制造方法)中使用本发明的陶瓷制造用粉体。制造工艺具有(i)在使用激光的照射部中配置以上所述本发明的陶瓷制造用粉体的步骤,(ii)基于三维制造数据使用激光照射陶瓷制造用粉体,由此烧结或熔融并然后凝固该陶瓷制造用粉体的步骤,和(iii)重复步骤(i)和(ii)以形成制造物的步骤。在本发明中烧结或熔融并然后凝固的表述不必然将粉体根本没有熔融的情况限定为烧结和不必然将没有粉体保持未熔融的情况限定为熔融。目前,还有术语“液相烧结”,并且各个术语的区域变得不明确。因此,解释中也没有排除烧结(由此粉体彼此粘结)、液相烧结(在其后存在熔解物质从而包围粉体)、和此外的熔解(在其后一些粉体保持未熔融)。另外,在本发明的制造工艺中,如果必要,在形成制造物的步骤之后,优选进行热处理。在这种情况下,加热方式不受限制并且可根据目的来选择和使用,例如电阻加热方法、感应加热方法、红外灯方法、激光方法或电子束方法。出于改进制造物的致密性或强度等的目的,热处理还适合于制造物的晶体晶粒直径的调节。另外,作为热处理中的釉料,不论有机材料或无机材料优选进行浸渍、涂敷等。在本发明的使用方法中,可通过将本发明的粉体铺开并平整并然后用激光照射粉体来进行步骤(i)和(ii)。另外,还可通过将本发明的粉体喷射至预定位置并用激光照射该预定位置来进行步骤(i)和(ii)。具体地,作为用于在使用激光的照射部中依次重复烧结或熔融和凝固并且获得制造物的方法,存在所谓的粉体床熔融方法或包覆方法。使用的激光波长未受限制,但是优选使用在透镜或纤维中被调节至10μm至2mm的期望焦点尺寸的激光。焦点尺寸是影响制造精度的参数之一,并且为了满足0.1mm的制造精度,同时根据情况,线宽度优选与其大约相同,并且100μm或更小的焦点尺寸是优选的。同时,连续进行或以脉冲模式进行用激光照射都没有关系。实例是nd:yag激光,并且波长接近1,070nm。将参考图1描述粉体床熔融方法。在这个方法中使用的机器包括粉体容器11、制造阶段部12、再涂覆部(recoaterportion)13、扫描器部14、激光源15等。作为动作,使用再涂覆部13操作粉体,同时粉体容器11和制造阶段部12适当上下移动,并且将粉体在比待制造的制造物更宽的区域中薄薄地铺开并平整。此外,使用从激光源15产生的激光和扫描器部14在粉体层上直接画出制造物的一个横截面形状。烧结或熔融并凝固画出的区域,重复这个操作以层叠制造物的横截面并形成最终制造物。将使用图2描述包覆方法。包覆方法是从包覆喷嘴21中存在的多个粉体供给孔22喷射粉体,并且用激光23照射聚集了粉体的区域,由此在期望的位置顺序地形成制造物的方法,并且具有能够将粉体制造为弯曲表面等的特性。以上描述的本发明的制造工艺能够稳定的制造并且能够获得确保制造精度的三维制造物。[实施例][实施例1]本实施例涉及通过含有本发明的吸收体来改进制造精度。为了使关于制造精度的差异变得明晰,通过用激光照射来熔融和凝固1.5mm厚的粉体丸粒,并且观察在用激光照射部和未照射部之间的边界中的状态。作为样品1,将al2o3粉体、gd2o3粉体、和tb4o7粉体的粉体混合物(组成比为al2o3:64.40体积%、gd2o3:32.73体积%和tb4o7:2.87体积%)形成为1.5mm厚的粉体丸粒并用具有100μm焦点直径和30w激光功率的nd:yag激光(1,070nm)以100mm/sec和250mm/sec的两种激光照射速率在40条以50μm间距排列的10mm长的线中照射。另外,作为比较样品1,单独使用al2o3粉体,并且作为比较样品2(gdtb),使用由alo3-al2o3共晶体形成的单一粉碎粉体(用于形成共晶体的原材料组成比为al2o3:64.40体积%、gd2o3:32.73体积%和tb4o7:2.87体积%),并且以与样品1相同的方式使用激光照射两种样品。作为本文采用的吸收体的实例的tb4o7处于不仅包括tb3+还包括tb4+的状态。另外,在体积组成计算中,使用al2o3:3.96[g/cm3]、gd2o3:7.40[g/cm3]和tb4o7:7.60[g/cm3]作为真密度。即使当这些真密度是稍微不同的值时,本发明的本质也不受影响。