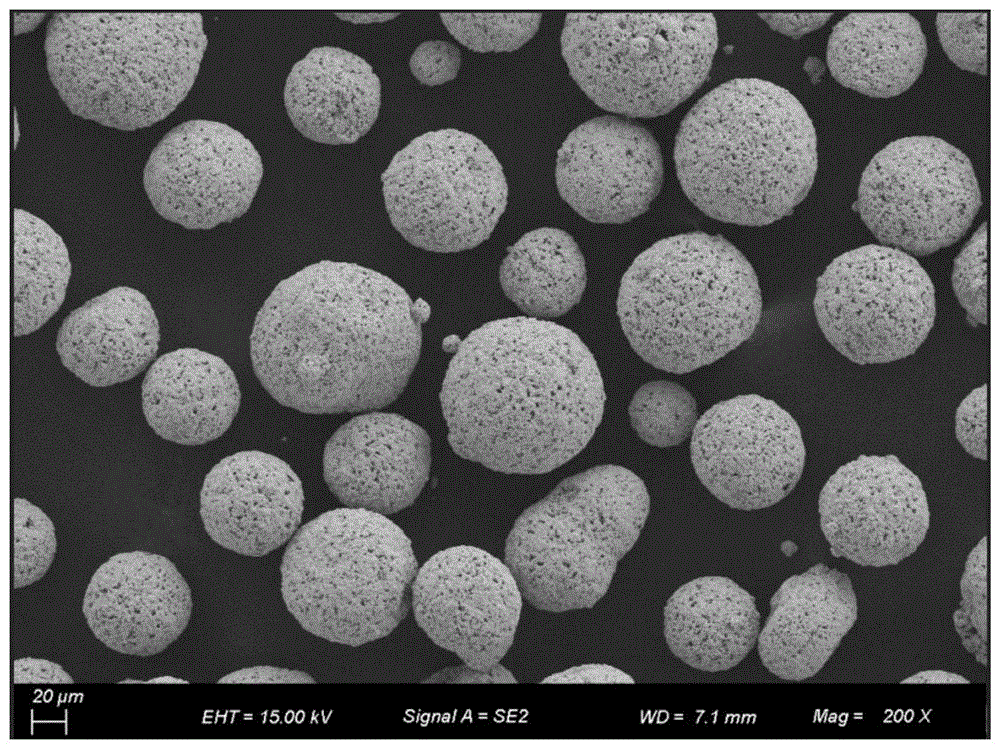
本发明涉及合金
技术领域:
,特别涉及一种自润滑3D打印合金粉末及其制备方法。
背景技术:
:随着现代工业等领域的飞速发展,对在高温条件下工作的减摩材料提出了更高的要求,从而使得材料在高温条件下的磨擦、磨损和润滑的性能要求逐渐得到重视。碳化钨合金以其耐高温、高硬度、高耐磨性和高强度耐著称,作为工具材料已有悠久历史,但传统的碳化钨合金大量用作高速切削车刀、窑炉结构材料、喷气发动机部件、金属陶瓷材料、电阻发热元件等传统领域。对于应用到这些传统领域的碳化钨合金的综合性能提出了越来越高的要求,主要研究方向也是侧重在提高合金的力学性能。随着近几年3D打印技术的发展和进步,碳化钨合金的应用领域也逐渐扩张到3D打印领域,但由于是新兴领域,目前对于3D打印碳化钨合金的研究甚少,而碳化钨合金粉末在3D打印领域应用过程中主要面对的问题是合金粉末的摩擦系数较大,导致其作为打印材料时流动性严重不足,容易发生摩擦阻塞,进而无法实现合金粉末的连续打印。为了解决上述问题,专利CN108941596A公开了一种3D打印特种合金粉末及其制备方法,利用碳化钨粉、钴粉、铬粉、铝粉和钛粉混合后球磨,再进行感应等离子球化处理,得到3D打印特种合金粉末,这种合金粉末可以有效的改善粉末的物理和化学特性,主要表现在改善合金粉末的流动性、减小粉末的孔隙率、提高粉末密度、降低粉末的脆性、改善颗粒表面光洁度、提高粉末纯度、精准控制含氧量,但上述3D打印合金粉末的摩擦性能和流动性仍然存在不足。技术实现要素:有鉴于此,本发明的目的在于提供一种自润滑3D打印合金粉末及其制备方法,本发明提供的3D打印合金粉末粒度分布均匀,摩擦系数低,具有优异的流动性。为了实现上述发明目的,本发明提供了以下技术方案:本发明提供了一种自润滑3D打印合金粉末,包括以下质量百分含量的组分:钴6~20%,六方氮化硼3%~8%,碳化钨70~90%和晶粒抑制剂0.18~1%,各组分的质量百分含量之和为100%。优选地,所述晶粒抑制剂包括碳化钒、碳化铬和碳化钽中的一种或多种。本发明还提供了上述自润滑3D打印合金粉末的制备方法,包括如下步骤:将钴粉、碳化钨粉、六方氮化硼粉和晶粒抑制剂与溶剂混合,得到混合物料;将所述混合物料进行球磨后干燥,得到混合粉末;将所述混合粉末进行感应等离子粉体球化处理,得到自润滑3D打印合金粉末。优选地,所述钴粉、碳化钨粉、六方氮化硼和晶粒抑制剂的粒径独立为8~15μm。优选地,所述溶剂包括醇类溶剂或水。优选地,所述球磨采用硬质合金球与混合物料在球磨机中进行。优选地,所述球磨的时间为24~72h。优选地,所述干燥的温度为100~150℃,所述干燥的时间为3~6h。优选地,所述混合粉末的粒径为4~8μm。优选地,所述感应等离子粉体球化处理的离子气气源为Ar和H2,所述Ar和H2的体积为比22~26:1。本发明提供了一种自润滑3D打印合金粉末,包括以下质量百分含量的组分:钴6~20%,六方氮化硼3%~8%,碳化钨70~90%和晶粒抑制剂0.18~1%,各组分的质量百分含量之和为100%;本发明提供的合金粉末组成中,钴作为粘结相,碳化钨作为硬质相,球磨后的晶粒抑制剂能使得抑制晶粒长相均匀分布在粉末中,提高了抑制相在粘结相中的溶解度,降低碳化钨在粘结相中的浓度,促使碳化钨溶解-析出量减小,抑制碳化钨晶粒的生长,提高晶粒的均匀性,而晶粒尺寸的均匀性能够避免在球磨过程中无序的碰撞摩擦;六方氮化硼作为自润滑剂也能够减小合金粉末相互之间的摩擦力,提高打印过程中合金粉末的流动性能和铺粉效率,打印出来的产品自带润滑性,产品的连续性及结构稳定性和使用寿命均得到显著提升。