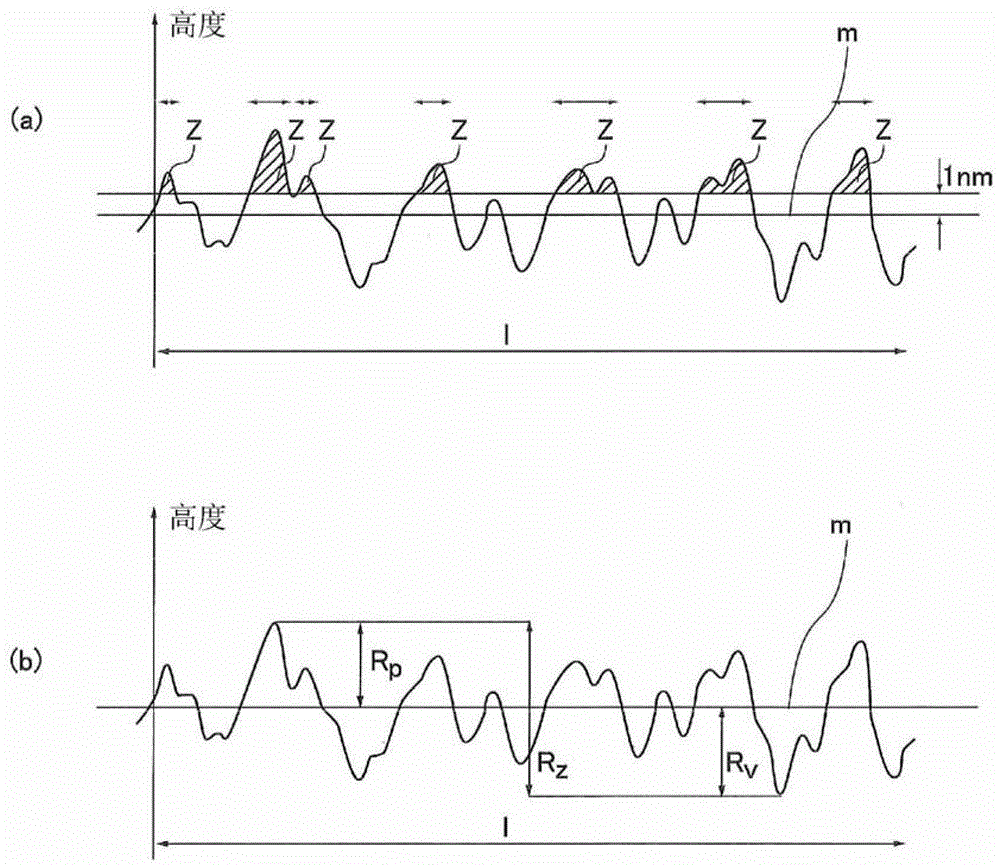
本发明涉及用于液晶显示器、等离子体显示器、有机EL显示器等平板显示器的显示器用玻璃基板的制造方法、玻璃基板以及显示器用面板。
背景技术:以往以来,在采用了作为显示用面板而使用的液晶显示器面板、等离子体显示器面板、或有机EL显示器面板的平板显示器的制造中,使用曝光装置并通过光蚀刻(Photolithography)在玻璃基板上形成精细的薄膜图案。用于这些平板显示器的显示器面板是在将玻璃基板投入到生产线上之后,经过搬运、成膜、光蚀刻、蚀刻、掺杂或布线等各个处理而制造得到的。在各个处理中,由于各种各样的原因,含有玻璃基板的面板处在容易产生静电的环境中。例如,将玻璃基板投入至生产线上时,从夹着隔纸而层积得到的2片以上的玻璃基板中将隔纸剥离除去从而一张一张地取出玻璃基板。此时,玻璃基板在除去隔纸时易产生静电。另外,为了成膜等而使用半导体制造装置的情况下,将玻璃基板放置在载置台上来进行成膜。此时,在玻璃基板上易产生由于气流而导致的静电、接触静电或剥离静电。剥离静电是将密合在载置台上的玻璃基板从载置台上取下时产生的静电。这样的静电会引起各种各样的问题,因此优选尽可能不产生静电。例如,在玻璃基板上形成TFT(薄膜晶体管)和布线图案时,灰尘或尘垢等杂质会因静电而附着在玻璃基板或布线图案上,有时会产生布线图案的缺损、剥离。另外有时由于蓄积的电荷的放电会产生TFT的破坏等。另外,玻璃基板有时会因上述静电而粘附在载置台上,从而有时在将玻璃基板从载置台上取下时会发生破裂。这种情况下,已知有使用离子发生器来进行带有静电的玻璃基板的除电的方法(专利文献1)。另外,对于曝光装置,也已知有放置处理基板(玻璃基板)的台面的表面具有1μm~100μm的表面粗糙度的曝光装置(专利文献2)。与此相对,已知有能够抑制在从接触状态将玻璃基板剥离时产生的静电的显示器用玻璃基板(专利文献3)。具体而言,该玻璃基板是板厚为0.3mm~6mm的显示器用玻璃基板,其中,通过使用测定长度为200mm、截止值为0.8mm~25mm的相位补偿型2RC带通滤波器的触针式表面粗糙度测定器测定得到的WCA(滤波中心线波纹度)的平均值为0.03μm~0.5μm。该玻璃基板能够减小与载置台之间的接触面积,而且能够抑制静电。进一步,也已知有对玻璃表面进行化学处理以使其算术平均粗糙度Ra为0.3nm~1.5nm(专利文献4)。具体而言,通过使玻璃基板的算术平均粗糙度Ra为0.3nm~1.5nm,由此能够减小玻璃基板与载置台之间的接触面积,其结果能够减少静电量。现有技术文献专利文献专利文献1:日本特开2009-64950号公报专利文献2:日本特开2007-322630号公报专利文献3:日本特开2002-72922号公报专利文献4:日本特开2010-275167号公报
技术实现要素:发明所要解决的课题但是,为了在玻璃基板的玻璃表面上形成表面凹凸,即使使上述WCA(滤波中心线波纹度)的平均值为0.03μm~0.5μm、或者即使对玻璃表面进行化学处理以使其算术平均粗糙度Ra为0.3nm~1.5nm,有时也无法充分得到抗静电效果。特别是对于与线宽和间距狭窄的布线图案一同使用的面向高精细/高分辨率显示器的例如形成有氧化物半导体或低温多晶硅半导体的玻璃基板,按照以往的使用上述参数进行管理,无法充分对应面向高精细/高分辨率显示器的玻璃基板的品质要求。例如,对于面向高精细/高分辨率显示器的玻璃基板,在所形成的布线图案中即使仅产生微小缺陷则作为显示器也是不适合的。另外,还存在如下问题:若布线图案的线宽或布线图案的间距间隔狭窄,则由于静电而导致的放电,即使该放电是低水平的放电,也容易产生半导体元件的静电破坏。因此,本发明的目的在于提供一种显示器用玻璃基板的制造方法和玻璃基板、以及使用了该玻璃基板的显示器用面板,所述显示器用玻璃基板的制造方法能够抑制玻璃基板移动或搬运时的静电,而且在半导体制造装置中从载置台与玻璃基板接触的状态将玻璃基板从载置台取下时,能够在该取下时难以产生静电。用于解决课题的方法本发明的一个方式是形成有半导体元件的显示器用玻璃基板的制造方法。