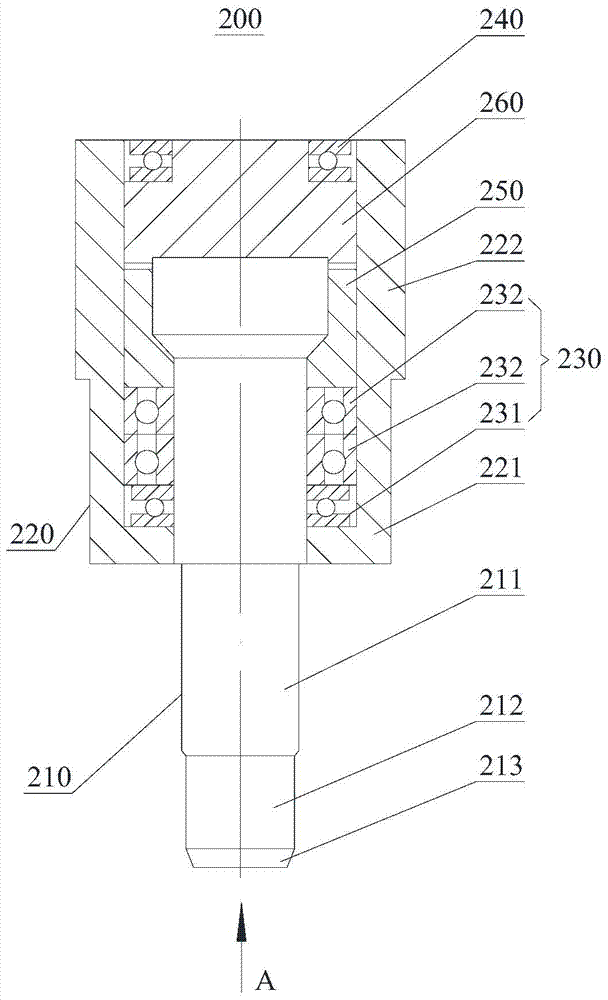
本发明涉及金属精密锻造工艺领域,具体而言,涉及一种汽车起动导向筒的复合挤压加工方法。
背景技术:汽车起动导向筒是汽车起动机中的关键零件,形状复杂,参见图1所示的M93汽车起动导向筒100,其上部具有异型曲面型腔120,下部具有螺旋内花键110。汽车工业中对汽车起动导向筒的精度要求高,尤其是对上部的异型曲面型腔120与下部的螺旋内花键110的同轴度要求。目前,汽车起动导向筒的加工方法通常是分别加工异型曲面型腔和螺旋内花键,具体参见发明专利申请ZL201310291452.5(发明人:王平、王斌、蔡永辉、林鑫焱、严潮红),其公开了一种提高起动导向筒内异型曲面型腔与内花键同轴度的加工方法,该加工方法包括如下步骤:(1)锯料、(2)退火、(3)制坯、(4)抛丸与磷皂化处理、(5)正挤、(6)镦粗、(7)反挤异型曲面型腔及导向孔、(8)基于导向孔旋转挤压螺旋内花键。上述加工工艺虽然在一定程度上提高了上部异型曲面型腔与下部螺旋内花键的同轴度,但仍存在如下问题:1、由于汽车起动导向筒上部异型曲面型腔与下部螺旋内花键是分两次锻造成形的,因此,加工效率低,锻造成本高。2、该加工工艺采用异型曲面型腔反向挤压冲头加工异型曲面型腔,采用螺旋内花键旋转挤压冲头加工汽车螺旋内花键,汽车起动导向筒的异型曲面型腔与螺旋内花键同轴度,不仅受到异型曲面型腔反向挤压冲头和螺旋内花键旋转挤压冲头的影响,还受到导向孔成形精度的影响,因此分次加工工艺很难保证异型曲面型腔与螺旋内花键同轴度,即很难保证汽车起动导向筒的精度。
技术实现要素:本发明的目的在于提供一种汽车起动导向筒的复合挤压加工方法,能够一步完成汽车起动导向筒的异型曲面型腔与螺旋内花键挤压成形,加工效率高、锻造成本低。本发明是这样实现的:一种汽车起动导向筒的复合挤压加工方法,包括以下步骤:锯料;退火;制坯得到坯料;抛丸与磷皂化处理;正挤;镦粗得到工件;钻镗工艺孔;磷皂化处理;异型曲面型腔及螺旋内花键复合挤压成形,得到汽车起动导向筒;其中异型曲面型腔及螺旋内花键复合挤压成形步骤是采用复合挤压冲头对经过磷皂化处理步骤的工件进行加工,复合挤压冲头包括用于旋转挤压加工螺旋内花键的第一冲头和用于反向挤压加工异型曲面型腔的第二冲头,第一冲头和第二冲头同轴设置,第二冲头套设在第一冲头的顶部,第一冲头可绕轴线相对第二冲头旋转的连接于第二冲头。在本发明较佳的实施例中,上述异型曲面型腔与螺旋内花键复合挤压成形步骤中,复合挤压冲头安装于压力机,且对准工艺孔的轴线,压力机带动复合挤压冲头下行,对工件进行复合挤压。在本发明较佳的实施例中,上述第一冲头的底端为导向部,钻镗工艺孔步骤中,钻镗得到的工艺孔的直径等于导向部的直径。在本发明较佳的实施例中,上述工艺孔的直径为φ17mm-φ19mm。在本发明较佳的实施例中,上述异型曲面型腔及螺旋内花键复合挤压成形步骤中,复合挤压冲头挤压形成的异型曲面型腔的有效深度大于22mm时,得到汽车起动导向筒。在本发明较佳的实施例中,上述锯料步骤的过程为:选择直径为φ49mm-φ51mm、材料牌号为20CrMo的热轧圆棒料,对其进行锯料,控制每段锯料的长度为52mm-53mm。