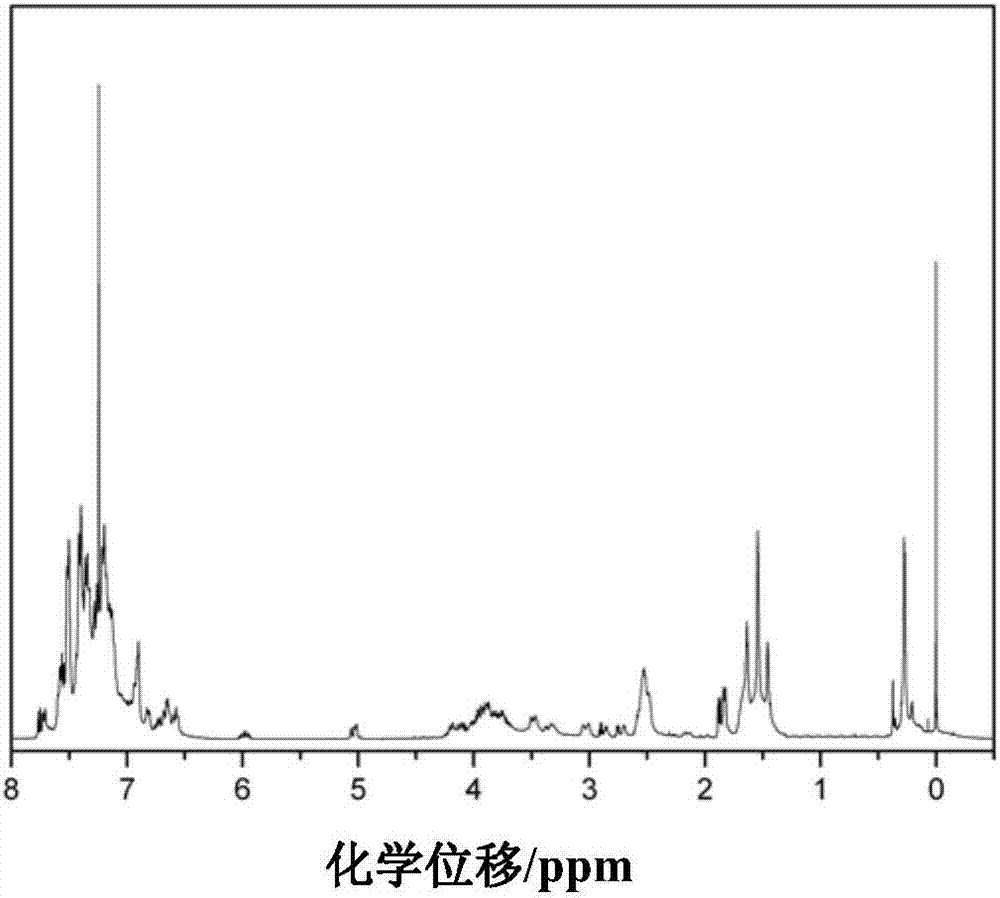
本发明涉及环氧树脂应用领域,具体涉及一种双层倍半硅氧烷环氧树脂改性剂及其制备方法和应用。
背景技术:
:环氧树脂具有优异的机械性能、电气性能和粘结性能而被广泛应用于结构复合材料、电子半导体封装、胶粘剂等领域。但是环氧树脂由于内应力大,本体比较脆,耐湿热性能较差,断裂韧性和冲击强度欠缺,很大程度上限制了其应用。因此对环氧树脂的增韧改性和耐湿热改性对环氧树脂的应用具有很重要的意义。针对环氧树脂的增韧问题,很多相关方法被开发出来。研究表明采用长链热塑性树脂、纳米粒子和有机硅化合物等进行增韧改性,效果明显。如公开号为cn104725782a的中国专利公开了一种纳米橡胶环氧树脂增韧剂的制备方法。该方法通过纳米橡胶粒子和其他助剂在预分散、细分散、浸润包覆和超声波处理等工艺后得到了一种粘度适中、易于分散的增韧改性剂。专利号为cn105906814a的中国专利采用了一种端环氧基团的聚醚作为环氧树脂的增韧剂。但是由于长链聚醚的存在,环氧树脂的玻璃化温度急剧降低,对其应用可能产生一定的影响。有机硅具有热稳定性好、耐候性、耐高低温性能良好、分子柔顺性好等优点,在环氧树脂中引入有机硅能很好的增韧环氧树脂并对其综合性能有所改善。如公开号为cn1560106a的中国专利公开了一种有机硅改性环氧树脂的制备方法,有效提高了环氧树脂的韧性和耐水性。但是由于该方法直接采用氯硅烷进行制备增韧剂,可能残余有机氯可能会对环氧封装胶的电气性能有一定的影响。且通常有机硅的玻璃化温度很低,引入有机硅可能会大大影响环氧树脂的玻璃化温度,从而对环氧树脂的应用范围产生影响。倍半硅氧烷是一种真正分子水平上的有机无机纳米杂化材料,其分子结构由si-o-si形成的主链和有机基团形成的侧链组成。目前,已有人报道采用倍半硅氧烷对环氧树脂进行改性,尤其以笼型倍半硅氧烷(poss)的研究较多。如公开号为cn102492116a的中国专利文献中公开了一种环氧树脂和多面体笼型倍半硅氧烷纳米杂化材料,该杂化材料是将γ-(2,3-环氧丙氧)丙基三甲氧基八笼型倍半硅氧烷作为纳米粒子添加到环氧树脂中,在固化剂作用下,八环氧基poss和环氧树脂发生交联反应,从而将八环氧基poss单体引入到环氧树脂结构中,形成了网络交联结构。制备得到的杂化材料表现出极低的介电常数和介电损耗值。但由于八环氧基poss的刚性结构,在提高杂化材料的耐热性能、机械性能的同时,往往会降低杂化材料的韧性。技术实现要素:本发明公开了一种双层倍半硅氧烷环氧树脂改性剂,将其应用于环氧树脂中,在不影响环氧树脂的玻璃化转变温度的同时,可以提高其韧性及耐湿热性能。具体技术方案如下:一种双层倍半硅氧烷环氧树脂改性剂,结构式如下式(ⅰ)或(ⅱ)所示:上式中,n选自1~20的整数,r选自相较于其它类型的倍半硅氧烷,本发明制备的双层倍半硅氧烷环氧树脂改性剂的环氧值为0.2~0.3mol/100g,其分子结构中具有多个环氧基团,可以有效的分散并反应到环氧树脂体系中;另一方面,结构中的双层倍半硅氧烷结构呈柔性特征,可以有效提高改性环氧树脂的韧性。