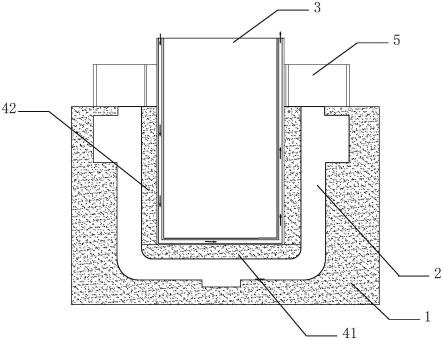
1.本技术涉及注塑机锁模液压系统铸造技术领域,具体的涉及一种注塑机锁模液压系统中的铸件铸型结构。
背景技术:2.注塑机锁模液压系统结构较为复杂,所需的液压铸件使用条件要求较高,如较高的机械性能,不允许出现裂纹、冷隔、缩孔、疏松、夹渣等缺陷,铸件不得渗油、漏油,因而对于液压铸件的铸造工艺要求也高。
3.图1-3所示,为注塑机锁模液压系统的一种液压铸件,该铸件的具体结构包括液压铸件本体a,位于液压铸件本体a中间设置有存在高液压和活塞杆行程的铸件液压腔b,以及同型腔液压腔b相连接的法兰c;铸件的铸件液压腔通常通过砂芯成形,传统的砂芯直接采用铬铁矿砂通过粘接剂构成,这种结构在浇注过程会存在砂型强度不够、冷却不均的问题,在铁液浇注过程可能会出现表面组织掉砂等现象,从而影响铸件液压腔的组织不够致密或出现气孔、夹渣等铸造缺陷,从而出现加工粗糙度达不到ra0.8μm和漏液、渗液的问题;法兰部位通过放置专用冷铁d,如图3所示,目的是为了加快热节处的激冷,消除法兰和铸件液压腔结合部位处的缩孔缩松缺陷,但是,实际生产中由于冷铁间隙控制不好,冷铁间隙一旦过大,该部位很容易出现漏液、渗液现象;此外,专用冷铁的使用直接影响铸件外观,导致铸件外观不平整,增加打磨工作量;而且冷铁在使用前需要进行抛丸、烘烤等处理,管控难度较大,若管控不好,还会使铸件表面产生气孔或渣孔等铸造缺陷,直接影响铸件内在质量。
4.此外,该液压铸件的材料为球墨铸铁qt450-10,外形轮毂尺寸φ990mm
×
625mm,重量1.3吨,最厚部位厚度135mm,液压铸件油压腔径向面加工粗糙度为ra0.8μm,因此对铸件的铸造性能要求极高,同时还要满足20mpa的液压要求,铸件不得出现漏液、渗液现象,目前大多数注塑机制造厂家还是用锻造的钢件为主,常规的铸造方法有很大难度;如该铸件的铸件液压腔部位的壁厚较厚(最厚可达135mm),因而热节分布都在铸件液压腔和法兰部位的结合厚壁处,该铸件传统的铸造方法是铸件液压腔朝上、法兰部位朝下的生产工艺,并且在热节处加冷铁以使腔体内的铁水相对均匀冷却,有时还要结合采用大冒口或发热冒口方式,减少热节处疏松缩孔等缺陷的产生。虽然经过上述努力,一定程度上可以生产出该液压铸件,但完全合格的成品率较低,即使合格的产品,也需要经切除去大冒口或发热冒口,或大量使用专用成形冷铁,冷铁管控难度大,打磨工作量多,造成生产成本高。另一方面,铸件液压腔朝上(法兰部位朝下)的生产工艺,存在最大的问题是铸件液压腔底部反面外观质量差,质量最差的铁水全部积聚该表面上,很大程度上影响了铸件的铸造质量,而且容易发生产品渗油、漏油现象。
技术实现要素:5.本技术针对现有技术的上述不足,提供一种结构紧固、强度高,铸件液压腔不用全部型砂构成的砂芯成形,直接通过用钢管作为砂型骨架的铸型成形,同时去掉法兰部位的
专用冷铁,获得的组织致密的铸件,满足高压条件下的使用的注塑机锁模液压系统中的铸件铸型结构。
6.为实现上述目的,本实用新型提供如下的技术方案:一种注塑机锁模液压系统中的铸件铸型结构,该结构包括位于下砂箱内的铸件型腔,所述的铸件型腔包括了型腔液压腔内壁,型腔液压腔内设置有型砂骨架钢管;所述的型砂骨架钢管的外层包覆有型砂层,所述的型砂层形成于型腔液压腔内壁与型砂骨架钢管之间,所述的型砂骨架钢管为中空设置,中空的内腔中能通入流动空气。