该制造方法具有:制作玻璃基板的工序;和对所述玻璃基板的主表面中的一侧的玻璃表面进行表面处理从而形成表面凹凸的工序。在进行了所述表面处理的所述玻璃表面中,分散设置有自所述表面凹凸的表面粗糙度中心面起具有1nm以上的高度的凸部,且所述凸部占所述玻璃表面面积的面积比率为0.5%~10%。此时,所述表面凹凸的Rz(Rz是通过原子力显微镜测定得到的表面凹凸的最大高度)优选为2(nm)以上。更优选为3nm以上。另外,所述面积比率优选为0.75%~7.0%,更优选为1.2%~4.0%。另外,所述表面处理优选为使用了等离子体的干法蚀刻处理。另外,所述玻璃基板优选为半导体元件形成用玻璃基板。特别优选的是,所述半导体元件形成用玻璃基板中,与所述玻璃表面相反侧的主表面为形成有低温多晶硅半导体或氧化物半导体的面。本发明的一个方式是玻璃基板。在该玻璃基板的主表面中的一侧的玻璃表面上分散设置有自表面凹凸的表面粗糙度中心面起具有1nm以上的高度的凸部。所述凸部占所述玻璃表面面积的面积比率为0.5%~10%,所述玻璃基板的主表面中,与所述一侧玻璃表面相反一侧的另一侧的玻璃表面作为器件面而使用。所述玻璃基板优选在所述另一侧的玻璃表面上形成半导体元件。此时,所述另一侧的玻璃表面优选为形成有低温多晶硅半导体或氧化物半导体的面。另外,所述玻璃基板在所述另一侧的玻璃表面上形成有具备膜厚小于20μm的栅极绝缘膜的薄膜晶体管。本发明的一个方式是在玻璃基板上形成有半导体元件的显示器用面板。在该显示器用面板的玻璃基板上具有第1主表面和第2主表面。所述第1主表面具有如下玻璃表面:在该玻璃表面分散设置有自表面凹凸的表面粗糙度中心面起具有1nm以上的高度的凸部,所述凸部占所述玻璃表面面积的面积比率为0.5%~10%。所述第2主表面位于所述第1主表面的相反侧,并形成有半导体元件。发明效果根据上述方式的显示器用玻璃基板的制造方法以及玻璃基板、显示器用面板,能够抑制玻璃基板的移动或搬运时的静电。另外,在半导体制造装置中,从载置台与玻璃基板接触的状态将玻璃基板从载置台取下时,能够使得在该取下时难以产生静电。另外,还能够抑制在显示器用面板上形成的半导体元件的静电破坏。附图说明图1是本实施方式的玻璃基板的截面图。图2(a)说明自玻璃表面的表面粗糙度中心面起具有1nm以上的高度的凸部的区域的图,(b)是说明Rz的图。图3A是示出使用原子力显微镜测量得到的玻璃基板的表面轮廓形状的一个示例及其表面凹凸的直方图的图。图3B是示出在图3A所示的分布中,高度为0nm以上的凸部的分布和直方图的图。图3C是示出在图3A所示的分布中,高度为1nm以上的凸部的分布和直方图的图。图3D是示出在图3A所示的分布中,高度为1.5nm以上的凸部的分布和直方图的图。图4是示出玻璃表面的表面凹凸的示例的图。图5是示出制造本实施方式的玻璃基板的方法的流程的图。图6是说明在图5所示的方法中所使用的蚀刻装置的一个示例的图。图7是说明在图5所示的方法中所使用的蚀刻装置的其它示例的图。图8是说明在实验例中所进行的静电试验的图。具体实施方式以下,基于本实施方式对本发明的显示器用玻璃基板的制造方法、玻璃基板以及显示器用面板进行详细说明。本发明中,玻璃表面的表面凹凸是指,在将原子力显微镜(ParkSystems社制造,型号XE-100)适当校正后的状态下以非接触模式测量得到的结果。另外,在测量中,为了测量算术平均粗糙度小于1nm这样的表面粗糙度小的表面,对原子力显微镜进行了调整。作为测量条件,如下所示:·扫描区域为1μm见方,·扫描速度为0.8Hz,·伺服增益为1.5,·取样为256点×256点,·设定点为自动设定(也可以为手动设定)。图1是利用本实施方式的显示器玻璃基板的制造方法制造得到的玻璃基板10的截面图。玻璃基板10能够用于液晶显示器面板、等离子体显示器面板、有机EL显示器面板等的平板显示器。玻璃基板10进一步也能够作为太阳能电池面板的玻璃基板来使用。例如是厚度为0.1mm~0.8mm、且尺寸为550mm×650mm~2200mm×2500mm的玻璃基板。对于玻璃基板,在玻璃基板的制造后,在玻璃基板的主表面上形成半导体元件。玻璃基板10的一侧的玻璃表面12是形成TFT等半导体元件的面(半导体元件形成面),是形成低温多晶硅薄膜或ITO(氧化铟锡)薄膜等多层薄膜的半导体元件形成面(形成有低温多晶硅半导体或氧化物半导体的面)。