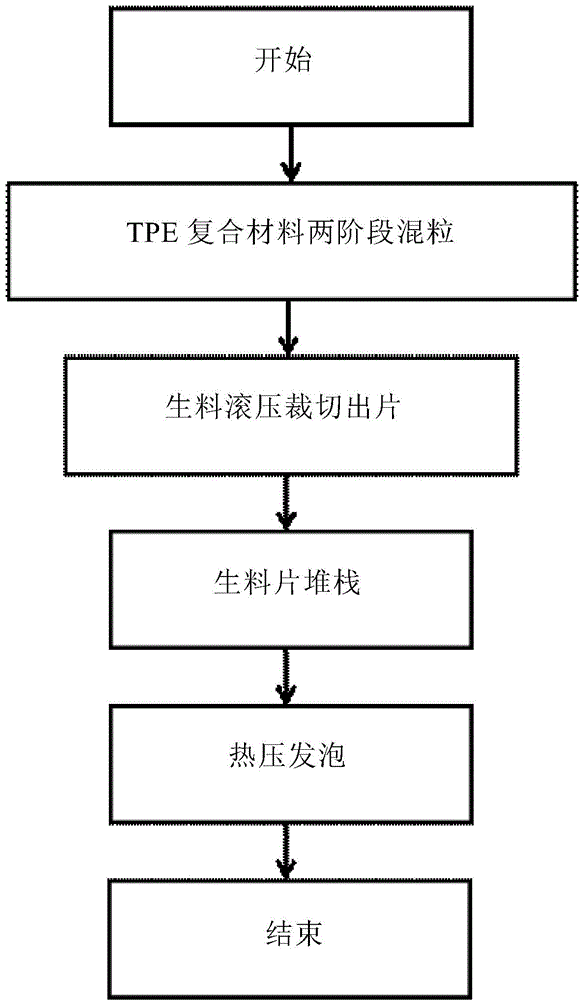
本发明是关于一种多层热塑性弹性体(TPE)发泡材料及其制造方法,特别是指一种发泡后即为多层结构的TPE材料及其制造方法。
背景技术:
:当今的发泡材料主要包含塑料与橡胶两大类,其中塑料发泡材料,如聚氯乙烯(polyvinylchloride,PVC)发泡材料、EVA发泡材料、EVA/聚乙烯(polyethylene,PE)发泡材料等,具有加工塑形容易、颜色美观的优点,但其亦具有弹性与止滑性差,及回收不易等缺点;而传统的橡胶发泡材料例如聚苯乙烯-丁二烯橡胶(styrene-butadienerubber,SBR)与氯丁橡胶(Chloroprenerubber)等,虽然具有弹性佳及止滑性佳的优点,其亦具有后加工及塑形不易、产品有异味、废料不易回收等缺点。反之,TPE发泡材料具有颜色亮白、弹性佳、止滑性佳、柔软、易于后加工且易于回收,实兼具塑料发泡材料与传统橡胶发泡材料的优点,且TPE为不具毒性的环保材料,所以由TPE制得的发泡材料已逐渐受到市场的重视。然而传统制程制得的TPE发泡材料,无法直接制得多层结构,而需藉由接着剂及/或中间网布层的使用,才能制得层与层间黏着力尚可的多层材料。有鉴于此,美国第2009/0286893号专利公开案揭示一种经改良的多层TPE发泡材料的制造方法,其藉由分别形成各层TPE发泡层后,再利用TPE薄膜中间层及热压合方式将各层结合而获得多层TPE发泡材料。然而于该制程中,各层是分别形成再经热压合,程序仍嫌繁琐。鉴于上述问题,仍有待发展一种更简便的多层TPE发泡材料制造方法。技术实现要素:本发明的第一目的在于提供一种多层热塑性弹性体发泡材料,其可藉由将包含特定成分比例的TPE弹性体生料组合物发泡而制得。本发明的多层热塑性弹性体,其层与层之间无需有接着层或中间层,即可达 0.5kgf/25mm以上,甚至1.0kgf/25mm以上的剥离强度,且本发明的多层热塑性弹性体无论硬度、密度、抗拉强度及延伸率等机械性质均可符合商业应用的要求。本发明的第二目的在于提供一种形成多层热塑性弹性体发泡材料的方法,其包含下列步骤:a)提供热塑性弹性体基质、交联剂、发泡剂及其他添加剂,以捏合机将其逐渐加热至熔融状态并均匀混合,使其形成生料混合物;b)将a)获得的该生料混合物送入第一混合机台翻搅,待其散热冷却至70至110℃的温度后,再送入第二混合机台,以形成生料薄带,并将所得的生料薄带裁切成生料薄片;c)将不同的生料薄片堆叠成多层生料薄片堆;及d)将c)所得的多层生料薄片堆直接发泡并待其冷却,即可获得多层热塑性弹性体发泡材料。藉由本发明的形成多层热塑性弹性体发泡材料的方法,可无须经热压合,即于单一发泡步骤中直接制得多层热塑性弹性体材料。本发明的另一目的,是提供由上述方法获得的多层发泡热塑性弹性体发泡材料。附图说明图1为本发明的多层热塑性弹性体发泡材料的示意图,其上层与下层间是直接接合而无网布层或胶层存在。图2为本发明的形成多层热塑性弹性体发泡材料的方法流程图。具体实施方式本发明的第一目的在于提供一种多层热塑性弹性体发泡材料,其可藉由将包含特定成分比例的TPE弹性体生料组合物发泡而制得。具体而言,本发明的多层热塑性弹性体发泡材料是藉由将包含特定种类及比例的基质(即「主胶」)、交联剂(架桥剂)及发泡剂的TPE弹性体的生料组合物发泡而制得。于该生料组合物中,可视需要加入其他功能性添加剂,例如发泡辅剂、交联辅剂、软化剂及/或填料等。