实验结果表明,本发明制备得到的自润滑3D打印合金粉末的摩擦系数为0.082~0.11,霍尔流速达到9.8s/50g。本发明还提供了一种自润滑3D打印合金粉末的制备方法,通过引入自润滑相和晶粒抑制剂,同时采用湿磨的方式进行球磨,能保证合金组分在球磨过程不被氧化和原料粉末的均匀分布,在感应等离子粉体球化处理时利用等离子体的高温作为热源对原料粉体进行熔化和汽化,可以实现对不规则原料粉体的球形化过程,提高合金粉末粒度的均匀性。附图说明图1为实施例1制备得到的自润滑3D打印合金粉末的SEM图。具体实施方式本发明提供了一种自润滑3D打印合金粉末,包括以下质量百分含量的组分:钴6~20%,六方氮化硼3%~8%,碳化钨70~90%和晶粒抑制剂0.18~1%,各组分的质量百分含量之和为100%。本发明提供的自润滑3D打印合金粉末,按质量百分含量计,包括钴6~20%,优选为5~10%或15~20%,更优选为10~15%;在本发明的合金粉末中,碳化钨是非常坚硬、非常耐磨、难熔的物质,其熔点可达到(2870±50)℃,而钴的熔点是1430℃左右,合金粉末在使用时随着温度升高至1430℃左右时,钴已达到熔点,是熔融状态,渗透到碳化钨的缝隙中,使碳化钨和钴进行紧密结合,温度冷却后形成硬质合金产品。本发明提供的自润滑3D打印合金粉末,按质量百分含量计,包括碳化钨70~90%,优选为75~85%,更优选为80%;在本发明中,所述碳化钨作为3D打印材料的基体硬质相,能够提高合金粉末的综合性能。本发明提供的自润滑3D打印合金粉末,按质量百分含量计,包括六方氮化硼3%~8%,优选为5~6%;在本发明中,所述六方氮化硼作为自润滑剂在3D打印粉末中能显著提高粉末的流动性能且能够减小粉末之间的摩擦力,提高铺粉的效率,打印原料自带润滑性,能够有效减小摩擦,进而提高产品成品率和使用寿命。本发明提供的自润滑3D打印合金粉末,按质量百分含量计,包括晶粒抑制剂0.18~1%,优选为0.3~0.8%,更优选为0.5%;在本发明中,所述晶粒抑制剂优选包括碳化钒、碳化铬和碳化钽中的一种或多种,更优选为碳化钽。在本发明中,所述晶粒抑制剂球磨后抑制晶粒长相均匀分布在粉末中,能提高抑制相在粘结相中的溶解度,降低碳化钨在粘结相中的浓度,促使碳化钨溶解-析出量减小,抑制碳化钨晶粒长大,实现合金粉末中晶粒的均匀分散性。本发明还提供了上述自润滑3D打印合金粉末的制备方法,包括如下步骤:将钴粉、碳化钨粉、六方氮化硼粉和晶粒抑制剂与溶剂混合,得到混合物料;将混合物料进行球磨后干燥,得到混合粉末;将混合粉末进行感应等离子粉体球化处理,得到自润滑3D打印合金粉末。本发明将钴粉、碳化钨粉、六方氮化硼粉和晶粒抑制剂与溶剂混合得到混合物料。本发明对所述钴粉、碳化钨粉、六方氮化硼粉和溶剂的来源没有特殊的限定,采用本领域技术人员熟知市售产品即可。在本发明中,所述混合物料中溶剂的用量优选为0.1~0.3L/kg,更优选为0.2L/kg。在本发明中,所述溶剂优选为醇类溶剂或水,所述醇类溶剂优选包括甲醇、乙醇、丁醇或其他可溶解的多元醇,在本发明实施例中,具体优选为乙醇。