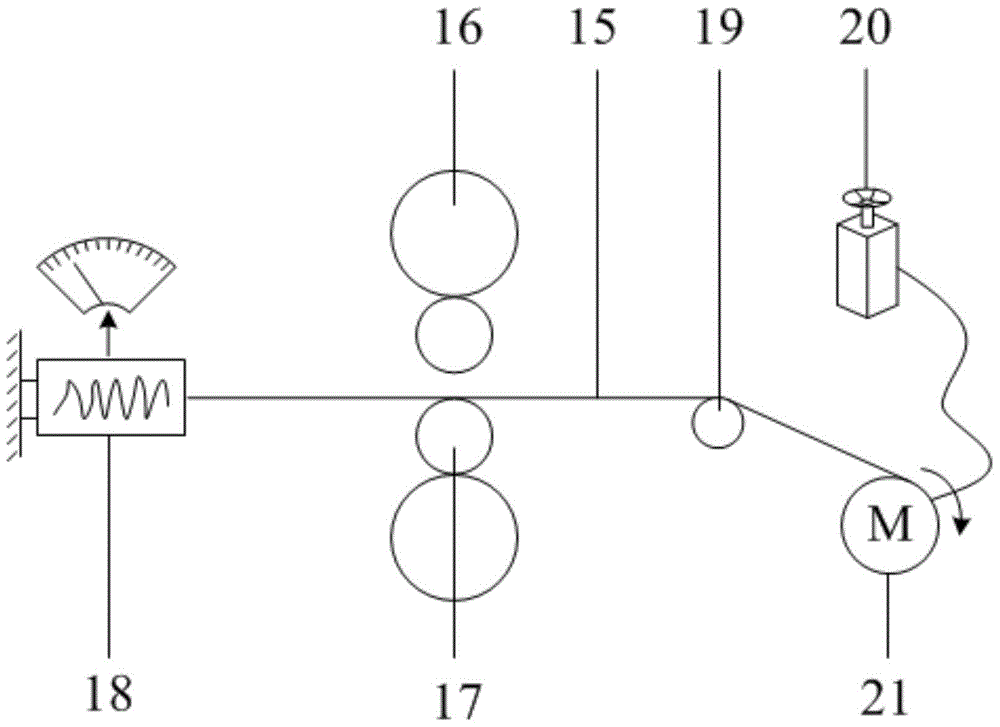
本发明属于极薄带轧制技术领域,特别是涉及一种金属极薄带轧制过程中张力施加装置及方法。
背景技术:近年来,随着微制造技术和微成形技术迅猛发展,金属、合金及金属基复合材料的极薄带需求量越来越大,这些极薄带已广泛应用于微电子行业、微制造行业、仪器仪表行业和微机电行业等。金属、合金及金属基复合材料的极薄带多是通过带张力轧制得到的,且合适的张力不仅有利于轧件减薄,还有利于生产效率的提高,也是保证极薄带板形的重要手段,因此,精确的张力控制对极薄带的生产具有非常重要的意义。在极薄带轧制过程中,可采用力矩电机对轧件施加前、后张力,但是,轧机传动系统将不可避免地产生机械阻力,而机械阻力包括力矩电机转子转动阻力、减速机齿轮组啮合传动阻力及工作辊辊颈与轴承座滑动阻力等,由于机械阻力的存在,使后张力始终大于等于机械阻力,即后张力的变化曲线是从一个大于0的数值开始的,且初始的后张力等于轧机传动系统的机械阻力,其如图3所示。因此,当轧件减薄至一定厚度时,容易因后张力过大导致断带现象的发生,迫使轧制过程终止。为此,亟需一种全新的张力施加方案,能够使后张力从0开始且全程连续可调,其如图4所述,从而避免断带现象的发生。
技术实现要素:针对现有技术存在的问题,本发明提供一种金属极薄带轧制过程中张力施加装置及方法,能够实现后张力从0开始,并满足张力的全程连续可调,有效避免断带现象的发生。为了实现上述目的,本发明采用如下技术方案:一种金属极薄带轧制过程中张力施加装置,包括主控计算机、操作台、PLC、第一力矩电机、第二力矩电机、第一换向开关、第二换向开关、第一变压器及第二变压器;在所述主控计算机内设置有张力控制系统人机界面,主控计算机通过PLC与操作台相连接,在操作台上分别设置有轧制正向启动开关和轧制反向启动开关;所述PLC一路依次通过变频器、第一变压器、第一换向开关与第一力矩电机的控制端相连,PLC另一路依次通过变频器、第二变压器、第二换向开关与第二力矩电机的控制端相连接;所述第一力矩电机通过第一换向开关进行转向调换,所述第二力矩电机通过第二换向开关进行转向调换;所述第一力矩电机通过第一变压器调整张力输出,所述第二力矩电机通过第二变压器调整张力输出。在所述主控计算机的张力控制系统人机界面上设有若干数据输入域,所述数据输入域包括轧件材质编号、轧件宽度、轧件入口厚度、轧件出口厚度、前张力系数和后张力系数。所述操作台上的轧制正向启动开关开启时,所述第一力矩电机定为前张力电机,所述第二力矩电机定为后张力电机。所述操作台上的轧制反向启动开关开启时,所述第二力矩电机定为前张力电机,所述第一力矩电机定为后张力电机。采用所述的金属极薄带轧制过程中张力施加装置的张力施加方法,包括如下步骤:步骤一:测量轧件处于不同厚度时的抗拉强度,建立轧件的抗拉强度随压下量的变化曲线,同时建立抗拉强度与压下量之间的曲线回归方程;步骤二:分别对第一力矩电机及第二力矩电机进行输入电压-张力标定,并建立第一力矩电机、第二力矩电机的输入电压-张力标定曲线,同时建立第一力矩电机、第二力矩电机的输入电压与张力之间的曲线回归方程;步骤三:将第一力矩电机及第二力矩电机的输入电压设置为0,分别测量使第一力矩电机及第二力矩电机进行匀速转动时的拉力,此时测得的拉力分别对应第一力矩电机及第二力矩电机的机械阻力;步骤四:将测得的拉力分