比较样品1不包括吸收体,并且比较样品2以gdalo3中的gd3+位点被tb取代的形式并且以很少存在tb4+并且吸收效果消失的状态存在。这两个没有吸收体效果的比较样品在250mm/sec的激光照射条件下保持几乎粉体状态,并且清楚地获得了在100mm/sec下熔解并然后凝固的结构。然而,样品不具有吸收效果,因此在加热状态下表面显著不平整,即使在凝固之后也无法获得在二维表面的制造物,并且形成了已局部熔融且凝固的颗粒滚动的状态。同时,在样品1中能够确认粉体混合物从250mm/sec充分熔解并且以平面形状形成二维制造物。另外,从紫外激发的荧光观察确认了在照射部中的制造物中tb4o7并入gdalo3的gd点位作为tb3+,并且与比较样品2中相同的吸收效果达到低的状态。从吸收体的价态发现了在样品1中,吸收体以吸收率为60%或更大的状态被混合至粉体中,并且在用激光照射之后,荧光观察显示很少存在四价吸收体并因此吸收率达到30%或更小。另外,在比较样品2中,荧光观察显示从制造之前的粉体状态吸收率为30%或更小并且即使在用激光照射之后吸收率没有改变仍为30%或更小。图4显示计算通过以下所观察的边界部分轮廓的偏差宽度的结果:即通过从显微照片以宽度3.83mm切出在用激光照射区域42和未照射区域41之间边界的图像而进行观察。比较样品1中宽度为391μm、比较样品2中宽度为273μm和样品1中宽度为85μm。另外,样品1中的已制造的区域和比较样品2的粉体在吸收体的效果方面处于相同状态,由此阐明了在样品1中在250mm/sec下吸收体起作用的粉体区域中能够进行制造并且已制造区域以250mm/sec很少起作用。从以上所述结果,发现了本发明的样品在制造精度方面比比较样品更有利,在工艺已完成的区域中没有再次受扰,能够获得制造物。另外,作为吸收体实例的金属氧化物tb4o7还具有4+的价态;然而,在已制造区域中价态降低至3+,由此吸收特性改变。取决于周围环境、材料构成、粉体层厚度等,激光的照射条件改变并因此不仅限于本实施例中描述的值。[实施例2]本实施例涉及添加作为吸收体候补物的tb4o7的效果。tb4o7在1,070nm附近吸收率为60%或更大的值,并且当形成仅tb3+的状态例如tb2o3时,吸收率达到30%或更小。在实施例1中,作为样品1,使用al2o3粉体、gd2o3粉体、和tb4o7粉体的粉体混合物(组成比为al2o3:64.40体积%、gd2o3:32.73体积%和tb4o7:2.87体积%),除此之外如表1中所示制备样品2、3、4和5以及比较样品3。此时,关于tb4o7粉体的粒径,使用粒径为大约2μm的粉体。以大约20μm的厚度在al2o3基材上铺开并平整这些粉体,然后使用nd:yag激光照射。条件为20μm的焦点尺寸、10w、50mm/sec和12条以50μm间距排列的4.5mm长的线。[表1]对于各个样品,以2mm的宽度范围观察在用激光照射区域和未照射区域之间的边界部分的宽度。结果示于表1中。在该表中,各个组合物的配混量(体积%)、边界部分的宽度(μm),并且添加tb4o7的效果表示为“优异◎”、“良好○”和“不可×”。同时,边界部分的宽度(偏差宽度)是基本上等效于制造物的侧表面的表面粗糙度的指标,并且随着该值提高,制造物的表面变得更粗糙。使用金属粉体制造的制造物的标准表面粗糙度据称为大约几十微米。因此,宽度与标准表面粗糙度相同的情况被评价为“◎”。在其它实施例中也同样,将在评价中使用相同的标准。在不包括吸收体的比较样品3中,在边界部分中产生了许多熔解物的颗粒,并且边界部分的宽度最宽。在另一方面,阐明了吸收体的添加(样品1至5)使边界部分的宽度变窄。即发现了该效果由包括本发明的吸收体来获得。特别地,确认了在样品1至3中宽度变得较窄。因此,阐明了当添加作为本发明的吸收体实例的tb4o7时,获得了表1中显示的测定结果,获得了在比没有添加吸收体的情况更宽的组成范围中制造精度改进的效果。[实施例3]本实施例涉及添加作为吸收体候补物的pr6o11(氧化镨)的效果。pr6o11或处于与其接近的价态在1,070nm附近吸收率为80%或更大的值,并且当例如pr2o3的pr3+状态多时,吸收率达到50%或更小。