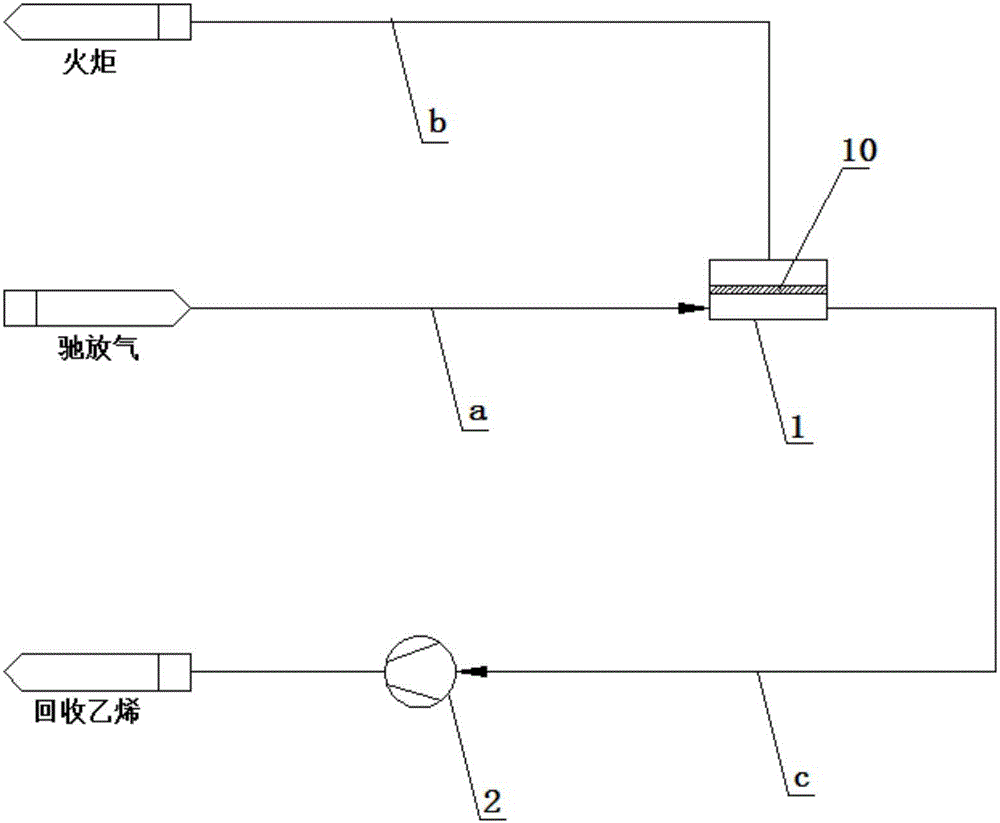
本发明涉及乙烯回收
技术领域:
,具体涉及一种在乙烯衍生物生产过程驰放气中乙烯的回收方法。
背景技术:
:在乙烯衍生物生产过程中,特别是乙烯氧化法生产环氧乙烷、乙醛、醋酸乙烯的生产过程,由原料氧气和催化剂带入的氩气、氮气,以及反应副产物二氧化碳等惰性气体会随着反应循环而不断累积,影响催化剂活性和反应进程,因此生产过程中需要排放一部分循环气。以环氧乙烷生产过程为例,驰放气主要成分包括乙烯、甲烷、乙烷、氧气、氩气、二氧化碳、氮气等,其中乙烯约占25~35%(V)。一个规模20万吨/年的环氧乙烷装置,驰放气量约280Nm3/hr,年损失乙烯700多吨,造成资源的极大浪费。因此,对乙烯衍生物生产过程驰放气中的乙烯进行回收具有极高的经济价值。目前,从驰放气中回收乙烯的方法主要采用膜分离和变压吸附技术。现有的膜分离工艺是利用分离膜对乙烯的优先渗透特性,实现其与氩气、氮气的分离,膜材料一般为橡胶态的高分子材料。该过程中,乙烯在膜的低压渗透侧富集,需要增设较大功率压缩机才能循环回收;而且,由于二氧化碳的渗透速率快,会随乙烯一同透过膜,还需要增设二氧化碳处理装置对渗透气进行二次分离,操作过程复杂,导致乙烯回收系统的投资和运行成本增加。而变压吸附技术是在高压时吸附剂选择性的吸附乙烯,减压过程脱附乙烯,从而得到低压的富乙烯气,同样需要消耗较大的压缩功。技术实现要素:鉴于现有技术存在的上述问题,本发明旨在提供一种工艺流程简单、投资成本低、能耗低的,从乙烯衍生物生产过程驰放气中回收乙烯的方法。通过采用优先渗透氩气、氮气和二氧化碳的分离膜,将乙烯在高压截留侧富集,实现循环回收。本发明的技术方案如下:一种乙烯衍生物生产过程驰放气中乙烯的回收方法,包括膜分离过程,所述膜分离过程中,驰放气进入内置分离膜的膜分离器分为渗透气和截留气,所述渗透气富含氩气、氮气和二氧化碳,所述截留气富含乙烯。进一步地,在上述技术方案中,所述分离膜为基膜和有效分离层构成的复合膜,所述的有效分离层的材料为全氟聚合物、聚酰亚胺、聚芳酰胺、自聚微孔高分子中的一种或几种。进一步地,在上述技术方案中,所述全氟聚合物为全氟间二氧杂环戊烯或环烷基醚的均聚物或它们与四氟乙烯的共聚物。例如科慕公司的AF系列,苏威公司的AD系列,以及AsahiGlass的进一步地,在上述技术方案中,所述分离膜的乙烯/氩气分离系数大于4进一步地,在上述技术方案中,所述分离膜的有效分离层的厚度为0.1-1μm,优先0.1-0.5μm。进一步地,在上述技术方案中,所述截留气直接或经循环压缩机升压后回收利用。进一步地,在上述技术方案中,所述渗透气经火炬排放或者作为燃料气使用。进一步地,在上述技术方案中,所述的驰放气中乙烯含量为20~80%,氩气含量为3~12%,氮气含量为2~10%,二氧化碳含量为1~15%,其余组分含量为5~60%。在本发明中所述的分离膜,可以采用将有效分离层的材料制备成溶液后,浸涂于多孔的聚合物基膜上并加热干燥的常规方法制备得到。一方面,有效分离层的材料为全氟聚合物时,全氟聚合物溶解于全氟溶剂后得到的溶液往往粘度很小,加上该溶液的表面张力小,溶液极易渗透进入基膜的膜孔深处,形成复合膜制作过程中需要避免的“孔渗”现象。该现象会造成基膜膜孔堵塞、气体渗透阻力大,同时复合在基膜表面上的分离层不完整,膜的选择性差等不利后果。针对该问题,本发明还提供作为本发明分离膜的全氟聚合物复合膜的制备方法,包括如下步骤:(1)基膜制备:将聚丙烯腈PAN,溶解于二甲基甲酰胺DMF中,配制成PAN含量为8~20wt.