7.采用上述结构,本技术的铸型结构,通过型砂骨架钢管以及由砂子包覆型砂骨架钢管而形成的型砂层构成铸型,在铸型中浇注铁水后,可以通过钢管内腔的空气流动,达到对铸件的激冷作用,激冷效果明显而均匀,并且还可以省略了生铁的使用,避免了对生铁的处理工序,并且还保证了铸件表面的质量;更为重要的是本技术通过提供型砂支撑作用的钢管,同时兼有加速铸件在浇注过程中的冷却速度作用;此外,本技术通过设置型砂骨架钢管来替换原来全部是型砂(或芯砂)的结构,砂骨架钢管能作为支撑和加固、增强作用的型砂骨架,这样可以有效保证型砂的强度和型砂的用量,在铁液浇注填充型腔的过程中,不会造成掉砂、夹渣和气孔出现,从而保证了整个型腔液压腔组织的致密,使得铸件在液压20mpa下使用时,仍然不会出现渗液现象。
8.进一步的,所述的型砂层包括第一型砂层和第二型砂层,所述的第一型砂层位于型腔液压腔的底部,所述的第二型砂层位于型腔液压腔的侧壁与钢管之间;采用上述结构,通过两种不同的型砂层的设置,实现对铸件不同部位的型砂的设置,一来可见降低型砂层的制作难度,二来还可以防止整体型砂层制作过程容易出现的砂型强度不够、冷却不均的问题而导致的铁液浇注过程可能会出现的表面组织掉砂等现象。
9.更进一步的,所述的第一型砂层的砂层厚度控制在型腔液压腔底部圆角线上5mm~10mm;采用该结构,既能保证浇铸过程型砂不会冲砂,并且还能保证此处铸件的浇铸质量。
10.更进一步的,所述的第二型砂层的砂层厚度控制在15mm~25mm;该结构既能保证浇铸过程型砂不会冲砂,并且还能保证此处铸件的浇铸质量。
11.更进一步的,所述的型砂骨架钢管为双层结构,双层结构中间为中空的夹层,中空的夹层具有进气口和出气口,所述的流动空气自进气口进入自出气口流出;采用上述结构,钢管不仅仅实现了对型砂的支撑和增强作用,还可以通过夹层实现空气流动,对铸件的浇铸液实现有效的冷却。
12.进一步的,所述的型腔液压腔的上部覆盖有上砂箱,所述的型砂骨架钢管穿过所述的上砂箱并延伸至型腔液压腔内;采用该结构,既可以对型砂骨架钢管的位置实现有效的固定,保证铸件浇铸尺寸的准确,同时还可以通过型砂骨架钢管通入流动空气对型腔内进行冷却、且不影响型腔内部的结构。
13.进一步的,所述的型砂骨架钢管的上端面凸出于上砂箱的上端面;采用上述结构,方便型砂骨架钢管的安装和位置的有效固定,并且也方便型砂骨架钢管内部空气的通入。
14.更进一步的,所述的上砂箱的砂层高度为60mm~100mm,采用该高度可以在钢管外侧围砂以保护钢管,可以防止铁水浇注时出气或冒口溢出的铁水进入钢管。
15.进一步的,所述的型砂层为铸造砂(型砂)和型砂粘结剂组成的型砂层;本技术的
型砂和型砂粘结剂等材料,均为行业制备砂芯或者铸件砂箱常用的材料即可,即都是由铸造砂(型砂)、型砂粘结剂等组成,这种砂型的制作方法摒弃了传统的用铬铁矿砂,使得铁液冷却速度适中,型砂发气量少,确保了铸件不渗液,减少铬铁矿砂的用量,降低了生产成本。
附图说明
16.图1本技术本技术铸件的结构示意图。
17.图2本技术的铸件剖视图的结构示意图。
18.图3本技术具有冷铁的铸件的结构示意图。
19.图4本技术的注塑机锁模液压系统中的铸件铸型的结构示意图。
20.图5本技术的注塑机锁模液压系统中的铸件铸型合模后的结构示意图。
