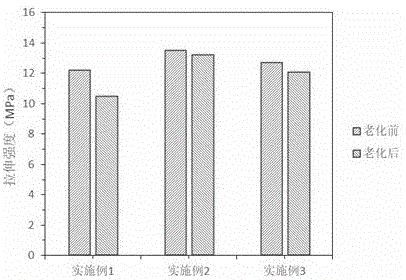
本发明涉及橡胶
技术领域:
,具体涉及一种高耐磨抗冲复合橡胶及其制备方法。
背景技术:
:橡胶行业是国民经济的重要基础产业之一,其为制造军舰、飞机、汽车、拖拉机、收割机等所必需的材料。作为基础产业材料,应用十分广泛,这更要求了橡胶具有普适性,可以适用于各种环境中。特别在一些娱乐用品、建筑产品、玩具等领域,需要耐磨性能优良且抗冲击效果较佳、生产成本较合理的橡胶制品。作物秸秆是作物生产过程中的主要副产品,但由于秸秆量大,缺少生态、经济有效的再利用方法,迫使一些生产部门通过焚烧处理,造成了环境污染,即便通过秸秆堆肥或直接翻入田土,秸秆自然降解时间过长,一般需要60天以上,转化效率不理想,影响了下茬作物的应用。因此,基于作物秸秆制得一种耐磨性能佳且具有高抗冲性能的橡胶是本领域亟待解决的问题。技术实现要素:有鉴于此,本发明的目的在于提供一种高耐磨抗冲复合橡胶及其制备方法,充分利用作物秸秆,可以变废为宝,减少环境污染。为解决以上技术问题,本发明提供的技术方案是,一种高耐磨抗冲复合橡胶,按重量份数计,包括以下组分,丁腈橡胶100份、氧化锌3~8份、硬脂酸0.5~1份、硫磺1~2份、促进剂0.5~1份、炭黑15~25份、生物质碳微球5~10份以及改性生物质氧化石墨烯1~5份;其中,所述生物质碳微球是以天然生物材料为碳源所制备的碳微球;其中,所述改性生物质氧化石墨烯是以天然生物材料为碳源所制备的氧化石墨烯经对苯二胺改性而成。优选的,所述天然生物材料为玉米秸秆、玉米芯、稻草、高粱杆、豆杆中的两种或多种的组合。优选的,所述碳微球的粒径为600~1200目。优选的,所述促进剂为2-硫醇基苯并噻唑。本发明还公开了一种高耐磨抗冲复合橡胶的制备方法,包括,制备生物质碳微球;制备改性生物质氧化石墨烯;按权利要求1所述的重量份数称取原料;将改性生物质氧化石墨烯加入去离子水中,超声分散0.5~1h;加入炭黑、生物质碳微球和硬脂酸,超声分散0.5~1h;加入氧化锌、硫磺和促进剂,超声分散0.5~1h,得到混合溶液;将混合溶液与丁腈橡胶混合,并超声分散0.5~1h,获得稳定的复合乳液;将复合乳液经喷雾干燥,雾化形成复合液液滴,在干燥介质中脱除水分,得到本发明的高耐磨抗冲复合橡胶。优选的,所述复合乳液的浓度为10mg/ml~500mg/ml。优选的,所述制备生物质碳微球的具体方法为:将天然生物材料在温度为60℃的条件下干燥24h,用粉碎机粉碎成1~10mm的粉末,得到富含纤维素的天然生物粉末;将天然生物粉末与水混合,加入高温水反应器中反应,反应器温度为180℃,反应1~2h,反应结束后冷却至室温;将得到的产物进行固液分离,对得到的液相进行离心,收集离心后的重相,用去离子水洗涤,即得生物质碳微球。优选的,所述制备改性生物质氧化石墨烯的具体方法为:制备生物质氧化石墨;将生物质氧化石墨与对苯二胺加入去离子水中,800w功率下超声1~2h,滴加氨水调节ph值至10,90~100℃下反应2~3小时;将所得产物真空抽滤,用无水乙醇与去离子水洗涤数次,置于-55℃下冷冻干燥,即得对苯二胺改性的生物质氧化石墨烯。优选的,所述制备生物质氧化石墨的具体方法为:将天然生物材料隔绝空气进行炭化处理,得到生物质炭;将生物质炭浸渍于含有ni2+的水溶液中24h,干燥得到负载ni的生物炭;将负载ni的生物质炭置于高温炉中反应,将生物炭进行石墨化处理,反应结束后用酸洗涤除去ni,得到生物质石墨;将生物质石墨置于浓硫酸中,加入nano3,在冰水浴中加入kmno4,不断搅拌,使溶液的温度不超过10℃;将混合溶液升温至40℃,反应24h,加入去离子水,继续反应1h;加入去离子水稀释后,再加入质量分数为30%的双氧水,至混合物澄清,过滤;用质量分数为5%的盐酸清洗过滤,将滤饼置于60℃的真空干燥箱中干燥24h,即得生物质氧化石墨。