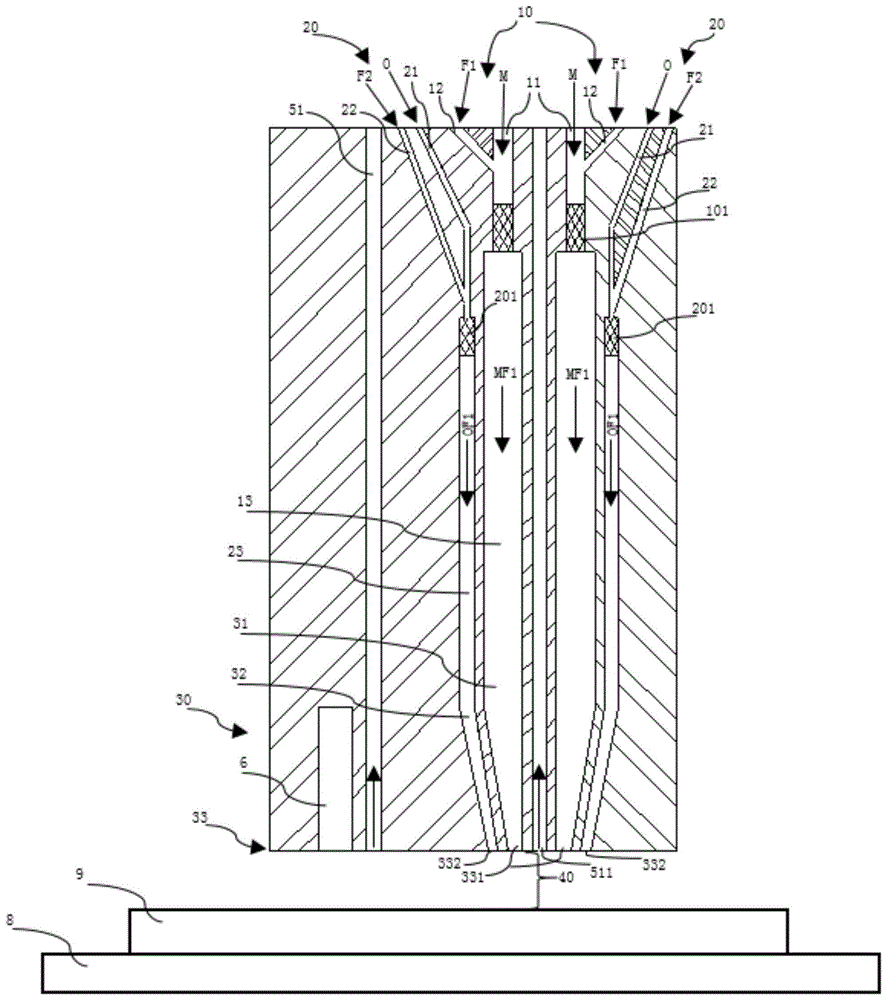
本发明涉及薄膜物质沉积
技术领域:
,尤其涉及一种沉积装置以及沉积方法。
背景技术:
:原子层沉积是一种可以将物质以单原子膜形式一层一层地镀在基底表面的方法。原子层沉积与普通的化学沉积有相似之处,但是,原子层沉积过程中,新一层原子膜的化学反应是直接与之前一层相关联的,这种方式使每次反应只沉积一层原子。电致发光二极管(OLED或QLED)相比于薄膜晶体管有源驱动液晶显示器具有自发光、对比度高、视角广、响应速度快、使用温度范围广以及可弯折性等优异的特性,被广泛认为是下一代显示的核心技术。但是由于电致发光二极管对水汽和氧气非常敏感,所以有效的封装技术对器件的产业化发展尤为关键。薄膜封装可以对刚性或柔性基板(如PEN、PES、PC、PET等)的器件进行封装,从而使器件向更薄的方向发展,并且可以实现柔性电致发光器件的可曲折性以及可卷绕性,为柔性显示技术带来了突破性进展。现有的电致发光器件薄膜封装中通常采用原子层沉积技术配合三甲基铝溶剂成膜氧化铝薄膜,用于阻隔外部水氧对电致发光器件的侵蚀。虽然氧化铝薄膜能够有效地阻隔水氧对器件的侵蚀,但是原子沉积技术沉积氧化铝薄膜速度很慢,消耗时间太长,通常100nm的厚度需要十几个小时。与无机材料相比,有机材料的热稳定性较差,玻璃化温度通常在100℃以下,而且电子发光器件为多层结构,存在多个界面,长时间在高于有机材料玻璃化温度的条件下加热会造成器件性能的退化。此外,原子沉积成膜设备成本高,只能在真空腔室内进行成膜,配套设备多。原子沉积设备维护成本也较高,原子沉积膜层不止在基板表面成膜,而是整个腔体内都会沉积膜层,这会导致长时间使用后膜层极易脱落,进而导致膜层良率下降,且腔体内部由于有零部件存在,不易清洁干净。技术实现要素:为了克服现有技术的不足,本发明的目的在于提供一种成膜效率高的沉积装置以及沉积方法,以降低热板烘烤器件的时间。本发明的另一个目的在于提供一种沉积装置以及沉积方法,允许在大气环境下工作。本发明的另一个目的在于提供一种沉积装置,其维护成本低,能够有效地将成膜区域控制在基板表面。本发明的另一个目的在于提供一种沉积装置以及沉积方法,可以方便地调节各气态反应物的输入量,以使得各气态反应物达到最佳的反应比例。根据本发明的一个方面,提供一种沉积装置,包括第一混合管路,具有用于输入第一气态反应物质的入口一、用于输入第一辅助气体的入口二、用于混合所述第一气态反应物质与所述第一辅助气体的第一腔体,所述入口一和所述入口二与所述第一腔体连通;第二混合管路,具有用于输入第二气态反应物质的入口三、用于输入第二辅助气体的入口四、用于混合所述第二气态反应物质与所述第二辅助气体的第二腔体,所述入口三和所述入口四与所述第二腔体连通;至少一输送头,所述输送头包括与所述第一腔体连通的入口六、与所述第二腔体连通的入口五以及输出面,所述输出面包括与所述入口五连通的出口一以及与所述入口六连通的出口二,从而所述第一腔体内的第一混合物经过所述入口六并从所述出口二输出,所述第二腔体内的第二混合物经过所述入口五并从所述出口一输出,所述第一混合物和所述第二混合物适于发生反应,反应生成的产物适于沉积在设于所述输出面下方的基片表面。进一步地,每一所述输送头的所述出口一与所述出口二相邻。进一步地,所述沉积装置还包括用于驱动所述输送头在水平方向和/或竖直方向移动的第一驱动装置。