TFT例如包括具备膜厚小于20μm的栅极绝缘膜的薄膜晶体管。面向高精细/高分辨率的显示器用面板中,栅极绝缘膜形成为例如5μm以上且小于20μm。另外,具备这样膜厚的栅极绝缘膜的TFT中,除了栅极绝缘膜以外,形成有半导体元件的各层也能够以膜厚较薄的形式形成。因此,对于玻璃表面12而言,Ra(算术平均粗糙度:JISB0601:2001)被抑制在0.2(nm)以下从而能够形成非常平滑的面。另一方面,在玻璃表面12的相反一侧,与玻璃表面12相对的玻璃表面14通过蚀刻而形成为粗面化处理面。具体而言,分散设置有自玻璃表面14的表面凹凸的表面粗糙度中心面起具有1nm以上高度的凸部,并且该凸部占玻璃表面14总面积的面积比率为0.5%~10%。需要说明的是,本实施方式中,通过蚀刻处理形成了表面凹凸,但并不限于蚀刻处理。只要是能够形成表面凹凸的表面处理即可。除蚀刻处理以外,表面处理还包括胶带研磨、毛刷研磨、研磨粒研磨、CMP(化学机械研磨)等物理研磨。图2(a)是以一维表示的方式来说明自玻璃表面14的表面粗糙度中心面起具有1nm以上的高度的形成于玻璃表面14上的凸部的区域的图,图2(b)是以一维表示的方式来说明Rz的图。图2(a)、图2(b)中,以一维表示的方式示出了表面轮廓形状,表面粗糙度中心面由平均基准线m示出。图2(a)中,以区域Z示出了自玻璃表面的表面粗糙度中心面(图中对应于平均基准线m)起具有1nm以上的高度的凸部(斜线的区域)的区域。此处,玻璃表面的表面粗糙度中心面是指,对以该中心面为基准的上述表面轮廓形状(二维的表面轮廓形状)的各位置的高度(高时为正、低时为负)进行相加(或者积分)时,位于总值(积分值)为0高度的平面。另外,在表面轮廓形状中,将相对玻璃表面14的表面凹凸的表面粗糙度中心面(图中为平均基准线m)的最大峰值高度定为Rp、最大谷深定为Rv,Rz为Rp和Rv的总值、即Rp+Rv。需要说明的是,Rz被定义在JISB0601:2001。使用图3A~图3D,对面积比率的测定方法进行说明。图3A是示出使用上述原子力显微镜测定得到的1μm×1μm(256点×256点)尺寸的表面轮廓形状的一个示例及其表面凹凸的直方图的图。高度为0nm的位置是玻璃表面的表面粗糙度中心面的位置。图3B~图3D分别示出自玻璃表面的表面粗糙度中心面起具有0nm以上、1nm以上以及1.5nm以上的高度的凸部所分散的分布和直方图。图3B~图3D中,高度为0nm以上的凸部、高度为1.0nm以上的凸部、高度为1.5nm以上的凸部分别以白色表示。对于凸部的高度为0nm、1nm、1.5nm以上的面积,根据算出的直方图,以0nm、1nm、1.5nm的高度进行切片,对0nm、1nm、1.5nm以上的图像中的像素数进行计数由此求出各凸部的面积。本实施方式的玻璃基板中,以图3C中示出的白色区域表示的高度为1nm以上的、玻璃表面14的全部区域中所含有的凸部占玻璃表面14全部区域的面积比率在0.5%~10%的范围内。由图3D可知:白色区域小于0.5%,1.5nm以上的高度的凸部的区域较小。如上所述,使高度为1nm以上的凸部占玻璃表面14面积的面积比率为0.5%~1%是基于如下理由。电荷的移动据说是在物体与物体之间的距离(例如玻璃基板与载置台等支撑体之间的距离)为某一程度以下、例如为1nm以下、进一步为0.2nm~0.8nm左右而产生的。因此,本发明人着眼于自玻璃表面14的表面凹凸的表面粗糙度中心面起具有1nm以上的高度的凸部。此时,发现了在不产生静电方面,使具有1nm以上的高度的凸部占玻璃表面14面积的面积比率为0.5%以上是有效的。据认为,面积比率小于0.5%的情况下,将玻璃基板放置在载置台上时、或放置后对玻璃基板进行吸附时,在玻璃基板的表面凹凸的凸部的周围部分与载置台的表面之间,凸部无法支撑玻璃基板,无法充分保持玻璃基板与载置台的表面的距离,从而引起静电。另一方面,面积比率超过10%的情况下,上述凸部与载置台之间的接触部分的面积增多,因此最大静电量增加。另外,按照面积比率超过10%的方式进行蚀刻的情况下,难以按目标对玻璃表面14的表面凹凸进行调整,无法确保表面品质,玻璃表面14上容易形成瑕疵缺陷。