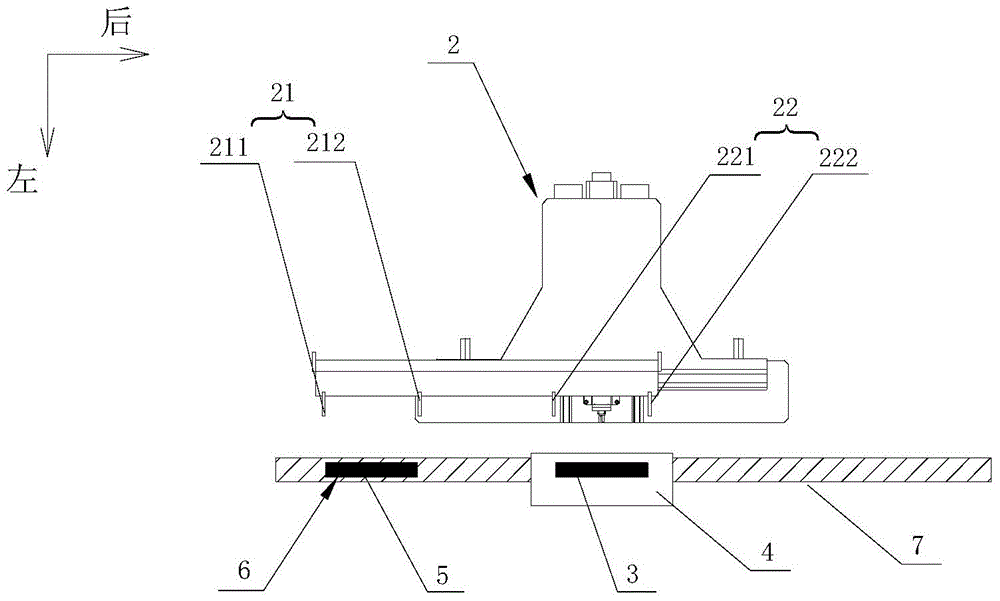
本发明涉及汽车座椅生产技术领域,特别是涉及一种汽车座椅滑道的自动冲压装置及自动冲压线。
背景技术:汽车座椅滑道是汽车座椅前后滑动的轨道,一般由薄板冲压成一定的形状再组装形成成品。现有技术中,采用自动冲压线实现汽车座椅滑道的冲压。所述自动冲压线通常包括若干冲床,需要将板材按照模具进行多次冲压成型,最终形成符合要求的成品。因此,自动冲压线上还设有夹持工件用的机械手,以实现工件的脱模以及工件在冲床之间的转移。对于座椅滑道而言,由于其具有内钩状的结构,如果垂直于沟槽的方向脱模,容易引起工件与模具的干涉,因此,现有技术中通常沿平行于沟槽的方向进行脱模。在沿沟槽方向推动工件进行脱模的过程中,需要克服工件与模具间的摩擦阻力。由于工件在成型过程中产生的弹性形变,工件与模具之间具有约300kgf的摩擦阻力,就需要机械手具备大于300kgf推力才能完成脱模。现有技术中,机械手所能够提供的推力普遍较小,因此,现有技术中机械手的工作方式通常为:首先沿沟槽方向推动工件脱模,然后再夹持工件移动,以实现工件在各冲床之间的转移。上述现有的自动冲压线中,工件的脱模与转移存在时间差,机械手必须首先完成脱模后再进行工件的转移,对于一条生产线而言,这种加工方式无疑在较大程度上影响了生产效率,降低了冲床的使用率。此外,为提高工件移动过程中的定位准确性,减小工件的定位偏差,对各机械手移动时行程的控制提出了较高的要求。为实现各机械手移动行程的准确控制,现有技术中一种典型的自动冲压线将所有冲床的冲压工位一字排开,并由一根横杆横贯所有冲床,由统一的动力源带动横杆运动,进而通过横杆带动与每个冲床对应的各个机械手同步运动,以实现对各机械手移动行程的精确控制。但是,受安装精度的影响,相邻冲床之间的中心距不可能完全相同,即在整个自动冲压线上,存在若干个不等的冲床中心距;上述现有的自动冲压线中,采用横杆统一控制各机械手,使得各机械手的行程一致,而一个固定的行程不可能适应所有的冲床中心距。因此,如何设计一种汽车座椅滑道的自动冲压装置及自动冲压线,以提高加工效率,成为本领域技术人员目前亟需解决的技术问题。
技术实现要素:本发明的目的是提供一种汽车座椅滑道的自动冲压装置及自动冲压线,能够同步实现工件的脱模与转移,提高了加工效率。为解决上述技术问题,本发明提供一种汽车座椅滑道的自动冲压装置,包括冲床和机械手,所述冲床具有冲压工位,所述冲压工位用于放置承载有被加工件的模具,所述冲压工位之前还设有用于放置待加工件的暂存位,所述待加工件处于所述被加工件的脱模方向上;所述机械手包括推料爪和脱模爪,所述推料爪和所述脱模爪能够沿所述脱模方向同步移动,以便在所述脱模爪推动所述被加工件脱离所述模具的同时,所述推料爪将所述待加工件由所述暂存位推送至所述冲压工位。本发明的自动冲压装置,在冲压工位之前设有暂存位,用于放置待加工件,相应地,机械手设有推料爪和脱模爪,当一次冲压完成后,机械手的推料爪作用于待加工件、脱模爪作用于被加工件,然后带动推料爪和脱模爪沿脱模方向同步移动,则在脱模爪推动被加工件脱离模具的同时,推料爪将待加工件由暂存位推送至冲压工位。可见,本发明同步实现了工件的脱模与传递,取代了现有技术中先脱模再传递的加工模式,从而在较大程度上提高了加工效率。