在本发明较佳的实施例中,上述退火步骤的过程为:将经过锯料步骤的锯料在炉内加热至780℃-810℃,保温4-7小时;然后降温至690℃-710℃,保温4-7小时;随炉冷至280℃-320℃,出炉空冷。在本发明较佳的实施例中,上述制坯步骤的过程为:将鸡心夹头装在经过退火步骤的锯料的一外圆端后,用顶尖顶住两中心孔,粗车外圆端直径至φ48.1mm-φ48.3mm,并将外圆端倒角至2×45°;再调头将鸡心夹头装在锯料的另一外圆端,用顶尖顶住两中心孔,粗车另一外圆端直径至φ48.1mm-φ48.3mm,并将另一外圆端倒角至2×45°,控制各外圆端长度为51.1mm-51.3mm,得到坯料。在本发明较佳的实施例中,上述正挤步骤中,正向挤压经过抛丸与磷皂化处理步骤的坯料,使坯料的上外圆端的直径为φ48.6mm-φ48.7mm,上外圆端的长度为37.5mm-38mm;使坯料的下外圆端的直径为φ34.5mm-φ34.6mm。在本发明较佳的实施例中,上述镦粗步骤中,将经过正挤步骤的坯料的上外圆端直径镦粗至φ59.6mm-φ59.7mm,得到工件。与现有技术相比,本发明的有益效果是:本发明复合挤压加工方法中,采用复合挤压冲头完成汽车起动导向筒的异型曲面型腔及螺旋内花键复合挤压成形。在冲压过程中,复合挤压冲头的第一冲头可绕其轴线旋转,第二冲头不旋转,第一冲头和第二冲头可同时进行各自对应的加工工作,能够一步完成异型曲面型腔、螺旋内花键成形,且加工得到的异型曲面型腔和螺旋内花键同轴。因此,本发明加工方法能保证汽车起动导向筒的精度,加工效率高、锻造成本低。附图说明为了更清楚地说明本发明实施例的技术方案,下面将对实施例中所需要使用的附图作简单地介绍,应当理解,以下附图仅示出了本发明的某些实施例,因此不应被看作是对范围的限定,对于本领域普通技术人员来讲,在不付出创造性劳动的前提下,还可以根据这些附图获得其他相关的附图。图1为现有技术中M93汽车起动导向筒的结构示意图;图2为本发明实施方式提供的用于加工汽车导向筒的复合挤压冲头的结构示意图;图3为图2中复合挤压冲头的A向结构示意图;图4为本发明实施方式提供的汽车起动导向筒的复合挤压加工方法的工艺流程图;图5为按照图4中复合挤压加工方法加工汽车起动导向筒时的形状变化示意图。图中标记分别为:100-汽车起动导向筒,110-螺旋内花键,120-异型曲面型腔;200-复合挤压冲头,210-第一冲头,211-螺旋内花键成形部,212-导向部,213-圆台;220-第二冲头,221-异型曲面成形部,222-阻挡部;230-第一球轴承,231-推力球轴承,232-向心球轴承,240-第二球轴承,250-定位套,260-压力块。具体实施方式参阅图4和图5所示,本发明实施例提供的一种汽车起动导向筒的复合挤压加工方法,用于加工如图1所示的汽车起动导向筒100,该方法包括以下步骤:锯料;退火;制坯得到坯料;抛丸与磷皂化处理;正挤;镦粗得到工件;钻镗工艺孔;磷皂化处理;异型曲面型腔120及螺旋内花键110复合挤压成形,得到汽车起动导向筒100;其中异型曲面型腔120及螺旋内花键110复合挤压成形步骤是采用复合挤压冲头200对经过磷皂化处理步骤的工件进行加工,参阅图2和图3所示,复合挤压冲头200包括用于旋转挤压加工螺旋内花键110的第一冲头210和用于反向挤压加工异型曲面型腔120的第二冲头220,第一冲头210和第二冲头220同轴设置,第二冲头220套设在第一冲头210的顶部,第一冲头210可绕轴线相对第二冲头220旋转的连接于第二冲头220。