本发明公开了上述的双层倍半硅氧烷环氧树脂改性剂的制备方法。当所述双层倍半硅氧烷环氧树脂改性剂的结构式如式(ⅰ)所示,制备方法包括如下步骤:以含氢双层倍半硅氧烷和烯丙基双酚a环氧树脂为原料,在催化剂作用下进行硅氢加成反应,再经后处理得到;当所述双层倍半硅氧烷环氧树脂改性剂的结构式如式(ⅱ)所示,制备方法包括如下步骤:以含氢双层倍半硅氧烷和烯丙基双酚a环氧树脂为原料,在催化剂作用下进行硅氢加成反应,向硅氢加成反应后的产物中加入含双键环氧化合物进行封端反应,再经后处理得到。作为优选,所述含氢双层倍半硅氧烷和烯丙基双酚a环氧树脂的质量比为1:0.5~2;所述的催化剂选自含铂催化剂,如氯铂酸、卡斯特催化剂、二氧化铂等;所述硅氢加成反应的温度为70~90℃,时间为12~24h。作为优选,所述的含双键环氧化合物选自烯丙基缩水甘油醚、丁香酚基缩水甘油醚等。作为优选,所述的后处理包括减压蒸馏。作为优选,所述含氢双层倍半硅氧烷的制备方法如下:a、将苯基三甲氧基硅烷、氢氧化钠、水混合,回流反应后,经过滤干燥得到中间产物;所述苯基三甲氧基硅烷、氢氧化钠和水的摩尔比为4:2:5;b、将步骤a得到的中间产物和三乙胺溶解在四氢呋喃溶剂中,降温至0℃以下,通氮气并加入甲基二氯硅烷,冰水浴反应后,再经后处理得到所述的含氢双层倍半硅氧烷;所述中间产物、三乙胺和甲基二氯硅烷的摩尔比为1:1:2。作为优选,所述烯丙基双酚a环氧树脂的制备工艺如下:将一定比例的环氧氯丙烷、烯丙基双酚a和苄基三乙基氯化铵混合后升温至60~80℃。干燥氮气保护下将氢氧化钠水溶液缓慢加入,而后反应1~5h,升温至100~120℃后将体系中的水分除去,而后降温至50~70℃,持续反应10~15h。将得到的产物用蒸馏水洗涤至中性,并蒸馏出过量的环氧氯丙烷,即得到所述的烯丙基双酚a环氧树脂。所述的环氧氯丙烷、烯丙基双酚a和苄基三乙基氯化铵的摩尔比为1:0.05~0.1:0.02~0.03。本发明公开了所述的双层倍半硅氧烷环氧树脂改性剂的应用,步骤如下:将环氧树脂、固化剂和所述的双层倍半硅氧烷环氧树脂改性剂分散在有机溶剂中,加热除去有机溶剂后,再进行固化处理。作为优选,所述的双层倍半硅氧烷环氧树脂改性剂,其n值选自1或2。经试验发现,当n值选自上述范围时,该改性剂可以有效分散在环氧树脂中,并且对环氧树脂的耐水性能、力学性能和韧性等都有明显改善。作为优选,所述的环氧树脂选自双酚a型环氧树脂、双酚f型环氧树脂、双酚s型环氧树脂中的至少一种;所述的固化剂选自4,4'-二氨基二苯基甲烷和/或3,3'-二氨基二苯基甲烷。与现有技术相比,本发明具有如下优点:本发明合成了一种新型的双层倍半硅氧烷环氧树脂改性剂,其分子结构中具有多个环氧基团,可以有效的分散并反应到环氧树脂体系中;另一方面,结构中的双层倍半硅氧烷结构呈柔性特征,可以有效提高改性环氧树脂的韧性;因此可以作为改性剂应用于环氧树脂的改性领域,相较于其它类型的倍半硅氧烷,它具有分散性好、分子柔顺性好的特点,在不影响环氧树脂的玻璃化转变温度的同时,可以提高其韧性及耐湿热性能。