作为样品6,使用al2o3粉体、gd2o3粉体、和pr6o11粉体的粉体混合物(组成比为al2o3:63.85体积%、gd2o3:33.29体积%和pr6o11:2.86体积%)。此时,关于pr6o11粉体的粒径,使用粒径为大约2μm的粉体。在体积组成计算中,使用al2o3:3.96[g/cm3]、gd2o3:7.40[g/cm3]和pr6o11:7.20[g/cm3]作为真密度。即使当这些真密度是稍微不同的值时,本发明的本质也不受影响。采用与实施例2中相同的方式,以大约20μm的厚度在al2o3基材上铺开并平整这些粉体,然后使用nd:yag激光照射。条件为20μm的焦点尺寸、10w、50mm/sec和12条以50μm间距排列的4.5mm长的线。[表2]以2mm的宽度范围观察在用激光照射区域和未照射区域之间的边界部分的宽度。结果示于表2中。如表2中显示,各个组合物的配混量(体积%)如以上所示,并且边界部分的宽度为42.7μm,并且添加pr6o11的效果为“良好○”。与实施例2中的样品3相比,显示了边界部分的宽度窄,并且阐明了当添加作为本发明的吸收体实例的pr6o11时,获得了表2中显示的测定结果,并且获得了比没有添加吸收体的情况制造精度更加改进的效果。[实施例4]本实施例涉及吸收体相对于除吸收体之外的组合物的效果。在表3中显示所研究的组合物。在体积组成计算中,使用al2o3:3.96[g/cm3]、zro2:5.68、y2o3:5.01[g/cm3]和tb4o7:7.60[g/cm3]作为真密度。即使当这些真密度是稍微不同的值时,本发明的本质也不受影响。以大约20μm的厚度在al2o3基材上铺开并平整包括这些组合物的粉体,然后使用激光照射。关于条件,以50、100、200和500mm/sec的扫描速率在100μm的焦点尺寸和30w中以50μm间距画出两条4.5mm长的线,并彼此比较熔融状态。[表3]在比较样品4中的纯al2o3保持在al2o3可以线形熔融并凝固的状态直至100mm/sec;然而,在添加了吸收体的样品7中,al2o3可以线形熔融并凝固直至500mm/sec。在比较样品5中的纯zro2保持在zro2可以线形熔融并凝固的状态直至100mm/sec;然而,在添加了吸收体的样品8中,zro2可以线形熔融并凝固直至500mm/sec。另外,接近al2o3-zro2体系的共晶组成的比较样品6保持在比较样品可以线形熔融并凝固的状态直至200mm/sec;然而,在添加了吸收体的样品9中,该样品可以线形熔融并凝固直至500mm/sec。此外,接近al2o3-y2o3体系的共晶组成的比较样品7保持在比较样品可以线形熔融并凝固的状态直至200mm/sec;然而,在添加了吸收体的样品10中,该样品可以线形熔融并凝固直至500mm/sec。从以上所述结果,能够确认:作为将作为吸收体实例的tb4o7添加至各种体系的结果,可通过以较高的速率扫描使体系熔融和凝固。因此,无论材料体系,该吸收体有助于改进制造物的制造精度。[实施例5]本实施例涉及在含有吸收体情况下的3d制造性质。在表4和5中显示形成在本实施例中所使用的粉体的组合物的各个粒径。另外,作为这些组合物的颗粒,使用球形颗粒,除了使其充当吸收体的tb4o7和pr6o11。[表4]al2o3zro2·y2o3gd2o3y2o3sio2tb4o7pr6o11粒径[μm]203025232833[表5]关于实施的材料体系,在表6和7中显示体积组成。[表6][表7]在体积组成计算中,使用al2o3:3.96[g/cm3]、zro2·y2o3:6.05[g/cm3]、gd2o3:7.40[g/cm3]、y2o3:5.01[g/cm3]、sio2:2.20[g/cm3]、tb4o7:7.60[g/cm3]、pr6o11:7.20[g/cm3]、al2o3·zro2(85:15重量%):4.13[g/cm3]、al2o3·zro2(70:30重量%):4.46[g/cm3]和2mgo·2al2o3·5sio2:2.60[g/cm3]作为真密度。即使当这些真密度是稍微不同的值时,本发明的本质也不受影响。在本实施例的研究中,作为制造机,使用由3dsystems,inc.制造的prox(商品名)系列dmp100。