复合挤压冲头200由加工螺旋内花键110的第一冲头210和加工异型曲面型腔120的第二冲头220组合而成,能够一步加工得到异型曲面型腔120和螺旋内花键110。第一冲头210和第二冲头220之间为动配合联接,在冲压的过程中,第一冲头210可绕其轴线旋转,旋转挤压加工螺旋内花键110,同时第二冲头220不旋转,直接反向挤压加工异型曲面型腔120,第一冲头210和第二冲头220同时进行各自对应的加工工作,使用复合挤压冲头200能够一步完成异型曲面型腔120、螺旋内花键110成形,从而能够提高汽车起动导向筒的加工效率高,降低锻造成本。复合挤压冲头200的第一冲头210和第二冲头220同轴设置,从而能有效保证加工得到的异型曲面型腔120和螺旋内花键110同轴,进而保证汽车起动导向筒100的精度。复合挤压冲头200的工作过程为:复合挤压冲头200的底端抵住待加工的坯料,压力机的压头压住本复合挤压冲头200下行。在此过程中,第一冲头210与坯料相互作用开始旋转,加工螺旋内花键110,第二冲头220在螺旋内花键110的基础上直接反向挤压冲压加工异型曲面型腔120,从而实现同步加工螺旋内花键110和异型曲面型腔120。进一步地,异型曲面型腔120与螺旋内花键110复合挤压成形步骤中,复合挤压冲头200安装于压力机,且对准工艺孔的轴线,压力机带动复合挤压冲头200下行,对工件进行复合挤压。在异型曲面型腔120与螺旋内花键110复合挤压成形步骤中,复合挤压冲头200的底端抵住待加工的坯料,压力机的压头压住复合挤压冲头200下行。在此过程中,第一冲头210与坯料相互作用开始旋转,加工螺旋内花键110,第二冲头220在螺旋内花键110的基础上冲压加工异型曲面型腔120,从而实现同步加工螺旋内花键110和异型曲面型腔120。进一步地,第一冲头210的底端为导向部212,钻镗工艺孔步骤中,钻镗得到的工艺孔的直径等于导向部212的直径。工艺孔的优选直径为φ17mm-φ19mm。该工艺孔的直径等于导向部212的直径,同时略小于汽车起动导向筒100的螺旋内花键110部分的内径,因此,导向部212可以插入工艺孔内,同时,便于在工艺孔的基础上,对工艺孔进行螺旋内花键110成形。进一步地,异型曲面型腔120及螺旋内花键110复合挤压成形步骤中,复合挤压冲头200挤压形成的异型曲面型腔120的有效深度大于22mm时,有效深度是指M93汽车起动导向筒的图纸要求深度,得到汽车起动导向筒100。进一步地,锯料步骤的过程为:选择直径为φ49mm-φ51mm、材料牌号为20CrMo的热轧圆棒料,对其进行锯料,控制每段锯料的长度为52mm-53mm。进一步地,退火步骤的过程为:将经过锯料步骤的锯料在炉内加热至780℃-810℃,保温4-7小时;然后降温至690℃-710℃,保温4-7小时;随炉冷至280℃-320℃,出炉空冷。