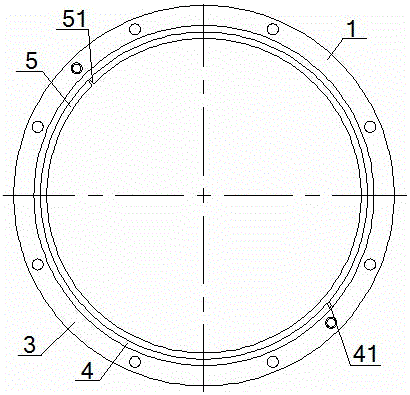
本发明涉及一种喷水推进装置叶轮罩结构,尤其涉及一种喷水推进装置叶轮罩结构及其制造方法,具体适用于延长叶轮罩使用寿命、降低叶轮罩维修成本、缩短叶轮罩维修时间。
背景技术:喷水推进装置中,叶轮位于叶轮罩内腔中,是推进装置形成高速水流的主要工作区域,叶轮外圆和叶轮罩内径之间需要有合适的装配间隙,间隙过小,叶轮在叶轮罩中转动会发生干涉,间隙过大,又会影响喷水推进装置的效率。喷水推进装置工作时需要从进流管道中吸入海水或河水,流过叶轮和叶轮罩,而水流中经常夹杂泥沙及一些尖锐杂质,在叶轮高速旋转的工作过程中,叶轮外圆和叶轮罩内壁会与水流中的杂质发生摩擦,叶轮罩内壁会被磨损,内孔直径变大,使叶轮与叶轮罩之间的间隙加大,影响喷水推进装置的工作效率。因此叶轮和叶轮罩一般均采用不锈钢材质铸造而成,减缓在使用过程中的磨损量。但是在叶轮罩长期使用造成磨损后,智能通过更换整个叶轮罩,才能保证叶轮与叶轮罩间的间隙在设计范围内。由于叶轮罩一般为铸件,更换时需要重新铸造,修理时间长,更换成本较高,可维修性差。中国专利授权公告号为CN101962065B,授权公告日为2012年10月31日的实用新型专利公开了一种船舶喷水推进装置叶轮罩的安装工艺及工装,该工装包括轴管和安装在轴管外围的外圆板,外圆板上设有与叶轮罩定位止口尺寸对应的工装定位止口。采用该工装进行叶轮罩安装时,首先将工装与叶轮罩连接为同轴的整体,将该整体通过调节装置安装在船体尾封板上,工装和叶轮罩分别位于船体尾封板内外;用调节装置使轴管与喷水推进装置同轴线后,进行尾封板与叶轮罩的环氧浇注,然后拆下工装,则实现了叶轮罩在船体尾封板的准确定位安装。虽然该实用新型的叶轮罩能够精确安装控制间隙范围,但其仍存在以下缺陷:1、该实用新型的叶轮罩在长期工作磨损后不易维修,由于叶轮与叶轮罩之间的间隙值要求严格,在叶轮罩损坏后,只能根据叶轮的实际尺寸配套制造新的叶轮罩,由于叶轮罩多为铸件,整体更换成本较高、需要较长的制作时间,照成整个船体的维修周期较长。
技术实现要素:本发明的目的是克服现有技术中存在的叶轮罩使用寿命短、不易修理的问题,提供一种使用寿命长、容易修理的喷水推进装置叶轮罩结构及其制造方法为实现以上目的,本发明的技术解决方案是:一种喷水推进装置叶轮罩结构,包括叶轮罩、叶轮,所述叶轮罩的中部同轴设置有叶轮;所述叶轮罩包括壳体、绝缘衬套和不锈钢衬套,所述不锈钢衬套的外圆周面通过绝缘衬套与壳体的内圆周面压紧配合,所述不锈钢衬套的中部同轴设置有叶轮,所述叶轮与不锈钢衬套之间的间隙值为0.5毫米–1毫米。所述壳体为管形结构的铸铝件;所述绝缘衬套由高密度聚乙烯板、聚四氟乙烯板或高分子聚乙烯板卷制而成,所述绝缘衬套的制作板材厚度为2毫米–3毫米;所述不锈钢衬套由不锈钢板卷制而成,所述不锈钢衬套的制作板材厚度为3毫米–4毫米。所述绝缘衬套的制作板材装配完成后其两边沿之间形成有绝缘衬套接缝,所述不锈钢衬套的制作板材装配完成后其两边沿之间形成有不锈钢衬套接缝,所述绝缘衬套接缝位置与不锈钢衬套接缝位置相异。