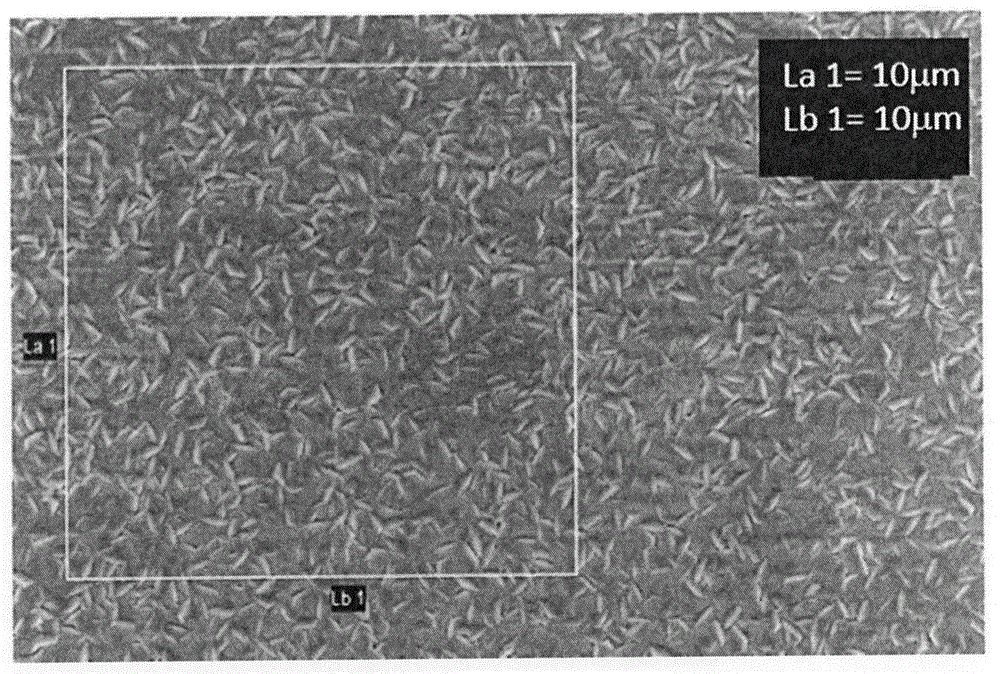
本发明涉及溅射沉积含添加剂的氮化铝薄膜的方法。具体而言,本发明涉及一种用于沉积含添加剂的氮化铝薄膜,例如含钪或钇的氮化铝薄膜的脉冲dc反应溅射方法。本发明还涉及含添加剂的氮化铝薄膜本身以及包括这些薄膜的压电器件。
背景技术:
:压电氮化铝(aln)薄膜可以应用于rf谐振器器件,如体声波(baw)滤波器。与未掺杂的氮化铝薄膜相比,含添加剂的氮化铝可以提高器件的机电耦合效率(keff)。例如,钪可以以降低铝含量为代价加入到合金中,以形成具有相对较高keff的al100-xscxn形式的含添加剂的氮化铝。应当理解,当组合物以al100-xscxn的形式表示时,值100-x和x表示为百分比,x作为百分比在化学计量术语中可以等于0.01x。特别地,c轴取向的al100-xscxn薄膜优选用于谐振器器件,因为这种取向增强了材料的压电特性。为了制造更高质量的rf谐振器器件,需要增加机电耦合系数。例如,增加含添加剂的氮化铝中存在的添加剂元素的量可以增加机电耦合系数(keff)。然而,随着含添加剂的氮化铝中存在的添加剂元素的量增加,晶体缺陷形成的可能性更大。晶体缺陷降低了含添加剂的氮化铝薄膜的质量和结晶度。这些晶体缺陷是非压电活性的,因此对含添加剂的氮化铝薄膜的机电耦合系数有不利影响。也就是说,缺陷几乎没有压电响应,因此可以降低每单位体积薄膜的压电耦合。图1示出了在使用已知沉积方法生产的alscn薄膜上观察到的晶体缺陷的sem图像。图2示出了晶体缺陷20的放大倍数更高的sem图像。此外,这些缺陷可能难以蚀刻,可能对后续层的生长产生不利影响,并因此可能影响后续处理步骤。因此,需要开发一种方法来增加含添加剂的氮化铝中存在的添加剂元素的量,同时保持可接受的缺陷密度和结晶度(或织构)。通常,为了制造高质量的器件,每100μm2小于50个缺陷的缺陷规格是理想的。通常,为了制造高质量的器件,小于2.0°fwhm的织构规格是理想的。ep3153603公开了一种通过脉冲dc反应溅射沉积含添加剂的氮化铝薄膜的方法。然而,需要开发新的方法来抑制含添加剂的氮化铝薄膜中的缺陷水平,特别是当添加剂浓度大于约8at%时。因此,希望进一步增加添加剂元素的浓度(特别是高于约8at%),同时抑制缺陷并将薄膜织构改善到高质量rf谐振器器件的商业制造可接受的水平。最终商业化的另一个条件是,这种方法可以以经济可行的方式实施。技术实现要素:本发明在其至少一些实施例中寻求解决至少一些上述问题、期望和需求。在本发明的至少一些实施例中,本发明提供了一种用于沉积含添加剂的氮化铝薄膜的方法,所述氮化铝薄膜具有低缺陷密度和高机电耦合系数(keff),并且适用于谐振器器件。根据本发明的第一方面,提供一种溅射沉积含添加剂的氮化铝薄膜的方法,所述薄膜含有选自钪或钇的添加剂元素,所述方法包括以下步骤:通过脉冲dc反应溅射将含添加剂的氮化铝薄膜的第一层沉积到设置在腔室内的衬底上;以及通过脉冲dc反应溅射在第一层上沉积含添加剂的氮化铝薄膜的第二层,第二层具有与第一层相同的成分;其中:沉积第一层的步骤包括以一定流速(sccm)将气体或气体混合物引入腔室,且87-100%的流速(sccm)是氮气流;沉积第二层的步骤包括以一定流速(sccm)将气体混合物引入腔室,所述气体混合物包括氮气和惰性气体,以及在沉积第一层的步骤中使用的流速(sccm)中的氮气百分比大于在沉积第二层的步骤中使用的流速(sccm)中的氮气百分比。