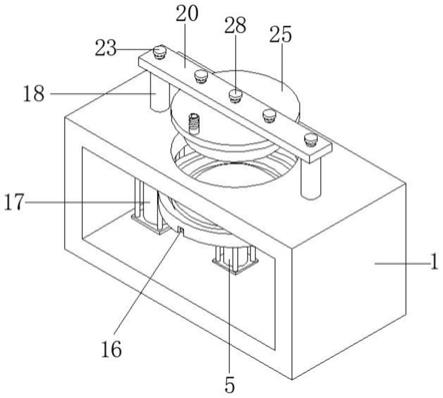
[0001]
本发明涉及化工泵密封环制作领域,具体涉及一种用于制造化工泵密封环的压铸模具。
背景技术:[0002]
密封环是一种带有缺口的环状密封件,把它放置在套筒的环槽内,套筒与轴一起转动,密封环靠缺口被压拢后所具有的弹性而抵紧在静止件的内孔壁上,即可起到密封的作用。各个接触表面均需经硬化处理并磨光。密封环用含铬的耐磨铸铁制造,根据制造方法和材料的不同,密封环有整体式密封环(用同一种材料制造)、组合式密封环、表面堆焊硬质合金和喷涂陶瓷等多种结构。现有的化工泵密封环一般通过压铸进行加工,压铸的实质是在高压作用下,使液态或半固态金属以及极高的速度填充进入压铸模具型腔,并在压力作用下成型和冷却凝固而获得铸件的一种成形工艺;压铸出的制件尺寸精度高。表面粗糙度低,材料利用率高,组织致密,具有较高的强度和硬度。
[0003]
目前,申请号为cn201920691196.1的中国专利公开了一种用于制造化工泵密封环的专用压铸模具,属于模具技术领域。它解决了现有的化工泵密封环的专用压铸模具容易变形报废,使用寿命短的问题。本用于制造化工泵密封环的专用压铸模具,包括模腔块,模腔块的中部位置具有呈环形的压铸通道,压铸通道内还滑动设置有与压铸通道大小、形状适配的上冲头、下冲头,上冲头、下冲头在压铸通道内轴向间隔配合并与压铸通道形成化工泵密封环的压铸腔,上冲头、下冲头两者和模腔块之间分别设置有防止上冲头、下冲头在模腔块的压铸通道内周向旋转移位的轴向导向装置。但是,使用该装置进行化工泵密封环压铸成型,不便于成型后的密封环和模具的分离,同时不便于装置的安装和使用。基于此,本发明设计了一种用于制造化工泵密封环的压铸模具。
技术实现要素:[0004]
解决的技术问题针对现有技术所存在的上述缺点,本发明提供了一种用于制造化工泵密封环的压铸模具。
[0005]
技术方案为实现以上目的,本发明通过以下技术方案予以实现:一种用于制造化工泵密封环的压铸模具,包括框板,所述框板顶端中心开设有贯通圆槽,所述框板顶端中心两侧对称开设有贯穿孔,所述框板在贯通圆槽底端边缘开设有辅助环槽,所述框板内腔顶端中心设置有中心气缸,所述中心气缸内部活动连接有中心活塞杆,所述中心活塞杆顶端中心固定有连接块,所述连接块中心开设有贯穿螺孔,所述连接块上方设置有下模盘,所述下模盘顶端边缘开设有辅助插环,所述下模盘底端中心开设有连接槽,所述下模盘顶端中心固定有支撑底盘,所述支撑底盘顶端开设有环槽,所述下模盘侧面对称开设有隐藏槽,所述隐藏槽侧面中心开设有连接螺孔,所述连接螺孔贯穿连接槽设置,
所述连接螺孔和贯穿螺孔内部螺纹连接有固定螺栓,所述框板内腔顶端中心两侧对称设置有侧气缸,所述侧气缸内部活动连接有侧活塞杆,所述侧活塞杆活动穿过贯穿孔,所述侧活塞杆顶端中心开设有安装螺孔,所述侧活塞杆上方设置有横板,所述横板底端对称开设有两组安装孔,所述安装孔顶端中心开设有配合螺孔,所述配合螺孔和安装螺孔内部螺纹连接有安装螺栓,所述横板底端中心等间距开设有定位螺孔,所述横板下方设置有上模盘,所述上模盘底端固定有插环,所述上模盘顶端中心等间距设置有螺孔,所述螺孔和定位螺孔内部螺纹连接有定位螺栓,所述上模盘顶端连通有液管,所述液管侧壁上设置有螺纹。
[0006]
更进一步地,所述辅助环槽的深度小于框板内腔顶端厚度的一半,所述中心气缸的高度大于框板内腔顶端至辅助环槽顶端的垂直距离的一半。
[0007]
更进一步地,所述下模盘的直径的辅助环槽的外直径,所述辅助插环的内直径等于辅助环槽的内直径,所述辅助插环的高度等于辅助环槽的深度,所述连接槽和连接块配合设置,所述支撑底盘的直径等于贯通圆槽的直径。
[0008]
更进一步地,所述连接螺孔的直径小于隐藏槽的高度,所述固定螺栓为双头螺栓且两端通过螺母进行固定,所述固定螺栓的长度小于下模盘的直径,所述固定螺栓的长度大于两组隐藏槽之间的最小垂直距离。
[0009]
