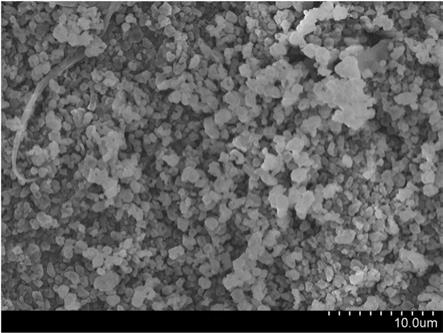
1.本发明涉及氮化铝材料技术领域,具体涉及一种氮化铝粉体及其制备方法。
背景技术:2.氮化铝自从1862年首次被合成以来,由于其具有优越的综合性能,世界上许多国家都对其开展了大量的研究开发和应用。氮化铝陶瓷的应用领域十分广泛,除了在电子工业可以作为理想的电子绝缘基板和大功率led封装材料外,在船舶与海洋工程领域的应用也日益得到关注。例如氮化铝陶瓷可以作为船用燃气轮机的热交换器材料和内燃机的耐热部件,氮化铝纳米粉体可以作为润滑油添加剂,改善摩擦部件的摩擦磨损情况,并对磨损部位具有良好的自修复功能。
3.目前氮化铝每年的需求量在不断增加,但其商品化应用程度还比较低,主要是由于原材料氮化铝粉末的纯度、粒度不达标,粉末难于烧结。
4.目前氮化铝的制备方法主要为直接氮化法和碳热还原法两种。采用直接氮化法制备氮化铝粉末具有设备和工艺简单、原料来源丰富、生产成本低廉等特点。但是直接氮化法在反应时会在铝表面形成氮化层,防止氮向内部扩散,导致铝的氮化程度较低。另一种方法为碳热还原法,这种方法制备的氮化铝粉末品质优良、粒度分布均匀、纯度高、具有优异的烧结性能。但是在烧结过程中所需的能耗较高,不易反应。专利cn200610085434.1中提供了一种抗水化易分散的氮化铝粉,主要利用表面修复技术对氮化铝粉末表面进行处理,防止氮化铝粉末在潮湿环境中水解,提高其抗水解能力。首先把氮化铝粉末与有机羧酸在有机溶剂进行搅拌,使得氮化铝粉末表面吸附一层有机羧酸,再加入非离子型表面活性剂,于60
‑
80℃水浴搅拌加热几小时,用乙醇溶液多次清洗,再将清洗后的氮化铝粉末在80
‑
100℃烘干。专利 cn201380046086.5提供了一种耐水性氮化铝粉末的制备方法,其为通过对氮化铝表面颗粒进行处理从而制备出耐水性的氮化铝粉末。其方法是使得颗粒表面存有氧化钇的氮化铝粉末与酸溶液进行接触,然后使氮化铝粉末与磷酸化合物进行接触,最后对氮化铝粉末进行过滤、水洗、干燥处理,从而制得具有耐水性的氮化铝粉末。专利cn200510024935.4提供了一种防止氮化铝水解的方法,利用表面处理技术来防止氮化铝在潮湿的环境中水解,首先把氮化铝粉末在四乙氧基硅烷溶液中进行浸泡处理,然后将经过浸泡处理的氮化铝粉末用乙醇溶液进行多次处理,再将清洗后的氮化铝粉末烘干即可。然而,上述方法制备的氮化铝在抗水解和抗氧化性能方面仍不理想,因此,研究一种能耗低、粒度好且兼具抗水解和抗氧化性能的氮化铝制备方法具有重要的意义。
技术实现要素:5.本发明的目的就是提供一种氮化铝粉体及其制备方法,以解决现有技术制备的氮化铝粒径较大、能耗高且抗水解和抗氧化性能不理想的问题。
6.本发明的目的是通过以下技术方案实现的:一种氮化铝粉体,所述氮化铝粉体的化学式为aln;该粉体通过以下方法制备得到:
7.a、称取al2o3和单晶糖,所述al2o3与单晶糖的质量比为0.05~0.1∶1;
8.b、将称量的单晶糖和al2o3加到纯净水中,然后搅拌混合3~4h;
9.c、将混合均匀的原料装到托盘中,并置于干燥箱内;然后按以下设定的加热程序进行处理:第一段加热温度为t1,保温时间为t1;第二段加热温度为t2,保温时间为t2;第三段加热温度为t3,保温时间为t3;第四段加热温度为t4,保温时间为t4;第五段加热温度为 t5,保温时间为t5;其中,80℃≤t1≤100℃,15h≤t1≤20h;100℃≤t2≤150℃,3h≤t2 ≤5h;150℃≤t3≤180℃,15h≤t3≤20h;180℃≤t4≤200℃,15h≤t4≤20h;200℃≤t5≤ 220℃,15h≤t5≤20h;
10.d、将经步骤c加热后的原料在氢气与氮气混合气氛条件下,经15~20h升温至 1000~1500℃,并保温反应8~10h;