第一层可以是晶种层。第一层可以为第二层的定向晶体生长提供成核位置,例如具有c轴取向。已经发现,在高度富氮的气氛(例如87-100%)中沉积第一层允许将高浓度的添加剂元素结合到氮化铝材料中,同时保持可接受水平的晶体缺陷、结晶度和织构。添加剂元素可以是钪。添加剂元素可以以0.5at%至40at%的量存在,任选地在8at%至40at%的范围内,任选地在10at%至35at%的范围内,任选地在15at%至30at%的范围内,或任选地在20at%至25at%的范围内。添加剂元素可以以大于8at%、大于10at%、大于15at%、大于20at%、大于25at%的量存在。添加剂元素可以以小于等于40at%的量存在。添加剂元素可以以上述上限和下限的任意组合存在。本发明的方法对于沉积具有高浓度添加剂元素(例如高于8at%)的含添加剂的氮化铝薄膜特别有效,同时保持可接受水平的缺陷密度、结晶度和织构。在沉积第一层的步骤中使用的流速(sccm)的88%或更多、89%或更多、90%或更多、91%或更多、92%或更多、93%或更多、94%或更多、95%或更多、96%或更多、97%或更多、98%或更多、99%或更多或100%可以是氮气流。在沉积第一层的步骤中使用的90-100%、94-100%或任选98-100%的流速(sccm)可以是氮气流。在沉积第一层的步骤中使用的流速(sccm)可以包括氮气流和惰性气体流,例如氩气流,或者由氮气流和惰性气体流组成。在沉积第一层的步骤中使用的流速(sccm)基本上仅由氮气流组成。优选地,在沉积第一层的步骤中,大约100%的流速(sccm)是氮气流。也就是说,在沉积第一层的步骤中的流速(sccm)优选仅是氮气流。在沉积第一层的步骤中使用的氮气的流速(sccm)可以是50-500sccm,任选60-250sccm,任选100-200sccm,或约150sccm。在沉积第一层的步骤中使用的氮气的流速(sccm)可以大于50sccm、60sccm、100sccm或150sccm。在沉积第一层的步骤中使用的氮气的流速(sccm)可以小于500sccm、250sccm、200sccm或150sccm。通过在第一层沉积期间使用富氮或仅含氮的气氛,所得含添加剂的氮化铝薄膜的缺陷密度、结晶度和织构可以相对于已知方法显著改善。这些效应在仅含氮的气氛中特别明显。不希望被任何理论或推测束缚的条件下,据信仅在富氮或仅含氮的气氛中沉积第一层具有两个有益效果。首先,第一层中加入的氩原子的数量减少。这减少了原子缺陷的潜在来源,原子缺陷可能导致晶体缺陷在含添加剂的氮化铝薄膜中传播。其次,拒信靶的溅射效率降低,因为靶材料仅被氮溅射,而非同时被氩溅射。因此,由靶溅射的铝(或添加剂元素,如钪或钇)原子较少。拒信这增加了沉积腔室中活性氮形态的比例,使得活性氮形态可以更有利地沉积到衬底上。这样,衬底上就能形成更富氮的第一层(例如初始晶种层),其上具有更少的原子点缺陷。