其中的热塑性弹性体基质是以软嵌段的苯乙烯-丁二烯-苯乙烯(SBS)、苯乙烯-乙烯/丁烯-苯乙烯(SEBS)、苯乙烯-异戊二烯-苯乙烯(SIS)及苯乙烯-乙烯-丙烯-苯乙烯(SEPS)、聚丁二烯(Polybutadiene)、马来酸酐接枝苯乙烯-乙烯/丁烯-苯乙烯(Maleic anhydride-graftedSEBS)等热塑性弹性体为主,但亦可使用其他种类的热塑性弹性体。优选的软嵌段热塑性弹性体基质为SBS、SEBS、SIS及聚丁二烯。上述软嵌段主胶的种类可依欲获得材料的性质单独使用或并用。若采用复数主胶种类,其种类间的比例亦可依需求调整。主胶的总重应占总热塑性弹性体基质的5重量%至95重量%,优选占总热塑性弹性体基质的50重量%至95重量%。除软嵌段主胶外,热塑性弹性体基质尚应包含可提供刚性的硬嵌段热塑性弹性体基质,例如(但不限于)聚苯乙烯(PS)及聚伸苯基氧化物(polyphenyleneoxide,PPO)等。硬嵌段基质的总重应占总热塑性弹性体基质的5重量%至95重量%,优选为5重量%至50重量%。亦可视情况添加其他聚合物基质,以调整材料的性质。该其他聚合物基质可选自例如(但不限于)低密度聚乙烯(LDPE)、高密度聚乙烯(HDPE)、乙烯-醋酸乙烯(EVA)、聚丙烯(PP)、热塑性聚胺基甲酸酯(TPU)、丙烯腈-丁二烯-苯乙烯共聚物(ABS)、丙烯腈-苯乙烯共聚物(AS)、奈纶(Nylon)、聚烯烃弹性体(polyolefinelastomer,POE)及其混合物所组成之群等,其含量以不超过总基质的50重量%为原则。本发明的交联剂为过氧化二异丙苯(dicumylperoxide,DCP)或双叔丁基过氧异丙基苯(bis(t-butylperoxyisopropy)benzene,BIPB),其含量与总基质含量的重量比应为0.01∶100至1.5∶100,优选为0.02∶100至1∶100。本发明的发泡剂是选自偶氮二甲酰胺(Azodicarbonamide,AC)、4,4’-氧代双苯磺酰肼(4,4′-Oxybis(benzenesulfonylhydrazide),OBSH)、对甲苯磺酰肼(P-Toluenesulfonhydrazide,TSH)所组成之群,其含量与总基质含量的重量比应为1∶100至20∶100,优选为2∶100至15∶100。除上述基质、交联剂及发泡剂外,本发明的生料组合物可视需要加入发泡辅剂、交联辅剂、软化剂、填料及其他功能性添加剂。适用于本发明的发泡辅剂可为例如(但不限于)氧化锌(ZnO)、硬脂酸锌(zincstearate,ZnSt)、尿素(urea)、水杨酸、硬脂酸铅(lead(II)stearate,PbSt)或其组合物,其含量可为发泡剂使用量的20%至100%。适用于本发明的交联辅剂可为例如(但不限于)三芳基氰脲酸酯(Triarylcyanurate,TAC)、三烃甲基丙烷三甲基丙酸酯(Trimethylolpropanetrimethacrylate,TRIM)、对苯二甲酸二烯丙酯(Diarylterephthalate,DATP),优选为三芳基氰脲酸酯,且其含量可为交联剂使用量的20%至50%。适用于本发明的软化剂可为例如(但不限于)白矿油(whitemineraloil)或环烷油(naphthenicoil),较佳为环烷油。适用于本发明的填料则可选自(但不限于)碳酸钙或滑石等,较佳为碳酸钙。填料的含量与基质总重的比例以不超过40∶100为宜。亦可视情况及需求加入其他功能性添加剂,例如防滑剂、抗静电剂、抗氧化剂、紫外线(UV)吸收剂、颜料等。该等添加剂的含量无特殊限制。一般而言,该等添加剂的含量与基质总重的比例不超过5∶100,优选为不超过3∶100。以上述生料组合物发泡而成的热塑性弹性体材料可具有良好的物理性质,故可直接将该生料组合物挤制、裁切成特定大小的生料薄片后将其堆叠,再直接将其发泡,即可于无须使用接着层或中间层的情况下,制得多层热塑性弹性体发泡材料。