一种喷水推进装置叶轮罩结构的制造方法,包括以下步骤:第一步:测量:分别测量叶轮的外圆周直径D1、壳体内孔的直径D2,测量完成后进行第二步;第二步:计算板材厚度:a、计算得出壳体与叶轮之间的间隙值为﹙D2-D1﹚÷2毫米;b、根据叶轮罩的大小设定绝缘衬套的板材厚度值的大小为L毫米,则不锈钢衬套的制造板材厚度计算值为﹝﹙D2-D1﹚÷2﹞-L-0.75毫米,其中0.75毫米为叶轮与不锈钢衬套之间的间隙值0.5毫米–1毫米的中间值;c、将不锈钢衬套的制造板材厚度计算值与现有不锈钢板材的厚度值进行对比,取最接近不锈钢衬套制造板材厚度计算值﹝﹙D2-D1﹚÷2﹞-L-0.75的不锈钢板厚度值M,然后计算出利用厚度为M毫米的不锈钢板制造的不锈钢衬套与叶轮的间隙值为﹝﹙D2-D1﹚÷2﹞-L-M毫米,比较该间隙值是否在设计间隙范围值以内,如果间隙尺寸在设计间隙尺寸范围值以内,则直接进行第三步;如果间隙值不在设计间隙范围值以内,则重新取M的值进行计算,直到间隙尺寸满足要求后进行第三步;第三步:制作装配:a、绝缘衬套的制作:切割绝缘衬套的制作板材,使其长度等于壳体内孔的内圆周周长;对切割下来的绝缘衬套制作板材的两端进行预弯曲,然后对进行预弯曲后的绝缘衬套制作板材进行卷制,使卷制后板材的外圆周直径比壳体内孔直径D2大0毫米–1毫米;b、不锈钢衬套的制作:切割制作不锈钢衬套的不锈钢板材,使不锈钢板材的长度比壳体内孔的内圆周周长大2.5毫米–3.5毫米;对切割下来的不锈钢板材的两端进行预弯曲,然后对进行预弯曲后的不锈钢板材进行卷制,使卷制后板材的外圆周直径比绝缘衬套内孔的理论直径D2-2L大1毫米–2毫米;c、装配:将卷制后的绝缘衬套装入壳体中部,再利用压力机将不锈钢衬套均匀的压入绝缘衬套的内孔中,使不锈钢衬套将绝缘衬套紧压在壳体的内壁上,测量装配完成后的不锈钢衬套的内孔直径是否满足设计要求,如满足则直接进行切割修整;如不满足则适度调整不锈钢衬套的装配位置,使不锈钢衬套与绝缘衬套更贴合壳体,直到不锈钢衬套的内孔直径满足设计要求后进行切割修整;d、切割修整:将不锈钢衬套两端卷曲重合部分的切割下来,直至不锈钢衬套形成一个圆管形,装配步骤完成、叶轮罩制作完成。与现有技术相比,本发明的有益效果为:1、本发明一种喷水推进装置叶轮罩结构中壳体内设置不锈钢衬套,叶轮工作时,水流夹杂的泥沙冲击不锈钢衬套的内壁,在叶轮长期工作后不锈钢衬套发生磨损,造成不锈钢衬套与叶轮之间的间隙变大,降低喷水推进装置的工作效率,这时仅需要更换不锈钢衬套,即可完成叶轮罩的修理工作,有效控制不锈钢衬套与叶轮之间的间隙大小。相对于现有技术需要重新铸造并整体更换叶轮罩,本设计仅更换不锈钢衬套,有效的缩短了叶轮罩的修理时间,降低了叶轮罩的修理成本、延长了壳体的使用寿命。因此,本设计的叶轮罩使用寿命长、可维修性好、修理时间短,修理成本低。2、本发明一种喷水推进装置叶轮罩结构中壳体采用铸铝件制作,而现有技术中叶轮罩采用铸钢件,本设计采用铸铝件能够有效减轻喷水推进装置的重量,提高推进效率。