因此,晶体缺陷生长的成核点较少,从而抑制缺陷的形成。此外,有更多的成核位置可供c轴氮端alscn以定向织构模式生长。c轴al1-xscxn生长可以增强含添加剂的氮化铝薄膜的压电性能。总的来说,这减少了含添加剂的氮化铝薄膜中缺陷的数量和密度,并且可以提高薄膜的机电耦合效率,从而允许薄膜中存在更高浓度的添加剂元素,同时保持可接受水平的缺陷密度和织构。在沉积第一层的步骤中使用的气体或气体混合物可以包括氮气和惰性气体。惰性气体可以是稀有气体。稀有气体被理解为元素周期表18族气体。惰性气体可以是氙气、氪气或优选氩气。由于在沉积第一层的步骤中使用的惰性气体的百分比增加到已知现有技术中使用的水平,没有观察到本发明的有益效果。在沉积第二层的步骤中使用的气体混合物的流速可以包括大约83%的氮气和大约17%的惰性气体,例如氩气。在沉积第二层的步骤中使用的气体混合物中氮气的流速(sccm)可以在50-250sccm的范围内;任选75-150sccm;或者任选约83sccm。在沉积第二层的步骤中使用的惰性气体如氩气的流速(sccm)可以在8-50sccm的范围内;任选10-25sccm;或者大约17sccm。在脉冲dc反应溅射过程中,惰性气体不会与物质发生化学反应。惰性气体可以是溅射气体。在沉积第二层的步骤中使用的气体混合物的惰性气体可以是稀有气体,例如氙气、氪气,或者优选氩气。稀有气体被理解为元素周期表18族气体。在沉积第一层的步骤中使用的气体或气体混合物中的氮气比例通常高于在沉积第二层的步骤中使用的气体混合物中的氮气比例。不希望被任何理论或推测束缚的条件下,在沉积第二层期间,使用包含较低比例氮气的气体混合物来沉积第二层可以提高溅射效率,并因此增加沉积速率。在沉积第一层的步骤中,腔室可以具有2-6mtorr的压力,任选约4mtorr。在沉积第二层的步骤中,腔室可以具有1.5-7.5mtorr的压力,任选约3mtorr。第一层的厚度可以小于70nm,任选小于60nm,任选小于50nm,任选小于30nm,任选小于25nm,任选小于20nm,或任选约17nm。第二层的厚度可以比第一层大至少6倍,任选大至少20倍,任选大至少25倍,任选大至少50倍,或任选大约60倍。含添加剂的氮化铝薄膜的厚度可以是0.3μm或以上;0.6μm或以上;或者大约1μm。含添加剂的氮化铝薄膜可以具有小于等于2μm的厚度。沉积第一层的步骤可以用施加到衬底的电偏压功率来执行。在沉积第一层的步骤期间施加到衬底的电偏压功率可以是rf偏压功率。在沉积第一层的步骤期间施加到衬底的电偏压功率可以大于200w,或者大于250w。在沉积第一层的步骤期间施加到衬底的电偏压功率可以小于350w,或者小于300w。向衬底施加相对高的偏压功率(例如,大于200w)可以使沉积的含添加剂的氮化铝薄膜具有压缩应力。本发明人发现,具有压缩应力的第一层(例如晶种层)通常使含添加剂的氮化铝薄膜具有更低的缺陷密度和更好的织构和结晶度。沉积第二层的步骤可以在没有电偏压功率施加到衬底或者施加到衬底的电偏压功率低于沉积第一层的步骤期间施加的电偏压功率的情况下进行。在沉积第二层的步骤期间施加到衬底的电偏压功率可以是rf偏压功率。可以选择在沉积第二层的步骤期间施加的电偏压功率,使得整个薄膜应力(即第一和第二层的应力)大约为零。