更进一步地,所述侧气缸的高度等于框板内腔的高度,所述安装孔的直径等于侧活塞杆的直径,所述配合螺孔贯穿横板设置,所述安装螺栓的长度略大于配合螺孔和安装螺孔的深度之和。
[0010]
更进一步地,所述上模盘的直径等于贯通圆槽的直径,所述插环的外直径等于环槽的外直径,所述插环的内直径等于环槽的内直径,所述螺孔和定位螺孔配合等间距设置,所述螺孔的深度小于上模盘的高度。
[0011]
更进一步地,所述液管连通设置在上模盘顶端位于插环外壁和上模盘边缘之间的区域中心位置,所述螺纹自液管侧壁顶端设置。
[0012]
更进一步地,所述下模盘顶端、支撑底盘、上模盘底端、插环侧壁上均设置有脱模剂。
[0013]
有益效果采用本发明提供的技术方案,与已知的公有技术相比,具有如下有益效果:本发明通过设置连接块、连接槽、贯穿螺孔、隐藏槽、连接螺孔、固定螺栓、安装螺孔、安装孔、配合螺孔和安装螺栓,利用连接块和连接槽的插接配合,可以将下模盘安装在中心活塞杆顶端,利用固定螺栓和连接螺孔以及贯穿螺孔的螺纹配合,可以将下模盘固定在中心活塞杆顶端,便于下模盘的安装和拆卸,同时利用安装孔和侧活塞杆的插接配合,可以将横板安装在侧活塞杆顶端,利用安装螺栓和安装螺孔以及配合螺孔的螺纹配合,便于横板的安装和拆卸。
[0014]
本发明通过设置定位螺孔、螺孔和定位螺栓,可以利用定位螺栓和定位螺孔以及螺孔的螺纹配合,将上模盘安装在横板底端,便于上模盘的安装和拆卸,装置整体拆分为若干部件,便于使用。
[0015]
本发明通过设置辅助环槽、辅助插环、环槽和插环,可以利用中心气缸推动中心活塞杆上移,在辅助插环和辅助环槽的配合下,将下模盘顶升在贯通圆槽底端,此时辅助插环插入辅助环槽内,支撑底盘位于贯通圆槽内,在环槽和插环的配合下,利用侧气缸带动侧活
塞杆下移,将上模盘带动在贯通圆槽顶端,此时插环插入环槽内,插环外壁、支撑底盘和贯穿圆槽共同形成压铸空间,可以利用中心气缸和侧气缸自由实现压铸空间的形成和取消,便于压铸后的物件的取出。
[0016]
本发明通过设置。
附图说明
[0017]
为了更清楚地说明本发明实施例或现有技术中的技术方案,下面将对实施例或现有技术描述中所需要使用的附图作简单地介绍。显而易见地,下面描述中的附图仅仅是本发明的一些实施例,对于本领域普通技术人员来讲,在不付出创造性劳动的前提下,还可以根据这些附图获得其他的附图。
[0018]
图1为本发明的主体结构示意图;图2为本发明的框板结构示意图;图3为本发明的辅助环槽结构示意图;图4为本发明的下模盘结构示意图;图5为本发明的剖面结构示意图;图6为本发明的上模盘结构示意图;图7为本发明的横板结构示意图;图8为本发明的立体剖面结构示意图;图中:1.框板 2.贯通圆槽 3.贯穿孔 4.辅助环槽 5.中心气缸 6.中心活塞杆 7.连接块 8.贯穿螺孔 9.下模盘 10.辅助插环 11.连接槽 12.支撑底盘 13.环槽 14.隐藏槽 15.连接螺孔16.固定螺栓 17.侧气缸 18.侧活塞杆 19.安装螺孔 20.横板21.安装孔 22.配合螺孔 23.安装螺栓 24.定位螺孔 25.上模盘 26.插环 27.螺孔 28.定位螺栓 29.液管 30.螺纹。
具体实施方式
[0019]
为使本发明实施例的目的、技术方案和优点更加清楚,下面将结合本发明实施例中的附图,对本发明实施例中的技术方案进行清楚、完整地描述。显然,所描述的实施例是本发明一部分实施例,而不是全部的实施例。基于本发明中的实施例,本领域普通技术人员在没有作出创造性劳动前提下所获得的所有其他实施例,都属于本发明保护的范围。
[0020]
下面结合实施例对本发明作进一步的描述。
[0021]