进一步地,制坯步骤的过程为:将鸡心夹头装在经过退火步骤的锯料的一外圆端后,用顶尖顶住两中心孔,粗车外圆端直径至φφ48.1mm-φ48.3mm,并将外圆端倒角至2×45°;再调头将鸡心夹头装在锯料的另一外圆端,用顶尖顶住两中心孔,粗车另一外圆端直径至φ48.1mm-φ48.3mm,并将另一外圆端倒角至2×45°,控制各外圆端长度为51.1mm-51.3mm,得到坯料。进一步地,正挤步骤中,正向挤压经过抛丸与磷皂化处理步骤的坯料,使坯料的上外圆端的直径为φ48.6mm-φ48.7mm,上外圆端的长度为37.5mm-38mm;使坯料的下外圆端的直径为φ34.5mm-φ34.6mm。进一步地,镦粗步骤中,将经过正挤步骤的坯料的上外圆端直径镦粗至φ59.6mm-φ59.7mm,得到工件。进一步地,复合挤压冲头200还包括套设于第一冲头210的第一球轴承230和定位套250,第一球轴承230和定位套250均位于第二冲头220内,定位套250位于第一球轴承230上。当第一冲头210自转时,第二冲头220不会发生转动,实现第一冲头210和第二冲头220之间的动配合联接。另外,定位套250的设置用于使第一冲头210的端部定位,从而防止第一冲头210在冲压转动的过程中发生晃动而失效。进一步地,第一球轴承230例如包括由下至上依次排列的1个推力球轴承231和2个向心球轴承232。第一球轴承230按上述方式组合的原因是:向心球轴承232用于承受径向负荷,2个向心球轴承232不仅占用空间较小,而且能够保证第一冲头210与第二冲头220之间的动配合联接效果较好,同时,推力球轴承231位于向心球轴承232上,推力球轴承231能够承载上方的压力机对第一球轴承230的轴向压力,避免第一球轴承230变形失效。进一步地,复合挤压冲头200还包括用于承压的压力块260,压力块260填充于第二冲头220内,且位于第一冲头210上。复合挤压冲头200的压力块260填充于第一冲头210和第二冲头220之间,工作时,压力机的压头压住第二冲头220和压力块260,压力块260将承受的压力传递至第一冲头210。压力块260的设置不仅能承载压力,而且防止第一冲头210与第二冲头220之间发生轴向相对运动,保证第一冲头210和第二冲头220能够各自对工件进行锻造,且异型曲面型腔120和螺旋内花键110的成形符合要求。进一步地,压力块260与第二冲头220接触的面凹陷形成环形槽,环形槽内设置有第二球轴承240。复合挤压冲头200的第二球轴承240设置于压力块260与第二冲头220之间,因此,第一冲头210在绕其轴向转动时,就算第一冲头210带动压力块260发生了转动,由于压力块260与第二冲头220之间为动配合联接,第二冲头220也不会同时绕轴向转动。优选地,第二球轴承240例如为1个推力球轴承231。由于推力球轴承231可承受轴向载荷,因此当压力机沿推力球轴承231的轴向,对推力球轴承231施压时,推力球轴承231不会变形失效,保持压力块260与第二冲头220之间的动配合联接。进一步地,第一冲头210还包括表面具有螺旋花纹的螺旋内花键成形部211,导向部212和螺旋内花键成形部211位于第二冲头220外,导向部212位于第一冲头210的底端,导向部212的直径小于螺旋内花键成形部211的直径。