别作为第一力矩电机及第二力矩电机的机械阻力补偿值,并将其分别代入第一力矩电机、第二力矩电机的输入电压与张力之间的曲线回归方程中,从而获得考虑机械阻力补偿时的第一力矩电机、第二力矩电机的输入电压与张力之间的曲线回归方程,该曲线回归方程作为后张力电机的输入电压计算时的参考方程;步骤五:测量轧件宽度和轧件入口厚度,估算轧件出口厚度,通过轧件入口厚度的实测值与设定值之间的大小关系,设定第一换向开关和第二换向开关的状态,具体分为以下两种情况:①第一力矩电机定为前张力电机,第二力矩电机定为后张力电机,当轧件入口厚度的实测值大于设定值时,第一换向开关和第二换向开关均不开启到换向位;当轧件入口厚度的实测值小于设定值时,第一换向开关不开启到换向位,第二换向开关开启到换向位;②第一力矩电机定为后张力电机,第二力矩电机定为前张力电机,当轧件入口厚度的实测值大于设定值时,第一换向开关和第二换向开关均不开启到换向位;当轧件入口厚度的实测值小于设定值时,第一换向开关开启到换向位,第二换向开关不开启到换向位;步骤六:在主控计算机人机界面上的数据输入域中分别输入以下数据:轧件材质编号、轧件宽度、轧件入口厚度、轧件出口厚度、前张力系数和后张力系数,当轧件入口厚度的实测值大于设定值时,第一换向开关和第二换向开关均不开启到换向位;当轧件入口厚度的实测值小于设定值时,第一换向开关不开启到换向位,第二换向开关开启到换向位;步骤七:对轧件施加预压紧力,开启操作台上的轧制正向启动开关,此时第一力矩电机定为前张力电机,第二力矩电机定为后张力电机,主控计算机根据人机界面上各数据输入域中的数据以及步骤二中建立的第一力矩电机的输入电压与张力之间的曲线回归方程,计算出第一力矩电机所需的输入电压值;主控计算机根据人机界面上各数据输入域中的数据以及步骤四中建立的第二力矩电机的输入电压与张力之间的曲线回归方程,计算出第二力矩电机所需的输入电压值,且输入电压值通过第一变压器输入到第一力矩电机中,以及通过第二变压器输入到第二力矩电机中,进而通过第一力矩电机建立前张力,以及通过第二力矩电机建立后张力;从而在所建立的前张力和后张力下进行第N道次(N=1、2、3···)的轧制;步骤八:当完成第N道次(N=1、2、3···)轧制后,控制极薄带轧机停机,然后在主控计算机人机界面上的数据输入域中分别输入以下数据:轧件宽度、轧件入口厚度、轧件出口厚度、前张力系数和后张力系数,且上述数据均为完成第N道次(N=1、2、3···)轧制后的轧件数据,当轧件入口厚度的实测值大于设定值时,第一换向开关和第二换向开关均不开启到换向位;当轧件入口厚度的实测值小于设定值时,第一换向开关开启到换向位,第二换向开关不开启到换向位;步骤九:对轧件施加预压紧力,开启操作台上的轧制反向启动开关,此时第二力矩电机定为前张力电机,第一力矩电机定为后张力电机,主控计算机根据人机界面上各数据输入域中的数据以及步骤四中建立的第一力矩电机的输入电压与张力之间的曲线回归方程,计算出第一力矩电机所需的输入电压值;主控计算机根据人机界面上各数据输入域中的数据以及步骤二中建立的第二力矩电机的输入电压与张力之间的曲线回归方程,计算出第二力矩电机所需的输入电压值,且输入电压值通过第一变压器输入到第一力矩电机中,以及通过第二变压器输入到第二力矩电机中,进而通过第二力矩电机建立前张力,以及通过第一力矩电机建立后张力;从而在所建立的前张力和后张力下进行第N+1道次(N=1、2、3···)的轧制;步骤十:重复步骤五~步骤九,直至轧件减薄至目标厚度。