11.e、反应完成后,将反应产物放入反应炉中进行烧结,在温度520~580℃,空气流量 2~4l/min条件下反应18~22h;
12.f、将反应得到的产物用混合溶液进行浸渍处理,所述混合溶液为盐酸与对苯二甲酸乙二醇酯或乙酸乙酯的混合物,浸渍搅拌时间为3~5h,然后静置1.5~2.5h,最后将产物干燥后即得到表面修饰的氮化铝粉体。
13.步骤a中,al2o3原料纯度为99.99%以上,d50在1μm以下。
14.步骤a中,所述单晶糖为c6(h2o)6。
15.步骤d中,氢气与氮气混合气氛中,氮气占气体总体积的75%~85%,气体总流量为3~5m 3
/h。
16.步骤f中,盐酸与对苯二甲酸乙二醇酯或乙酸乙酯的质量比为0.2~0.7∶1,盐酸浓度为 10%~50%;所述干燥为在75~85℃条件下干燥4~6h。
17.一种氮化铝粉体的制备方法,包括如下步骤:
18.a、称取al2o3和单晶糖,所述al2o3与单晶糖的质量比为0.05~0.1∶1;
19.b、将称量的单晶糖和al2o3加到纯净水中,然后搅拌混合3~4h;
20.c、将混合均匀的原料装到托盘中,并置于干燥箱内;然后按以下设定的加热程序进行处理:第一段加热温度为t1,保温时间为t1;第二段加热温度为t2,保温时间为t2;第三段加热温度为t3,保温时间为t3;第四段加热温度为t4,保温时间为t4;第五段加热温度为 t5,保温时间为t5;其中,80℃≤t1≤100℃,15h≤t1≤20h;100℃≤t2≤150℃,3h≤t2 ≤5h;150℃≤t3≤180℃,15h≤t3≤20h;180℃≤t4≤200℃,15h≤t4≤20h;200℃≤t5≤ 220℃,15h≤t5≤20h;
21.d、将经步骤c加热后的原料在氢气与氮气混合气氛条件下,经15~20h升温至 1000~1500℃,并保温反应8~10h;
22.e、反应完成后,将反应产物放入反应炉中进行烧结,在温度520~580℃,空气流量 2~4l/min条件下反应18~22h;
23.f、将反应得到的产物用混合溶液进行浸渍处理,所述混合溶液为盐酸与对苯二甲酸乙二醇酯或乙酸乙酯的混合物,浸渍搅拌时间为3~5h,然后静置1.5~2.5h,最后将产物干燥后即得到表面修饰的氮化铝粉体。
24.步骤a中,al2o3原料纯度为99.99%以上,d50在1μm以下。
25.步骤a中,所述单晶糖为c6(h2o)6。
26.步骤d中,氢气与氮气混合气氛中,氮气占气体总体积的75%~85%,气体总流量为3~5m 3
/h。
27.步骤f中,盐酸与对苯二甲酸乙二醇酯或乙酸乙酯的质量比为0.2~0.7∶1,盐酸浓度为 10%~50%;所述干燥为在75~85℃条件下干燥4~6h。
28.有益效果:
29.本发明制备氮化铝的方法不同于传统的直接氮化法和碳热还原法,其采用单晶糖作为碳源,并将单晶糖和氧化铝按照特定比例配成混合溶液,按特定的加热程序进行处理,制得初始的碳化铝,再对产物进行氮化处理得到氮化铝。通过本方法制得的氮化铝相比于直接氮化法和传统的以碳粉为碳源的碳热还原法,制得的氮化铝粒径更小,孔隙疏松,并且粒径的分布更加均匀,更易反应处理。将制得的氮化铝置于特定混合溶液中浸渍,对其进行表面处理,使其具有优异的耐水解和抗氧化特性。
30.本发明所采用的方法相比较之前的两种方法所需的能耗较低,同时粒度也较为稳定,兼具二者的长处。同时经过表面处理,使得产品具有优异的抗水解性能和抗氧化性能,从而具有更好的应用价值。
附图说明
31.图1是实施例1的氮化铝粉体的sem图。
32.图2是实施例1的氮化铝粉体的xrd图谱。
33.图3是氮化铝粉体的ph随时间变化曲线(室温25℃下)(其中,a:实施例1原始粉末, b:实施例1处理粉末,c:参比例1原始粉末,d:参比例1处理粉末)。
34.图4是实施例1的氮化铝粉体的显微图(400倍显微镜)。
具体实施方式
35.下面以具体实施例详细描述本发明的技术方案。