从不包括吸收体的比较样品8和由多种包括吸收体的组合物构成的样品11至24,在表8中所示制造条件下制备6×6×6mm制造物。如以下所述测定制造性质。制造物没有形成形状:差“×”,前表面或侧表面粗糙:稍差“○”,可获得具有指定尺寸的制造物:良好“◎”。另外,对于所有的制造物,粉体层的厚度设为20μm,并且使用氧化铝板作为基材。粉体层的厚度是指将图1中的制造阶段部12下移的值,并且通过用激光照射在厚度方向上粉体层熔融和收缩,因此粉体层的表观厚度在重复层叠时逐渐增加,并收敛至67至133μm的范围。因此,表4和5中所示组合物的平均粒径大于在制造过程中的粉体层(20μm),这不会引起任何实际问题。对于可制造的制造物,使用由klatencorcorporation制造的alpha-step(商品名)测量表面粗糙度ra,并确认制造精度。与制造物的前表面相比,侧表面相对显著地粗糙,因此在侧表面上进行评价。另外,在计算过程中扫描宽度为1mm。[表8]如表8中所示,不含本发明吸收体的比较样品8与实施例1的比较样品1类似地部分熔解,但是作为层叠制造的结果不能够维持形状为制造物。其它样品11至24可致密地形成为层叠的制造物,并且可测量侧表面的表面粗糙度。显示了本发明的吸收体改进表面粗糙度,特别地,可获得表面粗糙度被抑制为大约几十微米的制造物,并且精确制造是可能的。[实施例6]本实施例涉及除吸收体之外的组合物是单独的颗粒的情况和组合物是相同颗粒的情况。进行与其中实施例5的样品13、al2o3和gd2o3是共晶粉体(al2o3和gdalo3的混合状态)并向其中混合tb4o7的样品比较,并且此外与其中样品15、al2o3和y2o3是共晶粉体(al2o3和y3al5o12的混合状态)并向其中混合tb4o7的样品比较。采用与实施例5中相同的方式,作为制造机,使用由3dsystems,inc.制造的prox(商品名)dmp100。在表11中所示制造条件下制备6×6×6mm制造物。如以下所述测定制造性质。制造物没有形成形状:差“×”,前表面或侧表面粗糙:稍差“○”,和可获得具有指定尺寸的制造物:良好“◎”。另外,对于所有的制造物,粉体层的厚度设为20μm,并且使用氧化铝板作为基材。[表9][表10][表11]如表11中所示,对于两种样品25和26,制造性质为良好“◎”,并且表面粗糙度也为大约几十微米。如以上所述,能够确认在使用其中组合物形成单独的颗粒的粉体的情况下和如在本实施例中在使用其中在相同的颗粒中包括除吸收体之外的组合物的粉体(如在样品13和样品25中和在样品15和样品26中)的情况下,制造性质良好。因此,显示了本发明吸收体的效果不依赖于排除了吸收体的粉体的构成。[实施例7]本实施例涉及在使用本发明吸收体的情况下允许激光的照射条件改变的程度的实例。使用al2o3粉体、gd2o3粉体、和tb4o7粉体的粉体混合物(组成比为al2o3:64.40体积%、gd2o3:32.73体积%和tb4o7:2.87体积%),其为实施例5的样品13的粉体构成,并且作为制造机,使用由3dsystems,inc.制造的prox(商品名)dmp200。使用激光的照射速率为500mm/s,激光的照射线间距固定为130μm,并且通过改变激光功率提高和降低在制造过程中的能量密度。粉体层的厚度设为25μm,并且使用氧化铝板作为基材。以表12中所示激光功率制备6×6×6mm制造物,并且如以下所述测定制造性质。制造物没有形成形状:差“×”,前表面或侧表面粗糙:稍差“○”,和可获得具有指定尺寸的制造物:良好“◎”。[表12]当激光功率为65w时,粉体很少熔融,制造物的形体坍塌,并且制造性质为差“×”。当激光功率为75w和84w时,熔解所需的能量倾向于缺乏,制造物的表面变为粉体状,并且制造性质为稍差“○”。在95w-140w的范围内,制造物的表面平坦,并且制造性质为良好“◎”。此外,当激光功率在146w-154w的范围内时,能量的注入量大,表面膨胀并显示出变得不平整的趋势,并因此制造性质为稍差“○”。当激光功率为160w时,能量的注入量过大,制造物的形体坍塌,并且制造性质为差“×”。从以上已描述的内容,能够确认至少在75w-154w的范围内,允许能量密度提高至多大约两倍,并且粉体可稳定地制造。