在沉积第二层的步骤期间施加到衬底的电偏压功率可以小于100w。脉冲dc反应溅射可以使用磁控管进行。脉冲dc反应溅射通常包括在溅射沉积期间向溅射靶施加dc功率的脉冲。脉冲dc反应溅射可以使用单个靶来执行。靶可以是由铝和添加剂元素形成的复合靶。使用多个靶也是可能的,但在经济上可能不太有吸引力。所述方法可以进一步包括在沉积第一层的步骤之前蚀刻衬底表面的步骤,使得第一层沉积在衬底的蚀刻表面上。衬底可以是硅衬底。衬底可以包括金属层,例如钼层,含添加剂的氮化铝薄膜的第一层沉积在所述金属层上。所述方法可以进一步包括将金属层沉积到衬底前体上的步骤。当诸如钼层的金属层沉积到衬底前体上时,第一层沉积到金属层上。沉积金属层的步骤可以在蚀刻衬底的步骤之前进行。根据本发明的第二方面,提供一种通过第一方面的方法生产的含添加剂的氮化铝薄膜。根据本发明的第三方面,提供一种含添加剂的氮化铝薄膜,添加剂元素选自钪或钇,其含量范围为8at%至40at%,任选10at%至35at%,任选15at%至30at%,或任选20at%至25at%;所述氮化铝薄膜具有每100μm2小于50个缺陷的缺陷密度。添加剂元素可以以大于8at%、大于10at%、大于15at%、大于20at%、大于25at%的量存在。添加剂元素可以以小于等于40at%的量存在。添加剂元素可以以上述上限和下限的任意组合存在。根据本发明的第四方面,提供一种压电器件,包括根据本发明第二或第三方面的含添加剂的氮化铝薄膜。压电器件可以是体声波(baw)器件。压电器件可以包括第一和第二电极,含添加剂的氮化铝薄膜设置在第一和第二电极之间。虽然上面描述了本发明,但是其覆盖上面或者下面的描述、附图和权利要求中阐述的特征的任何组合。例如,关于本发明的一个方面公开的任何特征可以与本发明的任何其他方面的任何特征相结合。附图说明现在将参考附图仅以示例的方式描述本发明的实施例,其中:图1是示出al80sc20n缺陷的sem图像;图2是示出al80sc20n缺陷的sem图像;图3是al80sc20n缺陷的tem截面图;图4是包括点缺陷的alscn薄膜的第一层的图示;图5是没有点缺陷的alscn薄膜的第一层的图示;图6是包括具有拉伸应力的17nm厚的第一层的al80sc20n薄膜的sem图像;图7是包括具有压缩应力的17nm厚的第一层的al80sc20n薄膜的sem图像;以及图8是举例说明本发明方法的流程图。具体实施方式发明人发现了一种溅射沉积含添加剂的氮化铝薄膜的有利过程。所述方法有助于改善结晶度和织构,并减少含添加剂的氮化铝薄膜中的微晶缺陷。含添加剂的氮化铝薄膜含有添加剂元素,例如钪(sc)或钇(y)。下面给出的结果与氮化铝钪(al1-xscxn)有关。然而,所述方法通常适用于氮化铝钇(al1-xyxn)。所述薄膜通过反应溅射沉积,例如脉冲dc反应溅射。申请人的欧洲专利申请ep2871259和ep3153603中描述了关于可用于或易于适用于本发明的装置的一般细节,其全部内容通过引用并入本文。所述装置包括设置在腔室中的衬底。所述装置还包括靶。靶是由铝和添加剂元素形成的复合靶。靶的成分可以决定溅射沉积薄膜中包含的添加剂元素的量。