因此,本设计的叶轮罩质量更加轻便,有利于提高喷水推进装置效率。3、本发明一种喷水推进装置叶轮罩结构中壳体与不锈钢衬套成分存在差别容易发生电化学反映造成壳体腐蚀,降低叶轮罩的可靠性,因此本设计在壳体与不锈钢衬套之间设置绝缘衬套,避免壳体与不锈钢衬套直接接触,防止壳体与不锈钢衬套发生电化学腐蚀,延长壳体的使用寿命。因此,本设计有效防止壳体发生电化学腐蚀,延长了壳体的使用寿命。4、本发明一种喷水推进装置叶轮罩结构的制造方法中采用卷制工艺制造绝缘衬套和不锈钢衬套,不锈钢衬套将绝缘衬套紧压在壳体的内壁上,相对与其他制作方式,本方法使不锈钢衬套安装更贴合,利用不锈钢衬套的张力涨紧绝缘衬套,使不锈钢衬套与叶轮的配合间隙保持在一个较恒定的值,有利于喷水推进装置的正常运转。因此本设计的制造方法使不锈钢衬套安装更贴合,有利于喷水推进装置的正常运转。附图说明图1是本发明的结构示意图。图2为本发明的右视图。图中:叶轮罩1、叶轮2、壳体3、绝缘衬套4、绝缘衬套接缝41、不锈钢衬套5、不锈钢衬套接缝51、叶轮2的外圆周直径D1、壳体3内孔直径D2。具体实施方式以下结合附图说明和具体实施方式对本发明作进一步详细的说明。参见图1–图2,一种喷水推进装置叶轮罩结构,包括叶轮罩1、叶轮2,所述叶轮罩1的中部同轴设置有叶轮2;所述叶轮罩1包括壳体3、绝缘衬套4和不锈钢衬套5,所述不锈钢衬套5的外圆周面通过绝缘衬套4与壳体3的内圆周面压紧配合,所述不锈钢衬套5的中部同轴设置有叶轮2,所述叶轮2与不锈钢衬套5之间的间隙值为0.5毫米–1毫米。所述壳体3为管形结构的铸铝件;所述绝缘衬套4由高密度聚乙烯板、聚四氟乙烯板或高分子聚乙烯板卷制而成,所述绝缘衬套4的制作板材厚度为2毫米–3毫米;所述不锈钢衬套5由不锈钢板卷制而成,所述不锈钢衬套5的制作板材厚度为3毫米–4毫米。所述绝缘衬套4的制作板材装配完成后其两边沿之间形成有绝缘衬套接缝41,所述不锈钢衬套5的制作板材装配完成后其两边沿之间形成有不锈钢衬套接缝51,所述绝缘衬套接缝41位置与不锈钢衬套接缝51位置相异。一种喷水推进装置叶轮罩结构的制造方法,包括以下步骤:第一步:测量:分别测量叶轮2的外圆周直径D1、壳体3内孔的直径D2,测量完成后进行第二步;第二步:计算板材厚度:a、计算得出壳体3与叶轮2之间的间隙值为﹙D2-D1﹚÷2毫米;b、根据叶轮罩1的大小设定绝缘衬套4的板材厚度值的大小为L毫米,则不锈钢衬套5的制造板材厚度计算值为﹝﹙D2-D1﹚÷2﹞-L-0.75毫米,其中0.75毫米为叶轮2与不锈钢衬套5之间的间隙值0.5毫米–1毫米的中间值;c、将不锈钢衬套5的制造板材厚度计算值与现有不锈钢板材的厚度值进行对比,取最接近不锈钢衬套5制造板材厚度计算值﹝﹙D2-D1﹚÷2﹞-L-0.75的不锈钢板厚度值M,然后计算出利用厚度为M毫米的不锈钢板制造的不锈钢衬套5与叶轮2的间隙值为﹝﹙D2-D1﹚÷2﹞-L-M毫米,比较该间隙值是否在设计间隙范围值以内,如果间隙尺寸在设计间