这反映了本发明的粉体仅在粉体形式具有吸收能力,并且一旦并入制造物,吸收率降低并且不易受使用激光照射影响,这样地即使当激光的功率波动时,粉体不容易影响制造。[实施例8]本实施例是添加sio2颗粒的实施例。按以下顺序制造本实施例的陶瓷制造用粉体。作为主要组分,使用通过混合al2o3粉体(纯度:99.99%或更大,粒径:20μm)和gd2o3粉体(纯度:99.99%或更大,粒径:20μm)使得质量比达到1:1而获得的组分。作为吸收体,使用tb4o7粉体(纯度:99.9%或更大,粒径:4μm)。作为sio2颗粒,使用纯度为99.9%或更大和粒径为4μm的颗粒。称重形成主要组分的颗粒,形成吸收体的颗粒和sio2颗粒使得各个粉体的质量比达到96.4:3.5:0.14。在干式球磨机中混合称重的粉体30分钟,由此获得粉体混合物(陶瓷制造用粉体)(样品27)。加热陶瓷制造用粉体并使用稀硫酸溶解,并且通过icp原子发射光谱法进行组成分析。al2o3、gd2o3、tb4o7和sio2的质量比为48.2:48.2:3.5:0.14并且与制备的组成比相同。除以上所述组分之外的组分含量小于陶瓷制造用粉体的0.2质量%。从通过分析获得的组成比来计算sio2颗粒与除在样品27的陶瓷制造用粉体中包括的吸收体之外的组合物(形成陶瓷结构的主要组分)形成的颗粒的质量的质量α[%],即α=sio2/(al2o3+gd2o3+zro2),并发现了为α=0.146[%]。计算sio2颗粒与由形成吸收体的组合物形成的颗粒的质量的质量β[%],即β=sio2/(tb4o7+pr6o11),并发现了为β=4.03[%]。计算形成主要组分的颗粒和形成吸收体的颗粒的质量γ[%],即γ=(tb4o7+pr6o11)/(al2o3+gd2o3+zro2),并发现了为γ=3.61[%]。作为通过与能量分散x-射线结合的扫描电子显微法(sem-edx)来分析陶瓷制造用粉体中的一些的结果,能够确认粒径为几微米的sio2颗粒分散在粉体中的样态。[实施例9至25]除了根据表13改变原材料的种类和配混比,采用与实施例8中相同的方式制造样品28至44的陶瓷制造用粉体作为实施例9至25。作为氧化锆,使用zro2粉体(纯度:99.9%或更大,粒径:15μm)。作为氧化镨,使用pr6o11粉体(纯度:99.9%或更大,粒径:4μm)。作为采用与实施例8中相同的方式分析样品28至44的陶瓷制造用粉体组成的结果,al2o3、gd2o3、zro2、tb4o7、pr6o11和sio2的质量比与制备的组成比相同。除以上所述组分之外的组分含量小于陶瓷制造用粉体的0.5质量%。从通过采用与实施例8中相同的方式的分析获得的组成比来计算α、β和γ,并且结果示于表14中。作为通过sem-edx来分析所制备的陶瓷制造用粉体中的一些的结果,能够确认粒径为几微米的sio2颗粒分散在粉体中的样态。[比较例]根据表13中所示配混比采用与实施例8中相同的方式制造用于比较的陶瓷制造用粉体。但是,在本比较例中,没有使用sio2颗粒,并且仅使用al2o3和gd2o3和作为形成吸收体的颗粒的tb4o7形成用于比较的陶瓷制造用粉体。作为采用与实施例8中相同的方式分析比较例的陶瓷制造用粉体的组成的结果,al2o3、gd2o3和tb4o7的质量比与制备的组成比例相同。sio2小于用于比较的陶瓷制造用粉体的50ppm。除以上所述组分之外的组分含量小于陶瓷制造用粉体的0.2质量%。[表13][表14]α[%]β[%]γ[%]样品270.1464.033.61样品281.0005.0020.00样品291.0004.2123.75样品300.0661.155.71样品310.0070.0417.86样品320.0290.2511.40样品330.0910.6613.94样品340.2564.995.12样品350.6264.0115.62样品360.0692.642.62样品370.5132.1024.38样品380.1062.005.32样品390.0704.531.55样品400.3015.825.18样品411.0935.6619.33样品420.1051.975.35样品430.7533.8719.48样品440.1291.0811.96比较样品90011.17使用实施例8至25和比较例的陶瓷制造用粉体来形成陶瓷制造物。