例如,潜在的微小瑕疵可能会由于表面处理而增大,形成瑕疵缺陷。因此,上述面积比率为0.5%~10%,优选上述面积比率为0.75%~7.0%,更优选为1.2%~4.0%。另一方面,在抑制静电方面,优选Rz为2nm以上。在抑制静电方面,更优选Rz为3nm以上。但是,若Rz超过规定值,则玻璃表面的面强度大幅下降,进而表面凹凸增大从而导致容易产生上述瑕疵缺陷。以往的玻璃基板中,为了抑制剥离静电而使Ra为0.3nm~1.5nm,即使使该Ra为0.3nm~1.5nm,本实施方式中上述凸部占玻璃表面面积的面积比率也无法为0.5%~10%。另外,即使上述面积比率为0.5%~10%,Ra也未必为0.3nm~1.5nm。即,Ra与上述面积比率是相互没有关系的参数。本实施方式中,例如为了抑制玻璃基板10的静电或其静电量,使玻璃表面14上高度为1nm以上的凸部的面积比率为0.5%~10%。因此,在玻璃表面14上通过粗面化处理而大量形成表面凹凸。因此,认为在抑制玻璃基板10的静电或静电量时,玻璃表面14的Ra一般会因粗面化处理而增大。但是,该Ra会因在玻璃表面14上所形成的表面凹凸的凸部的分布而大幅度变化。例如,假设为凸部的最大高度(自周围凹部的最大突出高度)相同的图4(a)、(b)所示的2个示例。图4(a)中所示的示例是大部分的凸部的高度大致统一为较低的高度,极少一部分的凸部的高度相比周围的凸部突出这样的示例。图4(b)中所示的示例是2个以上的凸部中基本上所有的高度几乎一致的示例。此时,算术平均粗糙度Ra为Ra2>Ra1。并且,相比图4(b)所示的示例,图4(a)所示的示例中,凸部与载置台接触的面积较小,因此图4(a)所示的示例能够较大地抑制玻璃基板10的静电或静电量。因此,根据图4(a)、图4(b)所示的示例,为了抑制静电或静电量,最好使玻璃表面14的Ra较小。这一点与为了抑制静电或静电量而使玻璃表面14的Ra增大这样的一般想法矛盾。如此,Ra作为用于抑制玻璃基板10的静电或静电量的指标并不充分。考虑到这一点,本实施方式中按照玻璃表面14上高度为1nm以上的凸部的面积比率为0.5%~10%的方式进行玻璃表面14的粗面化处理。本实施方式的玻璃基板10中玻璃基板的静电或其静电量得到抑制,因此能够适当用于使用半导体制造装置来进行成膜等处理的玻璃基板,除此以外,也能够适当用于期望在玻璃基板上不附着灰尘或尘垢的彩色滤光片形成用玻璃基板。另外,本实施方式的玻璃基板10能够作为在上述的玻璃表面12上形成有具备膜厚小于20μm的栅极绝缘膜的TFT的玻璃基板而优选使用。近年来,在高精细/高分辨率显示器用面板中,以绝缘膜为主,半导体元件中所含的各层的膜厚变薄。在这样的背景下,可以举出为了对应像素间距变窄、或加快显示切换的要求,要求使栅极绝缘膜变薄。另外,从为了显示器用面板的省电化而使栅极电压变小的观点出发,也要求使栅极绝缘膜的膜厚变薄。作为高精细/高分辨率面板中的薄膜化的一个示例,正在进行使栅极绝缘膜的膜厚小于20nm的研究。对于栅极绝缘膜的膜厚,以往为70nm~100nm左右,但近年来形成有50nm,进一步形成有20nm这样的厚度。能够使栅极绝缘膜如此变薄是因为提高了栅极绝缘膜的膜品质,由此能够根据上述要求而使膜厚变薄。但是,另一方面,由于玻璃基板的静电会产生半导体元件的静电破坏这样的问题,例如在栅极绝缘膜中发生放电、使栅极绝缘膜受到损伤等。因此,作为用于形成有这样的栅极绝缘膜小于20μm的TFT的显示器用面板的玻璃基板,使用如上所述的能够抑制静电或静电量的玻璃基板是特别有效的。(显示器用面板)在这样的玻璃基板10的主表面上形成半导体元件,从而制作得到显示器用面板。具体而言,显示器用面板的玻璃基板10具有第1主表面和第2主表面。第1主表面是分散设置有自表面凹凸的表面粗糙度中心面起具有1nm以上的高度的凸部的上述玻璃表面14,上述凸部占玻璃表面14面积的面积比率为0.5%~10%。第2主表面是与第1主表面(玻璃表面14)相反一侧的面,第2主表面为上述玻璃表面12,并形成有半导体元件。例如,在第2主表面上形成有将电极、布线图案等图案化的导体薄膜或半导体元件。