%的溶液,加入高分子添加剂,过滤、脱泡后流延在无纺布上,空气中挥发0~30秒后,浸入凝胶浴水中,流动水洗2天后,室温下晾干,得到PAN基膜;所述高分子添加剂包括聚乙烯吡咯烷酮PVP,聚乙二醇PEG中的一种或多种;高分子添加剂加入量为PAN重量的1/6~5/6倍;(2)分离层溶液配制:将全氟聚合物的颗粒溶解于全氟溶剂中配制成分离层溶液,浓度为0.5wt.%~3wt.%,然后静置脱泡1h~4h;(3)复合膜制备:在步骤(1)所得基膜上涂敷步骤(2)所得溶液,在室温下阴干20~240min;在40~120℃下加热5~240min得到未洗脱高分子添加剂的全氟聚合物复合膜;(4)高分子添加剂洗脱:将步骤3所得复合膜在50~90℃的去离子水中浸泡1~24h,晾干后得到全氟聚合物复合膜。上述方法制备得到的全氟聚合物复合膜,对氮气、氩气和二氧化碳具有很好的渗透性,而且选择性高,可以很好地截留乙烯,实现驰放气中回收乙烯的目的。本发明的有益效果:1)乙烯在膜高压截留侧富集,消耗很少的压缩功即可实现循环回收;2)可同时脱除驰放气中的氩气、氮气和二氧化碳,较现有技术减少脱二氧化碳过程;3)系统设备投资少、操作能耗低、占地面积小。附图说明图1是本发明回收方法的工艺流程示意图;图中,a、驰放气;b、渗透气;c、截留气;1、膜分离器;2、循环压缩机;10、分离膜。具体实施方式现结合附图与实施例,对本发明作进一步详细描述,可以使本领域的普通技术人员更全面地理解本发明,但不以任何方式限制本发明。文中所述的压力为表压。对照例1本对照例采用一种现有的环氧乙烷生产过程驰放气中乙烯的回收方法,其驰放气量为1030.34Kg/hr,压力为18.85Kg/cm2,温度为35.64℃,组成如下:组分N2ArO2CH4C2H4C2H6CO2EOH2OKg/hr40.04102.80112.34404.78348.74.1414.380.123.04驰放气中需要脱除的惰性气体量分别为:组分N2ArCO2Kg/hr40.04102.814.38该驰放气进入内置乙烯优先渗透分离膜(申请号为201010585792.5发明专利中制备的硅橡胶复合膜)的膜分离器,乙烯、二氧化碳等渗透速率快,优先透过膜在渗透侧富集,得到低压的渗透气;氩气、氮气等在膜的截留侧富集,得到压力略低于原料气的截留气。其中:渗透气量1808.20Kg/hr,压力1.5Kg/cm2,温度33℃,组成如下:组分N2ArO2CH4C2H4C2H6CO2EOH2OKg/hr34.64147.14160.79690.85725.768.6232.760.267.39该渗透气需要经过增压压缩机升压后返回环氧乙烷反应器,需要的压缩机功率约260Kw。截留气量696.91Kg/hr,压力17.8Kg/cm2,温度30℃,组成如下:组分N2ArO2CH4C2H4C2H6CO2EOH2OKg/hr62.71102.80112.35293.31122.051.452.200.040.01截留气排出的惰性气体量分别为:组分N2ArCO2Kg/hr62.71102.802.20从对照例可以看出,现有的膜回收过程可以在回收乙烯的同时,有效的脱除驰放气中的氩气、氮气,但二氧化碳的脱除量很小,也在渗透侧不断累积,因此渗透气还需要进一步分离二氧化碳,回收过程的复杂性增加。而且,渗透气为低压,为实现循环利用,需要的压缩能耗很高。实施例1本实施例公开了一种环氧乙烷生产过程驰放气中乙烯的回收方法,在图1所示的工艺流程示意图中,其驰放气a的工艺条件,如气量、压力、温度以及组成与对照例1一致。