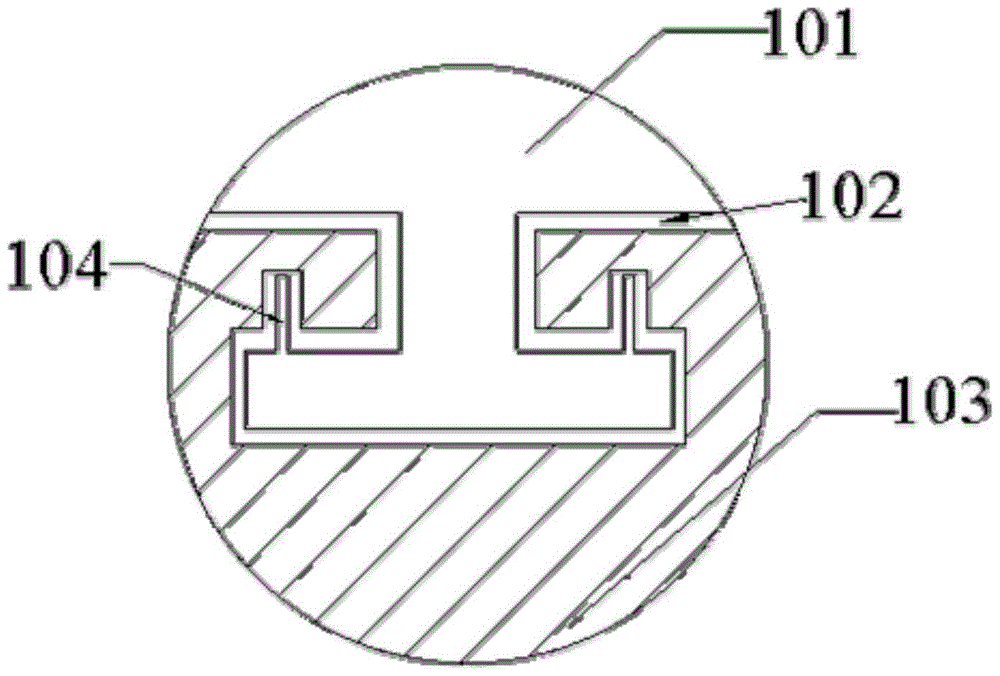
本发明属于超硬材料制备领域,特别地涉及一种具有内嵌结构的聚晶金刚石复合片及其制造方法。
背景技术:聚晶金刚石复合片是一种金刚石聚晶与硬质合金基体组成的复合材料,具有硬度高、耐磨性好的特点。现有聚晶金刚石-硬质合金复合片通常采用钨钴类硬质合金作为基体材料,然后在高温(通常1200~1600℃)、高压(通常5Gpa以上)的一次合成;也有采用CVD聚晶切割片增强的制造方法,如公开号为102700191A,公开日为2012年10月3日的中国发明专利ZL201210200657.3。其他,如在硬质合金上进行CVD或者PVD金刚石或者立方氮化硼、氮化钛涂层。该技术已经应用多年,但该技术仅仅是为提高硬质合金的切削性能,是硬质合金性能提升的拓展延续。采用CVD、PVD处理的金刚石涂层硬质合金,主要应用在金属切削方面。地质钻探用材料通常要求材料具有高硬度、高强度,高耐磨性、抗冲击等好的综合性能而不是单一性能。采用硬质合金进行CVD或者PVD处理的材料难以适应高性能地质钻探的使用要求,尤其是石油钻探高钻探深度的要求,这类钻探最忌讳井底损坏。钻探用材料的要求是具有抗冲击性,一般选用高含钴量的钨钴类硬质合金。高含钴量的硬质合金对金刚石聚晶的直接影响就是对金刚石使用过程的反催化,促使金刚石石墨化,从而,降低金刚石聚晶的性能。钨钴类硬质合金具有强度高、硬度高的特点,但其韧性差、抗冲击性能差,在地质钻探等场合难以适应要求。目前,为改善此类基底硬质合金的性能,还集中在添加晶粒细化剂等研究方向上。随着市场需求发展,现聚硬质合金-晶金刚石复合片向大尺寸,高厚度聚晶层发展,聚晶层厚度目前已经达到4mm。但由于硬质合金与金刚石聚晶具有不同的特性,这些材料由于膨胀系数及温度等影响,目前在大尺寸,高厚度硬质合金-金刚石聚晶复合片生产上容易产生结合界面应力破坏,从而导致复合片的界面失效,即复合片从界面处断裂分离。采用CVD聚晶母材切割片增强的聚晶复合片,是制造金刚石聚晶复合片的另外工艺。采用CVD法可生产大尺寸、高厚度聚晶金刚石母材。但在聚晶金刚石块体与基底材料的复合上,目前还鲜有研究。如公开号为102700191A,公开日为2012年10月3日的中国发明专利ZL201210200657.3公开了一种制造方法,但该方法只是采用简单的热压烧结工艺,聚晶CVD金刚石增强条与金刚石聚晶微粉之间无法形成有效的C-C共价键的化学键结合,聚晶微粉与微粉之间也未形成有效的C-C共价键的化学键结合,只是简单的聚晶混合烧结体,产品性能差是工艺缺陷的必然。另外,将CVD聚晶切割片与金刚石聚晶微粉埋入硬质合金粉末中进行压制、烧结,尤其是在氢气气氛下进行烧结,由于钴的“反催化”及氢气的“脱碳”效应,会显著降低金刚石聚晶及聚晶复合片的性能,这种制造方法有待进一步提升。采用大尺寸聚晶母材可以利用激光切割成各种现状的聚晶形状,但这种形状难以与基底硬质合金进行有效复合。尤其是,当需要基底硬质合金为不规则形,特别是带内横向或纵向、斜向盲孔结构时,更难以形成有效结合。