使用多个靶是可能的,但在经济上可能不太有吸引力。脉冲dc溅射包括在沉积过程中向靶施加dc功率的脉冲。在第一步骤中,含添加剂的氮化铝薄膜的第一层从靶溅射沉积到设置在腔室中的衬底上。第一层通过脉冲dc反应溅射沉积。第一层可以是晶种层。在沉积第一层期间,将包括氮气和任选的惰性气体如氩气的气体或气体混合物引入腔室。第一步骤中氮气的流速(sccm)为第一步骤中总气体流速(sccm)的87-100%。任选地,第一步骤中氮气的流速(sccm)为第一步骤中总气体流速(sccm)的90-100%、95-100%、98-100%或约100%。优选地,气体或气体混合物仅由氮气组成。第一层通常具有小于约70nm、小于60nm、小于50nm、优选小于20nm的厚度。在一些实施例中,第一层具有大约17nm的厚度。在第二步骤中,含添加剂的氮化铝薄膜的第二层随后沉积在第一层上,例如沉积在初始晶种层上。第二层的沉积可以是体沉积。第二层通过脉冲dc反应溅射沉积。在沉积第二层的过程中,将包括氮气和惰性气体如氩气的第二气体混合物引入腔室。其他惰性气体,例如氙气和氪气,也可以考虑,但因其成本较高而不太优选。氮气在第二气体混合物中的比例通常小于氮气在第一气体或气体混合物中的比例。在一个实施例中,在沉积第二层期间,氮气的流速为83sccm,且氩气的流速为17sccm。也就是说,第二步骤中氮气的流速约为总流速(sccm)的83%。在硅衬底上实验的典型沉积参数如表1所示。alscn第一步骤(晶种层)alscn第二步骤(体沉积)薄膜厚度<20nm~980nmn2流量(sccm)15083-85ar流量(sccm)017压板rf偏压功率(瓦特)>2500-100腔室压力(mtorr)43表1:通过两步过程沉积alscn的典型过程参数。通过上述方法,使用单个靶将1μm的al80sc20n薄膜溅射沉积到硅衬底上。表2示出了在沉积第一层(即初始晶种层)期间改变氮气的比例如何影响沉积的1μm的al80sc20n薄膜中的缺陷密度(每100μm2)。使用放大6000倍的扫描电子显微镜(sem)图像来确定缺陷密度。表3示出了在沉积第一层(即初始晶种层)期间改变氮气的比例如何影响沉积的al80sc20n薄膜的织构。x射线衍射(xrd)半峰全宽(fwhm)测量用于确定样本在衬底中心、半径中部和边缘的织构(或结晶度)。较低的fwhm值对应于结晶程度更高的膜。在沉积过程之前,在350℃下对硅衬底进行2分钟的脱气步骤。表2和表3的最后一行中列出的示例包括在溅射沉积过程之前在350℃下对衬底进行7.5nm低偏压蚀刻步骤的附加步骤。可从spts科技有限公司(sptstechnologieslimited)购得的se-ltx模块适用于执行预处理脱气和蚀刻步骤。1μm的al80sc20n薄膜(如表2和表3所示)包括17nm厚的压缩第一层(例如初始晶种层)和983nm的第二层(例如体层)。第一层是使用压板上的300瓦rf偏压产生的。第二层是使用允许在整个薄膜上实现零应力的rf偏压功率产生的。也就是说,第一层和第二层上的应力为零。通常,在第二步骤期间施加到压板的偏压小于在第一步骤期间施加到压板的偏压。在沉积第二层期间,氮气的流速为83sccm,氩气的流速为17sccm。