本发明的有益效果:本发明为了实现后张力从0开始且全程连续可调,在本发明的力矩电机和变压器之间设置有换向开关,在轧制前,当轧件入口厚度的实测值大于设定值时,即轧件厚度较厚时,此时轧机传动系统机械阻力小于该厚度下的后张力,则换向开关不开启到换向位,后张力电机在通电后进行常规的正向转动,此时后张力等于轧机传动系统机械阻力与后张力电机输出张力之和;当轧件入口厚度的实测值小于设定值时,即轧件厚度较薄时,此时轧机传动系统机械阻力大于该厚度下的后张力,则换向开关开启到换向位,后张力电机在通电后进行反向转动,此时后张力等于轧机传动系统机械阻力与后张力电机输出张力之差,进而实现了后张力从0开始的目标,且后张力全程连续可调,从而有效避免了断带现象的发生。本发明可精确控制前、后张力,并可为精准找到一个利于轧件减薄、生产效率提高及保证极薄带板形的前、后张力提供可能。本发明通过设置前张力系数和后张力系数,可获得恒前、后张应力轧制,当考虑异速比与轧制力后,通过计算可找到合适的前张力系数和后张力系数,获得最利于减薄的应力状态,可大大提高生产效率。附图说明图1为安装有本发明张力施加装置的极薄带轧机结构示意图;图2为第一、第二力矩电机的输入电压-张力标定原理图;图3为不考虑轧机传动系统机械阻力时力矩电机的输入电压-后张力关系曲线图;图4为考虑轧机传动系统机械阻力时力矩电机的输入电压-后张力关系曲线图;图5为第一力矩电机的输入电压-张力标定曲线图;图6为第二力矩电机的输入电压-张力标定曲线图;图7为轧件的抗拉强度随压下量的变化曲线图;图中,1—极薄带轧机,2—主控计算机,3—操作台,4—PLC,5—第一力矩电机,6—第二力矩电机,7—第一换向开关,8—第二换向开关,9—第一变压器,10—第二变压器,11—第一卷筒,12—第二卷筒,13—第一张力辊,14—第二张力辊,15—轧件,16—上支撑辊,17—下工作辊,18—拉压测力计,19—张力辊,20—变压器,21—力矩电机。具体实施方式下面结合附图和具体实施例对本发明做进一步的详细说明。如图1所示,一种金属极薄带轧制过程中张力施加装置,包括主控计算机2、操作台3、PLC4、第一力矩电机5、第二力矩电机6、第一换向开关7、第二换向开关8、第一变压器9及第二变压器10;在所述主控计算机2内设置有张力控制系统人机界面,主控计算机2通过PLC4与操作台3相连接,在操作台3上分别设置有轧制正向启动开关和轧制反向启动开关;所述PLC4一路依次通过变频器、第一变压器9、第一换向开关7与第一力矩电机5的控制端相连,PLC4另一路依次通过变频器、第二变压器10、第二换向开关8与第二力矩电机6的控制端相连接;所述第一力矩电机5通过第一换向开关7进行转向调换,所述第二力矩电机6通过第二换向开关8进行转向调换;所述第一力矩电机5通过第一变压器9调整张力输出,所述第二力矩电机6通过第二变压器10调整张力输出。在所述主控计算机2的张力控制系统人机界面上设有若干数据输入域,所述数据输入域包括轧件材质编号、轧件宽度、轧件入口厚度、轧件出口厚度、前张力系数和后张力系数。所述操作台3上的轧制正向启动开关开启时,所述第一力矩电机5定为前张力电机,所述第二力矩电机6定为后张力电机。所述操作台3上的轧制反向启动开关开启时,所述第二力矩电机6定为前张力电机,所述第一力矩电机5定为后张力电机。