即,对于第2主表面,除了形成电极用导体薄膜或形成半导体薄膜以外,还经过形成抗蚀膜、蚀刻、抗蚀剂剥离等光蚀刻工序,从而形成显示器用面板。在这样的显示器用面板中,在面板制造工序时,玻璃基板10的静电或静电量得到抑制,因此能够抑制半导体元件的静电破坏。特别是与以往所形成的非晶硅半导体相比,在玻璃基板10上形成低温多晶硅半导体或氧化物半导体的情况下,半导体元件的厚度变薄,而且与半导体元件连接的布线的宽度以及间距间隔变窄,间距间隔例如从5μm变窄至1.5μm~3μm左右。因此,防止因静电而导致的破坏的要求比以往更高。因此,在玻璃基板10上形成低温多晶硅半导体或氧化物半导体的情况下,能够抑制静电或静电量的玻璃基板10的效果大。另外,玻璃基板10适当用于形成有具备上述的膜厚小于20μm的栅极绝缘膜的TFT的显示器用面板。这样的膜厚小的栅极绝缘膜容易发生放电易而损伤,但通过使用玻璃基板10能够抑制玻璃基板的静电以及其静电量,因此可有效地抑制这样的TFT的静电破坏。因此得到了可实现栅极绝缘膜等的薄膜化、同时能够抑制因静电而导致的问题的高精细/高分辨率显示器用面板。(玻璃组成)作为玻璃基板10的玻璃的组成,以含有以下成分的玻璃为示例。(a)SiO2:50质量%~70质量%、(b)B2O3:5质量%~18质量%、(c)Al2O3:10质量%~25质量%、(d)MgO:0质量%~10质量%、(e)CaO:0质量%~20质量%、(f)SrO:0质量%~20质量%、(o)BaO:0质量%~10质量%、(p)RO:5质量%~20质量%(其中,R是选自Mg、Ca、Sr以及Ba中的至少1种)(q)R’2O:0质量%~2.0质量%(其中,R’是选自Li、Na以及K中的至少1种)(r)选自氧化锡、氧化铁及氧化铈中的至少1种的金属氧化物:合计为0.05质量%~1.5质量%。这样的玻璃基板10可以使用下拉法、浮法等来制造。在以下的说明中,对使用了下拉法的制造方法进行说明。图5是说明本实施方式的玻璃基板10的制造方法的流程的一个示例的图。显示器用玻璃基板的制造方法主要具有:熔解工序(步骤S10)、澄清工序(步骤S20)、搅拌工序(步骤S30)、成型工序(步骤S40)、缓慢冷却工序(步骤S50)、采取基板工序(步骤S60)、切断工序(步骤S70)、粗面化处理工序(步骤S80)、和端面加工工序(步骤S90)。通过上述熔解工序(步骤S10)、澄清工序(步骤S20)、搅拌工序(步骤S30)、成型工序(步骤S40)、缓慢冷却工序(步骤S50)、采取基板工序(步骤S60)、和切断工序(步骤S70),制作得到具有形成有半导体元件的面的玻璃基板10。通过之后所进行的粗面化处理工序,在玻璃基板10的主表面中的与形成有半导体元件的面相反一侧的玻璃表面14上形成表面凹凸。熔解工序(步骤ST10)在熔解炉中进行。在熔解炉中,将玻璃原料投入至蓄积在熔解炉中的熔融玻璃的液面上并进行加热来制作熔融玻璃。进一步,使熔融玻璃从设置在熔解炉的内侧侧壁的1个底部的流出口流向下游工序。熔解炉的熔融玻璃的加热除了在熔融玻璃自身通电进行自发热来加热的方法以外,还可以利用燃烧器辅助性地提供火焰来对玻璃原料进行熔解。需要说明的是,玻璃原料中添加有澄清剂。作为澄清剂没有特别限制,已知有SnO2、As2O3、Sb2O3等。但是,从降低环境负荷的观点出发,优选使用SnO2(氧化锡)作为澄清剂。澄清工序(步骤ST20)至少在澄清管内进行。澄清工序中,使澄清管内的熔融玻璃升温,由此熔融玻璃中所含有的含O2、CO2或SO2的气泡吸收由于澄清剂的还原反应而生成的O2而成长,气泡上浮至熔融玻璃的液面从而放出。进一步,在澄清工序中,使熔融玻璃的温度下降,由此使由澄清剂的还原反应得到的还原物质进行氧化反应。由此,熔融玻璃中残存的气泡中的O2等气体成分再次被吸收至熔融玻璃中,气泡消失。基于澄清剂的氧化反应以及还原反应能够通过控制熔融玻璃的温度来进行。需要说明的是,澄清工序能够使用减压脱泡方式,该减压脱泡方式是在澄清管内形成减压气氛的空间,使存在于熔融玻璃中的气泡在减压气氛中成长从而脱泡。接着,进行搅拌工序(步骤S30)。搅拌工序中,为了保持玻璃的化学方面以及热方面的均匀性,使熔融玻璃通过面向垂直方向的未图示的搅拌槽。