隙尺寸范围值以内,则直接进行第三步;如果间隙值不在设计间隙范围值以内,则重新取M的值进行计算,直到间隙尺寸满足要求后进行第三步;第三步:制作装配:a、绝缘衬套4的制作:切割绝缘衬套4的制作板材,使其长度等于壳体3内孔的内圆周周长;对切割下来的绝缘衬套4制作板材的两端进行预弯曲,然后对进行预弯曲后的绝缘衬套4制作板材进行卷制,使卷制后板材的外圆周直径比壳体3内孔直径D2大0毫米–1毫米;b、不锈钢衬套5的制作:切割制作不锈钢衬套5的不锈钢板材,使不锈钢板材的长度比壳体3内孔的内圆周周长大2.5毫米–3.5毫米;对切割下来的不锈钢板材的两端进行预弯曲,然后对进行预弯曲后的不锈钢板材进行卷制,使卷制后板材的外圆周直径比绝缘衬套4内孔的理论直径D2-2L大1毫米–2毫米;c、装配:将卷制后的绝缘衬套4装入壳体3中部,再利用压力机将不锈钢衬套5均匀的压入绝缘衬套4的内孔中,使不锈钢衬套5将绝缘衬套4紧压在壳体3的内壁上,测量装配完成后的不锈钢衬套5的内孔直径是否满足设计要求,如满足则直接进行切割修整;如不满足则适度调整不锈钢衬套5的装配位置,使不锈钢衬套5与绝缘衬套4更贴合壳体3,直到不锈钢衬套5的内孔直径满足设计要求后进行切割修整;d、切割修整:将不锈钢衬套5两端卷曲重合部分的切割下来,直至不锈钢衬套5形成一个圆管形,装配步骤完成、叶轮罩1制作完成。本发明的原理说明如下:制作方法中:根据叶轮罩1的大小设定绝缘衬套4的板材厚度值的大小为L毫米,由于船体大小不同,对应的叶轮罩2的大小也不一样,本设计中绝缘衬套4起隔离作用防止壳体3与不锈钢衬套5之间发生电化学腐蚀,对于小的叶轮罩1,其卷制半径较小,使用较薄的绝缘衬套4,即可达到绝缘效果;对于直径较大的叶轮罩1,由于其卷制半径较大,需要较厚的板材制造绝缘衬套4,使其机械性能与绝缘性能达到设计要求。故绝缘衬套4的板材厚度值L的大小是根据叶轮罩1的大小决定的。不锈钢板材厚度M的取值:由于不锈钢衬套5的制造板材厚度计算值﹝﹙D2-D1﹚÷2﹞-L-0.75不一定会刚好等于现有的不锈钢板的标准厚度,在实际制造过程中,利用不锈钢衬套5的制造板材厚度计算值﹝﹙D2-D1﹚÷2﹞-L-0.75做为参考量,对比现有不锈钢板标准厚度的取值,选取与﹝﹙D2-D1﹚÷2﹞-L-0.75最接近的值M做为不锈钢板材的厚度值进行验算,最后得出实际使用制造不锈钢衬套5的不锈钢板材的厚度。维修更换:当不锈钢衬套5由于长期使用磨损时,按原有设计尺寸制作新的不锈钢衬套5,然后用新的不锈钢衬套5更换磨损的不锈钢衬套5,即可完成维修更换。绝缘衬套接缝41位置与不锈钢衬套接缝51位置相异,这样的设计能够有效防止锈钢衬套接缝51处的不锈钢板通过绝缘衬套接缝41与壳体3发生电化学反映腐蚀壳体3。高密度聚乙烯板、聚四氟乙烯板或高分子聚乙烯板均具有硬度优韧性好,易加工处理的有点,同时具有优良的绝缘性能,因此符合绝缘衬套4的制作材料要求。