第一冲头210的导向部212位于最低端,用于扩大坯料的工艺孔,使工艺孔的内径适合进行螺旋内花键110成形;螺旋内花键成形部211位于导向部212上,用于进行螺旋内花键110成形。进一步地,导向部212的端面设置一高度为2~3mm、角度为45°的圆台213。复合挤压冲头200的导向部212的端面最先与坯料接触,因此,该端面受到的反作用力最大,容易产生裂纹。在导向部212的端面设置上述规格的圆台213后,圆台213受到坯料的反作用力,该反作用力作用在圆台213的圆锥面上时,会产生指向第一冲头210内部的分力,构成指向第一冲头210内部的压应力。这种分力可以改变环形区域的应力状态,有效解决导向部212端面裂纹的产生。进一步地,第二冲头220包括阻挡部222和异型曲面成形部221,异型曲面成形部221位于第二冲头220的底端,异型曲面成形部221的外径小于阻挡部222的外径,异型曲面成形部221的横截面与待加工的异型曲面型腔120的横截面相同。第二冲头220的异型曲面成形部221位于螺旋内花键成形部211上,用于在已成形的螺旋内花键110的基础上进行异型曲面型腔120成形;阻挡部222位于异型曲面成形部221上,用于阻挡本复合挤压冲头200进一步下行,从而控制异型曲面型腔120的深度。进一步地,异型曲面成形部221的长度等于汽车起动导向筒100的异型曲面型腔120的深度,阻挡部222的长度为异型曲面成形部221的长度的1倍~1.5倍。异型曲面成形部221的长度等于待加工汽车起动导向筒的异型曲面型腔120的深度,才能对工件加工出符合要求的汽车起动导向筒100的异型曲面型腔120。当异型曲面成形部221全部进入工件中,阻挡部222全部露在工件外时,即说明工件的异型曲面型腔120加工完成。另外,阻挡部222的长度过大,第二冲头220整的成本会比较高,阻挡部222的长度过小,第二冲头220无法承受压力机的压力,从而变形失效,当阻挡部222的长度为异型曲面成形部221的长度的1倍~1.5倍时,第二冲头220的结构最为合理。以下结合具体实施例对本发明M93汽车起动导向筒的复合挤压加工方法作进一步的详细描述。实施例1参阅图4和图5所示,实施例1提供了一种M93汽车起动导向筒的复合挤压加工方法,其加工工艺流程为:S101、锯料:选择直径为φ49mm、材料牌号为20CrMo的热轧圆棒料,对其进行锯料,控制每段锯料的长度为52mm。S102、退火:将锯料在炉内加热至780℃,保温4小时,然后降温至690℃,保温4小时,随炉冷至280℃,出炉空冷。S103、制坯:采用制坯机制坯,具体过程为:将鸡心夹头装在锯料的外圆一端后,用顶尖顶住两中心孔,粗车该外圆直径至φ48.1mm,并将端部倒角2×45°;再调头将鸡心夹头装在锯料的外圆另一端,用顶尖顶住两中心孔,,粗车另一端外圆直径至φ48.1mm,并端部倒角2×45°,控制外圆长度在51.1mm,得到坯料。S104、对坯料进行常规抛丸与磷皂化处理,以改进坯料表面质量,并润滑。S105、正挤:正向挤压坯料,使上端外圆直径控制在φ48.6mm,上端外圆长度控制在37.5mm;使下端外圆直径控制在φ34.5mm,下端外圆长度由坯料决定。