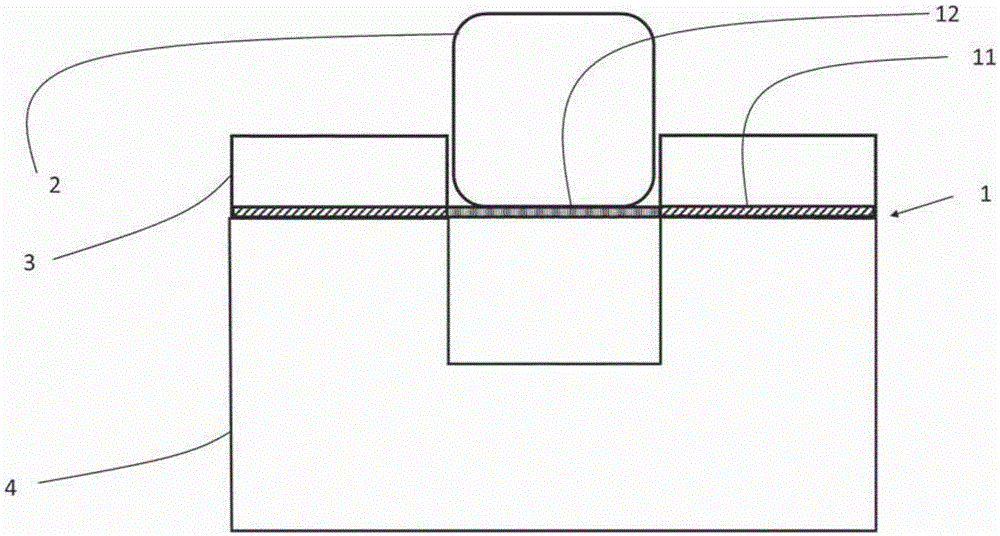
本发明涉及适用于汽车工业的具有特别定制特性的铝合金坯件。
背景技术:
:各种铝合金以板材或坯件的形式用于汽车应用中。在这些合金中,已知aa6xxx铝合金系列(例如aa6016-t4)兼具令人感兴趣的化学特征和机械特性,例如硬度、强度以及甚至是耐腐蚀性。这些特性通常使aa6xxx铝合金成为汽车工业中选择的材料。为了改进aa6xxx合金的机械强度,例如在wo2012/033954中提出,在固溶热处理之后将板材冷加工至少25%,然后进行热处理。然而,已知冷加工后的aa6xxx的可成形性比t4状态差。替代材料为aa5xxx铝合金,例如aa5182-o和aa5754-o,其提供了机械耐受性与可成形性的良好平衡。然而,在烤漆处理后,aa5xxx合金的机械技术参数低于aa6xxx合金。在6xxx铝合金板材或坯件内,机械特性是均匀的,而由该坯件成形的部件局部地受到各种应变。因此,在某些区域,所述部件必须是过度设计的,以满足获得目标性能值的最低要求。过去已进行了一些尝试来改善铝合金的可成形性。由德国专利申请de102009031449a1已知一种形成铝板材的方法,其包括局部加热铝板材的步骤。该方法也需要使铝板材热成型。德国专利申请de102013013359a1也记载了一种形成铝板材的方法,包括在250至325℃下局部加热铝板材以及使铝板材冷成型的步骤。然而,热处理温度太低以致无法改善铝板材或坯件的可成形性。由欧洲专利ep2554288b1已知一种热处理铝板材材料的方法,包括以下步骤:提供铝板材材料;将铝板材材料加热至高于或等于加热温度的温度(t);在加热期间保持所述温度(t);在淬火期间,将铝板材材料的至少一个淬火区域淬火至低于或等于淬火温度的温度(t);将铝板材材料的至少一个区域冷却至低于或等于冷却温度的温度(t),其中冷却在大于淬火时间段的冷却时间段内进行,并在淬火过程中通过工具保护冷却区域。该方法的缺点是,难于工业化,并需要另外的步骤和装置来加热整个铝板材以及在淬火过程中覆盖和保护铝板材的冷却区域。由国际专利申请wo97/44147a1已知一种通过在成形区域进行热处理来形成铝合金构件的方法。然而,这种方法需要加热源例如激光束,并且还需要在进行热处理步骤后的短时间内(即在热处理步骤后约12小时)形成铝合金构件。还由美国专利第8,211,251b2号已知通过局部加热铝板以将局部屈服强度提高至150至300mpa。然而,该方法不适于同时改善铝合金板材的屈服强度和可成形性。欧洲专利ep1601478b1记载了一种制造由铝合金制成的拉伸部件的方法,包括以下步骤:制造厚度为0.5至5mm的带材,其具有以下合金组成:1至6重量%的mg、小于1.2重量%的mn、小于1重量%的cu、小于1重量%的zn、小于3重量%的si、小于2重量%的fe、小于0.4重量%的cr、小于0.3重量%的zr,其他元素各自小于0.1重量%且总计小于0.5重量%,余量为al;从带材上切割下坯件;将坯件局部或全部加热至150至350℃的温度持续30秒或更短;在与后续操作相容的润滑剂的存在下,使用加热至150至350℃的温度的工具拉伸加热的坯件。然而,ep1601478b1的方法难以工业化,因为它需要拉伸或冲压工具加热至150至350℃的温度。还由专利和专利申请例如ep2075348b1、jp2011-115837a1、jp2013-023747a1、jp2013-010998a1、jp2010-22795a1已知多种加工铝合金的方法,然而,这些方法均在不能提供足够的可成形性的中等加热温度下操作。因此,在汽车工业中需要这样的6xxx系列铝合金坯件,其兼具高拉伸屈服强度和与冷冲压操作相适应的良好的可成形性特性。