实施例1:一种喷水推进装置叶轮罩结构,包括叶轮罩1、叶轮2,所述叶轮罩1的中部同轴设置有叶轮2,所述叶轮罩1包括壳体3、绝缘衬套4和不锈钢衬套5,所述不锈钢衬套5的外圆周面通过绝缘衬套4与壳体3的内圆周面压紧配合,所述不锈钢衬套5的中部同轴设置有叶轮2,所述叶轮2与不锈钢衬套5之间的间隙值为0.5毫米–1毫米;所述壳体3为管形结构的铸铝件;所述绝缘衬套4由高密度聚乙烯板、聚四氟乙烯板或高分子聚乙烯板卷制而成,所述绝缘衬套4的制作板材厚度为2毫米–3毫米;所述不锈钢衬套5由不锈钢板卷制而成,所述不锈钢衬套5的制作板材厚度为3毫米–4毫米;所述绝缘衬套4的制作板材装配完成后其两边沿之间形成有绝缘衬套接缝41,所述不锈钢衬套5的制作板材装配完成后其两边沿之间形成有不锈钢衬套接缝51,所述绝缘衬套接缝41位置与不锈钢衬套接缝51位置相异。一种喷水推进装置叶轮罩结构的制造方法,包括以下步骤:第一步:测量:分别测量叶轮2的外圆周直径D1、壳体3内孔的直径D2,测量完成后进行第二步;第二步:计算板材厚度:a、计算得出壳体3与叶轮2之间的间隙值为﹙D2-D1﹚÷2毫米;b、根据叶轮罩1的大小设定绝缘衬套4的板材厚度值的大小为L毫米,则不锈钢衬套5的制造板材厚度计算值为﹝﹙D2-D1﹚÷2﹞-L-0.75毫米,其中0.75毫米为叶轮2与不锈钢衬套5之间的间隙值0.5毫米–1毫米的中间值;c、将不锈钢衬套5的制造板材厚度计算值与现有不锈钢板材的厚度值进行对比,取最接近不锈钢衬套5制造板材厚度计算值﹝﹙D2-D1﹚÷2﹞-L-0.75的不锈钢板厚度值M,然后计算出利用厚度为M毫米的不锈钢板制造的不锈钢衬套5与叶轮2的间隙值为﹝﹙D2-D1﹚÷2﹞-L-M毫米,比较该间隙值是否在设计间隙范围值以内,如果间隙尺寸在设计间隙尺寸范围值以内,则直接进行第三步;如果间隙值不在设计间隙范围值以内,则重新取M的值进行计算,直到间隙尺寸满足要求后进行第三步;第三步:制作装配:a、绝缘衬套4的制作:切割绝缘衬套4的制作板材,使其长度等于壳体3内孔的内圆周周长;对切割下来的绝缘衬套4制作板材的两端进行预弯曲,然后对进行预弯曲后的绝缘衬套4制作板材进行卷制,使卷制后板材的外圆周直径比壳体3内孔直径D2大0毫米–1毫米;b、不锈钢衬套5的制作:切割制作不锈钢衬套5的不锈钢板材,使不锈钢板材的长度比壳体3内孔的内圆周周长大2.5毫米–3.5毫米;对切割下来的不锈钢板材的两端进行预弯曲,然后对进行预弯曲后的不锈钢板材进行卷制,使卷制后板材的外圆周直径比绝缘衬套4内孔的理论直径D2-2L大1毫米–2毫米;c、装配:将卷制后的绝缘衬套4装入壳体3中部,再利用压力机将不锈钢衬套5均匀的压入绝缘衬套4的内孔中,使不锈钢衬套5将绝缘衬套4紧压在壳体3的内壁上,测量装配完成后的不锈钢衬套5的内孔直径是否满足设计要求,如满足则直接进行切割修整;如不满足则适度调整不锈钢衬套5的装配位置,使不锈钢衬套5与绝缘衬套4更贴合壳体3,直到不锈钢衬套5的内孔直径满足设计要求后进行切割修整;d、切割修整:将不锈钢衬套5两端卷曲重合部分的切割下来,直至不锈钢衬套5形成一个圆管形,装配步骤完成、叶轮罩1制作完成。