21.图6本技术型砂骨架钢管的结构示意图。
22.如附图所示:a.液压铸件本体,b.铸件液压腔,c.法兰,d.专用冷铁,1.下砂箱,2.铸件型腔,21.型腔液压腔,3.型砂骨架钢管,4.型砂层,41.第一型砂层,42.第二型砂层,5.上砂箱。
具体实施方式
23.下面将结合实施例中的附图,对本技术实施例中的技术方案进行清楚、完整地描述,显然,所描述的实施例仅仅是优选实施例,而不是全部的实施例。基于本技术中的实施例,本领域普通技术人员在没有做出创造性劳动前提下所获得的所有其他实施例,都属于本实用新型保护的范围;
24.本技术的铸件型腔有与铸件相同的尺寸造型,因此,铸件型腔各个位置的部件名称可以理解为与铸件各个对应位置的部件名称一致。
25.此外要说明的是:当部件被称为“固定于”(及其与“固定于”类似含有的其它方式)另一个部件,它可以直接在另一个部件上或者也可以存在另一中间部件,通过中间部件固定。当一个部件被认为是“连接”(及其与“连接”类似含有的其它方式)另一个部件,它可以是直接连接到另一个部件或者可能同时存在另一中间部件。当一个部件被认为是“设置于”(及其与“设置于”类似含有的其它方式)另一个部件,它可以是直接设置在另一个部件上或者可能同时存在另一中间部件。本文所使用的术语“垂直的”、“水平的”、“左”、“右”以及类似的表述只是为了说明的目的。除非另有定义,本文所使用的所有的技术和科学术语与属于本实用新型的技术领域的技术人员通常理解的含义相同。本文中在本实用新型的说明书中所使用的术语只是为了描述具体的实施例的目的,不是旨在于限制本实用新型。本文所使用的术语“及/或”包括一个或多个相关的所列项目的任意的和所有的组合。
26.如附图4、5、6所示,为本技术的一种注塑机锁模液压系统中的铸件铸型结构,该结构包括位于下砂箱1内的铸件型腔2,所述的铸件型腔2包括了型腔液压腔21,型腔液压腔21内设置有型砂骨架钢管3;所述的型砂骨架钢管3的外层包覆有型砂层4,所述的型砂层4形成于型腔液压腔21的内壁与型砂骨架钢管3之间,所述的型砂骨架钢管3为中空设置,中空的内腔中能通入流动空气。
27.采用上述结构,本技术的铸型结构,通过型砂骨架钢管以及由砂子包覆型砂骨架钢管而形成的型砂层构成铸型,在铸型中浇注铁水后,可以通过钢管内腔的空气流动,达到
对铸件的激冷作用,激冷效果明显而均匀,并且还可以省略了生铁的使用,避免了对生铁的处理工序,并且还保证了铸件表面的质量;更为重要的是本技术通过提供型砂支撑作用的钢管,同时兼有加速铸件在浇注过程中的冷却速度作用;此外,本技术通过设置型砂骨架钢管来替换原来全部是型砂(或芯砂)的结构,砂骨架钢管能作为支撑和加固、增强作用的型砂骨架,这样可以有效保证型砂的强度和型砂的用量,在铁液浇注填充型腔的过程中,不会造成掉砂、夹渣和气孔出现,从而保证了整个型腔液压腔组织的致密,使得铸件在液压20mpa下使用时,仍然不会出现渗液现象。
28.具体的,如附图5所示,本技术所述的型砂层4包括第一型砂层41和第二型砂层42,所述的第一型砂层41位于型腔液压腔的底部,所述的第二型砂层42位于型腔液压腔的侧壁与型砂骨架钢管3之间;采用上述结构,通过两种不同的型砂层的设置,实现对铸件不同部位的型砂的设置,一来可见降低型砂层的制作难度,二来还可以防止整体型砂层制作过程容易出现的砂型强度不够、冷却不均的问题而导致的铁液浇注过程可能会出现的表面组织掉砂等现象。