可选地,所述机械手设置在所述冲床上,并能够在所述脱模方向所在的水平面内横向移动,以带动所述推料爪移入或移出所述暂存位,同时带动所述脱模爪移入或移出所述冲压工位。可选地,所述脱模爪和所述推料爪在所述脱模方向上的间距可调。可选地,所述脱模爪包括在所述脱模方向间隔分布的第一卡爪和第二卡爪,所述第一卡爪和所述第二卡爪的间距可根据所述被加工件进行调节;和/或,所述推料爪包括在所述脱模方向上间隔分布的第三卡爪和第四卡爪,所述第三卡爪和所述第四卡爪的间距可以根据所述待加工件进行调节。可选地,所述暂存位与所述冲压工位处于同一平面内。本发明还提供一种汽车座椅滑道的自动冲压线,包括若干由前至后依次排列的自动冲压装置,各所述自动冲压装置中的冲压工位呈一字排列,所述自动冲压装置为上述任一项所述的自动冲压装置,所述冲压工位处于与其相邻的前后两所述暂存位的正中间。本发明的自动冲压线包括若干上述自动冲压装置,各自动冲压装置均能够同步实现工件的脱模与传递,并将前一个冲床加工后的工件转移至后一个冲床的暂存位,以实现工件的直线步进式传递;对于整个生产线而言,这种直线步进式的传递方式使得工件仅在前后方向上移动,不存在上下运动,缩短了工件的传递路径,而且同步实现了脱模与传递,极大地提高了加工效率。可选地,还包括导向型架,所述导向型架将各所述暂存位以及各所述冲压工位由前至后依次连接,构成所述待加工件以及所述被加工件的移动轨道。可选地,还包括拆垛机,所述拆垛机将堆码的若干料片拆分成单个料片后推送至最前面的所述自动冲压装置的暂存位。可选地,所述导向型架、所述拆垛机以及所述模具的上表面平齐,且三者的中心线重合。可选地,各所述自动冲压装置中的机械手相互独立,且各所述机械手的行程可根据各自对应的冲床中心距进行调节。附图说明图1为本发明所提供汽车座椅滑道的自动冲压线在一种具体实施方式中的结构示意图;图2为本发明所提供自动冲压装置在一种具体实施方式中的第一工作状态示意图;图3为本发明所提供自动冲压装置在一种具体实施方式中的第二工作状态示意图;图4为本发明所提供自动冲压装置在一种具体实施方式中的第三工作状态示意图;图5为本发明所提供自动冲压装置在一种具体实施方式中的第四工作状态示意图;图6为本发明所提供自动冲压装置中机械手动作过程示意图;图7为本发明所提供自动冲压装置中被加工件处于模具中的状态示意图;图8为本发明所提供自动冲压装置所加工的被加工件一种设置方式的立体结构示意图。图1-8中:冲床1、冲压工位11、机械手2、推料爪21、第三卡爪211、第四卡爪212、脱模爪22、第一卡爪221、第二卡爪222、被加工件3、模具4、待加工件5、暂存位6、导向型架7、拆垛机8。具体实施方式本发明的核心是提供一种汽车座椅滑道的自动冲压装置及自动冲压线,能够同步实现工件的脱模与转移,提高了加工效率。需要说明的是,本发明所述的第一、第二等词仅为了区分结构相同或类似的多个部件或结构,不表示对设置顺序或者连接关系的某种特殊限定。本文中以与脱模方向平行的方向为前后方向,脱模方向是指被加工件脱离模具时的移动方向;脱模方向所指向的方向为后,与脱模方向相反的方向为前,也就是说,工件脱模后依次向后传递至下一个冲床继续进行冲压。在水平面内,垂直于前后的方向为左右方向,本文中也称为横向。