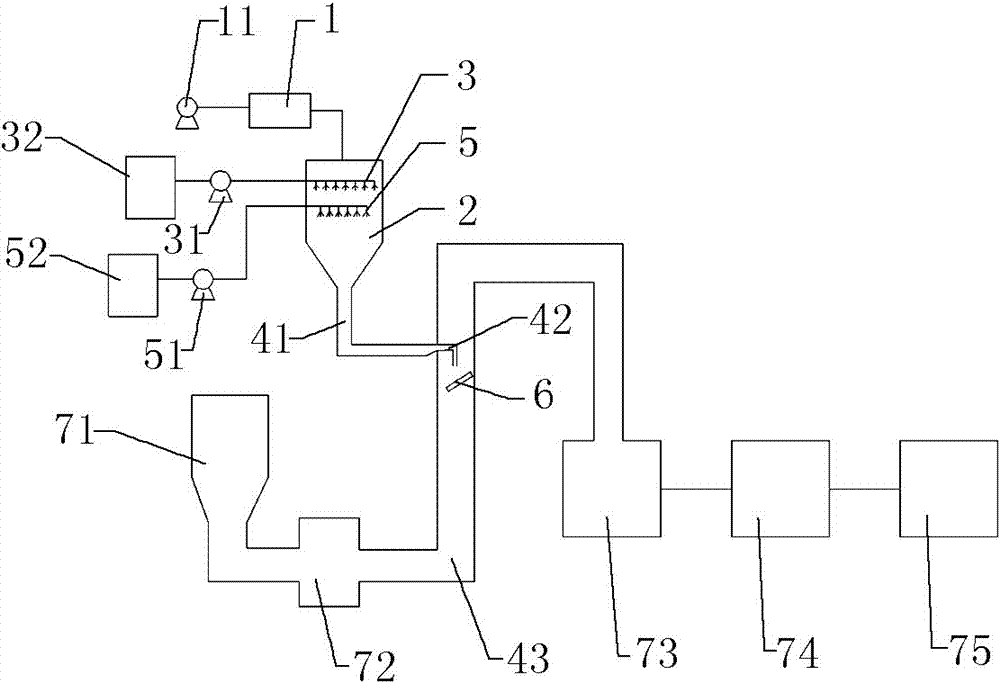
本发明涉及烟气脱硫系统
技术领域:
,特别是涉及一种利用尿素热解余热的so3脱除系统及其脱除方法。
背景技术:
:煤炭燃烧产生的烟气中含有一定浓度的so2和so3,其中so2是煤炭在锅炉中燃烧产生,浓度为1500~18000mg/m3,主要集中在3000~6000mg/m3;而so3来源于两部分,一部分是在锅炉内直接燃烧产生,浓度约占so2浓度的0.5%-1.5%;另一部分是so2经过scr脱硝反应器后被氧化成so3,这部分的转化率约占so2浓度的0.5%-1.5%。因此,在scr反应器出口烟气中so3浓度约占so2浓度的1%-3%。在通常的湿法脱硫过程中,只有一少部分so3能被脱除,大部分还是被直接排入大气中,so3的大气排放目前尚未制定统一的排放标准,由于so3在烟气中主要以气溶胶的形式存在,造成烟囱最终排放“蓝烟”、“烟羽拖尾”现象;so3会加重雾霾和温室效应;而且scr脱硝过程中未反应的氨与so3反应会生成硫酸氢铵,硫酸氢铵极易附着在空预器表面,吸附飞灰,造成空预器的压降增大,排烟温度升高,机组效率下降,运行成本增加,这种现象在负荷较低时尤为显著,即便在高负荷下由于氨逃逸以及部分so2催化转化为so3,同样会生成硫酸氢铵,长期运行积累也会危及空预器正常运行。此外,so3在空预器的低温段造成烟气中酸露点升高,空预器的低温腐蚀严重,在scr运行条件下,设备寿命下降。目前,烟气中so3的控制技术有:燃用低硫煤、混煤,使用低低温电除尘器,采用湿式静电除尘器,炉内或炉后喷碱性吸收剂等。使用低硫煤、混煤简单、直接,但是提高运行成本。使用低低温电除尘器或湿式静电除尘器对so3的脱除率高,但由于处于环保岛的末端,无法解决空预器积灰、腐蚀、堵塞等问题,不能降低空预器出口烟气温度,锅炉热效率低,投资成本高。向炉内喷射碱性吸收剂,如mg(oh)2,浆液迅速蒸发变成mgo颗粒,然后与so3反应生成mgso4,可有效脱除燃烧过程中产生的so3,降低scr反应器入口烟气中so3的浓度,但是锅炉内的温度较高,有700-1000℃,技术控制上难度较大,碱性吸收剂在进入锅炉内时瞬时蒸发成细小颗粒,分散效果差,对烟气中so3的脱除效率不高,造成碱性吸收剂的消耗量较大,运行成本较高,而且对scr中产生的so3的脱除效率相对较低。在炉后烟气中喷入碱性吸收剂,如mgo、nahso3、na2co3、天然碱等,若直接喷入碱性吸收剂颗粒,颗粒较大,利用效率不高;若雾化后干燥为细小颗粒,需额外增加配套的干燥设备,提高运行成本;且喷入位置一般在省煤器或scr与空气预热器之间,可有效降低so3的浓度,但是碱性吸收剂的喷射量较高,而钙基的吸收剂会增加飞灰的比电阻,会降低电除尘器的效率;在空预器后喷入碱性吸收剂则不能避免空预器的积灰、腐蚀和堵塞问题,空预器出口的烟气温度较高,锅炉的热效率低下。技术实现要素:本发明提供一种碱性吸收剂利用率高、运行成本低、提高能源利用率、可有效减缓或避免空预器的积灰、腐蚀和堵塞问题的利用尿素热解余热的so3脱除系统。解决的技术问题是:现有脱除烟气中so3的方法,或运行成本高,或无法避免空预器的积灰、腐蚀和堵塞问题,或碱性吸收剂的利用率低下,或碱性吸收剂颗粒分散均匀性差。