一边利用设置在搅拌槽中的搅拌器对熔融玻璃进行搅拌,一边使其向垂直下方向底部移动,导入至后工序。由此能够抑制波筋等玻璃的不均匀性。接着,进行成型工序(步骤S40)。成型工序中使用下拉法。下拉法是使用了例如日本特开2010-189220号公报、日本专利第3586142号公报的众所周知的方法。由此,成型得到具有规定厚度、幅宽的片状玻璃。作为成型方法,在下拉法中最优选溢流下拉法,但也可以为流涎下拉法。接着,进行缓慢冷却工序(步骤S50)。具体而言,对成型后的片状玻璃,按照不产生应变和弯曲的方式来控制冷却速度,从而使其在未图示的缓慢冷却炉中冷却至缓慢冷却点以下。接着,进行采取基板工序(步骤S60)。具体而言,连续生成的片状玻璃按照每一个恒定的长度的方式进行采取,得到玻璃基板。之后,在切断工序(步骤S70)中,按规定的尺寸对玻璃基板进行切断。接着,进行粗面化处理(步骤S80)。具体而言,对玻璃基板实施表面清洗处理,之后实施蚀刻处理。表面清洗处理中,例如使用了未图示的大气压等离子体清洗处理装置;蚀刻处理中,使用了采用大气压等离子体的蚀刻装置。大气压等离子体清洗处理装置中,例如,从在玻璃基板10的整个宽度方向上延长的狭缝状的喷嘴,向通过搬运辊搬运的玻璃基板10的玻璃表面14(与搬运辊接触的面)吹附使用了N2、O2的等离子体状态的气体。大气压等离子体清洗处理装置具有:N2、O2的供给路;设置在供给路途中的两侧的1对的相向电极;覆盖该一对相向电极各自表面的电介质,上述供给路的端部为等离子体照射口而朝向玻璃基板10。向玻璃表面14吹附这样的因等离子体而活性化的气体(自由基),由此能够使由附着在玻璃表面14上的不需要的有机物构成的薄膜氧化而除去。除去由有机物构成的薄膜是为了在后述的蚀刻处理中不会使由有机物构成的薄膜作为掩膜而发挥功能。因此,通过等离子体清洗的玻璃表面14除去了有机物从而呈现亲水性。此时玻璃表面14的水接触角优选为10度以下,更优选为5度以下。这样的优选方式能够通过调整基于活性化的气体的清洗时间或气体的流量来达成。即,作为表面清洗的条件,优选调整清洗时间以及活性化的气体的流量,由此使得水接触角为10度以上。需要说明的是,除使用大气压等离子体的清洗之外,也可以通过进行臭氧气体的吹附或紫外线的照射来除去有机物的薄膜。只要能够至少使有机物氧化或使有机物的薄膜改性然后除去即可。另外,也可以通过能够除去有机物的清洗液的涂布或浸渍处理来进行清洗。但是,为了有效地进行后述的干法蚀刻,优选通过臭氧气体的吹附或紫外线的照射来进行清洗。图6是示出使用了大气压等离子体的蚀刻装置的一个示例的图。使用了大气压等离子体的蚀刻装置30具有蚀刻头34和未图示的气体排气单元。蚀刻装置30中,对于由搬运辊32搬运的玻璃基板的一侧的玻璃表面14(与搬运辊32接触的面),从蚀刻头34的在玻璃基板10的整个宽度方向上延长的狭缝状的喷嘴向玻璃表面吹附蚀刻气体。蚀刻气体是具有通过使CF4和H2O的混合气体为等离子体状态从而生成的活性化的HF成分的气体。由此,玻璃表面通过蚀刻气体被粗面化。需要说明的是,在玻璃基板10的玻璃表面14上分散设置有自蚀刻处理后的表面凹凸的表面粗糙度中心面起具有1nm以上的高度的凸部。按照该凸部占玻璃表面14的总面积的面积比率为0.5%~10%的方式进行上述蚀刻处理。具体而言,对粗面化处理的条件(表面清洗的条件以及蚀刻条件)进行了设定。例如,蚀刻条件中,通过对玻璃基板10的搬运速度进行调整来调整蚀刻的处理时间、或对吹附至玻璃表面14的蚀刻气体的流量、气体的种类和浓度进行调整。需要说明的是,用于粗面化处理的蚀刻方法并不限于是使用蚀刻气体的干法蚀刻,也可以使用将蚀刻液涂布在粗面化处理的玻璃表面的湿法蚀刻。图7是示出使用了蚀刻液MS对玻璃表面进行粗面化处理的方法的图。蚀刻液MS储藏在容器28中。在玻璃基板10与容器28之间,按照玻璃表面14与蚀刻液MS接触而被搬运的方式来设置搬运辊22以及搬运涂布辊24。搬运涂布辊24的外围面由海绵材料构成。另外,搬运涂布辊24的外围面的一部分浸渍在蚀刻液MS中。因此,在搬运涂布辊24的表面上吸收有蚀刻液MS。吸收在搬运涂布辊24上的蚀刻液MS与玻璃基板10的玻璃表面14接触从而使蚀刻液MS涂布在玻璃表面14上。