在本发明中,所述钴粉、碳化物粉、六方氮化硼和晶粒抑制剂的粒径独立地优选为8~15μm;在本发明中,粒径均匀的原料能够在球磨过程中降低粉末之间的摩擦,进而降低因自摩擦生热与空气接触产生的氧化反应的剧烈程度。本发明对于混合的方式没有特殊要求,采用本领域常规的混合方式即可。在本发明中,所述混合顺序优选将钴粉、碳化钨粉、六方氮化硼粉和晶粒抑制剂进行第一混合后,再与溶剂进行第二混合。得到混合物料后,本发明将混合物料进行球磨后干燥,得到混合粉末。在本发明中,所述球磨优选采用硬质合金球与混合物料在球磨机中进行。在本发明中,所述硬质合金球与混合物料的体积比优选为3~6:1,更优选为4~5:1;在本发明中,所述球磨机的转速优选为25~36r/min,更优选为30r/min;在本发明中,所述球磨的时间优选为24~72h,更优选为30~60h。本发明在上述工艺参数下进行球磨处理能够保证球磨后浆料中粉末的平均粒度为4~8μm。在本发明中,所述干燥的温度优选为100~150℃,更优选为120~140℃;所述干燥的时间优选为3~6h,更优选为4~5h。在本发明中,所述干燥优选在真空条件下进行。在本发明中,所述混合粉末的粒径优选为4~8μm,更优选为6μm。得到混合粉末后,本发明将混合粉末进行感应等离子粉体球化处理,得到自润滑3D打印合金粉末。在本发明中,所述感应等离子球化处理的离子气气源优选为Ar和H2,所述Ar和H2的体积比优选为22~26:1,更优选23~25:1;所述感应等离子球化处理的淬冷气体优选为循环的Ar。在本发明中,所述感应等离子球化处理的功率优选为45~60Kw,更优选为47~48Kw。在本发明中,所述感应等离子球化处理的送粉率优选为5~10kg/h,更优选为6~9kg/h,最优选为7~8kg/h。在本发明中,所述感应等离子球化处理用仪器优选采用加拿大Tekan公司开发的射频等离子粉体处理系统。感应等离子粉体球化处理完成后,本发明优选从感应等离子球化处理后的反应器底部收集混合产物进行筛分处理。在本发明中,所述筛分的孔径大小优选为45~105μm,更优选为50~90μm;在本发明中,所述筛分用设备优选为振动筛,所述筛分方式采用本领域常规方案即可。下面结合实施例对本发明提供的一种自润滑3D打印合金粉末及其制备方法进行详细的说明,但是不能把它们理解为对本发明保护范围的限定。实施例1取粒度为8~15μm的钴粉、碳化钒粉、六方氮化硼粉、碳化钨粉按质量百分比:钴粉6%,碳化钒粉0.28%,六方氮化硼粉3.9%,碳化钨粉89.82%的比例进行第一混合,按照0.2L/kg的比例加入乙醇溶剂进行第二混合得到混合物料;将混合物料投入球磨机,转速为30r/min,所用硬质合金球与混合物料的体积比为3:1,球磨时间为28小时,球磨后的浆料在110℃真空条件下进行干燥3小时,然后随炉冷却,得到平均粒度为4~8μm的混合粉末。采用加拿大Tekan公司开发的射频等离子粉体处理系统对所述混合粉末进行感应等离子球化处理,其中Ar和H2为等离子气源(VAr:VH2=22:1),循环的Ar为淬冷气体,处理功率为45Kw,送粉率为5kg/h的条件,从系统反应器底部收集产物,在振动筛中进行分步循环筛分,得到粒度为45~105μm适合3D打印的自润滑合金粉末。对实施例1制备的自润滑3D打印合金粉末采用MMU-5G型摩擦磨损试验机进就摩擦系数检测,测得试块与45#钢的摩擦系数为0.11。