为解决上述技术问题,本发明采用如下技术方案:本发明利用尿素热解余热的so3脱除系统,包括空气加热器、热解炉、尿素喷枪、碱性吸收剂喷枪和涡流混合器;所述空气加热器的进气口与风机连通、出气口通过管道与热解炉的进气口连通;热解炉的进气口下方均匀设置有尿素喷枪、出气口通过热解气管道与喷氨管连接,进入喷氨管之前的系统内设置有碱性吸收剂喷枪,所述喷氨管的出气口与燃煤烟道连接,喷氨管的喷射方向与烟气流动方向相反;喷氨管的出气口下方倾斜设置有涡流混合器,燃煤烟道的进气口与锅炉后的省煤器出口连接、出气口依次与scr反应器、空气预热器和除尘器连接。本发明利用尿素热解余热的so3脱除系统,进一步的,所述尿素喷枪的进液口通过尿液输送泵与尿素溶液储罐连接;所述碱性吸收剂喷枪通过碱液输送泵与碱性吸收剂溶液储罐连接。本发明利用尿素热解余热的so3脱除系统,进一步的,所述碱性吸收剂喷枪的数量为1-10个,每个碱性吸收剂喷枪上带有1-7个喷嘴。本发明利用尿素热解余热的so3脱除系统,进一步的,所述碱性吸收剂喷枪设置在热解炉内、尿素喷枪正下方,所述碱性吸收剂喷枪与尿素喷枪的高度差为0.5m-1.5m。本发明利用尿素热解余热的so3脱除系统,进一步的,所述碱性吸收剂喷枪设置在热解气管道内,所述碱性吸收剂喷枪的喷射方向与热解气管道内气流方向一致;所述碱性吸收剂喷枪沿热解气管道延伸方向并排设置。本发明利用尿素热解余热的so3脱除系统,进一步的,所述尿素喷枪的喷射方向与热空气的流动方向垂直。本发明利用尿素热解余热的so3脱除系统,进一步的,所述涡流混合器与烟气流动方向的夹角为30-40°;所述涡流混合器固定在燃煤烟道的内侧壁上。本发明利用尿素热解余热的so3脱除系统的脱除方法,包括以下步骤:包括以下步骤:步骤一、空气加热:空气经过加热,温度升至600-650℃;步骤二、尿素热解:高温空气进入热解炉,与喷入的尿素溶液接触,尿素溶液发生热解,生成大量的nh3、hnco和co2;步骤三、吸收剂干燥:碱性吸收剂溶液雾化为细小液滴后,与尿素热解产物接触,碱性吸收剂液滴吸热瞬时蒸发干燥为细小颗粒,碱性吸收剂的喷射量为烟气中so3摩尔量的1~5倍;步骤四、so3脱除:步骤三所得细小颗粒均匀分散后与烟气中的so3和水蒸气反应生成硫酸盐颗粒;步骤五、除尘:经过scr反应器处理的烟气经过除尘器过滤去除其中的硫酸盐颗粒,然后进入后续的净化处理。本发明利用尿素热解余热的so3脱除系统的脱除方法,进一步的,步骤二中尿素溶液的浓度为35-52%,尿素的喷射量为烟气中nox摩尔量的0.4~0.6倍。本发明利用尿素热解余热的so3脱除系统的脱除方法,进一步的,步骤三中碱性吸收剂溶液的浓度为1-30%;所述碱性吸收剂为碳酸钠、碳酸氢钠、碳酸钾和碳酸氢钾中的一种或几种。本发明利用尿素热解余热的so3脱除系统及其脱除方法与现有技术相比,具有如下有益效果:本发明利用尿素热解余热的so3脱除系统在尿素热解系统中引入了碱性吸收剂溶液的雾化蒸发装置,利用尿素热解余热实现了吸收剂细小颗粒的制备,避免了配备附加的雾化蒸干设备和能源装置,简化了系统的构成,减少了能源的浪费,提高能源利用率,降低了系统的运行成本。本发明将碱性吸收剂细小颗粒喷入scr反应器之前的燃煤烟道中,并在烟道内设置了涡流混合器,提高了吸收剂细小颗粒的分散性,大大提高了so3的脱除效率。本发明利用尿素热解余热的so3脱除系统的脱除方法,在scr反应器前的烟道中喷入碱性吸收剂细小颗粒与烟气中的so3发生反应,生成对环境和系统无危害的硫酸盐固体颗粒,最终由除尘器捕集;降低了环境负担,同时减少so3对脱硝scr催化剂和空气预热器的影响。