以下结合附图,对本发明汽车座椅滑道的自动冲压线以及自动冲压装置进行具体介绍,以便本领域技术人员准确理解本发明的技术方案。如图1所示,本发明提供了一种汽车座椅滑道的自动冲压线,包括若干自动冲压装置,各自动冲压装置由前至后依次排列,且各自动冲压装置的冲压工位11呈一字型排列成一条直线,以便对工件进行多次冲压后形成最终的成品,形成一条自动冲压的流水线。在该流水线上,以工件的流动方向为前后方向,即工件的流动方向所指向的为后,与工件的流动方向相背的为前,换言之,流水线的上游对应前方,下游对应后方。本发明的自动冲压线中,工件的流动方向与工件的脱模方向相同,以便在工件传递过程中同步实现脱模;也就是说,本文所述的脱模方向即为前后方向,脱模时工件的移动方向指向后方,与其相反的方向为前方;脱模方向即为脱模时工件移出模具的方向,对应本文所述的后方。本发明的自动冲压装置包括冲床1和机械手2,机械手2与冲床1相互配合,机械手2可以实现工件的脱模,以及工件在各冲床1之间的传递,能够同步完成工件的脱模与传递。详细地,冲床1具有冲压工位11,在冲压过程中通常需要将被加工件3放置在模具4上,以便按照模具4对被加工件3进行冲压;承载有被加工件3的模具4可以放置在所述冲压工位11,以便通过冲床1对被加工件3进行冲压。本发明的自动冲压装置还包括暂存位6,暂存位6处于冲压工位11之前,用于放置待加工件5;且暂存位6可以处于被加工件3的脱模方向上,具体为脱模方向所在的延长线上,也就是说,暂存位6可以处于冲压工位11的正前方,以便待加工件5可以由前至后直线移动至冲压工位11进行冲压。机械手2包括推料爪21和脱模爪22,两者在前后方向布置,推料爪21与待加工件5对应,可以处于待加工件5的正左侧或者正右侧,以便其横向移动即可作用于待加工件5,从而向后推动待加工件5至冲压工位11;脱模爪22与被加工件3对应,可以处于被加工件3的正左侧或正右侧,以便其横向移动即可作用于被加工件3,从而向后推动被加工件3,使得被加工件3脱离模具4,实现被加工件3的脱模。推料爪21与脱模爪22可以在前后方向上同步移动,那么,当推料爪21卡住待加工件5、且脱模爪22卡住被加工件3时,可以驱动机械手2由前至后移动,以带动推料爪21和脱模爪22同步后移,进而推动待加工件5和被加工件3同步后移;由于暂存位6处于冲压工位11的正前方,推料爪21可以沿直线向后移动以便将待加工件5由暂存位6推送至冲压工位11,同时,脱模爪22向后推动被加工件3使得被加工件3脱离模具4完成脱模。所述被加工件3是指所述冲床1正在或者已经完成冲压加工的工件;所述待加工件5是指即将转移至冲压工位11进行冲压加工的工件,可以为原材料,也可以为经上一个冲床1加工后的半成品。在没有特殊说明的情况下,本文中所述的工件包括待加工件5和被加工件3。可见,本发明的自动冲压装置,在冲压工位11之前设置暂存位6,并将脱模方向与工件的移动方向相统一,通过推料爪21和脱模爪22可以同步实现待加工件5的转移以及被加工件3的脱模;与现有技术中先脱模后传递工件的方式相比,在较大程度上提高了加工效率。为便于描述,对于设有若干上述自动冲压装置的自动冲压线而言,各冲床1、各机械手2、各暂存位6以及各冲压工位11均可以由前至后依次排序,处于最前面的分别定义为第一冲床1、第一机械手2、第一暂存位6以及第一冲压工位11,并按照这种顺序依次定义后续的冲床1、机械手2、暂存位6以及冲压工位11。