此时,为了调整涂布在玻璃基板10上的蚀刻液MS的涂布量,通过挤压旋转的接触辊26来挤出吸收在搬运涂布辊24上的蚀刻液MS的一部分。即,装置中设置有对搬运涂布辊24的表面进行挤压的接触辊26。需要说明的是,进行使用了蚀刻液MS的粗面化处理时,除了这样调整涂布量以外,也可以对用于蚀刻液MS的氟酸的浓度、和蚀刻时间进行调整。例如,使用4000ppm~5000ppm这样浓度比较高的氟酸,并且对涂布量以及蚀刻时间进行调整,从而也能够粗面化为所期望的形状。图7所示的装置中,通过调整接触辊26挤压搬运涂布辊24的表面的程度,由此能够调整涂布在玻璃表面14上的蚀刻液MS的涂布量。即,在蚀刻处理后的玻璃表面14上,按照分散设置有自表面凹凸的表面粗糙度中心面起具有1nm以上的高度的凸部、并且该凸部占玻璃表面面积的面积比率为0.5%~10%的方式调整蚀刻处理的条件。利用水等对基于涂布蚀刻液MS而进行了蚀刻处理的玻璃基板10进行漂洗处理。由此,通过干法蚀刻或湿法蚀刻进行粗面化处理工序。也可以进行胶带研磨、毛刷研磨、研磨粒研磨、CMP(化学机械研磨)等物理研磨来代替干法蚀刻或湿法蚀刻。之后,进行端面加工工序(步骤S90)。端面加工工序中,进行玻璃表面以及端面的研削、研磨。端面加工中使用了例如金刚石砂轮或树脂砂轮等。除此之外,显示器用玻璃基板的制造方法还具有清洗工序以及检查工序,但此处将这些工序的说明省略。由此得到的玻璃基板10搬运至面板制造商,在面板制造商处,对玻璃基板10的形成了玻璃表面12的主表面进行电极用导体薄膜的形成或半导体薄膜的形成,除此之外,经过抗蚀膜的形成、蚀刻、抗蚀剂剥离等光蚀刻工序,从而形成电极、布线或半导体元件等,制作得到显示器用面板。需要说明的是,在玻璃基板10的玻璃表面12上,除形成半导体元件等之外,还可以通过光蚀刻工序形成含有黑色矩阵或RGB图案的彩色滤光片。如以上所述,按照分散设置有自蚀刻处理的玻璃表面14的表面凹凸的表面粗糙度中心面起具有1nm以上的高度的凸部、且该凸部占玻璃表面面积的面积比率为0.5%~10%、优选为0.75%~7.0%、更优选为1.2%~4.0%的方式,对于玻璃基板10进行蚀刻处理。由此,即使在半导体制造装置等的载置台与玻璃基板接触之后取下玻璃基板时,也难以在该接触或取下时产生静电。特别是在难以产生静电方面,优选表面凹凸的Rz(Rz是通过原子力显微镜测定得到的表面凹凸的最大高度)为2(nm)以上。[实施例]为了调查本实施方式的效果,制作了使用了硼铝硅酸盐玻璃的液晶显示装置用玻璃基板。(粗面化处理)对制作的玻璃基板进行上述的大气压等离子体清洗。即,使等离子体状态的N2、O2的混合气体以每分钟规定的量流向玻璃基板的整个宽度,对玻璃基板的玻璃表面进行清洗。进一步,使用图6所示的蚀刻装置30进行了蚀刻。在蚀刻装置30中使自由基化的蚀刻气体HF流向玻璃基板的整个宽度,从而进行蚀刻,所述蚀刻气体HF是使CF4、H2O的混合气体通过使用稀有气体等而生成的等离子体中而得到的。下述表1所示的试料1~8是对CF4、H2O的供给量、以及加入到CF4、H2O的混合气体中的载体气体的种类(N2或Ar气体)进行各种各样的变化,由此对通过粗面化处理而形成的表面凹凸的形态进行各种各样改变的示例。试料0是完全未进行干法蚀刻的示例。[表面凹凸]关于玻璃基板10的玻璃表面14的表面凹凸,从制作的玻璃基板10切出试料(长50mm、宽50mm),使用原子力显微镜(ParkSystems公司制造,型号XE-100)以非接触模式分别对试料进行测量。测量之前,为了对算术平均粗糙度Ra小于1nm这样的表面粗糙度小的表面凹凸进行测量,对装置进行了调整。测量时,使扫描区域为1μm×1μm(取样数为256点×256点)、扫描速度为0.8Hz。另外,使该原子力显微镜的非接触模式的伺服增益为1.5。设定点为自动设定。通过该测量得到了关于表面凹凸的二维表面轮廓形状。由该表面轮廓形状得到表面凹凸的直方图,以从表面粗糙度中心面的高度为1nm的高度进行切片,对高度为1nm以上的图像中的像素数进行计数从而求出凸部的面积,由此求出了凸部的面积比率(%)。同时求出了Rz(nm)。