附图说明图1为实施例1制备的双层倍半硅氧烷环氧树脂改性剂的核磁共振硅谱;图2为实施例1制备的双层倍半硅氧烷环氧树脂改性剂的核磁共振氢谱;图3为实施例3制备的双层倍半硅氧烷环氧树脂改性剂的核磁共振硅谱;图4为实施例3制备的双层倍半硅氧烷环氧树脂改性剂的核磁共振氢谱。具体实施方式下面结合具体实施案例对本发明进行进一步描述,但本发明的保护范围并不仅限于此:以下实施例中,含氢双层倍半硅氧烷和烯丙基双酚a环氧树脂采用相同的制备工艺,具体如下:含氢双层倍半硅氧烷的制备工艺是将苯基三甲氧基硅烷、氢氧化钠、水按照一定比例混合,以异丙醇为溶剂回流反应4h后过滤并干燥得到ddsq-na;其中苯基三甲氧基硅烷、氢氧化钠、水摩尔比为4:2:5。将ddsq-na和三乙胺在四氢呋喃为溶剂下冰水浴降温至0℃以下,通氮气并缓慢加入甲基二氯硅烷,冰水浴反应1h,经过后处理即可制得含氢双层倍半硅氧烷;其中ddsq-na、三乙胺和甲基二氯硅烷摩尔比为1:1:2;后处理工艺为依次进行水洗、盐酸洗、饱和碳酸氢钠洗,水洗三遍,蒸馏后再用100ml甲醇洗三遍并真空干燥即得到产物。烯丙基双酚a环氧树脂制备工艺是将摩尔比为1:0.05:0.02的环氧氯丙烷、烯丙基双酚a和苄基三乙基氯化铵混合后升温至70℃。干燥氮气保护下将20%氢氧化钠水溶液缓慢加入,而后反应2h,升温至110℃采用分水器将体系中的水分除去,而后降温至60℃,持续反应10h以上。将得到的产物用蒸馏水洗涤至中性,并蒸馏出过量的环氧氯丙烷,即得到烯丙基双酚a环氧树脂。实施例1将10g烯丙基双酚a环氧树脂和0.14g卡斯特催化剂(50ppm)加入到100ml甲苯中,氮气保护下升温至75℃,而后将溶解于100ml甲苯中的14.4g含氢双层倍半硅氧烷在2h内缓慢加入,滴加完成后继续反应12h。减压蒸馏除去溶剂即可得到双层倍半硅氧烷环氧树脂改性剂,记为epddsq-1,n值为1(式i型)。本实施例制备产物的硅谱及氢谱分别如图1、2所示,并通过滴定环氧值来确定其分子结构中的环氧值为2.01mmol/g。将50ge51环氧树脂,18.5gdds环氧树脂固化剂和3.45gepddsq-1在50℃下溶解于丙酮中分散均匀,而后在90℃下真空除去溶剂,将其浇铸于钢制模具中,在140℃固化2小时,在160℃固化2小时,在180℃固化2小时。脱模的样品无气泡,外观透明无明显缺陷。样品的性能列于下表1中。实施例2将10g烯丙基双酚a环氧树脂和0.14g卡斯特催化剂(50ppm)加入到100ml甲苯中,氮气保护下升温至75℃,而后将溶解于100ml甲苯中的19.2g含氢双层倍半硅氧烷在2h内缓慢加入,滴加完成后继续反应12h。减压蒸馏除去溶剂即可得到产物epddsq2,n值为2(式i型),环氧值为1.68mmol/g。