技术实现要素:为解决上述问题,本发明的目的在于提供一种具有内嵌结构的聚晶金刚石复合片制造方法,硬质合金具有内盲孔等异形结构同时具有复合过渡层,减缓或消除金刚石与硬质合金材料使用过程钴反催化效应,是提高硬质合金聚晶复合片性能的一种有效方法。本发明又一目的在于提供一种具有内嵌结构的聚晶金刚石复合片,使得金刚石复合片具有内盲孔等异形结构同时具有复合过渡层。为实现上述目的,本发明的技术方案为:一种具有内嵌结构的聚晶金刚石复合片制造方法,包括以下步骤:S10,选用硬质合金喂料与过渡层喂料,于顶部设置有若干倒T型凹槽的模具中进行共注射,倒T型凹槽的一字边两侧设置有横向盲孔,注射压力为8~82MPa,注射温度140~200℃,后将注射件脱脂、烧结,烧结温度1200~1500℃,时间2~24小时,得含过渡层注射烧结复合件;S20,聚晶准备S201,选用球形微米级金刚石,金刚石微粉粒度为1~40微米,与接合剂进行混合球磨;S202,将球形微米级金刚石与接合剂混合球磨产物进行真空干燥,干燥温度500~600℃;S203,将干燥物压制成聚晶片;S30,聚晶复合片合成S301,将硬质合金基底与聚晶压制片装入叶蜡石块体中;S302,将组装好的叶蜡石块体放入六面顶或两面顶中,逐步加压致3.1~8.4GPa,通电流加热,维持5~16min;S303,卸掉载荷,进行后续脱除处理并在聚晶层渗入硅合金即获得聚晶复台片。优选地,设置有盲孔的模具为具有纵向盲孔的模具,注射压力为8~60MPa。优选地,设置有盲孔的模具为具有横向盲孔的模具,注射压力为8~80MPa。优选地,设置有盲孔的模具为具有斜向盲孔的模具,注射压力为8~82MPa。优选地,设置有盲孔的模具为具有横向,纵向和斜向三向盲孔的模具,注射压力为10~82MPa。优选地,所述过渡层喂料为无碳氮化物氮化钛,粘结剂为水基材料。优选地,所述过渡层喂料为无碳氮化物氮化硼,粘结剂为水基材料。优选地,所述过渡层喂料为无碳氮化物氮化铝,粘结剂为水基材料。本发明又一技术方案为:一种具有内嵌结构的聚晶金刚石复合片,通过上述任一所述的方法获得,底层为顶部具有倒T型凹槽的硬质合金基底层,硬质合金基底层顶部的边缘上为过渡层,过渡层上方为与过渡层形状互补的金刚石聚晶层,三层结构嵌合形成整体结构。与现有技术相比,本发明的有益效果如下:(1)具有更加复杂的异形孔结构,可以进一步提高金刚石聚晶与硬质合金之间的结合把持力;(2)消除了产品在使用过程中钴反催化对产品性能的影响;(3)提高了产品的抗冲击性能;可以实现大尺寸,高厚度聚晶层因界面结合应力作用而产生的界面断裂,提高了产品的抗冲击性能。附图说明图1为本发明实施例1的具有内嵌结构的聚晶金刚石复合片的剖面结构示意图;图2为图1中A部分的放大结构示意图;图3为本发明实施例2的具有内嵌结构的聚晶金刚石复合片的剖面结构示意图;图4为图3中B部分的放大结构示意图;图5为本发明实施例3的具有内嵌结构的聚晶金刚石复合片的剖面结构示意图;图6为图5中C部分的放大结构示意图;图7为本发明实施例4的具有内嵌结构的聚晶金刚石复合片的剖面结构示意图;图8为图7中D部分的放大结构示意图。具体实施方式为了使本发明的目的、技术方案及优点更加清楚明白,以下结合附图及实施例,对本发明进行进一步详细说明。应当理解,此处所描述的具体实施例仅仅用以解释本发明,并不用于限定本发明。相反,本发明涵盖任何由权利要求定义的在本发明的精髓和范围上做的替代、修改、等效方法以及方案。进一步,为了使公众对本发明有更好的了解,在下文对本发明的细节描述中,详尽描述了一些特定的细节部分。对本领域技术人员来说没有这些细节部分的描述也可以完全理解本发明。实施例1S10,选用硬质合金喂料与氮化硼喂料,于具有倒T型凹槽的模具中进行共注射,倒T型凹槽的一字边两侧设置有纵向盲孔,注射压力为8~60MPa,注射温度140~200℃,然后将注射件脱脂、烧结,烧结温度1200~1500℃,时间2~24小时,得含过渡层的注射烧结复合件。