进一步地,所述沉积装置还包括用于放置基片的载体以及用于驱动所述载体在水平方向和/或竖直方向移动的第二驱动装置,所述载体与所述输送头的所述输出面相对,优选地,所述载体为可加热的载体。进一步地,所述第一混合管路还包括第一混合器,所述第一腔体通过所述第一混合器分别与所述入口一和所述入口二连通;和/或所述第二混合管路还包括第二混合器,所述第二腔体通过所述第二混合器分别与所述入口三和所述入口四连通。进一步地,所述沉积装置还包括抽气管路以及与所述抽气管路连通的至少一排气通道,所述排气通道设于所述输送头的一侧,所述排气通道的排气口靠近所述输送头的所述输出面,优选地,所述排气口与所述输出面共面。进一步地,所述出口一内侧的通道以及所述出口二内侧的通道设置为向所述排气口方向倾斜,优选地,所述出口一内侧的通道以及所述出口二内侧的通道相对于所述输出面的倾斜角度为60°。进一步地,至少一所述排气通道的所述排气口处设置有软X射线装置,所述软X射线装置适于将其附近的气体离子化。进一步地,所述沉积装置包括若干个所述输送头以及若干个排气通道,多个所述输送头共用一所述排气通道,优选地,各所述输送头的所述输出面共面。根据本发明的另一个方面,提供一种沉积方法,包括以下步骤:S1,混合第一气态反应物质和第一辅助气体得到第一混合物,混合第二气态反应物质和第二辅助气体得到第二混合物;S2,从一输出面将所述第一混合物与所述第二混合物相邻地输出至一基片的上方,所述输出面与所述基片之间形成反应区域,所述第一气态反应物质与所述第二气态反应物质在所述反应区域发生反应,生成的产物沉积于所述基片表面形成膜层。进一步地,步骤S2之后还包括以下步骤:使所述基片受热,所述基片的热量传递到所述反应区域,以使所述反应区域的温度达到反应所需的温度。进一步地,使所述第一混合物以及所述第二混合物流速一定,调节所述第一气态反应物质与所述第一辅助气体的混合比例和/或所述第二气态反应物质和所述第二辅助气体的混合比例,以改变各反应物质的输出量和/或所述反应区域内所述第一气态反应物质与所述第二气态反应物质的比例。进一步地,所述步骤S2之后还包括以下步骤:使所述输出面与所述基片发生相对移动,从而所述反应区域生成的产物沿所述基片表面沉积。进一步地,所述步骤S2之后还包括以下步骤:S3,将所述反应区域的气体产物或未反应的气体或所述基片处的杂质抽出。进一步地,所述步骤S2之前还包括以下步骤:对所述反应区域进行抽气,利用软X射线装置将被抽出的气体离子化,从而产生大量正负离子以用于中和所述基片表面的静电。根据一个实施方式,所述第一气态反应物质包括气态金属化合物,所述第一辅助气体为氢气,所述第二气态反应物质为臭氧,所述第二辅助气体为惰性气体,所述步骤S2中,所述金属化合物与所述氢气在所述反应区域内受热反应形成金属单质,所述臭氧氧化所述金属单质,从而得到金属氧化物沉积于所述基片表面。进一步地,所述第一气态反应物质还包括烃系溶剂。根据另一个实施方式,所述第一气态反应物质为气态金属化合物,所述第一辅助气体为烃系溶剂,所述第二气态反应物质为水汽,所述第二辅助气体为臭氧,所述步骤S2中,所述金属化合物与所述水汽以及所述臭氧反应生成金属氧化物,得到的所述金属氧化物沉积于所述基片表面。相比现有技术,本发明的有益效果在于:采用本发明的沉积装置进行薄膜沉积,可以多个输送头同时成膜,其成膜效率高,有利于降低基片被烘烤的时间;本发明的沉积装置以及沉积方法无需使用真空腔体,可以在大气环境或者无水无氧的环境下工作;本发明的沉积装置维护成本低,其成膜区域被控制在基片表面;本发明的沉积装置以及沉积方法可通过单向移动输送头或基片的方式沉积膜层。