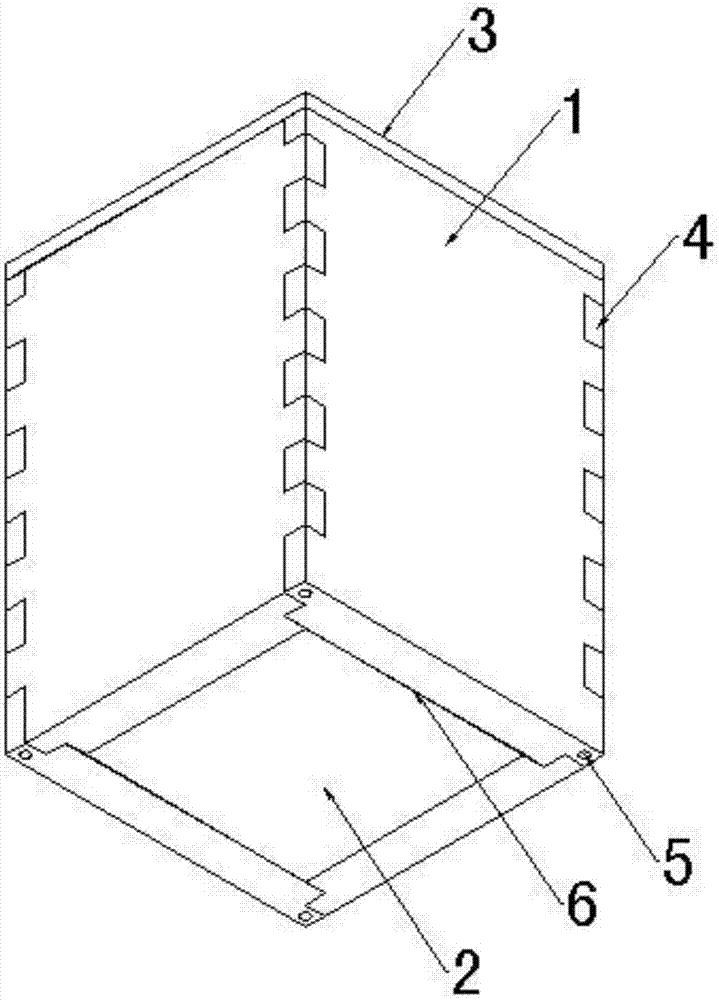
本发明属于锂电池负极材料生产领域,尤其涉及一种生产石墨负极材料用石墨负极材料的方形石墨坩埚及加工方法。
背景技术:
生产石墨负极材料主要使用艾奇逊及内串式石墨化炉,将石墨负极材料装入石墨坩埚内进行石墨化处理,将碳原子由热力学上不稳定的“二维无序重叠”排列转变为“三维有序重叠”排列。现国内生产石墨负极材料的厂家普遍采用圆形再生石墨坩埚(即使用石墨化石油焦与沥青等材料混捏压型,经过焙烧碳化后即投入使用)。由于圆形再生石墨坩埚生产成本较低,在生产石墨负极材料过程中,圆形再生石墨坩埚无可替代,所以每年将有100多万支圆形再生石墨坩埚流入负极材料市场,而圆形再生石墨坩埚的消耗占负极材料生产成本20%以上(即每吨石墨负极材料将消耗2.5个圆形再生石墨坩埚)。由于圆形再生石墨坩埚中的煤沥青没有经过石墨化处理,所以在生产石墨负极材料过程中圆形再生石墨坩埚如容易产生变形、开裂及大量杂质、有害气体释放,使用寿命4-5炉,同时将挥发物、杂质带入到石墨负极材料中,将对石墨负极材料品质造成影响。技术实现要素:本发明是要解决的技术问题是提供一种生产石墨负极材料用方形石墨坩埚及加工方法,结构牢固、容积大,可提高每炉次的产量,杂质、有害气体已得到充分挥发,从而使石墨负极材料品质得到保证,防止坩埚使用过程中变形、开裂,使用寿命长,生产成本低。本发明的技术解决方案:生产石墨负极材料用方形石墨坩埚,包括四块石墨侧板、石墨底板和石墨盖板,所述四块石墨侧板合围成方形侧壁,其特殊之处在于:相邻的两块石墨侧板之间相互指接并粘合,在相邻的两块石墨侧板指接处设有上下贯通的销孔,在所述销孔内镶有等静压石墨销轴,相互对应的等静压石墨销轴和销孔之间间隙配合并粘合。进一步地,所述石墨侧板底端设有内卡沿,四块石墨侧板内卡沿相互拼接并围成方形外卡口,所述石墨底板边缘设有方形有内卡口,所述内、外卡口卡接并粘合。进一步地,所述石墨侧板顶面内缘设有凸条,四个凸条围成方形内止口,所述石墨盖板底面设有方形外止口,所述石墨盖板与石墨侧板之间通过止口定位。一种如上所述的生产石墨负极材料用方形石墨坩埚的加工方法,其步骤如下:1、组件制作利用石墨毛坯加工所述的石墨盖板、石墨侧板、石墨底板和等静压石墨销钉;2、配制粘接剂按照重量百分比取50-60%高温呋喃树脂、10-20%煤沥青、10-20%细石墨粉和呋喃树脂固化剂20―30%,混匀,加热至70-100℃,备用;3、组装在四块石墨侧板的指接接口以及所述石墨侧板与石墨底板的连接处涂抹所述粘接剂,将其中二块石墨侧板指接后与石墨底板卡接并粘合;将其余二块石墨侧板指接与石墨底板卡接并粘合,同时完成四块石墨侧板指接;将等静压石墨销钉表面涂抹粘接剂后由上至下镶装在对应的石墨侧板销孔内;4、固化将组装好的方形石墨坩埚放到烘干炉内进行固化,起始固化,室温升至110-150℃,升温时间1.5-2.5h,保温0.5-1.5h;再升温至170-200℃,升温时间1.5-2.5h,保温1.5-2.5h;5、炭化固化后将石墨坩埚在真空烧结炉中炭化,升温至350℃,升温时间4-5h;再升温至450℃,升温时间5-7h;450℃保温1-2h;再升温至550℃,升温时间5-7h;升温至750℃,升温时间5-7h;750±25℃保温2-3h,炭化时通氮气进行保护,通气量15~20l/min,方形石墨坩埚制作完成。