该驰放气a进入内置优先渗透氩气、氮气和二氧化碳等气体的分离膜10的膜分离器1,被分成两股气流:氩气、氮气和二氧化碳等优先透过膜10在渗透侧富集,成为渗透气b;乙烯等在截留侧富集,成为截留气c;所述分离膜为由基膜和全氟聚合物构成的分离膜,采用实施例3所述的方法制备得到。其中:渗透气b气量631.29Kg/hr,压力1.5Kg/cm2,温度33℃,进入火炬系统排放。其组成如下:组分N2ArO2CH4C2H4C2H6CO2EOH2OKg/hr40.17102.80148.69190.09122.041.3621.300.044.82渗透气b排出的惰性气体量分别为:组分N2ArCO2Kg/hr40.17102.8021.30截留气c气量1166.92Kg/hr,压力17.5Kg/cm2,温度32℃,经循环压缩机2升压后循环回收。其组成如下:组分N2ArO2CH4C2H4C2H6CO2EOH2OKg/hr29.7276.6147.38516.35486.545.873.800.180.49本实施例中,因二氧化碳也在渗透侧富集,可与氩气、氮气一同被脱除,相比对照例1节省了二氧化碳分离过程,简化了工艺流程。而且,由于乙烯在高压截留侧富集,仅需要功率约10Kw的小型压缩机即可实现循环回收,所需压缩功仅为对照例1的4%,大大降低了设备投资成本和运行能耗。实施例2本实施例公开了一种醋酸乙烯生产过程驰放气中乙烯的回收方法,在图1所示的工艺流程示意图中,其驰放气a气量为128Kg/hr,压力为6Kg/cm2,温度为38℃,组成如下:组分N2ArO2CH4C2H4C2H6CO2Kg/hr7.506.241.430.50107.641.742.95驰放气中需要脱除的惰性气体量分别为:组分N2ArCO2Kg/hr7.506.242.95该驰放气a进入内置优先渗透氩气、氮气和二氧化碳等气体的分离膜10的膜分离器1,被分成两股气流:氩气、氮气和二氧化碳等优先透过膜10在渗透侧富集,成为渗透气b;乙烯等在截留侧富集,成为截留气c;所述分离膜为由基膜和全氟聚合物构成的分离膜,采用实施例3所述的方法制备得到。其中:渗透气b气量58.77Kg/hr,压力1.5Kg/cm2,温度33℃,进入火炬系统排放。其组成如下:组分N2ArO2CH4C2H4C2H6CO2Kg/hr7.526.241.940.2437.680.574.59渗透气b排出的惰性气体量分别为:组分N2ArCO2Kg/hr7.526.244.59截留气c气量369.753Kg/hr,压力5Kg/cm2,温度30℃,经循环压缩机2升压后循环回收。其组成如下:组分N2ArO2CH4C2H4C2H6CO2Kg/hr17.5814.652.841.44322.705.275.27本实施例中,二氧化碳也与氩气、氮气一同被脱除,乙烯回收所需压缩功仅为5Kw。实施例3按照如下方法制备得到全氟聚合物复合膜:(1)将PAN和PVP(k-30)溶解于DMF中,配制成PAN含量为13wt.%、PVP含量为8wt.%的溶液,过滤、脱泡后流延在无纺布上,空气中挥发10秒后,浸入凝胶浴水中,流动水洗2天后,室温下晾干,得到PAN基膜;(2)分离层溶液配制:将AD60溶解于GaldenHT70中配制成分离层溶液,浓度为1wt.%,然后静置脱泡2h;(3)将步骤(1)的基膜上涂覆步骤(2)的溶液,在室温下阴干30min,在60℃下加热20min得到全氟聚合物复合膜;(4)将步骤3所得全氟聚合物复合膜在80℃的去离子水中浸泡24h,晾干后得到全氟聚合物复合膜。