本发明的以上以及其他技术特征以及有益效果将在接下来的具体实施方式中进一步说明。附图说明图1为本发明的沉积装置的一个实施例示意图;图2为本发明的沉积装置的另一个实施例的示意图;图3为实施例1的Al2O3薄膜的切面电镜图;图4为实施例1的Al2O3薄膜表面的形貌图;图5为实施例2的Al2O3薄膜的切面电镜图;图6为实施例2的Al2O3薄膜表面的形貌图;图中:10、第一混合管路;11、入口一;12、入口二;13、第一腔体;101、第一混合器;20、第二混合管路;21、入口三;22、入口四;23、第二腔体;201、第二混合器;30、输送头;31、入口五;32、入口六;33、输出面;331、出口一;332、出口二;40、反应区域;50、抽气管路;51、排气通道;511、排气口;6、软X射线装置;8、载体;9、基片。具体实施方式下面,结合具体实施方式,对本发明做进一步描述,需要说明的是,在不相冲突的前提下,以下描述的各实施例之间或各技术特征之间可以任意组合形成新的实施例。在本发明的描述中,需要说明的是,对于方位词,如有术语“中心”,“横向”、“纵向”、“长度”、“宽度”、“厚度”、“上”、“下”、“前”、“后”、“左”、“右”、“竖直”、“水平”、“顶”、“底”、“内”、“外”、“顺时针”、“逆时针”等指示方位和位置关系为基于附图所示的方位或位置关系,仅是为了便于叙述本发明和简化描述,而不是指示或暗示所指的装置或元件必须具有特定的方位、以特定方位构造和操作,不能理解为限制本发明的具体保护范围。需要说明的是,本申请的说明书和权利要求书中的术语“第一”、“第二”等是用于区别类似的对象,而不必用于描述特定的顺序或先后次序。应该理解这样使用的数据在适当情况下可以互换,以便这里描述的本申请的实施例。此外,术语“包括”和“具有”以及他们的任何变形,意图在于覆盖不排他的包含,例如,包含了一系列步骤或单元的过程、方法、系统、产品或设备不必限于清楚地列出的那些步骤或单元,而是可包括没有清楚地列出的或对于这些过程、方法、产品或设备固有的其它步骤或单元。如图1、2所示,本发明提供一种沉积装置,适于在一基片9表面沉积薄膜。该沉积装置包括第一混合管路10、第二混合管路20以及至少一输送头30。第一混合管路10具有:用于输入第一气态反应物质M的入口一11,用于输入第一辅助气体的F1的入口二12,以及用于混合第一气态反应物质M和第一辅助气体F1的第一腔体13;入口一11和入口二12与第一腔体13连通。第一气态反应物质M和第一辅助气体F1在第一腔体13内混合为第一混合物MF1。第二混合管路20具有:用于输入第二气态反应物质O的入口三21,用于输入第二辅助气体F2的入口四22,以及用于混合第二气态反应物质O和第二辅助气体F2的第二腔体23;入口三21和入口四22与第二腔体23连通。第二气态反应物质O和第二辅助气体F2在第二腔体23内混合为第二混合物OF2。输送头30包括:与第一腔体13连通的入口五31,与第二腔体23连通的入口六32,以及输出面33;输出面33包括与入口五31连通的出口一331以及与入口六32连通的出口二332,从而第一腔体13内的第一混合物MF1通过入口五31进入输送头30并从输出面33的出口一331输出,第二腔体23内的第二混合物OF2通过入口六32进入输送头30并从输出面33的出口二332输出。