技术实现要素:发明人通过下述方法已获得了这种兼具高的拉伸屈服应力和可成形性的铝合金坯件,所述方法包括以下连续步骤:a)提供6xxx系列铝合金板坯;b)任选地,使所述板坯均质化;c)热轧以及任选地冷轧所述板坯,获得板材;d)固溶热处理并淬火所述板材;e)以至少20%的冷加工压缩量冷轧所述板材,;f)将所述板材切割成坯件;g)在360℃至480℃的温度下,使所述坯件的凸缘的一部分快速退火足够的时间,以获得所述凸缘的该部分的再结晶,和冷却至低于100℃的温度。根据本发明,冲压的铝合金产品通过以下方式获得:将本发明的坯件的凸缘放置在压力机的坯件夹持器内;冲压所述坯件,获得粗冲压产品;从所述粗冲压产品中除去凸缘。本发明的冲压的铝合金产品可用于汽车应用。附图说明图1是冲压过程的整体示意图。坯件1保持在坯件夹持器3和模头4之间。可以区分坯件的两个区域:凸缘11,其在冲压开始时在坯件夹持器和模头之间;和坯件的其余部分12,其位于冲头2下方。图2a至2d为坯件1的俯视图,其示出了坯件的凸缘11、位于冲头下方的其余部分12,其余部分12为十字形状。所述凸缘具有再结晶部分111和非再结晶部分112。图3为条形图,其表示针对t4-状态下的aa6016(参照)、冷加工后的aa6016(cw)、退火后的aa6016(cw-a1)和根据本发明方法的样品(样品1至样品4)所获得的最大拉伸深度。图4是适合于对本发明的铝合金坯件1的凸缘的一部分111进行局部快速退火的装置的示意图,该装置具有加热系统51、加热板52和绝热件53。图5是表示穿过实施例2的组成1的快速退火坯件所测量的硬度的曲线图。图6是表示穿过实施例2的组成2的快速退火坯件所测量的硬度的曲线图。图7是表示根据本发明对组合物1和2使用50%冷加工所获得的最大拉伸深度(以mm计)的条形图。具体实施方式除非另有说明,在下文提到的所有铝合金均使用“铝业协会”在定期出版的“登记记录序列(registrationrecordseries)”中所定义的规则和名称命名。提到的冶金状态使用欧洲标准en-515命名。发明人已发现,冷加工的6xxx铝合金系列的可成形性可以在不损害其机械强度和耐受性的情况下得到改善。这些合金的改进性能通过在坯件的凸缘的一部分上进行短暂热处理获得,这在本文中也称为局部快速退火。根据本发明,使用6xxx系列铝合金制备板坯。本发明特别优选的铝合金组成为aa6016、aa6111、aa6013和aa6056。在本发明的一个实施方案中,所述6xxx系列铝合金包含以重量%计的以下组成:si:0.7-1.0;mg:1.2-1.6;cu:最高达0.8;mn:最高达0.7;zn:最高达1;fe:最高达0.5;ti:最高达0.15,余量为铝和最高达0.05且总计最高达0.15的不可避免的杂质,优选si:0.7-0.9;mg:1.2-1.6;cu:最高达0.3;mn:最高达0.3;zn:最高达0.05;fe:0.1-0.4;ti:0.01-0.05,余量为铝和最高达0.05且总计最高达0.15的不可避免的杂质。然后,任选地将板坯例如在约500℃的温度下均质化,通常持续8小时,优选在接近通常高于550℃的固相线温度下,持续至少1小时。通过将板坯热轧至通常约4至10mm的厚度获得铝合金板材。在热轧步骤之后,也可以直接进行任选的冷轧操作,以进一步减小铝板材的厚度。然后,将板材进行固溶热处理和淬火。优选的条件是在接近通常高于550℃的固相线温度的温度下加热约5分钟,然后水淬火。然后,进行冷轧以进一步将铝板材减小到更低的厚度并增加强度,其中冷加工压缩量为至少20%,优选至少30%,更优选至少50%。在冷轧操作之后,板材的晶粒是纤维状的、非再结晶的。优选地,该冷轧操作后,板材最终厚度为3mm或更小,通常为1.0至1.5mm。在该最后的冷轧步骤之后并且在切割步骤之前有利的是,在足以使伸长率a%在lt方向上增加至少15%且拉伸屈服强度在lt方向上的变化小于15%的时间和温度下,使板材退火。