在本发明的自动冲压线中,第一暂存位6至第一冲压工位11的前后距离,可以等于第一冲压工位11至第二暂存位6的前后距离,此时,与第一冲床1对应的第一机械手2在由前至后移动的过程中,将待加工件5由所述第一暂存位6转移至第一冲压工位11的同时,同步实现了被加工件3的脱模以及被加工件3由第一冲压工位11至第二暂存位6的转移。也就是说,第一个冲床1上的被加工件3可以作为第二暂存位6上的待加工件5,以便一个原材料在各冲床1之间由前至后依次传递,并经过各冲床1的依次冲压,最终形成合格的成品。同理,第二暂存位6至第二冲压工位11的前后距离,可以等于第二冲压工位11至第三暂存位6的前后距离,依次类推进行各暂存位6以及冲压工位11的布置;换言之,各冲压工位11均处于与其相邻的两个暂存位6的正中间。采用上述结构,本发明的自动冲压线可以通过机械手2在前后方向的直线步进式移动,同步实现工件的脱模以及在相邻冲床1之间的传递,极大地提高了加工效率。而且,工件在整个脱模和转移过程中仅存在前后方向的移动,不存在任何上下移动,有别于现有技术中的拉杆冲压线;此时,工件仅在一个方向上移动,相当于缩减了工件的运动维度,有助于提高工件的定位精度。由于各暂存位6和各冲压工位11均处于同一前后延长线上,可以使得各暂存位6在前后方向等间距布置,此时,也使得各冲压工位11在前后方向上等间距布置。本发明的自动冲压线还可以包括导向型架7,导向型架7相当于一个移动轨道,可以将各暂存位6以及各冲压工位11由前至后依次连接,当推料爪21推动待加工件5脱离暂存位6时,导向型架7可以对待加工件5进行支撑,并对待加工件5的移动进行导向,确保待加工件5沿导向型架7移动至冲压工位11;同理,当脱模爪22推动被加工件3脱离模具4和冲压工位11时,导向型架7可以对被加工件3进行支撑,并确保被加工件3沿直线向后移动至下一个暂存位6。导向型架7可以为滑轨结构,具体可以设置为具有沟槽状滑槽的轨道,以便对工件进行一定的导向约束;导向型架7还可以为类似挡板状的结构,以隔挡在工件的两侧,对工件进行导向约束。实际上,导向型架7可以构成待加工件5以及被加工件3的移动轨道,一方面可以起到支撑工件的作用,另一方面可以确保工件沿直线向后移动至下一个工作位置,避免工件在转移过程中偏移。本发明的自动冲压线还可以包括拆垛机8,拆垛机8用于对堆码的若干料片进行拆分,以形成单个料片,作为对汽车座椅滑道进行冲压加工的原材料。拆垛机8可以处于第一暂存位6的前方,然后将拆分出的单个料片推送至第一暂存位6,以便通过第一冲床1进行冲压加工,并依次向后传递至各个冲床1进行多次冲压,最终形成合格的成品。通常情况下,若干料片依次堆码存放,所述若干是指数量不确定的多个,故可以设置拆垛机8对料片进行拆分,以形成便于加工的单个料片,实现汽车座椅滑道的全自动冲压生产,无需人工拆分,不仅提高了加工效率,还避免了人工拆分容易产生的双料片或多料片冲压问题。本发明的自动冲压线中,导向型架7、拆垛机8以及冲压工位11上所放置模具4的上表面可以平齐,形成由前至后连续的整个平面,且三者的中心线可以相互重合,以保证工件在脱模以及传递过程中的定位可靠性。