待沉积薄膜的基片9适于设置在输出面33下方,从而在基片9与输出面33之间形成反应区域40,从输出面33输出的第一混合物MF1和第二混合物OF2在反应区域40相遇,第一混合物MF1与第二混合物OF2可发生化学反应,反应生成的产物沉积在基片9的表面。本发明提供的沉积装置可用于在基片9表面沉积金属氧化物,如氧化铝、氧化钛、氧化锆、氧化锌、氧化铈、氧化钼、氧化锰、氧化锡、氧化铟、氧化钨等,还可用于在基片9表面沉积硫化物、氮化物或非金属氧化物,如二氧化硅、硫化锌、硫化锶、硫化钙、氮化硅、氮化铝。本领域的技术人员可以根据需要沉积的物质,选择合适的第一气态反应物质M和第二气态反应物质O。第一辅助气体F1以及第二辅助气体F2可以不参与反应,主要起到调节反应区域40内第一气态反应物质M和第二气态反应物质O含量的作用;或者,第一辅助气体F1或第二辅助气体F2也可以参与反应,一方面用于调节第一气态反应物质M或第二气态反应物质O含量,另一方面参与到第一气态反应物质M和第二气态反应物质O的反应过程中。本发明的沉积装置可在正常大气压下工作,可以不像现有的原子沉积一样抽真空。本发明的沉积装置能够在不改变输送到反应区域40的气体流速的情况下,改变反应区域40内第一气态反应物质M与第二气态反应物质O的比例或含量。以下举例说明:假设第一混合物MF1输送到反应区域40的最佳气体流速为A,若想要减少一定时间内输送到反应区域40的第一气态反应物质M的量,则可以减小第一混合物MF1中第一气态反应物质M的流速(也即减小入口一11的流速),同时增加第一辅助气体F1的流速(也即增加入口二12的流速),保证第一混合物MF1的总流速仍然为A,此时,一定时间内输送到反应区域40内的第一气态反应物质M的量被减少。同理,也可以在不改变输送到反应区域40内的气体流速的情况下,同时减少输送到反应区域40的第一气态反应物质M和第二气态反应物质O的量。本发明的沉积装置的优点在于:在反应区域40内始终保持最佳流速的前提下,可以随时改变反应区域40内第一气态反应物质M以及第二气态反应物质O的含量,从而调节第一气态反应物质M与第二气态反应物质O达到最佳反应比例。若第一混合物MF1和第二混合物OF2的反应需要在一定的温度下进行,可以通过对基片9进行加热,使基片9的热量扩散到反应区域40,以使得反应区域40的温度达到反应温度。本发明的沉积装置将成膜区域控制在基片9的表面处(也即反应区域40内),避免了反应产物沉积在设备或装置的其他位置。在一些实施例中,基片9到输出面33之间的距离不超过50mm,也即反应区域40的高度不超过50mm。基片9与输出面33之间的距离不宜过大,否则从基片9扩散到反应区域40的热量损失较多,使反应区域40达到所需的反应温度,基片9可能需要承受更高的温度,这对基片9的稳定性会产生较大的影响。优选地,基片9到输出面33之间的距离为20mm,在该距离下,反应区域40的温度基本接近基片9表面的温度,热量损失较少。进一步地,每一输送头30的出口一331与出口二332相邻,从而第一混合物MF1与第二混合物OF2被输出后即可在反应区域40相遇,进而发生反应。采用本发明的沉积装置进行薄膜沉积时,允许不通过往复移动基片9或输送头30的方式进行薄膜的沉积,若基片9的表面积大于输出面33,则可通过单向移动基片9或输送头30,以进行成膜。在一些实施例中,沉积装置包括用于驱动输送头30在水平方向和/或竖直方向移动的第一驱动装置(图中未示出)。