本实施例中,轧件15为304不锈钢带,轧件宽度为50mm,初始轧件厚度为488μm,目标轧件厚度为3μm。采用所述的金属极薄带轧制过程中张力施加装置的张力施加方法,包括如下步骤:步骤一:测量轧件15处于不同厚度时(本实施例中分别为488μm、388μm、300μm、243μm、178μm、136μm、90μm、45μm、36μm、20μm及15μm)的抗拉强度,建立轧件15的抗拉强度随压下量的变化曲线,其如图7所示,同时建立抗拉强度与压下量之间的曲线回归方程,曲线回归方程具体如下:f1=-2.61×10-3x2+2.75x+786(压下量≤352μm)f1=-5.3000×10-4x3+0.6050x2-231.80x+31156(压下量>352μm)式中,f1为抗拉强度,x为压下量;步骤二:分别对第一力矩电机5及第二力矩电机6进行输入电压-张力标定,其标定原理图如图2所示,并建立第一力矩电机5、第二力矩电机6的输入电压-张力标定曲线,其如图5、图6所示,同时建立第一力矩电机5、第二力矩电机6的输入电压与张力之间的曲线回归方程,曲线回归方程具体如下:n1=0.01247v12+1.100v1-44.233n2=0.01368v22+1.418v2-54.852式中,v1为第一力矩电机5的输入电压,v2为第二力矩电机6的输入电压,n1为第一力矩电机5输出的张力,n2为第二力矩电机6输出的张力;步骤三:将第一力矩电机5及第二力矩电机6的输入电压设置为0,分别测量使第一力矩电机5及第二力矩电机6进行匀速转动时的拉力F1和F2,此时测得的拉力F1和F2分别对应第一力矩电机5及第二力矩电机6的机械阻力,具体为:F1=45N,F2=55N;步骤四:将测得的拉力F1和F2分别作为第一力矩电机5及第二力矩电机6的机械阻力补偿值,并将其分别代入第一力矩电机5、第二力矩电机6的输入电压与张力之间的曲线回归方程中,从而获得考虑机械阻力补偿时的第一力矩电机5、第二力矩电机6的输入电压与张力之间的曲线回归方程,该曲线回归方程作为后张力电机的输入电压计算时的参考方程,曲线回归方程具体如下:n3=0.01247v12+1.100v1+0.767n4=0.01368v22+1.418v2+0.148式中,v1为第一力矩电机5的输入电压,v2为第二力矩电机6的输入电压,n3为考虑机械阻力补偿时第一力矩电机5输出的张力,n4为考虑机械阻力补偿时第二力矩电机6输出的张力;步骤五:先将轧件15安装到极薄带轧机1上,然后测量轧件宽度为50mm和轧件入口厚度为488μm,估算轧件出口厚度为388μm,通过轧件入口厚度的实测值与设定值之间的大小关系,设定第一换向开关7和第二换向开关8的状态,具体分为以下两种情况:①第一力矩电机5定为前张力电机,第二力矩电机6定为后张力电机,当轧件入口厚度的实测值大于设定值时,第一换向开关7和第二换向开关8均不开启到换向位;当轧件入口厚度的实测值小于设定值时,第一换向开关7不开启到换向位,第二换向开关8开启到换向位;②第一力矩电机5定为后张力电机,第二力矩电机6定为前张力电机,当轧件入口厚度的实测值大于设定值时,第一换向开关7和第二换向开关8均不开启到换向位;当轧件入口厚度的实测值小于设定值时,第一换向开关7开启到换向位,第二换向开关8不开启到换向位;步骤六:在主控计算机2人机界面上的数据输