本领域技术人员应该可以理解,在座椅滑道的生产过程中,为实现工件在各冲床1之间转移时的准确定位,需要将机械手2与工件之间的定位偏差控制在0.2mm内。然而,在实际安装中,相邻冲床1的中心距的实际值必然与理论值存在偏差,实践中,安装误差最大可达到0.5mm。为此,要将机械手2与工件之间的定位偏差控制在0.2mm内,就必须使得机械手2在传递工件时的行程与冲床1的实际中心距相匹配;否则,将会导致工件在转移过程中出现定位偏差,或者导致机械手2与工件的干涉(即机械手2不能有效夹持工件)。如背景技术所述,现有技术中对各机械手2进行统一驱动,使得各机械手2的行程一致,此时就需要对冲床1的中心进行精确定位,以保证在整个自动冲压线中相邻冲床1的中心距始终保持一致,这无疑对安装以及操作提出了更高的要求。更为关键的是,冲床1中心距的安装误差是客观存在的,只能减小无法消除;即使对冲床1中心距进行了精确控制,也无法使得各个机械手2的实际行程与各自对应的冲床1中心距完全匹配。针对上述技术问题,本发明的自动冲压线中,各自动冲压装置相对独立,各自动冲压装置中的机械手2也相互独立,则可以根据需要调整各机械手2的行程,以使得各机械手2的行程与各自对应的冲床1中心距匹配,避免机械手2与工件相干涉,提高工件在传递过程中的定位精度,保证整个自动冲压线正常运行。换言之,机械手2的行程可调,具体可以根据实际的冲床1中心距进行调节,可以为无级调节,即机械手2的行程可以柔性调节,以便更好的与冲床1中心距匹配。需要说明的是,在图1所示的实施方式中采用了九个自动冲压装置,本领域技术人员完全可以根据产品所需的工序数合理设置冲床1以及机械手2的个数,不限于图1所示的实施方式。本发明的自动冲压线所包括的部件较多,各部件的结构较为复杂,以下结合附图,对自动冲压装置的结构以及原理进行详细说明,关于自动冲压线中的其他部件可以参照现有技术进行设置,此处不再赘述。请结合图2-5,本发明的自动冲压装置中,可以将机械手2设置在冲床1上,具体可以设置在冲压工位11的一侧,在图2-5中,机械手2可以处于冲压工位11的右侧;机械手2可以横向移动,图2-5实际上为机械手2工作状态的俯视图,其中,所述横向具体可以为图中的竖直方向,竖直向上的方向为右,竖直向下的方向为左。以冲压工位11设置在左侧为例,则机械手2可以设置在冲压工位11的右侧,机械手2可以向左移动至与冲压工位11对应的位置,或者向右移动远离冲压工位11,以带动脱模爪22移入或移出冲压工位11,同时带动推料爪21移入或移出暂存位6。本文所述的横向,可以为在水平面内垂直于前后的方向,具体可以定位为左右方向;也可以为水平面内任意一个能够与所述前后方向相交的直线的延伸方向;由于暂存位6和冲压工位11处于前后方向,则只要所述横向与前后方向相交,机械手2即可移动至与暂存位6和冲压工位11对应的位置。当机械手2设置在冲床1上时,机械手2横向移动较小距离即可到达与冲压工位11对应的位置,则机械手2的动力源至执行结构(本文中所述的推料爪21和脱模爪22)的传递路径较短,此时,可以减小力在传递过程中的损失,尤其可以提高脱模爪22的作用力,使得脱模爪22能够产生足够的脱模力。详细地,可以将脱模爪22设置在动力源的驱动主路径上,然后通过连杆或者其他辅助轴将动力传递给推料爪21,从而保证脱模爪22能够产生足够的脱模力。