第一驱动装置用于驱动输送头30的移动,其可以仅用于驱动输送头30在水平方向移动,也即在基片9的上方水平移动,在移动过程中,基片9与输送头30之间的垂直距离保持不改变。第一驱动装置还可以仅用于驱动输送头30在竖直方向移动,也即调整基片9与输送头30之间的距离。第一驱动装置还可以既用于驱动输送头30在基片9的上方水平移动,也用于驱动输送头30在竖直方向的移动。在另一些实施例中,沉积装置包括用于放置基片9的载体8以及用于驱动载体8在水平方向和/或竖直方向移动的第二驱动装置(图中未示出)。第二驱动装置可以仅用于驱动载体8在水平方向移动,也可以仅用于驱动载体8在竖直方向移动,还可以既用于驱动载体8在水平方向移动,也用于驱动载体8在竖直方向移动。在一些实施例中,载体8为可加热的载体,从而利用加热载体8来对基片9进行加热,以使基片9表面以及反应区域40达到反应温度。在一些实施例中,第一混合管路10还包括第一混合器101,第一腔体13通过第一混合器101分别与入口一11和入口二12连通。换句话说,从入口一11进入的第一气态反应物质M和从入口二12进入的第一辅助气体F1首先在第一混合器101内进行混合,然后再输送至第一腔体13内。第一混合器101可以是但不限于现有的各种气体混合器,通过设置第一混合器101,可以进一步提高第一混合物MF1的均匀程度。在一些实施例中,第二混合管路20还包括第二混合器201,第二腔体23通过第二混合器201与入口三21和入口四22连通。换句话说,从入口三21进入的第二气态反应物质O以及从入口四22进入的第二辅助气体F2首先在第二混合器201内进行混合,然后再输送至第二腔体23内。第二混合器201可以是但不限于现有的各种气体混合器。在一些实施例中,入口三21以及入口四22处分别设有等离子体发射装置,以使得第二气态反应物质O和第二辅助气体F2等离子体化。利用等离子体可以获得更多的活性基团,也可以活化基片9表面,从而有利于膜层的沉积,提高膜层致密性。进一步地,沉积装置还包括抽气管路50以及与抽气管路50连通的至少一排气通道51,排气通道51设于输送头30的一侧,排气通道51的排气口511靠近输送头30的输出面33,从而反应区域40内的废气或者未反应完的气体适于通过排气通道51进入抽气管路50。在一些实施例中,排气口511与输送头30的输出面33共面。在一些实施例中,出口一331内侧的通道以及出口二332内侧的通道设置为向排气口511方向倾斜,以使得从出口一331以及出口二332输出的气体相对于输出面33向排气口511的方向倾斜,从而反应产生的废气或者混合气中未参与反应的气体可顺利通过排气口511进入排气通道51。优选地,出口一331内侧的通道以及出口二332内侧的通道相对于输出面33的倾斜角度为60°。值得一提的是,在一些实施例中,抽气管路50连接抽气设备,以将各排气通道51中的气体抽出。在一些实施中,至少一排气通道51的排气口511处设置有软X射线装置6,软X射线装置6适于将进入排气通道51的气体离子化,从而产生可以消除静电的正负离子。设置软X射线装置6主要作用是消除基片9表面以及颗粒物杂质的静电,以保证在成膜之前将基片9表面的颗粒物通过排气通道51排出。由于静电的作用,环境内一些颗粒物可能会吸附在基片9的表面,导致成膜时产生孔洞缺陷。利用软X射线可将气体离子化从而产生大量正负离子,根据异性电荷互相吸引的原理,正负离子能够快速中和基片9表面残留的静电,达到消除颗粒物与基片9之间的静电吸引力的作用,从而使颗粒物容易被抽出。