表2:不同氮气百分比流量下硅衬底上1μm的al80sc20n薄膜的缺陷密度。表3:不同氮气百分比流量下硅衬底上1μm的al80sc20n薄膜的xrdfwhm测量。表2显示,随着氮气比例(即百分比流量)的增加,衬底边缘、半径中部和中心的缺陷密度降低。表3显示,随着第一(晶种)步骤中氮气比例的增加,织构(0002)fwhm值在衬底的边缘、半径中部和中心趋于降低。当第一(晶种)层沉积过程中使用的气体仅由氮气组成时,这些影响最为明显。不希望被任何理论或推测束缚的条件下,据信晶体缺陷是由点缺陷引起的,例如原子未对准、错位或空位。alscn薄膜中的大部分晶体缺陷被认为源于生长alscn薄膜的衬底材料的表面。产生的缺陷在整个薄膜中传播,并且在薄膜表面可以观察到。图3示出了al80sc20n薄膜中晶体缺陷30的tem截面。缺陷30在薄膜中传播。这些缺陷在含添加剂的氮化铝薄膜中特别突出,其中添加剂元素(例如钪或钇)的原子浓度大于约8at%。对于alscn薄膜,据信alscn颗粒可以是氮或铝(钪)端的。不希望被任何理论或推测束缚的条件下,据信如果氮层被沉积为初始原子层,当另一种类型的原子也被加入到初始氮原子层中时,将形成晶体缺陷。图4示出了铝/钪原子40,其被加入到初始氮原子层中以形成点缺陷。这种缺陷可以在整个alscn薄膜中传播。同样不希望被任何理论或推测束缚的条件下,据信在沉积第一层期间增加氮气含量的比例有利于沉积基本上没有点缺陷的晶种层。例如,初始原子层50可以基本上仅由氮组成(如图5所示)。在第一层(即初始晶种层)的沉积过程中,优选使用富氮或仅含氮的气氛。这减少了含添加剂的氮化铝薄膜中缺陷的数量和密度,并且可以提高膜的机电耦合效率,从而允许薄膜中存在更高浓度的添加剂元素,同时保持可接受水平的缺陷密度和织构。使用已知的方法,例如在第一步骤的沉积中氮气的比例小于约83-87%的情况下,在具有高浓度添加剂元素(例如大于8at%)的含添加剂的氮化铝薄膜中保持可接受水平的缺陷密度和织构是不容易实现的。表2和表3中所示的al80sc20n薄膜是通过沉积压缩初始晶种层,随后进行体沉积来制备的,使得al80sc20n薄膜中的总应力为零。沉积薄膜中的应力可以通过改变衬底偏压功率来控制。表4显示了如果第一层具有拉伸或压缩应力,1μm的al80sc20n薄膜的xrdfwhm测量如何变化。表4的1μm的al80sc20n薄膜是通过在第一层沉积期间仅将氮气引入腔室而形成的。第一层的厚度为17nm,且第二(体)层的厚度为983nm。图6和7显示了分别沉积有拉伸和压缩第一层的薄膜的al80sc20n表面的sem图像。与沉积有拉伸第一层的al80sc20n薄膜相比,沉积有压缩第一层的al80sc20n薄膜显示出更低的缺陷密度和更优的织构。第一层应力中心织构fwhm(度)边缘织构fwhm(度)拉伸1.661.77压缩1.581.63表4:第一层应力变化时硅衬底上1μm的al80sc20n薄膜的fwhm织构。研究了衬底材料和表面条件的影响。使用单一复合靶将1μm的al80sc20n薄膜沉积到钼(mo)涂覆的衬底上。其它金属材料可以代替钼用作涂层材料。根据图8所示的方法制备钼涂覆的衬底。衬底前体首先脱气(步骤802)。