S20聚晶金刚石准备S201,选用球形微米级金刚石,金刚石微粉粒度1~40微米,与接合剂进行混合球磨;S202,将混合球磨产物进行真空干燥,干燥温度500~600℃;S203,将干燥物压制成聚晶片;S30,聚晶金刚石复合片合成S301,将硬质合金基底与聚晶压制片装入叶蜡石块体中;S302,将组装好的叶蜡石块体放入六面顶或两面顶中,逐步加压致3.2~8GPa,通电流加热,维持5~12min;S303,卸掉载荷,进行后续脱除处理并在聚晶层渗入硅合金即获得聚晶复台片。参见图1所示为采用上述方法获的具有内嵌结构的聚晶金刚石复合片的剖面结构示意图,图2为图1中A部分的局部放大图,该聚晶金刚石复合片底层为顶部具有倒T型凹槽的硬质合金基底层103,倒T型凹槽的一字边的两侧设置有纵向盲孔104,硬质合金基底层顶部的边缘上为过渡层102,过渡层102上方为与过渡层形状互补的金刚石聚晶层101,三层结构嵌合形成整体结构。纵向盲孔中的硬质合金注射材料起到加强复合片强度的作用。经检测,与目前市售复合片比较,磨耗比达到49.2~52.6万。产品耐热性能检测,产品在750℃焙烧2分钟后,磨耗比达49.1~52.5万。说明产品焙烧前后磨耗比相差不大,在硬质合金表面处理后,使用过程金刚石与基底之间未产生石墨化效应,与通过ZL201210200657.3的方法所得的金刚石聚晶复合片在同等条件下进行比较,性能提高21%。实施例2S10,选用硬质合金喂料与氮化铝喂料,于具有倒T型凹槽的模具中进行共注射,倒T型凹槽的一字边两侧设置有横向盲孔,注射压力8~80MPa,注射温度140~200℃,后将注射件脱脂、烧结。烧结温度1200~1480℃,时间2~24小时,得含过渡层注射烧结复合件;S20,聚晶准备S201,选用球形微米级金刚石,金刚石微粉粒度1~40微米,与接合剂进行混合球磨;S202,将混合球磨产物进行真空干燥,干燥温度500~600℃;S203,将干燥物压制成聚晶片;S30,聚晶金刚石复合片合成S301,将硬质合金基底与聚晶压制片装入叶蜡石块体中;S302,将组装好的叶蜡石块体放入六面顶或两面顶中,逐步加压至3.1~7.8GPa,通电流加热,维持5~16min;S303,卸掉载荷,进行后续脱除处理并在聚晶层渗入硅合金即获得聚晶复台片。参见图3所示为采用上述方法获得具有内嵌结构的聚晶金刚石复合片的剖面结构示意图,图4为图3的B部分的局部放大图,该聚晶金刚石复合片底层为顶部具有倒T型凹槽的硬质合金基底层103,倒T型凹槽的一字边的两侧设置有横向盲孔104,硬质合金基底层顶部的边缘上为过渡层102,过渡层102上方为与过渡层形状互补的金刚石聚晶层101,三层结构嵌合形成整体结构。横向盲孔中的硬质合金注射材料起到加强复合片强度的作用。经检测,与目前市售复合片比较,磨耗比达到48.6~50.2万。产品耐热性能检测,产品在750℃焙烧2分钟后,磨耗比达48.4~50.3万。说明产品焙烧前后磨耗比相差不大,说明,在硬质合金表面处理后,使用过程金刚石与基底之间未产生石墨化效应。与通过ZL201210200657.3的方法所得的金刚石聚晶复合片在同等条件下进行比较,性能提高18%。