此外,采用软X射线装置6除静电不会对成膜环境产生二次污染。在一些实施例中,如图2所示,沉积装置包括多个输送头30,各输送头30的输出面33与基片9之间均形成反应区域40,通过设置多个输送头30,有利于进一步提高沉积效率。各输送头30的入口五31分别与第一腔体13连通,各输送头30的入口六32分别与第二腔体23连通。图1中虚线示意出了各入口五31与第一腔体13连通、各入口六32与第二腔体23连通,本发明对实现连通的具体结构并不进行限定,可以是但不限于多个气管、气体通道等。优选地,各输送头30的输出面33共面。在图2所示的实施例中,沉积装置还包括与抽气管路50连通的多个排气通道51。图1中虚线示意出了各排气通道51与抽气管路50连通,本发明对实现连通的具体结构并不进行限定,可以是但不限于多个气管、气体通道等。进一步地,多个输送头30共用一排气通道51,也即在一排气通道51的周围设置多个输送头30,与各输送头30对应的反应区域40内的废气均可通过该共用的排气通道51排出。图2中仅示意了两个输送头30共用一排气通道51的实施例,但并不限制在其他实施例中可以是四个或更多个输送头30共用一个排气通道51,例如,可以将多个输送头30沿圆周围绕设置在一排气通道51的周围。本发明还提供一种沉积方法,包括以下步骤:S1,混合第一气态反应物质M和第一辅助气体F1得到第一混合物MF1,混合第二气态反应物质O和第二辅助气体F2得到第二混合物OF2;S2,从一输出面33将第一混合物MF1与第二混合物OF2相邻地输出至一基片9的上方,输出面33与基片9之间形成反应区域40,第一气态反应物质M与第二气态反应物质O在反应区域40内发生反应,生成的产物沉积于基片9表面,从而形成膜层。本发明的沉积方法可用于在基片9表面沉积金属氧化物,如氧化铝、氧化钛、氧化锆、氧化锌、氧化铈、氧化钼、氧化锰、氧化锡、氧化铟、氧化钨等,还可用于在基片9表面沉积硫化物、氮化物或非金属氧化物,如二氧化硅、硫化锌、硫化锶、硫化钙、氮化硅、氮化铝。在一些实施例中,步骤S2之后还包括以下步骤:使基片9受热,基片9的热量传递到反应区域40,以使反应区域40的温度达到第一混合物MF1与第二混合物OF2的反应温度。在一些实施例中,使第一混合物MF1以及第二混合物OF2的流速一定,调节第一气态反应物质M与第一辅助气体F1的混合比例和/或第二气态反应物质O与第二辅助气体F2的混合比例,以改变各反应物质的输出量和/或反应区域40内第一气态反应物质M与第二气态反应物质O的比例。在一些实施例中,步骤S2之后还包括以下步骤:使输出面33与基片9发生相对移动,从而反应区域40生成的产物沿基片9表面沉积。在一些实施例中,步骤S2之前以及之后还包括以下步骤:S3,将反应区域40的废气或未反应的气体或基片9表面的杂质抽出。在一些实施例中,步骤S2之前还包括以下步骤:对反应区域40进行抽气,利用软X射线装置6将被抽出的气体离子化,从而产生大量正负离子,利用异性电荷相互吸引的原理,快速中和基片9表面的静电。该步骤主要是消除因静电导致颗粒物吸附在基片9的表面,经过该步骤后,基片9表面的静电被消除,颗粒物随着气流被抽出,有利于减少在基片9表面沉积的膜层的缺陷。在一些实施例中,第一气态反应物质M包括气态金属化合物,第一辅助气体F1为氢气,第二气态反应物质O为臭氧,第二辅助气体F2为惰性气体,步骤S2中,金属化合物与氢气在反应区域40内受热反应形成金属单质,臭氧氧化该金属单质,从而得到金属氧化物沉积于基片9表面。