29.作为示例,本技术所述的第一型砂层41的砂层厚度控制在型腔液压腔底部圆角线上5mm~10mm;即第一型砂层41自型腔液压腔内壁的底部开始向上延伸至型腔液压腔底部圆角线上5mm~10mm;采用该结构,既能保证浇铸过程型砂不会冲砂,并且还能保证此处铸件的浇铸质量。
30.作为示例,本技术所述的第二型砂层42的砂层厚度控制在15mm~25mm;该结构既能保证浇铸过程型砂不会冲砂,并且还能保证此处铸件的浇铸质量。
31.作为示例,如附图4-6所示,本技术所述的型砂骨架钢管3为双层结构,双层结构中间为中空的夹层,型砂骨架钢管的内腔也是中空,可以降低重量,中空的夹层具有进气口和出气口(图6中箭头位置示出),所述的流动空气自进气口进入自出气口流出、实现空气在钢管内的循环冷却;采用上述结构,钢管不仅仅实现了对型砂的支撑和增强作用,还可以通过夹层实现空气流动,对铸件的浇铸液实现有效的冷却。
32.如附图4-5所示,本技术所述的型腔液压腔21的上部覆盖有上砂箱5,所述的型砂骨架钢管3穿过所述的上砂箱5并延伸至型腔液压腔21内;采用该结构,既可以对型砂骨架钢管的位置实现有效的固定,保证铸件浇铸尺寸的准确,同时还可以通过型砂骨架钢管通入流动空气对型腔内进行冷却、且不影响型腔内部的结构。
33.如附图4-5所示,本技术所述的型砂骨架钢管3的上端面凸出于上砂箱5的上端面;采用上述结构,方便型砂骨架钢管的安装和位置的有效固定,并且也方便型砂骨架钢管内部空气的通入。
34.作为示例,本技术所述的上砂箱的砂层高度为60mm~100mm,采用上述结构,在钢管的外周围护型砂,对钢管进行有效的保护,防止铁液高温对钢管造成影响,而且还可以防止铁水浇注时出气或冒口溢出的铁水进入钢管。
35.作为示例,所述的型砂层为铸造砂(型砂)和型砂粘结剂组成的型砂层;本技术的型砂和型砂粘结剂等材料,均为行业制备砂芯或者铸件砂箱常用的材料即可,即都是由铸造砂(型砂)、型砂粘结剂等组成,这种砂型的制作方法摒弃了传统的用铬铁矿砂,使得铁液冷却速度适中,型砂发气量少,确保了铸件不渗液,减少铬铁矿砂的用量,降低了生产成本。
36.本技术的铸型具体制作方法:第1步如图4所示,在液压腔(由模样作为支撑形成铸
件的型腔结构,制作完成后去除模样从而在此处形成铸件型腔,方便后续铁液的浇铸成型)内放入第一型砂层,第一型砂层的厚度控制在型腔液压腔底部圆角线上5mm~10mm;第2步如附图4、5所示在液压腔内放入钢管,控制钢管侧面同型腔液压腔内壁之间的砂层厚度15mm~25mm,厚度要均匀一致为第二型砂层;第3步是不断敲打钢管,将钢管下沉到第一型砂砂层,边放砂(第二型砂层的砂)边轻敲钢管,钢管与型腔液压腔壁之间的空间填满型砂并紧实。
37.本技术的技术方案通过在原来全部是型砂(或芯砂)的结构中设置了作为支撑和加固、增强作用的型砂骨架即一种具有中空夹层的空心钢管,这样可以有效保证型砂的强度和型砂的用量,在铁液浇注填充型腔的过程中,不会造成掉砂、夹渣和气孔出现,从而保证了整个液压腔组织的致密,使得铸件在液压20mpa下使用时,仍然不会出现渗液现象;而且本技术的空心钢管的中空夹层内可以通入流动冷却气体,实现对型腔有效散热,可以去除原有法兰处的冷铁的使用、而且冷却效果好。