在制造物的形成中,使用其中安装了50w的nd:yag激光器(束直径:65μm)的由3dsystems,inc.制造的prox(商品名)系列dmp100。如图5a和图5b中示意显示的主要部分,首先,在氧化铝基台130上激光照射部中铺开并平整陶瓷制造用粉体,形成20μm厚的粉体层102作为第一层。接下来,使用来自激光源181的30w激光180照射粉体层,将在5mm×42mm矩形区域中存在的粉体熔融并凝固。描画速率设为100mm/s至140mm/s,并且描画间距设为100μm。另外,如图5a中所示,以相对于矩形形状一侧45度的角形成所画的线。接下来,新铺开和平整20μm厚的粉体层从而覆盖熔融和凝固的部分。如图5b中所示,用激光照射在矩形区域正上方的粉体层,使得所画的线与第一层中所画的线正交,将5mm×42mm矩形区域熔融和凝固。重复以上所述层叠制造步骤,由此形成意图使用在三点弯曲强度测试中的具有5mm×42mm底面和6mm高度的棱柱状制造物。采用相同的步骤,还形成了用于水吸收性质测试的具有22mm×22mm方形底面和12mm高度的棱柱状制造物。作为使用光学显微镜观察样品27至44和比较样品9的制造物表面的结果,在样品27至39和样品42至44的制造物中,制造物表面上不平整性为30μm或更小,在样品40、样品41和比较样品9的制造物中为40μm或更小。从氧化铝基台分离制造物并抛光,由此获得用于三点弯曲强度测试的w40mm×d4mm×h3mm陶瓷制造物(图6a)和用于水吸收比测试的w20mm×d20mm×h10mm陶瓷制造物(图6b)。在三点弯曲强度测试中,使用由instron制造的压缩测试机。在表15中显示各个实施例和比较例1的陶瓷制造物的三点弯曲强度。水吸收比表示为在饱和且表面干燥的条件下陶瓷制造物中包括的水的总量与绝对干燥条件下陶瓷制造物质量的百分比。当由w1表示绝对干燥条件下陶瓷制造物的质量,并且由w2表示在饱和且表面干燥的条件下陶瓷制造物的质量时,可由w=(w2-w1)/w1×100来计算水吸收比w[%]。首先,测量在80℃下干燥四个小时的绝对干燥条件下陶瓷制造物的质量w1[g]。接下来,将陶瓷制造物淹没在煮沸槽中的水面以下,煮沸30分钟,并然后通过添加水冷却至室温,由此获得饱和试样。从水中移除排水试样,用湿纱布快速擦拭表面,并且测量去除水滴的在饱和且表面干燥的条件下的陶瓷制造物的质量w2[g]。由w=(w2-w1)/w1×100计算水吸收比w[%]并且总结在表15中。[表15]三点弯曲强度[mpa]吸收率[%]样品2734.40.4样品2828.60.5样品2924.80.8样品3031.90.4样品3130.90.9样品3233.20.7样品3334.40.6样品3427.70.7样品3527.90.5样品3632.00.7样品3724.50.6样品3828.10.5样品3931.50.6样品4023.10.6样品4122.70.9样品4229.00.5样品4326.30.4样品4427.30.4比较样品916.61.2由实施例8至25的陶瓷制造用粉体制备的陶瓷制造物具有20mpa或更大的高的三点弯曲强度和1.0%或更小的小的水吸收比。特别地,满足α≤1.0、0.04≤β≤5和γ≤20的样品27、28、30至36、38、39、和42至44的陶瓷制造物具有25mpa或更大的高的三点弯曲强度。[工业可利用性]本发明的陶瓷制造用粉体通过在粉体床熔融方法或包覆方法中添加吸收体能够获得具有高制造精度的陶瓷制造物,并且可用于需要复杂形状的陶瓷部件的领域中。本申请要求2017年7月14日提交的日本专利申请号2017-138505和2018年7月10日提交的日本专利申请号2018-130952的权益,其通过引用全本并入本文。[参考标记列表]11粉体容器12制造阶段部13再涂覆部14扫描器部15、181激光源21包覆喷嘴22粉体供给孔23、180激光41未照射区域42用激光照射区域102粉体层130基台当前第1页1 2 3