36.参比例1:根据专利cn200610085434.1的实施例1进行重复性实验
37.把85g氮化铝粉末和10g硬脂酸浸泡在100ml乙醇溶液中,并不停的搅拌4h,然后静置 1~2h。在上述混合物中添加5g吐温80,于60℃水浴搅拌加热5h;将混合物过滤,过滤出的氮化铝粉末用乙醇溶液清洗三次。将清洗后的氮化铝粉末80℃下烘干5h,即可获得抗水性效果突出的氮化铝粉。
38.实施例1
39.称取150g氧化铝粉末,同时称取1.76kg单晶糖c6(h2o)6。将二者加入到3.3kg蒸馏水中充分混合。将搅拌好的反应原料装到托盘里面,设定加热温度和保温时间曲线。第一段加热温度设定为90℃,保温时间为18h。第二段加热温度为125℃,保温时间为4h。第三段加热温度为170℃,保温时间为17h。第四段加热温度为190℃,保温时间为17h。第五段加热温度为210℃,保温时间为17h。将经加热处理后的原料进到反应炉里进行烧结,气氛为20%的氢气与80%的氮气。气体流量为4m3/h。经过17h反应温度升到1250℃,保持反应温度9h。将反应完毕的产品进行脱碳处理,脱去反应中未反应完全的碳。脱碳处理为将产品放入反应炉进行烧结,反应温度为550℃,空气流量为3l/min,反应20h。将反应得到的氮化铝粉末加入到10wt%盐酸和对苯二甲酸乙二醇酯(质量比k1为0.5)的混合溶液中,不停搅拌4h,然后
静置2h。浸渍完全后,将产品在80℃的条件下烘干5h,即得到表面修饰的氮化铝粉体。对所得产物进行表征,结果见图1
‑
图4所示。由图2实施例1的xrd衍射图谱可知,所制备的粉末为纯相的aln粉末。由图3可知,经处理的粉体ph值均随时间变化程度减小,说明处理后粉体具有更佳的抗水性能,但实施例1粉体处理前后的ph值变化均比参比例1的变化程度小,说明实施例1粉体具有更佳的抗水性能。
40.测试所得产物的抗水解性能,结果见表1所示。表1所示为抗水化处理粉末在水中浸泡 48h之后,粉末中的氮含量。水解效果的表示方式为在水中浸泡48h前后粉末中氮含量的差值与浸泡之前粉末中氮含量的百分比。
41.实施例2~6
42.改变盐酸和对苯二甲酸乙二醇酯的质量比k1(具体参见表1),其他工艺操作同实施例1,测试所得产物的抗水解性能,结果见表1所示。
43.表1:
[0044][0045]
由表1可得出,本发明相比于参比专利cn200610085434.1,有效地提高了氮化铝粉末的抗水解能力。
[0046]
实施例7~12
[0047]
将对苯二甲酸乙二醇酯替换为乙酸乙酯,同时改变盐酸和乙酸乙酯的质量比k1(具体参见表2),其他工艺操作同实施例1,测试所得产物的抗水解性能,结果见表2所示。
[0048]
表2:
[0049][0050]
由表2可知,本发明能有效提高氮化铝粉末的抗水解能力。将表1和表2对比可得,当混合溶液组成为盐酸和对苯二甲酸乙二醇酯,k1=0.5时制得氮化铝粉末的抗水解性能最好。
[0051]
对实施例1和实施例10所制得的氮化铝粉末和参比例1制得的氮化铝粉末,以及对照样品(本发明未经过混合溶液浸渍处理的氮化铝样品)进行氧化实验测试。将氮化铝粉末置于空气环境480h。并测试其前后样品含氧量的变化情况,氧化效果表示为氧化处理前后样品含氧量的差值与处理前氧含量的比例,如表3所示。
[0052]
表3:
[0053][0054]
实施例13~19
[0055]
改变氮化时烧结温度,其他操作同实施例1,测试所得产物粒径,结果见表4所示。
[0056]
表4:
[0057]
实施例温度(℃)d50(μm)k=(d90
‑
d10)/d50)1310001.571.231411001.521.21512001.461.021613001.281.131714001.401.231815001.421.341916001.781.6
[0058]
如表4所示,在本发明温度范围内,所得产物的粒度较小,且较为均匀。