使得scr反应器出口处的so3浓度低于5ppm。so3与吸收剂接触时间长,提高了so3的脱除率,降低了碱性吸收剂的喷射量,运行成本较低,更加经济环保。下面结合附图对本发明的利用尿素热解余热的so3脱除系统及其脱除方法作进一步说明。附图说明图1为实施例1中so3脱除系统的结构示意图;图2为实施例2中so3脱除系统的结构示意图。附图标记:1-空气加热器;11-风机;2-热解炉;3-尿素喷枪;31-尿素输送泵;32-尿素溶液储罐;41-热解气管道;42-喷氨管;43-燃煤烟道;5-碱性吸收剂喷枪;51-碱液输送泵;52-碱性吸收剂溶液储罐;6-涡流混合器;71-锅炉;72-省煤器;73-scr反应器;74-空气预热器;75-除尘器。具体实施方式实施例1如图1所示,本发明利用尿素热解余热的so3脱除系统包括空气加热器1、热解炉2、尿素喷枪3、碱性吸收剂喷枪5和涡流混合器6;空气加热器1的进气口与风机11连通、出气口通过管道与热解炉2的进气口连通;热解炉2的进气口下方均匀设置有尿素喷枪3,尿素喷枪3的进液口通过尿素输送泵31与尿素溶液储罐32连接,尿素喷枪3的喷射方向与热空气的流动方向垂直;热解炉2的出气口与热解气管道41连接,热解气管道41内设置有碱性吸收剂喷枪5,碱性吸收剂喷枪5通过碱液输送泵51与碱性吸收剂溶液储罐52连接,碱性吸收剂喷枪5的数量为1-10个,每个碱性吸收剂喷枪5上设置1-7个喷嘴,碱性吸收剂喷枪5沿热解气管道41延伸方向并排设置,碱性吸收剂喷枪5的喷射方向与热解气管道41内气流方向一致;热解气管道41另一端通过喷氨管42与燃煤烟道43连接,喷氨管42的喷射方向与烟气流动方向相反;燃煤烟道43的内侧壁上设置有涡流混合器6,涡流混合器6倾斜设置在喷氨管42的出气口下方,涡流混合器6与烟气流动方向的夹角为30-40°;燃煤烟道43的进气口与锅炉71后省煤器72的烟气出口连接、出气口依次与scr反应器73、空气预热器74和除尘器75连接。实施例2如图2所示,本发明利用尿素热解余热的so3脱除系统包括空气加热器1、热解炉2、尿素喷枪3、碱性吸收剂喷枪5和涡流混合器6;空气加热器1的进气口与风机11连通、出气口通过管道与热解炉2的进气口连通;热解炉2的进气口下方均匀设置有尿素喷枪3,尿素喷枪3的进液口通过尿素输送泵31与尿素溶液储罐32连接,尿素喷枪3的喷射方向与热空气的流动方向一致;尿素喷枪3正下方设置有碱性吸收剂喷枪5,碱性吸收剂喷枪5与尿素喷枪3的高度差为0.5-1.5m,碱性吸收剂喷枪5通过碱液输送泵51与碱性吸收剂溶液储罐52连接,碱性吸收剂喷枪5的数量为1-10个,每个碱性吸收剂喷枪5上设置1-7个喷嘴,碱性吸收剂喷枪5的喷射方向与热解气管道41内气流方向一致;热解炉2的出气口与热解气管道41连接,热解气管道41另一端通过喷氨管42与燃煤烟道43连接,喷氨管42的喷射方向与烟气流动方向相反;燃煤烟道43的内侧壁上设置有涡流混合器6,涡流混合器6倾斜设置在喷氨管42的出气口下方,涡流混合器6与烟气流动方向的夹角为30-40°;燃煤烟道43的进气口与锅炉71后省煤器72的烟气出口连接、出气口依次与scr反应器73、空气预热器74和除尘器75连接。