进一步地,固化时,由室温升至130℃,升温时间2h;130℃保温1h;再由130℃升到至180℃,升温时间2h,180℃保温2h。进一步地,炭化时,由180℃升温至350℃,升温时间4h;再由350℃升温至450℃,升温时间6h;450℃保温1h;再由450℃升温至550℃,升温时间6h;由550℃升温至750℃,升温时间6h;750±25℃保温2h。进一步地,步骤2中按照重量百分比为55%高温呋喃树脂、12%煤沥青、12%细石墨粉和21%呋喃树脂固化剂。进一步地,所述细石墨粉的粒径≤325目。本发明的有益效果是:1、方形石墨坩埚比圆形再生石墨坩埚容积增加20%,即每一炉次,生产石墨负极材料产量将提升7-8吨。2、方形石墨坩埚由于侧板使用石墨板指接而成,同时石墨板已经过高温石墨化处理,杂质、灰分和有害气体得到充分挥发,从而促使石墨负极材料品质得到保证。3、由于方形石墨坩埚采用石墨板指接而成,坩埚将不存在变形、开裂等现象,同时没有损坏的石墨板可重复加工再利用,保证方形石墨坩埚比圆形再生石墨使用寿命提升1倍以上。4、通过使用改进后的方形石墨坩埚,将使石墨负极材料生产成本将降低10%左右。5、采用本发明的粘合剂可以在高温下形成碳网,使侧板和底板牢固地粘接为一体;通过固化、碳化处理,可防止石墨坩埚高温下开裂、变形,延长使用寿命,可使用10炉-15炉。附图说明图1是本发明的立体图;图2是本发明的结构示意图;图3是图2中a-a剖视图;图4是图2中b-b剖视图;图中:1-石墨侧板,2-石墨底板,3-石墨盖板,4-指接接口,5-等静压石墨销轴,6-外卡口,7-内卡口,8-内止口,9-外止口。具体实施方式以下结合附图和实施例对本发明进行详细说明。生产石墨负极材料用方形石墨坩埚,包括四块石墨侧板1、石墨底板2和石墨盖板3,所述四块石墨侧板3合围成方形侧壁,相邻的两块石墨侧板1之间相互指接并粘合,在相邻的两块石墨侧板1指接处设有上下贯通的销孔,在所述销孔内镶有等静压石墨销轴5,相互对应的等静压石墨销轴5和销孔之间间隙配合并粘合。所述石墨侧板1底端设有内卡沿,四块石墨侧板1内卡沿相互拼接并围成方形外卡口6,所述石墨底板1边缘设有方形内卡口7,所述内、外卡口卡接并粘合。所述石墨侧板1顶面内缘设有凸条,四个凸条围成方形内止口8,所述石墨盖板3底面设有方形外止口9,所述石墨盖板3与石墨侧板1之间通过止口定位。一种如上所述生产石墨负极材料用方形石墨坩埚的加工方法,具体实施例如下:实施例1如上所述生产石墨负极材料用方形石墨坩埚的加工方法,其步骤如下:1、组件制作利用石墨毛坯车削形状如上所述的石墨盖板3、石墨侧板1、石墨底板2和等静压石墨销钉5;2、配制粘接剂按照重量百分比取50%高温呋喃树脂、13%煤沥青、12%粒径≤325目(≤0.44微米)的细石墨粉和25%呋喃树脂固化剂,所述细石墨粉的粒径≤325目,混匀,加热至75℃,备用;3、组装在四块石墨侧板的指接接口以及所述石墨侧板的外卡口与石墨底板的内卡口上涂抹所述粘接剂,将其中二块石墨侧板指接后与石墨底板卡接并粘合;将其余二块石墨侧板指接并与石墨底板卡接且粘合,同时完成四块石墨侧板指接;将等静压石墨销钉表面涂抹所述粘接剂后由上至下镶装在对应的石墨侧板销孔内;4、固化将组装好的方形石墨坩埚放到烘干炉内进行固化,起始固化,固化条件见