在钼沉积模块中将钼涂层沉积到脱气的衬底前体上(步骤806)。使用低偏压蚀刻处理蚀刻钼涂层(步骤808)。随后将衬底转移到溅射沉积模块,以进行两步alscn沉积过程(步骤810和812)。两步alscn沉积过程包括i)在富氮或仅含氮的气氛中,将第一层沉积到衬底的钼涂覆表面上(步骤810),随后ii)将第二层沉积(即,体沉积)到第一层上(步骤812)。步骤810和812中使用的过程条件可以与上面结合本发明的其他实施例描述的相同或不同。表5和表6示出了当使用图8的方法将1μm的al80sc20n薄膜沉积到钼(mo)涂覆的衬底上时,在第一层的沉积过程中,缺陷密度和织构如何通过改变氮气的比例而变化。表5:不同氮气百分比流量下钼衬底上1μm的al80sc20n薄膜的缺陷密度。表6:不同氮气百分比流量下硅衬底上1μm的al80sc20n薄膜的fwhm织构。表5和表6显示,在沉积第一层期间,通过在气体气氛中仅使用氮气,可以降低钼涂覆衬底上的1μm的al80sc20n薄膜的缺陷密度,并且可以改善织构。此外,在沉积alscn之前通过温和蚀刻来调节衬底表面也有助于抑制结晶缺陷的形成,并且可以改善所得alscn薄膜的织构和结晶度。研究了第一层厚度对缺陷密度、结晶度和织构的影响。在沉积第一层期间,仅使用氮气在钼涂覆的衬底上制备1μm的al80sc20n薄膜。根据图8的方法制备钼衬底。改变第一层的厚度,并使用xrdfwhm测量来测量所得薄膜的织构。结果如表7所示。第一层越薄,al80sc20n薄膜越织构化(即织构越好)。这种效应在衬底边缘更明显。第一层的合适厚度通常小于70nm、小于60nm、小于50nm、小于30nm、小于25nm或小于20nm。表7:第一层厚度对al80sc20n织构的影响。特别地,已经发现在富氮或仅含氮气氛中沉积较薄的第一层显著降低了缺陷密度,并改善了结晶度和织构。即使在高添加剂元素浓度下,也能观察到这些有益效果。因此,本发明的方法特别适用于沉积具有高添加剂元素浓度的含添加剂的氮化铝薄膜,同时保持可接受水平的缺陷密度、结晶度和织构。上述方法可用于沉积含添加剂的氮化铝薄膜,例如al1-xscxn,其具有不同浓度的添加剂元素。1μm的al1-xscxn薄膜以0at%、9at%、15at%和20at%沉积在裸硅衬底上。含添加剂的氮化铝薄膜由单一的复合靶沉积而成。沉积薄膜中添加剂材料的量由靶的成分决定。第一层用施加到衬底上的200-350w的rf偏压功率沉积。在第一层沉积期间,只有氮气被引入腔室。也就是说,沉积第一层的步骤中的流速由氮气流组成。第一层的厚度约为20nm。测量沉积膜薄边缘和中心的织构,且结果如表8所示。表8:不同晶种成分的硅衬底上1μm的al1-xscxn薄膜的fwhm织构。本发明人发现沉积约20nm的第一层(例如,初始晶种层),其中100%的流速(sccm)是氮气流(n2),在多种添加剂元素浓度下改善了沉积薄膜的织构。所有添加剂元素浓度下都有所改善。这对于较高添加剂元素浓度尤其有利,而使用已知的现有方法会导致不可接受的缺陷水平和较差的织构。本方法对于高于8at%、9at%、10at%、15at%、20at%和25at%的添加剂元素浓度,可以实现可接受的织构和缺陷密度水平。当前第1页12