优选的,所述生物质石墨、浓硫酸、nano3、kmno4的重量比为1:20~30:0.5~1:3~4。本发明的有益效果:(1)本发明通过科学合理的配方提高了橡胶的机械强度,使得制备得到的橡胶具有良好的耐磨性能、抗冲击性能和防老化性能,可以有效满足商业和工业生产等要求(2)本发明充分利用作物秸秆,大范围应用,可以变废为宝,减少环境污染。附图说明附图用来提供对本发明的优选的理解,并且构成说明书的一部分,与本发明的实施例一起用于解释本发明,并不构成对本发明的限制。在附图中:图1为本发明实施例1、实施例2、实施例3老化前后的拉伸强度;图2为本发明实施例1、实施例2、实施例3老化前后的断裂伸长率。具体实施方式为了使本领域的技术人员更好地理解本发明的技术方案,下面结合附图和具体实施例对本发明作进一步的详细说明。实施例1(1)制备生物质碳微球;将质量比为1:1:1:1的玉米秸秆、玉米芯、稻草、高粱杆在温度为60℃的条件下干燥24h,用粉碎机粉碎成10mm的粉末,得到富含纤维素的天然生物粉末;将天然生物粉末与水混合,加入高温水反应器中反应,反应器温度为180℃,反应1h,反应结束后冷却至室温;将得到的产物进行固液分离,对得到的液相进行离心,收集离心后的重相,用去离子水洗涤,即得生物质碳微球。(2)制备改性生物质氧化石墨烯;将质量比为1:1:1:1的玉米秸秆、玉米芯、高粱杆、豆杆隔绝空气进行炭化处理,得到生物质炭;将生物质炭浸渍于含有ni2+的水溶液中24h,干燥得到负载ni的生物炭;将负载ni的生物质炭置于高温炉中反应,将生物炭进行石墨化处理,反应结束后用酸洗涤除去ni,得到生物质石墨;将生物质石墨置于浓硫酸中,加入nano3,在冰水浴中加入kmno4,不断搅拌,使溶液的温度不超过10℃;将混合溶液升温至40℃,反应24h,加入去离子水,继续反应1h;加入去离子水稀释后,再加入质量分数为30%的双氧水,至混合物澄清,过滤;用质量分数为5%的盐酸清洗过滤,将滤饼置于60℃的真空干燥箱中干燥24h,即得生物质氧化石墨;所述生物质石墨、浓硫酸、nano3、kmno4的重量比为1:25:0.5:3.5;将生物质氧化石墨与对苯二胺加入去离子水中,800w功率下超声1h,滴加氨水调节ph值至10,100℃下反应2小时;将所得产物真空抽滤,用无水乙醇与去离子水洗涤数次,置于-55℃下冷冻干燥,即得对苯二胺改性的生物质氧化石墨烯。(3)将重量份数为1份的改性生物质氧化石墨烯加入去离子水中,超声分散0.5h;(4)加入20份炭黑、5份生物质碳微球和1份硬脂酸,超声分散0.5h;(5)加入5份氧化锌、1.5份硫磺和1份促进剂,超声分散0.5h,得到混合溶液;(6)将混合溶液与100份丁腈橡胶混合,并超声分散0.5h,获得稳定的复合乳液,复合乳液的浓度为300mg/ml;(7)将复合乳液经喷雾干燥,雾化形成复合液液滴,在干燥介质中脱除水分,得到本实施例的高耐磨抗冲复合橡胶材料。实施例2本实施例2的制备方法与实施例1基本相同,不同之处在于各组分的含量,按重量份数计,丁腈橡胶为100份、氧化锌为5份、硬脂酸为1份、硫磺为1.5份、促进剂为1份、炭黑为20份、生物质碳微球为8份、改性生物质氧化石墨烯为3份;最终得到本实施例的高耐磨抗冲复合橡胶材料。实施例3本实施例3的制备方法与实施例1基本相同,不同之处在于各组分的含量,按重量份数计,丁腈橡胶为100份、氧化锌为5份、硬脂酸为1份、硫磺为1.5份、促进剂为1份、炭黑为20份、生物质碳微球为10份、改性生物质氧化石墨烯为5份;最终得到本实施例的高耐磨抗冲复合橡胶材料。