将50ge51环氧树脂,18.5gdds环氧树脂固化剂和3.45gepddsq2在50℃下溶解于丙酮中分散均匀,而后在90℃下真空除去溶剂,将其浇铸于钢制模具中,在140℃固化2小时,在160℃固化2小时,在180℃固化2小时。脱模的样品无气泡,外观透明无明显缺陷。样品的性能列于下表1中。实施例3将10g烯丙基双酚a环氧树脂和0.14g卡斯特催化剂(50ppm)加入到100ml甲苯中,氮气保护下升温至75℃,而后将溶解于100ml甲苯中的57.6g含氢双层倍半硅氧烷在2h内缓慢加入,滴加完成后继续反应12h。而后加入0.63g烯丙基缩水甘油醚并反应6h。减压蒸馏除去未反应的烯丙基缩水甘油醚和溶剂即可得到产物epddsq3,n值为1(式ii型,式中r基团为),环氧值为1.35mmol/g。本实施例制备产物的硅谱及氢谱分别如图3和4所示。将50ge51环氧树脂,18.5gdds环氧树脂固化剂和3.45gepddsq3在50℃下溶解于丙酮中分散均匀,而后在90℃下真空除去溶剂,将其浇铸于钢制模具中,在140℃固化2小时,在160℃固化2小时,在180℃固化2小时。脱模的样品无气泡,外观透明无明显缺陷。样品的性能列于下表1中。实施例4将10g烯丙基双酚a环氧树脂和0.14g卡斯特催化剂(50ppm)加入到100ml甲苯中,氮气保护下升温至75℃,而后将溶解于甲苯中的57.6g含氢双层倍半硅氧烷在2h内缓慢加入,滴加完成后继续反应12h。而后加入1.2g丁香酚缩水甘油醚并反应6h。减压蒸馏除去未反应的丁香酚缩水甘油醚和溶剂即可得到产物epddsq4,n值为1(式ii型,式中r基团为),环氧值为1.26mmol/g。将50ge51环氧树脂,18.5gdds环氧树脂固化剂和3.45gepddsq4在50℃下溶解于丙酮中分散均匀,而后90℃下真空除去溶剂,将其浇铸于钢制模具中,在140℃固化2小时,在160℃固化2小时,在180℃固化2小时。脱模的样品无气泡,外观透明无明显缺陷。样品的性能列于下表1中。对比例将50ge51环氧树脂,18.5gdds环氧树脂固化剂在50℃下溶解于丙酮中分散均匀,而后在90℃下真空除去溶剂,将其浇铸于钢制模具中,在140℃固化2小时,在160℃固化2小时,在180℃固化2小时。脱模的样品无气泡,外观透明无明显缺陷。样品的性能列于下表1中。表1项目实施例1实施例2实施例3实施例4对比例拉伸强度(mpa)89.693.588.389.958.3冲击强度(kj/m2)25.629.626.326.513.9玻璃化温度(℃)162163163167169断裂韧性(mpa·m1/2)1.141.221.091.080.65吸水率(23℃,%)1.10.80.90.82.6吸水率(100℃,%)1.51.21.31.23.5从表1可以看出,加入双层倍半硅氧烷环氧树脂改性剂后,与未改性环氧树脂相比,环氧树脂的拉伸强度、冲击强度和断裂韧性都有显著提高,吸水率明显降低。玻璃化转变温度没有明显下降,显著改性了环氧树脂的综合性能。当前第1页12