实施例2取粒度为8~15μm的钴粉、碳化铬粉、六方氮化硼粉、碳化钨粉按质量百分比:钴粉10%,碳化铬粉0.5%,六方氮化硼粉5%,碳化钨粉84.5%的比例进行第一混合,按照0.2L/kg的比例加入乙醇溶剂进行第二混合得到混合物料;将混合物料投入球磨机,转速为30r/min,所用硬质合金球与混合物料的体积比为3:1,球磨时间为28小时,球磨后的浆料在110℃真空条件下进行干燥3小时,然后随炉冷却,得到平均粒度为4~8μm混合粉末。采用加拿大Tekan公司开发的射频等离子粉体处理系统对所述混合粉末进行感应等离子球化处理,其中Ar和H2为等离子气源(VAr:VH2=25:1),在循环的Ar为淬冷气体,功率为60kw,送粉率为10Kg/h,从系统反应器底部收集产物,在振动筛中进行分步循环筛分,得到粒度为45~105μm适合3D打印的自润滑合金粉末。对实施例2制备的自润滑3D打印合金粉末采用MMU-5G型摩擦磨损试验机进就摩擦系数进行检测,测得试块与45#钢的摩擦系数为0.09。实施例3取粒度为8~15μm的钴粉、碳化钽粉、六方氮化硼粉、碳化钨粉按质量百分比:钴粉20%,碳化钽粉1%,六方氮化硼粉8%,碳化钨粉71%的比例进行进行第一混合,按照0.2L/kg的比例加入乙醇溶剂进行第二混合得到混合物料;将混合物料投入球磨机,转速为30r/min,所用硬质合金球与混合物料的体积比为3:1,球磨时间为28小时,球磨后的浆料在110℃真空条件下进行干燥3小时,然后随炉冷却,得到平均粒度为4~8μm混合粉末。采用Ar和H2为等离子气源,在循环的Ar为淬冷气体,功率为60kw,送粉率为10Kg/h的条件下,采用加拿大Tekan公司开发的射频等离子粉体处理系统对所述混合粉末进行感应等离子球化处理,从反应器底部收集产物,在振动筛中进行分步循环筛分,得到粒度为45~105μm适合3D打印的自润滑合金粉末。对实施例3制备的自润滑3D打印合金粉末采用MMU-5G型摩擦磨损试验机进就摩擦系数进行检测,测得试块与45#钢的摩擦系数为0.082。实施例4本实施例与实施例1的主要区别在于溶剂为丁醇。对比例1本对比例与实施例1的区别仅在于没有添加六方氮化硼粉(用碳化钨粉补充其用量)。实验结果表征:1、利用激光粒度分析仪对实施例1得到的自润滑3D打印合金粉末进行表征,结果如表1所示:表1实施例1合金粉末的激光粒度分布(μm)D10D50D9045.8486.50105.602、依据国家标准GB1482-84的规定设计、生产的霍尔流速计对本发明实施例1和对比例1的合金粉末进行流动性测试,采用Hall时间进行表征,结果如表2所示:表2本发明实施例1和对比例1合金粉末的Hall时间对比性能实施例1对比例1Hall时间9.8sec/50g12.3sec/50g由表1数据分析可知:本发明实施例1制备的自润滑3D打印合金粉末的晶粒分布均匀;由表2数据分析可知,本发明实施例1制备的合金粉末50g流过漏斗小孔的时间为9.8sec,对比例1合金粉末50g流过漏斗小孔的时间为12.3sec,流完50g合金粉末所用时间越短,说明其流动性越好,因此,本发明实施例1制备的自润滑3D打印合金粉末具有优异的流动性。以上所述仅是本发明的优选实施方式,应当指出,对于本
技术领域:
的普通技术人员来说,在不脱离本发明原理的前提下,还可以做出若干改进和润饰,这些改进和润饰也应视为本发明的保护范围。当前第1页1 2 3