值得一提的是,本发明所说的惰性气体是指对第一气态反应物质M以及第二气态反应物质O均为惰性的气体,其不参与到反应中,例如氩气。优选地,第一气态反应物质M还包括烃系溶剂,烃系溶剂的作用在于稀释气态金属化合物,使气态金属化合物失去自燃性。烃系溶剂可以是但不限于己烷、庚烷等脂肪烃以及甲苯、二甲苯等芳香族烃。在一个实施例中,第一气态反应物质M为烃系溶剂稀释到浓度25%以下的三甲基铝,三甲基铝与氢气在高温的反应区域40混合后发生热分解反应生成铝单质,然后铝单质被臭氧氧化形成氧化铝,生成的氧化铝沉积在基片9表面。在另一些实施例中,第一气态反应物质M为气态金属化合物,第一辅助气体F1为烃系溶剂,第二气态反应物质O为水汽,第二辅助气体F2为臭氧,步骤S2中,金属化合物与水汽以及臭氧反应生成金属氧化物,得到的金属氧化物沉积于基片9表面。该实施例中,第一辅助气体F1将气态金属化合物稀释到一定浓度,以保证气态金属化合物失去自然性。在一些实施例中,气态金属化合物为三甲基铝,水汽以及臭氧经过等离子体发射装置被等离子体化,等离子体化的水汽以及臭氧与三甲基铝反应生成氢氧化铝,经过反应区域40的高温灼烧将氢氧化铝转换为氧化铝,生成的氧化铝沉积在基片9表面。水汽、臭氧等离子体可以提高氢氧化铝灼烧后分解生成的氧化铝中氧的活性基团的浓度,有利于氧化铝薄膜的沉积。【实施例1】采用如图1所示的沉积装置,在基片9表面沉积成膜,沉积方法为:A、将基片9(Si基板)设置在载体8上,使得基片9与输出面33之间的距离为20mm,利用载体8对基片9进行加热,使基片9表面温度以及反应区域40的温度达到85~110℃;B、利用烃系溶剂将三甲基铝(TMA)稀释,得到第一气态反应物质M,第一气态反应物质M中三甲基铝的浓度为25%,将第一气态气体反应物质M从入口一11输入;将氢气从入口二12输入,三甲基铝与氢气在第一混合器101中充分混合后,进入第一腔体13;C、将臭氧从入口三21输入,将氩气从入口四22输入,臭氧与氩气在第二混合器201中充分混合后,进入第二腔体23;D、第一腔体13内的第一混合物经过入口五31进入输送头30,并通过出口一331从输出面33输出,第二腔体23内的第二混合物经过入口六32进入输送头30,并通过出口二332输出;氢气与三甲基铝在反应区域40内先进行灼烧分解反应生成金属铝单质,生成的金属铝单质与出口二332输出的臭氧进行氧化反应生成氧化铝以及其他废气;E、反应产生的废气以及剩余未反应的气体经过排气口511进入排气通道51,最后经过抽气管路50被抽到外部,同时,设置在排气通道51处的软X射线装置6可去除前进路线上的静电,以确保成膜前基板残留的颗粒物能够被抽气管路3抽到外部。可以在入口一11、入口二12、入口三21以及入口四22均未送气时,先开启与抽气管路50连接的抽气装置以及软X射线装置6,以进一步确保成膜前基片9表面的颗粒物被抽干净。经过步骤D和步骤E形成的流动重复过程,在基片9表面生长厚度为70nm的Al2O3薄膜。采用瑞典的PGX+便携式接触角测试仪测试该样片的接触角,通过计算来得到样片的表面能,沉积薄膜的接触角与表面能参数值见表1。表1ConditionWatercontactanglesSurfaceenergy/(mN·m-1)PGT30s75.2°40.3接触角是在气、液、固三相交点处所作的气/液界面的切线穿过液体与固/液界线之间的夹角,是润湿程度的量度,通过杨氏公式可以由其得到固体的表面能。