全氟聚合物复合膜对纯Ar和C2H4的渗透性能以及分离性能的测试结果为:JAr=105GPU,JC2H4=11.9GPU,α=8.82。实施例4按照如下方法制备得到全氟聚合物复合膜:(1)将PAN溶解于DMF中,配制成PAN含量为13wt.%的溶液,过滤、脱泡后流延在无纺布上,空气中挥发10秒后,浸入凝胶浴水中,流动水洗2天后,室温下晾干,得到PAN基膜;(2)分离层溶液配制:将AD60溶解于GaldenHT70中配制成分离层溶液,浓度为0.5wt.%,然后静置脱泡2h;(3)将步骤(1)的基膜浸渍于步骤(2)的溶液中,将膜从溶液中取出,在室温下阴干30min,在60℃下加热20min,得到全氟聚合物复合膜。该方法制备得到的全氟聚合物复合膜的纯Ar和C2H4的渗透性能以及分离性能的测试结果为:JAr=80.5GPU,JC2H4=12.98GPU,α=6.2。采用该分离膜,按照实施例1所述的方法对环氧乙烷生产过程驰放气中的乙烯进行回收,渗透气b以及截留气c中气量组成如下:渗透气b气量701.27Kg/hr,压力1.5Kg/cm2,温度33℃,进入火炬系统排放。其组成如下:组分N2ArO2CH4C2H4C2H6CO2EOH2OKg/hr40.07102.80161.35223.20144.531.6122.640.045.04渗透气b排出的惰性气体量分别为:组分N2ArCO2Kg/hr40.07102.8022.64截留气c气量1117.96Kg/hr,压力17.5Kg/cm2,温度32℃,经循环压缩机2升压后循环回收。其组成如下:组分N2ArO2CH4C2H4C2H6CO2EOH2OKg/hr30.6378.7137.01491.51471.165.702.750.170.33本实施例乙烯的损失量144.53kg/hr,高于实施例1中的122.04kg/hr。而且由于实施例1中膜的渗透性能较高,实施例1实际使用的膜面积较本实施例可以减少23%,可节约膜组件的投资。实施例5本实施例公开了一种环氧乙烷生产过程驰放气中乙烯的回收方法,在图1所示的工艺流程示意图中,其驰放气a的工艺条件,如气量、压力、温度以及组成与对照例1一致。该驰放气a进入内置分离膜10的膜分离器1,被分成两股气流:氩气、氮气和二氧化碳等优先透过膜10在渗透侧富集,成为渗透气b;乙烯等在截留侧富集,成为截留气c;所述分离膜为由聚酰亚胺材料制备的复合膜。其中:渗透气b气量662.17Kg/hr,压力1.5Kg/cm2,温度33℃,进入火炬系统排放。其组成如下:组分N2ArO2CH4C2H4C2H6CO2EOH2OKg/hr21.97102.80131.48193.13185.280.5421.950.044.97渗透气b排出的惰性气体量分别为:组分N2ArCO2Kg/hr21.97102.8021.95截留气c气量1032.82Kg/hr,压力17.5Kg/cm2,温度32℃,经循环压缩机2升压后循环回收。其组成如下:组分N2ArO2CH4C2H4C2H6CO2EOH2OKg/hr43.9066.3153.33472.77388.356.271.710.150.03本实施例中,在渗透侧脱除氩气和二氧化碳量可以满足原设计的要求,但氮气的脱除量小于原设计的要求,存在氮气浓度会累积升高的问题,同时乙烯的损失量185.28kg/hr,也要高于实施例1中的122.04kg/hr。从本发明所提供的对照例和实施例可见,本发明的方法相比现有技术可一步同时脱除驰放气中的氩气、氮气和二氧化碳,而且可显著降低乙烯的回收能耗,减少投资和运行成本。当前第1页1 2 3