应用实施例1采用实施例1中所示的so3脱除系统,按照以下脱除方法控制so3脱除系统,具体包括以下步骤:步骤一、空气加热:空气经过加热,温度升至600-650℃;步骤二、尿素热解:高温空气进入热解炉2,与喷入的尿素溶液接触,尿素溶液发生热解,生成大量的nh3、hnco和co2;尿素溶液的浓度为35-52%,尿素的喷射量为烟气中nox摩尔量的0.4~0.6倍,高温空气在热解炉2内的流速控制为0.8-2m/s;实施例的具体取值如表1所示;步骤三、吸收剂干燥:碱性吸收剂溶液经过碱性吸收剂喷枪5雾化为细小液滴,与350-550℃的含有尿素热解产物的热气体接触,碱性吸收剂液滴吸热瞬时蒸发干燥为细小颗粒,所得细小颗粒平均直径小于50μm,部分碱性吸收剂与尿素热解产物发生化学反应,生成二氧化碳、水、氰酸盐细小颗粒;所用碱性吸收剂溶液的浓度为1-30%,碱性吸收剂为碳酸钠、碳酸氢钠、碳酸钾和碳酸氢钾中的一种或几种;碱性吸收剂的喷射量为烟气中so3摩尔量的1~5倍;实施例的具体取值如表1所示;步骤四、so3脱除:步骤三所得细小颗粒随热解气喷入燃煤烟道43,均匀分散后与烟气中的so3和水蒸气反应生成硫酸盐颗粒;各实施例的具体取值如表1所示;步骤五、除尘:经过scr反应器73处理的烟气经过除尘器75过滤取出其中的硫酸盐颗粒,然后进入后续的净化处理。同时设置未喷射碱性吸收剂的空白对照组。表1各应用实施例参数控制对照组1应用1应用2应用3尿素溶液浓度%48354852尿素喷射量0.580.520.580.63碱性吸收剂的种类无碳酸钠碳酸钠和碳酸氢钠碳酸氢钾碱性吸收剂的浓度%011530碱性吸收剂喷射量01.21.61.6表中:1、尿素喷射量为烟气中nox的摩尔量的倍数;2、碱性吸收剂喷射量为烟气中so3的摩尔量的倍数。上述各应用实施例,待系统工作稳定后,对scr出口的烟气so3浓度进行测量:测量的具体结果如表2所示。表2so3浓度测量结果对照组1应用1应用2应用3so3浓度ppm14.74.12.92.2实施例1所示脱除系统,在热解气管道内设置碱性吸收剂喷枪,利用尿素热解后的高温烟气制备碱性吸收剂微细颗粒,利用脱硝系统的涡流混合器将制备的碱性吸收剂微细颗粒均匀分散,使微细颗粒与烟气中的so3充分接触,提高了碱性吸收剂对so3的脱除效率。由表2可知,本发明所示脱除方法与未喷射碱性吸收剂相比,在scr反应器出口处的so3浓度降低了70-85%,将其控制在5ppm以内,so3得到了有效的脱除。应用实施例2采用实施例2中所示的so3脱除系统,采用与应用实施例1相同的脱除方法,测得的scr出口的烟气中的so3浓度如表3所示。表3so3浓度测量结果对照组应用1应用2应用3so3浓度ppm14.74.32.82.4实施例2所示脱除系统,在热解炉内设置碱性吸收剂喷枪,利用尿素热解后的高温烟气制备的碱性吸收剂微细颗粒,然后通过涡流混合器将制备的微细颗粒均匀分散,使微细颗粒与烟气中的so3充分接触,提高了碱性吸收剂对so3的脱除效率。由表3可知,本发明所示脱除方法与未喷射碱性吸收剂相比,在scr反应器出口处的so3浓度降低了70-85%,控制在了5ppm以内,so3得到了有效的脱除。以上所述的实施例仅仅是对本发明的优选实施方式进行描述,并非对本发明的范围进行限定,在不脱离本发明设计精神的前提下,本领域普通技术人员对本发明的技术方案作出的各种变形和改进,均应落入本发明权利要求书确定的保护范围内。当前第1页12