如图2-5所示,机械手2的动力源与脱模爪22在前后方向的位置一致,而推料爪21设置在动力源的前方;动力源可以处于脱模爪22的左侧或者右侧,然后可以通过左右延伸的驱动轴等连接件直接与脱模爪22连接,实现对脱模爪22的驱动;可以通过前后延伸的辅助连杆或者传递轴与所述驱动轴连接,将动力传递给推料爪21。如背景技术所述,脱模所需的脱模力较大,机械手2设置在冲床1上时,可以有效提升脱模力;再者,与现有技术中机械手2设置在冲床1的前后两侧相比,将机械手2设置在冲床1上时,可以缩小冲床1中心距,进而缩小了工件的传递距离,提高传递效率。为适应暂存位6与冲压工位11的布置,本发明的机械手2中,脱模爪22和推料爪21之间的前后间距也可以设置为可调的结构。推料爪21可以安装在脱模爪22的正前方,推料爪21与脱模爪22的前后间距可以等于暂存位6与冲压工位11之间的前后间距;机械手2可以带动推料爪21横向移动至正对暂存位6一侧的位置、脱模爪22横向移动至正对冲压工位11一侧的位置,直接通过推料爪21卡固待加工件5,同时通过脱模爪22卡固被加工件3,无需在其他方向调整机械手2的位置,也不需要对推料爪21和脱模爪22的位置进行单独调节,简化了操作步骤,同时减小了机械手2作用于工件时的定位偏差。对于机械手2而言,实现推料爪21和脱模爪22在前后方向上间距可调的结构形式多样。例如,可以在机械手2上设置由前至后延伸的纵杆,然后将推料爪21和脱模爪22安装在纵杆上,并可以设置安装方式,使得推料爪21和脱模爪22均可以沿纵杆前后移动,以调节推料爪21和脱模爪22的前后间距;还可以在纵杆上设置卡位等定位结构,在推料爪21和脱模爪22的位置调整合适后将两者固定。或者,可以在机械手2上设置前后间隔分布的若干安装位,然后将推料爪21和脱模爪22可拆卸的安装在相应的安装位上,则通过安装位的变换可以调整推料爪21和脱模爪22的前后间距。详细地,本发明的机械手2中,脱模爪22具体可以包括前后间隔分布的第一卡爪221和第二卡爪222,第一卡爪221和第二卡爪222分别对应卡接在被加工件3的前后两端,从而实现对被加工件3的卡固,则脱模爪22向后移动时,即可推动被加工件3后移,使得被加工件3脱模模具4,同时将被加工件3后移至下一个暂存位6。为便于通过第一卡爪221和第二卡爪222实现对被加工件3的卡固,第一卡爪221和第二卡爪222之间的前后间距可以根据被加工件3进行调节,以便两者之间的间距能够与被加工件3匹配,从而有效卡紧被加工件3,提高被加工件3的脱模可靠性。同理,推料爪21可以包括前后间隔分布的第三卡爪211和第四卡爪212,第三卡爪211和第四卡爪212分别可以卡接在待加工件5的前后两端,以便推料爪21将待加工件5卡固,从而推动待加工件5由暂存位6移动至冲压工位11。第三卡爪211和第四卡爪212之间的前后间距也可以根据待加工件5进行调整,以便有效卡紧待加工件5,顺利实现待加工件5的推动转移。实现第一卡爪221和第二卡爪222前后间距可调的方式多样,可以将第一卡爪221和第二卡爪222可滑动地连接在脱模爪22的主体上,然后滑动调节两者之间的间距;所述可滑动的连接方式可以为滑槽或者其他形式的滑动轨道。