优选地,在lt方向上伸长率a%增加至少20%或甚至是25%。通常,该退火可以通过在150至260℃、优选160至190℃的温度下的间歇处理来进行,通常持续5至30分钟。然而,如果有连续退火炉,则其他条件也是可行的。该操作可使伸长率最大化,而不使强度发生显著变化。然后,将该板材切割成所需尺寸和形状的坯件。然后,对铝合金坯件的凸缘的一部分进行局部快速退火和冷却,该步骤包括热且短暂的加热,以至少部分地使所述凸缘的该部分再结晶。在本发明中,坯件的凸缘为坯件的这样的区域,其被设计成在冲压过程开始时置于坯件夹持器和模头之间。图1示出了典型的冲压过程。坯件1保持在坯件夹持器3和模头4之间。凸缘11在冲压过程开始时位于坯件夹持器和模头之间,坯件的其余部分12位于冲头2的下方。图2a至2d为俯视图,其示出了具有凸缘11和位于冲头下方的其余部分12的坯件1的实例,所述其余部分12在该示例性实例中是十字形的。凸缘的两个部分表示为:凸缘的再结晶部分111由砖形表示,凸缘的其余部分112由点表示。凸缘的其余部分112和坯件的其余部分12基本上保持不受快速退火的影响。所述凸缘的该部分111的至少25%的晶粒是再结晶的,优选地,所述凸缘的该部分的至少50%或甚至至少75%的晶粒是再结晶的。在一个实施方案中,所述凸缘的该再结晶部分占所述凸缘表面的至少80%,如图2a所示。然而,在例如图2c和2d所示的其他实施方案中,只有凸缘的特定位置(与模头形状相关)进行快速退火,获得局部再结晶。图4是适于使铝合金坯件1的所述凸缘的该部分局部快速退火的装置的示意图,所述装置具有加热系统51、加热板52和绝热件53。所述凸缘的一部分111与加热板接触而获得局部再结晶。这样进行快速退火(通常使用局部加热坯件的接触板52进行),使得凸缘的一部分的温度为360℃至480℃,优选为380℃至460℃,更优选为400℃至440℃,持续足以获得再结晶的时间(通常至少5秒)并且足够短以获得局部效应(通常小于60秒)。可以调节快速退火条件以获得所需的铝坯件可成形性特性,例如通过使用不同尺寸和形状的加热接触板。优选地,快速退火时间为10至30秒。然后,将局部快速退火的坯件冷却至低于100℃的温度,优选人工冷却。优选地,冷却速率为至少30℃/s并且优选为至少50℃/s。人工冷却可以用强制空气流或水淬火进行。水淬火可限制朝向坯件中心的加热程度,这种加热可能导致强度降低。局部快速退火优选通过传热、通过使坯件与加热的铝板接触来实现。在一个实施方案中,通过使坯件在20秒内与加热到470℃的宽度为40mm的接触板接触而获得约400℃的温度,然后进行水淬火,进而获得快速退火的铝坯件。快速退火可进行一次或连续进行多次。在一个实施方案中,快速退火重复至少两次,但是对于生产率而言,有利地是仅进行一次局部快速退火。为了满足工业生产率要求,可以通过红外或激光照射、感应或传导进行局部快速退火。在一个实施方案中,局部快速退火处理在多个操作中通过使坯件在20秒内与不同宽度的配置(layout)接触来实现,例如,在约470℃的温度下与宽度为20、30和40mm的三种靠模样板(contourplate)配置接触而获得局部为400至420℃的坯件温度,并在各加热操作后进行水淬火。多次局部快速退火可允许在部分凸缘内进行更多的再结晶。局部快速退火导致坯件夹持器下方的金属局部软化,可实现推迟如更深部件的失效极限。改善的可成形性与强度的平衡特别适用于冷加工过程和例如在汽车工业中的应用。通过本发明的方法获得的局部再结晶铝坯件可以在冲压之前在室温下储存至少一天或甚至至少一周或更长时间而不损害其有利的特性。然后,通过冲压将局部快速退火的铝坯件成形为其最终形状,并优选通过切割从粗冲压产品上除去凸缘,例如冲压产品基本上由相同冶金状态(即在冷轧和任选的退火后获得)的铝组成。