由于接触角与表面结构有关,因此接触角的测量可以反映在不同生长条件下薄膜表面的平整度。由表1可知,沉积的氧化铝薄膜的接触角小于90°,说明可以在该条件下沉积用于OLED封装的Al2O3薄膜。采用扫描电子显微镜(SEM)对制得的Al2O3薄膜的切面放大200000倍进行观察,如图3所示,可以看出制备的Al2O3薄膜表面平整且成膜质量较高,均匀性接近,几乎没有明显的翘曲、褶皱以及开裂现象。利用原子力显微镜(AFM)获得Al2O3薄膜表面的形貌图,如图4所示。AFM所扫描的范围是1.2μm×1.2μm,测试结果显示,制备样片表面的平均粗糙度(Ra)为0.297nm,表明Al2O3薄膜具有良好的表面均匀性。【实施例2】采用如图1所示的沉积装置,在基片9表面沉积成膜,沉积方法为:A、将基片9(Si基板)设置在载体8上,使得基片9与输出面33之间的距离为20mm,利用载体8对基片9进行加热,使基片9表面温度以及反应区域40的温度达到85~110℃;B、将三甲基铝从入口一11输入;将烃系溶剂从入口二12输入,三甲基铝与烃系溶剂在第一混合器101中充分混合后,进入第一腔体13,第一腔体13内的第一混合物中,三甲基铝的浓度为25%;C、将水汽从入口三21输入,水汽经过设置在入口三21处的等离子发射装置(图2中未示出)被等离子体化;将臭氧从入口四22输入,臭氧经过设置在入口四22处的等离子发射装置(图2中未示出)被等离子体化;等离子体化的水汽与臭氧在第二混合器201中充分混合后,进入第二腔体23;D、第一腔体13内的第一混合物经过入口五31进入输送头30,并通过出口一331从输出面33输出,第二腔体23内的第二混合物经过入口六32进入输送头30,并通过出口二332输出;三甲基铝与水汽和臭氧混合气在反应区域40内进行灼烧分解反应生成氧化铝以及其他废气;E、反应产生的废气以及剩余未反应的气体经过排气口511进入排气通道51,最后经过抽气管路50被抽到外部,同时,设置在排气通道51处的软X射线装置6可去除前进路线上的静电,以确保成膜前基板残留的颗粒物能够被抽气管路3抽到外部。可以在入口一11、入口二12、入口三21以及入口四22均未送气时,先开启与抽气管路50连接的抽气装置以及软X射线装置6,以进一步确保成膜前基片9表面的颗粒物被抽干净。经过步骤D和步骤E形成的流动重复过程,在基片9表面生长厚度为70nm的Al2O3薄膜。采用瑞典的PGX+便携式接触角测试仪测试该样片的接触角,通过计算来得到样片的表面能,沉积薄膜的接触角与表面能参数值见表2。表2由表2可知,沉积的氧化铝薄膜的接触角小于90°,说明可以在该条件下沉积用于OLED封装的Al2O3薄膜。采用扫描电子显微镜(SEM)对制得的Al2O3薄膜的切面放大200000倍进行观察,如图5所示,可以看出制备的Al2O3薄膜表面平整且成膜质量较高,均匀性接近,几乎没有明显的翘曲、褶皱以及开裂现象。利用原子力显微镜(AFM)获得Al2O3薄膜表面的形貌图,如图6所示。AFM所扫描的范围是1.2μm×1.2μm,测试结果显示,制备样片表面的平均粗糙度(Ra)为0.297nm,表明Al2O3薄膜具有良好的表面均匀性。上述实施方式仅为本发明的优选实施方式,不能以此来限定本发明保护的范围,本领域的技术人员在本发明的基础上所做的任何非实质性的变化及替换均属于本发明所要求保护的范围。当前第1页1 2 3