或者,可以在脱模爪22的主体上设置卡槽,在卡槽上设置若干卡接位,将第一卡爪221和第二卡爪222安装在卡槽上,并选择不同的卡接位进行连接,以调整两者之间的间距。还可以采用丝杠、螺杆等结构实现第一卡爪221和第二卡爪222的安装,然后通过丝杠或螺杆的移动实现第一卡爪221和第二卡爪222相对位置的调整。本领域技术人员可以采用类似第一卡爪221和第二卡爪222的结构对第三卡爪211和第四卡爪212进行设置,以实现第三卡爪211和第四卡爪212前后间距的调整。当然,脱模爪22和推料爪21的形式不限于上述两个卡爪的具体结构,两者均可以设置为一个卡爪的结构形式,分别卡接在被加工件3的前端和待加工件5的前端,此时也可以推动被加工件3和待加工件5后移。但是,采用前后两个卡爪的结构形式可以实现对工件更为有效的掌控,以提高工件脱模以及移动的可靠性。此外,暂存位6与冲压工位11可以处于同一平面内,以便待加工件5可以处于被加工件3的正前方,则推料爪21和脱模爪22可以直接由前至后推动待加工件5和被加工件3,不存在上下方向的分运动,提高了工件移动的准确度。为实现推料爪21以及脱模爪22的前后移动,可以采用皮带驱动,使得皮带在前后方向上移动,以带动推料爪21和脱模爪22前后移动。或者,可以采用电机或者气缸等驱动推料爪21和脱模爪22前后移动。请进一步参考图6,本发明的自动冲压装置的动作过程如下:首先,驱动机械手2横向移动至预设位置,以带动脱模爪22移动至与冲压工位11对应的位置,同时带动推料爪21移动至与暂存位6对应的位置,机械手2具体可以左移至正对冲压工位11和暂存位6右侧的位置,由图2所示位置变动至图3所示位置,完成图6中的箭头S1所示的步骤;然后,驱动机械手2动作,以便脱模爪22卡紧被加工件3、且推料爪21卡紧待加工件5,如图3所示;接着,驱动机械手2向后移动,脱模爪22推动被加工件3脱离模具4并将被加工件3推送至下一个暂存位6,同时,推料爪21将待加工件5由暂存位6推送至冲压工位11,如图4所示,完成图6中的箭头S2所示的步骤;再后,脱模爪22和推料爪21横向移动,具体可以右移,以释放被加工件3和待加工件5,以便冲床1能够下压对待加工件5进行加工,如图5所示,完成图6中箭头S3所示的步骤;最后,在冲床1下压和回上死点的过程中,机械手2向前移动,回到初始位置,完成图6中箭头S4所示的步骤,为下一个工作循环做准备。请进一步参考图7和图8,本文中的模具4通常包括上模和下模,工件为图8所示的结构,为具有内钩槽的框架结构;冲压时,工件安装在下模和上模之间,如图7所示,下模用于加工形成所述内沟槽的结构,具体可以将工件套装在下模上,然后将上模压装在工件上。进行脱模时,上模和下模是分开的,可以直接将上模取下,工件承载在下模上。也就是说,上文中凡是涉及到脱模,所述模具4均是指下模。相应地,如图7所示,本文中所述的脱模方向是指沿着内钩槽的方向,或者说内沟槽的延伸方向。以上对本发明所提供汽车座椅滑道的自动冲压线及自动冲压装置进行了详细介绍。本文中应用了具体个例对本发明的原理及实施方式进行了阐述,以上实施例的说明只是用于帮助理解本发明的核心思想。应当指出,对于本技术领域的普通技术人员来说,在不脱离本发明原理的前提下,还可以对本发明进行若干改进和修饰,这些改进和修饰也落入本发明权利要求的保护范围内。