因此,冲压的铝合金产品通过以下方式获得:-将本发明的坯件的凸缘置于压力机的坯件夹持器内;-冲压所述坯件以获得粗冲压产品;-从所述粗冲压产品中除去凸缘。应注意的是,优选压力机的坯件夹持器不被加热。坯件在与冲压步骤分开的步骤中进行快速退火。有利地,冲压产品基本上是非再结晶的,其中小于25%的晶粒被再结晶,优选小于15%的晶粒被再结晶,更优选小于5%的晶粒被再结晶。任选地,冲压产品可以通过oem涂装线,并接受油漆烘烤热处理,通常在180℃下持续20分钟。冲压产品基本上由均质的铝合金构成,其强度更高,即相比于通过本发明方法的相同处理步骤a)至f)获得的相同合金的坯件在t4-状态下测得的lt方向上的拉伸屈服强度,所述冲压产品通常在lt方向上的拉伸屈服强度比其高至少25%,优选高至少50%,更优选高至少75%。优选地,相比于在“tempersforaluminumandaluminumalloyproductseditedbythealuminumassociation”(2011)中的相同铝业协会编号下登记的合金在t4-状态下定义为最小拉伸强度的拉伸屈服强度,所述冲压产品在lt方向上的拉伸屈服强度比其高至少25%,优选高至少50%,更优选高至少75%。优选地,冲压产品在lt方向上的拉伸屈服强度为至少250mpa,优选至少290mpa,更优选至少320mpa。在一个实施方案中,本发明的冲压产品由合金aa6016制成,并具有至少310mpa的拉伸屈服强度。在一个实施方案中,本发明的冲压产品在涂装线之后,通常在180℃下热处理20分钟后,在lt方向上的拉伸屈服强度为至少290mpa,优选至少350mpa,更优选至少400mpa,甚至更优选至少430mpa。本发明的冲压的铝合金产品有利地用于汽车应用。不囿于任何理论,发明人认为通过快速局部退火引起的再结晶适于在铝板材板中产生强度梯度。通过迫使凸缘区域有助于形成和释放临界区域而使该梯度产生更好的应变分布。实施例实施例1根据本发明制备aa6016铝合金坯件:·铸造aa6016铝合金板坯,其具有下表1中的组成,以重量%计:重量%sifecumnmgcrznti60161.150.150.120.090.350.020.010.02表1·使所述铝合金板坯均质化;·热轧所述板坯,获得厚度为5.45mm的铝合金板材;·固溶热处理和淬火;·通过施用压缩量为45%和66%的2个冷轧步骤冷轧所述板材,获得1.03mm的最终厚度;·在175℃(a1)或在200℃(a2)下退火5分钟;·切割成所需的尺寸和形状,获得铝合金坯件;·使坯件的凸缘的一部分快速退火为了比较,将样品冷轧至1mm的厚度,然后进行固溶热处理、淬火并自然时效至t4状态,其称为6016-t4。冷轧后未经任何进一步处理得到的产品称为6016-cw。冷轧后和退火a1或a2后获得的产品分别称为6016-cw-a1和6016-cw-a2。在长横向(lt)方向上测量一些产品的机械特性,并示于表2中。表2如图2所示,通过不对称十字模头测试评估铝合金的冲压能力和可成形性。所述测试包括:定位厚度约1mm的坯件样品;将坯件的凸缘保持在坯件夹持器内;使用液压机将30巴的坯件夹持器压力施加至坯件,测定通过将220mm×160mm的不对称十字冲模配置施用至坯件所获得的最大拉伸深度。通过传热,即通过在一个或多个操作中使坯件与轮廓宽度为20、30或40mm的加热板52接触,实现局部快速退火(图4)。加热系统51的温度设定为470℃,对应于坯件上约400℃的温度。将坯件铺设在初始温度为至多50℃的绝热体53上。持续时间设定为每次通过20秒。然后,在每次通过后对坯件进行水淬火。表3中给出了坯件的一部分凸缘的快速退火条件。凸缘经处理的区域的宽度以mm为单位给出。样品1对于20、30和40mm的轮廓宽度快速退火三次,而样品2仅对于30mm的轮廓宽度处理一次。