特定而言,以上述生料组合物直接发泡而成的多层热塑性弹性体发泡材料可具有约130kg/m3的密度,甚至达30kg/m3的高发泡密度,大于2kgf/m3,甚至大于4kgf/m3的抗拉强度(根据ASTMD412-06a,DieC)、大于50%,甚至大于100%或115%的延伸率(根据ASTMD412-06a,DieC),尤其是其层与层之间的剥离强度可达0.5kgf/25mm以上,甚至lkgf/25mm以上(样品:Lxw=200mmx25mm,于拉力机以200mm/min的速度进行剥离测试并纪录剥离前的最大承受强度)。本发明的多层热塑性弹性体发泡材料的各层可具有相同或不同特性,例如可将添有不同颜料但其他原料完全相同的生料薄片堆叠后直接发泡,以制得性质均一但具有多色的多层热塑性弹性体发泡材料;或可将含有较多发泡剂的生料薄片堆叠于含有较少发泡剂的生料薄片上并发泡,以形成上软下硬的多层热塑性弹性体发泡材料。本发明的另一目的是提供一种形成多层热塑性弹性体发泡材料的方法,其包含下列步骤:a)提供热塑性弹性体基质、交联剂、发泡剂及其他添加剂,以捏合机将其逐渐加热至熔融状态并均匀混合,以形成生料混合物;b)将a)获得的该生料混合物送入第一混合机台翻搅,使其散热冷却至70至110℃的温度,再送入第二混合机台,以形成生料薄带,并将所得的生料薄带裁切成生料薄片;c)将不同的生料薄片堆叠成多层生料薄片堆;及d)将c)所得的多层生料薄片堆直接发泡并待其冷却,以获得多层热塑性弹性体发泡材料。针对a)至d)各步骤详述如下:步骤a):捏合本发明的生料混合物中所包含的各成分已如前所述。可于单一阶段加入全部成分并进行加热及捏合,而获得堪用的生料混合物。然而,如欲获得良好的多层热塑性弹性体发泡材料时,最好是采用含以下步骤a1)及a2)的多阶段捏合方式:a1):将热塑性弹性体基质、聚合物基质(若采用时)、发泡辅剂与其他添加剂(例如软化油、填料等)送入捏合机,均匀混合并加热至熔融阶段(视基质种类而定,一般约为150℃至180℃)后再冷却并造粒,以获得热塑性弹性体基质颗粒;及a2):将a1)所获得的该热塑性弹性体基质颗粒送入捏合机中,待温度到达90℃至120℃后再加入发泡剂、交联剂及交联辅剂,继续捏合直至均匀分散为止。采用上述多阶段捏合方式的理由在于:第一阶段捏合的目的是将热塑性弹性体基质、聚合物基质及其他添加剂均匀混合,但是此时温度较高,故于温度较低的第二阶段始加入发泡剂、交联剂及交联辅剂,以维持其反应性。步骤b):压片及裁切本发明的方法中是采用二阶段的压片方式,其第一阶段是将步骤a)所获得的膏状生料混合物送入混合机台并进行翻搅,使其得以散热冷却至70至110℃的温度,以避免聚合反应所生的内热对交联剂产生作用。接着将生料组合物送入第二混合机台,使其压制成厚度及宽度均一的生料薄带。待生料薄带冷却后,依照所需长度将其切割成固定长度的生料薄片。可以任何习知的方式进行切割。步骤c)堆叠依据需求将不同的生料薄片(例如主成分比例不同的生料薄片,或主成分比例相同但颜色不同的生料薄片)依序堆叠,以形成生料薄片堆。步骤d)发泡将步骤c)所获得的生料薄片堆直接放入油压机的模具中并施以一定的温度与压力,以进行多层发泡。可使用传统进行EVA发泡的发泡机。优选的发泡条件为150℃至180℃的温度、120kg/m3至200kg/m3的压力及10分钟至60分钟的时间。将经发泡的薄片堆于常温下静置一段时间,以进行冷却。冷却所需时间依材料厚度而有所不同,一般是介于为20至60分钟之间。待经发泡的薄片堆冷却后,即可获得本发明的多层热塑性弹性体发泡材料。实例以下藉由实例详细说明本发明及其功效,但是该等实例仅为进一步具体说明本发明之用,无限制本发明范畴之意。