入域中分别输入以下数据:轧件材质编号为G304、轧件宽度为50mm、轧件入口厚度为488μm、轧件出口厚度为388μm、前张力系数为0.1和后张力系数为0.1,当轧件入口厚度的实测值大于设定值时,第一换向开关7和第二换向开关8均不开启到换向位;当轧件入口厚度的实测值小于设定值时,第一换向开关7开启到换向位,第二换向开关8不开启到换向位;本实施例中,第一力矩电机5定为前张力电机,第二力矩电机6定为后张力电机,且轧件入口厚度的实测值大于设定值10μm,因此第一换向开关7和第二换向开关8均不开启到换向位;步骤七:对轧件15施加预压紧力,开启操作台3上的轧制正向启动开关,此时第一力矩电机5定为前张力电机,第二力矩电机6定为后张力电机,主控计算机2根据人机界面上各数据输入域中的数据以及步骤二中建立的第一力矩电机5的输入电压与张力之间的曲线回归方程,计算出第一力矩电机5所需的输入电压值分别为352V;主控计算机2根据人机界面上各数据输入域中的数据以及步骤四中建立的第二力矩电机6的输入电压与张力之间的曲线回归方程,计算出第二力矩电机6所需的输入电压值分别为335V,且输入电压值通过第一变压器9输入到第一力矩电机5中,以及通过第二变压器10输入到第二力矩电机6中,进而通过第一力矩电机5建立前张力为1928N,以及通过第二力矩电机6建立后张力为1985N;从而在所建立的前张力和后张力下进行第N道次(N=1、2、3···)的轧制(本实施例中该步骤为第1道次);步骤八:当完成第N道次(N=1、2、3···)轧制后(本实施例中该步骤为第1道次),控制极薄带轧机停机,然后在主控计算机2人机界面上的数据输入域中分别输入以下数据:轧件宽度为50mm、轧件入口厚度为400μm、轧件出口厚度为300μm、前张力系数为0.1和后张力系数为0.1,且上述数据均为完成第N道次(N=1、2、3···)轧制后(本实施例中为第1道次)的轧件数据,当轧件入口厚度的实测值大于设定值时,第一换向开关7和第二换向开关8均不开启到换向位;当轧件入口厚度的实测值小于设定值时,第一换向开关7开启到换向位,第二换向开关8不开启到换向位;本实施例中,完成第1道次轧制后,且轧件入口厚度的实测值大于设定值10μm,因此第一换向开关7和第二换向开关8均不开启到换向位;步骤九:对轧件15施加预压紧力,开启操作台3上的轧制反向启动开关,此时第二力矩电机6定为前张力电机,第一力矩电机5定为后张力电机,主控计算机2根据人机界面上各数据输入域中的数据以及步骤四中建立的第一力矩电机5的输入电压与张力之间的曲线回归方程,计算出第一力矩电机5所需的输入电压值分别为336V;主控计算机2根据人机界面上各数据输入域中的数据以及步骤二中建立的第二力矩电机6的输入电压与张力之间的曲线回归方程,计算出第二力矩电机6所需的输入电压值分别为342V,且输入电压值通过第一变压器9输入到第一力矩电机5中,以及通过第二变压器10输入到第二力矩电机6中,进而通过第二力矩电机6建立前张力为2016N,以及通过第一力矩电机5建立后张力为1832N;从而在所建立的前张力和后张力下进行第N+1道次(N=1、2、3···)的轧制(本实施例中该步骤为第2道次);步骤十:重复步骤五~步骤九,直至轧件15减薄至3μm的目标厚度。实施例中的方案并非用以限制本发明的专利保护范围,凡未脱离本发明所为的等效实施或变更,均包含于本案的专利范围中。