在对样品1至4进行快速退火之后,一部分凸缘至少部分地再结晶。样品退火样品20mm30mm40mm样品16016-cw-a1xxx样品26016-cw-a2x样品36016-cw-a2xx样品46016-cw-a2xx表3:快速退火条件图3给出了拉伸深度结果。冷轧后且退火前的冷加工样品(cw)具有差的可成形性,其最大拉伸深度为约12mm。在退火(cw-a1)之后,拉伸深度略微提高至约15mm,这有助于更好的可成形性。与仅退火的样品如6016-cw-a1相比,根据本发明方法获得的所有样品均显示出改善的拉伸能力。通过使用宽为20、30和40mm的接触板施加3次局部快速退火加热而获得的样品1显示出与aa6016-t4的拉伸深度能力相当的拉伸深度能力。由于局部快速退火处理的部分被限制在凸缘区域并从冲压的产品上移除并切下,因此冲压产品仅由相同冶金状态的铝合金构成。这证明是特别有利的,因为它可实现可成形性与机械耐受性的良好平衡。本发明的方法表现为用于形成具有较高的可成形性与强度平衡的铝板材产品的工业上可行的方法,所述铝板材产品通常太复杂而不能用常规方法冲压。因此,该方法特别适用于通常需要良好的可成形性与强度平衡的汽车应用。实施例2铸造两种本发明的铝合金组成(1和2)。这些组成在下表4中详述,以重量%计。重量%sifecumnmgznti组成10.80.190.150.101.400.02组成20.80.190.960.101.40.70.02表4然后,将铸锭去皮,在580℃下均质化1小时(称为580)或在500℃下均质化8小时(称为500),热轧,固溶热处理,淬火并通过50%或75%的冷加工冷轧至1.5mm厚。将1.5mm的板材在170℃下退火15分钟并切割成坯件。通过在已在580℃下均质化1小时的样品上测试不同的退火条件来定义退火条件。将坯件在170℃下加热15分钟,给出了本发明的优选实施方案的强度和伸长率,对于50%的冷加工而言,在lt方向上的a%增加33%,而在lt方向上的拉伸屈服强度小幅下降2%。结果在表5中给出。表5:退火后获得的机械特性使坯件在凸缘的一部分上局部快速退火,以在冲压过程中软化置于模头内的凸缘区域。通过传热,即使用加热到约450℃的铝接触板以获得约400℃的局部坯件温度,实现局部快速退火。使用下述条件,以一步或三步完成快速退火:#1:1步:在20秒内使用宽度为40mm的配置,然后进行水淬火。#3:3步:分别在20秒内使用宽度为20、30和40mm的配置,并在每步后进行水淬火。#0:参照样品,接受50%冷加工,没有进行局部快速退火。使用5kg重量的维氏硬度计(vickers)装置测量坯件的硬度特性。这些测量可表征坯件在冲压之前的特性梯度。在短暂的热处理之后,可以获得清晰且明确定义的性能梯度(图5和图6),其特征在于硬的和未改性的中心部分和凸缘的软的再结晶部分。在图5和6中,样品如下所述:组成——均质化——冷加工——快速退火。因此,这些测量表明,本发明的局部快速退火适于通过使坯件的一部分凸缘至少部分地再结晶来控制坯件的性能梯度。使用十字模头测试测量可成形性。使用了两种类型的坯件:大坯件:椭圆形坯件320×290mm×mm小坯件:椭圆形坯件280×250mm×mm(加热区域:宽20mm,而不是40mm)在局部快速退火后,通过580℃均质化和50%冷加工的组成1的最大拉伸深度从12mm增加到最大25mm(图7)。即使获得的最大拉伸深度低于例如aa6016-t4铝合金,但测得的机械强度(tys>200mpa)也非常高,并且产生强度更大的产品,这样最终可以降低规格以实现更轻的产品。多个样品在180℃下进一步接受20分钟的热处理,以模拟油漆烘烤处理。对来自坯件中心部分的样品进行机械测试。结果在表6中给出。表6:油漆烘烤模拟后的机械特性。当前第1页12