使用平板硫化机分别对实施例1、实施例2、实施例3的高耐磨抗冲复合橡胶材料进行硫化,硫化温度为150℃,硫化时间30min,压强10mpa,硫化完成后,取出胶片,静置至室温,得到测试样品1、样品2和样品3。对样品1、样品2和样品3进行拉伸强度测试,测试方法按照gb/t528-2009标准测试;对样品1、样品2和样品3进行冲击强度测试,测试方法按照gb/t1697-2001标准测试;;对样品1、样品2和样品3进行磨耗测试,测试方法按照gb/t1689-1998标准测试;测试结果如表1所示。表1样品1样品2样品3拉伸强度,mpa12.213.513.3断裂伸长率,%175617261718摩擦系数1.361.341.35磨损率,mm3/n·m0.010.0080.007冲击强度,kj/m246.548.351.2由表1中数据可知,样品2的改性氧化石墨烯和碳微球的含量较样品1增加,拉伸强度明显增加,可能是由于改性氧化石墨烯和碳微球均匀分散在橡胶基体中,在受到外界拉力的时候,碳微球可以增加复合材料的物理交联点,阻止裂纹的扩散;但是当改性氧化石墨烯和碳微球的含量进一步增加时,拉伸强度却有所下降。摩擦系数越小说明复合材料的耐磨性越高,样品2的改性氧化石墨烯和碳微球的含量较样品1增加,摩擦系数降低,耐磨性提高,但是,当样品3中改性氧化石墨烯和碳微球的含量进一步增加时,反而摩擦系数有所降低,可能是由于随着改性氧化石墨烯和碳微球的增加,碳微球分散也不均匀,导致复合材料的缺陷增加,在摩擦力矩的作用下,复合材料开始破损,增大了摩擦系数。冲击强度随改性氧化石墨烯和碳微球的含量的增加而逐渐增加,样品3的冲击强度最大。将样品1、样品2、样品3放入热氧老化箱中,温度为90℃,老化时间96h。再次测试样品1、样品2、样品3老化后的拉伸强度和断裂伸长率;测试结果如图1、图2所示。从结果可以看出,样品2老化后的拉伸强度最大,断裂伸长率也最高,可能是由于样品3中改性氧化石墨烯和碳微球的含量较大,可能影响了分散性,与橡胶的接触面减少,増强效率降低。实施例4(1)按照实施例1的方法制备生物质碳微球;(2)制备生物质氧化石墨烯;将质量比为1:1:1:1的玉米秸秆、玉米芯、高粱杆、豆杆隔绝空气进行炭化处理,得到生物质炭;将生物质炭浸渍于含有ni2+的水溶液中24h,干燥得到负载ni的生物炭;将负载ni的生物质炭置于高温炉中反应,将生物炭进行石墨化处理,反应结束后用酸洗涤除去ni,得到生物质石墨;将生物质石墨置于浓硫酸中,加入nano3,在冰水浴中加入kmno4,不断搅拌,使溶液的温度不超过10℃;将混合溶液升温至40℃,反应24h,加入去离子水,继续反应1h;加入去离子水稀释后,再加入质量分数为30%的双氧水,至混合物澄清,过滤;用质量分数为5%的盐酸清洗过滤,将滤饼置于60℃的真空干燥箱中干燥24h,即得生物质氧化石墨;所述生物质石墨、浓硫酸、nano3、kmno4的重量比为1:25:0.5:3.5;将生物质氧化石墨置于去离子水中,进行超声波剥离2h得到生物质氧化石墨烯分散液,真空干燥,得到生物质氧化石墨烯。(3)将重量份数为3份的生物质氧化石墨烯加入去离子水中,超声分散0.5h;(4)加入20份炭黑、8份生物质碳微球和1份硬脂酸,超声分散0.5h;(5)加入5份氧化锌、1.5份硫磺和1份促进剂,超声分散0.5h,得到混合溶液;(6)将混合溶液与100份丁腈橡胶混合,并超声分散0.5h,获得稳定的复合乳液,复合乳液的浓度为300mg/ml;(7)将复合乳液经喷雾干燥,雾化形成复合液液滴,在干燥介质中脱除水分,得到本实施例的复合橡胶材料。