对于熟习此项技术者为明显的任何修改或更改,均属于 本说明书的揭示内容范畴。实例1:将40份的SBS(LCY475)、30份SIS(Shell,KratonD1117)、25份聚丁二烯(TSRC,TaipolBR0150)、5份POE(DowChemical,EngageEG8150)、15份PS、10份PP、50份碳酸钙、20份环烷油以及1.5份ZnSt置于捏合机,逐渐加热至160度以进行第一阶段捏合,使上述成分得以均匀混合,再以抽粒机冷却造粒后备用。将所得热塑性弹性体基质颗粒、7.5份发泡剂AC、0.25份交联剂BIPB以及0.075份交联辅剂TAC(TCITokyoChemicalIndustryCo.,Ltd)置于捏合机中,逐渐加温至100℃以进行第二阶段捏合而获得生料组合物。生料组合物送入第一台双滚轮机,散热至80℃,再送入第二台双滚轮机中裁切成640mm*990mm*0.5mm的生料薄片。将两片生料薄片推迭成的生料薄片堆置于发泡机中,于170℃的温度、150kg/m3的压力条件下热压发泡20分钟,最后于常温静置20分钟。实例2:同实例1,仅以OBSH取代AC。实例3:同实例1,仅以马来酸酐接枝SEBS(ShellChemical,FG1901)取代部分SBS,以ABS取代PP。比较例1:将30份的SBS(LCY475)、30份SIS(Shell,KratonD1117)、10份马来酸酐接枝SEBS(ShellChemical,FG1901)、25份聚丁二烯(TSRC,TaipolBR0150)、5份POE(DowChemical,EngageEG8150)、15份PMMA、10份PET、50份碳酸钙、20份环烷油及1.5份ZnSt置于捏合机逐渐加热至160度均匀混合,再以抽粒机冷却造粒后备用。将所得热塑性弹性体基质颗粒、7.5份发泡剂AC、0.25份交联剂BIPB以及0.075份交联辅剂TAC(TCITokyoChemicalIndustryCo.,Ltd)在捏合机中混合并逐渐加温至140℃以获得生料。生料送入第一台双滚轮机台散热至80℃,再送入第二台双滚轮机中裁切成640mm*990mm*0.5mm的生料薄片。将两片生料薄片推迭成的生料片,置于发泡机中,并于170℃的温度及150kg/m3的压力下试图进行发泡20分钟,但无法获得热塑性弹性体发泡材料。实例5:机械性质测试对前述各实例进行硬度、密度、抗拉强度、延伸率及剥离强度测试,结果如下:实例1实例2实例3比较例1SBS40403030马来酸酐接枝SEBS--1010SIS30303030聚丁二酸25252525POE5555PS151515-PP1010--ABS--10-PMMA---15PET---10碳酸钙50505050环烷油20201620ZnSt1.51.51.51.5AC7.5-7.57.5OBSH-7.5--BIPB0.250.250.250.25TAC0.0750.0750.0750.075硬度*292512**密度*(kg/m3)132136130**抗拉强度*(kgf/m2)5.346.855.20**延伸率*(%)155124180**剥离强度*(kgf/25mm)1.541.491.85***各性质的测试方式如下:硬度:ASTMD2240-05;密度:ASTMD1056-07;抗拉强度:ASTMD412-06a,DieC;延伸率:ASTMD412-06a,DieC;剥离强度:样品Lxw=200mmx25mm,于拉力机以200mm/min的速度进行剥离测试,并纪录其剥离前的最大承受强度。**因无法形成发泡材料,无法进行测试。当前第1页1 2 3