实施例3S10,选用硬质合金喂料与氮化铝喂料,于具有倒T型凹槽的模具中进行共注射,倒T型凹槽的一字边两侧设置有斜向盲孔,注射压力8~82MPa,注射温度150~210℃,后将注射件脱脂、烧结,烧结温度为1200~1500℃,时间为2~24小时,得含过渡层注射烧结复合件;S20,聚晶金刚石片准备S201,选用球形微米级金刚石,金刚石微粉粒度1~40微米,与接合剂进行混合球磨;S202,将混合球磨产物进行真空干燥,干燥温度500~600℃;S203,将干燥物压制成聚晶金刚石片;S30,聚晶复合片合成S301,将硬质合金基底与聚晶压制片装入叶蜡石块体中;S302,将组装好的叶蜡石块体放入六面顶或两面顶中,逐步加压致3.6~8.4GPa,通电流加热,维持5~12min;S303,卸掉载荷,进行后续脱除处理并在聚晶层渗入硅合金即获得聚晶复台片。参见图5所示为采用上述方法获得的具有内嵌结构的聚晶金刚石复合片的剖面结构示意图,图6为图5的C部分的局部放大图,该聚晶金刚石复合片底层为顶部具有倒T型凹槽的硬质合金基底层103,倒T型凹槽的一字边的两侧设置有斜向盲孔106,硬质合金基底层顶部的边缘上为过渡层102,过渡层102上方为与过渡层形状互补的金刚石聚晶层101,三层结构嵌合形成整体结构。斜向盲孔中的硬质合金注射材料起到加强复合片强度的作用。经检测,与目前市售复合片比较,磨耗比达到52.6~54.3万。产品耐热性能检测,产品在750℃焙烧2分钟后,磨耗比达52.4~54.2万。说明产品焙烧前后磨耗比相差不大,在硬质合金表面处理后,使用过程金刚石与基底之间未产生石墨化效应。与通过ZL201210200657.3的方法所得的金刚石聚晶复合片在同等条件下进行比较,性能提高24%。实施例4S10,选用硬质合金喂料与氮化铝喂料,于具有倒T型凹槽的模具中进行共注射,倒T型凹槽的一字边两侧设置有纵向,横向和斜向三向盲孔,注射压力10~82MPa,注射温度150~210℃,后将注射件脱脂、烧结,烧结温度为1200~1500℃,时间为2~24小时,得含过渡层注射烧结复合件;S20,聚晶金刚石片准备S201,选用球形微米级金刚石,金刚石微粉粒度1~40微米,与接合剂进行混合球磨;S202,将混合球磨产物进行真空干燥,干燥温度500~600℃;S203,将干燥物压制成聚晶金刚石片;S30,聚晶复合片合成S301,将硬质合金基底与聚晶压制片装入叶蜡石块体中;S302,将组装好的叶蜡石块体放入六面顶或两面顶中,逐步加压致3.6~8.4GPa,通电流加热,维持5~12min;S303,卸掉载荷,进行后续脱除处理并在聚晶层渗入硅合金即获得聚晶复台片。参见图7所示为采用上述方法获得的具有内嵌结构的聚晶金刚石复合片的剖面结构示意图,图8为图7的D部分的局部放大图,该聚晶金刚石复合片底层为顶部具有倒T型凹槽的硬质合金基底层103,倒T型凹槽的一字边的两侧设置有纵向盲孔104,横向盲孔105和斜向盲孔106,硬质合金基底层顶部的边缘上为过渡层102,过渡层102上方为与过渡层形状互补的金刚石聚晶层101,三层结构嵌合形成整体结构。纵向盲孔,横向盲孔和斜向盲孔中的硬质合金注射材料起到加强复合片强度的作用。经检测,与目前市售复合片比较,磨耗比达到52.6~54.3万。产品耐热性能检测,产品在750℃焙烧2分钟后,磨耗比达52.4~54.2万。说明产品焙烧前后磨耗比相差不大,在硬质合金表面处理后,使用过程金刚石与基底之间未产生石墨化效应。与通过ZL201210200657.3的方法所得的金刚石聚晶复合片在同等条件下进行比较,性能提高24%。以上所述仅为本发明的较佳实施例而已,并不用以限制本发明,凡在本发明的精神和原则之内所作的任何修改、等同替换和改进等,均应包含在本发明的保护范围之内。