实施例5(1)按照实施例1的方法制备改性生物质氧化石墨烯;(2)将重量份数为3份的改性生物质氧化石墨烯加入去离子水中,超声分散0.5h;(3)加入20份炭黑和1份硬脂酸,超声分散0.5h;(4)加入5份氧化锌、1.5份硫磺和1份促进剂,超声分散0.5h,得到混合溶液;(5)将混合溶液与100份丁腈橡胶混合,并超声分散0.5h,获得稳定的复合乳液,复合乳液的浓度为300mg/ml;(6)将复合乳液经喷雾干燥,雾化形成复合液液滴,在干燥介质中脱除水分,得到本实施例的复合橡胶材料。实施例6(1)按照实施例1的方法制备生物质碳微球;(2)加入20份炭黑、8份生物质碳微球和1份硬脂酸,超声分散0.5h;(3)加入5份氧化锌、1.5份硫磺和1份促进剂,超声分散0.5h,得到混合溶液;(4)将混合溶液与100份丁腈橡胶混合,并超声分散0.5h,获得稳定的复合乳液,复合乳液的浓度为300mg/ml;(5)将复合乳液经喷雾干燥,雾化形成复合液液滴,在干燥介质中脱除水分,得到本实施例的复合橡胶材料。实施例7(1)将20份炭黑和1份硬脂酸,超声分散0.5h;(2)加入5份氧化锌、1.5份硫磺和1份促进剂,超声分散0.5h,得到混合溶液;(3)将混合溶液与100份丁腈橡胶混合,并超声分散0.5h,获得稳定的复合乳液,复合乳液的浓度为300mg/ml;(4)将复合乳液经喷雾干燥,雾化形成复合液液滴,在干燥介质中脱除水分,得到本实施例的复合橡胶材料。实施例8将100份丁腈橡胶加入双辊炼塑机,包辊后,依次加入3份改性氧化石墨烯、1份硬脂酸、5份氧化锌、8份碳微球、1份促进剂和1.5份硫磺进行混炼,打三角包三次,薄通5次,调整辊距,下片,得到本实施例的复合橡胶材料。使用平板硫化机分别对实施例4~8的复合橡胶材料进行硫化,硫化温度为150℃,硫化时间30min,压强10mpa,硫化完成后,取出胶片,静置至室温,得到测试样品4~8。按照上述测试方法分别对样品4~8进行性能测试,并与样品2的性能进行比较,结果如表2所示。表2样品2样品4样品5样品6样品7样品8拉伸强度,mpa13.512.612.211.29.813.1断裂伸长率,%17261701171210269471705摩擦系数1.341.451.621.511.721.38磨损率0.0080.0210.0420.0380.0510.017冲击强度,kj/m248.345.241.242.932.146.8由表2中数据可知,样品4未对生物质氧化石墨烯进行改性,复合橡胶材料的各项性能均有所降低,对苯二胺对生物质氧化石墨烯进行改性后,能够提高其热稳定性,这可能是由于生物质氧化石墨烯被对苯二胺改性后,其表面含氧官能团减少,吸附的游离水减少,结构变得稳定,能够提高复合橡胶材料的性能。样品5中未添加碳微球,样品6中未添加改性生物质氧化石墨烯,样品7中未添加改性生物质氧化石墨烯和碳微球,可以明显看出,改性生物质氧化石墨烯和碳微球对复合橡胶材料的性能影响较大,而且改性生物质氧化石墨烯和碳微球的合理配比的性能明显优于只添加其中一项的性能,改性生物质氧化石墨烯和碳微球两者的添加具有协同增效的作用。样品8采用机械混炼工艺进行制备,复合橡胶材料的各项性能均有所降低,可能是由于机械混炼工艺使得改性生物质氧化石墨烯和碳微球的混合不够均匀,可能影响了分散性,与橡胶的接触面减少,导致増强效率降低,影响最终复合橡胶材料的性能。以上所述仅为本发明的优选实施例而已,并不用于限制本发明,尽管参照前述实施例对本发明进行了详细的说明,对于本领域的技术人员来说,其依然可以对前述各实施例所记载的技术方案进行修改,或者对其中部分技术特征进行等同替换。凡在本发明的精神和原则之内,所作的任何修改、等同替换、改进等,均应包含在本发明的保护范围之内。当前第1页12