[静电评价]玻璃基板的静电评价中使用了730mm×920mm尺寸且厚度为0.5mm的玻璃基板10。从如图8所示那样将玻璃基板10放置在基板台40上而利用升降销42对其进行支撑的状态,使升降销42相对基板台40的载置面下降,由此使玻璃基板10下降从而放置在基板台40上。基板台具有对铝制的台进行阳极氧化处理(alumite)后的表面。进一步,利用未图示的吸引装置以50kPa将玻璃基板10从设置在基板台40的载置面的吸引口吸引后,终止吸引,使升降销42上升。以这样的玻璃基板10的下降、吸引、吸引终止、上升为1个循环,反复进行了多次循环直到静电量饱和。1个循环为10秒。另外,对每个循环测量静电量。通过测量玻璃中央部的玻璃表面的电势来代替静电量的测量。测量使用了表面电势计(欧姆龙(OMRON)社制造的ZJ-SD)。表面电势计的设置高度为10mm。静电测定环境以基于温湿度计的实测值表示为23.5℃、74%~75%。由该测量结果得到了表示最大静电量的最大电势和带电速度。测定是对玻璃基板的与基板台侧相反一侧的面的电势进行测定的。最大电势是反复多次进行上述循环直至玻璃基板10的静电量为饱和状态为止的饱和时的电位。带电速度是电势的绝对值超过100V为止的循环的次数。需要说明的是,测定侧的玻璃基板的表面的电势为负值。表1中使用绝对值来表示。使通过蚀刻处理而形成的具有1nm以上的高度(自表面凹凸的表面粗糙度中心面的高度)的凸部占玻璃表面14的总面积的面积比率与Rz变化时,将此时的带电速度和最大电势的评价结果示于下述表1。[表1]需要说明的是,试料1、2的算术平均粗糙度Ra为0.3nm~1.5nm,但如表1所示,面积比率未在0.5%~10%的范围内。从表1的评价结果可知:带电速度(次数)超过10次的试料(带电速度低,为允许的情况),且最大电势的绝对值小于17kV的试料是试料3~8,面积比率均为0.5%~10%。进一步,可知面积比率为0.75%~7.0%的情况下,最大电势低于16.2kV(静电量是允许范围的条件),难以产生静电的问题。面积比率包含在1.2%~4.0%的范围的试料5~7的最大电势低于16kV,带电速度也低,在该方面更为优选。即,更优选凸部的面积比率为1.2%~4.0%。以上,对本发明的显示器用玻璃基板的制造方法以及玻璃基板、显示器用面板进行了详细说明,但本发明并不限定于上述实施方式,在不脱离本发明的主体思想的范围内,可以进行各种各样的改良及变更,这自不必而言。特别是对于与线宽和间距狭窄的布线图案一同使用的面向高精细/高分辨率显示器的例如氧化物半导体或低温多晶硅半导体形成用的玻璃基板,按照以往的使用上述参数进行管理,无法充分对应这些玻璃基板的品质要求。根据本发明,能够在玻璃基板上所形成的布线电极的线宽狭窄、且即使是微小的缺陷也不能被允许的面向高精细/高分辨率显示器的玻璃基板中,抑制静电的问题。另外,不仅能够消除由于放电而产生的问题,也能够通过减少杂质因静电而附着在玻璃基板上的量来提高与玻璃的密合性低的Cu系电极布线的成品率。即,通过使用本发明的玻璃基板,即使在线宽狭窄的情况下,也能够使用与玻璃的密合性低的布线/电极材料。例如,能够使用Ti-Cu合金等Cu系电极材料,该Ti-Cu合金等Cu系电极材料与Al系电极或Cr、Mo电极等相比密合性低,但电阻低。如此,电极材料的选择范围扩大,由此能够消除在面向电视机等的大型面板中容易成为问题的RC延迟(布线延迟)的问题。另外,可以预想到面向手机终端的小型面板在今后会进一步高精细化,而本发明可提供能够消除面向这样的手机终端的小型面板中所产生的RC延迟的问题的玻璃基板。另外,上述说明中,使用设置有半导体元件作为器件的玻璃基板,对静电的问题进行了说明,但本发明即使作为面向形成有彩色滤光片等作为器件的显示器的玻璃基板的静电解决方法也是有效的。例如,在彩色滤光片(CF)面板中,黑色矩阵(BM)的细线化正在发展,根据本发明,即使是液晶显示器用的CF面板的BM线宽为20μm以下、例如细线化至5μm~10μm的液晶用面板也不会产生由于杂质而引起的BM剥离。符号的说明10玻璃基板12、14玻璃表面22搬运辊24搬运涂布辊26接触辊28容器30蚀刻装置34蚀刻头40基板台42升降销