S106、镦粗:使坯料上端外圆直径镦粗到φ59.6mm,得到工件。S107、钻镗工艺孔:工艺孔直径为φ17mm。S108、对钻镗工艺孔后的工件进行常规磷皂化处理。S109、采用复合挤压冲头200对工件进行异型曲面型腔120及螺旋内花键110复合挤压成形:将复合挤压冲头200安装在压力机上,并随压力机滑块下行,对工件进行复合挤压,直至挤压形成的异型曲面型腔120有效深度大于22mm,最后得到一种M93汽车起动导向筒100。其中,复合挤压冲头200包括用于旋转挤压加工螺旋内花键110的第一冲头210和用于反向挤压加工异型曲面型腔120的第二冲头220,第一冲头210和第二冲头220同轴设置,第二冲头220套在第一冲头210的顶部,第一冲头210和第二冲头220之间采用动配合联接,第一冲头210可绕其轴线旋转。第一冲头210包括导向部212和表面具有螺旋花纹的螺旋内花键成形部211,导向部212和螺旋内花键成形部211位于第二冲头220外,导向部212位于第一冲头210的底端,导向部212的直径小于螺旋内花键成形部211的直径。第二冲头220包括阻挡部222和异型曲面成形部221,异型曲面成形部221位于第二冲头220的底端,异型曲面成形部221的外径小于阻挡部222的外径,异型曲面成形部221的横截面与待加工的异型曲面型腔120的横截面相同。实施例2参阅图4和图5所示,实施例2提供了一种M93汽车起动导向筒的复合挤压加工方法,其加工工艺流程为:S201、锯料:选择直径为φ51mm、材料牌号为20CrMo的热轧圆棒料,对其进行锯料,控制每段锯料的长度为53mm。S202、退火:将锯料在炉内加热至810℃,保温7小时,然后降温至710℃,保温7小时,随炉冷至320℃,出炉空冷。S203、制坯:采用制坯机制坯,具体过程为:将鸡心夹头装在锯料的外圆一端后,用顶尖顶住两中心孔,粗车该外圆直径至φ48.3mm,并将端部倒角2×45°;再调头将鸡心夹头装在锯料的外圆另一端,用顶尖顶住两中心孔,粗车另一端外圆直径至φ48.3mm,并端部倒角2×45°,控制外圆长度在51.3mm,得到坯料。S204、对坯料进行常规抛丸与磷皂化处理,以改进坯料表面质量,并润滑。S205、正挤:正向挤压坯料,使上端外圆直径控制在φ48.7mm,上端外圆长度控制在38mm;使下端外圆直径控制在φ34.6mm,下端外圆长度由坯料决定。S206、镦粗:使坯料上端外圆直径镦粗到φ59.7mm,得到工件。S207、钻镗工艺孔:工艺孔直径为φ19mm。S208、对钻镗工艺孔后的工件进行常规磷皂化处理。S209、采用与实施例1相同的复合挤压冲头200对工件进行异型曲面型腔120及螺旋内花键110复合挤压成形:将复合挤压冲头200安装在压力机上,并随压力机滑块下行,对工件进行复合挤压,直至挤压形成的异型曲面型腔120的有效深度大于22mm,最后得到一种M93汽车起动导向筒100。以上所述仅为本发明的优选实施例而已,并不用于限制本发明,对于本领域的技术人员来说,本发明可以有各种更改和变化。凡在本发明的精神和原则之内,所作的任何修改、等同替换、改进等,均应包含在本发明的保护范围之内。