表1;表1步骤温度(℃)时间(h)起始固化室温~1202保温1201升温120~1702保温17025、炭化固化后立即放在真空烧结炉中炭化,工艺条件见表2,炭化时通氮气进行保护,通气量15l/min,石墨方形坩埚制作完成;表2步骤温度(℃)时间(h)升温180~3504升温350~4506保温4501升温450~5506升温550~7506保温750±252制作石墨负极材料时,将石油焦(或天然石墨)装入所制石墨坩埚中,放入艾奇逊石墨化炉中,升温至2600-3000℃,降温,15天后取出,反复使用10炉后,石墨坩埚表面氧化,重新加工处理。实施例2如上所述生产石墨负极材料用方形石墨坩埚的加工方法,其步骤如下:1、组件制作利用石墨毛坯车削形状如上所述的石墨盖板3、石墨侧板1、石墨底板2和等静压石墨销钉5;2、配制粘接剂按照重量百分比取58%高温呋喃树脂、11%煤沥青、11%粒径≤325目的细石墨粉和20%呋喃树脂固化剂,混匀,加热至100℃,备用;3、组装在四块石墨侧板的指接接口以及所述石墨侧板的外卡口与石墨底板的内卡口上涂抹所述粘接剂,将其中二块石墨侧板指接后与石墨底板卡接并粘合;将其余二块石墨侧板指接并与石墨底板卡接且粘合,同时完成四块石墨侧板指接;将等静压石墨销钉表面涂抹所述粘接剂后由上至下镶装在对应的石墨侧板销孔内;4、固化将组装好的方形石墨坩埚放到烘干炉内进行固化,固化条件见表3;表3步骤温度(℃)时间(h)起始固化室温~1402保温1401升温140~2002保温20025、炭化固化后在真空烧结炉中炭化,固化工艺条件见表2,炭化时通氮气进行保护,通气量20l/min,方形石墨坩埚制作完成。制作石墨负极材料时,将石油焦(或天然石墨)装入所制石墨坩埚中,放入艾奇逊石墨化炉中,升温至2600-3000℃,降温,15天后取出,重复使用12炉后表面氧化,重新加工处理。实施例3如图所示,如上所述生产石墨负极材料用方形石墨坩埚的加工方法,其步骤如下:1、组件制作利用石墨毛坯加工形状如上所述的石墨盖板3、石墨侧板1、石墨底板2和等静压石墨销钉5;2、配制粘接剂按照重量百分比取55%高温呋喃树脂、12%煤沥青、12%粒径≤325目的细石墨粉和21%呋喃树脂固化剂,混匀,加热至85℃,备用;3、组装在四块石墨侧板的指接接口以及所述石墨侧板的外卡口与石墨底板的内卡口上涂抹所述粘接剂,将其中二块石墨侧板指接后与石墨底板卡接并粘合;将其余二块石墨侧板指接并与石墨底板卡接且粘合,同时完成四块石墨侧板指接;将等静压石墨销钉表面涂抹所述粘接剂后由上至下镶装在对应的石墨侧板销孔内;4、固化将组装好的方形石墨坩埚放到烘干炉内进行固化,固化条件见表4;表4步骤温度,℃时间,h起始固化室温~1302保温1301升温1802保温18025、炭化固化后在真空烧结炉中炭化,工艺条件见表2,炭化时通氮气进行保护,通气量18l/min,石墨方形坩埚制作完成。制作石墨负极材料时,将天然石墨装入石墨坩埚中,放入艾奇逊石墨化炉中,升温至2600-3000℃,降温,15天后取出,重复使用15炉后,石墨坩埚表面氧化,重新加工处理。以上仅为本发明的具体实施例而已,并不用于限制本发明,对于本领域的技术人员来说,本发明可以有各种更改和变化。凡在本发明的精神和原则之内,所作的任何修改、等同替换、改进等,均应包含在本发明的保护范围之内。当前第1页12