实施例1如图1、图2、图3、图4和图5所示,一种用于制造化工泵密封环的压铸模具,包括框板1,框板1顶端中心开设有贯通圆槽2,框板1顶端中心两侧对称开设有贯穿孔3,框板1在贯通圆槽2底端边缘开设有辅助环槽4,辅助环槽4的深度小于框板1内腔顶端厚度的一半,框板1内腔顶端中心设置有中心气缸5,中心气缸5的高度大于框板1内腔顶端至辅助环槽4顶端的垂直距离的一半,中心气缸5内部活动连接有中心活塞杆6,中心活塞杆6顶端中心固定有连接块7,连接块7中心开设有贯穿螺孔8,连接块7上方设置有下模盘9,下模盘9的直径的辅助环槽4的外直径,下模盘9顶端边缘开设有辅助插环10,辅助插环10的内直径等于辅助环槽4的内直径,辅助插环10的高度等于辅助环槽4的深度,下模盘9底端中心开设有连接槽11,连接
槽11和连接块7配合设置,下模盘9顶端中心固定有支撑底盘12,支撑底盘12的直径等于贯通圆槽2的直径,支撑底盘12顶端开设有环槽13,下模盘9侧面对称开设有隐藏槽14,隐藏槽14侧面中心开设有连接螺孔15,连接螺孔15的直径小于隐藏槽14的高度,连接螺孔15贯穿连接槽11设置,连接螺孔15和贯穿螺孔8内部螺纹连接有固定螺栓16,固定螺栓16为双头螺栓且两端通过螺母进行固定,固定螺栓16的长度小于下模盘9的直径,固定螺栓16的长度大于两组隐藏槽14之间的最小垂直距离;实施例2实施例2是对实施例1的进一步改进。
[0022]
如图1、图2、图5和图6所示,框板1内腔顶端中心两侧对称设置有侧气缸17,侧气缸17的高度等于框板1内腔的高度,侧气缸17内部活动连接有侧活塞杆18,侧活塞杆18活动穿过贯穿孔3,侧活塞杆18顶端中心开设有安装螺孔19,侧活塞杆18上方设置有横板20,横板20底端对称开设有两组安装孔21,安装孔21的直径等于侧活塞杆18的直径,安装孔21顶端中心开设有配合螺孔22,配合螺孔22贯穿横板20设置,配合螺孔22和安装螺孔19内部螺纹连接有安装螺栓23,安装螺栓23的长度略大于配合螺孔22和安装螺孔19的深度之和;实施例3实施例3是对实施例2的进一步改进。
[0023]
如图1、图6、图7和图8所示,横板20底端中心等间距开设有定位螺孔24,横板20下方设置有上模盘25,上模盘25的直径等于贯通圆槽2的直径,上模盘25底端固定有插环26,插环26的内直径等于环槽13的内直径,上模盘25顶端中心等间距设置有螺孔27,螺孔27和定位螺孔24配合等间距设置,螺孔27的深度小于上模盘25的高度,螺孔27和定位螺孔24内部螺纹连接有定位螺栓28,上模盘25顶端连通有液管29,液管29连通设置在上模盘25顶端位于插环26外壁和上模盘25边缘之间的区域中心位置,液管29侧壁上设置有螺纹30,螺纹30自液管29侧壁顶端设置,下模盘9顶端、支撑底盘12、上模盘25底端、插环26侧壁上均设置有脱模剂。
[0024]
使用时,首先对装置进行组装,利用连接块7和连接槽11的插接配合,将下模盘9安装在中心活塞杆6顶端,利用固定螺栓16螺纹连接连接螺孔15和贯穿螺孔8,将下模盘9固定在中心活塞杆6顶端,接着利用安装孔21和侧活塞杆18的插接配合,将横板20安装在侧活塞杆18顶端,利用安装螺栓23和安装螺孔19以及配合螺孔21的螺纹配合,将横板20固定在侧活塞杆18顶端,最后利用定位螺栓28和定位螺孔24以及螺孔27的螺纹配合,将上模盘25安装在横板20底端,装置组装完成,将装置拆分为多个组件,便于对其进行安装和使用,在进行密封环压铸时,启动中心气缸5和侧气缸17,利用中心气缸5带动中心活塞杆6上移,驱动下模盘9到达贯通圆槽2底端,此时辅助插环10插接在辅助环槽4内,支撑底盘12位于贯通圆槽2内,侧气缸17带动侧活塞杆18下移,驱动上模盘25下移至贯通圆槽2顶端,此时插环26插接在环槽13内,插环26外壁、支撑底盘12和贯穿圆槽2共同形成压铸空间,利用液管29上的螺纹30外接压力送液设备,进行密封环的压铸,可以利用中心气缸5和侧气缸17自由实现压铸空间的形成和取消,便于压铸后的物件的取出。
[0025]
以上实施例仅用以说明本发明的技术方案,而非对其限制;尽管参照前述实施例对本发明进行了详细的说明,本领域的普通技术人员应当理解:其依然可以对前述各实施例所记载的技术方案进行修改,或者对其中部分技术特征进行等同替换;而这些修改或者
替换,并不会使相应技术方案的本质脱离本发明各实施例技术方案的精神和范围。